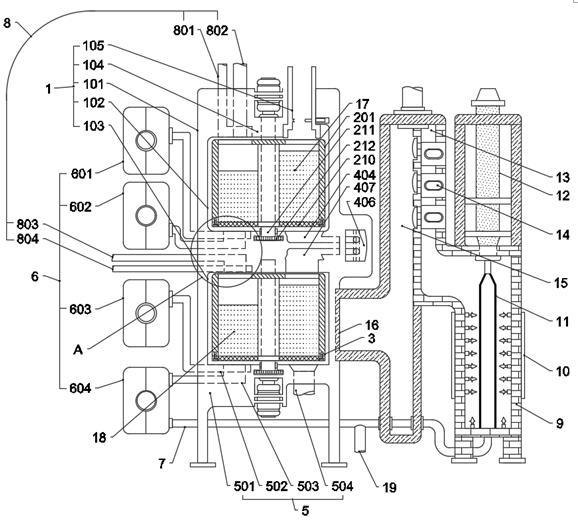
1.本发明属于石油加工技术领域,具体是涉及一种石脑油裂解装置。
背景技术:
2.石脑油是一种轻质油品,由原油蒸馏或石油二次加工切取相应馏分而得,是管式炉裂解制取乙烯和丙烯,催化重整制取苯、甲苯和二甲苯的重要原料,石脑油裂解法是石脑油在高温条件下裂化成较小的分子,小分子通过自由基反应形成气态轻质烯烃。
3.我国原油偏重导致石脑油的收率较低,存在乙烯裂解与催化重整原料供应不足的问题,为了提高石脑油的利用效率,通过对石脑油中的正构烷烃与非正构烷烃进行分离,所得的正构烷烃部分可作为优质乙烯裂解原料,非正构烷烃部分可作为优质催化重整原料或高辛烷值汽油调和组分,对于芳烃指数较高的裂解原料,易产生结焦现象,结焦过程易发生在对流段、辐射段和废热锅炉工艺侧,随着结焦过程加剧,管内流动阻力和传热过程恶化,导致管内压降增大、辐射炉管表面温度和废热锅炉出口温度升高,迫使裂解炉进行周期性停料清焦。
4.目前工业生产中的全馏分石脑油吸附处理设备都是通过分子筛吸附柱对原料进行吸附处理,并且吸附柱在置换和脱附过程中,置换剂和脱附剂都需要完全穿透吸附柱,在柱状分子筛中置换剂和脱附剂的渗透速率较慢,影响整体的反应速效,降低了正构烷烃的脱附效率。
技术实现要素:
5.针对现有技术存在的不足,本发明实施例的目的在于提供一种石脑油裂解装置,以解决上述背景技术中的问题。
6.为实现上述目的,本发明提供如下技术方案:一种石脑油裂解装置,包括裂解炉,所述石脑油裂解装置还包括:预处理机构,所述预处理机构中包括第一处理腔和第二处理腔,分别用于对石脑油原料进行脱芳烃处理以及正构烷烃提取;芳烃吸附组件,回转布设于第一处理腔中,其中包括回转壳体,所述回转壳体内布设有若干的筛分腔体,且筛分腔体的数量至少为3个,用于循环处理石脑油原料,所述筛分腔体内均布设有一阶分子筛层,用于对石脑油原料进行脱芳烃处理,且所述筛分腔体内均活动装配有回转板,所述回转板与筛分腔体的内壁滑动密封抵接,回转板一侧与一阶分子筛层相接,用于推动一阶分子筛层在筛分腔体中运动,用以滑动调节所述一阶分子筛层在回转壳体中的横截面积;正构烷烃提取组件,布设于第二处理腔中,所述正构烷烃提取组件与芳烃吸附组件结构相同,且其内布设有二阶分子筛层,用于对脱芳烃处理后的石脑油原料进行正构烷烃的提取;芳烃排料组件,布设于芳烃吸附组件与正构烷烃提取组件之间,其内弹性装配有
若干的弹性封堵片二,用于配合芳烃吸附组件的转动对芳烃吸附组件内若干筛分腔体进行隔绝密封,同时用于排出芳烃吸附组件内若干筛分腔体中不同的反应产物;正构烷烃排料组件,布设于正构烷烃提取组件一侧,用于排出正构烷烃提取组件中不同的反应产物;分离釜组件,与所述芳烃排料组件和正构烷烃排料组件相连通,用于对芳烃吸附组件和正构烷烃提取组件中的反应产物进行分离,以使经由脱芳烃处理并进行正构烷烃提取后的原料送入裂解炉中进行裂解;以及输入管组,用于向所述芳烃吸附组件和正构烷烃提取组件中输入置换剂和脱附剂,用以排出所述一阶分子筛层和二阶分子筛层中吸附的物质,以使所述芳烃吸附组件和正构烷烃提取组件能够循环处理石脑油原料。
