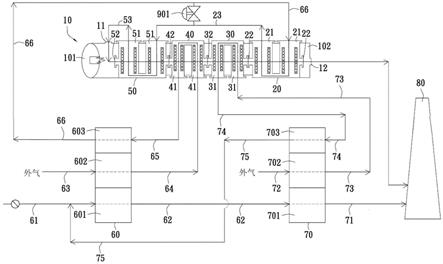
1.本发明涉及一种节能型双转轮高浓度冷侧旁通过温控制系统及其方法,尤其涉及一种当挥发性有机化合物(vocs)浓度变高时,具有调节热回收量或浓度的功能,使有机废气在处理时,能防止直燃式焚烧炉(to)不会因炉温太高而发生过热的现象,甚至导致停机的情况发生,而适用于半导体产业、光电产业或化学相关产业的有机废气处理系统或类似设备。
背景技术:
2.目前在半导体产业或光电产业的制造生产过程中都会产生具有挥发性有机气体(voc),因此,在各厂区都会安装处理挥发性有机气体(voc)的处理设备,以避免挥发性有机气体(voc)直接排入空气中而造成空气污染。而目前通过该处理设备所脱附的浓缩气体大都是输送到该焚烧炉来进行燃烧,再将燃烧后的气体来输送到烟囱来进行排放。
3.但是近年来,不管是中央政府或是各地方政府都对空气污染非常重视,也因此在烟囱的排放标准上制定了有关大气品质标准,同时将依国际管制趋势发展,逐期检讨。
4.因此,本发明人鉴于上述问题,希望提出一种具有提升有机废气处理效率的节能型双转轮高浓度冷侧旁通过温控制系统及其方法,令使用者可轻易操作组装,提供使用者便利性。
技术实现要素:
5.本发明的主要目的,在于提供一种节能型双转轮高浓度冷侧旁通过温控制系统及其方法,主要用于有机废气处理系统,且设有一直燃式焚烧炉(to),一第一热交换器、一第二热交换器、一第三热交换器、第四热交换器、一第一冷侧输送管路、一第四冷侧输送管路、一第一吸附转轮、一第二吸附转轮及一烟囱,并通过在该第一脱附浓缩气体管路与该第一冷侧输送管路之间、该第一脱附浓缩气体管路与该第四冷侧输送管路之间、该第一冷侧输送管路与该第四冷侧输送管路之间或是于该第一脱附浓缩气体管路上增设一冷侧比例风门,由此,当挥发性有机化合物(vocs)浓度变高时,能通过该冷侧比例风门来调控风量的大小,以具有调节热回收量或浓度的功能,使有机废气在处理时,能防止直燃式焚烧炉(to)不会因炉温太高而发生过温的现象,甚至导致停机的情形发生,进而增加整体的实用性。
6.可选地,一直燃式焚烧炉,该直燃式焚烧炉设有一炉头及一炉膛,该炉头与该炉膛相通,该直燃式焚烧炉系设有入口及出口,该入口设于该炉头处,该出口设于该炉膛处;一第一热交换器,该第一热交换器设于该直燃式焚烧炉的炉膛内,该第一热交换器设有第一冷侧管路及第一热侧管路;一第二热交换器,该第二热交换器设于该直燃式焚烧炉的炉膛内,该第二热交换器设有第二冷侧管路及第二热侧管路;一第三热交换器,该第三热交换器设于该直燃式焚烧炉的炉膛内,该第三热交换器设有第三冷侧管路及第三热侧管路;一第四热交换器,该第四热交换器设于该直燃式焚烧炉的炉膛内,该第四热交换器设有第四冷侧管路及第四热侧管路。
7.可选地,一第一冷侧输送管路,该第一冷侧输送管路的一端与该第一冷侧管路的另一端连接,该第一冷侧输送管路的另一端与该第四冷侧管路的一端连接;一第四冷侧输送管路,该第四冷侧输送管路的一端与该第四冷侧管路的另一端连接,该第四冷侧输送管路的另一端与该直燃式焚烧炉的入口连接。
8.本发明的另一目的,在于提供一种节能型双转轮高浓度冷侧旁通过温控制系统及其方法,通过在该第一脱附浓缩气体管路与该第一冷侧输送管路之间、该第一脱附浓缩气体管路与该第四冷侧输送管路之间或是该第一冷侧输送管路与该第四冷侧输送管路之间所增设的冷侧比例风门,以当该第一冷侧输送管路内或是该第四冷侧输送管路内的挥发性有机化合物(vocs)浓度变高时,能通过该冷侧比例风门来将该第一脱附浓缩气体管路内的部分脱附浓缩气体输送到该第一冷侧输送管路内或是该第四冷侧输送管路内,使该第一冷侧输送管路内的脱附浓缩气体或是该第四冷侧输送管路内的脱附浓缩气体能与该第一脱附浓缩气体管路内的部分脱附浓缩气体再一次的混合,使温度较低的该第一脱附浓缩气体管路内的部分脱附浓缩气体能让温度较高的该第一冷侧输送管路内的脱附浓缩气体或是该第四冷侧输送管路内的脱附浓缩气体进行降温,由此,以具有调节热回收量或浓度的功能,使有机废气在处理时,能防止直燃式焚烧炉(to)不会因炉温太高而发生过热的现象,甚至导致停机的情况发生,进而增加整体的实用性。
