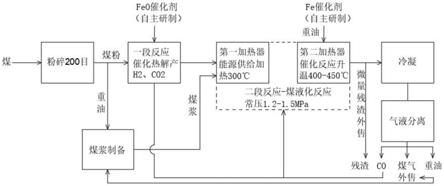
1.本实用新型属于能源制备领域,具体是一种低温常压煤催化产氢连续制油系统。
背景技术:
2.随着国内经济进入新常态,国际能源格局出现新变化,环保约束越来越强,煤制油产业面临的内外部环境较此前更加严峻复杂,有利条件和制约因素交织,增长潜力和发展压力并存。
3.现有煤液化油生产技术存在包含需持续供能维持高温反应致能耗与排放高、煤加压气化反应分解一氧化碳和氢致水耗高、制备工艺流程长致设备造价以及投资与运营成本高在内的突出问题。
技术实现要素:
4.本实用新型的目的在于克服现有技术的缺陷,提供一种低温常压煤催化产氢连续制油系统。
5.为实现上述目的,本实用新型采用了如下技术方案:
6.一种低温常压煤催化产氢连续制油系统,包含:
7.粉碎模块,其用于将煤粉碎成煤粉,得到的重油用于煤浆制备;
8.一段反应模块,将来自煤粉的co和h2o与外加的feo催化剂进行催化热解,得到c02和h2;以及
9.二段反应模块,其反应过程中用到包含煤液化反应器、气液分离器以及气罐,所述煤液化反应器用于将煤进行液化处理,并得到co气体,所述气液分离器将分离而出的co气体处理后送入到气罐中。
10.优选的,所述粉碎模块中包含粉碎机,经过粉碎后的煤粉为200目。
11.优选的,所述二段反应模块中,
12.来自一段反应中的c02和h2加入到第一加热器中,同时在煤浆内安装提升泵,并与第一加热器连通,所述第一加热器通过管道与煤液化反应器连通。
13.优选的,所述第一加热器的加热温度为0
‑
300℃,所述煤液化反应器中的反应压力为1.2
‑
1.5mpa,反应时间为4
‑
6min。
14.优选的,所述二段反应模块中,
15.所述煤液化反应器中添加有石油重油和fe催化剂,且煤液化反应器通过支管与自身侧壁连接,并在该支管上依次安装第一循环泵和第二加热器,所述煤液化反应器中的煤浆转变为不饱和液体,c02转变为co气体。
16.优选的,所述第二加热器的加热温度为400
‑
450℃。
17.优选的,所述气液分离器与煤液化反应器之间的连通管道上安装有冷凝器,且气液分离器与煤浆的连通管道上还安装有第二循环泵,并在气液分离器的出口端处安装压滤机,其过滤得到残渣和不饱和产品。
18.优选的,所述气罐的上下两端均安装有安全阀,所述气罐的一个出口端处安装有减压器,其用于对部分co气体降压后作为一段反应和二段反应的动力燃料,另一个出口端处安装有压缩机。
19.与现有技术相比,本实用新型提供了一种低温常压煤催化产氢连续制油系统,具有如下有益效果:
20.本实用新型实现两段反应催化产氢连续制油,其能源转化率≥99%。同时其整个系统具有包含设备少投资省、转化率高、能耗水耗低、环境友好的显著优势,以及无燃料煤消耗、无二氧化碳排放及超低水耗以及无高温高压反应。
附图说明
21.图1是本实用新型的工艺流程示意图;
22.图2是本实用新型的二段反应系统连接图。
23.附图标记:1、提升泵;2、第一加热器;3、煤液化反应器;4、第二加热器;5、第一循环泵;6、冷凝器;7、气液分离器;8、压滤机;9、第二循环泵;10、气罐;11、压缩机;12、减压器;13、安全阀。
具体实施方式
24.以下结合附图1,进一步说明本实用新型一种低温常压煤催化产氢连续制油系统的具体实施方式。本实用新型一种低温常压煤催化产氢连续制油系统不限于以下实施例的描述。
25.本实施例给出一种低温常压煤催化产氢连续制油系统的具体结构,如图1
‑
2所示,一种低温常压煤催化产氢连续制油系统,包含:
26.粉碎模块,其用于将煤粉碎成煤粉,得到的重油用于煤浆制备;
27.一段反应模块,将来自煤粉的co和h2o与外加的feo催化剂进行催化热解,得到c02和h2;以及
28.二段反应模块,其反应过程中用到包含煤液化反应器3、气液分离器7以及气罐10,煤液化反应器3用于将煤进行液化处理,并得到co气体,气液分离器7将分离而出的co气体处理后送入到气罐10中。