7.作为本发明进一步的方案,所述预处理机构还包括:外壳体,用于活动装配所述芳烃吸附组件与正构烷烃提取组件;进料构件,靠近芳烃吸附组件顶部一侧设置,其内弹性装配有若干弹性封堵片,所述弹性封堵片用于配合芳烃吸附组件的转动对芳烃吸附组件中的若干筛分腔体进行隔绝密封;以及原料管组,布设于外壳体一侧,且靠近芳烃吸附组件一侧设置,用于优先向芳烃吸附组件中输入待处理的石脑油原料。
8.作为本发明进一步的方案,所述进料构件还包括:原料进槽,布设于进料构件一侧,与原料管组相连通;置换剂进槽,布设于原料进槽一侧,且开口面积大于所述原料进槽,用于向芳烃吸附组件中输入置换剂;以及脱附剂进槽,布设于置换剂进槽一侧,且开口面积大于所述置换剂进槽,用于向芳烃吸附组件中输入脱附剂。
9.作为本发明进一步的方案,所述芳烃吸附组件还包括:隔断壁,布设于若干筛分腔体之间,且其上开设有若干定位槽口,所述定位槽口靠近回转壳体顶部一侧设置,用于配合弹性封堵片对若干筛分腔体进行隔绝密封;定位槽口二,布设于回转壳体底部一侧,用于配合所述弹性封堵片二对回转壳体底部进行隔绝密封;压条,固定布设于定位槽口与定位槽口二一侧,用于在所述回转壳体转动时推动所述弹性封堵片与弹性封堵片二的弹性滑动;导向件,固定布设于筛分腔体之间,用于限定回转板的滑动方向,且所述回转板与隔断壁之间装配有弹性件,用于驱动回转板的弹性复位;以及孔板,靠近回转壳体底部一侧设置,用于对若干筛分腔体中的一阶分子筛层进行承托。
10.作为本发明进一步的方案,所述芳烃吸附组件还包括:磁极滑动部,装配于回转板末端,且布设于回转板和筛分腔体的内壁之间;以及固定电磁片,固定装配于第一处理腔的内壁上,用于通过脉冲电流对所述磁极滑动部进行吸附,以使所述回转板在回转壳体转动的过程中,相对回转壳体以设定角度旋转,从而调节筛分腔体中一阶分子筛层的横截面积。
11.作为本发明进一步的方案,所述芳烃排料组件还包括:基座,固定装配于外壳体中;置换剂排出槽,朝向所述回转壳体底部一侧设置,且与所述置换剂进槽匹配设置,用于排出置换剂排出液;脱附剂排出槽,朝向所述回转壳体底部一侧设置,且与所述脱附剂进槽匹配设置,用于排出脱附剂排出液;以及脱芳烃液排出槽,朝向所述回转壳体底部一侧设置,且与所述原料进槽匹配设置,用于排出石脑油脱芳烃排出液。
12.作为本发明进一步的方案,所述裂解炉中布设有加热壁,所述加热壁一侧与正构烷烃提取组件装配相接,用于为正构烷烃提取组件中的反应提供热能。
13.综上所述,本发明实施例与现有技术相比具有以下有益效果:本发明通过回转布设于预处理机构中的芳烃吸附组件和正构烷烃提取组件,能够循环对石脑油原料进行预处理,降低石脑油原料中的芳烃组分,并提高预处理产物中正构烷烃的组分,有效降低裂解炉内的结焦情况,提升裂解产物中烯烃的收率,并且利用可改变分子筛横截面积的芳烃吸附组件和正构烷烃提取组件,有效提升分子筛的筛分速效,减少所需反应时间,达到提升产值的目的。
14.为更清楚地阐述本发明的结构特征和功效,下面结合附图与具体实施例来对本发明进行详细说明。
附图说明
15.图1为本发明的一种实施例中提供的石脑油裂解装置的结构示意图。
16.图2为本发明的一种实施例中提供的石脑油裂解装置中图示标记a的结构示意图。
17.图3为本发明的一种实施例中提供的石脑油裂解装置中芳烃吸附组件的立体结构示意图。
18.图4为本发明的一种实施例中提供的石脑油裂解装置中芳烃吸附组件的俯视图。
19.图5为本发明的一种实施例中提供的石脑油裂解装置中芳烃排料组件的结构示意图。
