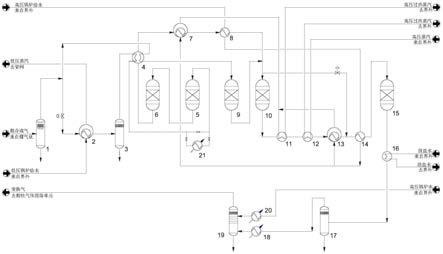
一种低水气比co变换装置
技术领域
1.本实用新型属于煤化工装置co变换工艺技术领域,涉及一种低水气比co变换装置。
背景技术:
2.在煤气化配套装置中,一氧化碳变换装置通过变换反应调节气化装置产出粗煤气的氢碳比,满足下游产品的需要,其工艺技术的选择,既要结合不同气化工艺产出的粗煤气的特点,也要考虑到后续装置及下游产品的要求。各种气化工艺产出的粗煤气的组成相差较大,即便针对下游同一产品,与不同气化工艺配套的变换工艺技术也不尽相同。co变换工艺的选择,除了应适应粗煤气组成及满足产品要求以外,还应考虑安全及节能等问题。
3.在煤气化工艺中.激冷型流程越来越受到关注,主要包括国外引进的gsp粉煤气化工艺和国内自主开发的“航天炉”、se东方炉粉煤气化工艺等。激冷型粉煤气化与废热锅炉型粉煤气化(典型工艺如shell粉煤气化)均产生高浓度co的粗合成气.激冷型粉煤气化水气比在0.7~1.0.废热锅炉型粉煤气化0.2左右,粉煤气化的变换操作压力约3.8mpa,其粗煤气的co干基很高,达60%以上,有的甚至到70%,变换反应的推动力大,一氧化碳变换反应属于强放热反应,是一个热力学控制过程,反应的热点温度高达450℃以上。反应非常剧烈,非常容易造成变换炉超温。
4.目前,工业生产中一氧化碳变换反应大多数采用多段绝热反应器串联工艺,从而达到工艺气中一氧化碳的转换率要求。传统采用高水气比co变换工艺,该工艺是通过在粗煤气中补加过量蒸汽至高水气比来完成变换反应。先使部分或全部气体通过第一反应器,在第一反应器的人口添加了大量的蒸汽,通常使水气比达到1.4以上,该技术存在的主要问题:由于水气比和co含量都高,反应的推动力大,反应的深度难以控制。实际运行中,在催化剂使用初期阶段,有时不得不采用氮气稀释或提高水气比或移出部分催化剂的办法来降温,影响催化剂的使用寿命;同时变换工段的蒸汽消耗大,变换气的热回收系统最终通过设置多台换热器,加热脱盐水和循环水冷却等方式来实现,变换气的冷凝液量大,极大增加了下游污水处理的负荷与难度,装置能耗高,投资大。
技术实现要素:
5.本实用新型的目的在于针对现有技术存在的不足之处,而提供了一种低水气比co变换工艺及装置,整个工艺流程具有能量集成效果好、节能降耗显著等特点。
6.本实用新型的目的可以通过以下技术方案实现:
7.一种低水气比co变换装置,该装置包括低压蒸汽发生器、1#脱毒槽,1#变换炉,2# 脱毒槽,1#变换炉和水解反应器;粗合成气的输出管道与1#气液分离器相连,所述1#气液分离器的顶部粗合成气输出端分为两股物流;
8.第一股物流通过管道依次经过低压蒸汽发生器和2#气液分离器,2#气液分离器顶部输出端经过原料气加热器后依次进入1#脱毒槽、1#变换炉、原料气加热器和1#高压蒸汽
发生器,所述1#高压蒸汽发生器的输出端与1#高压锅炉给水预热器相连;
9.第二股物流通过原料气加热器和2#脱毒槽与1#高压锅炉给水预热器输出端相连后进入2#变换炉;2#变换炉的输出端依次经过1#高压蒸汽过热器、2#高压蒸汽过热器、2#高压蒸汽发生器、2#高压锅炉给水预热器后进入水解反应器,所述水解反应器的输出端依次与脱盐水加热器和3#气液分离器相连;
10.所述3#气液分离器顶部的输出端经过变换气水冷器后,进入4#气液分离器,所述4# 气液分离器顶部的输出端送去界外酸性气体脱出单元。
11.上述装置中:所述2#变换炉的输入端引出一根管道作为调节旁路,与2#高压蒸汽发生器的输出端相连。
