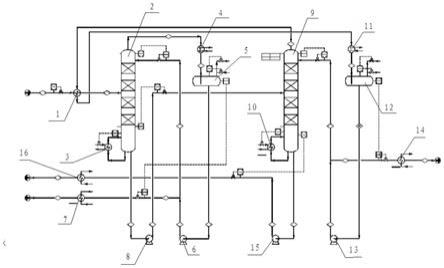
一种基于c5c6异构化装置的石脑油深加工方法及装置
技术领域
1.本发明公开涉及粗石脑油深加工技术领域,尤其涉及一种基于c5c6异构化装置的石脑油深加工方法及装置。
背景技术:
2.石油化工行业是我国国民经济的支柱产业之一,目前,石油资源约有一半依靠进口,产品的需求量也在逐年增长。随着我国经济的快速增长和世界经济环境的复苏,石油产品的需求量也逐年增长。
3.随着石油化工工业的蓬勃发展,许多有机化工原料可以在石油加工副产品中加工获得。其中石脑油切割产品是石油的主要分离产品之一,是重要的有机化工原料和工业生产的基础用油,与人们的日常生活密切相关,应用领域广泛,涉及到机械、冶金、电子、化工、医药、食品、农业、林业、纺织等国民经济的各种行业。随着国际社会对环境保护的重视以及人类健康的关注,我国逐步开发出了具有环保性能的各种特殊用途的油品,品种也不断的向专业化的方向发展。
4.石脑油经切割后的各种产品主要用途是作为生产乙烯和催化重整的原料、另外还作为汽油的调和组分和溶剂油的切割料。相对炼厂的车用无铅汽油来说,石脑油调和的汽油成本较低,因此许多炼化企业为增加成品油利润,会用石脑油和石化助剂调配车用无铅汽油。目前以中石油、中石化为主的几大炼厂仍是石脑油生产的主力,产量占七成以上。
5.综上,提供一种新的工艺方法生产加工石脑油是非常有意义的。
技术实现要素:
6.鉴于此,本发明公开提供了一种基于c5c6异构化装置的石脑油深加工方法及装置,在原有的c5c6异构化装置上进行改造,以提供一种高效、经济的石脑油深加工方法。
7.本发明提供的技术方案,具体为,一种基于c5c6异构化装置的石脑油深加工方法,包括:以加氢脱芳之后的石脑油为原料进行精脱硫,其中精脱硫后石脑油原料中h2s<5ppm;rsh<10ppm;采用多塔精馏精分方法精制脱硫后的石脑油原料,得到粗己烷、精制石脑油、重石脑油,其中粗己烷作为c5c6异构化工艺中的进料。
8.优选地,所述精脱硫具体采用碱洗-水洗-吸附-氧化法对原料石脑油进行脱硫。
9.优选地,所述加氢脱芳之后的石脑油为直流石脑油或加氢石脑油中的一种;硫含量:h2s<1000ppm;rsh<100ppm;溴指数:<3g/100g。
10.优选地,采用的脱硫剂为w702复合氧化物精脱硫剂和w201硫醇转化催化剂。
11.优选地,精脱硫中,硫醇转化塔氧气补入量:0.7-1.0m3/h;精脱硫塔直径2000mm,床层总高度5400mm,单层装填;w201硫醇转化塔直径2000mm,床层总高度5400mm,单层装填,w201硫醇转化催化剂装填量为18m3;w702复合氧化物精脱硫剂装填量为18m3。
12.优选地,所述多塔精馏精分方法利用石脑油中各组分的相对挥发度的不同,采用两塔分离,在分馏塔中,液体与再沸器产生的气体逆流接触,从而切割出不同馏分范围的产
品。
13.优选地,所述多塔精馏精分方法具体包括如下步骤:
14.1)原料储存罐中脱硫后的原料通过第一精馏塔原料预热器(1)中1.0mpa加热蒸汽加热,使原料温度达到100℃后,送入第一精馏塔(2)内进行精馏分离,轻组分自塔顶蒸出;
15.2)蒸出的轻组分由第一精馏塔冷凝器(4)冷凝后,自流进入第一精馏塔塔顶回流罐(5)中;通过第一精馏塔塔顶回流泵(6)采出后,一部分打回第一精馏塔(2)作为塔的回流,另一部分即为轻组分产品采出,经第一换热器(7)降温至40℃至轻组分储罐;
16.3)第一精馏塔(2)塔底油由第一精馏塔塔底泵(8)采出,直接送入第二精馏塔(9)进一步分离;
17.4)第一精馏塔(2)塔顶气相自塔顶蒸出,经第二精馏塔冷凝器(11)冷凝后,自流进入第二精馏塔塔顶回流罐(12)中;通过第二精馏塔塔顶回流泵(13)采出后,部分回流,部分作为溶剂油产品采出,经第二换热器(14)降温至40℃至产品储罐;