20.图6为本发明的一种实施例中提供的石脑油裂解装置中进料构件的结构示意图。
21.附图标记:1
‑
预处理机构;101
‑
外壳体;102
‑
第一处理腔;103
‑
第二处理腔;104
‑
进料构件;1041
‑
原料进槽;1042
‑
置换剂进槽;1043
‑
脱附剂进槽;1044
‑
弹性封堵片;105
‑
原料管组;2
‑
芳烃吸附组件;201
‑
回转壳体;202
‑
筛分腔体;203
‑
隔断壁;204
‑
定位槽口;205
‑
定位槽口二;206
‑
压条;207
‑
导向件;208
‑
回转板;209
‑
弹性件;210
‑
孔板;211
‑
驱动轴;212
‑
振动齿盘;213
‑
磁极滑动部;214
‑
固定电磁片;3
‑
正构烷烃提取组件;4
‑
芳烃排料组件;401
‑
基座;402
‑
置换剂排出槽;403
‑
脱附剂排出槽;404
‑
脱芳烃液排出槽;405
‑
弹性封堵片二;406
‑
储液器;407
‑
出液管道;5
‑
正构烷烃排料组件;501
‑
底座;502
‑
正构烷烃置换剂排出管;503
‑
正构烷烃脱附剂排出管;504
‑
异构烷烃排出管;6
‑
分离釜组件;601
‑
第一釜体;602
‑
第二釜体;603
‑
第三釜体;604
‑
第四釜体;7
‑
正构烷烃管路;8
‑
输入管组;801
‑
第一进液管;802
‑
第二进液管;803
‑
第三进液管;804
‑
第四进液管;9
‑
裂解炉;10
‑
烧嘴组件;11
‑
辐射管;12
‑
急冷锅炉;13
‑
排烟管;14
‑
对流管组;15
‑
对流腔体;16
‑
加热壁;17
‑
一阶分子筛层;18
‑
二阶分子
筛层;19
‑
稀释蒸汽管。
具体实施方式
22.以下结合具体实施例对本发明的具体实现进行详细描述。
23.请参阅图1
‑
图6,本发明的一种实施例中的石脑油裂解装置,包括裂解炉9,所述石脑油裂解装置还包括:预处理机构1,所述预处理机构1中包括第一处理腔102和第二处理腔103,分别用于对石脑油原料进行脱芳烃处理以及正构烷烃提取;芳烃吸附组件2,回转布设于第一处理腔102中,其中包括回转壳体201,所述回转壳体201内布设有若干的筛分腔体202,且筛分腔体202的数量至少为3个,用于循环处理石脑油原料,所述筛分腔体202内均布设有一阶分子筛层17,用于对石脑油原料进行脱芳烃处理,且所述筛分腔体202内均活动装配有回转板208,所述回转板208与筛分腔体202的内壁滑动密封抵接,回转板208一侧与一阶分子筛层17相接,用于推动一阶分子筛层17在筛分腔体202中运动,用以滑动调节所述一阶分子筛层17在回转壳体201中的横截面积;正构烷烃提取组件3,布设于第二处理腔103中,所述正构烷烃提取组件3与芳烃吸附组件2结构相同,且其内布设有二阶分子筛层18,用于对脱芳烃处理后的石脑油原料进行正构烷烃的提取;芳烃排料组件4,布设于芳烃吸附组件2与正构烷烃提取组件3之间,其内弹性装配有若干的弹性封堵片二405,用于配合芳烃吸附组件2的转动对芳烃吸附组件2内若干筛分腔体202进行隔绝密封,同时用于排出芳烃吸附组件2内若干筛分腔体202中不同的反应产物;正构烷烃排料组件5,布设于正构烷烃提取组件3一侧,用于排出正构烷烃提取组件3中不同的反应产物;分离釜组件6,与所述芳烃排料组件4和正构烷烃排料组件5相连通,用于对芳烃吸附组件2和正构烷烃提取组件3中的反应产物进行分离,以使经由脱芳烃处理并进行正构烷烃提取后的原料送入裂解炉9中进行裂解;以及输入管组8,用于向所述芳烃吸附组件2和正构烷烃提取组件3中输入置换剂和脱附剂,用以排出所述一阶分子筛层17和二阶分子筛层18中吸附质,以使所述芳烃吸附组件2和正构烷烃提取组件3能够循环处理石脑油原料。
