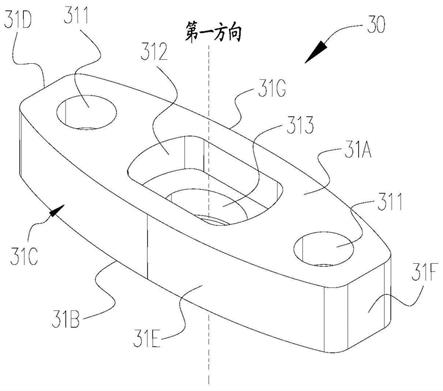
1.本发明涉及模拟吸烟技术领域,特别地,涉及一种发热组件及雾化组件、雾化器、气溶胶发生装置。
背景技术:
2.吸液件由于其抗氧化、耐高温、耐腐蚀、使用寿命长以及不易产生焦糊等特性,被广泛应用于气溶胶发生装置的吸液加热模块中,然而在吸液件的实际生产工艺中,在保证吸液件具有一定的产品合格率的前提下,如何使制得的吸液件既具有较高的导液速率同时吸液件的强度也满足要求是人们研究的重点。
3.目前,市场上的气溶胶发生装置通常采用纤维棉材质的导液绳缠绕发热丝的发热组件,气溶胶形成基质传导效率低,且当气溶胶发生装置的输出功率过高时导液绳会因缺液而发生烧焦的现象,进而产生异味,影响用户吸烟口感;另外,发热丝上各处发热量基本一致,当导液绳上各部分吸收不等量的气溶胶形成基质时,气溶胶形成基质量多的部分无法被发热丝充分雾化,进而导致漏液,气溶胶形成基质量少的部分因无法满足雾化需要易发生导液绳干烧的情况,以上,均会降低用户的使用体验。
4.气溶胶发生装置,又名电子雾化器,其是一种通过加热气溶胶形成基质形成烟雾以供用户吸食的电子产品。使用时,形成的烟雾在用户的抽吸作用下进入至出气通道内,最终进入至用户口中。
5.在实际使用过程中,由于形成的烟雾的温度相对较高,烟雾在进入至出气通道内时无法充分冷凝,导致最终进入至用户口中的烟雾十分干燥,用户吸食口感不佳,降低了用户的使用体验。
技术实现要素:
6.基于此,有必要提供一种具有较高产品合格率,同时兼具较高导液速率以及较高强度的吸液件及其制备方法、发热组件及其制备方法。
7.本发明解决其技术问题所要采用的技术方案是:
8.一种吸液件,所述吸液件由硅藻土、玻璃粉以及造孔剂通过烧结工艺制得,所述吸液件中大于80%的孔径集中在14.21~20.21μm之间,所述吸液件的开放孔隙率为55~65%。
9.进一步地,所述造孔剂为聚甲基丙烯酸甲酯,所述造孔剂的球度为0.9~0.95,所述造孔剂的粒径为15~70μm。
10.进一步地,所述玻璃粉的tg(玻璃化温度)为750~800℃,玻璃粉的tf(粘流温度)为900~950℃。
11.一种如上述任一项所述的吸液件的制备方法,包括以下步骤:
12.1)制备预混料:将硅藻土、玻璃粉以及造孔剂混合均匀,得到预混料;
13.2)制备压铸料:将步骤1)制得的预混料与成型助剂混合,得到压铸料;
14.3)制备陶瓷胚体:将步骤2)制备的压铸料进行压铸成型,得到陶瓷胚体;
15.4)脱胶处理:将步骤3)制备的陶瓷胚体以0.5~1.5℃/min的升温速率升温至40~60℃,保温5~20min;再以0.5~1.5℃/min的升温速率升温至160~250℃,保温100~150min,然后停止加热,冷却;
16.5)制备吸液件:将步骤4)得到的陶瓷胚体以2~4℃/min的升温速率升温至180~250℃,保温5~20min;再以0.5~1.5℃/min的升温速率升温至450~550℃,保温40~80min;再以8~12℃/min的升温速率升温至970~1080℃,保温90~130min,得到吸液件。
17.进一步地,所述吸液件包括55~75%预混料和25~45%成型助剂,所述预混料包括15~50%硅藻土、20~60%玻璃粉以及10~50%造孔剂,所述成型助剂包括60~90%的石蜡和10~40%的硬脂酸。
18.进一步地,所述成型助剂由下述制备步骤制得:将所述石蜡和所述硬脂酸在75~120℃加热搅拌,搅拌过程中抽真空,搅拌时间为1.5~2.5小时。
19.进一步地,所述步骤2)中将预混料加入混合均匀的石蜡和硬脂酸中,在75~120℃加热搅拌,搅拌过程中抽真空,搅拌时间为3~5小时。
20.一种发热组件,所述发热组件包括上述任一项所述的吸液件和设置在所述吸液件上的发热件,所述吸液件包括上端面和雾化面,所述上端面和所述雾化面相对设置,所述吸液件用于将气溶胶形成基质由所述上端面传导至所述雾化面上,所述发热件设置在所述雾化面上,所述吸液件的上端面上凹陷有进液槽,所述进液槽用于接触气溶胶形成基质。
21.一种如上述的发热组件的制备方法,包括以下步骤:将金属浆料涂覆在吸液件的其中一端面,以2.5~4℃/min的升温速率升温至480~520℃,再将吸液件以8~12℃/min的升温速率升温至810~910℃,保温10~30min,使所述金属浆料形成发热件,得到发热组件。
22.进一步地,所述金属浆料包括48%~73%ag、5~35%pd和13~20%粘结剂。
23.本发明的有益效果是:本发明的吸液件通过硅藻土、烧结助剂和造孔剂通过烧结工艺制得,且吸液件中大于80%的孔径集中在14.21~20.21μm之间,吸液件的开放孔隙率为55~65%,该吸液件不仅具有较高导液速率,且吸液件的强度较高。
24.本发明提供的吸液件及其制备方法,通过选择合适比例的预混料和成型助剂混合制备压铸料,然后压铸、脱胶以及烧结制备吸液件,制备的吸液件的产品合格率较高,且制得的吸液件的强度较高,孔径大小分布均匀,导油速率较高。
25.本发明中选择球度为0.9~0.95的聚甲基丙烯酸甲酯作为造孔剂,造孔剂的粒径为15~70μm,烧结过程中造孔剂均匀且充分从陶瓷胚体中排出,形成陶瓷胚体的孔洞结构,孔径大小分布均匀。
26.本发明中采用较低玻璃化温度和粘流温度的玻璃粉,使陶瓷胚体能够在较低的温度下烧结,玻璃粉起到低温粘结作用,既能提高强度,同时不会破坏造孔剂挥发所残留的通孔,使得本发明制备的吸液件兼具较高的强度和较高的导油速率。
27.本发明提供的发热组件,包括吸液件和设置在所述吸液件上的发热件,所述吸液件由硅藻土和玻璃粉通过烧结工艺制得,所述吸液件中大于80%的孔径集中在14.21~20.21μm之间,使得本发明的发热组件不仅具有较高的导液速率,且发热组件的强度满足要求。
28.本发明提供的发热组件的制备方法,通过选择由硅藻土和玻璃粉经分阶段升温烧
结工艺制作的吸液件,并在吸液件的表面上涂覆金属浆料,升温加热,使金属浆料形成发热件,得到兼具较高导油速率和较高强度的发热组件。
29.本发明还提供了一种可根据待雾化气溶胶形成基质量的多少合理进行加热的发热组件;
30.还有必要提供一种带有该发热组件的雾化组件;
31.还有必要提供一种带有该雾化组件的雾化器;
32.更有必要提供一种带有该雾化器的气溶胶发生装置。
33.本发明解决其技术问题所采用的技术方案是:一种发热组件,所述发热组件包括吸液件和发热件,所述吸液件由多孔材料制成,所述吸液件包括上端面和雾化面,所述上端面和所述雾化面相对设置,所述吸液件用于将气溶胶形成基质由所述上端面传导至所述雾化面上,所述发热件设置在所述雾化面上,所述发热件上待雾化气溶胶形成基质多的区域的电阻大于所述发热件上待雾化气溶胶形成基质量少的区域的电阻。
34.进一步地,所述吸液件的上端面上凹陷有进液槽,所述进液槽用于接触气溶胶形成基质,所述发热件包括第一发热部和第二发热部,所述第一发热部与所述进液槽位置相对应,且所述第一发热部的电阻大于所述第二发热部的电阻。
35.进一步地,所述进液槽具有两个,两个所述进液槽分别位于所述上端面相对的两侧,所述第一发热部具有两个,两个所述第一发热部分别连接在所述第二发热部相对的两侧,且一个所述第一发热部与一个所述进液槽位置相对应,两个所述第一发热部关于所述第二发热部呈中心对称设置。
36.进一步地,所述第二发热部呈环状结构,所述第一发热部呈朝向所述第二发热部折弯的条形结构,所述第一发热部的一端与所述第二发热部平滑过渡连接。
37.进一步地,所述第一发热部的宽度尺寸t1小于所述第二发热部的宽度尺寸t2。
38.进一步地,所述第一发热部远离所述第二发热部的一端设置有接电部,所述接电部用于供电极柱抵接,所述上端面上凹陷有凹槽,所述第二发热部与所述凹槽位置相对应,所述接电部与所述进液槽及所述凹槽之间未减薄的区域位置相对应。
39.进一步地,所述吸液件内设置有过气通道,所述过气通道的一端贯通所述凹槽的槽底壁,所述过气通道的另一端贯通所述雾化面,所述第二发热部环设在所述过气通道的外周。
40.进一步地,所述上端面和雾化面相互平行,所述雾化面朝向所述上端面的方向定义为所述吸液件的第一方向,所述吸液件上沿所述第一方向由所述雾化面延伸至所述上端面的距离为吸液件的高度h,所述凹槽沿所述第一方向的深度为h,0.3≤h/h≤0.5。
41.一种雾化组件,所述雾化组件包括前述任一项所述的发热组件。
42.一种雾化器,所述雾化器包括前述的雾化组件,所述雾化器还包括储液件,所述储液件内设置有储液腔,所述储液腔用于存储气溶胶形成基质。
43.一种气溶胶发生装置,所述气溶胶发生装置包括前述的雾化器,所述气溶胶发生装置还包括电源装置,所述电源装置与所述雾化器电性连接。
44.本发明的有益效果是:本发明提供的发热组件或雾化组件或雾化器或气溶胶发生装置,设置在雾化面上的发热件上待雾化气溶胶形成基质量多的区域的电阻大于发热件上待雾化气溶胶形成基质量少的区域的电阻,使得发热件上的各区域能够根据气溶胶形成基
质的多少适应性地产生适量热量以满足雾化需要,有效避免了漏液及干烧,同时,由多孔材料制成的吸液件具有较高的耐高温性,可有效防止吸液件被烧焦,提升了用户的吸烟口感。
45.本发明还提供了一种烟雾冷凝效果好的雾化器;
46.同时提供了一种带有该雾化器的气溶胶发生装置。
