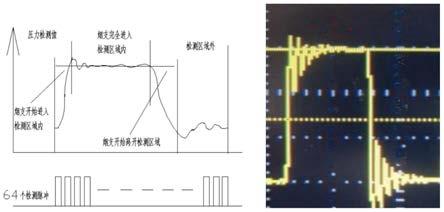
一种提高在线烟支通风度检测精度的方法和装置
1.技术领域:本发明属于烟支生产技术领域,特别涉及一种提高在线烟支通风度检测精度的装置,及其检测方法。
2.
背景技术:
中国专利zl201410015291.1一种烟支在鼓轮上输送时一种检测漏气的方法,描述了利用相邻两个槽位烟支分别进行两路气流设计,第一路进、出气端各设立气压传感器检测气压p1p2;第二路在出气端设置气压传感器检测气压p3; 其利用轴编码器的64个增强脉冲进行64次压力信号检测,并进行数据处理的一种技术方案。显然,由于检测装置通常为一与检测鼓相匹配的弧形的区域,位于检测鼓轮的顶部区域,每支烟间隔且轮流进入检测区域再离开该区域,然后下一支烟支再进入检测区域,因此,对于每支烟支的进出检测区域,必然存在气路的充气和放气的过程,显然该技术方案没有考虑烟支入和离开检测区域时气流、气压的充气和放气的过程造成检测气压的波动对检测数据的影响,实践证明,该压力的变化及波动可占整个检测区域长度的50%,因此必然会造成大量无效的数据,肯定会影响其运算的准确性。另外,对于一些卷接机组并没有采用轴编码器协助产生机器脉冲,所以,额外安装一个轴编码器也不方便,甚至会影响其他器件的运行。
3.图1为采用轴编码器产生的64个检测脉冲的示意图;图中为烟支进出检测区域的一个周期内的几个阶段:烟支进入检测区域时的第一阶段,烟支的端部截面部分进入检测区,气流开始进入烟支,压力逐步上升,并震荡。
4.烟完全进入检测区域的第二阶段,压力已经上升并稳定。
5.烟支离开检测区域时的第三阶段,烟支的端部截面部分离开检测区,进入烟支的开始气流减少,压力逐步下降,并震荡。
6.烟完全离开检测区域的第四阶段,压力已经下降并稳定。
7.检测区域等待下一支烟的进入。
8.可见,利用轴编码器产生64个检测脉冲,对上述四个阶段构成的一个周期进行采样,没有起到提高检测精度的作用。
9.公开于该背景技术部分的信息仅仅旨在增加对本发明的总体背景的理解,而不应当被视为承认或以任何形式暗示该信息构成已为本领域一般技术人员所公知的现有技术。
10.
技术实现要素:
本发明的目的在于提供一种提高在线烟支通风度检测精度的装置,从而克服上述现有技术中的缺陷。
11.为实现上述目的,本发明提供了一种提高在线烟支通风度检测精度的装置,包括:进气管、检测鼓、设置于检测鼓两侧的石墨弧板、石墨弧板与烟支对应的一侧设置有气槽、烟支同步信号、数据采集运算单元组成,气槽的气路与进气管和烟支进气端石墨弧板处和出气端石墨弧板处的压力传感器连通,石墨弧板气槽的圆弧长度即为烟支的检测区域长度;
数据采集运算单元在获取烟支同步信号后,对其信号的脉冲周期进行运算,在避开烟支进出检测区域时的气压气流不稳定的时间段后,再进行n次分频,形成n个检测触发脉冲;气压气流不稳定的时间段通过有效检测时间长度:t1获得。
12.压力传感器对应每个检测触发脉冲产生一个检测数据,对n个检测数值进行平均运算,获得准确的烟支进气端、出气端的压力值,进而获取更准确的烟支通风度值。气压气流不稳定的时间段通过有效检测时间长度:t1获得,t1=(β
‑
α)*t,系数α为自烟支同步脉冲的起始上升沿至发出首个允许检测脉冲上升沿的延时,α取值范围为30
‑‑
65%;系数β为自烟支同步脉冲的起始上升沿至最后一个检测脉冲周期的结束的延时,β取值范围40
