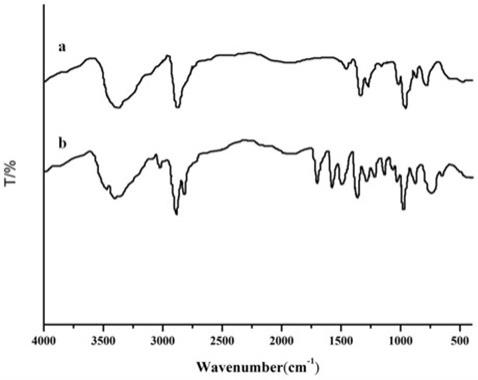
1.本发明属于单晶硅制绒技术领域,具体涉及一种单晶硅制绒剂及绒面单晶硅的制备方法。
背景技术:
2.在硅晶体中,单晶硅太阳电池具有光电转换效率高、使用寿命长、成本逐渐降低的优势,在市场上的份额逐渐提升。现今,国内外很多研究人员致力于怎样提高太阳能电池的光电转化效率,目前最常见的方法是在太阳能电池所用的硅片表面进行刻蚀,在表面制造出绒面结构。人们利用各种工艺让绒面结构均匀,比如在制绒剂里加入各种添加物来,这样做生产成本有所降低,可以减少硅片表面对太阳光的反射,提高太阳能电池光电转换效率。目前,金刚石线锯切割技术被广泛应用到硅晶体的切片工艺中,其加工后的硅片具有加工效率高、生产成本低、环境污染小和硅片表面质量好等优点。但切割后的划痕越来越多样化,硅片表面制绒时所需制绒液的要求也在逐渐提高。
3.现有技术如公开号cn111485290a公开了一种单晶硅制绒剂及绒面单晶硅的制备方法;该单晶硅制绒剂包含碱性化合物和腐蚀剂;腐蚀剂包含以下组分:5wt%~20wt%的尿素;1wt%~10wt%的乳酸钠;余量为水。将单晶硅置于制绒剂中,加热后得到绒面单晶硅。制得的制绒剂能够有效地降低硅片表面出现亮块、白斑、雨点的概率,使得金字塔型绒面的型小且均匀,从而使绒面单晶硅的合格率得到明显的提高。
技术实现要素:
4.本发明的目的在于提供一种具有优良稳定性以及能够降低泡沫性能的单晶硅制绒剂,将其用于单晶硅处理,得到的绒面单晶硅具有绒面均匀、尺寸细小的形貌结构,同时具有较低的反射率。
5.本发明为实现上述目的所采取的技术方案为:一种单晶硅制绒剂,包括碱液和制绒添加剂;制绒添加剂包括改性聚乙烯醇;改性聚乙烯醇由甘西鼠尾草酸甲改性聚乙烯醇。
6.本发明采用改性聚乙烯醇作为单晶硅制绒剂的成分,其可能能够降低制绒剂的表面张力,利于去除气泡,且使单晶硅制绒剂具有优良的稳定性;另一方面,该改性聚乙烯醇可能具有较好的网状结构,对单晶硅进行处理时,能够均匀地平铺在单晶硅表面,得到绒面均匀的单晶硅,进而得到性能优良的绒面单晶硅。
7.进一步地,在本发明的一些实施例中,制绒添加剂还包括酒石酸、硼酸、十二烷基磺酸钠、苯甲酸钠、水。
8.进一步地,在本发明的一些实施例中,制绒添加剂中,各成分重量份分别为:改性聚乙烯醇为5~25份、酒石酸为1~3份、硼酸为0.5~1.5份、十二烷基磺酸钠为0.5~2.5份、苯甲酸钠为0.25~1.75份、水为50~85份。
9.进一步地,在本发明的一些实施例中,碱液为氢氧化钠水溶液、氢氧化钾水溶液中的一种;碱液的浓度为2.5~5.5wt%。
10.进一步地,在本发明的一些实施例中,改性聚乙烯醇的制备方法为:将聚乙烯醇溶于水中,然后加入甘西鼠尾草酸甲、催化剂,在加热条件下进行反应,干燥,洗涤,干燥,得到改性聚乙烯醇。
11.更进一步地,在本发明的一些实施例中,按重量份计,聚乙烯醇为10~20份、水为70~120份、甘西鼠尾草酸为1~5份、催化剂为0.35~0.75份。
12.更进一步地,在本发明的一些实施例中,加热温度为75~90℃,时间为2~4h。
13.进一步地,在本发明的一些实施例中,碱液和制绒添加剂的质量比为5~10:1。
14.本发明还公开了一种单晶硅制绒剂的制备方法,包括:将碱液、制绒添加剂与水混合均匀制得单晶硅制绒剂。
15.本发明还公开了一种单晶硅制绒剂在制备绒面单晶硅中的用途。
