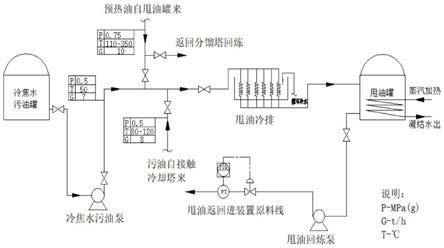
1.本发明涉及一种焦化污油回炼工艺,更具体的说,尤其涉及一种焦化污油密闭回炼的工艺。
背景技术:
2.在炼油工业中,延迟焦化装置是处理重质渣油轻质化的重要手段之一,是炼油厂提高轻质油收率和生产石油焦的主要手段,在我国炼油工业中发挥着重要作用。延迟焦化装置的生产工艺分为焦化和除焦两部分,焦化为连续操作,除焦为间隙操作,就生产规模而言,有一炉两塔(焦炭塔)流程、两炉四塔流程,每台塔的切换周期一般为24小时。
3.由于焦炭塔的周期性切换操作,使得焦炭塔老塔在投用前需进行吹汽放空、注水冷焦、除焦、预热等过程,使老塔达到投用条件,在吹汽放空、老塔预热以及冷焦水系统会产生部分污油,由于这些污油产生的品质不同、温度不同、产生的时间段不同,同时含有部分水分,造成该部分污油相对常规炼油工艺难以回收利用,传统的工艺是将这部分污油经过冷排降温后外甩进入甩油罐区,经过沉降、加温蒸发脱水后再用机泵送回原料线进装置回炼。
4.该工艺的缺点:(1)产生的污油需要冷却后外甩进入甩油罐,增加了冷却水负荷,罐区加温增加了蒸汽消耗,造成装置能耗增加。
5.(2)需设置两台甩油罐组,大大增加的装置占地面积,增加设备投资及运行管理费用。
6.(3)不同温位的油品冷却后进入同一罐组,对高品质油品热能不能回收利用。
7.(4)甩油罐组为常压容器,罐内加温产生的voc异味治理困难,当前环保要求也越来越严格,甩油罐顶的异味无法满足环保要求。
技术实现要素:
8.针对现有技术的不足,本发明提供了一种焦化污油密闭回炼的工艺,改进焦化污油回炼工艺,去除甩油罐组,加设污油蒸发塔,充分利用装置余热给含水污油持续加温,根据工艺运行的不同阶段灵活调整污油回炼,使装置保持加工量最大化,装置能耗最低化,实现含水污油本装置内密闭回炼。
9.本发明的焦化污油密闭回炼的工艺,其特征在于:所述的工艺由以下步骤组成:a:原料污油储存至冷焦水污油罐内,冷焦水污油罐的出油管上设置有冷焦水污油泵;在分馏塔区设置污油蒸发塔,冷焦水污油泵的出油口连接有两路出油管,一路与污油蒸发塔相连,另一路与冷却器相连,装置吹汽放空、预热、冷焦水系统产生的含水污油通过换热升温后进入污油蒸发塔;b:设置污油与柴油换热器,产生的油污与进空冷前的柴油经污油与柴油换热器进行换热升温至130℃,后进入污油蒸发塔;
c:污油蒸发塔的底部设置塔底循环泵,塔底循环泵的进油口与污油蒸发塔的塔底出口相连,塔底循环泵的出油口连接有两路出油管,一路出油管与柴油或顶循等低温热源换热后返回污油蒸发塔内循环,另一路连接至分馏塔蜡油上进料线返回分馏塔回炼;d:污油蒸发塔底的循环油始终保持循环状态,将装置柴油低温热带入蒸发系统,让污油蒸发塔含水污油进行初步蒸发脱水,起到热量蓄能器的作用,充分回收装置低温余热,使得污油逐步达到回炼要求;e:污油蒸发塔顶设置气相联通线接至原料缓冲罐的气象线进分馏塔,油品中的水分加温汽化进入分馏塔,最终在分馏塔顶回流罐冷凝排出;f:根据焦炭塔周期性换塔操作带来的甩油量的变化及分馏塔热量周期性的变化,利用污油蒸发塔作为装置接受、储存本装置产生的含水污油的作用,通过周期性的调整回炼,让污油蒸发塔起到装置热量缓冲、含水污油量缓冲的作用;g:污油回炼量及回炼时机根据装置运行情况调整;h:设置外甩油线直接进分馏塔的回炼线,预热后期的280℃高温位污油可直接进入分馏塔回炼;i:污油总管在进污油蒸发塔前接至冷却器后,连接有两路连接管,一路进应急罐作为装置紧急停工或事故状态污油外甩进入应急罐的流程,另一路接至原料进装置原料线,若污油外送量较大,也可将污油经冷却器后外送至原料线进行回炼,该回炼操作要注意采用小量回炼,防止含水污油大量影响装置正常生产。
10.进一步地,所述的步骤g中,加热炉辐射进出口温差大,加热炉负荷大,此阶段不宜进行回炼,这一阶段时蒸发塔储蓄热量、蒸发脱水的阶段,随着预热结束,分馏塔热量充足,加热炉负荷降低,可通过污油进蜡油上回流线加大污油回炼,使污油在分馏塔内进一步蒸发脱水回炼;在下一焦炭塔换塔之前将蒸发塔内含水污油回炼至最低液位,以便储存下一换塔时的大量含水甩油,从而实现蒸发塔周期性暂存及污油经分馏系统回炼的目的。
11.进一步地,所述的塔底循环泵选用流量为25
‑
30m
³
/h,扬程60m的化工流程泵或ay油泵。
12.进一步地,所述的污油与柴油换热器设置为面积为55
‑
70
㎡
的管壳式换热器。
13.进一步地,所述的设备之间的连接管道管径设置为dn80