47.本发明解决其技术问题所采用的技术方案是:一种雾化器,所述雾化器包括储液件、雾化组件和进气管,所述雾化组件设置在所述储液件的一端,所述储液件内设置有储液腔和出气通道,所述储液腔用于存储气溶胶形成基质,所述雾化组件包括发热组件、雾化腔及进气口,所述发热组件加热气溶胶形成基质生成的烟雾充斥于所述雾化腔内,所述进气口与所述雾化腔及外部大气均连通,所述雾化腔与所述出气通道的进气端连通,所述进气管的进气端与外部大气连通,所述进气管的出气端延伸至所述出气通道的进气端。
48.进一步地,所述出气通道相对所述雾化腔设于所述发热组件的另一侧,所述发热组件上开设有过气通道,所述过气通道与所述雾化腔及所述出气通道的进气端均连通,所述进气管通过所述过气通道穿过所述发热组件,所述过气通道的通道壁与所述进气管的外壁之间形成一间隙。
49.进一步地,所述进气管为直管,所述出气通道为笔直通道,所述进气管的中轴线与所述出气通道的中轴线共线。
50.进一步地,所述发热组件包括吸液件和发热件,所述吸液件包括相对设置的上端面和雾化面,所述上端面设置有与所述储液腔连通的进液槽,所述发热件设置在所述雾化面上,所述过气通道开设在所述吸液件上。
51.进一步地,所述上端面凹陷形成有凹槽,所述过气通道的一端贯通所述凹槽的槽底壁,所述过气通道的另一端贯通所述雾化面,所述凹槽的横截面积大于所述过气通道的横截面积。
52.进一步地,所述雾化组件还包括雾化支架和雾化底座,所述雾化支架和所述雾化底座配合连接,所述雾化腔形成于所述雾化底座内,所述发热组件设置在所述雾化支架和所述雾化底座之间,所述进气口开设在所述雾化底座上,所述雾化底座上还开设有进气孔,所述进气孔与外部大气连通,所述进气管的进气端与所述雾化底座连接且与所述进气孔对应连通。
53.进一步地,所述储液件包括外壳和收容于所述外壳内的通气管,所述储液腔由所述外壳的内腔形成,所述出气通道由所述通气管的内腔形成,所述雾化支架上设置有进液口和出气槽,所述进液口与所述储液腔连通,所述出气槽与所述凹槽连通,所述出气通道与所述出气槽连通。
54.进一步地,所述出气槽为锥形槽,所述出气槽的大口端与所述凹槽对应连通,所述出气槽的小口端与所述出气通道连通。
55.进一步地,所述储液件还包括烟嘴,所述烟嘴套设在所述外壳上端的外部,所述烟嘴上开设有出烟口,所述出烟口与所述出气通道的出气端连通。
56.一种气溶胶发生装置,所述气溶胶发生装置包括前述任一项所述的雾化器,所述气溶胶发生装置还包括电源装置,所述电源装置与所述雾化器电性连接。
57.本发明的有益效果是:本发明提供的雾化器或电子烟,通过设置进气管,使进气管的出气端延伸至出气通道的进气端,如此,温度较高的烟雾和温度较低的外部气体于出气
通道的进气端混合,使得烟雾充分冷凝形成较大烟雾颗粒,冷凝效果好,提升了吸食口感,用户使用体验提升。
附图说明
58.下面结合附图和实施例对本发明作进一步说明。
59.图1是本发明实施例1制备的吸液件31在超景深显微镜放大300倍下的微观形貌图;
60.图2是本发明实施例1制备的吸液件31在超景深显微镜放大600倍下的微观形貌图;
61.图3是本发明实施例1制备的吸液件31的sem(扫描电子显微镜)图;
62.图4是本发明实施例1制备的吸液件31的又一sem(扫描电子显微镜)图;
63.图5是本发明实施例1制备的吸液件31的孔径分布图;
64.图6是本发明雾化器及气溶胶发生装置实施例一的雾化器的立体图;
65.图7是图6所示雾化器的剖视图;
66.图8是图7所示雾化器中发热组件的立体图;
67.图9是图8所示发热组件的俯视图;
68.图10是图8所示发热组件的仰视图;
69.图11是图8所示发热组件中吸液件的剖视图;
70.图12是传统发热件的结构示意图;
71.图13是干烧温度测试中获取的时间-温度曲线图;
72.图14是雾化温度测试中获取的时间-温度曲线图;
73.图15是本发明雾化器及气溶胶发生装置实施例二的雾化器的剖视图;
74.图16是图15所示雾化器中发热组件的立体图;
75.图17是图16所示发热组件的俯视图;
76.图18是图16所示发热组件的仰视图。
77.图中零部件名称及编号分别为:
78.雾化器100
ꢀꢀꢀꢀꢀꢀꢀꢀꢀꢀ
雾化组件110
ꢀꢀꢀꢀꢀꢀꢀꢀꢀ
储液件10
79.发热组件30
ꢀꢀꢀꢀꢀꢀꢀꢀꢀ
吸液件31
ꢀꢀꢀꢀꢀꢀꢀꢀꢀꢀꢀꢀ
发热件32
80.上端面31a
ꢀꢀꢀꢀꢀꢀꢀꢀꢀꢀ
雾化面31b
ꢀꢀꢀꢀꢀꢀꢀꢀꢀꢀꢀ
进液槽311
81.凹槽312
ꢀꢀꢀꢀꢀꢀꢀꢀꢀꢀꢀꢀ
过气通道313
ꢀꢀꢀꢀꢀꢀꢀꢀꢀ
连接面31c
82.第一端面31d
ꢀꢀꢀꢀꢀꢀꢀꢀ
第二端面31e
ꢀꢀꢀꢀꢀꢀꢀꢀꢀ
第三端面31f
83.第四端面31g
ꢀꢀꢀꢀꢀꢀꢀꢀ
第一发热部321
ꢀꢀꢀꢀꢀꢀꢀ
第二发热部322
84.接电部323
ꢀꢀꢀꢀꢀꢀꢀꢀꢀꢀ
雾化支架21
ꢀꢀꢀꢀꢀꢀꢀꢀꢀꢀ
进液口211
85.出气槽212
ꢀꢀꢀꢀꢀꢀꢀꢀꢀꢀ
雾化底座22
ꢀꢀꢀꢀꢀꢀꢀꢀꢀꢀ
雾化腔221
86.进气口222
ꢀꢀꢀꢀꢀꢀꢀꢀꢀꢀ
进气孔223
ꢀꢀꢀꢀꢀꢀꢀꢀꢀꢀꢀ
密封件23
87.电极柱24
ꢀꢀꢀꢀꢀꢀꢀꢀꢀꢀꢀ
进气管25
ꢀꢀꢀꢀꢀꢀꢀꢀꢀꢀꢀꢀ
密封套26
88.储液腔101
ꢀꢀꢀꢀꢀꢀꢀꢀꢀꢀ
出气通道102
ꢀꢀꢀꢀꢀꢀꢀꢀꢀ
外壳11
89.通气管12
ꢀꢀꢀꢀꢀꢀꢀꢀꢀꢀꢀ
烟嘴13
ꢀꢀꢀꢀꢀꢀꢀꢀꢀꢀꢀꢀꢀꢀ
出烟口131
90.插接部231
具体实施方式
91.现在结合附图对本发明作详细的说明。此图为简化的示意图,仅以示意方式说明本发明的基本结构,因此其仅显示与本发明有关的构成。
92.吸液件31及其制备方法、发热组件30及其制备方法实施例
93.本发明提供了一种吸液件31的制备方法,包括以下步骤:
94.1)制备预混料:将硅藻土、玻璃粉以及造孔剂混合均匀,得到预混料;
95.2)制备压铸料:将步骤1)制得的预混料与成型助剂混合,得到压铸料;
96.3)制备陶瓷胚体:将步骤2)制备的压铸料进行压铸成型,得到陶瓷胚体;
97.4)脱胶处理:将步骤3)制备的陶瓷胚体以0.5~1.5℃/min的升温速率升温至40~60℃,保温5~20min;再以0.5~1.5℃/min的升温速率升温至160~250℃,保温100~150min,然后停止加热,冷却;
98.5)制备吸液件31:将步骤4)得到的陶瓷胚体以2~4℃/min的升温速率升温至180~250℃,保温5~20min;再以0.5~1.5℃/min的升温速率升温至450~550℃,保温40~80min;再以8~12℃/min的升温速率升温至970~1080℃,保温90~130min,得到吸液件31;
99.所述步骤2)中按照55~75%的预混料和25~45%的成型助剂混合。
100.所述步骤1)中玻璃粉的tg(玻璃化温度)为750~800℃,玻璃粉的tf(粘流温度)为900~950℃,玻璃粉的tm(熔化温度)为950-1100℃。可以理解地,在其它未示出的实施方式中,烧结助剂还可以是磷酸铝。
101.所述步骤1)中按照15~50%硅藻土、20~60%玻璃粉以及10~50%造孔剂进行混合制备预混料。
102.所述硅藻土的粒径为5~35μm。
103.所述造孔剂为聚甲基丙烯酸甲酯,所述造孔剂的球度为0.9~0.95,所述造孔剂的粒径为15~70μm。
104.所述造孔剂还可以是淀粉、石墨、碳粉或木质素中的任意一种。
105.所述成型助剂包括60~90%的石蜡和10~40%的硬脂酸。
106.所述成型助剂由下述制备步骤制得:将所述石蜡和所述硬脂酸在75~120℃加热搅拌,搅拌过程中抽真空,搅拌时间为1.5~2.5小时。
107.将预混料加入混合均匀的石蜡和硬脂酸中,在75~120℃加热搅拌,搅拌过程中抽真空,搅拌时间为3~5小时。
108.所述步骤3)中压铸成型的温度为70~80℃,压铸压力为0.5~1mpa,压铸时间为3~10s。
109.一种由上述吸液件31的制备方法制备的吸液件31,所述吸液件31由硅藻土和玻璃粉通过烧结工艺制得,所述吸液件31中大于80%的孔径集中在14.21~20.21μm之间,孔径大小分布均匀。
110.一种由上述吸液件31的制备方法制备的吸液件31的开放孔隙率为55~65%。优选的,所述吸液件31的开放孔隙率为60.6%。
111.一种含有上述所述的吸液件31的发热组件30的制备方法,包括以下步骤:将制备的吸液件31的其中一端面作为印刷面,在所述印刷面上涂覆金属浆料,以2.5~4℃/min的升温速率升温至480~520℃,再将吸液件31以8~12℃/min的升温速率升温至810~910℃,
保温10~30min,所述金属浆料形成发热件32,得到发热组件30。
112.在所述印刷面上涂覆金属浆料之前先对印刷面进行打磨处理,印刷面的打磨厚度为0.1~0.3mm。
113.所述金属浆料包括48%~73%ag、5~35%pd和13~20%粘结剂。
114.一种由上述发热组件30的制备方法制备的发热组件30,所述发热组件30包括吸液件31和设置在所述吸液件31上的发热件32,所述吸液件31由硅藻土和玻璃粉通过烧结工艺制得,所述吸液件31中大于80%的孔径集中在14.21~20.21μm之间。
115.所述吸液件31的开放孔隙率为55~65%。
