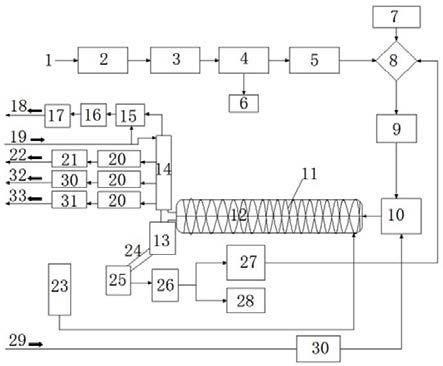
1.本发明涉及资源循环利用技术领域,具体是涉及一种将废弃塑料解聚转化为燃油的生产线及方法。
背景技术:
2.目前,对于塑料废弃物的处理,最有前景的方法是将塑料废弃物转化为高能燃料。近年来,利用生物质和塑料废弃物合成车用燃料是一个热门话题,研究人员作出了巨大努力,但是考虑到生产成本、能源利用效力和可持续性等因素,目前常用的塑料废物的利用的化学方法主要有以下几种:1、燃烧:在适当的焚烧厂将废弃塑料燃料,从中获得热量或者将热能用于发电得到电能。
3.2、气化:将废弃塑料加热气化,通常加热温度为900-1300℃;此方法合成的气体必须通过费托合成等方法转化为燃料。
4.3、催化热解:在500至1000℃的温度下,高压和催化剂作用下进行热解。热解生成原油、生物泥浆、焦炭和合成气,这些产物必须在下一步转化为燃料。
5.4、液化:温度在250至400℃之间,在高压、催化剂条件下,部分废弃塑料液化为可燃油,但目前该方法的大多数工艺都是在有机溶剂或水存在的情况下进行研究的。
6.综上,目前对于塑料废物的利用大多数仍然是低端利用方法,虽然已经有较多的研究人员着手于将废弃塑料液化为车用燃料,但该方法目前仍然处于研究阶段,即使有少数企业开始进行产业化处理,但目前的液体油的收率都较低,通常只有50-70%。
技术实现要素:
7.为了克服现有技术存在的缺点,本发明提出了一种将废弃塑料解聚转化为燃油的生产线及方法。实现从固体废弃塑料到液体燃油的高收率转化,该方法投资小,成本低,易于实现产业化。
8.本发明提供一种将废弃塑料解聚转化为燃油的生产线,具体为:缓冲罐(2)、干燥机(3)、筛选台(4)、破碎机(5)、混料装置(8)、双螺旋挤压给料机(9)、塑料切削装置(10)、解聚窑(12)依次连接,解聚窑(12)和蒸馏塔(14)、固体沉淀容器(13)三通连接;所述的解聚窑(12)内设置有双螺旋输送机构(11)。
9.所述的蒸馏塔(14)的设置有上、中、下三个液体出口,上部液体出口依次连接冷却器(20)、汽油储油容器(21)、汽油输出管路(22);中部液体出口依次连接冷却器(20)、柴油储油容器(30)、柴油输出管路(32);下部液体出口依次连接冷却器(20)、重油储油容器(31)、重油输出管路(33);蒸馏塔(14)的顶部气体出口依次连接气体冷却器(15)、气体滤清器(16)、气体缓冲罐(17)、可燃气输出管路(18)。
10.循环水供应管路(19)为气体冷却器(15)、蒸馏塔(14)提供冷却水。
11.所述的固体沉淀容器(13)依次连接密封螺旋输送器(24)、催化剂再生罐(25)、振
动筛(26);振动筛(26)连接再生催化剂容器(27)和固体残留物容器(28)。再生催化剂容器(27)可通过输送机构连接混料装置(8)的加料口。
12.所述的塑料切削装置(10)通过旋转气闸阀(30)连接氮气供应管路(29)。
13.所述的生产线还设置有氢气罐(23)及相应的管路连接至解聚窑(12)。
14.所述的塑料切削装置(10)、解聚窑(12)均为无氧空间。仅在初始反应时通入氮气,替换塑料切削装置(10)和解聚窑(12)中的空气,反应开始后即可停止供应氮气,原因在于反应产生的气体可以维持系统内的压力,无需再充入氮气即可维持大气压且实现无氧空间。
15.所述的筛选台(4)还连接有废料仓(6),所述的混料装置(8)的加料口还连接有催化剂仓(7)。
16.所述的解聚窑(12)采用电加热或燃气加热,从进料端到出渣端,采用不同的温度场从外部分段加热,解聚窑(12)分为低温段和高温段,低温段占解聚窑(12)整体长度的25%-35%,解聚窑外壁用5-20cm的石棉或玻璃棉隔热。
17.一种将废弃塑料解聚转化为燃油的方法,包括原料处理、解聚反应、蒸馏、催化剂回收步骤;原料经过干燥、除杂、破碎后,添加催化剂进行挤压脱除空气和剩余水分,然后无氧氛围下切削成颗粒,在320-400℃的温度下,无氧、密闭且常压状态下,以纯氧化铝为催化剂,对塑料材料进行催化解聚并转化为蒸汽,蒸汽经蒸馏后得到液体油和可燃气体。
