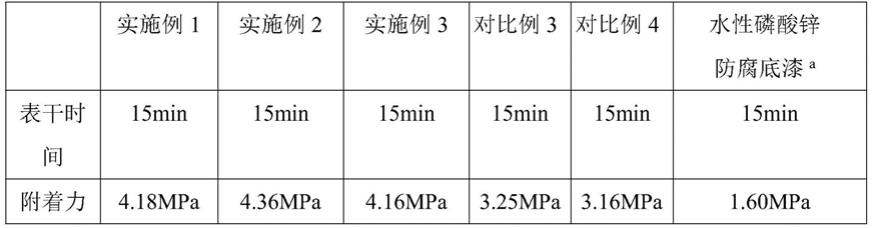
1.本发明属于金属防腐涂料技术领域,具体涉及带锈金属表面的锈转涂料。
背景技术:
2.金属腐蚀造成的损失大于自然灾害的总合。针对金属腐蚀防护问题,有机防腐涂料因具有屏蔽效应、化学防护效应、电化学防护等作用,是当下最为有效可行的手段。但研究表明需要确保良好涂层/金属界面结合才能实现防腐涂层的功能。常用的基材前处理包括机械法和化学除锈法等,可以确保涂层/金属界面的良好结合。但是在野外受到设备、场地以及环保等限制无法进行有效的基材处理。为此,带锈涂料成为研究热点。带锈涂料又称低表面容忍涂料,是能直接将锈层稳定、钝化或转化,使得活泼的锈层变为稳定的物质,达到对金属表面除锈和保护的双重目的。现在广泛研究的带锈涂料包括三种类型:渗透型、稳定型和转化型。国内基于溶剂型环氧树脂开发了部分产品性能较为优良,但是受环保限制不利于推广使用。
3.水性涂料是满足绿色环保要求的未来涂料行业发展的重要方向。磷酸、植酸、以及单宁酸等是最为有效的锈转化功能成分,但这些物质本身多数呈酸性致使水性成膜体系的稳定性存在隐患,限制了高性能水性低表面处理涂料的发展。如专利cn 112300702 a中,仅能使用少了的磷酸、植酸,且需要利用醇胺成分进行中和获得弱酸性,使得锈层的转化能力下降,在锈蚀基材表面附着力较低。专利cn 112662252 a中创新的使用酸性树脂作为成膜物可与酸性功能成分良好相容,但其锈面完整的包封附着力效果仍有改进空间,另外,其采用磷酸作为主要功能成分,在环保上可能在未来受到限制。
技术实现要素:
4.为解决现有涂料存在的不足,本发明第一目的在于,提供了一种单组分固化酸性水性锈转涂料(本发明也简称为酸性水性锈转涂料),旨在改善涂料在锈面附着力,改善后续功能涂料的复合效果以及防腐效果。
5.本发明第二目的在于,提供所述的单组分固化酸性水性锈转涂料的制备方法。
6.本发明第三目的在于,提供所述的单组分固化酸性水性锈转涂料的应用。
7.一种单组分固化酸性水性锈转涂料,为包含酸性改性水性丙烯酸树脂乳液、酸性锈转化功能成分、功能缓蚀剂、助剂a、渗透剂、水的水性涂料;
8.所述的助剂a为具有式1结构式的化合物;
[0009][0010]
在锈面锈转方面,酸性成分有助于锈面转化,但难于避免非锈面的腐蚀损伤,从而影响水性涂料在整个金属表面的成膜性以及成膜均匀性。针对该技术问题,本发明经过研究发现,将所述的酸性改性水性丙烯酸树脂乳液、酸性锈转化功能成分、功能缓蚀剂、助剂a联合,存在协同性,能够改善水性涂料的操作性以及成膜性,能够改善涂料和锈面的整体成
膜附着力和包封效果。
[0011]
本发明中,所述的酸性改性水性丙烯酸树脂乳液在丙烯酸聚合物链上接枝修饰有磺酸基、羧酸基中的至少一种酸基的聚合物的乳液,其可以是蓝德堡mt
‑
718a,ph优选为2
‑
2.3。
[0012]
作为优选,所述的酸性锈转化功能成分为单宁酸、植酸和丙酸中至少一种。
[0013]
作为优选,所述的功能缓蚀剂为磷酸锌和三聚磷酸铝中的至少一种。
[0014]
作为优选,渗透剂为甘油、edta中的至少一种。
[0015]
作为优选,所述的水性涂料中:
[0016]
酸性改性水性丙烯酸树脂乳液的重量份为:100
‑
200份;
[0017]
酸性锈转化功能成分的重量份为:5
‑
20份;
[0018]
功能缓蚀剂的重量份为:10
‑
40份;
[0019]
助剂a的重量份为5
‑
10份;
[0020]
渗透剂的重量份为5
‑
20份;
[0021]
水的重量份为30
‑
80份。
[0022]
作为优选,所述的水性涂料中还添加有消泡剂、润湿分散剂中的至少一种添加剂;
[0023]
优选地,所述的消泡剂为有机硅改性消泡剂为有机硅改性消泡剂r910s、r920s中的至少一种;
[0024]
优选地,所述的润湿分散剂为byk191、byk192中的至少一种。
[0025]
作为优选,所述的消泡剂的重量份小于或等于2份,进一步优选为1~1.5份;
[0026]
所述的润湿分散剂的重量份小于或等于2份,进一步优选为1~1.5份。