16.本发明还公开了一种绒面单晶硅的制备方法,包括以下步骤:s1:将单晶硅片进行预处理;s2:将预处理后的单晶硅片置于单晶硅制绒剂中进行制绒;s3:将制绒后的单晶硅片清洗、干燥,得到绒面单晶硅。
17.本发明将单晶硅片置于含有改性聚乙烯醇的制绒剂中进行处理,各成分之间相互作用,能够使碱液对硅表面进行均匀地腐蚀,得到绒面均匀、尺寸细小的形貌结构,进而得到反射率较低的绒面单晶硅,使其在硅太阳能电池领域具有广泛的应用。
18.进一步地,在本发明的一些实施例中,步骤s1中,单晶硅片的预处理步骤为:将单晶硅片依次进行超声清洗、水洗、无水乙醇洗涤。
19.进一步地,在本发明的一些实施例中,步骤s2中,制绒温度为65~85℃,制绒时间为10~20min。
20.本发明的有益效果如下:(1)本发明采用改性聚乙烯醇作为单晶硅制绒剂的成分,其可能能够降低制绒剂的表面张力,利于去除气泡,且使单晶硅制绒剂具有优良的稳定性;另一方面,该改性聚乙烯醇可能具有较好的网状结构,对单晶硅进行处理时,能够均匀地平铺在单晶硅表面,得到绒面均匀的单晶硅,进而得到性能优良的绒面单晶硅。
21.(2)本发明将单晶硅片置于含有改性聚乙烯醇的制绒剂中进行处理,各成分之间相互作用,能够使碱液对硅表面进行均匀地腐蚀,得到绒面均匀、尺寸细小的形貌结构,进而得到反射率较低的绒面单晶硅,使其在硅太阳能电池领域具有广泛的应用。
22.因此,本发明是一种具有优良稳定性以及能够降低泡沫性能的单晶硅制绒剂,将其用于单晶硅处理,得到的绒面单晶硅具有绒面均匀、尺寸细小的形貌结构,同时具有较低的反射率。
附图说明
23.图1为实施例1中聚乙烯醇改性前后的红外光谱图;图2为单晶制绒剂的泡沫体积;图3为实施例9中绒面单晶硅的sem图。
具体实施方式
24.下面用实施例来进一步说明本发明的实质性内容。应当指出,这些实施例仅用来对本发明进行具体描述,不应当理解为对本发明的限制。本实施例中所用试剂如无特殊说明,均为市购。
25.需要说明的是,在本发明的一些实施例中,改性聚乙烯醇的制备方法为:按重量份计,将10~20份聚乙烯醇溶于70~120份水中,在70~80℃、400~600r/min搅拌速率下溶解1~3h,然后加入1~5份甘西鼠尾草酸甲、0.35~0.75份质量浓度为5%的浓硫酸,在75~90℃下反应为2~4h,在50~75℃下干燥20~30min,用去离子水洗涤3~5次,在50~75℃下干燥40~60min,得到改性聚乙烯醇。
26.需要说明的是,在本发明的一些实施例中,一种单晶硅制绒剂的制备方法,包括:向制绒添加剂中添加碱液、水,在500~800r/min机械搅拌15~30min至混合均匀,然后置于45~55℃恒温水浴中保温20~30min,其中碱液、制绒添加剂与水的质量比5~10:1:40~60,制得单晶硅制绒剂,其中制绒添加剂的成分为:改性聚乙烯醇为5~25份、酒石酸为1~3份、硼酸为0.5~1.5份、十二烷基磺酸钠为0.5~2.5份、苯甲酸钠为0.25~1.75份、水为50~85份。
27.为了优化单晶制绒剂的制绒效果以及制绒均匀,采取的优选措施包括:在制绒添加剂中添加0.5~2.5份异麦芽酮糖醇与5
′‑
肌苷酸二钠混合物,其中异麦芽酮糖醇与5
′‑
肌苷酸二钠混合物的重量比为1:0.25~0.5。异麦芽酮糖醇与5
′‑
肌苷酸二钠混合物的添加,其与制绒添加剂的其他成分相互作用,进一步提高了制绒剂的稳定性与消泡性,然后将制绒剂与碱液共同作用于单晶硅片,得到绒面更为均匀以及反射率较低的单晶硅。
