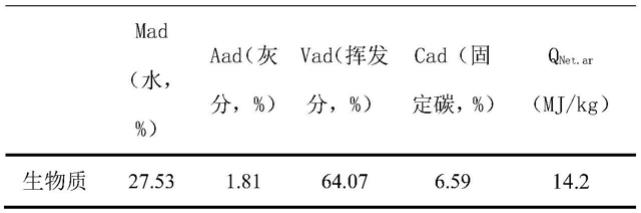
1.本实用新型涉及生物质热解技术领域,尤其是涉及一种实施生物质热解方法的系统。
背景技术:
2.生物质和其他粘性含碳物料(如油田油性污泥、含矿尘泥、工业污泥、危险废液)的热化学转化(如碳化、热解、气化)可产生固态、液态和气态产物,这些产物按需求制成可回收、易利用、易运输及易储存的能源形态,可供热发电或用作化工及其它产业的原料。根据原料不同和热处理目的的差异,可采用碳化、气化、热解、液化或者其他相关的热化学反应和工艺。
3.热解采用的反应器形式很多,如移动床、固定床、流化床、烧蚀床、悬浮炉和回转窑等,其中工业生产以移动床、固定床、回转窑和流化床为主。各种热解方式一般都有其特定的目的,即主要回收热解产物中的某一二种主要物质。
4.相关技术中,低温干馏炉具有升温、降温速度快,操作简单、方便的特点,不锈钢干馏炉可以在隔绝空气下,通过干馏炉炉外四周电热棒加热升温到300~800℃,热解生成固体产物和油气混合物,整个过程耗时30~120分钟。固体产物残留在干馏炉内,油气混合气被引出,经过间冷和直冷后,得到热解油和不凝气。但是此种方式存在以下技术问题:该工艺无法对热解气进行深度净化,导致热解气燃烧后的烟气含杂质高,需进一步净化,导致运行成本增加,并且放大后热解气难以满足内燃机对气体品质要求,而且整个密封采用机械密封,密封效果差,存在安全隐患。
技术实现要素:
5.本实用新型旨在至少解决现有技术中存在的技术问题之一。为此,本实用新型的一个目的在于提出一种实施生物质热解方法的系统,该系统可以有效净化热解气,可以提高热解气的品质。
6.根据本实用新型的实施生物质热解方法的系统,包括:氮气装置;热解装置,所述热解装置与所述氮气装置相连;灰尘分离装置,所述灰尘分离装置与所述热解装置相连;直冷装置,所述直冷装置与所述热解装置相连;间冷装置,所述间冷装置分别与所述直冷装置相连;过滤装置,所述过滤装置与所述间冷装置相连;储气装置,所述储气装置与所述过滤装置相连。
7.由此,根据本实用新型的实施生物质热解方法的系统,采用物理冷却法来减少热解气中焦油和杂质含量,既能达到深度净化要求,又能避免因化学法带来运行成本极高问题。而且,采用分级冷却净化系统,可分别获取轻质油品和重质油,提高油品的外售价格。采用分级冷却净化系统,减轻活性炭和热解炭的运行负荷,提高使用寿命。
8.在本实用新型的一些示例中,所述间冷装置还与所述热解装置相连。
9.在本实用新型的一些示例中,所述直冷装置为多个,多个所述直冷装置顺次相连。
10.在本实用新型的一些示例中,所述系统还包括:换热装置和制冷机,所述换热装置、所述制冷机、所述直冷装置和所述间冷装置之间连接有冷却液管路。
11.在本实用新型的一些示例中,所述直冷装置具有热解油气进口和冷却液进口,所述热解油气进口位于所述热解装置的底部,所述冷却液进口位于所述热解装置的顶部。
12.在本实用新型的一些示例中,所述过滤装置包括冷阱和过滤器,所述冷阱连接在所述间冷装置和所述过滤器之间。
13.在本实用新型的一些示例中,所述冷阱为多个且顺次相连,所述过滤器为多个且顺次相连。
14.在本实用新型的一些示例中,所述系统还包括:质量流量计,所述质量流量计设置在所述过滤器和所述储气装置之间。
15.本实用新型的附加方面和优点将在下面的描述中部分给出,部分将从下面的描述中变得明显,或通过本实用新型的实践了解到。