29.本实用新型中煤催化制氢连续转油关键技术及成套装备,采用自主研制的氧化铁和铁催化剂,配套设计开发出煤原料自催化热解制氢、低温节能连续催化转油及冷凝气固液分离两段一体化工艺流程及装备,实现了低温(350℃)常压(1.5mpa)高效制备煤化油:1吨褐煤可转化并实收约0.58吨煤化油(制1吨煤化油消耗原料煤约1.72吨)、剩余二氧化碳全部转化为一氧化碳(煤气)燃料返系统循环供能,能源转化率≥99%。同时,吨油水耗≤0.65m3/t(gb/t37759
‑
2019《节水型企业现代煤化工行业》要求煤炭直接液化取水量≤6.50m3/t)、能耗≤0.03吨标煤(仅设备启动升温至350℃耗能,达到温度值后系统自产能源循环供能)、反应速度40米/s、设备占地100
㎡
。具有设备少投资省、转化率高、能耗水耗低、环境友好的显著优势,以及无燃料煤消耗、无二氧化碳排放及超低水耗、无高温高压反应的突出特点。
30.其技术原理为:
31.煤炭直接液化的原理是煤通过溶剂抽提和在高温、高压、催化剂的作用下,煤浆加氢使煤中复杂的有机物分子结构发生变化,提高h/c比,直接转化为液体油品的过程。
32.如图1所示,粉碎模块中包含粉碎机,经过粉碎后的煤粉为200目。
33.如图2所示,二段反应模块中,
34.来自一段反应中的c02和h2加入到第一加热器2中,同时在煤浆内安装提升泵1,并与第一加热器2连通,第一加热器2通过管道与煤液化反应器3连通。
35.如图2所示,第一加热器2的加热温度为0
‑
300℃,煤液化反应器3中的反应压力为1.2
‑
1.5mpa,反应时间为4
‑
6min。
36.如图2所示,二段反应模块中,
37.煤液化反应器3中添加有石油重油和fe催化剂,且煤液化反应器3通过支管与自身侧壁连接,并在该支管上依次安装第一循环泵5和第二加热器4,煤液化反应器3中的煤浆转变为不饱和液体,c02转变为co气体。
38.如图2所示,第二加热器4的加热温度为400
‑
450℃。
39.如图2所示,气液分离器7与煤液化反应器3之间的连通管道上安装有冷凝器6,且气液分离器7与煤浆的连通管道上还安装有第二循环泵9,并在气液分离器7的出口端处安装压滤机8,其过滤得到残渣和不饱和产品。
40.如图2所示,气罐10的上下两端均安装有安全阀13,气罐10的一个出口端处安装有减压器12,其用于对部分co气体降压后作为一段反应和二段反应的动力燃料,另一个出口端处安装有压缩机11。
41.其具体的工艺流程为:
42.一段反应:一氧化碳变换反应。co和h2o在feo催化剂环境下,加热至不高于450℃,得到co2和h2;
43.二段反应:煤液化反应。
44.包括以下子步骤:1、将来自一段反应的co2和h2加入至第一加热器2,同时向第一加热器2内加入煤浆,加热至300℃,送入煤液化反应器3;
45.2、在煤液化反应器3内装有石油重油和fe催化剂,石油重油、fe催化剂和煤浆通过第二加热器4和第一循环泵5循环加热,使得反应温度达到400~450℃时,煤浆转变为不饱和液体,co2转变为co气体;
46.3、经冷凝器6和气液分离器7后,完全反应的液体物料经压滤机8过滤出来,其中反应物煤灰和固体杂质为残渣,过滤液为不饱和产品;
47.4、从气液分离器7分离出来的co储存入气罐10中,一部分co经压缩机11输送至一段反应,作为原料,另一部分co经过减压器12降压后作为一段反应和二段反应的动力燃料;
48.5、气液分离器7分离出的物料还包括未完全反应的物料,其经第二循环泵9输入第一加热器2,重新反应。
49.以上内容是结合具体的优选实施方式对本实用新型所作的进一步详细说明,不能认定本实用新型的具体实施只局限于这些说明。对于本实用新型所属技术领域的普通技术人员来说,在不脱离本实用新型构思的前提下,还可以做出若干简单推演或替换,都应当视为属于本实用新型的保护范围。