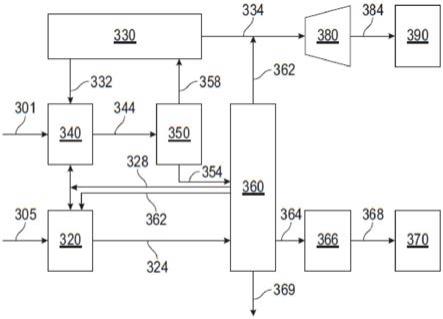
从废塑料热解回收轻质烯烃
[0001][0002]
相关申请的交叉引用
[0003]
本技术要求于2019年6月13日提交的ussn 62/861,166的优先权,其公开内容通过引用并入本文。
技术领域
[0004]
本技术提供了回收由塑料废料热解产生的轻质烯烃的系统和方法。
背景技术:
[0005]
塑料废料的再循环是越来越重要的主题。通常,塑料废料中的聚烯烃通过各种方法如热解或气化进行转化以产生能量。虽然这提供了第二次使用废塑料的途径,但最终从塑料废物产生能量的方法也导致塑料废物转化为co2。为了使该过程完全闭环,使得聚合物可以再循环以返回到相同的用途,这些热解和气化产物需要经过进一步的热解或转化过程以将它们返回到轻质烯烃单体。然后可以将烯烃单体再聚合回聚烯烃以用于相同的用途。遗憾的是,这种制备轻质烯烃的方法在能量使用、所需资本方面是高的,并且产生轻质烯烃单体的相对低产率。
[0006]
期望开发可允许具有改进烯烃产率和/或使用能量降低的聚烯烃用闭环再循环路径的系统和方法。特别地,期望开发可以允许从对应于聚合物混合物的塑料废物中单独回收各单体的系统和方法。
[0007]
美国专利us 5,326,919公开了从聚合物材料中回收单体的方法。通过在诸如砂之类的传热材料存在下在流通式反应器中以500℃/秒的速率加热聚合物来热解聚合物。旋风分离器用于将热解期间产生的流体产物与固体分离。然而,所得气相单体产物对应于烯烃的混合物,因此不适于合成新聚合物。
[0008]
美国专利us 9,212,318公开了用于热解塑料以形成烯烃和芳族物质的催化剂体系。催化剂体系包括fcc催化剂和zsm-5催化剂的组合。
技术实现要素:
[0009]
在各个方面,提供了热解混合聚烯烃进料的方法。该方法包括将包含聚烯烃混合物的原料暴露于聚烯烃热解条件以形成热解流出物。聚烯烃的混合物可包括两种或更多种类型的单体。聚烯烃热解条件可包括以100℃/秒或更高的速率加热原料以形成温度为500℃至900℃的经加热的反应混合物。聚烯烃热解条件可进一步包括将经加热的反应混合物冷却至小于500℃的温度以形成热解流出物,使得经加热的反应混合物在500℃或更高的温度下0.1秒至5.0秒。在热解之后,可以对热解流出物进行初始分离以至少形成热解产物馏分和包含固体颗粒的馏分。除了聚烯烃原料的热解之外,可以将单独的蒸汽裂化器进料通入蒸汽裂化反应器以形成蒸汽裂化器反应器流出物。可以将蒸汽裂化器反应器流出物的至少一部分通入初级分馏器以形成至少第一分馏器产物和一种或多种具有比第一分馏器产
物更高沸程的另外分馏器产物。可以将第一分馏器产物的至少一部分和热解产物馏分的至少一部分通入工艺气体压缩机以形成压缩的烯烃产物馏分。热解产物馏分的体积可以对应于至少一部分的第一分馏器产物和热解产物馏分的组合体积的0.1vol%至20vol%。该方法可以进一步包括从压缩的烯烃产物馏分至少分离包含乙烯的第一产物料流和包含丙烯的第二产物料流。
[0010]
在各个方面,提供了用于进行聚烯烃热解和蒸汽裂化的整合系统。该系统可以包括用于形成聚烯烃原料的聚烯烃处理段。该系统还可以包括热解反应器,该热解反应器包括热解入口和热解出口。热解入口可以与聚烯烃处理段流体连通。该系统还可以包括第一分离段,该第一分离段包括第一分离段入口、第一蒸气出口和第一固体出口。第一分离段入口可以与热解出口流体连通。该系统还可以包括与第一蒸气出口流体连通的热解骤冷段。该系统还可以包括第二分离段,第二分离段包括第二分离段入口、第二轻质物出口和第二重质物出口。第二分离段入口可以与热解骤冷段流体连通。该系统还可以包括蒸汽裂化反应器,该蒸汽裂化反应器包含反应器出口。该系统还可以包括初级分馏器,该初级分馏器包含一个或多个分馏器入口和多个分馏器出口。一个或多个分馏器入口可以与反应器出口和第二重质物出口流体连通。该系统可进一步包括至少一个骤冷塔,该骤冷塔包括一个或多个骤冷塔入口和一个或多个骤冷塔出口。至少一个骤冷塔入口可以与至少一个分馏器出口和第二重质物出口流体连通。该系统还可以包括工艺气体压缩机,该工艺气体压缩机包括压缩机入口和压缩机出口。压缩机入口可以与一个或多个骤冷塔出口流体连通。另外,所述系统可以包括多个烯烃分离段,该烯烃分离段至少包含乙烯出口和丙烯出口。多个烯烃分离段可以与压缩机出口流体连通。
附图说明
[0011]
图1显示了用于热解各种原料的工艺组列一部分的实例。
[0012]
图2显示了用于热解各种原料的工艺组列的另一部分。
[0013]
图3显示了用于各种原料热解的整合工艺组列的实例的概览。
[0014]
图4显示了用于各种原料热解的整合工艺组列的另一个实例的概览。
[0015]
发明详述
[0016]
本文的详细描述和权利要求书中的所有数值都被“约”或“大致”所指示的值修饰,并且考虑了本领域普通技术人员预期的实验误差和变化。
[0017]
在各个方面,提供了用于整合聚烯烃热解用反应器与蒸汽裂化器用流出物处理组列的系统和方法。聚烯烃可以对应于,例如塑料废物中的聚烯烃。将聚烯烃热解工艺与蒸汽裂化器处理组列整合可以将聚合物混合物转化为单体单元同时降低或最小化成本和/或设备占用空间。这可以允许聚烯烃以高产率直接转化为轻质烯烃单体同时由于与蒸汽裂化工艺组列的整合而显著降低资本和能源使用。可以部分地通过选择具有各种聚合物类型的适当混合物的进料和/或通过限制塑料废热解产物的体积相对于来自蒸汽裂化工艺组列中蒸汽裂化器的体积来实现整合。通过选择具有适当聚烯烃混合物的塑料废料和/或其他聚烯烃来源作为原料,所得聚烯烃热解产物可以在蒸汽裂化工艺组列中分离以产生用于各种聚合物级小烯烃产品的单独馏分。
[0018]
除了选择合适的进料封套之外,还可以通过包括一个或多个污染物去除段来实现
