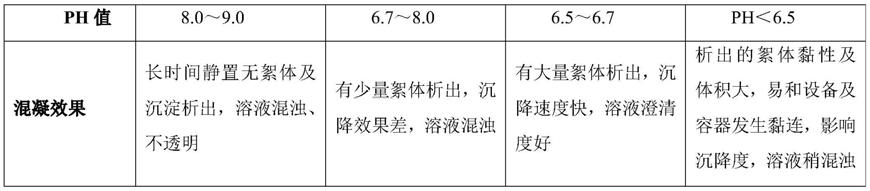
1.本发明属于汽车涂装技术领域,具体涉及一种水性涂料清洗废液的处理及综合利用的方法。
背景技术:
2.传统溶剂型喷漆涂料以有机溶剂(苯、酮、酯等)作为分散介质,使用期间会产生大量的污染物,而其中的高有机物释放量(voc)更是对人体健康有害。水性喷漆涂料是以水作为分散介质,当前汽车涂装的核心课题就是环境保护,而其中最重要的就是要从源头进行改变。因此,要使用具有环保性的涂料,广泛应用能够减少voc的环保型漆料。在工业发达国家,该类涂装生产线已经全面普及,而近几年在我国的汽车制造领域,也已经开始全面使用水性漆涂料。
3.此外,在汽车喷涂工艺中,为保证漆面的颜色纯度等符合质量要求,会涉及清洗环节,持续使用清洗剂对喷涂机器人内部的管路、阀门、喷嘴等装置进行冲洗,由此产生了大量水性涂料清洗废液。这也带来了另外一个非常严重的环境问题,就是水性涂料清洗废液的处置问题。由于其含有有机成分,cod(化学需氧量)含量较高,属于危险废弃物,因此急需针对该污染物进行研究,制定相应工艺进行废水处理,使其满足排放标准,减少对环境的污染。
4.水性涂料清洗废液内部成分复杂,可粗略分为三大类,其中包括约70%的水,约15%的杂质,如树脂、颜料及云母等以及约15%左右的水性涂料清洗溶剂,如乙二醇丁醚、二乙二醇丁醚及2-丁氧基乙醇等。分散相具有较小的粒度,在水中多以胶体或者乳浊液的形式存在,具有较强的亲水性,稳定性较强,整体cod含量高达400000~600000mg/l,这给其后续的废水回收造成了极大的困难,单纯依靠水处理系统的物化与生化反应无法实现达标处理及排放。经过大量研究与实验后,行业内提出了多种处理方案:如盐析法、膜组合及其改良法。
5.其中,盐析法对水性涂料清洗废液的处理,主要是直接加入盐析剂(钙盐),使溶剂中的固体漆料部分发生混凝,之后通过过滤的方法,将漆渣与清液分离,漆渣委托处置,清液排入水处理系统。但是,盐析过程需要根据每次处理的废液量加入大量的盐析剂,这些盐析剂均为一次性使用,处置成本相对较高。此外,盐析过程仅能够完成初步的固液分离,清液中依然混有大量有机污染物,分离不彻底,回收的废水cod含量较高。膜组合及其改良法对水性涂料清洗废液的处理中,超滤过程对于膜的要求较高,由于溶剂中含有粘性漆渣类物质,易粘附在超滤膜上难以清洗,随着超滤量增加,膜的渗透效果降低,需要经常更换,成本较高。因此,急需研发一种可对水性涂料清洗废液进行彻底分离并综合利用的方法。
技术实现要素:
6.本发明提供一种低成本、高质量的水性涂料清洗废液的处理及综合利用的方法,解决了对水性涂料清洗废液含有的三大类物质进行彻底分离并进行综合利用的问题,据各
自的性质分别进行处置及综合利用,使处理后回收的废水cod能够进一步降低,同时降低处置的成本,减少对环境的污染。
7.本发明的目的是通过以下技术方案实现的:
8.一种水性涂料清洗废液的处理及综合利用的方法,包括以下步骤:
9.a、向水性涂料清洗废液中加入混凝剂,其内悬浮颗粒杂质聚集成絮体后加入助凝剂,絮体形成固体沉淀,与水性涂料清洗废液中的液相分离,固体经过分离、预沉淀及压滤处理处理后,得到漆渣,清液单独收集;
10.b、向收集的清液中加入适量的盐析剂,在盐析作用下,对其中的有机溶剂成分进行萃取,再经过精制提纯处理,可得到有效成分高于85%的再生溶剂,水层单独收集;
11.c、将步骤b收集的水层经过浓缩结晶处理后,得到浓缩药剂,返回盐析分相器中继续作为盐析剂循环使用,并回收cod含量在10000mg/l以内废水,将其排入厂区综合污水生化处理系统,经水解、兼氧、好氧等生化处理后,回收得到cod含量低于500mg/l,能够直接向城市管网中达标排放的工业废水。
