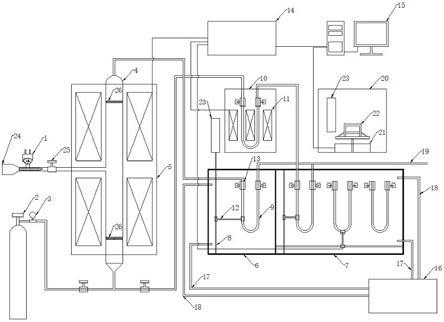
1.本实用新型涉及一种通过流化式热解煤炭制备及分析焦油馏分的装置,采用低温干馏的方式将煤等固体矿物燃料在低温条件下进行热解耦合反应,并对生成的气态焦油产物冷凝后得到焦油馏分,同步自动实现流化床内煤热解过程焦油产率测定及焦油中各馏分测定,属于煤化工中煤的清洁高效利用技术领域。
背景技术:
2.目前,低阶煤主要用于直接燃烧,不仅造成严重的环境污染,而且利用率较小。因此,通过有效途径对低阶煤进行处理加工,提高煤炭资源的利用率和增值率,实现煤炭洁净利用,是目前亟待解决的问题。
3.低阶煤具有化学活性好、无黏结性的特点,是优质的低温干馏煤。煤低温干馏技术是煤在隔绝空气(或在非氧化气氛)条件下加热升温到500~600℃,受热分解成煤气、低温煤焦油和半焦的热加工过程,是低阶煤化学加工的一个重要技术途径。因此,可以采用低温干馏的方法,实现煤的气-液-固组分的分质转化,进而对三相物质进一步分质利用,是低变质煤高效、环保利用的最佳途径。
4.传统的铝甑低温干馏设备操作复杂,并且只能确定焦油的理论产率,不能确定焦油中各馏分的含量。同时,铝甑低温干馏设备通常采用微波加热的方式,与实际工业应用具有较大差别,不能直观的反映出流化床热解多联产项目焦油总产率和各馏分产率。此外,现有的分析焦油馏分的设备通常为人工操作,操作过程繁琐,劳动效率低,影响分析效率。如何开发适用于流化式的干馏设备,提高自动化水平,提高焦油的干馏分析效率,是本领域研究人员应解决的技术问题。
技术实现要素:
5.本实用新型的目的在于克服现有技术中存在的上述不足,而提供一种试验过程全面的分析设备,采用低温干馏的方式将煤等固体矿物燃料在低温条件下进行热解耦合反应,并将生成的气态焦油产物冷凝后得到焦油馏分,同步实现流化床内煤热解过程焦油产率测定及焦油中各馏分测定,以解决目前低温干馏方法不能确定焦油中各馏分含量、与实际工业应用有较大差别、人工操作繁琐、劳动效率低、影响分析效率等问题。
6.本实用新型解决上述问题所采用的技术方案是:一种通过流化式热解煤炭制备及分析焦油馏分的装置,其特征是,包括进料系统、进气系统、流化式反应器、一级加热炉、一级冷凝箱、二级冷凝箱、二级加热炉、冷凝水箱、称重系统、冷凝管外壁干燥系统和控制系统;所述流化式反应器布置在一级加热炉内,且在流化式反应器的内部上下侧设置有筛板,所述流化式反应器的下部通过进气管与进气系统连接,所述流化式反应器的中部通过进料管与进料系统连接,所述流化式反应器的顶部通过出气管连接至一级冷凝箱内部的冷凝管;所述一级加热炉与控制系统连接,所述一级冷凝箱和二级冷凝箱均与冷凝水箱连接,所述一级冷凝箱和二级冷凝箱内均安装有导轨,所述导轨内安装有机械手;所述二级加热炉
与控制系统连接,所述二级加热炉的前侧布置有冷凝管外壁干燥系统,所述二级加热炉的气体出口连接至二级冷凝箱内部的冷凝管,所述称重系统与控制系统连接。
7.进一步的,所述进料系统包括封闭式料仓、螺旋给料机和气体阀,所述螺旋给料机连接封闭式料仓的出料口,所述气体阀安装在螺旋给料机的出口。所述封闭式料仓设置有连通惰性气源的平衡风接口和气体置换接口,所述螺旋给料机密封式设计,输送样品时无气体泄漏。
8.进一步的,所述一级加热炉内布置有多个加热原件,所述一级加热炉采用多段控温。
9.进一步的,所述筛板的开孔尺寸小于样品粒度。
10.进一步的,所述冷凝管与出气管的连接处进行密封设计,所述冷凝管的进出口均安装有旋转阀门,所述冷凝管的出口连接至排气管道。