28.需要说明的是,在本发明的一些实施例中,步骤s1中,单晶硅片的预处理具体步骤为:选择无机械损伤的单晶硅片,将单晶硅片在55~65℃下超声清洗3~5min,然后再依次用水清洗、无水乙醇各洗涤2~3次,干燥,得到预处理后的单晶硅。
29.需要说明的是,在本发明的一些实施例中,步骤s2中,将预处理后的单晶硅片完全浸泡在上述制绒剂中,在65~85℃下制绒10~20min,制绒完成后,快速取出,得到制绒后的单晶硅片。
30.需要说明的是,在本发明的一些实施例中,步骤s3中,将制绒后的单晶硅片用水清洗3~5次,干燥,得到绒面单晶硅。
31.以下结合具体实施方式和附图对本发明的技术方案作进一步详细描述:实施例1:改性聚乙烯醇的制备方法为:按重量份计,将13份聚乙烯醇(购自湖北鑫润德化工有限公司)溶于115份水中,在75℃、500r/min搅拌速率下溶解2h,然后加入4.5份甘西鼠尾草酸甲、0.45份质量浓度为5%的浓硫酸,在90℃下反应为3h,在60℃下干燥25min,用去离子水洗涤3次,在60℃下干燥40min,得到改性聚乙烯醇。
32.实施例2:一种单晶硅制绒剂的制备方法,包括:向制绒添加剂中添加浓度为4.5wt%的氢氧化钠溶液、水,在600r/min机械搅拌20min至混合均匀,然后置于45℃恒温水浴中保温30min,其中碱液、制绒添加剂与水的质量比5:1:50,制得单晶硅制绒剂,其中制绒添加剂的成分为:实施例1中的改性聚乙烯醇为13份、酒石酸为2份、硼酸为1.5份、十二烷基磺酸钠为0.5份、苯甲酸钠为1.55份、水为75份。
33.实施例3:一种单晶硅制绒剂的制备方法,与实施例2不同的是:向制绒添加剂中添加浓度为4.5wt%的氢氧化钠溶液、水,在500r/min机械搅拌30min至混合均匀,然后置于50℃恒温水浴中保温25min,其中碱液、制绒添加剂与水的质量比8:1:60,制得单晶硅制绒剂,其中制绒添加剂的成分为同实施例2。
34.实施例4:一种单晶硅制绒剂的制备方法,与实施例2不同的是:制绒添加剂的成分为实施例1中的改性聚乙烯醇为20份、酒石酸为3份、硼酸为1份、十二烷基磺酸钠为1.5份、苯甲酸钠为1.75份、水为85份。
35.实施例5:一种单晶硅制绒剂的制备方法,与实施例2不同的是:制绒添加剂的成分为:实施例1中的改性聚乙烯醇为13份、1份异麦芽酮糖醇与5
′‑
肌苷酸二钠混合物,其中异麦芽酮糖醇与5
′‑
肌苷酸二钠混合物的重量比为1:0.25,酒石酸为2份、硼酸为1.5份、十二烷基磺酸钠为0.5份、苯甲酸钠为1.55份、水为75份。
36.实施例6:一种单晶硅制绒剂的制备方法,与实施例5不同的是:在制绒添加剂的成分中添加2份异麦芽酮糖醇与5
′‑
肌苷酸二钠混合物,其中异麦芽酮糖醇与5
′‑
肌苷酸二钠混合物的重量比为1:0.25。
37.实施例7:一种单晶硅制绒剂的制备方法,与实施例5不同的是:异麦芽酮糖醇与5
′‑
肌苷酸二钠混合物的重量比为1:0.5。
38.实施例8:一种单晶硅制绒剂的制备方法,与实施例5不同的是:制绒添加剂的成分为:聚乙烯醇(购自湖北鑫润德化工有限公司)为13份、1份异麦芽酮糖醇与5
′‑
肌苷酸二钠混合物,其中异麦芽酮糖醇与5
′‑
肌苷酸二钠混合物的重量比为1:0.25,酒石酸为2份、硼酸为1.5份、十二烷基磺酸钠为0.5份、苯甲酸钠为1.55份、水为75份。