9.本发明的另一目的,在于提供一种节能型双转轮高浓度冷侧旁通过温控制系统及其方法,通过在该第一脱附浓缩气体管路上增设一冷侧比例风门,而该冷侧比例风门的另一端供外气进入,其中该外气可为新鲜空气或是其他气体,以当由该第一吸附转轮的脱附区所产生的脱附浓缩气体在进入该第一脱附浓缩气体管路后,且该第一脱附浓缩气体管路内的温度变得较高或是浓度变得较高时,可通过该冷侧比例风门的另一端所输入外气来进行调节,使该第一脱附浓缩气体管路内的脱附浓缩气体能达到降温的效果或是浓度降低的效果,进而增加整体的操作性。
10.可选地,一第一吸附转轮,该第一吸附转轮设有吸附区、冷却区及脱附区,该第一吸附转轮连接有一废气进气管路、一第一净气排放管路、一第一冷却气进气管路、一第一冷却气输送管路、一第一热气输送管路及一第一脱附浓缩气体管路,该废气进气管路的一端连接至该第一吸附转轮的吸附区的一侧,该第一净气排放管路的一端与该第一吸附转轮的吸附区的另一侧连接,该第一冷却气进气管路的一端与该第一吸附转轮的冷却区的一侧连接,该第一冷却气输送管路的一端与该第一吸附转轮的冷却区的另一侧连接,该第一冷却气输送管路的另一端与该第三热交换器的第三冷侧管路的一端连接,该第一热气输送管路的一端与该第一吸附转轮的脱附区的另一侧连接,该第一热气输送管路的另一端与该第三热交换器的第三冷侧管路的另一端连接,该第一脱附浓缩气体管路的一端与该第一吸附转轮的脱附区的一侧连接,该第一脱附浓缩气体管路的另一端与该第一热交换器的第一冷侧管路的一端连接。
11.可选地,一第二吸附转轮,该第二吸附转轮设有吸附区、冷却区及脱附区,该第二吸附转轮连接有一第二净气排放管路、一第二冷却气进气管路、一第二冷却气输送管路、一第二热气输送管路及一第二脱附浓缩气体管路,该第一净气排放管路的一端连接至该第二吸附转轮的吸附区的一侧,该第二净气排放管路的一端与该第二吸附转轮的吸附区的另一侧连接,该第二冷却气进气管路的一端与该第二吸附转轮的冷却区的一侧连接,该第二冷
却气输送管路的一端与该第二吸附转轮的冷却区的另一侧连接,该第二冷却气输送管路的另一端与该第二热交换器的第二冷侧管路的一端连接,该第二热气输送管路的一端与该第二吸附转轮的脱附区的另一侧连接,该第二热气输送管路的另一端与该第二热交换器的第二冷侧管路的另一端连接,该第二脱附浓缩气体管路的一端与该第二吸附转轮的脱附区的一侧连接。
12.可选地,一烟囱,该第二净气排放管路的另一端与该烟囱连接。该直燃式焚烧炉的出口连接至该烟囱;该第一冷却气进气管路为供新鲜空气或是外气来进入;该第二冷却气进气管路为供新鲜空气或是外气来进入。
13.可选地,该废气进气管路还设有一废气连通管路,该废气连通管路与该第一冷却气进气管路连接,该废气连通管路还设有一废气连通控制阀门,以控制该废气连通管路的风量;该第一净气排放管路还设有一第一净气连通管路,该第一净气连通管路系与该第二冷却气进气管路连接,该第一净气连通管路还设有一第一净气连通控制阀门,以控制该第一净气连通管路的风量。
14.可选地,该第二脱附浓缩气体管路还设有一风机;该第二净气排放管路还设有一风机;该第一脱附浓缩气体管路还设有一风机。该第二脱附浓缩气体管路的另一端与该废气进气管路相连接;该第二脱附浓缩气体管路的另一端与该第一冷却气进气管路相连接。
15.可选地,在该第一脱附浓缩气体管路与该第一冷侧输送管路之间设一冷侧比例风门,以通过该冷侧比例风门来调控该第一脱附浓缩气体管路与该第一冷侧输送管路的风量;在该第一脱附浓缩气体管路与该第四冷侧输送管路之间设一冷侧比例风门,以通过该冷侧比例风门来调控该第一脱附浓缩气体管路与该第四冷侧输送管路的风量;在该第一冷侧输送管路与该第四冷侧输送管路之间设一冷侧比例风门,以通过该冷侧比例风门来调控该第一冷侧输送管路与该第四冷侧输送管路的风量。在该第一脱附浓缩气体管路上设有一冷侧比例风门,而该冷侧比例风门的另一端供外气进入,以通过该冷侧比例风门来调控该第一脱附浓缩气体管路的风量。为了能够更进一步了解本发明的特征、特点和技术内容,请参考以下有关本发明的详细说明与附图,所附图示仅提供参考与说明用,并非用来限制本发明。
附图说明
16.图1为本发明的第一种实施例具有冷侧比例风门的系统架构示意图。
17.图2为本发明的第二种实施例具有冷侧比例风门的系统架构示意图。
18.图3为本发明的第三种实施例具有冷侧比例风门的系统架构示意图。
19.图4为本发明的第四种实施例具有冷侧比例风门的系统架构示意图。
20.图5为本发明的第一种实施例的主要步骤流程图。
21.图6为本发明的第二种实施例的主要步骤流程图。
22.图7为本发明的第三种实施例的主要步骤流程图。
23.图8为本发明的第四种实施例的主要步骤流程图。
