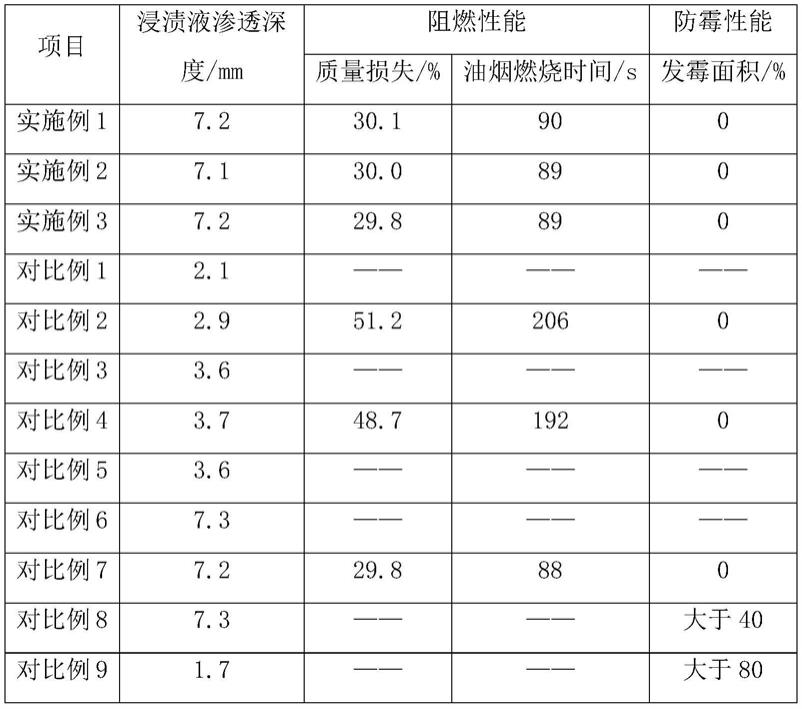
1.本发明涉及木材阻燃处理技术领域,特别是阻燃防腐竹木建材制备方法。
背景技术:
2.一直以来,由于实木、竹等材料的渗透性较差,人们采用加压浸注等方式将阻燃剂浸注到木材中,但是阻燃剂的渗透性依然不够理想,且高压条件一方面对生产条件的要求苛刻使得配套设备等的生产难度增加,另一方面也会提高生产成本,所以如何提高竹木渗透性对提高竹木建材阻燃、防腐性能极其重要。
技术实现要素:
3.本发明的目的在于克服现有技术实木、竹等材料的渗透性较差,加压浸注阻燃剂能耗高的缺点,提供阻燃防腐竹木建材制备方法。
4.本发明的目的通过以下技术方案来实现:
5.阻燃防腐竹木建材制备方法,包括对竹木依次进行的加热、第一碱处理、酸处理、第二碱处理、浸渍和干燥,其中,
6.所述第一碱处理处理剂为dbu;
7.所述酸处理处理剂为双氧水;
8.所述第二碱处理处理剂为氨水;
9.所述浸渍为浸渍防腐液和/或阻燃液。
10.作为优选的,所述第一碱处理前先将竹木加热至温度为50
‑
70℃,加热时间10
‑
30min。
11.作为优选的,所述第一碱处理中将竹木浸泡在dbu溶液中,所述dbu溶液中dbu的浓度为0.5
‑
1wt%,浸泡时间为2
‑
4h。
12.作为优选的,所述酸处理中将竹木浸泡在双氧水中,所述双氧水的浓度为3
‑
5wt%,浸泡时间为0.5
‑
1h。
13.作为优选的,所述第二碱处理中将竹木浸泡在氨水中,所述氨水的浓度为15
‑
20wt%,浸泡时间为0.5
‑
1h。
14.作为优选的,所述阻燃液中包括月桂醇硫酸钠3重量份、二氰二胺20~40重量份、磷酸二铵15~30重量份、硼酸10~30重量份、钼酸铵1~5重量份,磷酸化的蓖麻油4~6重量份。
15.作为优选的,防腐液中包括3~4重量份n
‑2‑
苯并咪唑基氨基甲酸甲酯5
‑
8重量份、聚乙二醇3
‑
4重量份、亚麻籽油2
‑
3重量份和乙醇90
‑
100重量份。
16.作为优选的,所述浸渍步骤是将竹木浸泡在防腐液和/或阻燃液中,所述浸渍在高压条件下进行,所述高压为0.2
‑
0.5mpa。
17.作为优选的,所述浸渍步骤的浸渍时间为10
‑
30min。
18.作为优选的,所述浸渍前对竹木进行干燥至含水率小于3%。
19.本发明中通过对竹木依次进行加热、第一碱处理、酸处理和第二碱处理,对渗透通道进行扩展和疏通,提高阻燃剂、防霉剂的渗透效果,从而提高阻燃和防水效果。
具体实施方式
20.为使本发明实施方式的目的、技术方案和优点更加清楚,下面将对本发明实施方式中的技术方案进行清楚、完整地描述,显然,所描述的实施方式是本发明一部分实施方式,而不是全部的实施方式。
21.因此,以下对本发明的实施方式的详细描述并非旨在限制要求保护的本发明的范围,而是仅仅表示本发明的选定实施方式。基于本发明中的实施方式,本领域普通技术人员在没有作出创造性劳动前提下所获得的所有其他实施方式,都属于本发明保护的范围。
22.需要说明的是,在不冲突的情况下,本发明中的实施方式及实施方式中的特征可以相互组合。
23.实施例1:
24.本实施例提供了一种阻燃防腐竹木建材制备方法,包括对竹木依次进行的加热、第一碱处理、酸处理、第二碱处理、浸渍和干燥,其中,