12.上述装置中:来自界外的高压锅炉给水经过1#高压锅炉给水预热器和2#高压锅炉给水预热器后分为两股,一股去1#高压蒸汽发生器、另外一股去2#高压蒸汽发生器。
13.上述装置中:所述1#高压蒸汽发生器和2#高压蒸汽发生器副产的高压饱和蒸汽经过 1#高压蒸汽过热器过热后送至界外;来自界外的高压饱和蒸汽经过2#高压蒸汽过热器过热后送至界外;来自界外的高压锅炉给水经过高压锅炉给水冷却器后进入4#气液分离器。
14.上述装置中:所述1#脱毒槽的输入端管道上设置了开工蒸汽加热器。
15.一种利用上述的装置实现低水气比co变换的方法,该方法包括以下步骤:
16.1)粗合成气进入1#气液分离器气液分离后,被分为两个物流,第一股物流管道上设置了流量调节阀,用于控制第一股和第二股物流的流量分配比例,所述第一股物流通过经过低压蒸汽发生器,粗合成气的温度被降低后进入2#气液分离器进行气液分离,顶部气相经过原料气加热器升温后,经过1#脱毒槽进入1#变换炉发生一氧化碳变换反应,1#变换炉出口变换气经过原料气加热器被降温后,进入1#高压蒸汽发生器副产高压饱和蒸汽,出口变换气被进入1#高压锅炉给水预热器被进一步冷却;
17.2)第二股物流通过原料气加热器升温后,经过2#脱毒槽与来自1#高压锅炉给水预热器出口的变换气混合后进入2#变换炉继续进行一氧化碳变换反应;
18.3)步骤2)在2#变换炉内发生一氧化碳变换反应后,变换气温度被升高,然后依次进入1#高压蒸汽过热器、2#高压蒸汽过热器、2#高压蒸汽发生器和2#高压锅炉给水预热器后进入水解反应器脱除有机硫;
19.4)步骤3)脱除有机硫后的变换气先经过脱盐水加热器、3#气液分离器、变换气水冷器后进入4#气液分离器,从4#气液分离器顶部出来的气体送至下游酸性气体脱除单元。
20.上述方法中:通过低压蒸汽发生器将粗合成气冷却分离后,使得进入1#变换炉的粗合成气水气比控制在0.2~0.3之间。
21.上述方法中:所述第一股物流管道上设置了流量调节阀,用于控制第一股和第二股物流的流量分配比例为6:4~4:6之间。
22.上述方法中:1#变换炉入口温度控制在200~260℃之间,1#变换炉出口温度控制在390~435℃,2#变换炉出口温度控制在400~440℃,水解反应器的入口温度控制在 165~185℃。
23.本实用新型技术方案中:所述的反应炉为轴向或轴径向反应器,采用绝热固定床结构。
24.本实用新型技术方案中:所述的1#气液分离器(1)的内件型式采用叶片式或离心管束式高效分离结构或采用丝网除沫器结构以及它们的改进型式。
25.本实用新型的有益效果:
26.提供了一种低水气比co变换工艺及装置。主要优势如下:一是将粗煤气合理分为两股物流且仅将其中一股的水气比降低,同时副产低压蒸汽,减少后续系统设备和管道负荷,降低投资;二是分股入炉,通过控制1#变换炉入口粗合成气的水气比,进而控制反应深度和床层热点温度,避免了1#变换炉出现超温现象;三是进入2#变换炉的混合气中co浓度大幅降低,极大降低了2#变换炉的发生甲烷化反应的可能性。四是采用分股入炉的方式,气量调节灵活方便,上游气量变化和co含量的波动对变换炉操作影响较小。
附图说明
27.图1是本实用新型的工艺流程示意图。
28.图中:1
‑
1#气液分离器,2
‑
低压蒸汽发生器,3
‑
2#气液分离器,4
‑
原料气加热器,5
‑
1# 脱毒槽,6
‑
1#变换炉,7
‑
1#高压蒸汽发生器,8
‑
1#高压锅炉给水预热器,9
‑
2#脱毒槽,10
‑
2# 变换炉,11
‑
1#高压蒸汽过热器,12
‑
2#高压蒸汽过热器,13
‑
2#高压蒸汽发生器,14
‑