24.本实施例在实际应用时,当全馏分石脑油原料经由预处理机构1处理送入裂解炉9前,全馏分石脑油首先进入预处理机构1中的芳烃吸附组件2内,并送入芳烃吸附组件2内的一组筛分腔体202中,此时全馏分石脑油在筛分腔体202内一阶分子筛层17的吸附作用下,其中所包含的芳烃被一阶分子筛层17吸附,含有正异构烷烃的排出液穿过一阶分子筛层17进入正构烷烃提取组件3中,并经由正构烷烃提取组件3中的二阶分子筛层18将正构烷烃吸附,最终将含有异构烷烃的排出液通过正构烷烃提取组件3一侧排出,此时芳烃吸附组件2和正构烷烃提取组件3在外部驱动作用下旋转,使得未吸附芳烃组分一侧的筛分腔体202替换当前已吸附芳烃组分的筛分腔体202,且此时该组筛分腔体202中的一阶分子筛层17在跟随回转壳体201转动的过程中,通过回转板208的转动作用,使得回转板208与筛分腔体202之间的容积增大,在一阶分子筛层17总质量分数不变的情况下,一阶分子筛层17的横截面积增大,此时通入置换剂的过程中,置换剂能够充分与一阶分子筛层17接触,并将一阶分子筛层17孔隙间无效容积中的石脑油原料排出,并输送至分离釜组件6中进行分离,并且当该侧筛分腔体202转动至脱附剂一侧进行脱附时,所述回转板208的旋转角度再次增大,使得一阶分子筛层17的横截面积继续增大,当脱附剂通入筛分腔体202中时,能够更加充分的与一阶分子筛层17接触,并将一阶分子筛层17中吸附的芳烃析出,并排出到分离釜组件6中进
行分离,此时该侧筛分腔体202中不含芳烃以及正异构烷烃组分,可再次旋转至石脑油进料口一侧进行芳烃的吸附,所述正构烷烃提取组件3能够吸附脱芳烃排出液中的正构烷烃,并通过脱附剂析出二阶分子筛层18中的正构烷烃,原理与芳烃吸附组件2相同,此处不做赘述,获得的正构烷烃经由正构烷烃管路7输送至裂解炉9中经裂解得到所需的裂解气产物。
25.在本实施例中,通过回转布设于预处理机构1中的芳烃吸附组件2和正构烷烃提取组件3,能够循环对石脑油原料进行预处理,降低石脑油原料中的芳烃组分,并提高预处理产物中正构烷烃的组分,有效降低裂解炉内的结焦情况,提升裂解产物中烯烃的收率,并且利用可改变分子筛横截面积的芳烃吸附组件2和正构烷烃提取组件3,有效提升了分子筛的筛分速效,减少反应时间,达到提升产值的目的。
26.在本实施例中的一种情况中,所述一阶分子筛层17优选采用层析硅胶固体吸附剂,能够快速有效脱出石脑油原料中的芳烃组分,且对正异构烷烃组分的影响较小,所述二阶分子筛层18优选采用5a分子筛,可快速吸附c3
‑
c4正构烷烃,适用于正异构烷烃的分离,上述两种组分的分子筛均为石脑油处理中的常用吸附剂,为本领域中的公知常识,此处不做具体赘述。
27.在本实施例中的一种情况中,所述芳烃吸附组件2和正构烷烃提取组件3中的置换剂均可采用惰性气体例如氮气进行置换,所述芳烃吸附组件2中的脱附剂可采用正辛醇进行脱附,所述正构烷烃提取组件3可采用正丁烷进行脱附,此处不做具体限定。