25.所述第一碱处理前先将竹木加热至温度为50℃,加热时间30min;
26.所述第一碱处理中将竹木浸泡在dbu溶液中,所述dbu溶液中dbu的浓度为0.5wt%,浸泡时间为4h;
27.所述酸处理中将竹木浸泡在双氧水中,所述双氧水的浓度为3wt%,浸泡时间为1h;
28.所述第二碱处理中将竹木浸泡在氨水中,所述氨水的浓度为15wt%,浸泡时间为1h;
29.所述浸渍为浸渍防腐液和阻燃液,所述浸渍在高压条件下进行,所述高压为1.2mpa,浸渍时间为30min,所述阻燃液中包括月桂醇硫酸钠3重量份、二氰二胺20重量份、磷酸二铵 30重量份、硼酸10重量份、钼酸铵5重量份,磷酸化的蓖麻油4重量份;防腐液中包括4 重量份、n
‑2‑
苯并咪唑基氨基甲酸甲酯5重量份、聚乙二醇3重量份、亚麻籽油3重量份和乙醇90重量份。
30.实施例2:
31.本实施例提供了一种阻燃防腐竹木建材制备方法,包括对竹木依次进行的加热、第一碱处理、酸处理、第二碱处理、浸渍和干燥,其中,
32.所述第一碱处理前先将竹木加热至温度为70℃,加热时间10min;
33.所述第一碱处理中将竹木浸泡在dbu溶液中,所述dbu溶液中dbu的浓度为1wt%,浸泡时间为2h;
34.所述酸处理中将竹木浸泡在双氧水中,所述双氧水的浓度为5wt%,浸泡时间为0.5h;
35.所述第二碱处理中将竹木浸泡在氨水中,所述氨水的浓度为20wt%,浸泡时间为0.5h;
36.所述浸渍为浸渍防腐液和阻燃液,所述浸渍前对竹木进行干燥至含水率小于3%,所述浸渍在高压条件下进行,所述高压为0.8mpa,浸渍时间为10min,所述阻燃液中包括月
桂醇硫酸钠3重量份、二氰二胺40重量份、磷酸二铵15重量份、硼酸30重量份、钼酸铵1重量份,磷酸化的蓖麻油6重量份;防腐液中包括3重量份、n
‑2‑
苯并咪唑基氨基甲酸甲酯8重量份、聚乙二醇4重量份、亚麻籽油2重量份和乙醇100重量份。
37.实施例3:
38.本实施例提供了一种阻燃防腐竹木建材制备方法,包括对竹木依次进行的加热、第一碱处理、酸处理、第二碱处理、浸渍和干燥,其中,
39.所述第一碱处理前先将竹木加热至温度为60℃,加热时间20min;
40.所述第一碱处理中将竹木浸泡在dbu溶液中,所述dbu溶液中dbu的浓度为0.8wt%,浸泡时间为3h;
41.所述酸处理中将竹木浸泡在双氧水中,所述双氧水的浓度为4wt%,浸泡时间为0.8h;
42.所述第二碱处理中将竹木浸泡在氨水中,所述氨水的浓度为18wt%,浸泡时间为0.8h;
43.所述浸渍为浸渍防腐液和阻燃液,所述浸渍前对竹木进行干燥至含水率小于3%,所述浸渍在高压条件下进行,所述高压为1mpa,浸渍时间为20min,所述阻燃液中包括月桂醇硫酸钠3重量份、二氰二胺30重量份、磷酸二铵20重量份、硼酸20重量份、钼酸铵3重量份,磷酸化的蓖麻油5重量份;防腐液中包括3.5重量份、n
‑2‑
苯并咪唑基氨基甲酸甲酯7重量份、聚乙二醇3
‑
4重量份、亚麻籽油2
‑
3重量份和乙醇90
‑
100重量份。
44.对比例1:
45.与实施例3的区别在于,第一碱处理前未进行加热。
46.对比例2:
47.与实施例3的区别在于,未进行第一碱处理。
48.对比例3:
49.与实施例3的区别在于,未进行酸处理。
50.对比例4:
51.与实施例3的区别在于,未进行第二碱处理。
52.对比例5:
53.与实施例3的区别在于,未进行酸处理和第二碱处理。
54.对比例6:
55.与实施例3的区别在于,防腐液为市售木材防腐剂
‑
cca配置,防霉剂为市售木材防火阻燃剂,所述防腐剂和防霉剂均来自三裕化工(深圳)有限公司。
56.对比例7:
57.浸渍前未对竹木进行干燥。
58.实施例8:
59.与实施例3的区别在于,浸渍步骤中的浸渍液为水。
60.对比例9:
61.将竹木加热至温度为60℃,加热时间20min,然后再压力1mpa条件下浸渍20min,浸渍液为水。
[0062][0063]
本技术中,选择的竹木为厚50mm、宽100mm的木条,浸渍完成后将木条剖开,通过浸湿与未浸湿木材颜色的不同,确定浸渍液浸透深度。
[0064]
本实施例中浸渍前对竹木进行干燥对浸渍效果或阻燃效果的影响较小,本技术中该步骤主要是使得浸渍液浸透与未浸透部分之间的分界线更加清晰,可以方便测定浸渍液浸透深度。若为进行干燥,浸渍液浸透与未浸透部分也可区分,但可能误差稍大。
[0065]
本技术中的阻燃性能按照ga/t42.1
‑
1992检验。
[0066]
测试防霉的竹木样品的尺寸为50mm(顺纹长)
×
20mm
×
5mm,每组重复数10块,利用上述处理方法进行处理,然后进行如下测试:主要模拟墙板在适宜环境温湿度条件下的霉变情况, 参考gb/t 18261
‑
2013规定的户外试验方法并进行改良,制成专用的防霉测试箱.防霉测试箱体部分由整理箱和密封观察窗构成。实验箱底部用带温控的加热棒加热水,形成水蒸气;在水的上部有托盘,不与水接触,但装有土壤,上面喷洒各种霉菌孢子悬浮液;中上部有横杆,用于悬挂霉变测试木材样品,不与水和土壤相接触;最上部为对坡型的顶盖,一面开口进行观察;整个装置保持密闭,放置在环境温度为25℃~28℃的房间内。试样接菌培养4周后,目测试菌感染面积。
[0067]
本技术中,首先对竹木进行加热,破坏细胞结构,方便后面处理剂以及阻燃、防霉剂的渗入。
[0068]
dbu指1,8
‑
二氮杂双环[5.4.0]十一碳
‑7‑
烯,可以进一步对处理剂以及阻燃、防霉剂的渗入通道进行扩展、疏通,但是由于dbu具有强碱性,所以dbu的浓度不宜过高。
[0069]
dbu具有碱性,为了减少对竹木的影响,dbu处理后,用双氧水和氨水进行后续处理,一方面双氧水可以比较温和的中和dbu的碱性,另一方面,双氧水和氨水可以生成气体,
对深入通道进行进一步的扩展和疏通。
[0070]
本技术的重点在于对竹木进行前处理,方便阻燃剂、防霉剂的渗入,从而提升阻燃、防霉效果。
[0071]
浸渍后对木板进行干燥,干燥的条件本领域技术人员可以根据需要进行合理选择。
[0072]
尽管参照前述实施例对本发明进行了详细的说明,对于本领域的技术人员来说,其依然可以对前述各实施例所记载的技术方案进行修改,或者对其中部分技术特征进行等同替换, 凡在本发明的精神和原则之内,所作的任何修改、等同替换、改进等,均应包含在本发明的保护范围之内。