2#高压锅炉给水预热器,15
‑
水解反应器,16
‑
脱盐水加热器,17
‑
3#气液分离器,18
‑
变换气水冷器,19
‑
4#气液分离器,20
‑
高压锅炉给水冷却器,21
‑
开工蒸汽加热器。
具体实施方式
29.下面结合实施例对本实用新型做进一步说明,但本实用新型的保护范围不限于此:
30.一种低水气比co变换装置,该装置包括低压蒸汽发生器2、1#脱毒槽5,1#变换炉6, 2#脱毒槽9,2#变换炉10和水解反应器15;粗合成气的输出管道与1#气液分离器1相连,所述1#气液分离器1的顶部粗合成气输出端分为两股物流;
31.第一股物流通过管道依次经过低压蒸汽发生器2和2#气液分离器3,2#气液分离器3 顶部输出端经过原料气加热器4后依次进入1#脱毒槽5、1#变换炉6、原料气加热器4和 1#高压蒸汽发生器7,所述1#高压蒸汽发生器7的输出端与1#高压锅炉给水预热器8相连;
32.第二股物流通过原料气加热器4和2#脱毒槽9与1#高压锅炉给水预热器8输出端相连后进入2#变换炉10;2#变换炉10的输出端依次经过1#高压蒸汽过热器11、2#高压蒸汽过热器12、2#高压蒸汽发生器13、2#高压锅炉给水预热器14后进入水解反应器15,所述水解反应器15的输出端依次与脱盐水加热器16和3#气液分离器17相连;
33.所述3#气液分离器17顶部的输出端经过变换气水冷器18后,进入4#气液分离器19,所述4#气液分离器19顶部的输出端送去界外酸性气体脱出单元。
34.所述2#变换炉10的输入端引出一根管道作为调节旁路,与2#高压蒸汽发生器13的输出端相连。
35.来自界外的高压锅炉给水经过1#高压锅炉给水预热器8和2#高压锅炉给水预热器14 后分为两股,一股去1#高压蒸汽发生器7、另外一股去2#高压蒸汽发生器13。
36.所述1#高压蒸汽发生器7和2#高压蒸汽发生器13副产的高压饱和蒸汽经过1#高压蒸汽过热器11过热后送至界外;来自界外的高压饱和蒸汽经过2#高压蒸汽过热器12过热后
送至界外;来自界外的高压锅炉给水经过高压锅炉给水冷却器20后进入4#气液分离器19。
37.所述1#脱毒槽5的输入端管道上设置了开工蒸汽加热器21。
38.实施例1
39.来自上游煤气化装置的484880kg/h粗合成气(206℃,3.84mpa,水气比为0.91)进入 1#气液分离器气液分离后,被分为两个物流,第一股物流管道上设置了流量调节阀,用于控制第一股和第二股物流的流量分配比例为6:4,所述第一股物流(流量为290928kg/h) 通过经过低压蒸汽发生器后,副产92503kg/h低压饱和蒸汽(165℃,0.5mpa),粗合成气的水气比被降低至0.24后,进入2#气液分离器进行气液分离,顶部气相经过原料气加热器升温至200℃后,经过1#脱毒槽后进入1#变换炉发生一氧化碳变换反应,1#变换炉入口温度为200℃,1#变换炉出口变换气出口温度为405℃,经过原料气加热器后,被冷却至 353℃,进入1#高压蒸汽发生器副产17632kg/h高压饱和蒸汽,出口变换气被冷却至250℃,进入1#高压锅炉给水预热器被进一步冷却至195℃;第二股物流(流量为193952kg/h)通过原料气加热器升温至210℃后,经过2#脱毒槽与来自1#高压锅炉给水预热器出口的变换气混合后进入2#变换炉继续进行一氧化碳变换反应,变换气温度被升高至400℃后,然后依次进入1#高压蒸汽过热器、2#高压蒸汽过热器和2#高压蒸汽发生器和2#高压锅炉给水预热器后,温度为180℃进入水解反应器脱除有机硫;脱除有机硫后的变换气先进入脱盐水加热器、3#气液分离器、变换气水冷器后,温度降低至40℃后,进入4#气液分离器后,变换气(流量为372042kg/h,温度为40℃)被送至下游酸性气体脱除单元。