[0027]
进一步优选,所述的水性涂料中:
[0028]
酸性改性水性丙烯酸树脂乳液的重量份为:100
‑
120份;
[0029]
酸性锈转化功能成分的重量份为:10
‑
20份;
[0030]
功能缓蚀剂的重量份为:25
‑
35份;
[0031]
助剂a的重量份为5
‑
10份;
[0032]
渗透剂的重量份为5
‑
10份;
[0033]
所述的消泡剂的重量份为1~1.5份;
[0034]
所述的润湿分散剂的重量份为1~1.5份;
[0035]
水的重量份为50
‑
70份。
[0036]
本发明还提供了所述的单组分固化酸性水性锈转涂料的制备方法,将各成分混合均匀即得。
[0037]
本发明优选的单组分固化酸性水性锈转涂料的制备方法,其包括以下步骤:
[0038]
步骤(1):将酸性锈转化功能成分、功能缓蚀剂、助剂a、渗透剂、润湿分散剂和水混合,获得组分a;
[0039]
步骤(2):在酸性改性水性丙烯酸树脂乳液和消泡剂混合,得到组分b;
[0040]
步骤(3)将步骤(1)的组分a缓慢加入步骤(2)的组分b中,制成混合溶液,即得。
[0041]
本发明还包括所述的单组分固化酸性水性锈转涂料的应用,将其涂覆在生锈金属的表面。
[0042]
本发明所述的应用,其也可以涂覆在未生锈的表面。
[0043]
有益效果
[0044]
本发明基于所述的酸性改性水性丙烯酸树脂乳液、酸性锈转化功能成分、功能缓蚀剂、助剂a的联合,能够实现协同,能够显著改善水性涂料的成膜性和操作性、能够在锈面以及整个金属面形成高附着力的底膜,其不仅能够将锈面转化,避免涂料对非锈面的腐蚀;此外,还有助于改善其他功能涂料的复合。
[0045]
本发明所述的水性涂料,不含磷酸等对环境造成污染的成分,绿色环保,且涂料组成的稳定性好,可以长期存放;所选用的功能成分均为环保成分,利于后续推广应用。
附图说明
[0046]
图1为实施例1的锈面涂覆涂料微观图;
[0047]
图2为对比例1的锈面涂覆涂料微观图;
[0048]
图3为实施例1和对比例1的阻抗模值对比图;
[0049]
图4为对比例2的制备的产物的图片;
[0050]
图5为实施例1和对比例3的涂料在涂覆前以及涂覆后的形貌图;
具体实施方式
[0051]
以下案例,所采用的酸性改性水性丙烯酸树脂乳液为蓝德堡mt
‑
718a,其ph为2
‑
2.3。
[0052]
所述的消泡剂为有机硅改性消泡剂r910s;
[0053]
所述的润湿分散剂为byk191。
[0054]
测试:
[0055]
锈面附着力测定步骤:
[0056]
将涂料直接涂装在不经任何打磨等处理的gb/t 10125
‑
2012中性连续盐雾三天锈蚀碳钢表面,测定其附着力(附着力测试标准astm4541)。
[0057]
非锈蚀表面附着力测定步骤:
[0058]
在完好q235碳钢金属表面(表面除油后经砂纸手工打磨至sa1级别)进行涂料涂刷,测定其附着力(附着力测试标准astm4541);
[0059]
实施例1:
[0060]
酸性基团改性丙烯酸树脂乳液100份,锈转化功能成分(单宁酸)10份,功能缓蚀剂(三聚磷酸铝)30份,助剂a(式1中,
‑
oh位于8
‑
位)5份,渗透剂(甘油)10份,消泡剂(有机硅改性消泡剂)1.5份,润湿分散剂1份,去离子水60份。
[0061]
(1)将10份单宁酸,30份三聚磷酸铝、5份助剂a混合物,10份甘油,润湿分散剂1份溶于60份去离子水中,10000rpm搅拌10min,获得组分a;
[0062]
(2)在100份酸性基团改性丙烯酸树脂乳液中加入1.5份有机硅改性消泡剂100rpm速率搅拌20min获得组分b;
[0063]
(3)将步骤(1)的组分a缓慢加入步骤(2)的组分b中,制成混合溶液,并用100rpm速率搅拌20min备用。
[0064]
锈面涂覆微观图片见图1,锈面涂层性能表1所示,光面附着力数据见表2。
[0065]
实施例2:
[0066]
酸性基团改性丙烯酸树脂乳液100份,锈转化功能成分(单宁酸)20份,功能缓蚀剂(三聚磷酸铝)30份,助剂a(式1中,
‑
oh位于8