‑‑
98%,t为相邻两个烟支同步信号之间的时长周期。
13.背负骂名的思路为:不使用常规喷嘴,利用运算单元形成检测允许脉冲,使得检测数据能够避开烟支进出检测区域时所造成的波动。代替了常规喷嘴的抑制波动的作用。
14.优选地,上述技术方案中,烟支同步信号,包括烟支到位传感器的脉冲信号以及机器时钟的脉冲信号,所述烟支同步信号与每一烟支的速度和位置相对应。
15.优选地,上述技术方案中,一支烟支只对应有一个烟支同步信号的脉冲。
16.优选地,上述技术方案中,设置在烟支进气端石墨弧板处和出气端石墨弧板处的压力传感器对应压力值为:pin为烟支进气端压力传感器值,pout为烟支出气端压力传感器值;烟支进入或者离开石墨弧板圆弧气槽检测区域造成pin 和pout
‑
变化率9%
‑
4.8%范围内。
17.优选地,上述技术方案中,数据采集运算单元根据烟支同步信号,当卷烟机速度大于x支/分的情况下进行以下运算,x为大于100的正整数:s1,获取相邻两个烟支同步信号之间的时长周期t;s2,设定自烟支同步脉冲的起始上升沿至发出首个允许检测脉冲上升沿的延时,系数为α 30
‑‑
65%;s3,设定自烟支同步脉冲的起始上升沿至最后一个检测脉冲周期的结束的延时,系数为β 40
‑‑
98%;s4,获得有效检测时间长度:t1=(β
‑
α)*t;s5,设定t1时间内需要的压力传感器数据采集的次数n和脉冲占空比n1%,获得周期为t2=t1/n和占空比n1%检测触发脉冲;s6,自烟支同步脉冲的起始上升沿开始α延时后,运算控制单元发出发出允许检测脉冲,即n个周期为t1/n、占空比为n1%的多个允许检测脉冲序列;s7,所述数据采集单元根据运算控制单元发出的检测触发脉冲,对所述两对进气槽的进气端和出气槽的出气端的压力传感器的数据进行采集,获得每支烟支对应n个压力传感器的数据,分别为p1进、p1出,和p2进、p2出各n个数据;s8,对每个压力传感器的上述n个有效数据进行平均值计算:p=(p1+
……
+pn)/n,即p1进平均、p1出平均,和p2进平均、p2出平均;s9,若所述两组进气槽的进气端均对应烟支的点燃端,两组出气槽的出气端均对应烟支的过滤嘴端,即两组检测均采用正向检测气流,气流从烟支的点燃端流向烟支的过滤嘴端;
进而获得:p进平均=(p1进平均+p2进平均)/2,p出平均=(p1出平均+p2出平均)/2,所述烟支的通风度f=(p进平均
ꢀ‑ꢀ
p出平均),或者:烟支的通风度f=(p进平均
ꢀ‑ꢀ
p出平均)/p进平均;s10,若所述一组进气槽的进气端对应烟支的点燃端以及出气槽的出气端对应烟支的过滤嘴端(正向检测气流,即检测气流从烟支的点燃端流向烟支的过滤嘴端)、另一组进气槽的进气端对应烟支的过滤嘴端以及出气槽的出气端对应烟支的点燃端(反向检测气流,即气流从烟支的过滤嘴端流向烟支的点燃端);进而获得:烟支的正向通风度f正=(p1进平均 *c1
ꢀ‑ꢀ
p1出平均*c2),或者f正=(p1进平均 *c1
ꢀ‑ꢀ
p1出平均*c2)/p1进平均,烟支的反向通风度f反=(p2进平均*c3
‑ꢀ
p2出平均*c4),或者f反=(p2进平均*c3
‑ꢀ
p2出平均*c4)/p2进平均,c1c2c3c4为调整系数,为监测参数校准所需的调节常数;s11,烟支正向过滤嘴通风度:fv1=β1*f正,β1为设定的调节系数,烟支反向过滤嘴通风度:fv2=β2*f反,β2为设定的调节系数,烟支过滤嘴通风度:pv=fv1*c1+fv2*c2。