18.5)第二精馏塔(9)塔底采出的重组分产品,由第三精馏塔塔底泵(15)经重组分冷却器(16)冷却至40℃后,送至重组分储罐。
19.优选地,步骤1)中所述第一精馏塔(2)为微正压操作,塔顶操作压力为150kpa,第一精馏塔(2)塔底由第一精馏塔再沸器(3)提供热量,第一精馏塔再沸器(3)为立式热虹吸式再沸器,加热介质为250℃导热油,加热量由塔釜温度控制;
20.所述第二精馏塔(9)为微正压操作,塔顶操作压力为150kpa(a),塔底由第二精馏塔再沸器(10)提供热量,第二精馏塔再沸器(10)为立式热虹吸式再沸器,加热介质为250℃的导热油,加热量由塔釜温度控制。
21.另一方面,本发明还提供了一种基于c5c6异构化装置的石脑油深加工装置,包括脱硫装置、石脑油精馏装置;所述石脑油精馏装置包括两串联连接的第一精馏塔(2),第二精馏塔(9);所述第一精馏塔(2),第二精馏塔(9)的塔顶分别与第一精馏塔塔顶回流罐(5)及第二精馏塔塔顶回流罐(12)连通,通过所述第一精馏塔塔顶回流罐(5)及第二精馏塔塔顶回流罐(12)实现塔回流或组分收集。
22.优选地,所述脱硫装置包括依次连接的静态混合器、碱洗罐、碱液循环泵、水洗罐、脱硫塔及w201硫醇转化塔,所述脱硫塔中设有w702复合氧化物精脱硫剂床层;
23.所述碱液沉降罐与水分离器入口开孔位于设备底部1/3高度处;且二者均设液位计。
24.本发明的有益效果:
25.本发明提供的工艺方法,以粗石脑油为原料,原料来源充足可靠,工艺技术成熟、设备先进,经济效益显著,得到的产物粗己烷、精制石脑油、重石脑油,其中粗己烷作为异构化装置的进料,其余产品销往本地各调油生产商;生产得到的粗己烷、精制石脑油、重石脑油产品质量高,有利于实现生产的灵活性。
26.制备工艺中,合理利用了水资源,提高了水资源的有效利用率,减少原水用量和污水排放量,做到水资源循环利用,让有限的水资源发挥更大的作用,且设备布置合理装置区、储运罐区的布局与厂区的总体规划相协调。
附图说明
27.此处的附图被并入说明书中并构成本说明书的一部分,示出了符合本发明的实施例,并与说明书一起用于解释本发明的原理。
28.为了更清楚地说明本发明实施例或现有技术中的技术方案,下面将对实施例或现有技术描述中所需要使用的附图作简单地介绍,显而易见地,对于本领域普通技术人员而言,在不付出创造性劳动的前提下,还可以根据这些附图获得其他的附图。
29.图1为本发明公开实施例提供的一种基于c5c6异构化装置的石脑油深加工装置图。
具体实施方式
30.这里将详细地对示例性实施例进行说明,其示例表示在附图中。下面的描述涉及附图时,除非另有表示,不同附图中的相同数字表示相同或相似的要素。以下示例性实施例中所描述的实施方式并不代表与本发明相一致的所有实施方式。相反,它们仅是与如所附权利要求书中所详述的、本发明的一些方面相一致的系统的例子。
31.随着国际国内的炼油行业都朝着大型化发展,以降低单位加工成本,本实施方案在现有装置预处理单元的基础上进行改造,加工10万吨/年石脑油,将塔顶产品作为c5c6异构化装置的部分原料;
32.一种基于c5c6异构化装置的石脑油深加工方法,所述石脑油深加工方法是将粗石脑油进一步加工,分离出三种馏分的油品,分别为粗己烷、精制石脑油、重石脑油;
33.石脑油又名轻汽油,是一种无色透明液体,系石油馏分之一。石脑油由原油蒸馏或石油二次加工切取相应馏分而得。石脑油可分离出多种有机原料,主要用作重整和化工原料。其中,石蜡基石脑油主要用作烯烃原料,而重质石脑油则用作芳烃原料。