11.进一步的,所述机械手通过控制系统发送的指令可移动到导轨的相应位置,并可实现旋转阀门的拆下、安装以及移动冷凝管的操作。
12.进一步的,所述二级加热炉前置的冷凝管外壁干燥系统可去除冷凝管外壁残留的水分。
13.进一步的,所述进气系统包括气体钢瓶,所述气体钢瓶的出口安装有减压阀。
14.进一步的,所述控制系统包括控制柜和计算机,所述控制柜与计算机连接。
15.进一步的,所述一级冷凝箱和二级冷凝箱的底部通过冷却水进水管连接冷凝水箱,所述一级冷凝箱和二级冷凝箱的顶部通过冷却水出水管连接冷凝水箱。
16.进一步的,所述称重系统包括冷凝管外壁干燥系统、冷凝管支架和称量天平,所述冷凝管支架设置在称量天平的上方。
17.本实用新型与现有技术相比,具有以下优点和效果:使用该装置通过低温干馏的方式将煤等固体矿物燃料在低温条件下进行热解耦合反应,并对生成的气态焦油产物冷凝后得到焦油馏分,不但可以同步实现流化床内煤热解过程焦油产率测定及焦油中各馏分测定,还可以减少人工操作,提高劳动效率和分析效率,并且试验过程更加接近实际工业应用情况。
附图说明
18.图1是本实用新型的装置结构示意图。
19.图中:封闭式料仓1、气体钢瓶2、减压阀3、流化式反应器4、一级加热炉5、一级冷凝箱6、二级冷凝箱7、导轨8、冷凝管9、二级加热炉10、加热原件11、机械手12、旋转阀门13、控制柜14、计算机15、冷凝水箱16、冷却水进水管17、冷却水出水管18、排气管道19、称重系统20、称量天平21、冷凝管支架22、冷凝管外壁干燥系统23、螺旋给料机24、气体阀25、筛板26。
具体实施方式
20.下面结合附图并通过实施例对本实用新型作进一步的详细说明,以下实施例是对本实用新型的解释而本实用新型并不局限于以下实施例。
21.实施例。
22.参见图1,本实施例中,一种通过流化式热解煤炭制备及分析焦油馏分的装置,包
括进料系统、进气系统、流化式反应器4、一级加热炉5、一级冷凝箱6、二级冷凝箱7、二级加热炉10、冷凝水箱16、称重系统20、冷凝管外壁干燥系统23和控制系统;流化式反应器4布置在一级加热炉5内,且在流化式反应器4的内部上下侧设置有筛板26,流化式反应器4的下部通过进气管与进气系统连接,流化式反应器4的中部通过进料管与进料系统连接,流化式反应器4的顶部通过出气管连接至一级冷凝箱6内部的冷凝管9;一级加热炉5与控制系统连接,一级冷凝箱6和二级冷凝箱7均与冷凝水箱16连接,一级冷凝箱6和二级冷凝箱7内均安装有导轨8,导轨8内安装有机械手12;二级加热炉10与控制系统连接,二级加热炉10的前侧布置有冷凝管外壁干燥系统23,所述二级加热炉10的气体出口连接至二级冷凝箱7内部的冷凝管9,称重系统20与控制系统连接。
23.本实施例中,进料系统包括封闭式料仓1、螺旋给料机24和气体阀25,螺旋给料机24连接封闭式料仓1的出料口,气体阀25安装在螺旋给料机24的出口。封闭式料仓1设置有连通惰性气源的平衡风接口和气体置换接口,螺旋给料机24密封式设计,输送样品时无气体泄漏。
24.本实施例中,一级加热炉5内布置有多个加热原件11,一级加热炉5采用多段控温。
25.本实施例中,筛板26的开孔尺寸小于样品粒度。
26.本实施例中,冷凝管9与出气管的连接处进行密封设计,冷凝管9的进出口均安装有旋转阀门13,冷凝管9的出口连接至排气管道19。
27.本实施例中,机械手12通过控制系统发送的指令可移动到导轨8的相应位置,并可实现旋转阀门13的拆下、安装以及移动冷凝管9的操作。
