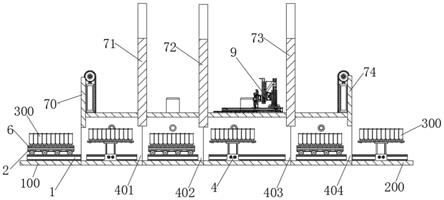
1.本发明涉及一种保温杯加工装置,尤其是一种对杯体抽真空并焊接抽真空孔的保温杯抽真空装备及其抽真空方法。
背景技术:
2.目前保温杯一般都是真空保温杯,即双层结构杯体的夹层被抽成真空,保温杯的保温性能由夹层的真空度决定,现有抽真空工艺一般分为有尾抽真空工艺和无尾抽真空工艺,而密封性能更好、可靠性更高的无尾抽真空工艺,被行业内各企业广泛采用。无尾抽真空工艺主要指保温杯抽真空孔封接的方式为采用钎焊料封接,行业采用的钎焊料一般为玻璃基材,原理是在真空炉内利用高温将钎焊料融化后与保温杯底部抽真空孔融合一体来实现封接,进而使保温杯实现真空保温的功能。无尾抽真空工艺需要全程在高真空条件下进行,目前是将保温杯放入单炉真空机的真空炉内,从常温低抽开始到高温高抽执行再到降温等全部的抽真空过程,该过程需要的能耗非常的高,且加工周期长,一炉产品的加工周期需要5小时以上,生产效率和节能方面都非常的低下,且不能适应目前的自动化改造。
3.为此,业内技术人员进行了多方改进,如专利“201910255200.4用于真空保温杯连续抽真空的真空室及连续抽真空工艺”,其方案自进料到出料依次包括预热室、钎焊室和冷却室三室;又如专利“201821858591.6保温杯全自动高真空钎焊设备”,其方案包括相互连接依次设置的预抽室、加热室、焊接室、冷却室及出杯室。上述两个方案仅仅是拆分了现有抽真空工艺,设置了多个腔室,本质还是针对玻璃基材钎焊料的封接工艺,但玻璃基材钎焊料需要专门采购配备,玻璃基材钎焊料的成本也较高,而且包含重金属对环境也造成一定的污染,其熔融封接的温度还要求达到500度以上,其材料熔融封接后为黑色,对喷塑杯体塑粉的吸附性也较差,此外,该种封接属于异种材料焊接,焊接牢度相对不高,进而会使部分杯体在封接后掉落钎焊材料,导致不真空,报废率高。
技术实现要素:
4.本发明的目的是提供一种保温杯抽真空装备及其抽真空方法,既大大降低了成本、确保了焊接质量、对环境没有重金属污染,又大大降低了焊接难度、提高了产品合格率和加工效率,节能减排的同时,实现自动化批量生产。
5.为实现上述目的,本发明采用如下技术方案:
6.技术方案1:一种保温杯抽真空装备,其包括依次设置的预抽室、加热室、焊接室和冷却室,相邻腔室均通过可上下移动的插板阀连通或隔离,腔室底部均设有物料连续输送装置,预抽室、加热室、焊接室均设有加热装置;还包括可控活动设于焊接室上方的激光焊接装置;所述焊接室顶面设有至少一块透明视窗,且激光焊接装置的激光束穿过透明视窗熔融设于杯底中心孔处的焊接球;所述加热室和焊接室均与高真空抽气系统连接,预抽室和冷却室均与低真空抽气系统连接;所述预抽室的入口处设有可上下移动的入口阀,冷却室的出口处设有可上下移动的出口阀。
7.优选的,还包括可控活动设于焊接室上方的视觉扫描相机。
8.优选的,所述透明视窗为耐高温玻璃;所述透明视窗的可视范围覆盖所有保温杯;所述透明视窗的数量与所有保温杯数量相同且一一对应;所述透明视窗均为边长尺寸30~60mm的方形或直径为30~60mm的圆形。
9.优选的,所述物料连续输送装置包括分别设于各个腔室底部的轨道、设于各个腔室外侧的传动机构、可控活动设于轨道上的料车、置于料车上用于放置保温杯的料架;所述传动机构控制料车沿轨道行驶,且传动机构均包括与动力源连接的传动轴组件、设于传动轴组件尾端的传动齿轮、设于料车底部与传动齿轮配合传动的齿条。
10.优选的,各个腔室处还设有检测到位机构;所述检测到位机构包括设于腔室外的感应开关、与感应开关信号连接的感应片、一端与感应片固定的检测杆、设于检测杆穿入腔室内一端的平衡块、设于料车侧面靠近平衡块一端的撞块、为感应片提供回复力的磁铁;所述撞块与平衡块接触过渡面为弧面,平衡块与撞块接触后,感应开关通过感应片的旋转形变接通或闭合,控制料车的停止或运行。