附图说明
16.本实用新型的上述和/或附加的方面和优点从结合下面附图对实施例的描述中将变得明显和容易理解,其中:
17.图1是根据本实用新型实施例的生物质热解方法的工艺流程图;
18.图2是根据本实用新型实施例的生物质热解方法的步骤示意图;
19.图3是根据本实用新型实施例的实施生物质热解方法的系统的示意图。
20.附图标记:
21.系统100;
22.氮气装置1;热解装置2;灰尘分离装置3;直冷装置4;间冷装置5;换热装置6;制冷机7;冷阱8;过滤器9;质量流量计10;真空泵11;储气装置12;泵13。
具体实施方式
23.下面参考图1和图2描述根据本实用新型实施例的生物质热解方法。
24.如图1所示,根据本实用新型实施例的生物质热解方法可以包括以下步骤:s1、将生物质送入热解装置2中,热解装置2进行液体密封后进行热解,得到热解油气和热解炭。该热解装置2对原料无严格的要求,即可满足处理不同形状的原料。热解装置2包括料框,针对不同原料选用不同的料框。根据物料的特性,当用于处理粒径≥1mm的粒状料,料框选用不同孔径的网状料框;当用于处理粉料时,料框选用无孔料框。因此,该热解装置2可满足各种废弃物包括生物质、医疗污泥、化工污泥、制药厂废弃物、造纸厂废弃物、废弃电路板的处理,也可满足的废旧轮胎、废塑料、生物质、煤、油页岩等资源化回收利用。
25.热解装置2可以包括:热解炉,热解炉包括顶盖和炉体,顶盖和炉体之间采用液体密封,例如,炉体可以设置有液封槽,顶盖的下端伸入液封槽内以进行液体密封。液体密封可以提高热解装置2的密封效果,操作方便,而且一旦热解装置2出线超压异常,也能及时泄压,安全可靠。
26.将备好的物料装入料框后,放入热解炉中,关上炉门并接上氮气连接管和热解气出口连接管,在确保整个油气管道阀门开启时,向炉膛通入一定量氮气,氮气由氮气装置1
提供,将整个系统100内部置换2
‑
3次,排除内部空气,关上放气阀,确保整个系统100的气密性良好。其中,氮气装置1可以为氮气瓶。
27.热解装置还包括:电子计量装置,电子计量装置可以为电子计量秤。将电子计量秤与物料料框连接杆连接,在远程电脑控制系统100中设置升温程序,通常整个升温分为三个阶段,三个阶段分别为干燥阶段、热解阶段和热裂解阶段,干燥阶段是将热解装置2内部温度升高至第一预定温度,并保温第一预定时间,热解阶段是将热解装置2内部温度从第一预定温度升高至第二预定温度,并保温第二预定时间,热裂解阶段是将热解装置2内部温度从第二预定温度升高至第三预定温度,并保温第三预定时间。
28.具体地,第一阶段为干燥过程,将炉膛温度升高至300℃后保温5
‑
100min,优选15
‑
45min,升温速率控制在5
‑
50℃/min,优选15
‑
30min;第二阶段为热解阶段,将炉膛温度从300℃升高至500℃后保温5
‑
100min,优选20
‑
60min,升温速率控制在5
‑
50℃/min,优选15
‑
30min;第三阶段为热裂解阶段,将炉膛温度从500℃升高至1000℃后保温5
‑
100min,优选10
‑
30min,升温速率控制在15
‑
30℃/min,优选15
‑
25min。停炉时间主要通过热解结束后物料质量改变情况来判断。判断依据通过热解过程中电子计量秤数据的变化情况来控制炉膛的结束,其判断依据是持续30分钟电子计量秤显示的数据相差0.5%以内,表明热解完成,加热装置自动关停。