聚烯烃热解与蒸汽裂化器处理组列的整合。污染物去除段可以位于蒸汽裂化处理组列之前和/或蒸汽裂化处理组列之内。污染物去除段可以包括,但不限于捕集污染物的保护床和洗涤段,例如酸性和/或碱性洗涤段。例如,可以将保护床包括或添加到蒸汽裂化工艺组列中以处理可能存在于一些聚合物配制中的硅。
[0019]
聚烯烃聚合物通常用于各种工业和消费应用。在一些情况下,可以获得大量的对应于单一类型聚烯烃的聚合物/塑料废料,但更典型地聚烯烃废料对应于聚乙烯、聚丙烯和/或基于小烯烃的其它聚合物链的混合物。
[0020]
聚烯烃可以在热解条件下热解以形成包括烯烃单体的气相热解产物。尽管热解条件可以改变烯烃单体的选择性,但热解反应产生烯烃单体的混合物。这可以对应于包含c
2-c4烯烃的混合物,包含c
2-c3烯烃的混合物,或包含c2烯烃,c3烯烃,任选的c4烯烃,和一种或多种另外的烯烃(如c5或c6烯烃)的混合物。由于分离各种类型的烯烃单体的成本和复杂性,通常替代地使用塑料废物热解来形成液体燃料和/ 或产生热量以发电。然而,期望能够由塑料废料/聚烯烃热解形成聚合物级烯烃馏分,因为来自聚烯烃热解的乙烯和/或丙烯单体产率可以高于来自原油馏分的蒸汽裂化的乙烯和/或丙烯产率。举例来说,来自混合聚烯烃聚合物的热解的乙烯加丙烯单体的产率可为45wt%或更高,或50wt%或更高,如至多65wt%,相对于原料中聚烯烃的重量计。这与石脑油蒸汽裂化的烯烃产率大致相当。这是出乎意料的,因为来自蒸汽裂化的烯烃产率通常与用于蒸汽裂化的进料的沸程和/或分子量成反比,直到其中进料包含太多沸点高于真空瓦斯油范围的组分和/或包含太多具有低氢碳比的组分的点。例如,典型原油馏分的蒸汽裂化通常产生相对于进料重量约30wt%至40wt%的乙烯加丙烯产率。不受任何特定理论的束缚,相对于液体原油馏分的热解,来自聚烯烃聚合物的热解的乙烯和/或丙烯单体的产率增加可部分地归因于包含聚烯烃聚合物的进料中链烷烃化合物的量增加。
[0021]
在整合方法中,由蒸汽裂化工艺组列生产的乙烯和/或丙烯的至少一部分可以对应于由聚烯烃(例如来自塑料废料的聚烯烃)的热解产生的乙烯和/或丙烯。衍生自聚烯烃热解的乙烯和/或丙烯的量可以采用任何方便的方式测定,例如通过质量平衡。例如,可以进行第一处理运行,其中进入蒸汽裂化工艺组列的唯一流出物是来自相应蒸汽裂化反应器的流出物。然后可以进行第二处理运行,其中来自蒸汽裂化反应器的流出物保持恒定同时将来自热解反应器的另外流出物在合适的位置添加到蒸汽裂化工艺组列中。所获得的乙烯和/或丙烯产率的差异可对应于来自聚烯烃热解过程的额外产率。
[0022]
蒸汽裂化是一类热解方法,其可用于转化各种类型的石油进料和/ 或原油馏分以形成烯烃产物。传统上,蒸汽裂化不被认为是处理聚合物/塑料废料的合适方法。蒸汽裂化器包括对流段和辐射段。在蒸汽裂化期间,进料在对流段中预热。大部分裂化发生在辐射段中,其中温度为800℃或更高,但停留时间仅为几毫秒。为了减少或最小化裂化段中由于焦炭形成所引起的结垢,将蒸汽裂化器进料在进入辐射段之前蒸发。另外,为了促进进料在进入辐射段之前蒸发,将蒸汽裂化器的重质进料在暴露于热解条件之前分离以除去底部产物馏分。因此,蒸汽裂化器进料通常具有450℃或更低的t95沸点。相比之下,基于聚合物链长度,混合聚烯烃废料可对应于沸点远高于500℃的聚合物。即使这种聚烯烃没有通过分离除去,由于在对流区或辐射区中的条件下不能蒸发聚烯烃,这种聚烯烃也会导致蒸汽裂化器的快速结垢。
[0023]
在一些方面,可以对基本上由轻质(c
2-c4)烃组成的进料进行蒸汽裂化,例如乙烷蒸汽裂化。轻质烃的这种蒸汽裂化可以产生约70%的乙烯和/或丙烯产率。然而,提供足够量的轻质烃进料以提供用于工业规模聚合物生产的烯烃并不总是可行的。因此,蒸汽裂化也用于处理原油馏分和/或其它液体进料。
[0024]
在其中用于蒸汽裂化的进料对应于液体进料的这些方面中,通常进行蒸汽裂化器产物的分馏以分离出蒸汽裂化器产物的较高和较低价值部分。例如,除了轻质烯烃之外,来自液体进料(如原油馏分)的蒸汽裂化的产物可以包括蒸汽裂化器石脑油、蒸汽裂化器瓦斯油和蒸汽裂化器焦油。对于轻质烯烃,可以使用另外的分离段来分离轻质烯烃产物内的c2、c3和c4烯烃。在该讨论中,用于蒸汽裂化的液体进料是指在20℃和100kpa-a下至少部分为液体的进料。
[0025]
已经发现蒸汽裂化器处理组列的产物回收和分离段可用于处理来自塑料废料/聚烯烃热解过程的有限量热解流出物。通过将塑料废物/ 聚烯烃热解过程与蒸汽裂化过程整合,可以减少或最小化热解过程所需的额外分离设备的量,同时仍然允许将轻质烯烃单体分离成乙烯、丙烯和/或塑料废物混合物中存在的其它单体。
[0026]
在本说明书中,提及"c
x
"馏分、料流、部分、进料或其它量被定义为馏分(或其它量),其中50wt%或更多的馏分对应于具有"x"个碳数的烃。当指定范围时,例如"c
x-cy",50wt%或更多的馏分对应于具有在 "x"和"y"之间的碳数的烃。"c
x+
"(或"c
x-")的规格对应于其中50wt%或更多的馏分对应于具有指定碳数或更多(或指定碳数或更少)的烃的馏分。
[0027]
聚烯烃原料
[0028]
在各个方面,当将塑料废料/聚烯烃热解工艺与蒸汽裂化处理组列整合时,用于热解的原料可包括一种或多种聚烯烃聚合物或基本上由一种或多种聚烯烃聚合物组成。本技术所述的系统和方法可适用于处理对应于单一类型烯烃聚合物的塑料废料。然而,当塑料原料含有包括多种单体类型的聚合物时可以实现另外的益处。在其中原料基本上由聚烯烃聚合物组成的方面,原料可以包括聚烯烃聚合物和任何添加剂、改性剂、包装染料和/或通常在配制期间和/或之后添加到聚合物中的其它组分。原料可以进一步包括通常在聚合物废料中发现的任何组分。最后,原料可以进一步包括一种或多种溶剂或载体,使得热解过程的原料对应于聚烯烃聚合物的溶液或浆料。
[0029]