11.优选的,所述顶料机构间隔设置;所述预抽室前方的装料平台上、冷却室后方的卸料平台上,均设有与所述物料连续输送装置的轨道相对应的轨道;所述料车底部设有至少三对轮毂。
12.优选的,每组顶料机构对称设置在轨道外侧;所述料架边沿伸出料车边缘;所述顶料机构包括位于料架边沿下方的顶杆,且顶杆与动力源连接,在动力源作用下,顶杆顶起料架边沿将料架从料车上顶起。
13.优选的,所述料架上设有放置保温杯的定位夹具,且定位夹具与料架为拔插式连接。
14.技术方案2:一种保温杯抽真空装备的抽真空方法,其包括上述的保温杯抽真空装备,执行以下步骤,
15.s1:开启入口阀,装载保温杯的料架通过料车经轨道从装料平台进入低真空预抽室的指定位置定位停车,顶料机构将料架顶起脱离料车,料车退出低真空预抽室回到装料平台,顶料机构带动料架下降复位并关闭入口阀,系统检测入口阀关闭后开始低抽作业,当检测到真空度达到4
×
102pa时,加快抽真空速度,同时开始预热,温度达到200度后关闭加热,当检测到真空度达到1
×
10-1
pa时预抽完成;
16.s2:预抽完成后,打开加热室的插板阀,低真空预抽室顶料机构将料架顶起,同时高真空加热室的料车经轨道进入低真空预抽室定位停车,顶料机构下降将料架放置在料车上,料车带料架经轨道进入高真空加热室并关闭加热室的插板阀,此时低真空预抽室重复步骤s1;系统检测关闭加热室阀后,开始高抽作业同时开始加热炉内温度到450度,当检测到真空度达到1
×
10-3
pa时,在温度450度的条件下保温20分钟,激活吸气剂;
17.s3:高真空保温焊接室与高真空加热室同步开始高抽作业,将高真空保温焊接室的真空度达到1
×
10-3
pa,温度达到450度,且一直保持;在s2步骤激活吸气剂后,打开焊接室的插板阀,料车带料架经轨道进入高真空保温焊接室定位停车后,顶料机构将料架顶起脱离料车,料车退回到高真空加热室,顶料机构带动料架下降复位并关闭焊接室阀,此时高真空加热室重复步骤s2;系统检测关闭焊接室的插板阀后,激光焊接装置的激光焊接枪位置归零,从零点位置开始透过透明视窗按照预设行进参数依次进行焊接,所述预设行进参数
与料架保温杯摆放间隔对应,激光焊接枪使焊接球与保温杯抽真空孔熔融为一体完成焊接;
18.s4:焊接完成后,打开冷却室的插板阀,高真空保温焊接室顶料机构将料架顶起,同时低真空冷却室的料车经轨道进入高真空保温焊接室定位停车,顶料机构下降将料架放置在料车上,料车带料架经轨道进入低真空冷却室并关闭冷却室的插板阀,此时高真空保温焊接室重复步骤s3;系统检测关闭冷却室的插板阀后,监测冷却室室温和室内压力,当室温降到230度时,打开充气阀,向冷却室填充空气或氮气,当室内压力与外部压力相同时,冷却完成;
19.s5:冷却完成后,打开出口阀,料车带料架经轨道进入卸料平台定位停车,卸料后料车退回到低真空冷却室并关闭出口阀,此时低真空冷却室重复步骤s4。
20.优选的,所述步骤s3中激光焊接装置在焊接前,可控活动设于焊接室上方的视觉扫描相机透过透明视窗扫描所有保温杯的焊接位置,激光焊接枪根据视觉扫描结果透过透明视窗进行定点焊接,使焊接球与保温杯抽真空孔熔融为一体完成焊接。