24.符号说明
25.10、直燃式焚烧炉(to)
ꢀꢀꢀꢀꢀꢀꢀꢀꢀ
101、炉头
26.102、炉膛
ꢀꢀꢀꢀꢀꢀꢀꢀꢀꢀꢀꢀꢀꢀꢀꢀꢀꢀꢀꢀ
11、入口
27.12、出口
ꢀꢀꢀꢀꢀꢀꢀꢀꢀꢀꢀꢀꢀꢀꢀꢀꢀꢀꢀꢀꢀ
20、第一热交换器
28.21、第一冷侧管路
ꢀꢀꢀꢀꢀꢀꢀꢀꢀꢀꢀꢀꢀ
22、第一热侧管路
29.23、第一冷侧输送管路
ꢀꢀꢀꢀꢀꢀꢀꢀꢀ
30、第二热交换器
30.31、第二冷侧管路
ꢀꢀꢀꢀꢀꢀꢀꢀꢀꢀꢀꢀꢀ
32、第二热侧管路
31.40、第三热交换器
ꢀꢀꢀꢀꢀꢀꢀꢀꢀꢀꢀꢀꢀ
41、第三冷侧管路
32.42、第三热侧管路
ꢀꢀꢀꢀꢀꢀꢀꢀꢀꢀꢀꢀꢀ
50、第四热交换器
33.51、第四冷侧管路
ꢀꢀꢀꢀꢀꢀꢀꢀꢀꢀꢀꢀꢀ
52、第四热侧管路
34.53、第四冷侧输送管路
ꢀꢀꢀꢀꢀꢀꢀꢀꢀ
60、第一吸附转轮
35.601、吸附区
ꢀꢀꢀꢀꢀꢀꢀꢀꢀꢀꢀꢀꢀꢀꢀꢀꢀꢀ
602、冷却区
36.603、脱附区
ꢀꢀꢀꢀꢀꢀꢀꢀꢀꢀꢀꢀꢀꢀꢀꢀꢀꢀ
61、废气进气管路
37.611、废气连通管路
ꢀꢀꢀꢀꢀꢀꢀꢀꢀꢀꢀꢀ
6111、废气连通控制阀门
38.62、第一净气排放管路
ꢀꢀꢀꢀꢀꢀꢀꢀꢀ
621、第一净气连通管路
39.6211、第一净气连通控制阀门
ꢀꢀꢀ
63、第一冷却气进气管路
40.64、第一冷却气输送管路
ꢀꢀꢀꢀꢀꢀꢀ
65、第一热气输送管路
41.66、第一脱附浓缩气体管路
ꢀꢀꢀꢀꢀ
661、风机
42.70、第二吸附转轮
ꢀꢀꢀꢀꢀꢀꢀꢀꢀꢀꢀꢀꢀ
701、吸附区
43.702、冷却区
ꢀꢀꢀꢀꢀꢀꢀꢀꢀꢀꢀꢀꢀꢀꢀꢀꢀꢀ
703、脱附区
44.71、第二净气排放管路
ꢀꢀꢀꢀꢀꢀꢀꢀꢀ
711、风机
45.72、第二冷却气进气管路
ꢀꢀꢀꢀꢀꢀꢀ
73、第二冷却气输送管路
46.74、第二热气输送管路
ꢀꢀꢀꢀꢀꢀꢀꢀꢀ
75、第二脱附浓缩气体管路
47.751、风机
ꢀꢀꢀꢀꢀꢀꢀꢀꢀꢀꢀꢀꢀꢀꢀꢀꢀꢀꢀꢀ
80、烟囱
48.901、冷侧比例风门
ꢀꢀꢀꢀꢀꢀꢀꢀꢀꢀꢀꢀ
902、冷侧比例风门
49.903、冷侧比例风门
ꢀꢀꢀꢀꢀꢀꢀꢀꢀꢀꢀꢀ
904、冷侧比例风门
50.s100、输入待吸附的气体
ꢀꢀꢀꢀꢀꢀꢀ
s200、输入待吸附的气体
51.s110、第一吸附转轮吸附
ꢀꢀꢀꢀꢀꢀꢀ
s210、第一吸附转轮吸附
52.s120、输入第一冷却气体
ꢀꢀꢀꢀꢀꢀꢀ
s220、输入第一冷却气体
53.s130、输送第一热气脱附
ꢀꢀꢀꢀꢀꢀꢀ
s230、输送第一热气脱附
54.s140、脱附浓缩气体输送
ꢀꢀꢀꢀꢀꢀꢀ
s240、脱附浓缩气体输送
55.s150、焚烧后的气体输送
ꢀꢀꢀꢀꢀꢀꢀ
s250、焚烧后的气体输送
56.s160、第二吸附转轮吸附
ꢀꢀꢀꢀꢀꢀꢀ
s260、第二吸附转轮吸附
57.s170、输入第二冷却气体
ꢀꢀꢀꢀꢀꢀꢀ
s270、输入第二冷却气体
58.s180、输送第二热气脱附
ꢀꢀꢀꢀꢀꢀꢀ
s280、输送第二热气脱附
59.s190、冷侧比例风门调控
ꢀꢀꢀꢀꢀꢀꢀ
s290、冷侧比例风门调控
60.s300、输入待吸附的气体
ꢀꢀꢀꢀꢀꢀꢀ
s400、输入待吸附的气体
61.s310、第一吸附转轮吸附
ꢀꢀꢀꢀꢀꢀꢀ
s410、第一吸附转轮吸附
62.s320、输入第一冷却气体
ꢀꢀꢀꢀꢀꢀꢀ
s420、输入第一冷却气体
63.s330、输送第一热气脱附
ꢀꢀꢀꢀꢀꢀꢀ
s430、输送第一热气脱附
64.s340、脱附浓缩气体输送
ꢀꢀꢀꢀꢀꢀꢀ
s440、脱附浓缩气体输送
65.s350、焚烧后的气体输送
ꢀꢀꢀꢀꢀꢀꢀ
s450、焚烧后的气体输送
66.s360、第二吸附转轮吸附
ꢀꢀꢀꢀꢀꢀꢀ
s460、第二吸附转轮吸附
67.s370、输入第二冷却气体
ꢀꢀꢀꢀꢀꢀꢀ
s470、输入第二冷却气体
68.s380、输送第二热气脱附
ꢀꢀꢀꢀꢀꢀꢀ
s480、输送第二热气脱附
69.s390、冷侧比例风门调控
ꢀꢀꢀꢀꢀꢀꢀ
s490、冷侧比例风门调控
具体实施方式
70.图1~8,是本发明实施例的示意图,而本发明的节能型双转轮高浓度冷侧旁通过温控制系统及其方法的最佳实施方式运用于半导体产业、光电产业或化学相关产业的挥发有机废气处理系统或类似设备,主要是挥发性有机化合物(vocs)浓度变高时,能具有调节热回收量或浓度的功能,使有机废气在处理时,能防止直燃式焚烧炉(to)不会因炉温太高而发生过热的现象,甚至导致停机的情况发生。