116.硅藻土包括二氧化硅sio2以及少量的氧化物和有机质,其中sio2的质量分数为80%以上,其中硅藻土中的氧化物包括:氧化铝al2o3、氧化铁fe2o3、氧化钙cao、氧化镁mgo、氧化钾k2o、氧化钠na2o、氧化磷p2o5;玻璃粉既用作吸液件31的骨料,还用作吸液件31的助烧剂,降低烧结温度,并在高温产生具有粘结作用的玻璃相,提高吸液件31的强度。玻璃粉包括:o:49.94%,na:3.34%;mg:0.83%;al:4.6%;si:28.35%;k:2.35%;ca:3.81%;ba:6.78%,使用前将玻璃粉粉碎至粒径为1.5~6μm,控制玻璃粉的粒径有利于玻璃粉的分散操作和烧结,能够使吸液件31兼具较高的强度和较高的开放孔隙率。玻璃粉的粒径小于1.5μm,玻璃粉的比表面积大,不利于混料与分散操作,会导致吸液件31的开放孔隙率较低;玻璃粉的粒径大于6μm,玻璃粉混料后的均匀性差,烧结后,会出现聚集现象,导致吸液件31的强度较差。
117.本发明中玻璃粉的tg(玻璃化温度)为750~800℃,玻璃粉的tf(粘流温度)为900~950℃。玻璃粉在高温状态下,玻璃粉中的玻璃相液化,陶瓷胚体中存在显著数量的液态玻璃相;并且硅藻土在液态玻璃相内有溶解度;液态玻璃相能润湿硅藻土,在此基础上,硅藻土颗粒间的每一空隙都变成毛细管,在这种毛细管里产生巨大的毛细管力,毛细管力即为吸液件31烧结动力,促进硅藻土烧结,因此可以增强吸液件31的强度;玻璃粉体在原料中占有的比例较多,因此在高温状态下,液化后的玻璃相可以粘连硅藻土颗粒,起到加固作用。采用满足较低tg(玻璃化温度)和tf(粘流温度)的玻璃粉,使陶瓷胚体能够在较低的温度下烧结,玻璃粉能够起到低温粘结作用,既能提高强度,同时也不会破坏造孔剂挥发所残留的通孔,从而使制备得到的吸液件31兼具较高的强度和较高的开放孔隙率。
118.造孔剂用于增加多孔陶瓷中孔洞的结构,控制造孔剂的粒径可以控制制备的吸液件31中孔洞结构的大小,本发明中采用聚甲基丙烯酸甲酯作为造孔剂,造孔剂的粒径为15~70μm,造孔剂的球度为0.9~0.95。
119.实施例1
120.本实施例的吸液件31由67%预混料和33%成型助剂制得,其中,所述预混料包括33%硅藻土、30%玻璃粉以及37%造孔剂,所述成型助剂包括85%硬脂酸和15%石蜡制得,所述硅藻土的中值粒径为19.85μm,所述玻璃粉的中值粒径为3.68μm,所述造孔剂为聚甲基丙烯酸甲酯,所述造孔剂的球度为0.95,所述造孔剂的中值粒径为30μm,中值粒径是指一个样品的累计粒度分布百分数达到50%时所对应的粒径,物理意义是粒径大于它的颗粒占50%,小于它的颗粒也占50%。
121.本实施例的吸液件31的制备方法,包括以下步骤:
122.1)制备预混料:将本实施例的33%硅藻土、30%玻璃粉以及37%造孔剂采用滚筒
球磨机搅拌混合均匀,混合时间为4h,使得造孔剂在预混料中均匀分布,得到预混料;可以理解地,在其它未示出的实施方式中,还可以采用v型混料机或者搅拌机等设备进行干混混合;
123.2)制备压铸料:先将85%石蜡和15%硬脂酸采用油温机加热至100℃,使石蜡和硬脂酸融化,采用搅拌机搅拌,并在搅拌过程中抽真空,真空度为-0.098mpa,搅拌时间为2小时,排出熔融状态下的石蜡和硬脂酸中的气泡,得到混合均匀的成型助剂,然后将步骤1)制得的预混料与上述混合均匀的成型助剂采用油温机加热至100℃,采用搅拌机搅拌,在搅拌过程中抽真空,真空度为-0.098mpa,搅拌时间为4小时,排出熔融状态下的预混料、石蜡以及硬脂酸中的气泡,得到压铸料;
124.3)制备陶瓷胚体:将步骤2)制备的压铸料加入rz-8型热压注浆机内,在压铸温度为75℃,压铸压力为0.6mpa下进行压铸成型,压铸时间为6s,得到陶瓷胚体;可以理解地,在其它未示出的实施方式中,注浆机的容量较小时,可将压铸料进行切粒至粒径小于5mm,将切成粒状的压铸料倒入注浆机内进行压铸即可;
125.4)脱胶处理:将步骤3)制备的陶瓷胚体进行第一阶段升温,以1℃/min的升温速率升温至50℃,保温10min;然后进行第二阶段升温,以0.5℃/min的升温速率升温至200℃,保温120min,然后停止加热,冷却;其中,第一阶段升温的作用是使得陶瓷胚体的内部和外部温度升高,第一阶段升温之后保温一段时间使得陶瓷胚体的内部外部温度一致,保证后续工艺处理过程中成型助剂能够均匀从陶瓷胚体中脱出,第二阶段升温的作用是使得陶瓷胚体中的成型助剂部分排出,以便保持陶瓷胚体的强度,便于后期高温烧结处理,由于石蜡的熔点为52-78℃,沸点为300-550℃,硬脂酸的熔点为67-73℃,沸点为176-184℃,在第二阶段的保温过程中,使得硬脂酸汽化并从陶瓷胚体中排出,石蜡融化并在重力作用下从陶瓷胚体中排出。
126.5)制备吸液件31:将步骤4)得到的陶瓷胚体以3℃/min的升温速率升温至200℃,保温10min;再以1℃/min的升温速率升温至500℃,保温30min;再以10℃/min的升温速率升温至1050℃,保温120min,最后停止加热,自然冷却得到吸液件31。其中,第一阶段保温的作用是使陶瓷胚体的内部和外部温度一致,防止由于陶瓷胚体内部和外部存在温差,使得陶瓷胚体出现变形、开裂等现象;第二阶段保温的作用是彻底排放造孔剂,使得陶瓷胚体中不含有有机成分,防止第三阶段升温过程中温度较高,残余的有机成分挥发导致陶瓷胚体出现开裂现象;第三阶段保温的作用是将陶瓷胚体各部分均匀烧制成吸液件31,保证吸液件31的强度。由于造孔剂聚甲基丙烯酸甲酯的沸点为195~205℃,在第一阶段保温与第二阶段保温之间,聚甲基丙烯酸甲酯汽化并从陶瓷胚体中排出,从而形成陶瓷胚体中的孔洞结构,为实现聚甲基丙烯酸甲酯充分且均匀地从陶瓷胚体中排出,此时的升温速率较慢。
127.本实施例的含有上述吸液件31的发热组件30的制作方法,包括以下步骤:将上述制备的吸液件31的其中一端面作为印刷面,对所述印刷面进行打磨处理,印刷面的打磨厚度为0.2mm,然后在所述印刷面上涂覆金属浆料,所述金属浆料包括:65%ag、20%pd以及15%粘结剂,粘接剂的型号b76,生产厂家为国药试剂,以3℃/min的升温速率升温至500℃,再将吸液件31以10℃/min的升温速率升温至880℃,保温20min,所述金属浆料形成发热件32,发热件32的厚度为40μm,得到发热组件30。
128.吸液件31的印刷面为吸液件31上设置发热件32的端面,对吸液件31的印刷面进行
打磨处理,有两个作用:第一,能够将吸液件31的印刷面上在烧结工艺中产生的封闭孔打磨掉;第二,吸液件31烧结后表面不平整,打磨印刷面以避免厚膜或薄膜工艺形成发热件32时凹凸的表面导致的短路问题。为了实现打磨,在制造陶瓷胚体的时候,陶瓷胚体高度会比设计高度多0.1~0.3mm左右,烧结成吸液件31后,吸液件31的高度相对于陶瓷胚体的高度收缩,但是多孔陶瓷的高度仍然会比设计高度多。
129.本实施方式中,采用80目的砂轮对吸液件31的印刷面进行打磨处理,从而保持印刷面上孔洞结构的形貌。可以理解地,在其它未示出的实施方式中,还可以利用砂纸、磨头等工具对印刷面进行打磨处理。印刷面的打磨厚度随吸液件31的设计要求不同可有所调整。
130.本实施例在所述吸液件31的印刷面上涂覆金属浆料后,以3℃/min的升温速率升温至500℃,使得粘结剂发生汽化并从发热组件30上排出,此时,为了粘结剂能够充分从发热组件30上排出,此时升温速率稍慢,然后以10℃/min的升温速率升温至880℃,保温20min,相比第一阶段的升温速率,第二阶段的升温速率较高,从而提高了生产效率。在第二阶段的保温时间内,玻璃粉将ag和pd与硅藻土粘接,使得金属浆料与吸液件31的印刷面紧密结合。
131.实施例2
132.本实施例的吸液件31由60%预混料和40%成型助剂制得,其中,所述预混料包括25%硅藻土、35%玻璃粉以及40%造孔剂,所述成型助剂包括25%硬脂酸和75%石蜡制得,所述硅藻土的中值粒径为55μm,所述玻璃粉的中值粒径为1.5μm,所述造孔剂为聚甲基丙烯酸甲酯,所述造孔剂的球度为0.9,所述造孔剂的中值粒径为15μm。
133.本实施例的吸液件31的制备方法,包括以下步骤:
134.1)制备预混料:将本实施例的25%硅藻土、35%玻璃粉以及40%造孔剂采用滚筒球磨机搅拌混合均匀,混合时间为4h,得到预混料。
135.2)制备压铸料:先将75%石蜡和25%硬脂酸采用油温机加热至100℃,使石蜡和硬脂酸融化,采用搅拌机搅拌,并在搅拌过程中抽真空,真空度为-0.098mpa,搅拌时间为2小时,排出熔融状态下的石蜡和硬脂酸中的气泡,得到混合均匀的成型助剂,然后将步骤1)制得的预混料与上述混合均匀的成型助剂采用油温机加热至100℃,采用搅拌机搅拌,在搅拌过程中抽真空,真空度为-0.098mpa,搅拌时间为4小时,排出熔融状态下的预混料、石蜡以及硬脂酸中的气泡,得到压铸料;
136.3)制备陶瓷胚体:将步骤2)制备的压铸料加入rz-8型热压注浆机内,在压铸温度为75℃,压铸压力为0.7mpa下进行压铸成型,压铸时间为4s,得到陶瓷胚体;
137.4)脱胶处理:将步骤3)制备的陶瓷胚体进行第一阶段升温,以1.5℃/min的升温速率升温至50℃,保温10min;然后进行第二阶段升温,以0.5℃/min的升温速率升温至200℃,保温150min,然后停止加热,冷却。
138.5)制备吸液件31:将步骤4)得到的陶瓷胚体以2℃/min的升温速率升温至200℃,保温20min;再以0.8℃/min的升温速率升温至500℃,保温60min;再以10℃/min的升温速率升温至1010℃,保温120min,最后停止加热,自然冷却得到吸液件31。
139.本实施例的含有上述吸液件31的发热组件30的制作方法,包括以下步骤:将上述制备的吸液件31的其中一端面作为印刷面,对所述印刷面进行打磨处理,印刷面的打磨厚