21.与现有技术相比本发明的有益效果:一是采用激光焊接的方式,从常温低抽、高温高抽、保温高抽焊接到低抽降温,缩短了整体工艺流程,大大降低了能耗,免去了玻璃基材钎焊料的使用,降低了封接材料成本的同时,也避免了使用玻璃基材钎焊料的缺点,即对抽真空封接工艺的温度要求更低,降低能耗的同时,也避免了重金属排放对环境的污染;二是直接采用与杯体材质相同的金属焊接球进行激光焊接,这样同种金属焊接牢度更高、稳定性更强且封接后颜色与杯身一致,对塑粉的吸附性也与杯身一致,提高后序喷涂效果;三是激光焊接在透明视窗处进行,这样既保证了激光焊接的正常进行,也确保了焊接室的保温性能,提高产品加工质量;四是通过物料连续输送装置,将物料连续输送至各个腔室,多室连续作业抽真空,实现批量生产,降低能耗的同时,提高生产效率,还可以实现对接其他工序生产线,自动化程度高,每个腔室可以设置单独启闭的室门,这样可以单独对各个腔室进行查看检修。
22.进一步的有益效果:一是视觉扫描相机设于焊接室上方,视觉扫描相机透过透明视窗扫描需要焊接的位置,根据扫描结果,激光焊接装置的激光焊接枪透过透明视窗进行焊接作业,焊接定位更精确,焊接质量更高;二是透明视窗的可视范围覆盖所有保温杯,透明视窗采用耐高温玻璃,这样既确保了高真空保温焊接室的保温性能,又保证了激光焊接的顺利完成,提高焊接质量;三是透明视窗的数量设为与保温杯数量相同且一一对应,这样既便于视觉扫描相机的对应扫描和激光焊接装置的对应焊接,也提高了焊接室的保温性能;四是保温杯放于料车的料架上,料车在分段设于腔室底部的轨道上将保温杯传送至各个腔室进行抽真空作业,料车底部设有至少三对轮毂,能够保证料车在各个分段轨道上平稳过渡,便于对保温杯连续作业,节约能源、提高生产效率;五是通过撞块撞击检测杆上平衡块,由检测杆另一端的感应片、感应开关控制料车的停止或运行,使料车在预定位置停车,定位准确,实现各个腔室的自动化作业;六是每间隔一段轨道,设置至少一组顶料机构,具体地说,顶料机构设于预抽室和焊接室底部,这样相邻两端轨道共用一个料车,有效减少料车和顶料机构的使用数量,大大节约成本,且焊接室中的顶料机构将料架从料车上顶出,料车退出焊接室后,料架被放置在轨道上进行焊接,料架稳定性更强,焊接精度更高;七是顶料机构对称设置在轨道两侧,同时将料架边沿顶起,料架顶起更平稳;八是料架设置定位
夹具,便于保温杯定点定位,定位夹具的拔插式连接,能够适用于不同型号的保温杯,扩大适用范围的同时,便于快速换模,大大提升加工效率;九是激光焊接装置的行进参数可以根据激光焊接装置上激光焊接枪的数量进行更改,当激光焊接枪设为一把时,行进参数可以设为归零后,依次逐个对保温杯进行焊接,当激光焊接枪设为两把或两把以上时,行进参数可以设为依次成排对保温杯进行焊接,当激光焊接枪数量设为与料架上保温杯数量相同时,行进参数可以设为一次同时对料架上所有保温杯进行焊接,可以根据生产线具体情况选择采用合适数量的激光焊接枪,对应更改焊接行进参数,适用范围广,利于推广;十是激光焊接装置、物料连续输送装置中的动力源、检测到位机构、传动机构等都安装在真空炉外面,避免了这些机构在高温环境下工作隔热难、寿命短的问题,且减少了炉体腔室的空间,简化了整体结构的同时节约能源,也更便于检修。
附图说明
23.图1是本发明保温杯抽真空装备的结构示意图;
24.图2是本发明保温杯抽真空装备的俯视结构示意图;
25.图3是本发明保温杯抽真空装备中单段腔室轨道的结构示意图;
26.图4是检测到位机构的结构示意图;
27.图5是待加工保温杯的结构示意图;
28.图6是料架的俯视结构示意图;
29.图7是本发明保温杯抽真空装备的电路图。
具体实施方式
30.为了使本发明的技术方案更加清晰,以下结合附图1-7,对本发明进行详细说明。应当理解的是,本说明书中描述的具体实施方式仅仅是为了解释本发明,并不是为了限定本发明的保护范围。