‑
位)10份,渗透剂(甘油)10份,消泡剂(有机硅改性消泡剂)1.5份,润湿分散剂1份,去离子水60份。
[0067]
(1)将20份单宁酸,30份三聚磷酸铝、10份助剂a,10份甘油,润湿分散剂1份溶于60份去离子水中,10000rpm搅拌10min,获得组分a;
[0068]
(2)在100份酸性基团改性丙烯酸树脂乳液中加入1.5份有机硅改性消泡剂100rpm速率搅拌20min获得组分b;
[0069]
(3)将步骤(1)的组分a缓慢加入步骤(2)的组分b中,制成混合溶液,并用100rpm速率搅拌20min备用。
[0070]
锈面涂层性能表1所示。
[0071]
实施例3:
[0072]
酸性基团改性丙烯酸树脂乳液100份,锈转化功能成分(植酸和丙酸以1:1形成的混合物)20份,功能缓蚀剂(三聚磷酸铝)30份,助剂a(式1中,
‑
oh位于8
‑
位)5份,渗透剂(甘油)10份,消泡剂(有机硅改性消泡剂)1.5份,润湿分散剂1份,去离子水60份。
[0073]
(1)将20份植酸和丙酸混合物,30份三聚磷酸铝、5份助剂a,10份甘油,润湿分散剂1份溶于60份去离子水中,10000rpm搅拌10min,获得组分a;
[0074]
(2)在100份酸性基团改性丙烯酸树脂乳液中加入1.5份有机硅改性消泡剂100rpm速率搅拌20min获得组分b;
[0075]
(3)将步骤(1)的组分a缓慢加入步骤(2)的组分b中,制成混合溶液,并用100rpm速率搅拌20min备用。
[0076]
锈面涂层性能表1所示。
[0077]
对比例1:
[0078]
和实施例1相比,区别仅在于,仅采用组分a作为涂料,具体的配方为:
[0079]
将10份单宁酸,30份三聚磷酸铝,5份助剂a,10份甘油,润湿分散剂1份溶于60份去离子水中,10000rpm搅拌10min,获得单组分锈转化液备用。
[0080]
按实施例1方法进行测定,微观结构见图2,阻抗结果见图3。实施例1的电化学阻抗约为对比例1的四十倍。
[0081]
对比例2:
[0082]
和实施例1相比,区别仅在于,采用常规树脂乳液(蓝德堡mt
‑
719)替换本发明所述的酸性基团修饰树脂乳液,具体的配方为:
[0083]
通丙烯酸树脂乳液(蓝德堡mt
‑
719)100份,锈转化功能成分(单宁酸)10份,功能缓蚀剂(三聚磷酸铝)30份,助剂a(式1中,
‑
oh位于8
‑
位)5份,渗透剂(甘油)10份,消泡剂(有机硅改性消泡剂)1.5份,润湿分散剂1份,去离子水60份。
[0084]
制备的涂料图片见图4,显示普通丙烯酸树脂与酸性功能成分无法相容,ab混合后发生破乳,难于成功制得所述的涂料。
[0085]
对比例3:
[0086]
和实施例1相比,区别仅在于,采用六次甲基四胺替换助剂a,其配方为:
[0087]
酸性基团改性丙烯酸树脂乳液100份,锈转化功能成分(单宁酸)10份,功能缓蚀剂(三聚磷酸铝)30份,防闪锈剂(六次甲基四胺)5份,渗透剂(甘油)10份,消泡剂(有机硅改性
消泡剂)1.5份,润湿分散剂1份,去离子水60份。锈面以及光面的附着力结果分别见表1和表2。
[0088]
对比例4:
[0089]
和实施例1相比,区别仅在于,未添加助剂a,其他工艺和成分均同实施例1。
[0090]
在完好q235碳钢金属表面(表面除油后经砂纸手工打磨至sa1级别)进行涂刷,见图5所示,最左侧为待刷涂金属试样。如图对比例3由于涂刷过程中的闪锈现象,造成涂层的不均匀。而实施例使用了助剂a,能够有效缓解非锈面受酸性成分的损伤问题,可以获得均匀稳定的涂层,且涂层具有更优的附着力(表2)。
[0091]
表1初步性能(锈蚀基材表面)
[0092][0093]
注:a由涂善公司提供的牌号为e7040水性环氧磷酸锌底漆的底漆;
[0094]
表2非锈蚀表面结合强度
[0095] 实施例1对比例3对比例4蓝德堡mt
‑
718a附着力8.98mpa2.75mpa1.85mpa3.12mpa
[0096]
综上可见,本发明所述的成分,能够在锈面以及光滑面均能够获得良好的成膜包封效果,且附着力更优。