度为0.2mm,然后在所述印刷面上涂覆金属浆料,所述金属浆料包括:65%ag、20%pd以及15%粘结剂,粘接剂的型号b76,生产厂家为国药试剂,以3℃/min的升温速率升温至500℃,再将吸液件31以10℃/min的升温速率升温至880℃,保温20min,所述金属浆料形成发热件32,发热件32的厚度为40μm,得到发热组件30。
140.本实施例在所述吸液件31的印刷面上涂覆金属浆料后,以3℃/min的升温速率升温至500℃,使得粘结剂发生汽化并从发热组件30上排出,此时,为了粘结剂能够充分从发热组件30上排出,此时升温速率稍慢,然后以10℃/min的升温速率升温至880℃,保温20min,相比第一阶段的升温速率,第二阶段的升温速率较高,从而提高了生产效率。在第二阶段的保温时间内,玻璃粉将ag和pd与硅藻土粘接,使得金属浆料与吸液件31的印刷面紧密结合。
141.实施例3
142.本实施例的吸液件31由75%预混料和25%成型助剂制得,其中,所述预混料包括40%硅藻土、25%玻璃粉以及35%造孔剂,所述成型助剂包括15%硬脂酸和85%石蜡制得,所述硅藻土的中值粒径为11.23μm,所述玻璃粉的中值粒径为4.43μm,所述造孔剂为聚甲基丙烯酸甲酯,所述造孔剂的球度为0.95,所述造孔剂的中值粒径为20μm。
143.本实施例的吸液件31的制备方法,包括以下步骤:
144.1)制备预混料:将本实施例的40%硅藻土、25%玻璃粉以及35%造孔剂采用滚筒球磨机搅拌混合均匀,混合时间为4h,得到预混料。
145.2)制备压铸料:先将85%石蜡和15%硬脂酸采用油温机加热至100℃,使石蜡和硬脂酸融化,采用搅拌机搅拌,并在搅拌过程中抽真空,真空度为-0.098mpa,搅拌时间为2小时,排出熔融状态下的石蜡和硬脂酸中的气泡,得到混合均匀的成型助剂,然后将步骤1)制得的预混料与上述混合均匀的成型助剂采用油温机加热至100℃,采用搅拌机搅拌,在搅拌过程中抽真空,真空度为-0.098mpa,搅拌时间为4小时,排出熔融状态下的预混料、石蜡以及硬脂酸中的气泡,得到压铸料;
146.3)制备陶瓷胚体:将步骤2)制备的压铸料加入rz-8型热压注浆机内,在压铸温度为75℃,压铸压力为0.7mpa下进行压铸成型,压铸时间为10s,得到陶瓷胚体;
147.4)脱胶处理:将步骤3)制备的陶瓷胚体进行第一阶段升温,以1.5℃/min的升温速率升温至50℃,保温10min;然后进行第二阶段升温,以1℃/min的升温速率升温至180℃,保温90min,然后停止加热,冷却。
148.5)制备吸液件31:将步骤4)得到的陶瓷胚体以4℃/min的升温速率升温至180℃,保温10min;再以1℃/min的升温速率升温至550℃,保温60min;再以10℃/min的升温速率升温至1080℃,保温120min,最后停止加热,自然冷却得到吸液件31。
149.本实施例的含有上述吸液件31的发热组件30的制作方法,包括以下步骤:将上述制备的吸液件31的其中一端面作为印刷面,对所述印刷面进行打磨处理,印刷面的打磨厚度为0.2mm,然后在所述印刷面上涂覆金属浆料,所述金属浆料包括:65%ag、20%pd以及15%粘结剂,粘接剂的型号b76,生产厂家为国药试剂,以3℃/min的升温速率升温至500℃,再将吸液件31以10℃/min的升温速率升温至880℃,保温20min,所述金属浆料形成发热件32,发热件32的厚度为40μm,得到发热组件30。
150.本实施例在所述吸液件31的印刷面上涂覆金属浆料后,以3℃/min的升温速率升
温至500℃,使得粘结剂发生汽化并从发热组件30上排出,此时,为了粘结剂能够充分从发热组件30上排出,此时升温速率稍慢,然后以10℃/min的升温速率升温至880℃,保温20min,相比第一阶段的升温速率,第二阶段的升温速率较高,从而提高了生产效率。在第二阶段的保温时间内,玻璃粉将ag和pd与硅藻土粘接,使得金属浆料与吸液件31的印刷面紧密结合。
151.实施例4
152.本实施例的吸液件31由55%预混料和45%成型助剂制得,其中,所述预混料包括50%硅藻土、20%玻璃粉以及30%造孔剂,所述成型助剂包括25%硬脂酸和75%石蜡制得,所述硅藻土的中值粒径为27.56μm,所述玻璃粉的中值粒径为5.24μm,所述造孔剂为聚甲基丙烯酸甲酯,所述造孔剂的球度为0.95,所述造孔剂的中值粒径为70μm。
153.本实施例的吸液件31的制备方法,包括以下步骤:
154.1)制备预混料:将本实施例的50%硅藻土、20%玻璃粉以及30%造孔剂采用滚筒球磨机搅拌混合均匀,混合时间为4h,得到预混料。
155.2)制备压铸料:先将75%石蜡和25%硬脂酸采用油温机加热至100℃,使石蜡和硬脂酸融化,采用搅拌机搅拌,并在搅拌过程中抽真空,真空度为-0.098mpa,搅拌时间为2小时,排出熔融状态下的石蜡和硬脂酸中的气泡,得到混合均匀的成型助剂,然后将步骤1)制得的预混料与上述混合均匀的成型助剂采用油温机加热至100℃,采用搅拌机搅拌,在搅拌过程中抽真空,真空度为-0.098mpa,搅拌时间为4小时,排出熔融状态下的预混料、石蜡以及硬脂酸中的气泡,得到压铸料;
156.3)制备陶瓷胚体:将步骤2)制备的压铸料加入rz-8型热压注浆机内,在压铸温度为75℃,压铸压力为0.7mpa下进行压铸成型,压铸时间为8s,得到陶瓷胚体;
157.4)脱胶处理:将步骤3)制备的陶瓷胚体进行第一阶段升温,以1.5℃/min的升温速率升温至50℃,保温10min;然后进行第二阶段升温,以1℃/min的升温速率升温至180℃,保温90min,然后停止加热,冷却。
158.5)制备吸液件31:将步骤4)得到的陶瓷胚体以4℃/min的升温速率升温至180℃,保温10min;再以1℃/min的升温速率升温至500℃,保温30min;再以10℃/min的升温速率升温至1080℃,保温130min,最后停止加热,自然冷却得到吸液件31。
159.本实施例的含有上述吸液件31的发热组件30的制作方法,包括以下步骤:将上述制备的吸液件31的其中一端面作为印刷面,对所述印刷面进行打磨处理,印刷面的打磨厚度为0.2mm,然后在所述印刷面上涂覆金属浆料,所述金属浆料包括:65%ag、20%pd以及15%粘结剂,粘接剂的型号b76,生产厂家为国药试剂,以3℃/min的升温速率升温至500℃,再将吸液件31以10℃/min的升温速率升温至880℃,保温20min,所述金属浆料形成发热件32,发热件32的厚度为40μm,得到发热组件30。
160.本实施例在所述吸液件31的印刷面上涂覆金属浆料后,以3℃/min的升温速率升温至500℃,使得粘结剂发生汽化并从发热组件30上排出,此时,为了粘结剂能够充分从发热组件30上排出,此时升温速率稍慢,然后以10℃/min的升温速率升温至880℃,保温20min,相比第一阶段的升温速率,第二阶段的升温速率较高,从而提高了生产效率。在第二阶段的保温时间内,玻璃粉将ag和pd与硅藻土粘接,使得金属浆料与吸液件31的印刷面紧密结合。
161.实施例5
162.本实施例的吸液件31由70%预混料和30%成型助剂制得,其中,所述预混料包括15%硅藻土、45%玻璃粉以及40%造孔剂,所述成型助剂包括35%硬脂酸和65%石蜡制得,所述硅藻土的中值粒径为35.0μm,所述玻璃粉的中值粒径为5.98μm,所述造孔剂为聚甲基丙烯酸甲酯,所述造孔剂的球度为0.95,所述造孔剂的中值粒径为50μm。
163.本实施例的吸液件31的制备方法,包括以下步骤:
164.1)制备预混料:将本实施例的15%硅藻土、45%玻璃粉以及40%造孔剂采用滚筒球磨机搅拌混合均匀,混合时间为4h,得到预混料。
165.2)制备压铸料:先将65%石蜡和35%硬脂酸采用油温机加热至100℃,使石蜡和硬脂酸融化,采用搅拌机搅拌,并在搅拌过程中抽真空,真空度为-0.098mpa,搅拌时间为1小时,排出熔融状态下的石蜡和硬脂酸中的气泡,得到混合均匀的成型助剂,然后将步骤1)制得的预混料与上述混合均匀的成型助剂采用油温机加热至100℃,采用搅拌机搅拌,在搅拌过程中抽真空,真空度为-0.098mpa,搅拌时间为4小时,排出熔融状态下的预混料、石蜡以及硬脂酸中的气泡,得到压铸料;
166.3)制备陶瓷胚体:将步骤2)制备的压铸料加入rz-8型热压注浆机内,在压铸温度为75℃,压铸压力为0.7mpa下进行压铸成型,压铸时间为10s,得到陶瓷胚体;
167.4)脱胶处理:将步骤3)制备的陶瓷胚体进行第一阶段升温,以1.2℃/min的升温速率升温至50℃,保温10min;然后进行第二阶段升温,以1℃/min的升温速率升温至220℃,保温90min,然后停止加热,冷却。
168.5)制备吸液件31:将步骤4)得到的陶瓷胚体以4℃/min的升温速率升温至220℃,保温20min;再以0.5℃/min的升温速率升温至500℃,保温30min;再以8℃/min的升温速率升温至970℃,保温90min,最后停止加热,自然冷却得到吸液件31。
169.本实施例的含有上述吸液件31的发热组件30的制作方法,包括以下步骤:将上述制备的吸液件31的其中一端面作为印刷面,对所述印刷面进行打磨处理,印刷面的打磨厚度为0.2mm,然后在所述印刷面上涂覆金属浆料,所述金属浆料包括:65%ag、20%pd以及15%粘结剂,粘接剂的型号b76,生产厂家为国药试剂,以3℃/min的升温速率升温至500℃,再将吸液件31以10℃/min的升温速率升温至880℃,保温20min,所述金属浆料形成发热件32,发热件32的厚度为40μm,得到发热组件30。