29.热解装置2包括热解炉和加热器,开启加热器,热量由热解炉四周向炉膛内辐射加热,料框外侧物料先升温,升温后的物料向内不断传热,加快炉内物料温度升高。对于颗粒料采用带网状的料框盛放物料,增强辐射传热作用,提高物料升温速度。随着不断加热,物料不断升温,被干燥产生的水蒸汽先进入后端,然后有机轻组分开始挥发,随后是重组分发生裂解。整个过程中,因各温度段的组分含量不同,发生反应的时间也存在一定差异,直接的表现是电子计量秤显示的固体物料重量在不断减少,同时在远程控制电脑显示出重量改变随温度变化曲线。炉膛四周加热管外侧采用耐高温保温材料,可以单独拆卸和安装,从而进行安装和更改单根或是多根加热管,增加使用寿命。
30.在加热管加热的作用下,原料在密闭空间内被逐渐加热,在200
‑
1000℃的温度下、15
‑
240分钟,生成气体产物、液体产物和固体产物。整个热解过程中,炉膛压力控制在
±
2kpa之间。所产生的气态物质经由油气出口被快速引出炉膛。上述油气出口数量为1
‑
6个,分别布置于炉顶和炉底。
31.s2、将热解油气送入冷却装置中进行冷却,得到热解油和热解气。需要说明的是,由于热解油气中含有灰尘,热解油气在进入到冷却装置之前可以先经过灰尘分离装置3,灰尘分离装置3可以将灰尘清除,具体地,灰尘分离装置3可以为旋风分离器。
32.物料加热产生的气体产物在真空泵11的作用下,经由热解炉炉顶或炉底(根据原料或是工艺具体要求选择炉顶或是炉底的油气出口)路线引出至旋风分离器进行除尘,将气体中带出的少量粉尘脱除掉,分别送入直冷装置4和间冷装置5中。其中,直冷装置4可以为直冷塔,间冷装置5可以为间冷塔。也就是说,热解油气出口可分为两路,一路与直冷装置4的热解油气进口相连,另一路与间冷塔的热解油气进口相连。
33.当然,还可以将直冷装置4冷却后的热解油气送入间冷装置5内。如此,经过多次冷却过滤,可以有效地将热解油气降温冷却,可以分离出热解油。其中,选用多个直冷装置4,这样经过多级冷却之后,热解气可以再进入到间冷装置5中,这样热解气的温度较低,含油
率也较低。
34.直冷装置4与换热装置6相连,制冷机7可以为直冷装置4和换热装置6提供冷却液。如图3所示,为确保将大部分重质油冷却回收,采用制冷机7对直冷塔冷却液进行换热降温,冷却液的温度始终维持在80℃以下,优选10
‑
50℃,通过调节阀门控制热解气串联经过两个直冷塔,或是单独经过每个直冷塔。通过直冷塔冷却后的热解气进入间冷塔中,与冷却液进行间接换热,换热装置6中的冷却液进口温度控制在20℃以下,优选5
‑
15℃,热解气出间冷塔温度可控制在65℃以下,优选30
‑
45℃,可满足大部分轻质油的冷却。
35.s3、将热解气送入过滤装置中进行过滤。其中,将经过冷阱8冷却的热解气经过过滤器9。考虑到热解气在间冷塔内停留时间有限,部分热解气即使达到露点以下,但难以在间冷塔内冷却下来,同热解气一并进入冷阱8中进一步冷却和冷凝。其中两个冷阱8既可以串联使用也可以并联单独使用,可根据热解气的气量和温度来调整。当热解气气速快,温度高,难以冷却时,可以通过调节制冷机7阀门和循环液温度加快冷却效果。采用此冷却器,既可以达到直冷效果又可以达到间冷的冷却效果,并且不会影响油的品质,同时易拆卸清洗。
36.冷却液、换热装置6、泵13和制冷机7之间的连接关系:冷却液与热解气在直冷塔中换热后,进入换热装置6中被冷介质冷却,冷介质来源于制冷机7,冷却液的温度始终维持在80℃以下,优选10
‑