18.当解聚窑采用燃气加热的方式时,可以将上述工艺得到的可燃气体混入燃气中用于解聚窑加热。
19.所述的原料处理步骤,具体为,将原料(1)初步除杂后加入到缓冲罐(2),然后输送至干燥机(3)进行预干燥,输送至筛选台(4)进行进一步除杂,除去金属、砂石、玻璃等硬物,除杂后输送至破碎机(5)破碎后,进入混料装置(8)与从催化剂仓(7)加入的催化剂粉末混匀,进入双螺旋挤压给料机(9),将原料挤压成圆棒,圆棒由的塑料切削装置(10)切成颗粒。
20.所述的解聚反应步骤,具体为,物料颗粒经双螺旋输送机构(11)搅拌并向前推进,物料在解聚窑(12)内从低温段向前推进至高温段,解聚反应与向前推进同时进行,推进至前端连接蒸馏塔(14)和固体沉淀容器(13)的位置前完成反应,转化为热油蒸汽,实现无氧、常压条件下连续加料和连续反应。
21.所述的蒸馏步骤,具体为,反应完成后得到的热油蒸汽不进行任何冷却进入蒸馏塔(14),蒸馏塔(14)的上、中、下三个液体出口分别输出的汽油、柴油、重油分别经冷却器(20)冷却后,分别进入汽油储油容器(21)、柴油储油容器(30)、重油储油容器(31),然后分别经汽油输出管路(22)、柴油输出管路(32)、重油输出管路(33)输出进行进一步处理;不能够冷却为液体油的气体经气体冷却器(15)和气体滤清器(16)处理后进入气体缓冲罐(17),过滤后经可燃气输出管路(18)输出,用于解聚窑(12)加热。
22.所述的催化剂回收步骤,具体为,残留固体在固体沉淀容器(13)中收集,然后经密封螺旋输送器(24)输送至催化剂再生罐(25),通入空气加热将焦炭消耗,得到再生催化剂与金属混合物,然后经振动筛(26)分离得到再生催化剂和金属,分别存放于再生催化剂容器(27)和固体残留物容器(28)。
23.所述的塑料切削装置(10)对物料进行切削在无氧环境下进行,切削后的物料颗粒粒度为5-10cm;含水量小于5%。
24.所述的催化剂添加量为3%-8%。
25.所述的解聚反应步骤中,物料在解聚窑(12)内停留的时间为10-40min。
26.所述的解聚反应,初始反应前,开启旋转气闸阀(30),经氮气供应管路(29)通入氮气,反应开始后,停止氮气供应。
27.所述的原料由pe、hdpe、ldpe、pp和ps中的一种或2种以上组成。
28.所述的原料主要由pe、hdpe、ldpe、pp和ps中的一种或2种以上组成,原料中可以掺杂10%以内的生物质废物或者含氧、含氯、含氟、含氮塑料。原料中掺杂的生物质废物或者含氧、含氯、含氟、含氮塑料达到10%以上时,连通相应的管路通入氢气。
29.本发明的有益效果在于:本发明整个工艺过程是在封闭、无氧的条件下进行,且实现连续生产,反应温度低于400℃,不产生二噁英,不产生污染;能耗低,节约成本,生产效率高;解聚和转化为热油蒸汽均在解聚窑一步完成,蒸馏步骤无需进一步加热,减少能源投入,节约成本;本发明的催化剂采用氧化铝,成本低,收率高,且实现回收循环利用;实现了对废弃塑料的综合利用,具有效率高、投资少、运行维护费低等特点。
30.本发明主要对pe、pp、hdpe、ldpe、ps等主要塑料废弃物进行解聚,液体油收率在90%以上;此类塑料的特点是碳氢比为1:2,此类塑料在市场中所占份额超过85%,再除去循环利用效果好的含氮塑料,此类塑料在废弃塑料中所占比例更大,本发明可以实现对此类塑料的高收率回收,这对解决目前的白色污染问题具有及其重要的意义。即使原料中混入生物质垃圾,在生物质含量小于等于10%时,仍然能够得到88%以上的液体油收率。
附图说明