34.一种基于c5c6异构化装置的石脑油深加工方法,包括:以加氢脱芳之后的石脑油为原料进行精脱硫,其中精脱硫后石脑油原料中h2s<5ppm;rsh<10ppm,以粗石脑油为原料,石脑油作为原油炼制产品,含有一定量的硫化物。本实施方案中原料石脑油的硫含量≤500ppm,若直接进入生产装置,则会对生产过程及产品产生一定的影响,主要表现在对设备的腐蚀及对产品指标的影响等。因此,原料进入生产装置之前首先进行脱硫;脱硫后的原料对设备腐蚀较小,生产的各种产品指标合格。采用碱洗-水洗-吸附-氧化法对原料石脑油进行脱硫。
35.采用的脱硫剂为w702复合氧化物精脱硫剂和w201硫醇转化催化剂。
36.具体到脱硫工序中,以原料粗石脑油,其中原料只能是直流石脑油或加氢石脑油,不能是裂解油;硫含量:h2s<1000ppm;rsh<100ppm;溴指数:<3g/100g;精脱硫后原料中的h2s<5ppm;rsh<10ppm。
37.原料油中所含的h2s、rsh等活性硫化物严重腐蚀设备、管道,并有极其强烈的恶臭味,对产品的质量有较大的影响。由于原料油中h2s含量较高,先通过碱洗,添加200ppmw803高效脱硫催化剂脱除原料油中的大部分h2s,通过水洗塔分离出原料油中夹带碱液,再用w702复合氧化物精脱硫剂串w201硫醇转化催化剂脱硫除臭工艺,确保精脱硫后原料中的h2s<5ppm;rsh<10ppm。
38.w702复合氧化物精脱硫剂用于脱除原料油中的h2s、元素硫,其脱硫原理为:
39.mo+h2s==ms+h2o m代表金属
40.w201硫醇转化催化剂用于将石脑油中硫醇性硫转化成二烷基二硫,其脱硫原理为:
41.2rsh+o2==rssr+mo+h2o
42.原料油与碱液经静态混合器混合反应,经碱洗除去大部分硫化氢,进入碱洗罐,沉降分层,碱液经碱液循环泵循环使用,油品进入水洗罐,将油品夹带微量碱液洗净后进入脱硫塔,油品自下而上通过w702复合氧化物精脱硫剂床层,将残留的h2s和元素硫吸附脱除,然后与空气或氧气混合,自下而上进入w201硫醇转化塔,把rsh转化为高沸点的二烷基二硫,从而确保精脱硫后原料中的h2s<5ppm;rsh<10ppm。
43.碱液沉降罐与水分离器入口开孔位于设备底部1/3高度处;且二者均设液位计,以利于观察碱液液位。
44.硫醇转化塔氧气补入量:0.7-1.0m3/h
45.精脱硫塔直径2000mm,床层总高度5400mm,单层装填。
46.硫醇转化塔直径2000mm,床层总高度5400mm,单层装填。
47.催化剂装填量:w702复合氧化物精脱硫剂装填量为18m3,w201硫醇转化催化剂装填量为18m3。
48.本实施方案采用多塔精馏精分方法精制脱硫后的石脑油原料,得到粗己烷、精制石脑油、重石脑油,其中粗己烷作为c5c6异构化工艺中的进料。石脑油精制选用生产成本最低的石油蒸馏法,即采用多塔精馏精分工艺,利用石脑油中各组分的相对挥发度不同的特性,采用2塔分离,在分馏塔中,液体与再沸器产生的气体逆流接触,从而切割出不同馏分范围的产品。石脑油在装置内经2塔依次精馏后,被分为各种产品,即粗石脑油、精制石脑油、重石脑油。
49.上述多塔精馏精分方法具体包括如下步骤:
50.1)原料储存罐中脱硫后的原料通过第一精馏塔原料预热器1中1.0mpa加热蒸汽加热,使原料温度达到100℃后,送入第一精馏塔2内进行精馏分离,轻组分自塔顶蒸出;
51.2)蒸出的轻组分由第一精馏塔冷凝器4冷凝后,自流进入第一精馏塔塔顶回流罐5中;通过第一精馏塔塔顶回流泵6采出后,一部分打回第一精馏塔2作为塔的回流,另一部分即为轻组分产品采出,经第一换热器7降温至40℃至轻组分储罐;
52.3)第一精馏塔2塔底油由第一精馏塔塔底泵8采出,直接送入第二精馏塔9进一步分离;
53.4)第一精馏塔2塔顶气相自塔顶蒸出,经第二精馏塔冷凝器11冷凝后,自流进入第二精馏塔塔顶回流罐12中;通过第二精馏塔塔顶回流泵13采出后,部分回流,部分作为溶剂油产品采出,经第二换热器14降温至40℃至产品储罐;