50℃。间冷塔冷却液的来源是制冷机7的冷介质。
37.s4、将过滤后的热解气存储在储气装置12中。经过直冷塔、间冷塔和冷阱8冷却后的热解气中98%的热解油被冷凝,但因热解气在整个冷阱8内停留时间较短,还有1
‑
1.8%的热解油随热解气一起进入后段过滤器9中。热解气从过滤器9的底部通入,通过气体分布器将热解气均匀分布在过滤器9底部,热解气先经过热解炭时可将热解气中的微小油滴脱附下来,当热解气进入活性炭层之后,热解气中的杂质气体和微量焦油被进一步脱附。通过过滤器9后热解气中的焦油含量降至50mg/nm3,大多数物料热解气的焦油含量可降至20mg/nm3以内,可作为能源满足大多数高标准的燃气系统100使用,达到长期满负荷运行,如燃气轮机、蓄热式辐射管等。
38.通过二级过滤器9后的热解气在真空泵11的作用下被引出,先通过质量流量计10对燃气进行计量,最终得到的不凝气送入储气装置12中进行储存或送入燃烧器中进行燃烧。在质量流量计10和真空泵11之间设置有气袋取气装置,来收集少量混合气用于检测气体成分。储气装置12为气罐或者气柜。
39.由此,根据本实用新型实施例的生物质热解方法,采用物理冷却法来减少热解气中焦油和杂质含量,既能达到深度净化要求,又能避免因化学法带来运行成本极高问题。而且,热解装置2采用液体密封,一方面密封效果比机械密封好、操作快捷方便,另一方面一旦炉膛出现超压异常,也能及时泄压,安全可靠。
40.如图3所示,根据本实用新型实施例的实施生物质热解方法的系统100,包括:氮气装置1、热解装置2、直冷装置4、间冷装置5、过滤装置和储气装置12。
41.热解装置2与氮气装置1相连,氮气装置1为氮气瓶,热解装置2包括热解炉、料框、计算机控制终端,热解炉设有氮气入口、物料进口、热解油气出口、热解炭出口,所述料框置于热解炉的中心,料框可以为圆柱形,通过连接杆与上方电子计量装置连接,电子计量装置与远程计算机相连。其中,电子计量装置为电子计量秤。
42.氮气入口设置在热解炉底部与氮气瓶出口连接,在热解开始前和热解结束后用于
炉膛通入氮气,对炉膛气氛进行置换,每次吹扫维持在3
‑
15min,氮气流速控制在5
‑
60l/min,氮气单次吹扫量控制在炉膛体积的3
‑
20倍,因此可以根据炉膛的体积来控制总的吹扫时间。
43.系统100还包括灰尘分离装置3,灰尘分离装置3可以为旋风分离器,旋风分离器包括热解油气进口、热解油气出口,热解油气进口与热解炉的热解油气出口相连,满足热解油气产物除尘要求。为了满足电子计量秤记录的数据为料框和物料的数据,料框的连接管与热解炉顶部盖采用水封或其他液封装置,整个热解过程炉膛压力控制在
±
2kpa,因此液封槽高度控制在25cm以上。
44.在热解过程中随着物料热裂解进行,物料的重量在不断减少,电子计量秤的计量数据随之不断改变,电子计量秤通过与远程计算机连接,可在计算机中显示物料质量随热解时间的变化曲线。热解过程中通过电子计量秤数据的变化情况来控制炉膛的结束,其判断依据是持续30分钟电子计量秤显示数据相差0.5%以内,表明热解完成,加热装置自动关停。其中,采用电子记录秤和远程计算机控制系统,直接获取物料热解过程的失重曲线,为工程应用提供数据支撑。