31.实施例1:一种保温杯抽真空装备,其设于装料平台100和卸料平台200之间,包括沿待加工件输送方向依次设置的四个真空腔室,分别为预抽室401、加热室402、焊接室403、冷却室404,以及设于腔室底部的物料连续输送装置,可控活动设于焊接室403上方的激光焊接装置9;所述各个真空腔室壳体采用304不锈钢或碳钢材质,隔热材料采用金属隔热屏,隔热屏至少包含三层金属材料如不锈钢、钼;所述相邻腔室之间均设有可控上下移动的插板阀,用于连通或隔离相邻的腔室,包括设于预抽室401入口处的入口阀71、设于预抽室401和加热室402之间的加热室阀71、设于加热室402和焊接室403之间的焊接室阀72、设于焊接室403和冷却室404之间的冷却室阀73、设于冷却室404出口处的出口阀74,插板阀及插板阀的上下移动均为现有技术,本实施例以链条、与链条配合的平衡齿轮和油缸构成插板阀的驱动机构7为例,但不限于该上下升降结构;所述预抽室401、加热室402、焊接室403均设有加热装置;所述加热室402和焊接室403均与高真空抽气系统连接,预抽室401和冷却室404均与低真空抽气系统连接;所述加热装置、高真空抽气系统、低真空抽气系统均为现有技术,低真空系统包括罗茨泵、滑阀泵,高真空系统包括旋片式真空泵、扩散泵;所述物料连续输送装置,用于连续运输待加工件至各个腔室进行抽真空作业;所述焊接室403顶面设有至少一块透明视窗10,且激光焊接装置9的激光束穿过透明视窗10,熔融设于杯底中心孔处的
焊接球11(参照附图5),焊接球11可以由铁、钛、不锈钢等与杯体相同的材料制成,激光焊接装置9及其控制机构为现有技术,激光焊接装置9包括激光焊接枪,控制激光焊接装置9活动的机构可以包括横向传动机构和纵向传动机构,且纵向传动机构设于横向传动机构上,实现激光焊接枪在横向、纵向上的自由移动;所述激光焊接枪的传动机构中电机可以是伺服电机,伺服电机由伺服系统的伺服驱动器和编码器控制,伺服系统、伺服驱动器、编码器、伺服电机均为现有技术,参照附图7所示,通过两个伺服电机m1、m2分别控制横向(即x轴)、纵向(即y轴)上的焊接;所述透明视窗10为耐高温玻璃;所述透明视窗10的可视范围覆盖所有保温杯。
32.参照附图2所示,本实施例的透明视窗10,采用多块组合的结构,透明视窗10的数量与焊接室内物料连续输送装置上的保温杯300数量相同且一一对应,透明视窗10均为边长尺寸30~60mm的方形或直径为30~60mm的圆形,确保焊接室保温性能的同时,又保证激光焊接枪的激光束穿过透明视窗顺利完成焊接;所述激光焊接装置的激光焊接枪按照需要可以设置一把对保温杯进行逐排逐个焊接,也可以设置两把以上对保温杯进行逐排焊接,也可以设置与保温杯同等数量的焊接枪一次完成焊接,提高焊接效率。
33.所述物料连续输送装置,包括控制器、分段设于各个腔室底部的轨道1、设于各个轨道1侧面的传动机构3、可控活动设于轨道1上的料车2、置于料车2上用于放置保温杯300的料架6、顶料机构4、检测到位机构5;所述控制器连接控制传动机构3、检测到位机构5、顶料机构4;所述料架6上设有放置保温杯300的定位夹具8;所述定位夹具8包括夹具体,以及在夹具体上呈矩形阵列排布设置的装夹体,保温杯300底部朝上倒扣在装夹体上;所述定位夹具8与料架6为拔插式连接,定位夹具8的设置,便于保温杯300定点定位,定位夹具8的拔插式连接,便于快速换模,适用于不同型号的保温杯,扩大适用范围的同时,大大提升加工效率;所述料车2底部均布设有至少三对轮毂21,轮毂21位于轨道1上且料车2通过传动机构3在轨道1上行驶或停止;所述预抽室401前方的装料平台100上、冷却室404后方的卸料平台200上,也均设有与所述物料连续输送装置的轨道相对应的轨道,传动机构3将装料平台100上装好保温杯的料车依次传输至预抽室401、加热室402、焊接室403、冷却室404,抽真空及焊接作业完成后,传输至卸料平台200;所述传动机构3控制料车2沿轨道1行驶,且传动机构3均包括与动力源连接的传动轴组件、设于传动轴组件尾端的传动齿轮34、设于料车2底