31.图1为本发明生产线示意图;图中:1-物料,2-缓冲罐,3-干燥机,4-筛选台,5-破碎机,6-废料仓,7-催化剂仓,8-混料装置,9-双螺旋挤压给料机,10-塑料切削装置,11-双螺旋输送机构,12-解聚窑,13-固体沉淀容器,14-蒸馏塔,15-气体冷却器,16-气体滤清器,17-气体缓冲罐,18-可燃气输出管路,19-循环水供应管路,20-冷却器,21-汽油储油容器,22-汽油输出管路,23-氢气罐,24-密封螺旋输送器,25-催化剂再生罐,26-振动筛,27-再生催化剂容器,28-固体残留物容器,29-氮气供应管路,30-旋转气闸阀,31-柴油储油容器,32-重油储油容器,33-柴油输出管路,34-重油输出管路。
具体实施方式
32.实施例1,本发明提供一种将废弃塑料解聚转化为燃油的生产线,具体为:缓冲罐(2)、干燥机(3)、筛选台(4)、破碎机(5)、混料装置(8)、双螺旋挤压给料机(9)、塑料切削装置(10)、解聚窑(12)依次连接,解聚窑(12)和蒸馏塔(14)、固体沉淀容器(13)三通连接;所述的解聚窑(12)内设置有双螺旋输送机构(11)。
33.所述的蒸馏塔(14)的设置有上、中、下三个液体出口,上部液体出口依次连接冷却器(20)、汽油储油容器(21)、汽油输出管路(22);中部液体出口依次连接冷却器(20)、柴油储油容器(30)、柴油输出管路(32);下部液体出口依次连接冷却器(20)、重油储油容器(31)、重油输出管路(33);蒸馏塔(14)的顶部气体出口依次连接气体冷却器(15)、气体滤清器(16)、气体缓冲罐(17)、可燃气输出管路(18)。
34.循环水供应管路(19)为气体冷却器(15)、蒸馏塔(14)提供冷却水。
35.所述的固体沉淀容器(13)依次连接密封螺旋输送器(24)、催化剂再生罐(25)、振动筛(26);振动筛(26)连接再生催化剂容器(27)和固体残留物容器(28)。再生催化剂容器(27)可通过输送机构连接混料装置(8)的加料口。
36.所述的塑料切削装置(10)通过旋转气闸阀(30)连接氮气供应管路(29)。
37.所述的生产线还设置有氢气罐(23)及相应的管路连接至解聚窑(12)。
38.所述的塑料切削装置(10)、解聚窑(12)均为无氧空间。仅在初始反应时通入氮气,替换塑料切削装置(10)和解聚窑(12)中的空气,反应开始后即可停止供应氮气,原因在于反应产生的气体可以维持系统内的压力,无需再充入氮气即可维持大气压且实现无氧空间。
39.所述的筛选台(4)还连接有废料仓(6),所述的混料装置(8)的加料口还连接有催化剂仓(7)。
40.所述的解聚窑(12)采用电加热或燃气加热,从进料端到出渣端,采用不同的温度场从外部分段加热,解聚窑(12)分为低温段和高温段,低温段占解聚窑(12)整体长度的25%-35%,解聚窑外壁用5-20cm的石棉或玻璃棉隔热。
41.实施例2,一种将废弃塑料解聚转化为燃油的方法,包括原料处理、解聚反应、蒸馏、催化剂回收步骤;原料经过干燥、除杂、破碎后,添加催化剂进行挤压脱除空气和剩余水分,然后无氧氛围下切削成颗粒,在320-400℃的温度下,无氧、密闭且常压状态下,以纯氧化铝为催化剂,对塑料材料进行催化解聚并转化为蒸汽,蒸汽经蒸馏后得到液体油和可燃气体。
42.所述的原料处理步骤,具体为,将原料(1)初步除杂后加入到缓冲罐(2),然后输送至干燥机(3)进行预干燥,输送至筛选台(4)进行进一步除杂,除去金属、砂石、玻璃等硬物,除杂后输送至破碎机(5)破碎后,进入混料装置(8)与从催化剂仓(7)加入的催化剂粉末混匀,进入双螺旋挤压给料机(9),将原料挤压成圆棒,圆棒由的塑料切削装置(10)切成颗粒。
43.所述的解聚反应步骤,具体为,物料颗粒经双螺旋输送机构(11)搅拌并向前推进,物料在解聚窑(12)内从低温段向前推进至高温段,解聚反应与向前推进同时进行,推进至前端连接蒸馏塔(14)和固体沉淀容器(13)的位置前完成反应,转化为热油蒸汽,实现无氧、常压条件下连续加料和连续反应。