71.而本发明的节能型双转轮高浓度冷侧旁通过温控制系统,主要包括有一直燃式焚烧炉(to)10、一第一热交换器20、一第二热交换器30、一第三热交换器40、一第四热交换器50、一第一冷侧输送管路23、一第四冷侧输送管路53、一第一吸附转轮60、一第二吸附转轮70及一烟囱80的组合设计(如图1至图4所示),其中该第一热交换器20设有第一冷侧管路21及第一热侧管路22,该第二热交换器30设有第二冷侧管路31及第二热侧管路32,该第三热交换器40设有第三冷侧管路41及第三热侧管路42,该第四热交换器50设有第四冷侧管路51及第四热侧管路52。另该直燃式焚烧炉(to)10设有一炉头101及一炉膛102,该炉头101与该炉膛102相通,且该第一热交换器20、第二热交换器30、第三热交换器40及第四热交换器50分别设于该直燃式焚烧炉(to)10的炉膛102内,而该直燃式焚烧炉(to)10设有入口11及出口12(如图1至图4所示),且该入口11设于该炉头101处,并该入口11与该第四热交换器50的第四冷侧管路51的另一端连接,再者,该出口12则设于该炉膛102处,而该出口12连接至该烟囱80,由此,使该有机废气能由该入口11来进入该炉头101内进行燃烧,再让经过燃烧后的气体能穿过该炉膛102并由该出口12来排出至烟囱80处进行排放,以具有节省能源的功能。
72.而上述的直燃式焚烧炉(to)10的炉头101能将经过焚烧的高温气体先输送到该第四热交换器50的第四热侧管路52的一侧以进行热交换,且由该第四热交换器50的第四热侧管路52的另一侧来将经过焚烧的高温气体再输送到该第三热交换器40的第三热侧管路42的一侧以进行热交换,再由该第三热交换器40的第三热侧管路42的另一侧来将经过焚烧的高温气体再输送到该第二热交换器30的第二热侧管路32的一侧以进行热交换,的后再由该第二热交换器30的第二热侧管路32的另一侧来将经过焚烧的高温气体再输送到该第一热交换器20的第一热侧管路22的一侧以进行热交换,最后由该第一热交换器20的第一热侧管路22的另一侧来输送到该炉膛102的出口12(如图1至图4所示),再由该炉膛102的出口12来输送到烟囱80,以通过该烟囱80来进行排放。
73.本发明的第一吸附转轮60设有吸附区601、冷却区602及脱附区603,该第一吸附转轮60连接有一废气进气管路61、一第一净气排放管路62、一第一冷却气进气管路63、一第一冷却气输送管路64、一第一热气输送管路65及一第一脱附浓缩气体管路66,(如图1至图4所示)而该第二吸附转轮70设有吸附区701、冷却区702及脱附区703,该第二吸附转轮70连接有一第二净气排放管路71、一第二冷却气进气管路72、一第二冷却气输送管路73、一第二热
气输送管路74及一第二脱附浓缩气体管路75。其中该第一吸附转轮60与该第二吸附转轮70分别为沸石浓缩转轮或是其他材质的浓缩转轮。
74.其中该废气进气管路61的一端连接至该第一吸附转轮60的吸附区601的一侧,使该废气进气管路61能将有机废气输送到该第一吸附转轮60的吸附区601的一侧,而该第一净气排放管路62的一端与该第一吸附转轮60的吸附区601的另一侧连接,且该第一净气排放管路62的一端连接至该第二吸附转轮70的吸附区701的一侧,以让该有机废气能经该第一吸附转轮60的吸附区601进行吸附有机物后再由该第一净气排放管路62来输送到该第二吸附转轮70的吸附区701内(如图1至图4所示)。该第二吸附转轮70的吸附区701的另一侧连接该设第二净气排放管路71,以通过该第二净气排放管路71的另一端来与该烟囱80连接,且该第二净气排放管路71设有一风机711(如图3及图4所示),使能通过该风机711来将该第二净气排管路71内的经过吸附后的气体推拉到该烟囱80内来进行排放。
75.该第一吸附转轮60的冷却区602的一侧连接该第一冷却气进气管路63,以供气体进入该第一吸附转轮60的冷却区602来进行冷却使用(如图1至图4所示),而该第一吸附转轮60的冷却区602的另一侧连接该第一冷却气输送管路64的一端,该第一冷却气输送管路64的另一端则与该第三热交换器40的第三冷侧管路41的一端连接,以将进入该第一吸附转轮60的冷却区602后的气体输送到该第三热交换器40内进行热交换(如图1至图4所示),再者,该第一热气输送管路65的一端与该第一吸附转轮60的脱附区603的另一侧连接,且该第一热气输送管路65的另一端与该第三热交换器40的第三冷侧管路41的另一端连接,以能将通过该第三热交换器40进行热交换的高温热气通过该第一热气输送管路65来输送到该第一吸附转轮60的脱附区603来进行脱附使用。
