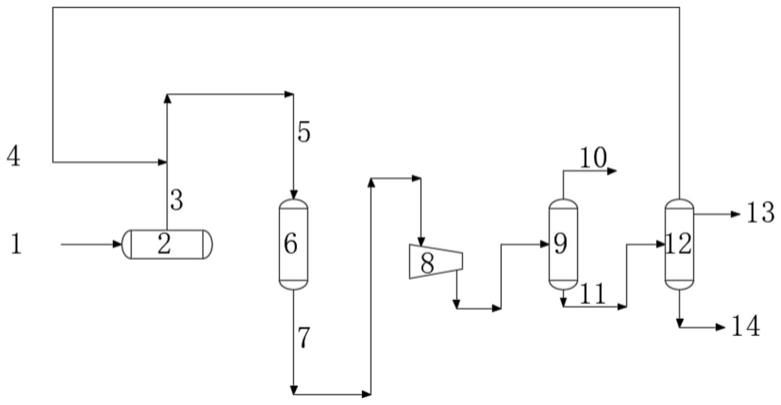
1.本发明涉及一种催化轻汽油降烯烃的方法。
背景技术:
2.流化催化裂化(fcc)装置生产的催化裂化汽油是我国车用汽油的主要来源,占总汽油消费量的70%以上。fcc汽油的一大特点是烯烃含量高,通常为40%~50%,远高于国六汽油标准对烯烃含量的限制值。为了满足汽油油品升级的需要,国内开发了多种汽油降烯烃技术,包括研发低烯烃产率的新型fcc催化剂,开发多产异构烷烃的流化催化技术。采用新的技术,催化汽油的烯烃含量有一定程度的降低,但是一般仍然高于国六b标准的要求(15%),需要进行汽油调和才能达标。而随着乙醇汽油的推广、家用汽车销售量的下滑和新能源汽车的普及,可以预见汽油消费量的增速将会放缓。因此,通过汽油调和的方式,虽然可以使烯烃含量达标,但是增加了汽油总产量,在提高油品的同时适当降低汽油产量成为炼化企业必须考虑的问题。一种有效的方法是通过化学反应转化催化汽油中的烯烃,从而降低催化汽油总烯烃含量和汽油总量。
3.专利cn102286296公开了一种以催化汽油为原料增产丙烯和乙烯的方法。该方法在现有蒸汽裂解装置外增加了一个催化裂解系统,通过催化裂解反应把催化汽油转化为富含乙烯和丙烯的催化裂解气。该催化裂解系统包括汽油催化裂解单元、烷烃脱氢单元和烯烃裂解单元。汽油首先在汽油催化裂解单元中裂解,获得碳三及以下馏分和碳四及以上馏分;碳四及以上馏分在烷烃脱氢单元中经脱氢反应把烷烃转化为烯烃,然后进入烯烃裂解单元再次裂解转化为碳三及以下馏分和碳四及以上馏分;最后从催化裂解系统产生的碳三以下馏分中分离出乙烯丙烯。该方法不仅降低了催化汽油的产量,还把催化汽油中的烷烃和烯烃转化为高附加值的乙烯丙烯,但是该工艺流程复杂,需要设置三个反应单元,且原料在三个单元间需要降温至40℃进行分离,然后升温至500℃~600℃进行反应,能耗巨大。
4.因此现有技术均存在工艺流程复杂、能耗高的问题,本发明有针对性的解决了上述问题。
技术实现要素:
5.本发明的目的是针对现有技术中存在的催化汽油降烯烃生产过程中工艺流程复杂、能耗高的问题,提供一种新的催化汽油降烯烃方法。该方法具有工艺流程简洁、能耗低、乙烯丙烯收率高等优点。
6.为达到本发明的目的,本发明提供了一种催化轻汽油降烯烃的方法,包括如下步骤:
7.(1)对轻汽油原料进行蒸发处理,得到气相裂解原料;
8.(2)对所述气相裂解原料进行烯烃催化裂解处理,获得裂解反应产物;
9.(3)对所述裂解反应产物进行分离处理,分离得到碳三及以下物流、气相循环物料、液化气和粗汽油;
10.(4)将气相循环物料循环回步骤(2)与所述气相裂解原料合并后进行烯烃催化裂解处理。
11.根据本发明的优选实施方式,所述轻汽油原料为催化裂解汽油经轻重分离后获得的催化轻汽油。
12.根据本发明的一些实施方式,以所述轻汽油原料的重量为100%计,其中碳五烃和碳六烃的总含量不小于90%。
13.根据本发明的优选实施方式,以所述轻汽油原料的重量为100%计,其中单烯烃(尤其指碳五碳六烯烃)的含量为20%以上,优选为20%-60%,更优选为30%-60%,进一步优选为40%-60%。
14.根据本发明的一些实施方式,所述步骤(1)中将轻汽油原料送入原料蒸发器中进行气化处理,得到气相裂解原料。
15.根据本发明的一些实施方式,所述催化裂解处理采用zsm-5分子筛催化剂。
16.根据本发明的优选实施方式,所述催化裂解处理的反应的反应温度为450-600℃,例如为500℃、530℃、540℃、550℃、580℃以及他们之间的任意值。