39.实施例9:一种绒面单晶硅的制备方法,包括以下步骤:s1:选择无机械损伤的单晶硅片,将单晶硅片在60℃下超声清洗3min,然后再依次用水清洗、无水乙醇各洗涤3次,干燥,得到预处理后的单晶硅;s2:将预处理后的单晶硅片将预处理后的单晶硅片完全浸泡在实施例2中的制绒剂中,在70℃下制绒15min,制绒完成后,快速取出,得到制绒后的单晶硅片。;s3:将制绒后的单晶硅片用水清洗3次,干燥,得到绒面单晶硅。
40.实施例10:一种绒面单晶硅的制备方法,与实施例9不同的是:步骤s2中,将预处理后的单晶硅片将预处理后的单晶硅片完全浸泡在实施例3中的制绒剂中,在70℃下制绒15min。
41.实施例11:一种绒面单晶硅的制备方法,与实施例9不同的是:步骤s2中,将预处理后的单晶硅片将预处理后的单晶硅片完全浸泡在实施例4中的制绒剂中,在70℃下制绒15min。
42.实施例12:一种绒面单晶硅的制备方法,与实施例9不同的是:步骤s2中,将预处理后的单晶硅片将预处理后的单晶硅片完全浸泡在实施例5中的制绒剂中,在70℃下制绒15min。
43.实施例13:一种绒面单晶硅的制备方法,与实施例9不同的是:步骤s2中,将预处理后的单晶硅片将预处理后的单晶硅片完全浸泡在实施例6中的制绒剂中,在70℃下制绒15min。
44.实施例14:一种绒面单晶硅的制备方法,与实施例9不同的是:步骤s2中,将预处理后的单晶硅片将预处理后的单晶硅片完全浸泡在实施例7中的制绒剂中,在70℃下制绒15min。
45.实施例15:一种绒面单晶硅的制备方法,与实施例9不同的是:步骤s2中,将预处理后的单晶硅片将预处理后的单晶硅片完全浸泡在实施例8中的制绒剂中,在70℃下制绒15min。
46.对比例1:一种单晶硅制绒剂的制备方法,与实施例2不同的是:制绒添加剂的成分为:聚乙烯醇(购自湖北鑫润德化工有限公司)为13份、酒石酸为2份、硼酸为1.5份、十二烷基磺酸钠为0.5份、苯甲酸钠为1.55份、水为75份。
47.对比例2:一种绒面单晶硅的制备方法,与实施例9不同的是:步骤s2中,将预处理后的单晶硅片将预处理后的单晶硅片完全浸泡在对比例1中的制绒剂中,在70℃下制绒15min。
48.性能测试表征:1.改性聚乙烯醇红外光谱测试采用nicolet 6700型傅立叶变换红外光谱仪测试改性前后聚乙烯醇的红外谱图。
49.图1为实施例1中聚乙烯醇改性前后的红外光谱图。曲线a、b分别为是聚乙烯醇、改性聚乙烯醇的红外谱图;由图1可以看出,相对于聚乙烯醇,改性聚乙烯醇在3052cm-1
附近出现的特征吸收峰为苯环的伸缩振动;在2847cm-1
附近出现的特征吸收峰为烷基中c-h的对称伸缩振动;在1721cm-1
附近出现的特征吸收峰为酯基的伸缩振动;因此,采用甘西鼠尾草酸甲对聚乙烯醇进行改性制得改性聚乙烯醇。
50.2. 单晶硅制绒剂稳定性测试将单晶硅制绒剂样品放置在23
±
2℃条件下,观察制绒剂有无分层和明显沉淀物。
51.表1 单晶硅制绒剂稳定性测试结果
组别实施例2实施例5实施例8对比例1稳定性45天后出现分层现象60天后出现分层现象40天后出现分层现象26天后出现分层现象
由表1可以看出,对比实施例2与对比例1,实施例2的稳定性优于对比例1,说明采用甘西鼠尾草酸甲对聚乙烯醇进行改性制得改性聚乙烯醇,将其作为制绒剂的成分,其提高了制绒剂的稳定性;对比实施例2与实施例5、实施例8与对比例1,实施例5的稳定性优于实施例2,实施例8的稳定性优于对比例1,说明在制绒剂中添加异麦芽酮糖醇与5
′‑
