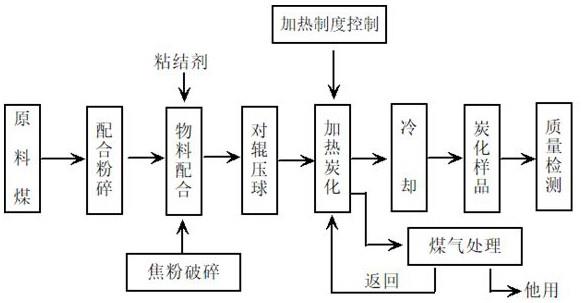
1.本发明涉及一种废弃焦粉的利用方法,尤其涉及一种废弃焦粉的高价值型焦生产方法。
背景技术:
2.炼铁的过程主要是利用焦炭和烧结矿进行还原反应而获得铁水,随着炼铁产能的扩大,相应的对于提供炼铁原料的焦炭产能也在快速扩张,很多钢铁企业为了多生产焦炭,焦炉会满负荷甚至超负荷生产。但随着各地政府对钢铁企业环保生产要求的提高,各项限煤措施出台导致钢铁企业只能通过购买焦炭来平衡限煤造成的焦炭缺口。
3.以某大型钢铁企业为例,该钢铁企业每年需要购入100多万吨焦炭,而焦炭在装卸、运输、生产等过程中会产生大量的焦粉,约占焦炭的10%,即每年产生10多万吨废弃焦粉,对废弃焦粉的利用大多是回配炼焦,用于烧结厂作为原燃料使用,造成了原材料极大的浪费,进而提高了生产成本。废弃焦粉的另一应用为型焦生产,但生产的产品大多为铸造焦,只能用于冲天炉的生产,利用价值低。
4.中国发明专利申请cn200510107212.0公开了一种合成焦碳及其制作方法,该合成焦碳包括焦粉150-300份、煤150-300份、氢氧化铝2-3份、高岭土2-30份、铝矾土2-30份和沥青50-100份,该制作方法是通过液体沥青混合所有物料并压制成型。该合成焦碳中加入了氢氧化铝、高岭土和铝矾土等成分,且沥青的含量较高,不利于后续的焦碳炭化,降低了型焦产品的质量,导致在替代高炉焦炭炼焦时焦粉的利用率较低。
5.中国发明专利申请cn201910942493.3公开了一种利用化工废弃物制备高强度炼铁用焦炭的方法,该方法将焦粉、煤粉、粘结剂粉碎研磨后加压造粒,再在表面喷上焦油使焦粉能粘在物料表面。该方法存在以下缺陷:1、实际生产过程中焦粉硫份约为8%,该方法对焦粉的硫份限制较大,导致能应用于该方法的焦粉局限性较大,也不利于高炉造渣生产。2、该方法中使用的肥煤和1/3焦煤的比重较低,加之气煤、瘦煤等煤种的挥发分非常高,导致成品的裂纹较多,影响成品质量和成品率。3、该方法需要加压造粒、喷焦油、粘焦粉、高温干馏并配合石墨坩埚或氮气保护,最终生产出一级标准的高炉焦炭用于高炉充当骨架和还原剂作用,流程复杂且不利于大规模生产,物料表面的焦油、焦粉的均匀性难以保证,导致成品率存在较大的不确定性。
技术实现要素:
6.本发明的目的在于提供一种废弃焦粉的高价值型焦生产方法,通过废弃焦粉与配合煤混合成型并炭化后制成型焦产品,使该型焦产品能替代部分高炉用焦炭,从而达到废弃焦粉的高价值利用的目的,同时节约物料和能耗。
7.本发明是这样实现的:一种废弃焦粉的高价值型焦生产方法,包括以下步骤:步骤1:将废弃焦粉破碎,在所述的焦粉中,灰分为12-13%、挥发分为1-1.5%、固定碳为
86-87%,且焦粉重量占焦粉和配合煤总重量的45-60%;步骤2:将单种煤按比例搅拌混合破碎,制成配合煤;所述的单种煤包括肥煤和1/3焦煤,其中,肥煤重量占焦粉和配合煤总重量的15-25%,1/3焦煤占焦粉和配合煤总重量的25-30%;步骤3:将步骤1中破碎的焦粉加入步骤2中混合破碎的配合煤中,构成配合物料,再向配合物料中加入粘结剂,且粘结剂的重量为配合物料重量的5-7%,配合物料通过粘结剂搅拌混合;步骤4:将步骤3中搅拌混合的物料进行对辊压球,物料球的尺寸为15*20mm;步骤5:将步骤4中制得的物料球加入炭化炉中进行炭化;炭化的加热方法为:以6-8℃/min的加热速度从常温升温至1000℃,并以1000℃的温度恒温30min;步骤6:将步骤5中炭化后的物料出炉并通过气体进行换热冷却,得到型焦产品,换热后的气体进行处理后回收至炭化炉用于加热。