聚烯烃原料可包括聚乙烯和聚丙烯中的至少一种。聚乙烯可对应于任何合适类型的聚乙烯,例如高密度或低密度形式的聚乙烯。类似地,可以使用任何合适类型的聚丙烯。除了聚乙烯和/或聚丙烯之外,塑料原料可以任选地包括聚苯乙烯、聚氯乙烯、聚酰胺(例如尼龙)、聚对苯二甲酸乙二醇酯和乙烯-乙酸乙烯酯中的一种或多种。仍然其它的聚烯烃可对应于丁二烯、异戊二烯和异丁烯的聚合物(包括共聚物)。在一些方面,聚乙烯和聚丙烯可以作为乙烯和丙烯的共聚物存在于混合物中。更一般地,聚烯烃可以包括各种烯烃,例如乙烯、丙烯、丁烯、己烯和/或适合于聚合的任何其它烯烃的共聚物。
[0030]
在本技术中,除非另有说明,原料中聚烯烃聚合物的重量对应于相对于原料中全部聚合物含量的重量。包括在配制的聚合物中的任何添加剂/改性剂/其他组分都包括在该重量中。然而,本技术所述的重量百分比不包括所使用的任何溶剂或载体,使得原料对应于聚合物的溶液或浆料。为了与在蒸汽裂化工艺组列中引入塑料热解产物的相容性,原料可以包括有限量的不同于聚乙烯和/或聚丙烯的聚合物。在各个方面中,用于热解的塑料原料
可以包括55wt%至100wt%的聚乙烯、聚丙烯、乙烯和丙烯的共聚物、其它c
4-c6烯烃和/或二烯或其组合。在其中原料对应于95wt%或更多的衍生自乙烯和丙烯的聚合物的方面,原料可以优选包括10wt%或更多的乙烯单体和10wt%或更多的丙烯单体。
[0031]
在其中塑料原料包括少于100wt%的聚乙烯和/或聚丙烯的方面,塑料原料可以任选地包括0.1wt%或更多的其它聚合物。例如,在一些方面塑料原料可以包含0.1wt%至35wt%、或1.0wt%至35wt%、或0.1wt%至20wt%、或1.0wt%至20wt%、或10wt%至35wt%、或5wt%至20wt%的聚苯乙烯。在进料中包含聚苯乙烯可以增加芳族物质的产率,包括苯乙烯的产率。在一些方面,可以分离苯乙烯并用于生产聚苯乙烯。另外或替代地,苯乙烯可以与通过蒸汽裂化工艺产生的蒸汽裂化石脑油共混。应注意随着聚苯乙烯的量增加,乙烯和/或丙烯单体的产率可能降低。限制聚苯乙烯的量可以允许由塑料原料中的聚乙烯/聚丙烯以大于常规蒸汽裂化器产率的量生产乙烯和/或丙烯。另外,聚苯乙烯可以通过在较低温度,例如约450℃下处理以将聚苯乙烯转化为苯乙烯单体而潜在地再循环。因此,限制聚烯烃进料中的聚苯乙烯含量也可以是有益的,以便允许聚苯乙烯在更有利的条件下处理。
[0032]
在一些方面,塑料原料可任选地包括0.1wt%至10wt%,或0.1wt%至2.0wt%,或0.1wt%至1.0wt%的聚氯乙烯、聚偏二氯乙烯或其组合;和/或0.1wt%至1.0wt%的聚酰胺。聚氯乙烯含有大约65wt%的氯。因此,聚氯乙烯(和/或聚偏二氯乙烯)的热解可导致相对于聚氯乙烯的初始重量形成大量的盐酸。在允许热解产物进入蒸汽裂化工艺组列之前,可以使用保护床以有限量除去由聚氯乙烯和/或聚偏二氯乙烯的热解产生的盐酸。关于聚酰胺,热解导致no
x
的形成。有限量的no
x
可以通过蒸汽裂化工艺组列处理。在其它方面,通过在将聚烯烃热解产物与蒸汽裂化处理组列组合之前包括另外的除氯段,可以任选地在进料中包含0.1wt%至10wt%的聚氯乙烯和/或聚偏二氯乙烯。
[0033]
在一些方面,塑料原料可任选地包括0.1wt%至10wt%或1.0wt%至 10wt%的聚对苯二甲酸乙二醇酯。另外或替代地,塑料原料可以任选地包含0.1wt%至10wt%或1.0wt%至10wt%的乙烯-乙酸乙烯酯。聚对苯二甲酸乙二醇酯和乙烯-乙酸乙烯酯两者都可以降低乙烯和/或丙烯单体的产率,同时还可能增加co,co2或其组合的产量。限制聚对苯二甲酸乙二醇酯和/或乙烯-乙酸乙烯酯的量可以允许由塑料原料中的聚乙烯/聚丙烯以大于常规蒸汽裂化器产率的量生产乙烯和/或丙烯。
[0034]
在各个方面,可以制备聚烯烃以掺入塑料原料中。用于制备聚烯烃的方法可包括减小聚烯烃的粒度和将聚烯烃与溶剂或载体混合。
[0035]
在其中聚合物废料/聚烯烃至少部分地作为固体引入热解反应器的方面,具有小的粒度可以促进固体输送到热解反应器中。较小的粒度还可以潜在地有助于在热解的短停留时间条件下实现聚合物/聚烯烃的期望转化水平。为了制备用于热解的固体,可以将固体聚合物/ 聚烯烃压碎、切碎、研磨或以其他方式物理处理以将中值粒度减小至3.0cm或更小,或2.5cm或更小,或2.0cm或更小,或1.0cm或更小,例如低至0.01cm或可能更小。为了确定中值粒度,粒度定义为含有颗粒的最小边界球体的直径。
[0036]
另外或替代地,可以将溶剂或载体加入到原料中。为了引入热解反应器中,聚合物废料/聚烯烃适宜地可以为溶液、浆料或其它流体型相的形式。如果使用溶剂来至少部分地溶剂化聚烯烃,则可以使用任何方便的溶剂。合适溶剂的实例可包括(但不限于)宽范围的
石油或石化产品。例如,一些合适的溶剂包括原油、石脑油、煤油、柴油和瓦斯油。其他潜在的溶剂可以对应于环烷和/或芳族溶剂,例如甲苯、苯、甲基萘、环己烷、甲基环己烷和矿物油。仍然其它溶剂可对应于炼油厂馏分,例如来自蒸汽裂化器产物的瓦斯油馏分或石脑油馏分。如果使用载体,则载体可以对应于液相或气相载体,例如蒸汽。
[0037]
处理条件-聚烯烃热解
[0038]
在各个方面,首先通过将聚烯烃切割成小颗粒和/或通过将聚烯烃溶解在溶剂中来制备聚烯烃废料。然后可以将制备的原料输送到合适的反应器,例如流化床热裂化器中。然后将原料加热至500℃-900℃之间的温度持续反应时间以进行热解。温度可部分取决于所需产物。较高的温度可以增加对乙烯的选择性,而较低的温度可以增加对丙烯的选择性。可以限制其中将原料保持在或高于500℃的反应时间,以减少或最小化焦炭的形成。在一些方面,反应时间可对应于0.1秒至 6.0秒、或0.1秒至5.0秒、或0.1秒至1.0秒、或1.0秒至6.0秒、或1.0秒至5.0秒。在反应时间结束时,将热解的原料冷却至低于 500℃。
[0039]
在一些方面,还可以将稀释剂蒸汽进料到热解反应器中以控制烯烃分压并提高乙烯和丙烯产率。该蒸汽还用作流化气体。该蒸汽与原料的重量比可以在0.3:1至10:1之间。