12.进一步地,步骤a,所述混凝剂为聚合氯化铝、聚合硫酸铁、硫酸亚铁、三氯化铁或硫酸铝。
13.更进一步地,所述混凝剂的加入量是原液质量的0.1~0.8%。
14.进一步地,步骤a,所述助凝剂为聚氧化乙烯或聚丙烯酰胺。
15.更进一步地,所述助凝剂的加入量为原液质量的0.0001~0.0008%。
16.进一步地,所述漆渣的热值在15000-25000kj/kg,可用于生产替代性燃料使用。
17.进一步地,步骤b,所述盐析剂为硫酸铵、硫酸钠、氯化镁、硫酸铝、硝酸铵、氯化铵、氯化钠、硫酸镁、氯化钙等。
18.更进一步地,所述加入盐析剂的量为原液质量的40~75%。
19.与现有技术相比,本发明的有益效果在于:
20.本发明水性涂料清洗废液的处理及综合利用的方法,可实现水性涂料清洗废液的处置及综合利用;废水回收效率高,且cod含量较低,能够加快污水处理系统中的处理速度,节省处理成本;此外,通过蒸馏过程可将分离过程中添加的药剂在液体中进行浓缩后回收,循环使用,使药物方面的成本大大降低。
附图说明
21.为了更清楚地说明本发明实施例的技术方案,下面将对实施例中所需要使用的附图作简单地介绍,应当理解,以下附图仅示出了本发明的某些实施例,因此不应被看作是对范围的限定,对于本领域普通技术人员来讲,在不付出创造性劳动的前提下,还可以根据这些附图获得其他相关的附图。
22.图1本发明水性涂料清洗废液的处理及综合利用的方法的流程图。
具体实施方式
23.下面结合实施例对本发明作进一步说明:
24.下面结合附图和实施例对本发明作进一步的详细说明。可以理解的是,此处所描述的具体实施例仅仅用于解释本发明,而非对本发明的限定。另外还需要说明的是,为了便
于描述,附图中仅示出了与本发明相关的部分而非全部结构。
25.应注意到:相似的标号和字母在下面的附图中表示类似项,因此,一旦某一项在一个附图中被定义,则在随后的附图中不需要对其进行进一步定义和解释。同时,在本发明的描述中,术语“第一”、“第二”等仅用于区分描述,而不能理解为指示或暗示相对重要性。
26.如图1所示,本发明水性涂料清洗废液的处理及综合利用的方法,包括以下步骤:
27.首先,加入混凝剂使水性涂料清洗废液中的悬浮颗粒杂质聚集抱团,形成絮体,再加入助凝剂,使絮体变得更加粗大密实,进一步提高混凝效果,形成大块絮体沉淀,使其中的固相与液相彻底分离,固体部分经过分离、预沉淀及压滤处理后,得到热值在15000-25000kj/kg的漆渣,可用于生产替代性燃料使用,清液单独收集。
28.其次,向清液中加入适量的盐析剂,在盐析作用下,对其中的有机溶剂成分进行萃取,与水分层,其中密度小的在上,密度大的在下,分层后的有机溶剂混有少量的水,经过精制提纯处理后,可得到有效成分高于85%的再生溶剂,水层单独收集。
29.最后,清液经过浓缩结晶处理后,得到浓缩药剂,可返回盐析分相器中继续做为盐析剂循环使用。同时,可回收cod含量在10000mg/l以内废水,将其排入厂区综合污水生化处理系统,经过水解、兼氧、好氧等生化处理后,最终可回收得到cod含量低于500mg/l的工业废水,可直接向城市管网中达标排放。
30.药剂的选择:
31.本发明在药物使用方面,混凝剂为干式投加,且混凝效果优异。助凝剂加入量少,助凝效果显著。