28.本实施例中,二级加热炉10前置的冷凝管外壁干燥系统23可去除冷凝管9外壁残留的水分。
29.本实施例中,进气系统包括气体钢瓶2,气体钢瓶2的出口安装有减压阀3。
30.本实施例中,控制系统包括控制柜14和计算机15,控制柜14与计算机15连接。
31.本实施例中,一级冷凝箱6和二级冷凝箱7的底部通过冷却水进水管17连接冷凝水箱16,一级冷凝箱6和二级冷凝箱7的顶部通过冷却水出水管18连接冷凝水箱16。
32.本实施例中,称重系统20包括冷凝管外壁干燥系统23、冷凝管支架22和称量天平21,所述冷凝管支架22设置在称量天平21的上方。
33.工作方法如下:
34.试验开始前,将原料装入封闭式料仓1内,关闭封闭式料仓1,将惰性气体接入气体置换接口,打开平衡风接口,利用惰性气体将封闭式料仓1中的空气完全置换。通过计算机15设置一级热解炉5、二级加热炉10、一级冷凝箱6、二级冷凝箱7的温度,设定机械手12的操作时间和动作,以及设定气体流量。计算机15根据不同分馏温度,对应生成不同编号,并分配给二级冷凝箱7内对应的冷凝管9。机械手12分别将不同编号的冷凝管9送入称重系统20,并一一进行称重。称重系统20记录各冷凝管9的初始质量。称重完成后,机械手12将各冷凝管9放入冷凝箱中。
35.试验开始后,一级加热炉5升温至设定温度,气体阀25打开,螺旋给料机24开始进料。进料完成后,螺旋给料机24停止旋转,气体阀25关闭。样品送入流化式反应器4后,在设定的温度下进行热解。热解气和惰性气体共同进入一级冷凝箱6中的冷凝管9内。焦油在一级冷凝管9内冷凝,其余不冷凝气体通过排气管道19排出。
36.样品热解完成后,控制系统控制关闭一级加热炉5,二级加热炉10开始升温。一级冷凝箱6内的机械手12通过导轨8移动至旋转阀门13处,关闭旋转阀门13,并将冷凝管9移动至二级加热炉10前置的冷凝管外壁干燥系统23。通过冷凝管外壁干燥系统23将冷凝管9外壁残留的水滴清除后送入称重系统20。称重系统20记录冷凝管9的质量,并与该冷凝管9的初始质量进行对比,获得该热解条件的焦油总质量。称重完成后的冷凝管9由机械手12送入二级加热炉10。根据设定,二级加热炉10分别加热到不同温度,对焦油进行分馏,分馏产生的气体送入二级冷凝箱7内置的冷凝管9中。完成一个分馏温度后,二级加热炉10加热至下一分馏温度。
37.二级冷凝箱7中的机械手12根据设定关闭对应温度的旋转阀门13,取下冷凝管9,将该温度对应编号的冷凝管9移至称重系统20内的冷凝管外壁干燥系统23。将下一编号冷凝管9接入,打开阀门13。冷凝管9外壁在称重系统20内的冷凝管外壁干燥系统23干燥后,通过机械手12移至称量天平21上方的冷凝管支架22中。称重系统20记录对应编号的冷凝管9质量,并通过与冷凝管9的初始质量对比,获得各馏分的实际质量。通过对比系统的进料量、焦油总质量和不同分馏温度焦油质量,获得该热解条件的焦油产率和各馏分产率。
38.本实施例中,控制系统中采用的控制软件、程序为现有技术,本说明书中未作详细描述的内容均属于本领域专业技术人员公知的现有技术。
39.此外,需要说明的是,本说明书中所描述的以上内容仅仅是对本实用新型结构所作的举例说明。凡依据本实用新型专利构思所述的构造、特征及原理所做的等效变化,均包括在本实用新型专利的保护范围内。本实用新型所属技术领域的技术人员可以对所描述的具体实施例做各种各样的修改、补充或采用类似的方式替代,只要不偏离本实用新型的结构或者超越本权利要求书所定义的范围,均应属于本实用新型的保护范围。