‑
100之间;所述的污油总管进污油蒸发塔线的管道材质设置为cr5mo材质,其余管道设置为碳钢无缝钢管。
14.本发明的有益效果是:(1)该工艺可充分利用装置低温热源,实现焦化装置含水污油在本装置内密闭回炼。
15.(2)取消了传统工艺配套的甩油罐组,及相应的加温、消防设施,减少了设备投资,降低了装置的占地面积。同时减少原有的甩油加温蒸汽消耗,降低了装置能耗。
16.(3)增加了装置的操作弹性及分馏系统调整的灵活性,选择不同的工段进行回炼操作,消除装置预热、吹汽阶段热源不足时的加热炉负荷制约瓶颈,保持装置加工量最大化。充分利用蒸发塔蓄热器的作用及空间,有效缓解了周期性操作给分馏塔带来的波动与影响。
17.(4)充分回收利用柴油低温热源用于加热蒸发塔污油,降低柴油进空冷的温度,减少柴油空冷电耗,降低了装置能耗。
18.(5)降低了原有污油外甩时冷排的冷却水消耗。
19.(6)减少了原有的甩油罐组的挥发性气体的排出,有利于厂区voc治理满足环保要求。
附图说明
20.图1为焦化装置传统污油回炼工艺的流程示意图;图2为本发明的工艺流程的示意图。
21.图中:1冷焦水污油罐,2污油蒸发塔,3原料缓冲罐,4冷焦水污油泵,5冷却器,6柴油污油换热器,7塔底循环泵。
具体实施方式
22.下面结合附图与实施例对本发明作进一步说明。
23.如图1和图2所示,在本发明中,取消了甩油罐组及相应的加温设施,在装置分馏塔区加设污油蒸发塔2,原冷焦水污油储存在冷焦水污油罐1内,经冷焦水污油泵4抽出,冷焦水污油泵4的出油口连接两路管道,一路连接至污油蒸发塔2,另一路连接至冷却器5,装置吹汽放空、预热、冷焦水系统产生的含水污油通过换热升温后进入污油蒸发塔2。
24.加设污油与柴油换热器6,产生的油污与进空冷前的柴油经污油与柴油换热器6进行换热升温至130℃,后进入污油蒸发塔2。
25.污油蒸发塔2的底部设置塔底循环泵7,塔底循环泵7的进油口与污油蒸发塔2的塔底出口相连,塔底循环泵7的出油口连接有两路出油管,一路出油管与柴油或顶循等低温热源换热后返回污油蒸发塔2内循环,另一路连接至分馏塔蜡油上进料线返回分馏塔回炼。
26.污油蒸发塔2底的循环油始终保持循环状态,将装置柴油低温热带入蒸发系统,让污油蒸发塔2含水污油进行初步蒸发脱水,起到热量蓄能器的作用,充分回收装置低温余热,污油蒸发塔2相当于一台“蓄热器”,同时吸收吹汽放空、预热甩油的高温位热源,不断储蓄热量,使得污油逐步达到回炼要求。
27.污油蒸发塔2顶设置气相联通线接至原料缓冲罐3的气象线进分馏塔,油品中的水分加温汽化进入分馏塔,最终在分馏塔顶回流罐冷凝排出。
28.根据焦炭塔周期性换塔操作带来的甩油量的变化及分馏塔热量周期性的变化,利用污油蒸发塔2作为装置接受、储存本装置产生的含水污油的作用,通过周期性的调整回炼,让污油蒸发塔2起到装置热量缓冲、含水污油量缓冲的作用;污油回炼量及回炼时机根据装置运行情况调整;加热炉辐射进出口温差大,加热炉负荷大,此阶段不宜进行回炼,这一阶段时蒸发塔储蓄热量、蒸发脱水的阶段,随着预热结束,分馏塔热量充足,加热炉负荷降低,可通过污油进蜡油上回流线加大污油回炼,使污油在分馏塔内进一步蒸发脱水回炼;在下一焦炭塔换塔之前将蒸发塔内含水污油回炼至最低液位,以便储存下一换塔时的大量含水甩油,从而实现蒸发塔周期性暂存及污油经分馏系统回炼的目的。
29.设置外甩油线直接进分馏塔的回炼线,预热后期的280℃高温位污油可直接进入分馏塔回炼。
30.污油总管在进污油蒸发塔前接至冷却器后,连接有两路连接管,一路进应急罐作
为装置紧急停工或事故状态污油外甩进入应急罐的流程,另一路接至原料进装置原料线,若污油外送量较大,也可将污油经冷却器后外送至原料线进行回炼,该回炼操作要注意采用小量回炼,防止含水污油大量影响装置正常生产。
31.本发明在使用时,以60万吨/年的焦化装置为例,塔体容积设置为100m
³
的立式塔,由于无分流精度要求,塔内结构采用人字挡板或规整填料即可。
32.塔底循环泵根据产生的污油量及压力要求,可选择流量25
‑
30m3/h,扬程60m的化工流程泵或ay油泵。
33.塔底循环泵选用流量为25
‑
30m
³
/h,扬程60m的化工流程泵或ay油泵。
34.污油与柴油换热器设置为面积为55
‑
70
㎡
的管壳式换热器。
35.设备之间的连接管道管径设置为dn80
‑
100之间;所述的污油总管进污油蒸发塔线的管道材质设置为cr5mo材质,其余管道设置为碳钢无缝钢管。