[0040]
原料/热解产物的加热和冷却可以采用允许原料快速加热的任何方便的方式进行。在一些方面,将原料加热至热解温度的至少一部分可以采用100℃/秒或更高,或200℃/秒或更高,例如高达1000℃/秒或可能更快的加热速率进行。作为一个实例,在热解反应器对应于流化床的方面中,原料的加热可以通过将原料与加热的流化颗粒混合来进行。砂是用于流化床的合适类型的颗粒的实例。在操作期间,砂(或另一种类型的传热颗粒)可以进入再生器以烧掉焦炭并加热颗粒。必须在再生器中供应额外的热量以补偿该过程中的低焦炭形成。然后可以在进入反应器之前将加热的颗粒与原料混合。通过将传热颗粒加热至高于期望热解温度的温度,传热颗粒可提供实现热解温度所需热量的至少一部分。例如,可以将传热颗粒加热到比期望的热解温度高100℃或更多的温度。任选地,如果原料、砂和流化蒸汽不能提供足够的材料来形成流化床,则可以添加额外的流化气体,例如额外的氮气,但这也将导致在产物回收期间需要处理的气流体积的相应增加。在离开热解反应器之后,可以使用旋风分离器或另一种固体/蒸气分离器将传热颗粒与热解流出物的蒸气部分分离。这种分离器还可以除去热解后存在的任何其他固体。应注意使用旋风分离器的分离可导致蒸汽裂化器流出物中n2的增加,这可使产物回收更具挑战性。任选地,除了旋风分离器或其他初级固体/蒸气分离器之外,可以在从旋风分离器下游的位置处包括一个或多个过滤器,以允许去除夹带在气相中的细颗粒。
[0041]
聚烯烃热解的困难之一可能是处理热解过程中放出的氯,例如由聚氯乙烯和/或聚偏二氯乙烯热解得到的氯。在一些方面,可以通过在传热颗粒中包括钙源(例如包括氧化钙颗粒)来减轻热解反应器中氯的产生。在热解环境内,氧化钙可与热解期间产生的氯反应以形成氯化钙。然后可以将该氯化钙作为传热颗粒的吹扫流的一部分从系统中吹扫。可以引入新鲜传热颗粒的相应补充流以在聚烯烃热解段中保持所需量的传热颗粒。
[0042]
在除去固体之后,可以使用热交换器(或另一种适宜的方法)将产物冷却到300℃-400℃的温度以停止反应并回收热量。然后可以实施进一步骤冷,例如使用来自蒸汽裂化器的初级分馏器的液体料流的骤冷。骤冷料流的实例可以是高度芳族液体,例如由热解或蒸汽裂化产生的瓦斯油馏分(例如蒸汽裂化瓦斯油)。骤冷和/或其他冷却的组合可足以使产
物的c
5+
部分变成液体,以促进分离。
[0043]
然后可以将冷却的料流送至液气分离器以将c
5+
液体和任何骤冷油与热解产物的剩余c
4-部分分离。c
4-馏分还可以包括热解过程中产生的任何气相氧化物(例如co
x
、no
x
、so
x
)。可以将液体料流输送至蒸汽裂化器的初级分馏器。可以将c
4-气体料流送至二级骤冷塔。在骤冷塔中用水洗涤c
4-料流,然后干燥以除去水。然后使经洗涤和干燥的c
4-气体料流的剩余部分通过一个或多个保护床以去除污染物,然后将经洗涤和干燥的c
4-气体料流的剩余部分送至蒸汽裂化器工艺组列的工艺气体压缩机的入口。在蒸汽裂化器工艺组列中,将经洗涤和干燥的 c
4-气体料流的剩余部分与来自蒸汽裂化器的气体产物组合。在聚烯烃热解气相产物上使用第二骤冷塔可以减少或最小化通过保护床以除去氯的流动量。替代地,如果c
4-气体料流基本上不含污染物如氯(即污染物通常不存在于蒸汽裂化器产物中),则可以将c
4-气体料流送入作为蒸汽裂化器工艺组列一部分的骤冷塔,和/或可以将c
4-气体料流在另一个位置,如在初级分馏器或工艺气体压缩机中引入。
[0044]
在各个方面,c
4-气体料流的体积可对应于进入工艺气体压缩机和/ 或烯烃分离段的总流量的较小部分。例如,c
4-气体料流的体积可以对应于工艺气体压缩机中气体流的0.1vol%至20vol%,或0.1vol%至 10vol%,或1.0vol%至20vol%,或5.0vol%至20vol%,或1.0vol%至 10vol%,相对于c
4-气体料流和从蒸汽裂化器产物提供给工艺气体压缩机的气体流的合并体积。
[0045]
来自聚合物热解和蒸汽裂化的混合气体产物通过一系列制冷、压缩和蒸馏步骤进行处理而分离。在一些方面,这可以允许形成具有至少99.9%纯度的聚合物级乙烯、丙烯、异丁烯、丁烯和丁二烯。为了实现这种纯度,分离步骤可以包括将乙烷与乙烯分离、将丙烷与丙烯分离和将丁烷和/或丁烯与丁二烯分离的步骤。
[0046]
处理条件-蒸汽裂化
[0047]
蒸汽裂化是一类热解方法。在各个方面,用于蒸汽裂化的进料可以对应于任何类型的液体进料(即,在20℃和100kpa-a下为液体的进料,如本技术所定义)。合适反应器进料的实例可包括全原油和部分原油(whole and partial crudes)、石脑油沸腾进料、馏出物沸程进料、渣油沸程进料(常压或真空)或其组合。另外或替代地,合适的进料可以具有100℃或更高、或200℃或更高、或300℃或更高、或400℃或更高的t10蒸馏点,和/或合适的进料可以具有450℃或更低、或400℃或更低、或300℃或更低、或200℃或更低的t95蒸馏点。应注意可以在进行蒸汽裂化之前分馏用于蒸汽裂化的进料以除去底部产物部分使得进入反应器的进料具有450℃或更低的t95蒸馏点。进料的蒸馏沸程可以例如根据astm d2887测定。如果由于某种原因astm d2887不合适,则可以替代地使用astm d7169。尽管本发明的某些方面是参考特定进料,例如具有限定t95蒸馏点的进料公开的,但是本发明不限于此,并且该描述并不意味着排除在本发明更宽范围内的其他进料。
[0048]
蒸汽裂化装置通常包括用于生产蒸汽裂化流出物的炉设施和用于从蒸汽裂化流出物中除去多种产物和副产物,例如轻质烯烃和热解焦油的回收设施。炉设施通常包括多个蒸汽裂化炉。蒸汽裂化炉通常包括两个主要区段:对流段和辐射段,辐射段通常包含燃烧器。来自辐射段的烟道气从辐射段输送到对流段。烟道气流过对流段和然后可以任选地进行处理以除去燃烧副产物,例如no