170.本实施例在所述吸液件31的印刷面上涂覆金属浆料后,以3℃/min的升温速率升温至500℃,使得粘结剂发生汽化并从发热组件30上排出,此时,为了粘结剂能够充分从发热组件30上排出,此时升温速率稍慢,然后以10℃/min的升温速率升温至880℃,保温20min,相比第一阶段的升温速率,第二阶段的升温速率较高,从而提高了生产效率。在第二阶段的保温时间内,玻璃粉将ag和pd与硅藻土粘接,使得金属浆料与吸液件31的印刷面紧密结合。
171.实验例
172.选取市面上购买的吸液件31作为对比例,将实验例1-实施例5制得的吸液件31与对比例中的吸液件31进行各项性能比较。
173.1、吸液件31的微观实验
174.预处理:将实施例1制备的吸液件31打磨处理后经过超声波清洗,然后烘干。
175.1)超景深显微镜实验
176.超景深显微镜具备了传统光学显微镜的景深和景深迭加技术,可以快速准确地对磨削表面的景深进行检测分析。本发明利用超景深显微镜(型号:leicadvm6)观察预处理后的实施例1制备的吸液件31表面,启动超景深显微镜,打开软件,将吸液件31放入载物台,调节超景深显微镜放大倍数,在软件中自动聚焦,保存照片,结果如图1和图2所示。其中,图1为超景深显微镜放大300倍观察吸液件31表面孔分布均匀,孔径大小接近一致;图2为超景深显微镜放大600倍观察吸液件31表面孔分布均匀,孔径大小接近一致。实验过程中还对实施例1制备的多孔陶瓷的三个不同区域进行测试,三个不同区域的孔分布均匀,孔径大小接近一致。
177.2)sem(扫描电子显微镜)测试
178.对预处理后的实施例1制得的吸液件31的表面进行sem测试,测试结果如图3和图4所示,图3为放大250倍的sem图,图4为放大500倍的sem图,由图3和图4可看出实施例1制得的吸液件31的孔分布均匀,孔径大小接近一致。
179.2、开放孔隙率的测定
180.所述开放孔隙率是指:材料的开口孔隙体积与材料在自然状态下总体积的百分比。
181.开放孔隙率的测试原理为:开放孔隙率=(m3-m1)/(m3-m2)*100%。其中m1为试样的干燥重量;m2为饱和试样在水中的重量;m3为饱和试样在空气中的重量。
182.开放孔隙率测试前吸液件31的取样条件为:样品经过超声清洗过,外观无污染、明显披锋以及裂痕等瑕疵。
183.开放孔隙率的测试过程为:称量吸液件31的干燥重量m1;吸液件31放入容器中,用去离子水完全浸没吸液件31,将容器放入抽真空装置中抽真空,抽真空至-100kpa后持续5min,在恢复常压后取出吸液件31;将吸液件31放入水中,称量吸液件31的饱和水重m2;将吸液件31中水中取出,用饱含水的吸液件将吸液件31表面多余的水分擦掉;称量吸液件31的饱和空重m3;计算开放孔隙率。上述抽真空设备采用vp225抽真空系统,称量质量采用赛多利斯entris124-1s分析天平,转移吸液件31时采用镊子。
184.测试环境条件为:室内温度在25
±
1℃,湿度在50-70rh%,具有排水设施,环境整洁无烟尘,周围没有机械振动源和电磁干扰源。
185.实施例1-5制得的吸液件31与对比例的吸液件31测试结果如表1所示,任一实施例与对比例均进行5次取样测试,计算实施例1-5与对比例的干燥空重的平均值、饱和水重的平均值以及饱和空重的平均值,进而计算得到实施例1-5与对比例的开放孔隙率的平均值。
186.表1.实施例1-5以及对比例的吸液件31的开放孔隙率测试结果
[0187][0188]
由表1可知,实施例1-5中制备的吸液件31的开放孔隙率范围为55~65%,由于开放孔隙率和吸液件31的强度之间存在相互制约关系,开放孔隙率越高,吸液件31的强度呈指数级降低,而同时吸液件31的开放孔隙率大小影响吸液件31的输油效率和供应烟油的均匀性,因此,本发明在保证吸液件31强度和输油效率的前提下,制得的吸液件31的开放孔隙率为55~65%之间,不仅保证输油效率,也保证了吸液件31的强度,而对比例的吸液件31的开放孔隙率较低,仅为53.25%。
[0189]
3、孔径和孔径分布测试
[0190]
利用压汞法测试实施例1制备的吸液件31的孔径和孔径分布。
[0191]
压汞法测试的原理是:利用汞对吸液件31表面不浸润的特性,用一定压力克服毛细管的阻力将汞压入吸液件31的孔洞结构中;对汞施加更高的压力,使汞进入孔径更小的孔洞结构;对汞施加的特定压力,对应汞能进入的孔洞结构的特定孔径,汞在特定压力下压入吸液件31的孔洞结构中的压入量包括:大于或者等于特定孔径的所有孔洞结构的孔体积。测试中,对汞施加的初始最小压力,初始最小压力对应初始最大孔径,测定的初始压入量包括:具有初始最大孔径的孔洞结构的孔体积。继续将对汞施加的压力提高至第一压力,第一压力对应第一孔径,测定的第一压入量包括:大于或者等于第一孔径的所有空洞结构的孔体积。第一压入量与初始压入量的差值,对应孔径范围在在初始最大孔径与第一孔径之间的孔洞结构的孔体积。逐步提高对汞施加的压力,可测得吸液件31中各孔径范围内孔洞结构的孔体积。直至压入量不再增加,此时的最大压入量包括:吸液件31中所有孔洞结构的孔体积。
[0192]
孔径分布测试结果如图5所示,从图5中看出,本发明实施例1制备的吸液件31大于80%的孔径集中在14.21~20.21μm之间,孔径大小分布较为均匀。而由上述实验方法测得对比例的吸液件3165%的孔径集中在20.35~27.25μm之间,孔径大小分布均匀性较差。
[0193]
4、导油速率测试
[0194]
导油速率即将预处理后的实施例1-5制备的吸液件31以及对比例的吸液件31放入盛有固定烟油量的专用器皿中,记录烟油从各个吸液件31下表面完全浸润整个吸液件31所需的时间。
[0195]
测试前吸液件31的预处理条件为:将实施例1-5以及对比例的吸液件31置于洁净的表面皿内,放入预先设置为120℃的电热鼓风干燥箱中,加热15min后取出,放置于干燥皿自然冷却至室温待测。
[0196]
测试环境的条件为:室内温度在25
±
1℃,湿度在40-70rh%,环境整洁无烟尘,周围没有机械振动源和电磁干扰源。
[0197]
导油速率的具体测试过程为:将专用器皿放入电子天平中去皮,向专用器皿注入摇匀的烟油;用镊子将预处理后的吸液件31放入盛有烟油的专用器皿正中间,吸液件31接触到烟油的同时按下秒表开始计时;观察烟油上升的情况,待烟油完全浸润吸液件31,按下秒表记录所需的时间。
[0198]
本发明的吸液件31应用在雾化器中,上述专用器皿为金属器皿,专用器皿统一规格为外径34.00
±
0.1mm,内径30.00
±
0.1mm,高度9.00
±
0.1mm,深度3.00
±
0.1mm;注入的烟油量为:1.3000
±
0.0050g;所用的镊子为塑料材质。可以理解地,吸液件31应用在其他领域时,专用器皿的尺寸以及注入烟油量随吸液件31尺寸的不同可有所调整。电子天平采用的是赛多利斯entris124-1s分析天平。
[0199]
由于吸液件31在不同的烟油中的导油速率不同,即吸液件31在不同的烟油中的导油时间不同,因此本发明的导油速率测试是测试实施例1-5的吸液件31以及对比例的吸液件31分别在三种烟油中的导油时间,三种烟油分别为含有70%质量分数植物甘油的烟油、含有60%质量分数植物甘油的烟油以及含有50%质量分数植物甘油的烟油,任一实施例与对比例的吸液件31均在同一种烟油中分别进行5次取样测试,计算实施例1-5与对比例的吸液件31在同一种烟油中的导液时间的平均值,再对实施例1-5的吸液件31分别在三种烟油中导油时间的平均值取平均得到平均导液时间,将实施例1-5平均导液时间与对比例导液时间的平均值作比较,测试结果如表2所示。
[0200]
表2.实施例以及对比例的导油时间的平均值测试结果
[0201]
[0202][0203]
由表2看出,实施例1-5制得的吸液件31在含有70%质量分数植物甘油的烟油中的平均导液时间为64s,对比例的吸液件31在含有70%质量分数植物甘油的烟油中导液时间的平均值为68s,实施例1-5制得的吸液件31的平均导油时间相比对比例的吸液件31导油时间的平均值提升了5.88%;实施例1-5制得的吸液件31在含有60%质量分数植物甘油的烟油中的平均导液时间为47s,对比例的吸液件31在含有60%质量分数植物甘油的烟油中导液时间的平均值为50s,实施例1-5制备的吸液件31的平均导油时间相比对比例的吸液件31导油时间的平均值提升了6.00%,实施例1-5制得的吸液件31在含有50%质量分数植物甘油的烟油中的平均导液时间为33s,对比例的吸液件31在含有50%质量分数植物甘油的烟油中导液时间的平均值为38s,实施例1-5制备的吸液件31的平均导油时间相比对比例的吸液件31导油时间的平均值提升了13.16%,即本发明制备的吸液件31的导油速率大于对比例的吸液件31的导油速率。
[0204]
5、强度测试
[0205]
分别取10pcs(片)实施例1制得的吸液件31以及10pcs(片)对比例的吸液件31进行强度测试,测试前取样条件是:样品表面无明显裂痕与缺料。
[0206]
吸液件31强度测试前的预处理条件为:将实施例1和对比例的吸液件31分别置于烘箱中以120℃烘干15min,然后置于干燥皿中自然冷却至室温待测。
[0207]