54.5)第二精馏塔9塔底采出的重组分产品,由第三精馏塔塔底泵15经重组分冷却器16冷却至40℃后,送至重组分储罐。
55.步骤1)中第一精馏塔2为微正压操作,塔顶操作压力为150kpa,第一精馏塔2塔底由第一精馏塔再沸器3提供热量,第一精馏塔再沸器3为立式热虹吸式再沸器,加热介质为250℃导热油,加热量由塔釜温度控制;
56.第二精馏塔(9)为微正压操作,塔顶操作压力为150kpa(a),塔底由第二精馏塔再沸器10提供热量,第二精馏塔再沸器(10)为立式热虹吸式再沸器,加热介质为250℃的导热
油,加热量由塔釜温度控制。
57.经过上述工艺方法,年操作天数:333天/年,8000小时,得到粗己烷1.04万吨/年,精制石脑油8.4万吨/年,重石脑油0.56万吨/年;且其均符合如下标准:
58.表1精制石脑油性质
[0059][0060]
表2精制石脑油杂质含量要求
[0061][0062]
表3粗己烷产品指标
[0063][0064][0065]
表4重石脑油产品产品指标
[0066][0067]
表5产品含硫、含氮量
[0068]
产品含硫量含氮量
粗己烷≦100ppm≦2ppm精制石脑油≦100ppm≦2ppm重石脑油≦100ppm≦2ppm
[0069]
上述工艺方法中最后还包括油气回收系统,涉及的罐区工艺具体包括如下:
[0070]
油品卸车:原料石脑油卸车经过厂区原有石脑油卸车鹤位及卸车泵,输送到本项目新建石脑油原料储罐。
[0071]
输送:罐区的石脑油通过石脑油输送泵p401a/b升压送至生产装置区。
[0072]
油品装车:由装置区产生的成品油由各自的输送泵输送至罐区储罐中,再由各自的装车泵从罐中抽出,升压输送到汽车装车栈台,通过装油鹤管装车外运。
[0073]
倒罐:本罐区在管线设计上能实现油品的相互倒罐的功能,在储罐储量不满的前提下,可以将任何一个罐倒空,以满足储罐检修及事故处理的要求。
[0074]
自控仪表:储罐设置雷达液位指示仪表,并设置高、低液位报警,高高和低低液位联锁关阀、停泵,报警信号引到装置控制室。
[0075]
将得到的产品装车是油气的主要散发源。产品装车时,产品进入车载油罐中,油面不断升高,气体空间被压缩,油罐内部压力超过泄放压力,油气排出油罐。并且车载油罐内温度接近环境温度,在装车初期由于产品温差造成了一部分产品的气化也随产品装车的过程挥发出车载油罐。轻质油鹤位在发油的过程中会挥发出大量的油气,不仅对环境造成污染,不利于人体健康,极易产生爆炸和发生火灾事故,而且造成能源浪费。因为油气挥发的部分主要是轻烃组份,具有很高的回收价值,经济效益可观,应该加以回收再利用。
[0076]
本实施方案的油气回收系统采用“冷凝+吸附”的油气回收工艺。该工艺是将制冷和吸附相结合,先在冷凝单元中将油气逐级从常温冷却至-75℃(此处温度场可根据实际需要变更设定),使混合气体中的大部分油气直接液化回收,剩余极少量油气在吸附单元中通过特定吸附工艺和空气进行吸附分离。整机系统通过以上过程不断循环,从而达到油气连续冷却分凝回收,同时确保终端被处理油气达标排放。
[0077]
另一方面,本实施方案还提供了一种基于c5c6异构化装置的石脑油深加工装置,包括脱硫装置、石脑油精馏装置;所述石脑油精馏装置包括两串联连接的第一精馏塔2,第二精馏塔9;第一精馏塔2,第二精馏塔9的塔顶分别与第一精馏塔塔顶回流罐5及第二精馏塔塔顶回流罐12连通,通过第一精馏塔塔顶回流罐5及第二精馏塔塔顶回流罐12实现塔回流或组分收集。
[0078]
脱硫装置包括依次连接的静态混合器、碱洗罐、碱液循环泵、水洗罐、脱硫塔及w201硫醇转化塔,脱硫塔中设有w702复合氧化物精脱硫剂床层;
[0079]