45.热解炉外壁四周设置有均匀布置的加热装置,当设计为小型热解炉单次处理能力在50kg以内可采用电加热棒进行加热,当单次处理能力在50kg以上时可选择蓄热式辐射管加热装置进行加热。加热管位于整个炉膛外出四周均匀布置,辐射管最高设计温度选1200℃。另外根据热解物料的差异,也可选用熔融盐作为加热源加热物料。根据物料的特性,当用于处理粒径≥1mm的粒状料,料框选用不同孔径的网状料框;当用于处理粉料时,料框选用无孔料框。而且,热解炉采用液体密封,一方面密封效果比机械密封好、操作快捷方便,另一方面一旦炉膛出现超压异常,也能及时泄压,安全可靠。
46.直冷装置4通过旋风分离器与热解装置2相连,间冷装置5直冷装置4相连,另外,间冷装置5还可以与热解装置2相连。其中,旋风分离器的热解油气出口可分为两路,一路与直冷装置4的热解油气进口相连,另一路与间冷装置5的热解油气进口相连。直冷装置4为直冷塔,直冷塔包括冷却液进口、热解油气进口、热解气出口、冷却液出口,冷却液进口位于直冷塔顶部,热解油气进口位于直冷塔底部,冷却液进口与泵13相连,冷却液出口与换热装置6相连。
47.直冷装置4为多个,多个直冷装置4顺次相连。如图3所示,直冷塔可以为两个,各塔可单独使用或串联使用。这样热解气可以经过多级冷却,从而可以更好地分离热解油。
48.间冷装置5为间冷塔,间冷塔单元冷却液进口、热解油气进口、热解气出口、热解油出口,间冷塔为两个,各塔可单独使用或串联使用,热解油气进口与直冷塔的热解油气出口相连,冷却液进口与制冷机7的冷却液出口相连,间冷塔可以单级设置或串联多级设置。进一步地,间冷塔可以为盘管式换热器、板式换热器。
49.如图3所示,过滤装置与间冷装置5相连,过滤装置可以包括冷阱8和过滤器9,冷阱8连接在间冷装置5和过滤器9之间,冷阱8包括热解气进口、冷液进口、热解气出口。
50.冷阱8为多个,而且多个冷阱8顺次相连,过滤器9为多个,多个过滤器9顺次相连。冷阱8可设置为单级或串联多级,冷阱8的热解气进口与间冷塔的热解油气出口相连,冷液进口与制冷机7的冷却液出口相连。过滤器9连接在冷阱8和储气装置12之间,过滤器9也可以为两个,两个过滤器9可以为单级或串联多级。
51.换热装置6、制冷机7、直冷装置4和间冷装置5之间串联有冷却液管路。由间冷塔送来温度低于65℃的热解气送入两个冷阱8中,热解气走管内,冷却液走壳内,将热解气温度降至20℃以内。此时热解气中98%的热解油被冷凝,但因热解气在整个冷阱8内停留时间较短,还有1
‑
1.8%的轻质油随热解气一起进入后段过滤器9中。在两个过滤器9分别装入粒径为3
‑
8mm的活性炭和1
‑
5mm的热解炭,热解炭装在过滤器9的底部和顶部,活性炭装在中间,活性炭的填装量为热解炭填装量的1.5
‑
3倍。热解气从过滤器9的底部通入,通过气体分布器将热解气均匀分布在过滤器9底部,热解气先经过热解炭可将热解气中的微小油滴脱附下来,当热解气进入活性炭层之后,热解气中的杂质气体和微量焦油被进一步脱附。通过过滤器9后热解气中的焦油含量降至50mg/nm3以内,大多数物料热解气的焦油含量可降至20mg/nm3以内,可作为能源满足大多数高标准的燃气系统100使用,达到长期满负荷运行,如燃气轮机、蓄热式辐射管等。
52.燃气计量和储存包括质量流量计10、真空泵11和储气装置12。通过净化后的燃气在真空泵11的作用下从过滤器9引出,先通过质量流量计10对燃气进行计量,最终得到的燃气送入储气装置12中进行储存。
53.由此,根据本实用新型实施例的实施生物质热解方法的系统100,采用物理冷却法来减少热解气中焦油和杂质含量,既能达到深度净化要求,又能避免因化学法带来运行成本极高问题。而且,采用分级冷却净化系统100,可分别获取轻质油品和重质油,提高油品的外售价格。采用分级冷却净化系统100,减轻活性炭和热解炭的运行负荷,提高使用寿命。
