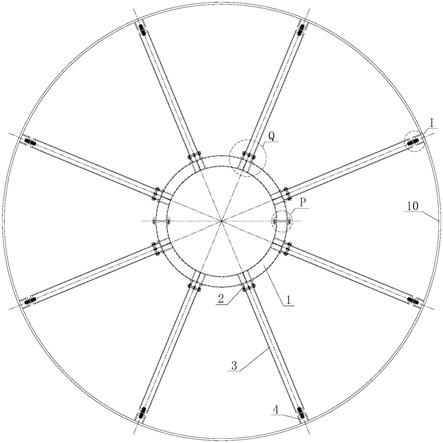
1.本实用新型涉及一种用于吸力桩制作时的内支撑架。
背景技术:
2.吸力桩导管架基础具有无桩体打桩施工、安装快速简便、节省施工时间、拆除方便等一系列优优势正越来越多地被用于海上风电基础。吸力桩是吸力桩导管架基础中的重要部件。通常吸力桩为20多米的圆筒体,其最大外径为12m,壁厚为30~55mm。吸力桩由若干段筒节拼接而成,每段筒节由矩形钢板卷制而成。由于吸力桩的直径大、壁厚薄,导致吸力桩卧倒放置时刚性差,很容易变形。因此每段筒节在卷制后利用检查样板检验并矫正每段筒节的圆度后,就要在每段筒节的内腔中设置支撑架,以增加筒节的刚性,防止筒节在组对滚轮架上组焊拼接和翻身时变形,控制筒节的尺寸满足规范要求,直到吸力桩整体制作完成并通过履带吊翻身呈直立状后坐落在运输工装的顶面上,吸力桩通过运输工装顶面上的八对导向板定位在运输工装的顶面上(见图1a和图1b),再卸掉内支撑架。传统的“*”形内支撑架无法从吸力桩底部的运输工装的内孔(直径为8m)中整体穿出,需要把“*”形内支撑架切割成多个杆件,这样既浪费钢材且切割拆卸耗时长。
技术实现要素:
3.本实用新型的目的在于克服现有技术的缺陷而提供一种用于吸力桩制作时的内支撑架,它既解决了大直径、壁厚薄的吸力桩在制作过程中易变形的问题,又便于拆卸与重复利用。
4.本实用新型的目的是这样实现的:一种用于吸力桩制作时的内支撑架,包括圈梁、八个支撑杆连接头、八根支撑杆和八个支撑杆调节头;其中,
5.所述圈梁由两个半圆形圆弧梁对接而成;
6.八个支撑杆连接头均布地径向固定在所述圈梁的外表面上,每个支撑杆连接头的外端均固定内侧法兰板;
7.八根支撑杆的内端各自固定外侧法兰板并各自通过若干螺栓一一对应地与八个支撑杆连接头的内侧法兰板连接,每根支撑杆的外端均固定一块封板,封板的中心开设一个螺纹孔;
8.每个支撑杆调节头均包括一根调节螺杆和一个支撑杆端头;所述调节螺杆包括六角形螺头和同轴地连接在螺头的两侧面中心的正牙螺杆和反牙螺杆;所述支撑杆端头包括一块底板和两块一一对应地垂直连接在底板的两侧的端板,且底板的中心开设一个螺纹孔,该螺纹孔与调节螺杆的一头螺杆旋接;八个支撑杆调节头上的调节螺杆的另一头螺杆一一对应地旋入八根支撑杆的封板上的螺纹孔中。
9.上述的用于吸力桩制作时的内支撑架,其中,所述圈梁为方管形圈梁并包括内圈板、外圈板和两块一一对应地连接在内圈板和外圈板的顶面之间和底面之间的环形面板;所述圈梁的内圈板和外圈板之间在对应八个支撑杆连接头的位置均设置三块加劲板。
10.上述的用于吸力桩制作时的内支撑架,其中,两个圆弧梁的对接端各自固定对接板,对接板与圆弧梁之间设置若干第一筋板。
11.上述的用于吸力桩制作时的内支撑架,其中,每个所述支撑杆连接头的外表面与圈梁的外表面之间以及与支撑杆连接头的外表面法兰板之间均各自均布地连接若干第二筋板。
12.上述的用于吸力桩制作时的内支撑架,其中,所述内支撑架还包括八根支撑杆配节段;每根支撑杆配节段的两端均固定法兰板并各自通过螺栓一一对应地连接在八根支撑杆的外侧法兰板上和八个支撑杆连接头的内侧法兰板上。
13.本实用新型的用于吸力桩制作时的内支撑架具有以下特点:设计合理,结构巧妙,便于拆卸与重复利用,且适用于多种内径的吸力桩的内支撑,很好地解决了大直径、壁厚薄的吸力桩在制作过程中易变形的问题,且大大提高了吸力桩的制作效率,并能节约吸力桩在制作时的辅材成本。
附图说明
14.图1a是吸力桩导管架的运输工装的透视图;
15.图1b是吸力桩安装在运输工装上的立面图;
16.图2是本实用新型的用于吸力桩制作时的内支撑架的平面图;
17.图3是图2中的p部位的放大图;
18.图3a是图3中的a-a向视图;
19.图4是图2中的q部位的放大图;
20.图4a是图4中的b-b向视图;