28.请参阅图1,在发明的一种优选实施例中,所述预处理机构1还包括:外壳体101,用于活动装配所述芳烃吸附组件2与正构烷烃提取组件3;进料构件104,靠近芳烃吸附组件2顶部一侧设置,其内弹性装配有若干弹性封堵片1044,所述弹性封堵片1044用于配合芳烃吸附组件2的转动对芳烃吸附组件2中的若干筛分腔体202进行隔绝密封;以及原料管组105,布设于外壳体101一侧,且靠近芳烃吸附组件2一侧设置,用于优先向芳烃吸附组件2中输入待处理的石脑油原料。
29.本实施例在实际应用时,所述进料构件104中的弹性封堵片1044弹性插装于进料构件104中,并且随回转壳体201的转动能够卡紧于回转壳体201一侧,使得所述的若干筛分腔体202之间隔绝封闭,防止不同组分的液体渗漏。
30.在本实施例中的一种情况中,所述原料管组105一侧的石脑油原料送进与回转壳体201的转动联动设置,以使所述回转壳体201在转动切换过程中切断石脑油原料的送进,确保石脑油原料稳定输送至各个筛分腔体202中。
31.请参阅图6,在发明的一种优选实施例中,所述进料构件104还包括:原料进槽1041,布设于进料构件104一侧,与原料管组105相连通;置换剂进槽1042,布设于原料进槽1041一侧,且开口面积大于所述原料进槽1041,用于向芳烃吸附组件2中输入置换剂;以及脱附剂进槽1043,布设于置换剂进槽1042一侧,且开口面积大于所述置换剂进槽1042,用于向芳烃吸附组件2中输入脱附剂。
32.本实施例在实际应用时,所述的置换剂进槽1042和脱附剂进槽1043分别与置换剂流通管道和脱附剂流通管道相连接,且置换剂进槽1042和脱附剂进槽1043的开口面积与筛分腔体202中一阶分子筛层17变化的横截面积相匹配,以使筛分腔体202中的一阶分子筛层17横截面积在转动过程中依次达到置换剂进槽1042和脱附剂进槽1043的开口面积,使得置换剂和脱附剂能够大量通入筛分腔体202中进行置换和脱附,由于置换剂和脱附剂在分离
釜组件6中可进行分离,因此通入量所受限制较小,可大量通入提高置换与脱附的效率,而原料进槽1041中的石脑油原料通入量与一阶分子筛层17的总质量分数呈线性相关,因此缩小原料进槽1041的开口面积,同时缩小了筛分腔体202中一阶分子筛层17的横截面积,能够提高一阶分子筛层17对石脑油原料的多重吸附效果,确保石脑油原料中的芳烃组分能够被充分吸收。
33.请参阅图2和图3,在本实施例中的一种优选实施例中,所述芳烃吸附组件2还包括:隔断壁203,布设于若干筛分腔体202之间,且其上开设有若干定位槽口204,所述定位槽口204靠近回转壳体201顶部一侧设置,用于配合弹性封堵片1044对若干筛分腔体202进行隔绝密封;定位槽口二205,布设于回转壳体201底部一侧,用于配合所述弹性封堵片二405对回转壳体201底部进行隔绝密封;压条206,固定布设于定位槽口204与定位槽口二205一侧,用于在所述回转壳体201转动时推动所述弹性封堵片1044与弹性封堵片二405的弹性滑动;导向件207,固定布设于筛分腔体202之间,用于限定回转板208的滑动方向,且所述回转板208与隔断壁203之间装配有弹性件209,用于驱动回转板208的弹性复位;以及孔板210,靠近回转壳体201底部一侧设置,用于对若干筛分腔体202中的一阶分子筛层17进行承托。