8.在所述的步骤1中,焦粉的破碎粒度小于1mm。
9.在所述的步骤2中,肥煤的灰分a
d
为8-10%,挥发分vm
d
为15-25%;所述的1/3焦煤的灰分a
d
为6.5-7.5%,挥发分vm
d
为33-35%。
10.在所述的步骤2中,单种煤的粒度小于6mm,混合破碎后的配合煤中粒度小于1mm的煤的比例为90-95%。
11.在所述的步骤3中,粘结剂为固态的中温沥青或固态的高温沥青,其中,高温沥青的软化点为125-135℃,中温沥青的软化点为80-90℃。
12.在所述的步骤3中,焦粉、配合煤和粘结剂的混合方法为固体混合。
13.在所述的步骤6中,型焦产品的焦炭反应性cri为37-39%,焦炭反应后强度csr为44-46%。
14.本发明与现有技术相比,具有如下有益效果:1、本发明通过废弃焦粉与配合煤混合成型并炭化后制成型焦产品,该型焦产品的焦炭反应性cri能达到37-39%,焦炭反应后强度csr能达到44-46%,使其能替代部分高炉用焦炭,有效减少了高炉使用焦炭量,实现了废弃焦粉与焦炭等价值利用,解决了现有技术中焦粉只能应用于烧结燃料或高炉喷吹的低价值利用问题。
15.2、本发明通过气体冷却型焦产品,并将换热后的余热回收用于炭化炉加热,实现了气体的内部循环,降低了生产能耗和成本。
16.3、本发明降低了炼铁过程中燃料和能源的消耗,弥补了限煤要求导致的焦炭短缺的问题,也满足了绿色环保生产的要求。
17.综上所述,本发明通过废弃焦粉与配合煤混合成型并炭化后制成型焦产品,型焦产品的焦炭反应性cri能达到37-39%,焦炭反应后强度csr能达到44-46%,使该型焦产品能替代部分高炉用焦炭,实现废弃焦粉与焦炭的等价值利用,节约高炉使用焦炭数量以及能生产过程中的能耗,降低高炉炼铁的生产成本,并弥补了限煤问题造成的焦炭部分缺口问题。
附图说明
18.图1是本发明废弃焦粉的高价值型焦生产方法的流程图。
具体实施方式
19.下面结合附图和具体实施例对本发明作进一步说明。
20.请参见附图1,一种废弃焦粉的高价值型焦生产方法,包括以下步骤:步骤1:将购自生产厂商的焦炭装卸、运输、生产等过程中产生的废弃焦粉通过破碎机破碎,在所述的焦粉中,灰分为12-13%、挥发分为1-1.5%、固定碳为86-87%,不限制焦粉的硫份,不仅使本发明的生产方法具有良好的适应性、通用性和实用性,也有利于焦粉与煤粉的配合,有利于在生产过程中的高炉造渣生产,且焦粉重量占焦粉和配合煤总重量的45-60%。
21.固定碳含量是制备焦炭的重要影响因素,直接影响到压制成产品的成品率,同时由于制备的型焦产品直接应用于高炉炼铁,固定碳的含量越高越好,若固定碳的含量低,会影响型焦产品在高炉内对矿石的还原效率,也会影响型焦产品在高炉内的发热量,导致高炉焦比和生产成本的提高。因此,本发明将固定碳的含量控制在86-87%,确保了压制成型的成品率,也使生产的型焦产品能在高炉内具有良好的发热量并对矿石进行有效的还原,从而使废弃的焦粉也能达到焦炭的等价值利用。