吸液件31强度的测试步骤为:用电子天平称量预处理后的吸液件31的磨前质量,将吸液件31装入装样瓶中,设定碰撞装置即滚筒球磨的参数,滚筒球磨的转速为200r/min,将装有吸液件31的装样瓶放置在滚筒球磨中进行碰撞,分别测试吸液件31在滚筒球磨的转动时间为0.5h和1h时吸液件31的掉粉量,用电子天平称量碰撞后的吸液件31的质量,计算吸液件31的掉粉量,通过掉粉量表征吸液件31的强度,掉粉量越多,吸液件31的强度越弱,掉粉量越少,吸液件31的强度越高。
[0208]
本次测试中,电子天平采用的是赛多利斯entris124-1s分析天平,用电子天平称量碰撞后的吸液件31的质量步骤之前,需要用气枪吹扫吸液件31,除去吸液件31表面的浮粉,提高测量精度。
[0209]
测试时环境的条件为:满足室内温度在25
±
1℃,湿度在40-70rh%,环境整洁无烟尘,周围没有机械振动源和电磁干扰源。
[0210]
强度测试结果如表3所示:
[0211]
表3.实施例1制得的吸液件31以及对比例的吸液件31的强度测试结果
[0212][0213]
由表3可以看出,对比例的吸液件31在滚筒球磨的转速为200r/min、转动时间分别为0.5h和1h的条件下的掉粉量均大于同等条件下实施例1制得的吸液件31的掉粉量,即在同等强度测试条件下,实施例1制得的吸液件31的强度大于对比例的吸液件31的强度,对比例的吸液件31和实施例1的吸液件31在同样的碰撞装置的转速下,碰撞装置的转动时间为1h时相比转动时间为0.5h的测试条件下,吸液件31的掉粉率在相同转速增量区间有上升的趋势。
[0214]
本发明提供的吸液件31通过选择合适比例的预混料与成型助剂混合,且吸液件31中大于80%的孔径集中在14.21~20.21μm之间,该吸液件31不仅具有较高导液速率,且吸液件31的强度较高。
[0215]
本发明提供的吸液件31的制备方法,通过选择合适比例的预混料和成型助剂混合制备压铸料,然后压铸、脱胶以及烧结制备吸液件31,制备的吸液件31的产品合格率较高,且制得的吸液件31的强度较高,孔径大小分布均匀,导油速率较高。
[0216]
本发明中选择球度为0.9~0.95的聚甲基丙烯酸甲酯作为造孔剂,造孔剂的粒径为15~70μm,烧结过程中造孔剂均匀且充分从陶瓷胚体中排出,形成陶瓷胚体的孔洞结构,孔径大小分布均匀。
[0217]
本发明中采用较低玻璃化温度和粘流温度的玻璃粉,使陶瓷胚体能够在较低的温度下烧结,玻璃粉起到低温粘结作用,既能提高强度,同时不会破坏造孔剂挥发所残留的通孔,使得本发明制备的吸液件31兼具较高的强度和较高的开放孔隙率。
[0218]
雾化器及气溶胶发生装置实施例一
[0219]
请参阅图6,本发明雾化器及气溶胶发生装置实施例一提供了一种气溶胶发生装置,该气溶胶发生装置包括雾化器100以及与雾化器100电性连接的电源装置(图未示出)。使用时,所述电源装置给雾化器100提供电能,雾化器100内的气溶胶形成基质在所述电源装置的电驱动作用下被加热雾化形成烟雾,烟雾在用户的抽吸作用下与外部大气混合后进入至用户口中,以供用户吸食。
[0220]
请参阅图7-图11,雾化器100包括雾化组件110,雾化组件110包括发热组件30,发热组件30包括吸液件31和发热件32,吸液件31由多孔材料制成,吸液件31包括上端面31a和雾化面31b,上端面31a和雾化面31b相对设置,吸液件31用于将气溶胶形成基质由上端面31a传导至雾化面31b上,发热件32设置在雾化面31b上,发热件32上待雾化气溶胶形成基质
量多的区域的电阻大于发热件32上待雾化气溶胶形成基质量少的区域的电阻。工作时,吸液件31将气溶胶形成基质传导至雾化面31b上,从而使得气溶胶形成基质在发热件32的加热作用下雾化形成烟雾,烟雾供用户吸食。
[0221]
本发明的发热组件30,当气溶胶形成基质由上端面31a传导至雾化面31b上并与发热件32接触时,发热件32上与较大量气溶胶形成基质接触的区域的电阻大,发热件32通电后该区域产生的热量相对较多,达到及时、充分雾化的目的,避免了气溶胶形成基质泄漏,同时,发热件32上与较少量气溶胶形成基质接触的区域的电阻小,发热件32通电后该区域产生的热量相对较少,避免了因发热量较大而发生干烧的情况。如此,发热件32上的各区域能够根据气溶胶形成基质量的多少适应性地产生热量以满足雾化需要,有效避免了漏液及干烧。
[0222]
在一个具体的实施方式中,吸液件31的上端面31a上凹陷有进液槽311,进液槽311用于接触气溶胶形成基质,气溶胶形成基质进入进液槽311进而被吸液件31吸收后传导至雾化面31b上。使用时,进入至进液槽311内的气溶胶形成基质经由进液槽311的槽底壁和进液槽311的槽侧壁同时向吸液件31的内部传导。由于设置进液槽311,减薄了吸液件31上对应进液槽311处的厚度,缩短了气溶胶形成基质对应进液槽311槽底壁处由上端面31a传导至雾化面31b的传导路径,因此,雾化面31b上对应进液槽311的部位导液效率高,单位时间内传导至该部位的气溶胶形成基质量较多。另外,吸液件31上除对应进液槽311以外的部位主要依靠进液槽311的槽侧壁向雾化面31b传导,气溶胶形成基质传导至雾化面31b的传导路径较长,因此,雾化面31b上错开进液槽311的部位导液效率低,单位时间内传导至该部位的气溶胶形成基质量较少。
[0223]
该过程中发热件32包括第一发热部321和第二发热部322,第一发热部321与进液槽311位置相对应,且第一发热部321的电阻大于第二发热部322的电阻。使用时,发热件32通电后,单位时间内,第一发热部321的发热量大于第二发热部322的发热量,由于第一发热部321与进液槽311位置相对应,发热量较大的第一发热部321满足了较大量气溶胶形成基质的雾化需求,避免了漏液,而发热量较小的第二发热部322满足了较少量气溶胶形成基质的雾化需求,从而有效避免了干烧。
[0224]
请参阅图8,在一个具体的实施方式中,进液槽311具有两个,两个进液槽311分别位于上端面31a相对的两侧,相应地,第一发热部321也具有两个,两个第一发热部321分别连接在第二发热部322相对的两侧,且一个第一发热部321与一个进液槽311位置相对应。通过设置两个进液槽311,使得气溶胶形成基质能够经由吸液件31的两侧同时被吸收,保证了吸液件31两侧雾化均匀。
[0225]
请参阅图10,具体地,第二发热部322大致呈椭圆形或圆形的环状结构,第一发热部321呈朝向第二发热部322折弯的条形结构,第一发热部321的一端与第二发热部322平滑过渡连接。第一发热部321折弯设置,增加了发热件32通电时第一发热部321产生热量的密度,有利于雾化面31b上与进液槽311位置对应部位的气溶胶形成基质被充分雾化。本实施方式中,两个第一发热部321关于第二发热部322呈中心对称设置。
[0226]
在一个具体的实施方式中,第一发热部321的宽度尺寸t1小于第二发热部322的宽度尺寸t2,根据电阻计算公式r=ρl/s,(ρ表示发热部的电阻率,l表示发热部的长度,s表示发热部的横截面积),可以得出,在ρ、l相同条件下,第一发热部321的电阻大于第二发热部
322的电阻,因此,第一发热部321产生的热量大于第二发热部322产生的热量。
[0227]
本实施方式中,第二发热部322呈椭圆形环状结构,第二发热部322沿长轴方向的最大尺寸t3为4.2mm,第二发热部322沿长轴方向的最小尺寸t4为3.4mm,因此,t2=0.4mm。
[0228]
另外,两个第一发热部321远离第二发热部322的一端均设置有接电部323,接电部323用于与所述电源装置的正、负极电性连接。使用时,所述电源装置的电流经由其中一个接电部323依次流经其中一个第一发热部321、第二发热部322以及另一个第一发热部321后流动至另一个接电部323,而后回到所述电源装置,该回路中,由于第二发热部322为环状结构,因此,第二发热部322可视为以并联的形式接入至两个第一发热部321之间,如此,第二发热部322产生的热量相对于第一发热部321进一步减少。
[0229]
另外,本实施方式中,接电部323为圆形结构,接电部323的半径为r2,r2=0.35mm。
[0230]
此外,本实施方式中带有并联结构的发热件32相较于传统的均匀发热件而言,发热件32上的第一发热部321的发热功率大于均匀发热件上任意部分的发热功率,因此,第一发热部321上的升温速率大于均匀发热件的升温速率。该结论推导过程如下:
[0231]
此处引入一市面上现有的均匀发热件,请参阅图12,该均匀发热件的接电部设置在两端,均匀发热件的材料、配比及厚度与本实施方式的发热件32均相同,不同点就在于二者的发热件32不同,可明显看出,均匀发热件的发热件32不存在并联结构,其为均匀线路。此处假设,发热功率均为p,发热件32和均匀发热件的发热件32长度均为l,二者发热件32的横截面积均为s,其中,发热件32的并联部分(即,第二发热部322)的发热件32长度为l1,发热件32的电流为i1,均匀发热件的电流为i1,得到,
[0232][0233]
即,
[0234][0235]
也即,
[0236][0237]
此时,发热件32上非并联部分(即,第一发热部321)发热件32的发热功率大于均匀发热件上与非并联部分同长度的发热件32的发热功率,即,
[0238][0239]
因此,发热件32上非并联部分发热功率密度大于均匀发热件上与非并联部分同长度的任意部分发热功率密度,从而使得发热件32上非并联部分的升温速率大于均匀发热件上与非并联部分同长度的任意部分的升温速率。
[0240]
针对以上结论,下面通过干烧温度测试和雾化温度测试分别进行验证。