x
。将烃引入位于对流段中的管状盘管(对流盘管)中。蒸汽也被引入盘管中,在盘管中蒸汽与烃组合以产生蒸汽裂化进料。通过烟道气的间接加热
和通过蒸汽的直接加热的组合导致蒸汽裂化进料中至少一部分烃组分的蒸发。然后将含有蒸发烃组分的蒸汽裂化进料从对流盘管转移到位于辐射段中的管状辐射管。在辐射管中蒸汽裂化进料的间接加热导致蒸汽裂化进料中至少一部分烃组分的裂化。辐射段中的蒸汽裂化条件可以包括,例如以下中的一种或多种:(i)760℃至880℃范围内的温度,(ii)1.0至5.0 巴(绝对压力)范围内的压力,或(iii)0.10至0.5秒范围内的裂化停留时间。
[0049]
将蒸汽裂化流出物从辐射段中导出并通常用水或骤冷油骤冷。将骤冷的蒸汽裂化流出物从炉设施引导至回收设施,用于分离和回收蒸汽裂化进料的反应和未反应组分。回收设施通常包括至少一个分离段,例如用于从骤冷流出物中分离轻质烯烃、蒸汽裂化器石脑油、蒸汽裂化器瓦斯油、蒸汽裂化器焦油、水、轻质饱和烃和分子氢中的一种或多种。
[0050]
蒸汽裂化进料通常包含烃和蒸汽,例如10.0wt%或更多的烃,基于蒸汽裂化进料的重量,或25.0wt%或更多,或50.0wt%或更多,或 65wt%或更多,和可能高达80.0wt%或可能仍然更高。尽管烃可包含一种或多种轻质烃例如甲烷、乙烷、丙烷、丁烷等,但包含大量的较高分子量烃可能是特别有利的。使用包含较高分子量烃的进料可以降低进料成本,但也会增加蒸汽裂化流出物中蒸汽裂化器焦油的量。在一些方面,合适的蒸汽裂化进料可包含10wt%或更多,或25.0wt%或更多,或50.0wt%或更多(基于蒸汽裂化进料的重量)的在环境温度和大气压下处于液相和/或固相的烃化合物,例如直至基本上整个进料对应于重质烃。
[0051]
蒸汽裂化进料的烃部分可以包括10.0wt%或更多,或50.0wt%或更多,或90.0wt%或更多(基于烃的重量)的石脑油、瓦斯油、减压瓦斯油、蜡质渣油、常压渣油、渣油混合物或原油中的一种或多种,例如直到基本上整个进料。这样的组分可以包括含有0.1wt%或更多沥青质的那些。当烃包括原油和/或其一种或多种馏分时,将原油在包含在蒸汽裂化进料中之前任选地脱盐。可以通过将常压管式蒸馏器("aps") 底部产物与原油分离然后对aps底部产物进行真空管式蒸馏器("vps") 处理来生产原油馏分。可以在辐射段的上游使用一个或多个气-液分离器,例如用于分离和导出原油或原油组分中任何非挥发物的一部分。在某些方面,通过在对流段中预热原油或其馏分(和任选地通过添加稀释蒸汽),分离包含非挥发物的底部产物蒸汽,和然后将主要为蒸气的顶部料流作为进料引导到辐射段而将这样的分离段与蒸汽裂化器整合。
[0052]
合适的原油可以包括原始原油,例如富含多环芳族物质的那些。例如,蒸汽裂化进料的烃可以包含90.0wt%或更多的一种或多种原油和/或一种或多种原油馏分,例如从常压蒸馏和/或减压蒸馏获得的那些;蜡状渣油;常压渣油;被原油污染的石脑油;各种渣油混合物;和蒸汽裂化器焦油。
[0053]
污染物去除段
[0054]
可任选地通过添加污染物去除段来促进将来自聚烯烃热解的部分流出物添加到蒸汽裂化处理组列中。在一些方面,可以在将聚烯烃热解流出物与蒸汽裂化处理组列组合之前的位置处将一个或多个污染物去除段并入反应系统中。另外或替代地,可以从其中将聚烯烃热解流出物与蒸汽裂化流出物组合处将一个或多个污染物去除段并入蒸汽裂化工艺组列。保护床(或保护床组)是污染物去除段类型的实例。任选地在酸性或碱性条件下的水洗涤是污染物去除段类型的另一个实例。
[0055]
聚烯烃可包括多种污染物,该污染物的存在量大于用作蒸汽裂化进料的原油馏
分。这可以包括在典型的原油馏分中基本上不存在的污染物例如氯。这还可以包括污染物,例如氧和氮,其可以采用增多的量存在于聚烯烃进料中。一些污染物可对应于下面的聚烯烃的组分,例如聚氯乙烯中的氯或聚胺中的氮。由于在制备配制的聚合物时包括的添加剂和/或由于包装、粘合剂和在配制后与聚烯烃整合的其它化合物,可能存在其它污染物。此类添加剂、包装、粘合剂和/或其它化合物可包括额外污染物例如氯、汞和/或硅。
[0056]
在将热解流出物与蒸汽裂化器处理组列结合之前和/或在工艺气体压缩机之后,一种类型的污染物去除可以是使用水洗涤来去除氯。任选地,水洗涤可以对应于胺洗涤和/或碱洗涤。使用胺洗涤和/或碱洗涤可有助于去除氯和其它污染物,如co2。进行胺洗涤的另一种选择可以是在用于热解和/或蒸汽裂化器流出物的初始骤冷的骤冷油中包括胺。这可以允许随后的水洗涤以除去氯。
[0057]
基于骤冷塔内的ph控制,可以实现另一种形式的污染物去除。基于用于ph控制的添加剂,热解流出物中(和/或蒸汽裂化器流出物中) 任何nh3的至少一部分可以转化为氨盐。然后可以将这些盐保留在骤冷水中和/或通过单独的水洗涤除去。
[0058]
另外或替代地,可以包括另外的保护床以除去cl和/或hcl。在其中聚烯烃进料包含2.0wt%或更少的聚氯乙烯和/或聚偏二氯乙烯的方面中,可以在补充骤冷塔之后包括用于除去氯化合物的保护床。用于除氯的合适保护床颗粒的实例包括氧化钙、氧化镁、氧化锌及其组合。在进料中存在较高氯量,例如至多10wt%的聚氯乙烯和/或聚偏二氯乙烯的方面,可以在热解之前进行进料的额外处理以除去氯。例如,在热解之前,可以将这种聚烯烃进料加热至350℃-450℃的温度以将氯转化为气相化合物。然后可以使加热的进料通过保护床(例如氧化钙保护床)和/或通过水洗涤、碱洗涤器或胺洗涤器以在进入热解反应器之前从进料中除去大部分氯。
[0059]
仍然另一种类型的保护床可以对应于用于除去氨的保护床。除了含氮聚合物如聚胺之外,各种类型的聚合物添加剂可包括氮。在热解环境中,该氮的一部分可以转化为氨。各种类型的吸附剂可用于除去氨,例如分子筛基吸附剂。另一种选择可以是具有补充骤冷塔,使得可以在将热解流出物与蒸汽裂化流出物组合之前使用水洗涤除去氨。通过将氮吸附剂(例如适合于氨吸附的分子筛)添加到位于工艺气体压缩机下游的一个或多个工艺气体干燥器中,可以进行更进一步的氮去除。
