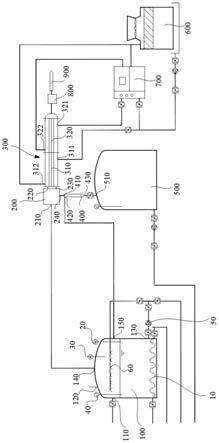
1.本发明涉及水处理技术领域,特别涉及一种焦油脱水系统和焦油脱水方法。
背景技术:
2.煤炭干馏时生成的具有刺激性臭味的黑色或黑褐色粘稠状液体,简称焦油。焦油一般作为加工精制的原料以制取各种化工产品,也可直接利用,如作为工业型煤、型焦和煤质活性炭用的粘结剂的配料组分,还可用作燃料油、高炉喷吹燃料以及木材防腐油和烧炭黑的原料,其应用范围较广。
3.焦化厂的半成品焦油含有大量的水,水分含水率通常在4%
‑
30%之间,需要将水降低到4%以下后才能外卖。目前的工艺是在半成品焦油储存罐中投加破乳剂,加温静置10天左右,焦油与水因密度不同而分离。
4.但是,该方法效果不稳定,经常出现焦油无法按计划时间脱水的情况,导致焦油脱水效率较低。
技术实现要素:
5.本发明的主要目的是提供一种焦油脱水系统,旨在提高含水焦油的脱水效率。
6.为实现上述目的,本发明提出的焦油脱水系统,包括加热罐、过度室、热交换器、分离室以及冷凝水罐,所述加热罐的进料口用于含水焦油的进料,所述加热罐的投入口用于添加共沸剂,所述加热罐的出料口用于成品焦油的排出,所述加热罐的混合蒸气排出口与所述过度室的第一进气口相连通,所述过度室的第一出气口与所述热交换器的第二进气口相连通,所述热交换器的第二回液口与所述过度室的第一回液口相连通,所述过度室的第一出液口与所述分离室的进液口相连通,所述分离室的出剂口与所述加热罐的回剂口相连通,所述分离室的出水口与所述冷凝水罐的入水口相连通。
7.可选地,所述热交换器包括第一热交换器和第二热交换器,所述第一热交换器与所述第二热交换器串联设置。
8.可选地,所述第一热交换器设有所述第二进气口,所述第二进气口与所述第一出气口相连通,所述第一热交换器上设有第一进水孔和第一出水孔,冷却塔中的循环冷却水通过所述第一进水孔进入所述第一热交换器,并通过所述第一出水孔回流到所述冷却塔。
9.可选地,所述第二热交换器的第三进气口与所述第一热交换器的第二出气口相连通,所述第二热交换器上设有第二进水孔和第二出水孔,冷冻机中的冷凝水通过所述第二进水孔进入所述第二热交换器,并通过所述第二出水孔回流到所述冷冻机,所述第二热交换器设有所述第二回液口,所述第二回液口与所述第一回液口相连通。
10.可选地,所述冷却塔与所述冷冻机相连通,所述冷却塔中的循环冷却水供所述冷冻机散热。
11.可选地,所述焦油脱水系统还包括吸附装置,所述吸附装置与所述热交换器相连通,用于吸附从所述热交换器逃逸的尾气,所述吸附装置与废气收集系统相连通。
12.可选地,所述加热罐采用蒸汽盘管加热。
13.可选地,所述加热罐内设置有温度传感器、压力传感器以及液位传感器。
14.可选地,所述加热罐外设置有加热罐循环泵,以将所述加热罐底部的混合液泵至所述加热罐内的喷淋装置。
15.本发明还提出一种焦油脱水方法,包括:
16.将含水焦油和共沸剂的混合物进行气液分离,以获得气体混合物和初级焦油;
17.将气液分离所得的所述气体混合物通过冷凝分离为液体共沸剂和液体冷凝水;
18.将冷凝分离所得的所述液体共沸剂与所述初级焦油混合并进行再次气液分离,并循环以上过程以降低所述初级焦油的含水量以获得成品焦油。
19.本发明的一个技术方案采用包括加热罐、过度室、热交换器、分离室以及冷凝水罐的焦油脱水系统对含水焦油进行脱水处理,将含水焦油和共沸剂投入加热罐进行加热以使共沸剂和含水焦油中的水共沸蒸馏,形成混合蒸汽和初级焦油,混合蒸汽从加热罐的上方排出依次进入过度室、热交换器以及分离室,完成混合蒸汽的冷凝分离,使混合蒸汽变成液体,其中的液体共沸剂回流到加热罐继续参与共沸蒸馏反应,其中的液体冷凝水进入冷凝罐中。如此,完成含水焦油的一次的共沸蒸馏,得到了去除部分水分的初级焦油。初级焦油与共沸剂在此进行共沸蒸馏,如此循环以使含水焦油中的含水量逐步降低,从而得到成品焦油。相较于往含水焦油中投加破乳剂并加温静止的脱水方法,本方案一方面加快了含水焦油的脱水处理速度,提高了含水焦油的脱水处理效率,而不需要等待含水焦油完成脱水后空置出含水焦油加温静止所需的储存罐,进而提升了含水焦油的生产效率;另一方面通过一次次的共沸蒸馏循环,含水焦油可以在计划的时间内完成脱水处理,不会出现因静止效果不佳需延长脱水处理时间,进而避免了因脱水时间加长而可能造成的焦油质量下降;再一方面,本方案不需要投加大量的破乳剂,降低了含水焦油的脱水处理成本。