22.所述的焦粉的破碎粒度小于1mm,有利于焦粉与煤粉和沥青的混合,提高混合的均匀性,避免产生局部聚集现象。
23.步骤2:将购自生产厂商的单种煤按照一定的比例加入破碎机中进行搅拌混合破碎,制成配合煤;所述的单种煤包括肥煤和1/3焦煤,其中,肥煤重量占焦粉和配合煤总重量的15-25%,1/3焦煤占焦粉和配合煤总重量的25-30%。
24.所述的肥煤的灰分a
d
为8-10%,挥发分vm
d
为15-25%;所述的1/3焦煤的灰分a
d
为6.5-7.5%,挥发分vm
d
为33-35%,有利于制备原料产品在加热过程中的融并和炭化反应,并保证产品达到一定的强度,同时能在高炉内快速气化。
25.本发明考虑了肥煤和1/3焦煤的最佳配比,确保在一定温度条件下肥煤和1/3焦煤形成胶质体后与焦粉以及粘结剂的相互反应和融并成焦,且本发明仅使用肥煤和1/3焦煤,肥煤作为生产的基础煤在受热情况下会产生大量的胶质体,而胶质体有利于对焦粉的融并作用,同时,1/3焦煤也可以产生一定数量的胶质体,且可以使生产产品的强度得以提高,避免了添加挥发分高的气煤和瘦煤等煤种,从而防止产品产生裂纹,有利于提高成品率和成品质量。
26.所述的单种煤的粒度小于6mm,混合破碎后的配合煤中粒度小于1mm的煤的比例为90-95%,可以使配合煤与焦粉和粘结剂能够充分均匀配合,防止物料发生局部聚集现象。
27.步骤3:将步骤1中破碎的焦粉加入步骤2中混合破碎的配合煤中,构成配合物料,再向配合物料中加入粘结剂,且粘结剂的重量为配合物料重量的5-7%,配合物料通过粘结剂经配合机搅拌混合。
28.所述的粘结剂为固态的中温沥青或固态的高温沥青,其中,高温沥青的软化点为125-135℃,中温沥青的软化点为80-90℃。
29.在所述的步骤3中,焦粉、配合煤和粘结剂的混合方法为固体混合,可以使粘结剂能够均匀分散至焦粉和配合煤中,避免了将粘结剂加热变成液体由于粘结剂量少而导致局部聚集的问题,同时还可以降低加热能耗。
30.步骤4:将步骤3中搅拌混合的物料加入辊压球机中进行对辊压球,物料球的尺寸为15*20mm。若物料球的尺寸过大,则在后续炭化炉内进行炭化时会加大炭化的难度,同时
也会导致型焦产品产生过多的破裂,从而大大降低成品率;另外,物料球尺寸过大会在炭化过程中消耗更多的能耗,提高生产成本。物料球的尺寸越小,制备难度和成本越高,同时物料球的尺寸过小也不利于在高炉中的气化反应步骤5:将步骤4中制得的物料球加入炭化炉中进行炭化;炭化的加热方法为:以6-8℃/min的加热速度从常温升温至1000℃,并以1000℃的温度恒温30min,无需板结、硬化、喷焦油、粘焦粉的复杂工序,有利于快速制备质量合格的产品,且恒温时间短,在确保产品质量提高的基础上可以节约能耗和生产成本。
31.步骤6:将步骤5中炭化后的物料出炉并通过氮气气体进行换热冷却,得到型焦产品;物料球炭化热解产生的气体进行脱硫和脱焦油处理后回收至炭化炉用于炭化炉的加热,还有部分气体可收集做他用,实现了加热过程中气体的内部循环,节约能源,流程经济。