40.实施例2
41.来自上游煤气化装置的484880kg/h粗合成气(206℃,3.84mpa,水气比为0.91)进入 1#气液分离器气液分离后,被分为两个物流,第一股物流管道上设置了流量调节阀,用于控制第一股和第二股物流的流量分配比例为5:5,所述第一股物流(流量为242440kg/h) 通过经过低压蒸汽发生器后,副产82146kg/h低压饱和蒸汽(165℃,0.5mpa),粗合成气的水气比被降低至0.2后,进入2#气液分离器进行气液分离,顶部气相经过原料气加热器升温至225℃后,经过1#脱毒槽后进入1#变换炉发生一氧化碳变换反应,1#变换炉入口温度为225℃,1#变换炉出口变换气出口温度为390℃,经过原料气加热器后,被冷却至274℃,进入1#高压蒸汽发生器副产10535kg/h高压饱和蒸汽,出口变换气被冷却至221℃,进入 1#高压锅炉给水预热器被进一步冷却至195℃;第二股物流(流量为242440kg/h)通过原料气加热器升温至240℃后,经过2#脱毒槽与来自1#高压锅炉给水预热器出口的变换气混合后进入2#变换炉继续进行一氧化碳变换反应,变换气温度被升高至430℃后,然后依次进入1#高压蒸汽过热器、2#高压蒸汽过热器和2#高压蒸汽发生器和2#高压锅炉给水预热器后,温度为165℃进入水解反应器脱除有机硫;脱除有机硫后的变换气先进入脱盐水加热器、3#气液分离器、变换气水冷器后,温度降低至40℃后,进入4#气液分离器后,变换气(流量为372434kg/h,温度为40℃)被送至下游酸性气体脱除单元。
42.实施例3
43.来自上游煤气化装置的484880kg/h粗合成气(206℃,3.84mpa,水气比为0.91)进入 1#气液分离器气液分离后,被分为两个物流,第一股物流管道上设置了流量调节阀,用于控制第一股和第二股物流的流量分配比例为4:6,所述第一股物流(流量为193952kg/h) 通过经过低压蒸汽发生器后,副产55218kg/h低压饱和蒸汽(165℃,0.5mpa),粗合成气的水
气比被降低至0.3后,进入2#气液分离器进行气液分离,顶部气相经过原料气加热器升温至260℃后,经过1#脱毒槽后进入1#变换炉发生一氧化碳变换反应,1#变换炉入口温度为260℃,1#变换炉出口变换气出口温度为435℃,经过原料气加热器后,被冷却至300℃,进入1#高压蒸汽发生器副产5978kg/h高压饱和蒸汽,出口变换气被冷却至245℃,进入 1#高压锅炉给水预热器被进一步冷却至210℃;第二股物流(流量为290928kg/h)通过原料气加热器升温至235℃后,经过2#脱毒槽与来自1#高压锅炉给水预热器出口的变换气混合后进入2#变换炉继续进行一氧化碳变换反应,变换气温度被升高至440℃后,然后依次进入1#高压蒸汽过热器、2#高压蒸汽过热器和2#高压蒸汽发生器和2#高压锅炉给水预热器后,温度为185℃进入水解反应器脱除有机硫;脱除有机硫后的变换气先进入脱盐水加热器、3#气液分离器、变换气水冷器后,温度降低至40℃后,进入4#气液分离器后,变换气(流量为381049kg/h,温度为40℃)被送至下游酸性气体脱除单元。
44.上述实施例和说明书中描述的只是说明本实用新型创造的原理,并不因此而限定本实用新型的保护范围,在不脱离本实用新型创造精神和范围的前提下,本技术实用新型还会有各种变化和改进,这些变化和改进都落入要求保护的本实用新型范围内。本实用新型未涉及部分均与现有技术相同或可采用现有技术加以实现。