附图说明
20.为了更清楚地说明本发明实施例或现有技术中的技术方案,下面将对实施例或现有技术描述中所需要使用的附图作简单地介绍,显而易见地,下面描述中的附图仅仅是本发明的一些实施例,对于本领域普通技术人员来讲,在不付出创造性劳动的前提下,还可以根据这些附图示出的结构获得其他的附图。
21.图1为本发明焦油脱水系统一实施例的结构示意图;
22.图2为图1焦油脱水系统一实施例的循环路径图。
23.附图标号说明:
[0024][0025][0026]
本发明目的的实现、功能特点及优点将结合实施例,参照附图做进一步说明。
具体实施方式
[0027]
下面将结合本发明实施例中的附图,对本发明实施例中的技术方案进行清楚、完整地描述,显然,所描述的实施例仅仅是本发明的一部分实施例,而不是全部的实施例。基于本发明中的实施例,本领域普通技术人员在没有作出创造性劳动前提下所获得的所有其他实施例,都属于本发明保护的范围。
[0028]
需要说明,本发明实施例中所有方向性指示(诸如上、下、左、右、前、后
……
)仅用于解释在某一特定姿态(如附图所示)下各部件之间的相对位置关系、运动情况等,如果该特定姿态发生改变时,则该方向性指示也相应地随之改变。
[0029]
另外,在本发明中涉及“第一”、“第二”等的描述仅用于描述目的,而不能理解为指示或暗示其相对重要性或者隐含指明所指示的技术特征的数量。由此,限定有“第一”、“第二”的特征可以明示或者隐含地包括至少一个该特征。另外,全文中的“和/或”包括三个方案,以a和/或b为例,包括a技术方案、b技术方案,以及a和b同时满足的技术方案;另外,各个实施例之间的技术方案可以相互结合,但是必须是以本领域普通技术人员能够实现为基础,当技术方案的结合出现相互矛盾或无法实现时应当认为这种技术方案的结合不存在,也不在本发明要求的保护范围之内。
[0030]
煤炭干馏时生成的具有刺激性臭味的黑色或黑褐色粘稠状液体,简称焦油。焦油一般作为加工精制的原料以制取各种化工产品,也可直接利用,如作为工业型煤、型焦和煤质活性炭用的粘结剂的配料组分,还可用作燃料油、高炉喷吹燃料以及木材防腐油和烧炭黑的原料,其应用范围较广。
[0031]
焦化厂的半成品焦油含有大量的水,水分含水率通常在4%
‑
30%之间,需要将水降低到4%以下后才能外卖。目前的工艺是在半成品焦油储存罐中投加破乳剂,加温静置10天左右,焦油与水因密度不同而分离。
[0032]
但是,一方面该方法效果不稳定,经常出现半成品焦油无法按计划时间脱水的情况,导致焦油质量下降;另一方面该方法所需的脱水时间较长,如半成品焦油无法按照计划时间完成脱水,则无法为后续新生产出的半成品焦油提供储存罐,进而影响半成品焦油的生产效率;再一方面该方法需要投加大量的破乳剂,脱水成本较大。鉴于此,本发明提出一种焦油脱水系统。
[0033]
请参照图1和图2,在本发明一实施例中,该焦油脱水系统包括加热罐100、过度室200、热交换器300、分离室400以及冷凝水罐500。其中,加热罐100设有进料口110、投入口120、出料口130、混合蒸气排出口140以及回剂口150,过度室200设有第一进气口210、第一出气口220、第一回液口230以及第一出液口240,热交换器300设有第二进气口(未示出)和第二回液口(未示出),分离室400设有进液口410、出剂口420以及出水口430,冷凝水罐500设有入水口510。
[0034]