76.而上述该第一吸附转轮60的冷却区602设有两种实施方式,其中第一种实施方式为该第一吸附转轮60的冷却区602的一侧所连接的第一冷却气进气管路63是供新鲜空气或外气进入(如图1所示),通过该新鲜空气或外气来提供该第一吸附转轮60的冷却区602降温用。第二种实施方式该废气进气管路61设有一废气连通管路611,而该废气连通管路611的另一端与该第一冷却气进气管路63连接(如图3所示),以能通过该废气连通管路611来将该废气进气管路61内的废气输送到该第一吸附转轮60的冷却区602以进行降温使用,该废气连通管路611设有一废气连通控制阀门6111,以控制该废气连通管路611的风量。
77.该第二吸附转轮70的冷却区702的一侧连接该第二冷却气进气管路72,以供气体进入该第二吸附转轮70的冷却区702来进行冷却使用(如图1至图4所示),而该第二吸附转轮70的冷却区702的另一侧连接该第二冷却气输送管路73的一端,该第二冷却气输送管路73的另一端则与该第二热交换器30的第二冷侧管路31的一端连接,以将进入该第二吸附转轮70的冷却区702后的气体输送到该第二热交换器30内进行热交换(如图1至图4所示),再者,该第二热气输送管路74的一端与该第二吸附转轮70的脱附区703的另一侧连接,且该第二热气输送管路74的另一端与该第二热交换器30的第二冷侧管路31的另一端连接,以能将通过该第二热交换器30进行热交换的高温热气通过该第二热气输送管路74来输送到该第二吸附转轮70的脱附区703来进行脱附使用。
78.而上述该第二吸附转轮70的冷却区702设有两种实施方式,其中第一种实施方式为该第二吸附转轮70的冷却区702的一侧所连接的第二冷却气进气管路72是供新鲜空气或外气进入(如图1所示),通过该新鲜空气或外气来提供该第二吸附转轮70的冷却区702降温
用。第二种实施方式该第一净气排放管路62设有一第一净气连通管路621,而该第一净气连通管路621的另一端与该第二冷却气进气管路72连接(如图3及图4所示),以能通过该第一净气连通管路621来将该第一净气排放管路62内的气体输送到该第二吸附转轮70的冷却区702以进行降温使用,另该第一净气连通管路621设有一第一净气连通控制阀门6211,以控制该第一净气连通管路621的风量。
79.该第一脱附浓缩气体管路66的一端与该第一吸附转轮60的脱附区603的一侧连接,而该第一脱附浓缩气体管路66的另一端与该第一热交换器20的第一冷侧管路21的一端连接,其中该第一热交换器20的第一冷侧管路21的另一端与该第一冷侧输送管路23的一端连接,而该第一冷侧输送管路23的另一端则与该第四热交换器50的第四冷侧管路51的一端连接(如图1至图4所示)。再者,该第四热交换器50的第四冷侧管路51的另一端与该第四冷侧输送管路53的一端连接,而该第四冷侧输送管路53的另一端则与该直燃式焚烧炉(to)10的入口11连接,以能将经过高温所脱附下来的脱附浓缩气体能通过该第一脱附浓缩气体管路66来输送到该第一热交换器20的第一冷侧管路21的一端内,且由该第一热交换器20的第一冷侧管路21的另一端来输送到该第一冷侧输送管路23的一端内,并由该第一冷侧输送管路23的另一端来输送到该第四热交换器50的第四冷侧管路51的一端内,再由该第四热交换器50的第四冷侧管路51的另一端来输送到该第四冷侧输送管路53的一端内,最后由该第四冷侧输送管路53的另一端来输送到该直燃式焚烧炉(to)10的入口11内(如图1至图4所示),使能让该直燃式焚烧炉(to)10的炉头101来进行高温裂解,以能减少挥发性有机化合物。该第一脱附浓缩气体管路66设有一风机661,以能将脱附浓缩气体来推拉进入该第一热交换器20的第一冷侧管路21的一端内。