18.上述的运算和方法的应用,可以实现代替轴编码器的功能,且安装简单快捷,且,无需利用软硬件进行无效数据的判断,简化了系统的设计,也降低了成本,平均值计算法,减小了因气压波动、机器运行波动、烟支抖动等因素造成的测量计算误差。
19.优选地,上述技术方案中,s2中系数α为40%
‑
55%。
20.优选地,上述技术方案中,s3中系数β为45%
‑
85%。
21.在线烟支通风度检测精度的装置,包括:进气管、节流进气喷嘴、 检测鼓、设置于检测鼓两侧的石墨弧板、设置在烟支进气端石墨弧板处和出气端石墨弧板处的压力传感器、烟支同步信号、数据采集运算单元组成,石墨弧板气槽的圆弧长度即为烟支的检测区域长度;节流进气喷嘴为一等径空心管,所述空心管内设置有小孔段,小孔段为上设通孔的隔板,隔板厚度l1,隔板中心附近区域内设定至少一个直径d:0.1
‑
0.7mm的微孔,l1/d满足:0.5<l1/d≤6构成短孔时,以形成一具有气流节流效果的元件。
22.在线烟支通风度检测精度的装置,包括:进气管、节流进气喷嘴、检测鼓、设置于检测鼓两侧的石墨弧板、石墨弧板与烟支对应的一侧设置有气槽、烟支同步信号、数据采集运算单元组成,所述气槽的气路与进气管和烟支进气端石墨弧板处和出气端石墨弧板处的压力传感器连通,其特征在于:所述石墨弧板气槽的圆弧长度即为烟支的检测区域长度;节流进气喷嘴为内设置有缩径段、小孔段和扩径段的空心管,所述缩径段为进气段,所述扩径段为出气段,所述小孔段的长度l2,孔径d,为一细长型孔,当小孔段长3
‑
15mm,孔径范围0.2mm
‑‑
2.5mm,形成一文丘理管,在其扩径段获得较低压力,而具有稳定气流压力的功能。
23.数据采集运算单元在获取烟支同步信号后,对其信号的脉冲周期进行运算,在避
开烟支进出气槽检测区域时的气压气流不稳定的时间段后,再进行n次分频,形成n个检测触发脉冲,形成有效的电气检测区;压力传感器对应每个检测触发脉冲产生一个检测数据,对n个检测数值进行平均运算,获得准确的烟支进气端、出气端的压力值,进而获取更准确的烟支通风度值。
24.稳定气流、气压的节流进气喷嘴与有效的电气检测区结合,实现α为5%
‑
45%,从而扩大了有效检测区域的长度在线烟支通风度检测精度的装置,包括节流进气喷嘴,节流喷气嘴内顺序设置有缩径段、小孔段和扩径段的空心管,所述缩径段为进气段,扩径段为出气段,小孔段为等径段,小孔段内设具微孔隔板,具有恒流与恒压气流喷嘴的组合:小孔段的长度l2,孔径d,为一细长型孔,小孔段长3
‑
15mm,孔径范围0.2mm
‑‑
2.5mm,微孔隔板设置在小孔段气流出口端与扩径段交接之处,隔板位于小孔段孔径、或者扩径段范围内,有至少一个小孔,孔径0.15
‑
0.8mm,进气气流压力被缩径段收缩,速度上升压力降低,从而在隔板微孔出口处附近产生一个较为恒定低压区,再利用具有节流功能的微孔隔板,从而实现恒压恒流的效果。
25.与现有技术相比,本发明具有如下有益效果:减少了对轴编码器的安装及其配套专业的信号采集运算模块的使用降低了设备成本;简化了运算检测触发脉冲的步骤,简化了运算软件的流程,提高了运算速度;将烟支进出检测区域时产生气压波动的检测参数不进行检测,形成有效的电气检测区,减少数据处理量,提升了采集效率;只对烟支进入检测区域后气压已经稳定的检测参数进行检测,提高了检测效率,提高了检测数据的有效性,提高了检测参数的精度。