44.所述的蒸馏步骤,具体为,反应完成后得到的热油蒸汽不进行任何冷却进入蒸馏塔(14),蒸馏塔(14)的上、中、下三个液体出口分别输出的汽油、柴油、重油分别经冷却器(20)冷却后,分别进入汽油储油容器(21)、柴油储油容器(30)、重油储油容器(31),然后分别经汽油输出管路(22)、柴油输出管路(32)、重油输出管路(33)输出进行进一步处理;不能够冷却为液体油的气体经气体冷却器(15)和气体滤清器(16)处理后进入气体缓冲罐(17),过滤后经可燃气输出管路(18)输出,用于解聚窑(12)加热。
45.所述的催化剂回收步骤,具体为,残留固体在固体沉淀容器(13)中收集,然后经密封螺旋输送器(24)输送至催化剂再生罐(25),通入空气加热将焦炭消耗,得到再生催化剂与金属混合物,然后经振动筛(26)分离得到再生催化剂和金属,分别存放于再生催化剂容器(27)和固体残留物容器(28)。
46.所述的塑料切削装置(10)对物料进行切削在无氧环境下进行,切削后的物料颗粒
粒度为5-10cm;含水量小于5%。所述的双螺旋挤压给料机(9)对物料进行压缩,这种压缩过程可以使物料温度升高至近100℃。排出物料中残留的水、空气和物料中自带的氧气。
47.所述的氧化铝为α-al2o3。
48.所述的催化剂添加量为3%-8%。
49.所述的解聚反应步骤中,物料在解聚窑(12)内停留的时间为10-40min。所述的双螺旋输送机构(11)推进反应物向前运行,促使窑内产生的油蒸汽在形成后尽快从反应室排出,以避免进一步与碳氢化合物气体反应。
50.所述的解聚反应,初始反应前,开启旋转气闸阀(30),经氮气供应管路(29)通入氮气,反应开始后,停止氮气供应。
51.所述的原料由pe、hdpe、ldpe、pp和ps中的一种或2种以上组成。
52.所述的原料中掺杂的生物质废物或者含氧、含氯、含氟、含氮塑料塑料达到10%以上时,连通相应的管路通入氢气。以提高收率。原因在于生物质废物或者含氧、含氯、含氟、含氮塑料塑料中含有的氧、氯、氟、氮等元素会消耗氢元素,从而使反应出油率降低。
53.气体和油的清洁:使用的原料中可能含有氯-氮和含氟塑料(如pvc、pu或ptfe)以及含氮和含硫化合物(如nh3、so2和h2s)(如旧橡胶、生物质),因此需要进行气体清洁。nahco3或用于清洁气体的ca(oh)2溶液适合用作吸附剂。气体中的co2也可通过氢氧化钙吸收去除。
54.采用上述的方法进行废弃塑料的处理,具体如下:(1)加入主成分为pp、pe、的废旧塑料100kg,物料粒度为5-8cm,加入6kgα-al2o3,解聚窑的低温段加热温度为180-220℃,高温段加热温度为330-360℃,物料在解聚窑内停留的时间为30min;蒸馏塔收集得到的汽油,柴油,重油的总收率为92.4%。
55.(2)加入主成分为pp、pe、hdpe、pp的废旧塑料100kg,物料粒度为5-6cm,加入3kgα-al2o3,解聚窑的低温段加热温度为200-250℃,高温段加热温度为350-370℃,物料在解聚窑内停留的时间为10min;蒸馏塔收集得到的汽油,柴油,重油的总收率为90.1%。
56.(3)加入主成分为pp、ps的废旧塑料100kg,物料粒度为6-7cm,加入8kgα-al2o3,解聚窑的低温段加热温度为200-220℃,高温段加热温度为320-360℃,物料在解聚窑内停留的时间为15min;蒸馏塔收集得到的汽油,柴油,重油的总收率为93.2%。
57.(4)加入主成分为pp、ps的废旧塑料100kg,含有生物质8%,物料粒度为8-10cm,加入4kgα-al2o3,解聚窑的低温段加热温度为200-220℃,高温段加热温度为320-360℃,物料在解聚窑内停留的时间为40min;蒸馏塔收集得到的汽油,柴油,重油的总收率为89.7%。
58.(5)加入主成分为pe、ps的废旧塑料100kg,含有生物质12%,物料粒度为5-7cm,加入5kgα-al2o3,通入氢气反应,解聚窑的低温段加热温度为200-240℃,高温段加热温度为350-400℃,物料在解聚窑内停留的时间为25min;蒸馏塔收集得到的汽油,柴油,重油的总收率为92.6%。