80.该第二脱附浓缩气体管路75的一端与该第二吸附转轮70的脱附区703的一侧连接,其中该第二脱附浓缩气体管路75的另一端有两种实施方式,而第一种实施方式乃是该第二脱附浓缩气体管路75的另一端与该废气进气管路61相连接(如图1及图3所示),使该浓缩气体能再通过该废气进气管路61来进入该第一吸附转轮60的吸附区601内,以进行再次吸附。第二种实施方式是该第二脱附浓缩气体管路75的另一端与该第一冷却气进气管路63相连接(如图2及图4所示),使该浓缩气体能再通过该第一冷却气进气管路63来进入该第一吸附转轮60的冷却区602内,以供进行冷却使用。再者,该第二脱附浓缩气体管路75设有一风机751(如图3及图4所示),以能将脱附浓缩气体来推拉进入该废气进气管路61或该第一冷却气进气管路63内。使通过第二吸附转轮70的脱附区703所产生的脱附气体能进入该第一吸附转轮60的吸附区601或是该第一吸附转轮60的冷却区602来进行循环利用,以使有机废气的处理效率能提升。
81.再者,本发明的节能型双转轮高浓度冷侧旁通过温控制系统,主要是有四种的实施例,而该四种的实施例中的直燃式焚烧炉(to)10、第一热交换器20、第二热交换器30、第三热交换器40、第四热交换器50、第一冷侧输送管路23、第四冷侧输送管路53、第一吸附转轮60、第二吸附转轮70及烟囱80是采相同的设计,因此,上述的直燃式焚烧炉(to)10、第一热交换器20、第二热交换器30、第三热交换器40、第四热交换器50、第一冷侧输送管路23、第四冷侧输送管路53、第一吸附转轮60、第二吸附转轮70及烟囱80内容不再重复,请参考上述的说明内容。
82.其中第一种实施例(如图1所示)的差异乃为在该第一脱附浓缩气体管路66与该第
一冷侧输送管路23之间增设一冷侧比例风门901,而该冷侧比例风门901的一端与该第一脱附浓缩气体管66路连接,且该冷侧比例风门901的另一端与该第一冷侧输送管路23连接,以通过该冷侧比例风门901来调控该第一脱附浓缩气体管路66与该第一冷侧输送管路23的风量,因此,当该第一冷侧输送管路23内的挥发性有机化合物(vocs)浓度变高时,能通过该冷侧比例风门901来将该第一脱附浓缩气体管路66内的部分脱附浓缩气体输送到该第一冷侧输送管路23内,使该第一冷侧输送管路23内的脱附浓缩气体能与该第一脱附浓缩气体管路66内的部分脱附浓缩气体再一次的混合,使温度较低的该第一脱附浓缩气体管路66内的部分脱附浓缩气体能让温度较高的该第一冷侧输送管路23内的脱附浓缩气体进行降温,由此,当挥发性有机化合物(vocs)浓度变高时,能通过该冷侧比例风门901来调控风量的大小,以具有调节热回收量或浓度的功能,使有机废气在处理时,能防止直燃式焚烧炉(to)10不会因炉温太高而发生过温的现象,甚至导致停机的情形发生。
83.第二种实施例(如图2所示)的差异为在该第一脱附浓缩气体管路66与该第四冷侧输送管路53之间增设一冷侧比例风门902,而该冷侧比例风门902的一端与该第一脱附浓缩气体管路66连接,且该冷侧比例风门902的另一端与该第四冷侧输送管路53连接,以通过该冷侧比例风门902来调控该第一脱附浓缩气体管路66与该第四冷侧输送管路53的风量,因此,当该第四冷侧输送管路53内的挥发性有机化合物(vocs)浓度变高时,能通过该冷侧比例风门902来将该第一脱附浓缩气体管路66内的部分脱附浓缩气体输送到该第四冷侧输送管路53内,使该第四冷侧输送管路53内的脱附浓缩气体能与该第一脱附浓缩气体管路66内的部分脱附浓缩气体再一次的混合,使温度较低的该第一脱附浓缩气体管路66内的部分脱附浓缩气体能让温度较高的该第四冷侧输送管路53内的脱附浓缩气体进行降温,由此,当挥发性有机化合物(vocs)浓度变高时,能通过该冷侧比例风门902来调控风量的大小,以具有调节热回收量或浓度的效能,使有机废气在处理时,能防止直燃式焚烧炉(to)10不会因炉温太高而发生过温的现象,甚至导致停机的情况发生。
84.第三种实施例(如图3所示)的差异为在该第一冷侧输送管路23与该第四冷侧输送管路53之间增设一冷侧比例风门903,而该冷侧比例风门903的一端与该第一冷侧输送管路23路连接,且该冷侧比例风门903的另一端与该第四冷侧输送管路53连接,以通过该冷侧比例风门903来调控该第一冷侧输送管路23与该第四冷侧输送管路53的风量,因此,当该第四冷侧输送管路53内的挥发性有机化合物(vocs)浓度变高时,能通过该冷侧比例风门903来将该第一冷侧输送管路903内的部分脱附浓缩气体输送该第四冷侧输送管路53内,使该第一冷侧输送管路23内的脱附浓缩气体能与该第四冷侧输送管路53内的脱附浓缩气体再一次的混合,使温度较低的该第一冷侧输送管路23内的脱附浓缩气体能让温度较高的该第四冷侧输送管路53内的脱附浓缩气体进行降温,由此,当挥发性有机化合物(vocs)浓度变高时,能通过该冷侧比例风门903来调控风量的大小,以具有调节热回收量或浓度的效能,使有机废气在处理时,能防止直燃式焚烧炉(to)10不会因炉温太高而发生过温的现象,甚至导致停机的情形发生。