26.采用人机界面输入数据采集的定位延时参数,装置使用更灵活,人机沟通更高效。
27.将电气检测区与节流嘴结合,增加了有效检测区域长度,借以获得更可靠的检测数据。
28.附图说明:图1为现有技术示意图;图2和图3为本发明的结构示意图;图4和图5为检测方法示意图;图6和图7为小进气喷嘴的结构示意图;图8为烟支进出检测区域的气压波动数据曲线示意图;具体实施方式:下面对本发明的具体实施方式进行详细描述,但应当理解本发明的保护 范围并不受具体实施方式的限制。
29.除非另有其它明确表示,否则在整个说明书和权利要求书中,术语“包 括”或其变换如“包含”或“包括有”等等将被理解为包括所陈述的元件或 组成部分,而并未排除其它元件或其它组成部分。
30.本方案为克服了上述技术方案存在缺点的新方法和装置1、一种在线烟支通风度检测装置或者由:进气管、检测鼓、位于检测鼓两外侧的石墨弧板、以及设置在石墨弧板进气端和出气端的压力传感器、烟支同步信号、数据采集运算
单元组成,或者由:进气管、进气喷嘴、检测鼓、位于检测鼓两外侧的石墨弧板、以及设置在石墨弧板进气端和出气端的压力传感器、烟支同步信号、数据采集运算单元组成,特征是:设置在检测鼓两外侧石墨弧板的进气端和出气端的压力传感器,在检测触发脉冲的协调下,检测烟支点燃端、过滤嘴端的压力值;数据采集运算单元在获取烟支同步信号后,对其信号的脉冲周期进行运算,在去除烟支进出检测区域时的波动数据后,再进行n次分频,形成n个检测触发脉冲;压力传感器对应每个检测触发脉冲产生一个检测数据,对n个检测数值进行平均运算,获得准确的烟支进气端、出气端的压力值,进气获取准确的烟支通风度值。
31.2、所述烟支同步信号,包括烟支到位传感器的脉冲信号以及机器时钟的脉冲信号,所述烟支同步信号与每一烟支的速度和位置相对应,优选,一支烟支只产生一个同步脉冲。
32.3、所述数据采集运算单元根据烟支同步信号,当卷烟机速度大于1000支/分的情况下进行以下运算:
①
获取相邻两个烟支同步信号之间的时长周期t;
②
设定自烟支同步脉冲的起始上升沿至发出首个允许检测脉冲上升沿的延时,系数为α(0
‑‑
50%),优选5%
‑
10%;
③
设定自烟支同步脉冲的起始上升沿至最后一个检测脉冲周期的结束的延时,系数为β(10
‑‑
70%),优选10%
‑
65%;
④
获得有效检测时间长度:t1=(β
‑
α)*t;
⑤
设定t1时间内需要的压力传感器数据采集的次数n、和脉冲占空比n1%,获得周期为t2=t1/n和占空比n1%检测触发脉冲;
⑥
自烟支同步脉冲的起始上升沿开始α延时后,运算控制单元发出发出允许检测脉冲,即n个周期为t1/n、占空比为n1%的多个允许检测脉冲序列。
33.⑦
所述数据采集单元根据运算控制单元发出的检测触发脉冲,对所述两对进气槽的进气端和出气槽的出气端的压力传感器的数据进行采集,获得每支烟支对应n个压力传感器的数据,分别为p1进、p1出,和p2进、p2出各n个数据。
34.⑧
对每个压力传感器的上述n个有效数据进行平均值计算:p=(p1+
‑‑‑
+pn)/n,即p1进平均、p1出平均,和p2进平均、p2出平均
⑧