加热罐100的进料口110用于含水焦油的进料,加热罐100的投入口120用于添加共沸剂,加热罐100的出料口130用于成品焦油的排出,加热罐100的混合蒸气排出口140与过度室200的第一进气口210相连通,过度室200的第一出气口220与热交换器300的第二进气口相连通,热交换器300的第二回液口与过度室200的第一回液口230相连通,过度室200的第一出液口240与分离室400的进液口410相连通,分离室400的出剂口420与加热罐100的回剂口150相连通,分离室400的出水口430与冷凝水罐500的入水口510相连通。
[0035]
当利用焦油脱水系统对含水焦油进行脱水处理时,先将含水焦油通过加热罐100的进料口110输送至加热罐100内,同时通过加热罐100的投入口120将共沸剂投放到加热罐100内,然后对加热罐100进行加热,共沸剂与含水焦油中的水一起蒸发形成混合蒸气,混合蒸气从加热罐100的混合蒸气排出口140排出,通过过度室200的第一进气口210进入到过度室200内,再经过度室200的第一出气口220、热交换器300的第二进气口进入热交换器300中,在热交换器300中进行冷凝换热后,混合蒸气变成液体,液体通过热交换器300的第二回液口、过度室200的第一回液口230进入过度室200,并通过过度室200的第一出液口240、分离室400的进液口410进入分离室400,在分离室400内液体完成分离,分离出的液体共沸剂通过分离室400的出剂口420、加热罐100的回剂口150回流到加热罐100内,分离出的液体冷凝水通过分离室400的出水口430、冷凝罐的入水口510进入冷凝罐。如此,完成对含水焦油的一次的共沸蒸馏,初步去除含水焦油中的部分水分得到留在加热罐100底部的初级焦油。回流到加热罐100内的液体共沸剂与初级焦油再次在加热罐100中进行共沸蒸馏,如此循环以降低初级焦油中的含水量,以得到成品焦油。
[0036]
当然,根据含水焦油的共沸蒸馏的循环情况,当共沸剂不足时,可通过加热罐100的投入口120向加热罐100中补充共沸剂,以保证焦油中的水与共沸剂的共沸蒸馏效果,使
含水焦油中的水分经一次次的共沸蒸馏,一步步的降低,直至达到标准含水量。值得注意的是,所说的标准含水量可以根据目标产品的不同的进行规定,如标准含水量为4%,标准含水量为1%等,在此不对成品焦油的含水量做限制。
[0037]
具体地,共沸剂能与含水焦油中的水共沸蒸馏,以形成气体混合物和初级焦油,共沸剂可以选用粗苯、苯、甲苯或环乙烷等,在此不对共沸剂的种类做限制。
[0038]
在一实施例中,在冷凝水罐500中设置液位传感器,以实时测量冷凝水罐500中的水位,以及时将冷凝水罐500中的冷凝水进行排放处理。在冷凝水罐500的冷凝水排放管路中设置有水泵,以更方便的将冷凝水罐500中的冷凝水进行排放处理。冷凝水罐500中的冷凝水可以直接排放或处理后达到排放标准后再排放,或者,可以引入到混合蒸气的冷凝分离过程中,为冷凝分离过程提供冷却水。
[0039]
本发明的一个技术方案采用包括加热罐100、过度室200、热交换器300、分离室400以及冷凝水罐500的焦油脱水系统对含水焦油进行脱水处理,将含水焦油和共沸剂投入加热罐100进行加热以使共沸剂和含水焦油中的水共沸蒸馏,形成混合蒸气和初级焦油,混合蒸气从加热罐100的上方排出依次进入过度室200、热交换器300以及分离室400,完成混合蒸气的冷凝分离,使混合蒸气变成液体,其中的液体共沸剂回流到加热罐100继续参与共沸蒸馏反应,其中的液体冷凝水进入冷凝罐中。如此,完成含水焦油的一次的共沸蒸馏,得到了去除部分水分的初级焦油。初级焦油与共沸剂再次进行共沸蒸馏,如此循环以使初级焦油中的含水量逐步降低,从而得到成品焦油。相较于往含水焦油中投加破乳剂并加温静止的脱水方法,本方案一方面加快了含水焦油的脱水处理速度,提高了含水焦油的脱水处理效率,而不需要等待含水焦油完成脱水后空置出含水焦油加温静止所需的储存罐,进而提升了含水焦油的生产效率;另一方面通过一次次的共沸蒸馏循环,含水焦油可以在计划的时间内完成脱水处理,不会出现因静止效果不佳需延长脱水处理时间的情况,进而避免了因脱水时间加长而可能造成的焦油质量下降;再一方面,本方案不需要投加大量的破乳剂,降低了含水焦油的脱水处理成本。