17.根据本发明的优选实施方式,所述催化裂解处理的反应压力为0.01-0.1mpag,例如为0.02mpag、0.03mpag、0.04mpag、0.05mpag、0.06mpag、0.07mpag、0.08mpag、0.09mpag以及它们之间的任意值。
18.根据本发明的优选实施方式,所述催化裂解处理的反应空速为5-15h-1
,例如为7h-1
、8h-1
、10h-1
、12h-1
、14h-1
以及它们之间的任意值。
19.根据本发明的优选实施方式,步骤(2)中将所述气相裂解原料送至烯烃裂解反应器。
20.根据本发明的优选实施方式,所述烯烃催化裂解处理包括:对所述气相裂解原料进行加热处理,升温至反应温度后进入反应器,发生烯烃催化裂解反应。
21.根据本发明的优选实施方式,所述步骤(3)包括:
22.(3a)对所述裂解反应产物进行分离处理,分离得到碳三及以下物流和碳四及以上物流;
23.(3b)对所述碳四及以上物流进行分离处理,得到气相循环物料、液化气和粗汽油。
24.根据本发明的优选实施方式,步骤(3a)中将所述裂解反应产物送入第一精馏塔进行分离处理,塔顶得到碳三及以下物流,塔釜得到碳四及以上物流。
25.根据本发明的优选实施方式,所述第一精馏塔为脱丙烷塔。
26.根据本发明的优选实施方式,所述裂解反应产物经压缩机增压至1.8mpag以上压力后送入脱丙烷塔。
27.根据本发明的一些实施方式,所述步骤(3b)中将所述碳四及以上物流送至第二精馏塔进行分离处理,塔顶得到气相循环物料和液化气,塔釜得到粗汽油。
28.根据本发明的优选实施方式,所述第二精馏塔的操作压力为0.3-0.5mpag,塔顶温度为40-60℃,塔釜温度为80-110℃
29.根据本发明的优选实施方式,所述第二精馏塔为脱丁烷塔。
30.根据本发明的一些实施方式,将所述气相循环物料循环回步骤(2)与所述气相裂解原料合并后进行烯烃催化裂解处理。
31.根据本发明的优选实施方式,所述气相循环物料与气相裂解原料一起作为裂解反应进料送至烯烃裂解反应器进行烯烃催化裂解处理。
32.根据本发明的优选实施方式,所述气相循环物料和所述气相裂解原料的质量之比为(0.2-0.5):1,优选为(0.3-0.4):1。
33.根据本发明的优选实施方式,所述气相循环物料和所述气相裂解原料的质量流量之比为(0.2-0.5):1,优选为(0.3-0.4):1。
34.根据本发明的优选实施方式,以所述气相循环物料的重量为100%计,其中碳四烃类的含量不小于95%。
35.根据本发明的一些实施方式,以所述气相循环物料的重量为100%计,其中碳四单烯烃类的含量为20-40%,例如为25%、30%、34%、35%、37%以及它们之间的任意值。
36.采用本发明的方法,以催化汽油经轻重分离得到的催化轻汽油为原料,其中主要组分为碳五碳六烃类,送入烯烃裂解反应器中,碳五碳六烃在zsm-5分子筛催化剂的作用下,发生催化裂解反应,生成乙烯、丙烯、丁烯等产物。反应产物在分离单元中分离出富含乙烯、丙烯等高附加值产物的碳三及以下物流,可以送入炼厂的气分或烯烃精馏系统分离,从碳四及以上物流分离出含碳四烃例如丁烯的循环物料,循环回反应器进一步裂解,同时分离出液化气和烯烃含量大幅降低的粗汽油。
37.采用本发明的方法,所述烯烃裂解反应器可以适用不同烯烃浓度的催化轻汽油原料,原料中单烯烃含量为20%~60%。原料中单烯烃浓度越高,则降烯烃的效果越明显,同时生产的乙烯丙烯产量越大,经济效益越显著。
38.采用本发明的方法,对碳四烃类进行循环可以有效提高乙烯丙烯的产量。同时,低烯烃浓度的碳四循环物料可以稀释轻汽油原料的烯烃浓度,有效防止结焦,因此本发明的方法不需要添加任何惰性稀释剂,分离流程简单,能耗相对较低。另外,通过优化循环物料流量,综合考虑能耗和装置收益,可以确定较优的循环量。