85.第四种实施例(如图4所示)的差异是于该第一脱附浓缩气体管路66上增设一冷侧比例风门904,而该冷侧比例风门904的另一端供外气进入,其中该外气可为新鲜空气或是其他气体,以通过该冷侧比例风门904来调控该第一脱附浓缩气体管路66的风量。因此,当由该第一吸附转轮60的脱附区603所产生的脱附浓缩气体在进入该第一脱附浓缩气体管路
66后,且该第一脱附浓缩气体管路66内的温度变得较高或是浓度变得较高时,可通过该冷侧比例风门904的另一端所输入外气来进行调节,使该第一脱附浓缩气体管路66内的脱附浓缩气体能达到降温的效果或是浓度降低的效果。
86.而本发明的节能型双转轮高浓度冷侧旁通过温控制方法,其主要用于有机废气处理系统,且包括有一直燃式焚烧炉(to)10、一第一热交换器20、一第二热交换器30、一第三热交换器40、一第四热交换器50、第一冷侧输送管路23、第四冷侧输送管路53、一第一吸附转轮60、一第二吸附转轮70及一烟囱80的组合设计(如图1至图4所示),其中该第一热交换器20设有第一冷侧管路21及第一热侧管路22,该第二热交换器30设有第二冷侧管路31及第二热侧管路32,该第三热交换器40设有第三冷侧管路41及第三热侧管路42,该第四热交换器50设有第四冷侧管路51及第四热侧管路52,其中该第一冷侧输送管路23的一端与该第一冷侧管路21的另一端连接,该第一冷侧输送管路23的另一端与该第四冷侧管路51的一端连接,该第四冷侧输送管路53的一端与该第四冷侧管路51的另一端连接,该第四冷侧输送管路53的另一端与该直燃式焚烧炉(to)10的入口11连接。该直燃式焚烧炉(to)10设有一炉头101及一炉膛102,该炉头101与该炉膛102相通,且该第一热交换器20、第二热交换器30、第三热交换器40及第四热交换器50分别设于该直燃式焚烧炉(to)10的炉膛102内,而该直燃式焚烧炉(to)10设有入口11及出口12(如图1至图4所示),且该入口11设于该炉头101处,并该入口11与该第四热交换器50的第四冷侧管路51的另一端连接,再者,该出口12则设于该炉膛102处,而该出口12连接至该烟囱80,由此,使该有机废气能由该入口11来进入该炉头101内进行燃烧,再让经过燃烧后的气体能穿过该炉膛102并由该出口12来排出至烟囱80处进行排放,以具有节省能源的功能。
87.而上述的直燃式焚烧炉(to)10的炉头101能将经过焚烧的高温气体先输送到该第四热交换器50的第四热侧管路52的一侧以进行热交换,且由该第四热交换器50的第四热侧管路52的另一侧来将经过焚烧的高温气体再输送到该第三热交换器40的第三热侧管路42的一侧以进行热交换,再由该第三热交换器40的第三热侧管路42的另一侧来将经过焚烧的高温气体再输送到该第二热交换器30的第二热侧管路32的一侧以进行热交换,的后再由该第二热交换器30的第二热侧管路32的另一侧来将经过焚烧的高温气体再输送到该第一热交换器20的第一热侧管路22的一侧以进行热交换,最后由该第一热交换器20的第一热侧管路22的另一侧来输送到该炉膛102的出口12(如图1至图4所示),再由该炉膛102的出口12来输送到烟囱80,以通过该烟囱80来进行排放。
88.本发明的第一吸附转轮60设有吸附区601、冷却区602及脱附区603,该第一吸附转轮60连接有一废气进气管路61、一第一净气排放管路62、一第一冷却气进气管路63、一第一冷却气输送管路64、一第一热气输送管路65及一第一脱附浓缩气体管路66(如图1至图4所示),而该第二吸附转轮70设有吸附区701、冷却区702及脱附区703,该第二吸附转轮70连接有一第二净气排放管路71、一第二冷却气进气管路72、一第二冷却气输送管路73、一第二热气输送管路74及一第二脱附浓缩气体管路75(如图1至图4所示)。其中该第一吸附转轮60与该第二吸附转轮70分别为沸石浓缩转轮或是其他材质的浓缩转轮。
89.而该控制方法的主要步骤(如图5所示)包括:步骤s100输入待吸附的气体:将废气通过该废气进气管路61的另一端来送入该第一吸附转轮60的吸附区601的一侧。而完成上述步骤s100后即进行下一步骤s110。