第一精馏塔原料预热器1与第一精馏塔2连通,第一精馏塔2塔顶与第一精馏塔塔顶回流罐5连通,其连通管路上设有第一精馏塔冷凝器4;第一精馏塔2塔顶出口管路上设有塔顶回流泵6,出口管路分为两支路,一支路与第一精馏塔2塔顶连通,另一支路与轻组分储罐连通,所述另一支路上设有第一换热器7;第一精馏塔2与第二精馏塔9连通,连通管路上设有第一精馏塔塔底泵8;第二精馏塔9塔底设有第二精馏塔再沸器10;第二精馏塔9塔顶与第二精馏塔塔顶回流罐12连通,连通管路上设有第二精馏塔冷凝器11;第二精馏塔塔顶回流罐12的出口管路上设有第二精馏塔塔顶回流泵13,出口管路分为两支路,第一支路与第二精馏塔9塔顶连通,第二支路与储罐连通,第二支路上设有第二换热器14;
[0080]
本装置换热器采用固定管板式换热器,换热器结构简单,相同直径下面积较大,制造成本低,管程清洗方便,管程可以分成多程,壳程也可以分成双程,规格范围广。涉及的油品储罐6台,均为内浮顶储罐,浮盘采用全接液式钢制内浮盘,储罐材质为q235b、q345r。
[0081]
泵选用离心泵、屏蔽泵。本装置精馏工段包括两台精馏塔,脱硫工段包括4台脱硫塔。
[0082]
油气回收系统中采用3台装车鹤管,鹤管选用油气回收型装车专用鹤管。油品管线管道材质选用碳钢,并在适当位置设置扫线接头,轻油介质(闪点小于60℃)管线用氮气扫线及置换。可燃介质管线及设备设置集中高点放空管道,其高度满足安全、环保规范的要求。
[0083]
本实施方案中主要控制点集中在装置区、罐区及装车栈台部分,采用自动控制;罐区、装置区、装车栈台部分仪表远传信号传至控制室的dcs系统;可燃气体检测报警信号进入现有控制室内原有气体报警控制柜。工艺参数的信号报警、指示、联锁将在异构化dcs中实现。
[0084]
采用本安型现场仪表时采用隔离式安全栅构成本安回路,所有现场安装的电子式设备、控制阀防护等级一般不低于ip65。主要控制方案工艺装置内过程流量检测选用法兰取压标准节流装置。
[0085]
对于石脑油储罐,现场指示的液位计一般选用磁翻板液位计,侧侧安装;远传指示的液位计一般选用导波雷达液位计。对于装置区,现场、远传指示的液位计一般选用双法兰液位计。
[0086]
压力表一般采用“y”系列弹簧管压力表,震动较大的场合选用耐震压力表。
[0087]
一般选用气动薄膜调节阀作为仪表阀门,根据需要,可选用偏心调节阀和气动蝶阀等,气动调节阀一般附带电气阀门定位器或电气转换器。联锁阀一般选用两位式气动切断球阀,气动切断球阀一般附带电磁阀、限位开关等。
[0088]
变送器全部选用本安型电子式智能变送器,其输出信号为二线制4~20ma.dc。根据使用场合不同,变送器可选为压力变送器、差压变送器等。
[0089]
可燃气体检测报警器选用扩散式催化燃烧型报警器,带一体化声光报警装置,信号进入现有控制室的气体报警控制柜。
[0090]
就地指示的温度测量仪表选用双金属温度计;远传温度测量选用铂热电阻、铠装、绝缘型检测元件,其输出信号为三线制rtd信号。
[0091]
本实施方案提供的上述工艺方法艺上采取了加氢脱芳之后的石脑油作为生产原料,避免了增加加氢精制环节的预处理设施的技术投入和设备投资。通过优化装置设计,合理选择工艺参数,降低了原料和燃料消耗。优化换热流程,合理利用余热能位,显著提高了有效能效率。且上述工艺方法采用dcs控制系统,具有运转平稳,操作可靠的特点,并因而大大地提高了装置的可靠性。
[0092]
本领域技术人员在考虑说明书及实践这里公开的发明后,将容易想到本发明的其它实施方案。本技术旨在涵盖本发明的任何变型、用途或者适应性变化,这些变型、用途或者适应性变化遵循本发明的一般性原理并包括本发明未公开的本技术领域中的公知常识或惯用技术手段。说明书和实施例仅被视为示例性的,本发明的真正范围和精神由权利要求指出。
[0093]
应当理解的是,本发明并不局限于上面已经描述并在附图中示出的精确结构,并且可以在不脱离其范围进行各种修改和改变。本发明的范围仅由所附的权利要求来限制。