若所述两组进气槽的进气端均对应烟支的点燃端,两组出气槽的出气端均对应烟支的过滤嘴端,即两组检测均采用正向检测气流,所述气流从烟支的点燃端流向烟支的过滤嘴端。
35.进而获得:p进平均=(p1进平均+p2进平均)/2,p出平均=(p1出平均+p2出平均)/2,所述烟支的通风度f=(p进平均
‑ꢀ
p出平均),或者:烟支的通风度f=(p进平均
‑ꢀ
p出平均)/p进平均。
36.⑨
若所述一组进气槽的进气端对应烟支的点燃端以及出气槽的出气端对应烟支
的过滤嘴端(正向检测气流,即检测气流从烟支的点燃端流向烟支的过滤嘴端)、另一组进气槽的进气端对应烟支的过滤嘴端以及出气槽的出气端对应烟支的点燃端(反向检测气流,即气流从烟支的过滤嘴端流向烟支的点燃端),进而获得:所述烟支的正向通风度f正=(p1进平均 *c1
ꢀ‑ꢀ
p1出平均*c2),或者f正=(p1进平均 *c1
ꢀ‑ꢀ
p1出平均*c2)/p1进平均;烟支的反向通风度f反=(p2进平均*c3
‑ꢀ
p2出平均*c4),或者f反=(p2进平均*c3
‑ꢀ
p2出平均*c4)/p2进平均,c1c2c3c4为调整系数,为监测参数校准所需的调节常数。
37.上述的运算和方法的应用,可以实现代替轴编码器的功能,且安装简单快捷,且,无需利用软硬件进行无效数据的判断,简化了系统的设计,也降低了成本,平均值计算法,减小了因气压波动、机器运行波动、烟支抖动等因素造成的测量计算误差。
ꢀ⑨
烟支正向过滤嘴通风度:fv1=β1*f正β1为设定的调节系数;烟支反向过滤嘴通风度:fv2=β2*f反,β2为设定的调节系数;烟支过滤嘴通风度:pv=fv1*c1+fv2*c2。
38.注:由于在线检测的仪器结构所限,无法直接实现烟支过滤嘴通风度的检测,考虑本文已经实现了整支烟支的通风度的检测,另外烟支的点燃段通风度具有相对的固定性,经过大量数据试验因而给出c1和c2的调整系数,从而实现过滤嘴通风度的在线检测。
39.同步信号变换以及采样运算流程 为了减少这样的气流波动,通常采用了恒压供气结合小孔喷嘴的技术方案,对气流通路预先设置一定的阻力(小孔阻力),从而减少烟支进出检测区域对气压造成的波动。尽管取得一定的效果但是却不能完全消除气压的震荡,进而影响参数的稳定检测。小孔喷嘴一种形式:设置在石墨弧板进气端的气流入口处,有逐渐收缩的进气段、小孔段、逐渐扩展的出气段构成。
40.小孔段,由至少一个通气小孔构成,所述小孔的孔径0.1mm
‑‑
2.5mm,优选0.1
‑‑
1.2mm,以此对进气气流形成一个预先设定的高阻力(相关设备说明书中有此描述),用于在小孔出气端形成一个稳定的不受后续影响的稳定气流,构成烟支检测恒流的检测要素,形成一17.5ml/s的气流量;或者优选0.3
‑‑
1.8mm,以此对进气气流形成一个预先设定的阻力,用于在小孔出气端形成一个稳定的不受后续影响的稳定气压力,与烟支本身的吸阻进行配合,构成烟支检测恒压、恒流的检测要素,形成一稳定 的气流压力值;小孔喷嘴另一种形式:节流进气喷嘴为一空心管,所述空心管内设置有小孔段,所述小孔段为上设通孔的隔板,隔板厚度l1,隔板中心附近区域内设定至少一个直径d:0.1
‑
0.7mm的微孔,l1/d满足:0.5<l1/d≤6构成短孔时,以形成一具有气流节流效果的元件;在线烟支通风度检测精度的装置,其特征在于:所述恒压式节流进气喷嘴为一空心管内设置有相互顺序连通的缩径段、小孔段和扩径段,所述缩径段为进气段,所述扩径段为出气段,所述小孔段的长度l2,孔径d,为一细长型孔,当小孔段长3