54.下面给出具体实施例。
55.粒度0.5~1mm的生物质(生物质分析数据见表1)。将备好的物料装入料框后,单次装入量为10kg放入热解炉中,关上炉门并接上氮气连接管和热解气出口连接管,检查炉膛气密性无异常后,在远程电脑控制系统100中设置升温程序,通常整个升温设为三个阶段,第一阶段:将炉膛温度升高至300℃后保温30min,升温速率控制在15℃/min;第二阶段:将炉膛温度从300℃升高至500℃后保温50min,升温速率控制在30℃/min;第三阶段:将炉膛温度从500℃升高至850℃后保温30min,升温速率控制在15℃/min。加热管加热的作用下,原料在密闭空间内被逐渐加热,生成气体产物、液体产物和固体产物。整个热解过程中,炉膛压力控制在
±
500pa之间。所产生的气态物质经由顶部油气出口被快速引出炉膛。热解产生的混合热解气进入旋风分离器中分离,脱除气体中粉尘后的热解气进入两级串联直冷塔进一步冷却,热解油气经过一级直冷塔喷淋冷却后,部分重质油被冷却后随着冷却液进入循环液罐中,未被冷却的油气通过直冷塔顶部气体导淋管送入二级直冷塔中,热解油气与冷却液逆向进一步接触,大部分重质油被冷却后随冷却液一并进入循环液罐中,进入一级直冷塔的油气温度最高时为560℃,离开二级直冷塔热解气温度最低降至70℃。通过真空循环冷却液泵13产生的低温水或液氨与循环液罐中的液体进行间接换热,控制循环液罐中的液体温度不超过65℃。通过直冷塔冷凝后的热解气进入盘管换热器中,通过二级盘管换热器换热,可将热解气温度进一步降低至50℃以下,其中部分轻质油得以冷凝和回收,而另一部轻质油随热解气一并进入后段。盘管换热器所需换热的制冷液来源于真空循环冷却液泵13。由盘管换热器送来温度低于50℃的热解气送入两级冷阱8中,热解气走管内,制冷液走壳内,将热解气温度降至20℃以内。冷阱8所需换热的制冷液来源于真空循环冷却液泵13。通过冷阱8冷却后的热解气进入后段二级过滤器9中,热解气从过滤器9的底部通入,通过气
体分布器将热解气均匀分布在过滤器9底部,热解气中的低露点焦油和杂质气体被进一步脱除。通过二级过滤器9后的热解气在真空泵11的作用下被引出,先通过质量流量计10对燃气进行计量,最终得到的不凝气送入气罐中进行储存或送入燃烧器中进行燃烧。通过对炭吸附后的热解不凝气中的焦油含量进行检测,多次检测的值控制在1
‑
9mg/nm3之间。
56.本实用新型所述工艺方法可长期平稳操作,所得到比较稳定的热解产物的产率和主要性质见表1。
57.表1生物质原料分析结果
[0058][0059]
本实用新型所述工艺方法可长期平稳操作,设备故障率极低。
[0060]
在本说明书的描述中,参考术语“一个实施例”、“一些实施例”、“示意性实施例”、“示例”、“具体示例”、或“一些示例”等的描述意指结合该实施例或示例描述的具体特征、结构、材料或者特点包含于本实用新型的至少一个实施例或示例中。在本说明书中,对上述术语的示意性表述不一定指的是相同的实施例或示例。
[0061]
尽管已经示出和描述了本实用新型的实施例,本领域的普通技术人员可以理解:在不脱离本实用新型的原理和宗旨的情况下可以对这些实施例进行多种变化、修改、替换和变型,本实用新型的范围由权利要求及其等同物限定。