32.混凝剂的选择:常用的混凝剂有聚合氯化铝、聚合硫酸铁、硫酸亚铁、三氯化铁、硫酸铝等。其中聚合氯化铝和聚合硫酸铁在使用时需要提前溶解,然后静置熟化一段时间才能使用,不但操作起来麻烦,而且溶解过程中还会引入额外的废水,增加了后续废水处理的水量。硫酸亚铁和三氯化铁投加后溶液的澄清度比较差,絮体比较碎。所述混凝剂的加入量是原液质量的0.1~0.8%。
33.经过对比,优选硫酸铝作为混凝剂,其优点是,无需提前溶解,可直接干式投加,且投加后絮体明显、沉降速度快、上清液澄清度好。
34.在硫酸铝的投加量方面,经检测,水性涂料清洗废液的ph=8~9,属于中性偏碱,在此ph值范围内,废液呈悬浊状态,具有良好的乳化性和分散性,不宜产生沉淀。经过验证,在投加硫酸铝后,废液的ph值由中性偏碱向中性偏酸方向转化,此时漆渣逐渐聚集成块析出。以下是投加硫酸铝后ph值的变化对废液混凝效果的影响,见表1。
35.表1
[0036][0037]
根据上述实验结果,得到投加后溶液ph在6.5~6.7之间为最佳,最优选的投加量是原液质量的0.3%~0.5%。
[0038]
助凝剂的选择:常用的助凝剂有聚氧化乙烯、聚丙烯酰胺(阴离子型、阳离子型、非
离子型)等等。所述助凝剂的加入量为原液质量的0.0001~0.0008%。
[0039]
经过试验,我们优选聚氧化乙烯,聚氧化乙烯投加量少,絮体粗大密实、沉降快,上清液澄清度好。聚氧化乙烯在使用之前需将其与水按1:1000的质量比预溶,聚氧化乙烯的最佳投加量为原液质量的0.0003%~0.0005%。
[0040]
盐析剂的选择:常用的盐析剂有硫酸铵、硫酸钠、氯化镁、硫酸铝、硝酸铵、氯化铵、氯化钠、硫酸镁、氯化钙等。其中钙盐、镁盐易结垢,氯离子在高温条件下腐蚀性大,硝酸铵使用安全性差,硫酸钠本身的溶解度低,而硫酸铝易形成胶体,使溶液变浑浊。所述加入盐析剂的量为原液质量的40~75%。
[0041]
经过对比试验,优选硫酸铵作为盐析剂,其主要优点是使用安全,溶解度高(20℃时溶解度是75.4g),不易形成胶体,属于多电荷离子盐等。经验证,使用硫酸铵作为盐析剂,能够使废水中有机溶剂的析出效率达到95%以上。
[0042]
实施例
[0043]
a、混凝反应分离漆渣,并生产替代性燃料。
[0044]
a1、将桶装水性涂料清洗废液集中至废液储罐中,待统一处理。通过离心泵将储罐中废液输送到反应槽中,按溶液质量0.3%~0.5%的比例加入硫酸铝,保持混合后溶液ph为6.5~6.7,再根据清液质量,按照0.0003%~0.0005%,加入聚氧化乙烯进行混凝处理。此步反应中,硫酸铝作为混凝剂,可使废液中的小颗粒悬浮物抱团形成絮体沉淀,聚氧化乙烯作为助凝剂使絮体颗粒变大,加快沉降速度,使废液中的固液分离更加彻底。
[0045]
a2、混凝反应后,通过离心泵将溶液输送至沉淀槽进行絮体沉淀,沉淀后将下层絮体沉淀通过离心泵排入污泥浓缩罐进行二次沉淀,可得到含水量为90%左右的漆渣。此步固液分离是通过重力沉降完成并分离的,故漆渣中含水量较大。
[0046]
a3、二次沉淀后的漆渣送入压滤机,进行压滤除水处理。压滤除水后,可得到含水量为60~65%,热值为15000~25000kj/kg的漆渣,集中收集后加入其他高热值废弃物,经过调质搅拌等处理后,可生产出含水量小于40%,热值大于15000kj/kg的替代性燃料,用于水泥窑协同处理,以替代一部分燃料煤。
[0047]
上述a2、a3过程中的清液部分均输送到滤清液中间罐中,待返回废液储罐进行循环处理。
[0048]
b、盐析反应去除废溶剂,制得再生溶剂。
[0049]