[0040]
进一步地,为提高焦油脱水过程中的混合蒸气的冷凝分离效果,热交换器300包括第一热交换器310和第二热交换器320,第一热交换器310与第二热交换器320串联设置。其中,热交换器300可以是间壁式、混合式或蓄热式等,在一实施例中,第一热交换器310和第二热交换器320均采用管式热交换器300,在此不会热交换器300的种类做限制。如此,通过两级低温冷凝换热以提高混合蒸气的冷凝分离效果。
[0041]
具体地,第一热交换器310设有第二进气口,第二进气口与第一出气口220相连通,第一热交换器310上设有第一进水孔311和第一出水孔312,冷却塔600中的循环冷却水通过第一进水孔311进入第一热交换器310,并通过第一出水孔312回流到冷却塔600。在第一热交换器310内,冷却塔600中的循环冷却水从第一进水孔311进入,并从第一出水孔312排出,以与第一热交换器310内的混合蒸气进行热交换,完成混合蒸气的冷凝分离。混合蒸气从过度室200的第一出气口220、第一热交换器310的第二进气口进入第一热交换器310,与第一热交换器310内的循环冷却水完成热交换后,通过第一热交换器310的第二出气口(未示出)进入第二热交换器320。如此完成混合蒸气的第一次冷凝分离,为保证良好的冷凝分离效果,第一热交换器310中的循环冷却水温度不高于35℃。
[0042]
第二热交换器320的第三进气口(未示出)与第一热交换器310的第二出气口相连
通,第二热交换器320上设有第二进水孔321和第二出水孔322,冷冻机700中的冷凝水通过第二进水孔321进入第二热交换器320,并通过第二出水孔322回流到冷冻机700,第二热交换器320设有第二回液口(未示出),第二回液口与第一回液口230相连通。在第二热交换器320内,冷冻机700中的冷凝水从第二进水孔321进入,并从第二出水孔322排出,以与第二热交换器320内的混合蒸气进行热交换,完成混合蒸气的冷凝分离。混合蒸气从第一热交换器310的第二出气口、第二热交换器320的第三进气口进入第二热交换器320,与第二热交换器320内的冷凝水完成热交换后,变成液体,通过第二热交换器320的第二回液口、过度室200的第一回液口230进入过度室200。如此完成混合蒸气的第二次冷凝分离,为保证良好的冷凝分离效果,第二热交换器320中冷凝水温度不高于25℃。
[0043]
如此,从加热罐100上部排出的混合蒸气,经过两级热交换器300冷凝,第一热交换器310中的循环冷却水温度不高于35℃,第二热交换器320中的冷凝水的温度不高于25℃,使混合蒸气经过充分的冷凝,保证了混合蒸气的冷凝效果,进而保证了焦油的脱水效果。同时也避免了因未充分冷凝而造成的混合蒸气的逃逸,进而避免了混合蒸气对大气的污染。
[0044]
进一步地,冷冻机700供冷凝水在第二热交换器320中循环流动,以进行第二热交换器320中的冷凝分离,为解决冷冻机700工作散热的问题,冷却塔600与冷冻机700相连通,冷却塔600中的循环冷却水供冷冻机700散热。在冷却塔600与冷冻机700之间形成循环冷却水的循环路径,使循环冷却水流经冷冻机700,对冷冻机700进行散热,保证了冷冻机700的正常工作温度。在冷却塔600的循环冷却水流动路径中设置循环泵,循环泵可将循环冷却水输送到第一热交换器310和冷冻机700。
[0045]