[0060]
除了在将热解流出物与蒸汽裂化器产物料流出物结合之前使用的上述污染物去除段之外,可以包括用于处理结合的流出物的其它污染物去除段。例如,硅通常存在于聚合物配制中使用的添加剂中。热解后,通常将硅分离成液体产物。可以将硅捕集器添加到蒸汽裂化工艺组列中以在液体蒸汽裂化器流出物离开骤冷塔之后从其中除去硅。
[0061]
固定床汞捕集器也可以包括在蒸汽裂化工艺组列中。热解反应环境中存在的升高的温度可以将聚烯烃进料中存在的任何汞转化为元素汞。然后可以使用保护床除去这种元素汞。应注意适合于汞去除的一些保护床也可适合于硅去除。这种保护床的实例包括包含任选负载在表面上耐火氧化物与具有过渡金属的保护床,例如用于脱金属催化剂或废加氢处理催化剂的氧化物和金属。另外或替代地,单独的保护床可用于硅和汞去除,或者用于硅去除和汞去除的单独吸附剂可包括在单个保护床中。合适汞吸附剂和硅吸附剂的实例可包括,但不限于适于吸附汞和/或硅的分子筛。
[0062]
其它污染物去除段可以对应于蒸汽裂化工艺组列中可能已经存在的污染物去除。
例如,任何氮氧化物可作为盐积聚在冷箱中,从而从工艺气体中除去氮氧化物。可以定期洗涤冷箱以除去由氮氧化物形成的累积盐。可以使用胺或碱洗涤除去co2。co可以通过co在下游位置的甲烷化除去。还可以包括另外的氨和/或氧去除段。
[0063]
配置实施例
[0064]
图3显示了包括蒸汽裂化工艺组列和热解反应器两者的可能整合系统的概览。在图3所示的配置中,提供补充骤冷塔以减少或最小化通常不存在于蒸汽裂化工艺组列中的污染物的引入。在图3中,将用于蒸汽裂化的进料305与蒸汽328一起引入蒸汽裂化段320以产生蒸汽裂化器流出物324。蒸汽裂化段320包括蒸汽裂化炉、初始进料分离器和用于冷却蒸汽裂化器流出物324的一个或多个骤冷冷却器。骤冷冷却器可以使用骤冷油362作为骤冷介质。图3显示了骤冷油362 返回到蒸汽裂化段320中的骤冷冷却器。任选但优选地,骤冷油362 也可以返回到聚烯烃处理段340中的骤冷冷却器(未示出)。蒸汽裂化器流出物324可以进入初级分馏器和骤冷塔段360。
[0065]
图3还示出了将混合的聚烯烃进料301送入聚烯烃处理段340。除了热解反应器之外,聚烯烃处理段340可以包括聚烯烃进料所需的任何预处理,例如将进料溶解在溶剂中或切碎进料以形成所需尺寸的颗粒。聚烯烃处理段340还可以包括用于从蒸气产物中分离砂和/或催化剂细粉的气固分离段(例如旋风分离器)、再生器和用于冷却所得热解流出物的骤冷段。可以将所得热解流出物344送入蒸气液体分离器 350。液体部分354可以进入初级分馏器和骤冷塔段360。任选地,液体部分354的至少一部分可以替代地返回(未示出)到蒸汽裂化段320,以进一步提高c2和/或c3烯烃的产率。蒸气部分358可以进入污染物去除段330。污染物去除段330可以包括例如用于除氯的水洗涤和用于冷却蒸气部分358的补充骤冷塔。另外或替代地,可以基于控制骤冷塔中使用的水的ph来实现氯去除(例如hcl去除)。蒸汽332也可以通过热交换产生并用作聚烯烃处理段340的输入。然后可以将所得的骤冷流出物334与来自初级分馏器和骤冷塔360的蒸气馏分组合,然后通入工艺气体压缩机380。然后可以将压缩的蒸气产物384送入产物回收段390以进一步加工和/或分离各种所需的烯烃单体。
[0066]
在图3所示的实施例中,初级分馏器和骤冷塔360还可产生焦油或底部产物馏分369、可再循环用作骤冷油的瓦斯油馏分362和石脑油沸程馏分364。石脑油沸程馏分可以任选地通过污染物去除段366 以形成污染物减少的馏分368。污染物去除段366可以包括例如硅捕集器。然后可以使污染物减少的馏分368经历进一步加工和/或分离 370以回收所需产物,例如石脑油产物和/或苯产物。
[0067]
图4显示了用于将聚烯烃热解与蒸汽裂化整合的配置的另一个概览实例。在图4中,不包括补充骤冷塔,而是使用污染物去除段430 来处理热解流出物344。这可以允许改性的热解流出物434与蒸汽裂化流出物324一起进入初级分馏器和骤冷塔段460以进行分离和骤冷。由初级分馏器和骤冷塔段460产生的骤冷油462和蒸汽424可以再循环到蒸汽裂化段320和聚烯烃处理段340两者。
[0068]
图1和2显示了将聚烯烃热解与蒸汽裂化工艺组列整合的配置的其它细节。在图1中,用于蒸汽裂化的进料105进入蒸汽裂化反应器 110。在图1所示的实例中,已经进行了任何任选高分子量馏分从进料 105的去除。任选地,进料105可以在进入蒸汽裂化反应器110之前与蒸汽102组合。可以操作蒸汽裂化反应器110以产生较低分子量烃,例如c
2-c4烯烃。在
这种蒸汽裂化条件下,蒸汽裂化反应器还可以产生各种馏分,例如蒸汽裂化石脑油、蒸汽裂化器瓦斯油和蒸汽裂化器焦油。
[0069]
然后可以将来自蒸汽裂化反应器110的蒸汽裂化器流出物115通入,例如骤冷段120其中将蒸汽裂化器流出物115间接冷却和/或与水或骤冷油(例如任选的骤冷油157)混合以冷却流出物。骤冷油可以对应于例如来自初级分馏器140的馏分,例如蒸汽裂化器瓦斯油馏分或底部产物馏分,这取决于配置。然后可以将骤冷流出物125通入初级分馏器140。任选地,骤冷流出物可以在进入初级分馏器140之前通过焦油分出罐或其它分离器(未示出)以除去蒸汽裂化器焦油。
[0070]
在图1所示的实施例中,初级分馏器140可以产生底部产物 159(如蒸汽裂化器焦油)、一种或多种中间产物155(如骤冷油和/或蒸汽裂化器瓦斯油)和包括气相组分(包括烯烃单体)和蒸汽裂化器石脑油的顶部产物151。中间产物155的一部分可以用作骤冷油。顶部产物151可以进一步处理,如图2所示。
[0071]