‑
8mm,孔径范围0.8mm
‑‑
2.5mm,形成一文丘理管,在其扩径段获得较低压力,而具有稳定气流压力的功能;具有恒流与恒压气流喷嘴的组合:小孔隔板设置在小孔段气流出口端与扩径段交
接之处,进气压力被缩径段收缩,速度上升压力降低,从而在隔板附近产生一个较为恒定低压区,再利用具有节流功能的微孔隔板,从而实现恒压恒流的效果。
41.进而达到稳定烟支进出检测区域时,因气流的开闭造成检测压力、检测气流的波动或者震荡。
42.数学模型:流量qin=(pin
‑
pout)/(r阻+r载),由于烟支进出检测区域,造成气压气流的脉动,即形成r载的波动,造成流量qin的波动,使得检测参数失准。
43.若r阻>>r载:当r载波动变化时,r阻+r载变化不大,继而使得流量qin=(pin
‑
pout)/(r阻+r载)=恒定值。
44.确保检测参数的稳定准确。
45.设置c1c2c3c4等调节参数的原因如下:烟支吸阻和通风度定义如下:卷烟吸阻和滤棒压降检测的测定定义和测量原理:其中对吸阻定义为吸阻draw resistance :将卷烟密封于测量设备中,输出端插入深度为9 mm,在gb/t 16447的标准条件下维持输出端流速为17.5 ml/s而对输出端施加的负压恒定气流流量。
46.需要在吸嘴端产生一个17.5ml/s的负压恒定气流流量,将分段测量的气流流量与17.5ml/s进行比值,即可获得标准的总通风度或者过滤嘴通风度数值。
47.因此,国家标准对应的是负压抽吸检测,负压恒定气流17.5ml/s的流量。而实际应用在线测量时,负压检测方式会吸入环境、烟支端部的烟末或灰尘而造成检测传感器失准或者堵塞,所以,目前的检测都是采用正压气流恒压、恒流检测以模拟实验室环境下获得的检测数据。因此,首先必须获得波动小、数据准确的压力值,然后根据试验室检测数据进行传感器的校准,利用c1c2c3c4调节系数使得实际检测数据得以修正达到模拟烟支通风度、吸阻的目的。
48.增加小孔喷嘴的原因:采用小孔喷嘴前后,烟支进出检测区域的气压波动数据曲线如图8:可见,采用小孔喷嘴的确能够起到稳定气压、形成恒定流量的目的,进而减少烟支进出检测区域造成的气压、气流流量的波动,扩大了气压、气流的稳定区域,增加了传感器有效工作时间。
49.技术效果:减少了对轴编码器的安装及其配套专业的信号采集运算模块的使用降低了设备成本;简化了运算检测触发脉冲的步骤,简化了运算软件的流程,提高了运算速度;将烟支进出检测区域时产生气压波动的检测参数不进行检测,减少数据处理量,提升了采集效率;只对烟支进入检测区域后气压已经稳定的检测参数进行检测,提高了检测效率,提高了检测数据的有效性,提高了检测参数的精度。
50.采用人机界面输入数据采集的定位延时参数,装置使用更灵活,人机沟通更高效。
51.前述对本发明的具体示例性实施方案的描述是为了说明和例证的目的。 这些描述并非想将本发明限定为所公开的精确形式,并且很显然,根据上述 教导,可以进行很多改变和变化。对示例性实施例进行选择和描述的目的在 于解释本发明的特定原理及其实际应用,从而使得本领域的技术人员能够实 现并利用本发明的各种不同的示例性实施方案以及各种不同的选择和改变。 本发明的范围意在由权利要求书及其等同形式所限定。