肌苷酸二钠混合物,进一步提高了制绒剂的稳定性,且改性聚乙烯醇、异麦芽酮糖醇与5
′‑
肌苷酸二钠混合物共同作用,显著提高了制绒剂的稳定性,使其能够长期储存。
52.3. 单晶制绒剂泡沫性能测试
采用震荡方法测试制绒剂的泡沫性能;取15ml实施例2、实施例5、实施例8与对比例1中的制绒剂置于具塞量筒中,震荡40s后停止,将具塞量筒放置在实验台上,记载泡沫高度并开始计时,在相同的时间记录下泡沫髙度,直至泡沫全部消失。
53.图2为单晶制绒剂的泡沫体积。d1、d2、d3、d4分别为实施例2、实施例5、实施例8与对比例1;由图2可以看出,在0s时,实施例2的泡沫体积低于18ml,对比实施例2与对比例1,实施例2的泡沫体积低于对比例1,且实施例2的消泡时间高于对比例1,说明采用甘西鼠尾草酸甲对聚乙烯醇进行改性制得改性聚乙烯醇,将其作为制绒剂的成分,其使制绒剂具有较低的表面张力,利于去除气泡;对比实施例2与实施例5、实施例8与对比例1,实施例5的泡沫体积低于实施例2,实施例8的泡沫体积低于对比例1,说明在制绒剂中添加异麦芽酮糖醇与5
′‑
肌苷酸二钠混合物,进一步降低了制绒剂的泡沫性能,使其能够更均匀的与单晶硅接触,得到均匀的绒面单晶硅。
54.4. 绒面单晶硅表面形貌测试采用tm 3000型扫描电子显微镜对制得的绒面单晶硅试样的形貌进行观察。
55.图3为实施例9中绒面单晶硅的sem图。由图3可以看出,实施例3中绒面单晶硅表面“金字塔”结构分布均匀,且尺寸细小,密集。
56.5. 绒面单晶硅反射率测试采用cary 100自我可见分光光度计测试绒面单晶硅制绒前后的反射率,并观察单晶硅的绒面外观以及采用金相显微镜观察绒面单晶硅的形貌。
57.表2 绒面单晶硅的绒面外观和相对反射率组别绒面外观绒面形貌相对反射率(%)实施例9较黑无条痕,金字塔细小,密集49.5实施例10较黑无条痕,金字塔细小,密集47.3实施例11较黑无条痕,金字塔细小,密集48.2实施例12黑无条痕,金字塔细小,均匀41.6实施例13黑无条痕,金字塔细小,均匀38.4实施例14黑无条痕,金字塔细小,均匀40.8实施例15稍黑无条痕,金字塔细小,均匀58.6对比例2表面有少量发白有条痕,金字塔稀疏,较大67.2由表2可以看出,实施例9-11中单晶硅的绒面外观较黑,绒面形貌无条痕,金字塔细小,密集;且相对反射率低于50%,对比实施例9与对比例2,实施例9中绒面单晶硅的相对反射率低于对比例2,说明采用甘西鼠尾草酸甲对聚乙烯醇进行改性制得改性聚乙烯醇,将其作为制绒剂的成分,并对单晶硅进行处理,得到绒面形貌较好,相对反射率较低的绒面单晶硅;实施例12-14中单晶硅的绒面外观黑,绒面形貌无条痕,金字塔细小,均匀;且相对反射率低于42%,对比实施例9与实施例12、实施例15与对比例2,实施例12中绒面单晶硅的绒面形貌优于实施例9,相对反射率低于实施例12,实施例15中绒面单晶硅的绒面形貌优于对比例2,相对反射率低于对比例2,说明在制绒剂中添加异麦芽酮糖醇与5
′‑
肌苷酸二钠混合物,并对单晶硅进行处理,得到绒面形貌更为优良,相对反射率更低的绒面单晶硅,使其在硅太阳能电池领域具有广泛的应用。
58.本发明的操作步骤中的常规操作为本领域技术人员所熟知,在此不进行赘述。
59.以上实施方式仅用于说明本发明,而并非对本发明的限制,本领域的普通技术人员,在不脱离本发明的精神和范围的情况下,还可以做出各种变化和变型。因此,所有等同的技术方案也属于本发明的范畴,本发明的专利保护范围应由权利要求限定。