部与传动齿轮34配合传动的齿条20;具体地说,传动轴组件包括两个与轨道1垂直的横向传动轴31,一个与横向传动轴31垂直并连接两个横向传动轴31的纵向传动轴32;所述纵向传动轴32的两端均设有伞齿轮组33,且纵向传动轴32通过伞齿轮组33配合传递动力到两个横向传动轴31;所述传动齿轮34设于横向传动轴31的尾端,且料车2底部的齿条20与传动齿轮34配合;所述动力源为电机30,且电机30通过传动皮带35传递动力至纵向传动轴32,电机30带动纵向传动轴32旋转,在伞齿轮组33的传动下两个横向传动轴31同时旋转,进而带动横向传动轴31上的传动齿轮34旋转,在传动齿轮34和齿条20作用下实现料车2在轨道1上行驶;所述电机30、纵向传动轴32、伞齿轮组33均设于真空炉外侧,横向传动轴31穿入真空炉内;所述电机30可以是伺服电机,伺服电机由伺服系统的伺服驱动器和编码器控制,伺服系统、伺服驱动器、编码器、伺服电机均为现有技术;参照附图7所示,所述真空炉内的四个腔室中传动机构的电机分别为m3、m4、m5、m6,分别控制料车2进入预抽室401预抽、进入加热室402高抽、进入焊接室403焊接、进入冷却室404冷却。
34.所述装料平台100、卸料平台200也分别设有料车2的传动机构,该传动机构可与上述真空炉各个腔室外的传动机构相同,也可以将装料平台100、卸料平台200的传动机构中电机分别连接变频器,参照附图7所示,由变频器控制电机。
35.所述顶料机构4,设于轨道1侧面,且每间隔一段轨道1,设置至少一组顶料机构4;每组顶料机构4中的两个顶料机构对称设置在轨道1两侧;所述料架6边沿伸出料车2边缘,顶料机构4通过顶起料架6边沿将料架6顶起;所述顶料机构4包括位于料架6边沿下方的顶杆,且顶杆与动力源连接,在动力源作用下,顶杆顶起料架边沿将料架从料车上顶起,动力源可以是油缸;具体地说,所述顶料机构4包括油缸41、传动齿条47、齿轮48、主传动轴45、次传动轴46、顶料座49、顶料齿条42、输入齿轮43、输出齿轮44、推板40;所述油缸41为顶料机构4的动力源,且油缸41与传动齿条47连接,带动传动齿条47的往复运动;所述齿轮48与传动齿条47配合,齿轮48固定在主传动轴45的一端,油缸41通过传动齿条47和齿轮48将动力传递给主传动轴45;所述顶料座49对称设于轨道1外两侧,所述输入齿轮43和输出齿轮44构成一对齿轮副,输入齿轮43和输出齿轮44相互配合连接,且均设于顶料座49内;所述顶料齿条42为两个,对称设于顶料座49内,且两个顶料齿条42分别与输入齿轮43、输出齿轮44配合,且控制顶料齿条42能够上下移动;所述推板40垂直设于顶料齿条42的顶部;所述主传动轴45依次穿过两个对称顶料座49内的输入齿轮43,次传动轴46依次穿过两个顶料座49内的输出齿轮44;所述料架6边沿伸出料车2边缘,推板40设于料架6边沿下方,在油缸41的驱动下,传动齿条47通过齿轮48带动主传动轴45旋转,在输入齿轮43和输出齿轮44作用下控制轨道1两侧顶料座49内的顶料齿条42同步上下移动,顶起或放下料架6。
36.所述检测到位机构5,参照附图4所示,设于真空炉外侧,其包括感应开关54、感应片53、磁铁55、检测杆50、平衡块51、撞块52;所述感应开关54安装在真空炉外侧的安装座56上,感应片53与感应开关54连接,感应片53和感应开关54均为现有技术,感应片53为导电的金属片;所述检测杆51穿插在真空炉腔室内外,且平衡块52设于检测杆50穿入腔室内的一端,感应片53设于检测杆50的另一端即穿出腔室的一端;所述撞块52设于料车2靠近检测杆50一端的侧面;所述磁铁55设于安装座56上,且磁铁55为感应片53提供回复力,使得感应片53恢复初始位置;所述撞块52与平衡块51接触过渡面为弧面,料车2行驶时,撞块52压向平衡块51,平衡块51带动检测杆50及感应片53绕检测杆50旋转一定角度,感应开关54检测到信号传输至控制器,控制料车停车,此时各个真空腔室开始指定的作业,各个真空腔室作业完成后,料车前进或后退,撞块52脱离平衡块51,感应片53在平衡块51的自重作用下复位,圆柱磁铁55同时将其吸牢,防止感应片53摆动,检测到位机构5完成料车2的定位停车功能,使料车2在预定位置停车,定位准确,实现各个腔室的自动化作业。