32.本发明重新加工再利用废弃焦粉,使生产的型焦产品的焦炭反应性cri能达到37-39%,焦炭反应后强度csr能达到44-46%,可部分替代高炉用焦炭,加入高炉后发生气化反应,产生的大量co还原气体用于还原高炉中的铁矿石,降低高炉生产过程燃料消耗,降低炼铁过程的生产成本,也解决了限煤要求导致的焦炭短缺问题。
33.实施例1:步骤1:将购自生产厂商的焦炭装卸、运输、生产等过程中产生的废弃焦粉通过破碎机破碎,在该焦粉中,灰分为12%、挥发分为1%、固定碳为87%,且焦粉重量占焦粉和配合煤总重量的55%。焦粉的破碎粒度小于1mm。
34.步骤2:将购自生产厂商的粒度小于6mm的肥煤和1/3焦煤加入破碎机中进行搅拌混合破碎,制成配合煤,混合破碎后的配合煤中粒度小于1mm的煤的比例为90%;该肥煤重量占焦粉和配合煤总重量的15%,且肥煤的灰分a
d
为8%,挥发分vm
d
为15%;该1/3焦煤占焦粉和配合煤总重量的30%,且1/3焦煤的灰分a
d
为7.5%,挥发分vm
d
为33%。
35.步骤3:将步骤1中破碎的焦粉加入步骤2中混合破碎的配合煤中,构成配合物料,再向配合物料中加入中温沥青作为粘结剂,且中温沥青的重量为配合物料重量的7%,配合物料通过粘结剂经配合机进行固体搅拌混合。
36.步骤4:将步骤3中搅拌混合的物料加入辊压球机中进行对辊压球,物料球的尺寸为15*20mm。
37.步骤5:将步骤4中制得的物料球加入炭化炉中进行炭化;炭化的加热方法为:以6℃/min的加热速度从常温升温至1000℃,并以1000℃的温度恒温30min。
38.步骤6:将步骤5中炭化后的物料出炉并通过气体进行换热冷却,得到型焦产品,换热后的气体进行处理后回收至炭化炉用于加热。
39.在本实施例中,生产得到的型焦产品的焦炭反应性cri为37.2%,焦炭反应后强度csr为46%。
40.实施例2:步骤1:将购自生产厂商的焦炭装卸、运输、生产等过程中产生的废弃焦粉通过破碎机破碎,在该焦粉中,灰分为13%、挥发分为1%、固定碳为86%,且焦粉重量占焦粉和配合煤总重量的60%。焦粉的破碎粒度小于1mm。
41.步骤2:将购自生产厂商的粒度小于6mm的肥煤和1/3焦煤加入破碎机中进行搅拌混合破碎,制成配合煤,混合破碎后的配合煤中粒度小于1mm的煤的比例为93%;该肥煤重量
占焦粉和配合煤总重量的15%,且肥煤的灰分a
d
为10%,挥发分vm
d
为20%;该1/3焦煤占焦粉和配合煤总重量的25%,且1/3焦煤的灰分a
d
为6.5%,挥发分vm
d
为35%。
42.步骤3:将步骤1中破碎的焦粉加入步骤2中混合破碎的配合煤中,构成配合物料,再向配合物料中加入高温沥青作为粘结剂,且高温沥青的重量为配合物料重量的5%,配合物料通过粘结剂经配合机进行固体搅拌混合。
43.步骤4:将步骤3中搅拌混合的物料加入辊压球机中进行对辊压球,物料球的尺寸为15*20mm。
44.步骤5:将步骤4中制得的物料球加入炭化炉中进行炭化;炭化的加热方法为:以8℃/min的加热速度从常温升温至1000℃,并以1000℃的温度恒温30min。
45.步骤6:将步骤5中炭化后的物料出炉并通过气体进行换热冷却,得到型焦产品,换热后的气体进行处理后回收至炭化炉用于加热。
46.在本实施例中,生产得到的型焦产品的焦炭反应性cri为37.8%,焦炭反应后强度csr为45.4%。