39.采用本发明的方法,催化轻汽油的产量降低30%~57%,烯烃含量降低了51%~66%,取得了同时减低汽油产量、降低汽油烯烃含量、增产乙烯丙烯的多重技术效果。
附图说明
40.图1为根据本发明一些实施方式的流程示意图。
41.其中,1为轻汽油原料,2为原料蒸发器,3为气相裂解原料,4为气相循环物料,5为裂解反应进料,6为烯烃裂解反应器,7为裂解反应产物,8为压缩机,9为脱丙烷塔,10为c3-物流,11为c4+物流,12为脱丁烷塔,13为液化气,14为粗汽油。
具体实施方式
42.下面结合具体实施例对本发明作进一步说明,但并不构成对本发明的任何限制。
43.图1示出了本发明一个实施例的流程图。轻汽油原料1进入原料蒸发器2气化后得到的气相裂解原料3和气相循环物流4混合作为裂解反应进料5,然后进入烯烃裂解反应器6,发生烯烃催化裂解反应,裂解反应产物7经压缩机8增压,然后送入脱丙烷塔9,从塔顶分离得到碳三及以下(c3-)物流10,塔釜得到碳四及以上(c4+)物流11,进入循脱丁烷塔12,塔顶气相组分作为气相循环物流4,塔顶液相采出为液化气13,塔釜为重组分粗汽油14。
44.【实施例1】
45.提供一股流量为10吨/小时的催化轻汽油原料,其中碳五碳六烯烃含量为50%(按质量分数,下同),碳五碳六烷烃含量为45%,碳四烃类含量为5%。按图1所示流程反应,其中烯烃催化裂解反应的反应温度为550℃,反应压力为0.05mpag,反应空速为10h-1
。反应产物经压缩机增压至2.0mpag后,送入脱丙烷塔。从脱丙烷塔顶获得c3-物料3.7吨/小时,其中烯烃(乙烯+丙烯)浓度81%。脱丁烷塔操作压力为0.35mpag,塔顶温度为48℃,塔釜温度为92℃,塔板数为38。气相循环物料的流量为4吨/小时,其中碳四烃类浓度97%,碳四单烯烃浓度为37%,循环比为0.4。液化气产量为0.9吨/小时。粗汽油产量为5.4吨/小时,其中烯烃浓度为20%。
46.【实施例2】
47.按照实施例1所述的条件和步骤,轻汽油原料中碳五碳六烯烃含量为60%,碳五碳六烷烃含量为35%,碳四烃类含量为5%。烯烃催化裂解反应温度为540℃,反应压力为0.03mpag,反应空速为7h-1
。反应产物经压缩机增压至2.0mpag后,送入脱丙烷塔。从脱丙烷塔顶获得c3-物料4.22吨/小时,其中烯烃(乙烯+丙烯)浓度83%。脱丁烷塔操作压力为0.5mpag,塔顶温度为55℃,塔釜温度为100℃,塔板数为45。气相循环物料的流量为5吨/小时,其中碳四单烯烃浓度为36%,循环比为0.5。液化气产量为0.89吨/小时。粗汽油产量为4.9吨/小时,其中烯烃浓度为26%。
48.【实施例3】
49.按照实施例1所述的条件和步骤,轻汽油原料中碳五碳六烯烃含量为40%,碳五碳六烷烃含量为55%,碳四烃类含量为5%。烯烃催化裂解反应温度为560℃,反应压力为0.03mpag,反应空速为5h-1
。反应产物经压缩机增压至2.0mpag后,送入脱丙烷塔。从脱丙烷塔顶获得c3-物料3.24吨/小时,其中烯烃(乙烯+丙烯)浓度81%。脱丁烷塔操作压力为0.45mpag,塔顶温度为52℃,塔釜温度为96℃,塔板数为25。气相循环物料的流量为4吨/小时,其中碳四单烯烃浓度为33%,循环比为0.4。液化气产量为0.82吨/小时。粗汽油产量为5.94吨/小时,其中烯烃浓度为15%。
50.【实施例4】
51.按照实施例1所述的条件和步骤,轻汽油原料中碳五碳六烯烃含量为30%,碳五碳六烷烃含量为65%,碳四烃类含量为5%。烯烃催化裂解反应温度为570℃,反应压力为0.02mpag,反应空速为12h-1