37.上述各个腔室还设有独立的室门,方便工程师进入室内解决在焊接过程中可能出现的问题,焊接室403设置单独的室门也便于调试激光焊接枪和保温杯的对位,提高加工精度。
38.一种采用上述保温杯抽真空装备的抽真空方法,包括如下步骤:
39.s1:料车2的料架6上装载好待加工的保温杯300,开启入口阀70,料车2经轨道从装料平台100进入预抽室401,到达指定位置时定位停车,顶料机构4将料架6顶起脱离料车2,料车2回程退出预抽室401,顶料机构4带动料架6下降复位并关闭入口阀70,系统检测入口阀70关闭后开始低抽作业,当检测到真空度达到4
×
102pa时,加快抽真空速度,同时开始预
热,温度达到200度后关闭加热,当检测到真空度达到4
×
10-1
pa时预抽完成;
40.s2:预抽完成后,打开加热室阀71,预抽室401的顶料机构4将料架6顶起,同时加热室402的料车经轨道进入预抽室401定位停车,顶料机构4下降将料架6放置在料车上,料架6随料车经轨道进入加热室402并关闭加热室阀71,此时预抽室401重复步骤s1;系统检测关闭加热室阀71后,开始高抽作业同时开始加热炉内温度到450度,当检测到真空度达到1
×
10-3
pa时,在温度450度的条件下保温20分钟,激活吸气剂;
41.s3:焊接室403与加热室402同步开始高抽作业,将焊接室403的真空度达到1
×
10-3
pa,温度达到450度,且一直保持;在s2步骤激活吸气剂后,打开焊接室阀72,料车带料架经轨道进入焊接室403定位停车后,顶料机构4将料架6顶起脱离料车2,料车2退回到加热室402,顶料机构4带动料架6下降复位并关闭焊接室阀72,此时加热室402重复步骤s2;系统检测关闭焊接室阀72后,焊接枪归零,从零点位置开始按照预设行进参数依次进行焊接(预设行进参数与料架保温杯摆放间隔对应),焊接枪使焊接球与保温杯抽真空孔熔融为一体完成焊接;
42.s4:焊接完成后,打开冷却室阀73,焊接室403顶料机构将料架6顶起,同时冷却室404的料车2经轨道进入焊接室403定位停车,顶料机构4下降将料架6放置在料车2上,料车带料架经轨道进入冷却室404并关闭冷却室阀73,此时焊接室403重复步骤s3;系统检测关闭冷却室阀73后,监测冷却室404室温和室内压力,当室温降到230度时,打开充气阀,向冷却室404填充空气或氮气,当室内压力与外部压力相同时,冷却完成;
43.s5:冷却完成后,打开出口阀74,料车带料架经轨道进入卸料平台200定位停车,卸料后料车2退回到冷却室404并关闭出口阀74,此时冷却室404重复步骤s4,如此连续作业。
44.实施例2:上述实施例1中的焊接室上方,还可以安装可控活动设置的视觉扫描相机,视觉扫描相机和控制其活动的机构为现有技术,视觉扫描相机的活动机构可以包括横向传动机构和纵向传动机构,且纵向传动机构设于横向传动机构上,实现横向、纵向上的自由移动。
45.在实施例1所述抽真空方法的步骤s3中,当系统检测关闭焊接室阀后,焊接前,视觉扫描相机透过透明视窗扫描需要焊接的位置,根据扫描结果,激光焊接枪透过透明视窗进行焊接作业;激光焊接枪根据视觉扫描相机的扫描结果进行定点焊接,焊接精度更高,更有效提高焊接加工质量。