47.实施例3:步骤1:将购自生产厂商的焦炭装卸、运输、生产等过程中产生的废弃焦粉通过破碎机破碎,在该焦粉中,灰分为12.5%、挥发分为1.5%、固定碳为86%,且焦粉重量占焦粉和配合煤总重量的60%。焦粉的破碎粒度小于1mm。
48.步骤2:将购自生产厂商的粒度小于6mm的肥煤和1/3焦煤加入破碎机中进行搅拌混合破碎,制成配合煤,混合破碎后的配合煤中粒度小于1mm的煤的比例为95%;该肥煤重量占焦粉和配合煤总重量的15%,且肥煤的灰分a
d
为8%,挥发分vm
d
为25%;该1/3焦煤占焦粉和配合煤总重量的25%,且1/3焦煤的灰分a
d
为7.5%,挥发分vm
d
为34%。
49.步骤3:将步骤1中破碎的焦粉加入步骤2中混合破碎的配合煤中,构成配合物料,再向配合物料中加入中温沥青作为粘结剂,且中温沥青的重量为配合物料重量的5%,配合物料通过粘结剂经配合机进行固体搅拌混合。
50.步骤4:将步骤3中搅拌混合的物料加入辊压球机中进行对辊压球,物料球的尺寸为15*20mm。
51.步骤5:将步骤4中制得的物料球加入炭化炉中进行炭化;炭化的加热方法为:以8℃/min的加热速度从常温升温至1000℃,并以1000℃的温度恒温30min。
52.步骤6:将步骤5中炭化后的物料出炉并通过气体进行换热冷却,得到型焦产品,换热后的气体进行处理后回收至炭化炉用于加热。
53.在本实施例中,生产得到的型焦产品的焦炭反应性cri为38.2%,焦炭反应后强度csr为45.1%。
54.实施例4:步骤1:将购自生产厂商的焦炭装卸、运输、生产等过程中产生的废弃焦粉通过破碎机破碎,在该焦粉中,灰分为13%、挥发分为1%、固定碳为86%,且焦粉重量占焦粉和配合煤总重量的51%。焦粉的破碎粒度小于1mm。
55.步骤2:将购自生产厂商的粒度小于6mm的肥煤和1/3焦煤加入破碎机中进行搅拌混合破碎,制成配合煤,混合破碎后的配合煤中粒度小于1mm的煤的比例为90%;该肥煤重量占焦粉和配合煤总重量的24%,且肥煤的灰分a
d
为9%,挥发分vm
d
为23%;该1/3焦煤占焦粉和
配合煤总重量的25%,且1/3焦煤的灰分a
d
为7.5%,挥发分vm
d
为35%。
56.步骤3:将步骤1中破碎的焦粉加入步骤2中混合破碎的配合煤中,构成配合物料,再向配合物料中加入高温沥青作为粘结剂,且高温沥青的重量为配合物料重量的5%,配合物料通过粘结剂经配合机进行固体搅拌混合。
57.步骤4:将步骤3中搅拌混合的物料加入辊压球机中进行对辊压球,物料球的尺寸为15*20mm。
58.步骤5:将步骤4中制得的物料球加入炭化炉中进行炭化;炭化的加热方法为:以6℃/min的加热速度从常温升温至1000℃,并以1000℃的温度恒温30min。
59.步骤6:将步骤5中炭化后的物料出炉并通过气体进行换热冷却,得到型焦产品,换热后的气体进行处理后回收至炭化炉用于加热。
60.在本实施例中,生产得到的型焦产品的焦炭反应性cri为38.8%,焦炭反应后强度csr为44.7%。
61.以上仅为本发明的较佳实施例而已,并非用于限定本发明的保护范围,因此,凡在本发明的精神和原则之内所作的任何修改、等同替换、改进等,均应包含在本发明的保护范围之内。