[0241]
干烧温度测试部分:
[0242]
测试条件:空气环境中干烧;
[0243]
加热模式:加热3s后停止加热30s,循环20次;
[0244]
发热功率:7.5w(发热件32的电阻为1.83ω,均匀发热件的电阻为0.63ω);
[0245]
温度测试:红外热像仪测温,实时数据采集频率0.04s,其中,红外热像仪的型号为flir-a655sc高性能热像仪;
[0246]
雾化面处理:喷涂黑体漆。
[0247]
测试方法:同时对发热件32上的五个固定点测温,将同一时间点的五个检测点(五个检测点均在发热件32上的主要发热部位,对于发热件32而言,检测点不设置在第二发热部322和接电部323,对于均匀发热件而言,检测点不设置在两侧的接电部323)的温度与热成像画面中的最高温度计算温度平均值,时间点与对应的温度平均值作为一个数据点。记录20次循环的数据,然后将20次循环的数据合并压缩成一个循环,得到附图13中干烧温度测试时间-温度曲线图。根据该时间-温度曲线图,得出下表4:
[0248]
表4:各时间段内发热件32升温速率及发热件32升温表
[0249][0250]
(干烧温度特征:升温速率的偏差范围
±
5℃/s)
[0251]
由表4可知,发热件32相较于均匀发热件而言,发热件32在0-0.5s及0.5-1s这两个时间段内,其上非并联部分的升温速率大于均匀发热件,尤其是在刚开始通电加热的0-0.5s内,升温速率明显提升。
[0252]
雾化温度测试部分:
[0253]
测试条件:吸液件加入气溶胶形成基质,导液充分;
[0254]
加热模式:加热3s后停止加热30s,循环20次;
[0255]
抽吸模式:7.5w(发热件32的电阻为1.76ω,均匀发热件的电阻为0.55ω);
[0256]
温度测试:红外热像仪测温,实时数据采集频率0.04s,其中,红外热像仪的型号为flir-a655sc高性能热像仪;
[0257]
气溶胶形成基质类型:标准烟油,类似50%vg50%pg。
[0258]
测试方法:与上述干烧温度测试部分中的测试方法相同,此处不再赘述。
[0259]
由以上测试得到附图14中雾化温度测试时间-温度曲线图。
[0260]
根据该时间-温度曲线图,得出下表5:
[0261]
表5:各时间段内发热件32升温速率及发热件32升温表
[0262][0263]
(雾化温度特征:升温速率的偏差范围
±
5℃/s)
[0264]
由表5可知,发热件32相较于均匀发热件而言,发热件32在0-0.64s及0.64-1s这两个时间段内,其上非并联部分的升温速率大于均匀发热件,尤其是在刚开始通电加热的0-0.64s内,升温速率明显提升。
[0265]
综上,发热件32在工作时,非并联部分的升温速率较快,能够及时、充分雾化较大量气溶胶形成基质,防止气溶胶形成基质泄露。
[0266]
请再次参阅图8-图11,本发明的吸液件31的上端面31a上凹陷形成有凹槽312,第二发热部322与凹槽312位置相对应。通过设置凹槽312,减薄了吸液件31对应凹槽312位置处的厚度,在吸液件31材料的比热容相同的前提下,凹槽312对应位置的热容量较少,进而提高了凹槽312对应位置的升温速率,从而提高了雾化面31b上对应第二发热部322位置处的雾化效率。另外,凹槽312减薄了吸液件31局部位置的厚度,减少了吸液件31整体的热容量,进而使得在发热件32通电时吸液件31能够快速升温,保证了及时雾化。本实施方式中,两个进液槽311对称设置在凹槽312的相对两侧。
[0267]
在一个具体的实施方式中,进液槽311与凹槽312隔开设置,接电部323与进液槽311及凹槽312之间未减薄的区域位置相对应,接电部323用于供电极柱抵接,以实现电性连接作用,由于接电部323与进液槽311及凹槽312均错开设置,当电极柱抵接在接电部323上时,吸液件31上对应接电部323的部位不会因厚度减薄而带来强度不足以至于折断的风险。
[0268]
另外,吸液件31内设置有过气通道313,具体地,过气通道313的一端贯通凹槽312的槽底壁,过气通道313的另一端贯通雾化面31b,第二发热部322环设在过气通道313的外周,如此,弥补了吸液件31因开设过气通道313而损失的强度。用户抽吸操作时,气溶胶形成基质雾化形成的烟雾在用户的抽吸作用下,由过气通道313贯通雾化面31b的一端流入,通过过气通道313及凹槽312后由吸液件31的上端面31a流出,最终进入至用户口中。本实施方式中,凹槽312的横截面呈腰圆形,过气通道313的横截面呈椭圆形。
[0269]
上端面31a和雾化面31b相互平行,本实施方式中规定,以雾化面31b朝向上端面31a的方向定义为吸液件31的第一方向,吸液件31上沿所述第一方向任意横向截取平面的外轮廓形状为圆形、椭圆或多边形等,此处不作限定。
[0270]
进液槽311与凹槽312均凹设在上端面31a上,吸液件31上沿吸液件31的第一方向由雾化面31b延伸至上端面31a的距离为吸液件31的高度h(单位:mm),凹槽312沿所述第一方向的深度为h(单位:mm),其中,0.3≤h/h≤0.5,在保证吸液件31本身强度的基础上,提高了导液效率。本实施方式中,h=2mm,h=1mm。
[0271]
请再次参阅图3,在一个具体的实施方式中,吸液件31还包括连接在上端面31a和
雾化面31b之间的连接面31c,连接面31c包括第一端面31d、第二端面31e、第三端面31f和第四端面31g,其中,第一端面31d和第三端面31f对称设置,第二端面31e和第四端面31g对称设置。本实施方式中,第一端面31d和第三端面31f均为平面且相互平行,第二端面31e和第四端面31g均为外倾的弧面。其中一个进液槽311靠近第一端面31d设置,另外一个进液槽311靠近第三端面31f设置,且两个进液槽311的中心线均位于第二端面31e与第四端面31g之间的对称平面上,如此,保证了吸液件31上对应第一端面31d和第三端面31f的两端的传导速率一致或趋于一致,有利于吸液件31各处气溶胶形成基质传导的均匀性。凹槽312及过气通道313的轴线均与吸液件31沿第一方向的中轴线共线,且凹槽312的横截面积大于过气通道313的横截面积。
[0272]
另外,请参阅图9、图10,进液槽311的半径为r,第一端面31d到与其靠近的进液槽311的中心轴的距离为c1,第一端面31d到吸液件31的中心轴的距离为c2,第一端面31d到第三端面31f的距离为c3,第二端面31e到第四端面31g的最大距离为k1,凹槽312沿长度方向的尺寸为c4,凹槽312沿宽度方向的尺寸为k2,过气通道313的长轴为a,过气通道313的短轴为b。本实施方式中,r=0.75mm,c1=1.5mm,c2=5.7mm,c3=11.4mm,k1=4.1mm,c4=4mm,k2=2.5mm,a=2.4mm,b=1.8mm。另外,接电部323的圆心到与之靠近的第三端面31f的距离t5=2.7mm,第一发热部321到与之靠近的第三端面31f的距离t6=1.2mm。
[0273]
本实施方式中,吸液件31由多孔陶瓷制成,多孔陶瓷相对于纤维棉材料具有耐高温性,可有效防止吸液件31被烧焦,提升了用户的吸烟口感。可以理解地,吸液件31还可以是多孔石墨或泡沫金属等。发热件32呈扁平状结构,发热件32可以是发热涂层、发热件32或发热片等,其中,发热涂层可以通过厚膜工艺或者薄膜工艺涂覆于雾化面31b上;发热件32可以通过激光活化快速金属化工艺形成在雾化面31b上;发热片可以通过其他辅助安装结构安装在雾化面31b上,所述辅助安装结构包括但不限于螺钉、螺栓、卡扣结构等,另外,发热片还可以以嵌件形式嵌入至雾化面31b上。
[0274]
请再次参阅图6、图7,雾化组件110还包括雾化支架21、雾化底座22和雾化腔221,雾化支架21和雾化底座22配合连接,雾化腔221形成于雾化支架21和雾化底座22之间,发热组件30设置在雾化支架21和雾化底座22之间,发热组件30加热气溶胶形成基质生成的烟雾充斥于雾化腔221内。
[0275]
雾化底座22大致呈上端具有开口的中空筒状结构,发热组件30安装在雾化底座22的上端内,雾化底座22内位于发热组件30下方的空间构成雾化腔221,雾化面31b的发热件32靠近雾化腔221设置,雾化腔221与过气通道313连通。使用时,雾化面31b上雾化形成的烟雾充斥于雾化腔221内。另外,雾化底座22的底部开设有进气口222,进气口222与雾化腔221及外部大气均连通,进气口222用于供外部气体在抽吸作用下进入至雾化腔221内。本实施方式中,进气口222具有两个,两个进气口222对称设置在雾化底座22的两侧。为了提升密封性,雾化底座22的内侧壁与发热组件30的吸液件31的外侧壁之间架设有密封件23,密封件23由硅胶或橡胶等密封材料制成。
[0276]
雾化支架21安装在雾化底座22的开口端,雾化支架21上开设有进液口211,进液口211与进液槽311对应连通,使用时,气溶胶形成基质通过进液口211流经进液槽311内,从而被吸液件31吸收。雾化支架21上还开设有出气槽212,出气槽212与凹槽312对应连通,在一个具体的实施方式中,出气槽212为锥形槽,其中,出气槽212的大口端与凹槽312对应连通。
当用户进行抽吸操作时,雾化腔221内的烟雾首先快速通过截面较小的过气通道313,由于凹槽312的横截面积大于过气通道313的横截面积,通过过气通道313进入至凹槽312内的气流速度降低,而后通过出气槽212的斜面时流速平稳增加,使得进入至用户口中的气流平缓,提升了使用体验。