第二原料101可以对应于包括聚烯烃的原料,例如包括塑料废料的原料。原料101可以进入制备段150。在制备段150中,原料可经物理处理以减小聚烯烃的粒度,与溶剂或载剂混合,或以其它方式加工以产生可引入热解反应器160中的制备料流155。任选地,制备料流155可以在进入热解反应器160之前与蒸汽152组合。在一些方面,蒸汽152可以对应于由冷凝水通过在反应器组列内其他位置处的热交换产生的蒸汽。任选地,制备料流155可以与从再生器(未示出)返回到反应器160的传热颗粒的加热的循环料流(未示出)组合。在聚烯烃原料的热解之后,热解流出物165可以进入分离段170以将固体172 与剩余产物175分离。这种分离器可以对应于例如旋风分离器。分离段170还可以包括一个或多个任选的过滤器,用于去除在旋风分离器或其他主分离器之后保留在蒸气中的细颗粒。任选地,代替在分离段 170中具有一个或多个过滤器和/或除了在分离段170中具有一个或多个过滤器之外,这样的过滤器可以位于一个或多个其他段的下游。然后可以将剩余的产物175骤冷或冷却180,任选地使用来自分馏器140 的骤冷油158。冷却180可足以允许对冷却的剩余产物185进行气液分离190。气液分离190可以例如将c
5+
料流192和c
4-产物料流195与冷却的剩余产物185分离。c
5+
料流可以进入分馏器140。可以将c
4-产物料流195送入蒸汽裂化器处理组列,例如通过将料流195送入图2 中的骤冷塔211,或者可以将c
4-产物料流195在送入蒸汽裂化器工艺组列之前在次级骤冷塔130中骤冷。在次级骤冷塔130中,可以从剩余的c
4-产物135中除去蒸汽133。
[0072]
图1中的连通性表示各种元件之间的流体连通。流体连通可包括直接流体连通和间接流体连通。在图1中,热解反应器110显示为与骤冷段120直接流体连通。热解反应器110显示为经由骤冷段120与初级分馏器140间接流体连通。
[0073]
图2显示了处理烯烃单体分离的蒸汽裂化工艺组列的一部分。可以将来自图1的馏分151和c
4-馏分135送入骤冷塔211。这可以除去水219同时形成石脑油馏分218和c
4-馏分215。c
4-馏分135可以例如与c
4-馏分215组合。然后可以将石脑油馏分218送入加氢处理器291 和/或另一类型的硅去除段以形成石脑油产物295。c
4-馏分215可以在工艺气体压缩机221中压缩。在使用单独骤冷塔的任选方面,来自单独骤冷塔的顶部馏分可以在工艺气体压缩机221的一个段之前和/或之内组合。
[0074]
在图2所示的实施例中,在压缩之后,压缩料流225可以通过洗涤段271,例如水洗
涤、碱洗涤或胺洗涤,以除去co2、hcl和/或nh3。然后可以将洗涤段流出物275通入工艺气体干燥器231。工艺气体干燥器231可以任选地但优选地包括污染物去除段。例如,工艺气体干燥器231可以包括分子筛或可以用作汞捕集器的另一种类型的结构。另外或替代地,工艺气体干燥器231可以包括一个或多个氨去除床。
[0075]
然后可以分离来自工艺气体干燥器/污染物去除231的流出物235 以形成含有组分单体的馏分。在图2所示的实例中,该过程可以通过将流出物235通入脱丙烷器241来开始。脱丙烷器241可以形成c
3+
产物249和c
2-产物245。c
3+
产物249可以经历进一步分离以允许回收 c3烯烃和c4产物。c
2-产物245可以任选地进入乙炔转化段281。在任选的乙炔转化之后,乙炔转化产物283可以进入脱甲烷器段285以将 co转化为ch4。脱甲烷器段285还可以包括用于除去包含ch4、co、no
x
和h2的料流289的分离器。然后可以将包含c2组分的剩余料流287送入冷箱252。冷箱252可促进在c2烯烃265与c2链烷烃269的分离261 之前额外除去氮氧化物化合物。在维护情况期间,在冷箱252中累积的任何氮氧化物化合物可以从系统中洗出。应注意冷箱252在图2中显示为在脱甲烷器段285和分离段261之间。在各个方面,冷箱252 可以对应于用于在蒸馏工艺流程中的各个位置处产物蒸馏用于急冷的多个段(未示出)。
[0076]
附加实施方案
[0077]
实施方案1.一种用于热解混合聚烯烃进料的方法,包括:将包含聚烯烃混合物的原料暴露于聚烯烃热解条件以形成热解流出物,所述聚烯烃混合物包含两种或更多种类型的单体,所述聚烯烃热解条件包括:以100℃/秒或更高的速率加热所述原料以形成具有500℃至900℃的温度的经加热的反应混合物,和将所述经加热的反应混合物冷却至小于500℃的温度以形成所述热解流出物,所述经加热的反应混合物在500℃或更高的温度下持续0.1秒至5.0秒;对热解流出物进行初始分离以至少形成热解产物馏分和包含固体颗粒的馏分;对蒸汽裂化器进料进行蒸汽裂化以形成蒸汽裂化器反应器流出物;将所述蒸汽裂化器反应器流出物的至少一部分通入初级分馏器中以至少形成第一分馏器产物和一种或多种具有比所述第一分馏器产物更高沸程的另外分馏器产物;将所述第一分馏器产物的至少一部分和所述热解产物馏分的至少一部分通入工艺气体压缩机中以形成压缩的烯烃产物馏分,所述热解产物馏分的体积占至少一部分的第一分馏器产物和热解产物馏分的组合体积的0.1vol%至20vol%;和从所述压缩的烯烃产物馏分中至少分离包含乙烯的第一产物料流和包含丙烯的第二产物料流,所述第一产物料流任选地包含乙烯,乙烯衍生自将包含聚烯烃混合物的原料暴露于聚烯烃热解条件,所述第二产物料流任选地包含丙烯,丙烯衍生自将包含聚烯烃混合物的原料暴露于聚烯烃热解条件。
[0078]
实施方案2.根据实施方案1所述的方法,其中原料包含0.1wt%或更多的聚氯乙烯、聚偏二氯乙烯、聚酰胺、聚苯乙烯、聚对苯二甲酸乙二醇酯、乙烯-乙酸乙烯酯或其组合,所述原料任选地包含0.1wt%至35wt%的聚苯乙烯。
[0079]