34.本实施例在实际应用时,当所述回转壳体201在驱动轴211的驱动下做定轴转动的过程中,位于回转壳体201两侧的压条206在旋转时压动一侧的弹性封堵片1044和另一侧的弹性封堵片二405弹性收缩,并且在弹性封堵片1044和弹性封堵片二405收缩过程中,使得回转壳体201贴合于进料构件104一侧转动,并且当弹性封堵片1044和弹性封堵片二405分别转动至定位槽口204和定位槽口二205一侧时,使其扣合于定位槽口204和定位槽口二205中,配合隔断壁203对回转壳体201的顶部和端部均进行隔绝密封,回转壳体201底部一侧布设有孔板210,且孔板210的孔隙小于分子筛的粒度大小。
35.在本实施例中的一种情况中,所述驱动轴211可优选连接减速机进行驱动,以使所述回转壳体201做定角度旋转,此处只要能够驱动回转壳体201匹配筛分腔体202的数量做定角度旋转即可,不做具体限定,所述正构烷烃提取组件3同理。
36.在本实施例中的一种情况中,所述驱动轴211一侧装配有振动齿盘212,以使回转壳体201在转动过程中能够产生振动,由于在本实施例中一阶分子筛层17优选采用层析硅胶吸附剂,所述的层析硅胶吸附剂为微小粉粒,在振动条件下能够更加快速的配合回转板208的转动而运动,并均匀填充在筛分腔体202中,使得置换剂和脱出剂在通入筛分腔体202的过程中能够和一阶分子筛层17均匀接触,提升了置换、脱附效率。
37.请参阅图2和图3,在发明的一种优选实施例中,所述芳烃吸附组件2还包括:磁极滑动部213,装配于回转板208末端,且布设于回转板208和筛分腔体202的内壁之间;以及固定电磁片214,固定装配于第一处理腔102的内壁上,用于通过脉冲电流对所述磁极滑动部213进行吸附,以使所述回转板208在回转壳体201转动的过程中,相对回转壳体201以设定角度旋转,从而调节筛分腔体202中一阶分子筛层17的横截面积。
38.本实施例在实际应用时,位于第一处理腔102壁面上的固定电磁片214在脉冲电流作用下产生一定频率的通断电,驱使固定电磁片214产生间歇式磁吸作用,当固定电磁片214处于磁吸状态下,能够穿过回转壳体201的壳体吸附磁极滑动部213,使得与磁极滑动部213装配连接的回转板208与筛分腔体202之间形成固定角度的腔体,此时腔体间的一阶分子筛层17在振动齿盘212的振动作用下均匀填满筛分腔体202与回转板208之间的腔体,形
成所需横截面积的一阶分子筛层17。
39.在本实施例中的一种情况中,所述回转壳体201采用非铁磁性材质构成,避免对磁极滑动部213和固定电磁片214的磁性效果产生干涉。
40.请参阅图1,在发明的一种优选实施例中,所述芳烃排料组件4还包括:基座401,固定装配于外壳体101中;置换剂排出槽402,朝向所述回转壳体201底部一侧设置,且与所述置换剂进槽1042匹配设置,用于排出置换剂排出液;脱附剂排出槽403,朝向所述回转壳体201底部一侧设置,且与所述脱附剂进槽1043匹配设置,用于排出脱附剂排出液;以及脱芳烃液排出槽404,朝向所述回转壳体201底部一侧设置,且与所述原料进槽1041匹配设置,用于排出石脑油脱芳烃排出液。