21.图4b是图4中的c-c向视图;
22.图5是图2中的i部位的放大图;
23.图5a是图5中的d-d向视图;
24.图5b是图5中的e-e向视图;
25.图6是本实用新型的内支撑架的支撑杆配节段的结构示意图。
具体实施方式
26.下面将结合附图对本实用新型作进一步说明。
27.请参阅图2至图6,本实用新型的用于吸力桩制作时的内支撑架,包括圈梁1、八个支撑杆连接头2、八根支撑杆3、八个支撑杆调节头4。
28.圈梁1为方管形圈梁并包括内圈板、外圈板和两块一一对应地连接在内圈板和外圈板的顶面之间和底面之间的环形面板;圈梁1由两个半圆形圆弧梁对接而成,两个圆弧梁的对接端各自焊接固定对接板11,对接板11与圆弧梁的外表面之间设置八块第一筋板12;
29.八个支撑杆连接头2均布地径向焊接在圈梁1的外表面上,每个支撑杆连接头2为一段长度为120mm、外径为203mm、壁厚为12mm的圆管,圆管的外端面上固定内侧法兰板21,每个支撑杆连接头2的外表面与圈梁1的外表面之间均布地连接六块第二筋板22;每个支撑杆连接头2的外表面与内侧法兰板21之间也均布地连接六块第二筋板22;圈梁1的内圈板和外圈板之间在对应八个支撑杆连接头2的位置均设置三块加劲板13,进行局部加强;
30.支撑杆3采用外径为203mm、壁厚为12mm的圆管;八根支撑杆3的内端各自固定外侧法兰板31并各自通过若干螺栓一一对应地与八个支撑杆连接头2上的内侧法兰板21连接;八根支撑杆3的外端各自固定一块封板32,封板32的中心开设一个螺纹孔;
31.每个支撑杆调节头4均包括一根调节螺杆41和一个支撑杆端头42;调节螺杆41包括六角形螺头和各自连接在螺头两端的正牙螺杆411和反牙螺杆412;支撑杆端头42包括一块底板421和两块一一对应地垂直连接在底板421的两侧的端板422而呈u形结构,且底板421的中心开设一个螺纹孔,该螺纹孔与调节螺杆41的反牙螺杆412旋接;八个支撑杆调节头4上的调节螺杆41的正压螺杆411一一对应地旋入八根支撑杆3的封板32上的螺纹孔中。
32.本实用新型的用于吸力桩制作时的内支撑架,还根据吸力桩10的内径大小选配八根支撑杆配节段5,以适用于不同内径的吸力桩10;每根支撑杆配节段5包括一段外径为203mm、壁厚为12mm的圆管和两块固定在圆管两端的法兰板50(见图6),圆管的长度根据吸力桩10的内径裁切;八根支撑杆配节段5的两端各自通过螺栓一一对应地连接在八根支撑杆3的外侧法兰板31上和八个支撑杆连接头2的内侧法兰板21上。
33.本实用新型的用于吸力桩制作时的内支撑架,在使用时,先把圈梁1的两个半圆形圆弧梁通过螺栓连接好,接着把八根支撑杆3(根据实际吸力桩筒径大小选配支撑杆配节段5)一一对应地与八个支撑杆调节头4连接好,再把八根支撑杆3用螺栓一一对应地与圈梁1外表面上的八个支撑杆连接头2连接好,把整个支撑架吊至吸力桩10内制作工艺辅助支撑的位置,各自调节八个支撑杆调节头4的调节螺杆41,使八个支撑杆调节头4的支撑杆端头42的两块端板422顶到吸力桩10的内壁上并与之焊接固定,完成对吸力桩10的支撑。
34.本实用新型的用于吸力桩制作时的内支撑架,在拆卸时,先整体用葫芦吊住,接着将八个支撑杆端头42的两块端板422从吸力桩10的内壁上割除(注意不得伤到吸力桩的内壁),再调节调节螺杆41使八个支撑杆调节头4与吸力桩10的内壁脱离,使整个内支撑架便于脱落,然后下放整个内支撑架至吸力桩导管架的运输工装上,将八根支撑杆3从八个支撑杆连接头2上拆卸下来,并将圈梁1的两个圆弧梁拆开,最后把八根支撑杆3和两个圆弧梁从吸力桩导管架的运输工装的内孔中运出。
35.以上实施例仅供说明本实用新型之用,而非对本实用新型的限制,有关技术领域的技术人员,在不脱离本实用新型的精神和范围的情况下,还可以作出各种变换或变型,因此所有等同的技术方案也应该属于本实用新型的范畴,应由各权利要求所限定。