实施方案3.上述实施方案任一项所述的方法,i)其中所述原料包含0.1wt%至10wt%(或0.1wt%至2.0wt%)聚氯乙烯、聚偏二氯乙烯或其组合;ii)其中所述原料包含0.1wt%至1.0wt%的聚酰胺;或iii)该i) 和ii)的组合,所述方法任选地还包括:分离所述热解产物馏分以形成较低沸点馏分和较高沸点馏分;和将所述较低沸点馏分送入污染物去除段以形成所述热解产物馏分的至少一部分,所述热解产物馏分的至少一部分包含比所述
较低沸点馏分更低的氯含量。
[0080]
实施方案4.上述实施方案任一项的方法,其中原料包含0.1wt%至10wt%的乙烯-乙酸乙烯酯,或其中所述原料包含0.1wt%至10wt%的聚对苯二甲酸乙二醇酯,或其组合。
[0081]
实施方案5.上述实施方案任一项的方法,其中一种或多种另外分馏器产物包含石脑油沸程产物,所述方法进一步包括:将至少一部分石脑油沸程产物送入硅去除段以形成改性石脑油沸程产物。
[0082]
实施方案6.上述实施方案中任一项的方法,其中a)经加热的反应混合物还包含传热颗粒,所述传热颗粒任选地包含氧化钙,b)经加热的反应混合物还包含10wt%或更多的蒸汽,或c)该a)和b)的组合。
[0083]
实施方案7.上述实施方案任一项的方法,其中至少一部分的第一分馏器产物和热解产物馏分在进入产物气体压缩机之前在骤冷塔中骤冷;或者其中至少一部分的第一分馏器产物和热解产物馏分在进入所述产物气体压缩机之前在单独的骤冷塔中骤冷。
[0084]
实施方案8.上述实施方案中任一项的方法,还包括将热解流出物和热解产物馏分中的至少一种与骤冷油混合。
[0085]
实施方案9.上述实施方案任一项的方法,其中一种或多种另外分馏器产物包含底部产物馏分、焦油馏分、瓦斯油馏分或其组合,骤冷油任选地包含瓦斯油馏分的至少一部分。
[0086]
实施方案10.上述实施方案中任一项的方法,所述方法还包括将压缩的烯烃产物馏分暴露于水洗涤、碱洗涤、胺洗涤或其组合,以形成经洗涤的压缩的烯烃产物馏分,并使经洗涤的压缩的烯烃产物馏分进入污染物去除段以形成污染物减少的产物馏分,其中从压缩的烯烃产物馏分中至少分离包含乙烯的第一产物料流和包含丙烯的第二产物料流包括从所述污染物减少的产物馏分中分离所述至少第一产物料流和第二产物料流。
[0087]
实施方案11.上述实施方案中任一项的方法,a)进一步包括物理处理聚合物进料以形成所述原料,所述聚烯烃混合物包含具有3.0mm 或更小的中值粒度的颗粒;b)进一步包括通过将聚合物进料与溶剂组合形成所述原料,所述聚烯烃混合物至少部分地被所述溶剂所溶剂化;或c)该a)和b)的组合。
[0088]
实施方案12.一种用于进行聚烯烃热解和蒸汽裂化的整合系统,包括:用于形成聚烯烃原料的聚烯烃处理段;热解反应器,其包括热解入口和热解出口,所述热解入口与所述聚烯烃处理段流体连通;第一分离段,所述第一分离段包括第一分离段入口、第一蒸气出口和第一固体出口,所述第一分离段入口与所述热解出口流体连通;热解骤冷段,所述热解骤冷段与所述第一蒸气出口流体连通;第二分离段,所述第二分离段包括第二分离段入口、第二轻质物出口和第二重质物出口,所述第二分离段入口与所述热解骤冷段流体连通;蒸汽裂化反应器,其包括反应器出口;初级分馏器,其包含一个或多个分馏器入口和多个分馏器出口,所述一个或多个分馏器入口与所述反应器出口和所述第二重质物出口流体连通;至少一个骤冷塔,其包含一个或多个骤冷塔入口和一个或多个骤冷塔出口,所述至少一个骤冷塔入口与至少一个分馏器出口和第二重质物出口流体连通;工艺气体压缩机,其包括压缩机入口和压缩机出口,所述压缩机入口与所述一个或多个骤冷塔出口流体连通;和至少包含乙烯出口和丙烯出口的多个烯烃分离段,所述多个烯烃分离段与压缩机出口流体连通。
[0089]
实施方案13.根据实施方案12所述的系统,其中至少一个骤冷塔包括与所述至少一个分馏器出口和所述第二重质物出口流体连通的共用骤冷塔;或者其中所述系统还包含与所述第二轻质物出口流体连通的补充骤冷塔,其中工艺气体压缩机经由所述补充骤冷塔与所述第二轻质物出口流体连通,并且其中所述工艺气体压缩机的压缩机出口经由一个或多个污染物去除段与所述多个烯烃分离段流体连通。
[0090]
实施方案14.根据实施方案12或13所述的系统,其中系统还包括热解再生器,所述热解反应器还包括传热颗粒,所述热解反应器和所述再生器流体连通以传递所述传热颗粒。
[0091]
实施方案15.根据实施方案12至14中任一项所述的系统,所述系统还包括a)与所述第二重质物出口流体连通的硅去除段;b)与所述多个分馏器出口中至少一个分馏器出口流体连通的硅去除段;c)与所述压缩机出口流体连通的汞去除段,所述多个烯烃分离段经由所述汞去除段与所述压缩机出口流体连通;或c)该a)、b和c)中两种或更多种的组合。
[0092]
补充实施方案a.实施方案1-11任一项的方法,其中以200℃/秒或更高的速率加热原料。
[0093]
补充实施方案b.实施方案1-11任一项的方法,其中c2产物料流包含90wt%或更多的乙烯,或其中c3产物料流包含90wt%或更多的丙烯,或其组合。
[0094]
补充实施方案c.实施方案1-11任一项的方法,其中从热解流出物中分离至少第二热解产物馏分,该方法进一步包括将第二热解产物馏分送入初级分馏器。
[0095]
当在本文中列出数值下限和数值上限时,涵盖从任何下限到任何上限的范围。虽然已经具体描述了本公开的说明性实施例,但是应当理解,在不脱离本公开的精神和范围的情况下,各种其他修改对于本领域技术人员而言将是显而易见的并且可以由本领域技术人员容易地进行。因此,不旨在将所附权利要求的范围限于本文所述的实施例和描述,而是将权利要求解释为涵盖本公开中存在的可专利新颖性的所有特征,包括将被本公开所属领域的技术人员视为其等同物的所有特征。
[0096]
上面已经参考许多实施方案和具体实施例描述了本公开。根据以上详细描述,本领域技术人员将想到许多变化。所有这些明显的变化都在所附权利要求的全部预期范围内。