41.本实施例在实际应用时,所述脱芳烃液排出槽404、置换剂排出槽402和脱附剂排出槽403分别与原料进槽1041、置换剂进槽1042和脱附剂进槽1043相匹配设置,以使所述筛分腔体202中的排出液能够稳定排出。
42.本实施例在实际应用时,所述回转壳体201一侧通过脱芳烃液排出槽404将脱芳烃排出液送入至储液器406中,并通过出液管道407输入至正构烷烃提取组件3中,所述储液器406能够对脱芳烃排出液进行加热加压,以使输入至正构烷烃提取组件3中的脱芳烃排出液符合正构烷烃提取的温压标准。
43.请参阅图1,在发明的一种优选实施例中,所述裂解炉9中布设有加热壁16,所述加热壁16一侧与正构烷烃提取组件3装配相接,用于为正构烷烃提取组件3中的反应提供热能。
44.本实施例在实际应用时,当预处理后的正构烷烃经由正构烷烃管路7混合稀释蒸汽管19中的稀释蒸汽后进入裂解炉9中,在辐射管11中经由烧嘴组件10均匀加热,并通入急冷锅炉12中形成裂解气排出装置外,烧嘴组件10中燃烧形成的烟气进入排烟管13后,通过对流管组14将热量导入至对流腔体15中,穿过对流腔体15一侧的正构烷烃管路7中的烃和稀释蒸汽在对流腔体15中预热至横跨温度后进入辐射管11,能够提高裂解效果,而加热壁16侧吸收的热量能够提升正构烷烃提取组件3中正构烷烃的吸附效率。
45.在本实施例中的一种情况中,所述的裂解炉9的工作原理为本领域中的公知常识,此处不做具体赘述。
46.请参阅图1,在发明的一种实施例中,所述正构烷烃排料组件5包括底座501、正构烷烃置换剂排出管502、正构烷烃脱附剂排出管503和异构烷烃排出管504,所述底座501中装配有正构烷烃置换剂排出管502和正构烷烃脱附剂排出管503,分别用于正构烷烃提取组件3中置换剂和脱附剂的排出,所述异构烷烃排出管504用于排出正构烷烃提取组件3中的异构烷烃排出液。
47.请参阅图1,在发明的一种实施例中,所述分离釜组件6包括第一釜体601、第二釜体602、第三釜体603和第四釜体604,所述第一釜体601用于芳烃吸附组件2中排出置换剂的分离;所述第二釜体602用于芳烃吸附组件2中排出脱附剂的分离;所述第三釜体603用于正构烷烃提取组件3中排出置换剂的分离;所述第四釜体604用于正构烷烃提取组件3中排出脱附剂的分离。
48.请参阅图1,在发明的一种实施例中,所述输入管组8包括第一进液管801、第二进液管802、第三进液管803和第四进液管804,所述第一进液管801用于向芳烃吸附组件2中输
入置换剂;所述第二进液管802用于向芳烃吸附组件2中输入脱附剂;所述第三进液管803用于向正构烷烃提取组件3中输入置换剂;所述第四进液管804用于向正构烷烃提取组件3中输入脱附剂。
49.本发明上述实施例中提供了一种石脑油裂解装置,通过回转布设于第一处理腔102和第二处理腔103中的芳烃吸附组件2和正构烷烃提取组件3,能够循环对石脑油原料进行预处理,且预处理的多段流程互不干涉,能够降低石脑油原料中的芳烃组分,并提高预处理产物中正构烷烃的组分,有效降低裂解炉内的结焦情况,提升裂解产物中烯烃的收率,并且利用可改变分子筛横截面积的芳烃吸附组件2和正构烷烃提取组件3,有效提升分子筛的筛分速效,减少反应时间,达到提升产值的目的。
50.以上所述仅为本发明的较佳实施例而已,并不用以限制本发明,凡在本发明的精神和原则之内所作的任何修改、等同替换和改进等,均应包含在本发明的保护范围之内。