b1、将上述步骤a2中沉淀槽中清液部分输送至上清液中间罐。通过离心泵,将清液导入盐析分相器中,根据清液质量加入一定量的硫酸铵进行盐析处理,盐析反应后,有机溶剂与水分层,其中密度小的有机溶剂层在上,密度大的水层在下,分层后的有机溶剂中会混有少量的水。
[0050]
b2、盐析处理后的上层废溶剂层输送至油相中间罐暂存。通过进料泵,将油相中间罐中的溶剂输送至蒸馏釜中,通过蒸汽管道对釜内溶剂加热,温度90-100℃,压强0.003-0.005mpa条件下进行减压蒸馏处理,经过冷凝冷却后,得到无色透明澄清液体,无杂质,不分层,内部有效成分含量超过85%的再生溶剂。
[0051]
b3、蒸馏过程剩余罐内残液排入残液中间罐,待返回废液储罐进行循环处理。
[0052]
c、蒸发浓缩制得浓缩药剂,并进行废水的生化处理。
[0053]
c1、步骤b1中下层清液水相输送至水相中间罐,通过离心泵输送至蒸发浓缩器中,
利用蒸汽管道加热,使釜内压强保持0.04-0.08mpa,温度80-90℃条件下进行蒸发浓缩。将溶液浓缩至原体积的45%后,得到的浓缩药剂通过离心泵输送回盐析分相器中,可继续用于盐析处理,能够加快循环处理过程中水分的蒸发速率。此步骤将盐析剂全部回收,长时间循环回收过程中可能产生损耗,可补充少量盐析剂后继续使用。
[0054]
c2、浓缩处理过程中,蒸汽经冷凝冷却后,凝结成的液体即为cod含量低于10000mg/l的废水,将其暂存到废水收集槽中,之后进入厂区污水处理系统,经过水解酸化、好氧生化等处理后,可将cod降低到500mg/l以下,最终可达标排放到城市污水管网中。
[0055]
步骤c中,盐析剂经过浓缩结晶处理后可以返回盐析分相器中,在多次实验基础上得出,在浓缩至溶剂原体积45%的时候,如继续浓缩处理,整体耗能大且水分蒸发速率极低,而此时浓缩后的盐析剂依然保有流动性,未结晶结垢,适合直接回用,可大大节省药剂方面的投入成本,同时提高了废水回收速度及效率。
[0056]
本方法对水性涂料清洗废液中包含的三组分物质分别进行回收,并进行了最大化利用。其中经本处理方法处理后,可得到内部有效成分在85%以上的再生溶剂,可直接作为产品销售。产品技术指标如表2。
[0057]
表2
[0058]
项目名称外观颜色有效成分含量,wt%ph技术指标透明的澄清液体,无杂质,不分层无色>85%6~9
[0059]
混凝剂种类,加入量和ph值不同时,对絮体效果和清液效果的影响见表3。助凝剂种类,加入量和ph值不同时,对絮体变化情况和清液效果的影响见表4。盐析剂种类,加入量的不同对废水中有机溶剂的析出效率的影响见表5。
[0060]
表3
[0061]
[0062][0063]
表4
[0064]
[0065][0066]
表5
[0067]
实施例盐析剂种类加入量(%)废水中有机溶剂的析出效率实施例1硫酸铵75≧95%实施例2硫酸钠19≧24%实施例3氯化镁45≧57%,有少许胶状物产生实施例4硫酸铝36≧45%实施例5碳酸钠21≧26%实施例6氯化铵37≧47%实施例7氯化钠35≧44%实施例8氯化钙74≧79%,有少许胶状物产生实施例9硫酸钠19≧24%实施例10硫酸铵40≧50%实施例11硫酸铵50≧63%实施例12硫酸铵60≧76%
[0068]
注意,上述仅为本发明的较佳实施例及所运用技术原理。本领域技术人员会理解,本发明不限于这里所述的特定实施例,对本领域技术人员来说能够进行各种明显的变化、重新调整和替代而不会脱离本发明的保护范围。因此,虽然通过以上实施例对本发明进行了较为详细的说明,但是本发明不仅仅限于以上实施例,在不脱离本发明构思的情况下,还可以包括更多其他等效实施例,而本发明的范围由所附的权利要求范围决定。