。反应产物经压缩机增压至1.9mpag后,送入脱丙烷塔。从脱丙烷塔顶获得c3-物料2.73吨/小时,其中烯烃(乙烯+丙烯)浓度83%。脱丁烷塔操作压力为0.4mpag,塔顶温度为48℃,塔釜温度为92℃,塔板数为35。气相循环物料的流量为3吨/小时,其中碳四单烯烃浓度为34%,循环比为0.3。液化气产量为0.82吨/小时。粗汽油产量为6.45吨/小时,其中烯烃浓度为10%。
52.【实施例5】
53.按照实施例1所述的条件和步骤,轻汽油原料中碳五碳六烯烃含量为20%,碳五碳六烷烃含量为75%,碳四烃类含量为5%。烯烃催化裂解反应温度为530℃,反应压力为0.02mpag,反应空速为10h-1
。反应产物经压缩机增压至1.9mpag后,送入脱丙烷塔。从脱丙烷塔顶获得c3-物料2.27吨/小时,其中烯烃(乙烯+丙烯)浓度82%。气相循环物料的流量为3吨/小时,其中碳四单烯烃浓度为30%,循环比为0.3。液化气产量为0.74吨/小时。粗汽油产
量为6.99吨/小时,其中烯烃浓度为7%。
54.表1.轻汽油原料和粗汽油的烯烃含量对比
[0055] 实施例1实施例2实施例3实施例4实施例5轻汽油原料50%60%40%30%20%粗汽油20%26%15%10%7%
[0056]
【实施例6~9】
[0057]
采用和实施例3完全相同的工艺流程和原料,仅改变循环比,分别为0.1,0.2,0.3,0.5。比较不同循环比下单元装置的相对于实施例3的利润和c3-产品产能,所述利润为产品销售收入扣除原料成本和加工成本后的值。
[0058]
表2.实施例3、6-9的结果比较
[0059] 实施例3实施例6实施例7实施例8实施例9循环比0.40.10.20.30.5利润基准-10%-4%-1%-1%c3-产品产量基准-8%-5%-2%+2%
[0060]
【比较例1】
[0061]
某石化公司40万吨/年fcc轻汽油醚化工业装置,采用烯烃含量为44wt%的催化轻汽油原料,其中叔碳烯烃含量约20wt%。轻汽油原料首先和甲醇混合,预热后进入一段醚化反应器,在反应温度65℃、反应压力1.0mpa、甲醇/叔碳烯烃摩尔比1.3、进料空速1.0hr-1的操作条件下,获得一段醚化产物。一段醚化产物在分离塔塔釜分离出醚化轻汽油,塔顶为甲醇和未反应的叔碳烯烃。塔顶物料经预热后进入二段醚化反应器再次反应,二段醚化产物经甲醇萃取后获得和醚化轻汽油汇合。甲醇用水萃取,萃取后进入甲醇蒸馏塔,塔顶的甲醇循环利用,塔釜排出废水。该轻汽油醚化工业装置的轻汽油中烯烃含量减少20.84%,甲醇消耗4.2吨/小时,产生废水约2.4吨/小时,汽油产量增加8.6%。
[0062]
在本发明中的提到的任何数值,如果在任何最低值和任何最高值之间只是有两个单位的间隔,则包括从最低值到最高值的每次增加一个单位的所有值。例如,如果声明一种组分的量,或诸如温度、压力、时间等工艺变量的值为50-90,在本说明书中它的意思是具体列举了51-89、52-88
……
以及69-71以及70-71等数值。对于非整数的值,可以适当考虑以0.1、0.01、0.001或0.0001为一单位。这仅是一些特殊指明的例子。在本技术中,以相似方式,所列举的最低值和最高值之间的数值的所有可能组合都被认为已经公开。
[0063]
应当注意的是,以上所述的实施例仅用于解释本发明,并不构成对本发明的任何限制。通过参照典型实施例对本发明进行了描述,但应当理解为其中所用的词语为描述性和解释性词汇,而不是限定性词汇。可以按规定在本发明权利要求的范围内对本发明作出修改,以及在不背离本发明的范围和精神内对本发明进行修订。尽管其中描述的本发明涉及特定的方法、材料和实施例,但是并不意味着本发明限于其中公开的特定例,相反,本发明可扩展至其他所有具有相同功能的方法和应用。