[0277]
另外,雾化支架21上位于进液口211及出气槽212之间部分的底部抵持在上端面31a上,且与接电部323位置相对应。雾化组件110还包括电极柱24,电极柱24安装在雾化底座22的下端,电极柱24具有两个,一个电极柱24与一个接电部323的位置相对应,当发热组件30安装到位后,电极柱24的一端与对应的接电部323相抵持。如此,吸液件31的边缘位置同时受到电极柱24顶部的挤压力以及雾化支架21底部的抵持力,吸液件31受到的挤压力和抵持力相互平衡,其合力为零,从而避免了扭矩施加在吸液件31上,进而避免了吸液件31发生变形甚至断裂。
[0278]
雾化器100还包括储液件10,储液件10内设置有相互隔离的储液腔101和出气通道102,储液腔101用于储存气溶胶形成基质,出气通道102用于供烟雾流入至用户口中。雾化组件110安装在储液件10的一端,储液腔101与进液槽311连通,出气通道102相对雾化腔221设于发热组件30的另一侧,且出气通道102的进气端与过气通道313连通。雾化器100还包括进气管25,进气管25的进气端与外部大气连通,进气管25的出气端延伸至出气通道102的进气端。
[0279]
用户抽吸操作时,一路气流经由进气口222进入至雾化腔221内并与烟雾混合,温度较高的烟气混合体经由过气通道313进入至出气通道102内,同时,另一路气流经由进气管25的进气端穿过进气管25后由进气管25的出气端流出,进而进入至出气通道102内,该路气体进入出气通道102内时的温度相较于由过气通道313进入出气通道102的气体温度低。上述两路气流在出气通道102的进气端混合,温度较高的烟雾与由进气管25流出的温度较低的空气混合,使得烟雾充分冷凝,最终经由出气通道102的出气端流出的烟雾颗粒较大,提高了烟雾的湿度,进而提升了吸烟口感。另外,由于外部大气对烟雾具有降温作用,保证了进入至用户口中的气流温度不会过高,避免了烫伤用户的情况发生。
[0280]
在一个具体的实施方式中,进气管25设置在雾化底座22上,进气管25为直管,出气通道102为笔直通道,进气管25的中轴线与出气通道102的中轴线共线,且进气管25通过过气通道313穿过发热组件30的吸液件31,进气管25的外管径尺寸小于过气通道313的横截面尺寸,使得过气通道313的通道壁与进气管25的外壁之间形成一间隙(图未标出)。进气管25的进气端与雾化底座22的底部连接,雾化底座22的底部还开设有与外部气体连通的进气孔223,进气管25与进气孔223对应连通。使用时,雾化腔221内的烟雾通过所述间隙后流动至出气通道102的进气端,同时,外部气体在抽吸作用下经由进气管25流动至出气通道102的进气端。上述过程中,由于进气管25的中轴线与出气通道102的中轴线共线,使得穿过进气管25的气体进入至出气通道102的过程中气阻减小,从而降低了用户抽吸烟雾时受到的阻力,方便用户使用。
[0281]
本实施方式中,进气管25的设置方式为竖置,可以理解地,在其他未示出的实施方式中,进气管25还可以横置,例如,进气管25由雾化底座22的侧壁伸入至发热组件30的上方且进气管25的出气端位于出气通道102的进气端位置,进气管25的进气端与外部大气连通,另外,进气管25可以是由硬质材料(例如,不锈钢、铜等)制成,还可以由软质材料制成(例
如,橡胶或硅胶)。如此,对于进气管25的设置方式及其材料不作限定,只需使得进气管25的进气端与外部大气连通,进气管25的出气端延伸至出气通道102的进气端即可。
[0282]
另外,本实施方式中,雾化腔221设置在发热组件30的下方,使用时,雾化腔221内的烟雾穿过发热组件30后才可进入至出气通道102内。可以理解地,在其他实施方式中,类似于棉花包裹发热丝的发热组件而言,其上雾化腔221设置在发热组件内部,此时,烟雾形成于发热组件30的内部,烟雾不需要经由发热组件的底部便可直接流动至出气通道102内,对于此类结构的发热组件而言,同样可以通过设置进气管25,将外部大气导入至出气通道102的进气端并与烟雾混合,以达到提高冷凝效果的作用。至于进气管25,可以由发热组件的底部穿过发热组件,也可以不穿过发热组件,只需使得雾化腔221与出气通道102的进气端连通,进气管25的进气端与外部大气连通,进气管25的出气端延伸至出气通道102的进气端即可。
[0283]
在一个具体的实施方式中,储液件10包括外壳11和收容于外壳11内的通气管12,储液腔101由外壳11的内腔形成,出气通道102由通气管12的内腔形成,雾化组件110安装在外壳11的下端内,通气管12的上端与外壳11的顶部连接,通气管12的下端与雾化支架21连接,且出气通道102与出气槽212的小口端连通。可以理解地,外壳11和通气管12还可以一体成型。
[0284]
雾化组件110与储液件10安装时,雾化底座22及雾化支架21均收容于外壳11的下端内,为了提升密封性,防止储液腔101内的气溶胶形成基质泄漏,雾化支架21与外壳11及通气管12之间安装有密封套26,密封套26可以由硅胶或橡胶等密封材料制成。
[0285]
储液件10还包括烟嘴13,烟嘴13套设在外壳11上端的外部,烟嘴13上开设有出烟口131,出烟口131与出气通道102的出气端连通,出烟口131供用户抽吸操作。
[0286]
所述电源装置安装在储液件10靠近雾化组件110的一端,所述电源装置包括电池,所述电池的正、负极分别与两个电极柱24电性连接,从而实现所述电池向发热组件30供电的作用。
[0287]
本发明雾化器及气溶胶发生装置实施例一提供的雾化器100,设置在雾化面31b上的发热件32上待雾化气溶胶形成基质量多的区域的电阻大于发热件32上待雾化气溶胶形成基质量少的区域的电阻,使得发热件32上的各区域能够根据气溶胶形成基质的多少适应性地产生适量热量以满足雾化需要,有效避免了漏液及干烧,同时,由多孔材料制成的吸液件31具有较高的耐高温性,可有效防止吸液件31被烧焦,提升了用户的吸烟口感。另外,通过设置进气管25,使进气管25的出气端延伸至出气通道102的进气端,使得温度较高的烟雾和温度较低的外部气体于出气通道102的进气端混合,使得烟雾充分冷凝形成较大烟雾颗粒,冷凝效果好,进一步提升了吸烟口感,用户使用体验提升。
[0288]
本发明雾化器及气溶胶发生装置实施例一提供的气溶胶发生装置,因其具有上述雾化器100全部的技术特征,故具有与上述雾化器100相同的技术效果。
[0289]
雾化器及气溶胶发生装置实施例二
[0290]
请参阅图15-图18,本发明雾化器及气溶胶发生装置实施例二提供了一种雾化器,该雾化器与雾化器及气溶胶发生装置实施例一的雾化器100的区别就在于,发热组件30的结构不同。
[0291]
具体地,雾化器及气溶胶发生装置实施例一中,进液槽311沿所述第一方向任意横
向截取平面的外轮廓形状为圆形,而本实施例中,进液槽311沿所述第一方向任意横向截取平面的外轮廓形状为“凹”形结构,两个所述“凹”形结构的凹陷部位相对设置,且“凹”形结构的凹陷部位呈圆弧形,该圆弧形的半径为r3,该圆弧形的圆心到与之靠近的第三端面31f之间的距离为t7,进液槽311到与之靠近的第三端面31f之间的距离为t8,本实施方式中,r3=0.8mm,t7=2.7mm,t8=0.6mm。
[0292]
本雾化器及气溶胶发生装置实施例二中,进液槽311的横向截面呈“凹”形结构,相较于雾化器及气溶胶发生装置实施例一的圆形结构而言,截面呈“凹”形结构的进液槽311的侧壁面积相对增加,如此,当气溶胶形成基质进入至进液槽311内,气溶胶形成基质向雾化面31b传导的面积得以增加,如此,单位时间内向雾化面31b传导的气溶胶形成基质量相对较多,提高了导液效率。
[0293]
为了适应进液槽311的形状,本雾化器及气溶胶发生装置实施例二中,发热件32的尺寸也作出相应调整,具体地,接电部323的半径r2=0.45mm,接电部323的圆心到与之靠近的第三端面31f的距离t5=2.7mm,第一发热部321到与之靠近的第三端面31f的距离t6=1.2mm,如此可见,第一发热部321与进液槽311位置相对应,从而使得发热量较大的第一发热部321满足了较大量气溶胶形成基质的雾化需求,避免了漏液,而发热量较小的第二发热部322满足了较少量气溶胶形成基质的雾化需求,从而有效避免了干烧。另外,t5=t7=2.7mm,使得接电部323的圆心与进液槽311的“凹”形结构的凹陷部位的圆弧中心于所述第一方向上相对应,使得当电极柱抵接在接电部323上时,吸液件31上对应接电部323的部位不会因厚度减薄而带来强度不足以至于折断的风险。
[0294]
另外,本实施例中,密封件23的顶部向下延伸形成插接部231,插接部231紧密插入至吸液件31的凹槽312内,如此,增加了密封件23与吸液件31之间的密封性,防止气溶胶形成基质进入至凹槽312内。
[0295]
需要说明的是,本雾化器及气溶胶发生装置实施例二的雾化器中未作阐述的结构与雾化器及气溶胶发生装置实施例一相同,此处不再赘述。
[0296]
本雾化器及气溶胶发生装置实施例二还提供了一种带有上述雾化器的气溶胶发生装置,因其具有上述雾化器全部的技术特征,故具有与上述雾化器相同的技术效果。
[0297]
以上述依据本发明的理想实施例为启示,通过上述的说明内容,相关的工作人员完全可以在不偏离本发明的范围内,进行多样的变更以及修改。本发明的技术范围并不局限于说明书上的内容,必须要根据权利要求范围来确定其技术范围。