进一步地,为避免混合蒸气在冷凝过程中逃逸而污染大气,焦油脱水系统还包括吸附装置800,吸附装置800与热交换器300相连通,用于吸附从热交换器300逃逸的尾气,吸附装置800与废气收集系统900相连通。具体地,因混合蒸气中含有共沸剂蒸气,而常用的共沸剂如粗苯、苯、甲苯、环乙烷等,往往为有毒或有害气体,如果不经处理而逃逸则对人体和大气环境造成影响。在本实施例中,吸附装置800与第二热交换器320相连通,用于吸附从第二热交换器320中逃逸的尾气,吸附装置800内可设置有活性炭对逃逸的尾气进行吸附处理。同时,吸附装置800与厂区的废气收集系统900相连通。逃逸的尾气先经吸附装置800吸附处理,然后吸附装置800将吸附处理后的尾气输送到厂区的废气收集系统900,经厂区废气处理系统统一处理,达到排放标准后再排放至大气中,避免了有毒及有害气体对人体和大气的影响。
[0046]
进一步地,为提高共沸蒸馏的效率和效果,加热罐100采用蒸汽盘管10加热。如此,可利用厂区的蒸汽对加热罐100进行加热,为含水焦油和共沸剂的共沸蒸馏提供加热源。一般地,产生出来的含水焦油温度为50
‑
60℃,共沸剂以粗苯为例,粗苯的沸点为60
‑
70℃,故含水焦油与共沸蒸馏的共沸温度差并不大,利用少量的厂区的蒸汽为含水焦油和共沸剂加热,即可达到共沸温度。一方面加热所需的蒸汽量较少,加热成本较低,从而降低了焦油脱水处理成本;另一方面,共沸温度较低,不必对含水焦油和共沸剂进行高温处理,不会因高温而对焦油的品质造成影响。
[0047]
同时,在加热罐100内设置有温度传感器20、压力传感器30以及液位传感器40,以方便对加热罐100内的温度、压力及液位进行及时的调节。
[0048]
为提高共沸蒸馏的效果,加热罐100外设置有加热罐循环泵50,以将加热罐100底
部的混合液泵至加热罐100内的喷淋装置60。因共沸剂与含水焦油的密度不同,以粗苯为例,粗苯比含水焦油的密度小,故大量的粗苯会在含水焦油的上层。在加热罐100的上方设置有喷淋装置60,通过加热罐循环泵50将加热罐100底部的含水焦油抽吸到喷淋装置60中,通过喷淋装置60将含水焦油喷洒至加热罐100的上层,以与上层的粗苯进行充分的混合。如此,一方面喷淋装置60使含水焦油与共沸剂之间的混合更加均匀,有利于共沸蒸馏,另一方面喷淋装置60的喷洒过程也可加大含水焦油和共沸剂的蒸发量,提供共沸蒸馏的效率。另外地,当经过多次的共沸蒸馏在加热罐100的底部得到含水量符合标准的成品焦油,成品焦油可以由加热罐循环泵50输送至焦油大罐。
[0049]
本发明还提出一种焦油脱水方法,该焦油脱水方法包括:将含水焦油和共沸剂的混合物进行气液分离,以获得气体混合物和初级焦油;将气液分离所得的气体混合物通过冷凝分离为液体共沸剂和液体冷凝水;将冷凝分离所得的液体共沸剂与初级焦油混合并进行再次气液分离,并循环以上过程以降低初级焦油的含水量以获得成品焦油。
[0050]
具体工作时,将含水焦油和共沸剂投入到加热罐100中进行加热共沸蒸馏,以进行气液分离,从加热罐100的上部排出混合蒸气,即获得的气体混合物,在加热罐100的底部得到初级焦油。气体混合物经过过度室200、热交换器300进行冷凝分离,得到液体的共沸剂和液体的冷凝水,液体的共沸剂通过分离室400回流到加热罐100,并与加热罐100内的初级焦油混合再次进行气液分离,并循环气液分离、冷凝分离的过程,以降低初级焦油中的含水量,以获得成品焦油。相较于往含水焦油中投加破乳剂并加温静止的脱水方法,本方法一方面加快了含水焦油的脱水处理速度,提高了含水焦油的脱水处理效率,而不需要等待含水焦油完成脱水后空置出含水焦油加温静止所需的储存罐,进而提升了含水焦油的生产效率;另一方面通过一次次的共沸蒸馏循环,含水焦油可以在计划的时间内完成脱水处理,不会出现因静止效果不佳需延长脱水处理时间,进而避免了因脱水时间加长而可能造成的焦油质量下降;再一方面,本方法不需要投加大量的破乳剂,降低了含水焦油的脱水处理成本。
[0051]
以上所述仅为本发明的可选实施例,并非因此限制本发明的专利范围,凡是在本发明的发明构思下,利用本发明说明书及附图内容所作的等效结构变换,或直接/间接运用在其他相关的技术领域均包括在本发明的专利保护范围内。