90.另,下一步进行的步骤s110第一吸附转轮吸附:通过该第一吸附转轮60的吸附区601进行吸附后,由该第一吸附转轮60的吸附区601的另一侧将吸附后的气体通过该第一净气排放管路62的另一端来输出至第二吸附转轮70的吸附区701。而完成上述步骤s110后即进行下一步骤s120。
91.其中上述的步骤s110中的第二吸附转轮70的吸附区701的另一侧所连接该第二净气排放管路71,以通过该第二净气排放管路71的另一端来与该烟囱80连接,且该第二净气排放管路71设有一风机711(如图3及图4所示),使能通过该风机711来将该第二净气排管路71内的经过吸附后的气体推拉到该烟囱80内以进行排放。
92.下一步进行的步骤s120输入第一冷却气体:通过该第一冷却气进气管路63的另一端来输送冷却气至该第一吸附转轮60的冷却区602进行冷却,再通过该第一冷却气输送管路64的另一端来将经过该第一吸附转轮60的冷却区602的冷却气输送到该第三热交换器40的第三冷侧管路41的一端。而完成上述步骤s120后即进行下一步骤s130。
93.其中上述的步骤s120中的第一吸附转轮60的冷却区602设有两种实施方式,其中第一种实施方式为该第一吸附转轮60的冷却区602的一侧所连接的第一冷却气进气管路63乃是供新鲜空气或外气进入(如图1所示),通过该新鲜空气或外气来提供该第一吸附转轮60的冷却区602降温用。第二种实施方式该废气进气管路61设有一废气连通管路611,而该废气连通管路611的另一端与该第一冷却气进气管路63连接(如图3所示),以能通过该废气连通管路611来将该废气进气管路61内的废气输送到该第一吸附转轮60的冷却区602以进行降温使用,该废气连通管路611设有一废气连通控制阀门6111,以控制该废气连通管路611的风量。
94.下一步进行的步骤s130输送第一热气脱附:通过与第三热交换器40的第三冷侧管路41的另一端所连接的第一热气输送管路65来将热气输送到该第一吸附转轮60的脱附区603进行脱附,再通过该第一脱附浓缩气体管路66的另一端来将脱附浓缩气体输送到第一热交换器20的第一冷侧管路21的一端。而完成上述步骤s130后即进行下一步骤s140。
95.其中上述的步骤s130中的第一脱附浓缩气体管路66设有一风机661(如图3及图4所示),以能将脱附浓缩气体来推拉进入该第一热交换器20的第一冷侧管路21内。
96.下一步进行的步骤s140脱附浓缩气体输送:该脱附浓缩气体再通过该第一热交换器20的第一冷侧管路21的另一端所连接的第一冷侧输送管路23来输送到该第四热交换器50的第四冷侧管路51的一端,且再通过该第四热交换器50的第四冷侧管路51的另一端所连接的第四冷侧输送管路53来输送到该直燃式焚烧炉(to)10的入口11。而完成上述步骤s140后即进行下一步骤s150。
97.下一步进行的步骤s150焚烧后的气体输送:将该直燃式焚烧炉(to)10的炉头101所燃烧后而产生的焚烧后的气体输送到该第四热交换器50的第四热侧管路52的一端,且由该第四热交换器50的第四热侧管路52的另一端输送到该第三热交换器40的第三热侧管路42的一端,而由该第三热交换器40的第三热侧管路42的另一端输送到该第二热交换器30的第二热侧管路32的一端,再由该第二热交换器30的第二热侧管路32的另一端输送到该第一热交换器20的第一热侧管路22的一端,最后由该第一热交换器20的第一热侧管路22的另一端输送到该直燃式焚烧炉(to)10的出口12。而完成上述步骤s150后即进行下一步骤s160。
98.下一步进行的步骤s160第二吸附转轮吸附:将第一净气排放管路62内的吸附后的
气体输送到第二吸附转轮70的吸附区701的一侧进行吸附,再将第二次吸附后的气体通过该第二净气排放管路71来输送至烟囱80排放。而完成上述步骤s160后即进行下一步骤s170。
99.下一步进行的步骤s170输入第二冷却气体:通过该第二冷却气进气管路72的另一端来输送冷却气至该第二吸附转轮70的冷却区702进行冷却,再通过该第二冷却气输送管路73的另一端来将经过该第二吸附转轮70的冷却区702的冷却气输送到该第二热交换器30的第二冷侧管路31的一端。而完成上述步骤s170后即进行下一步骤s180。
100.其中上述的步骤s170中的第二吸附转轮70的冷却区702设有两种实施方式,其中第一种实施方式为该第二吸附转轮70的冷却区702的一侧所连接的第二冷却气进气管路72是供新鲜空气或外气进入(如图1所示),通过该新鲜空气或外气来提供该第二吸附转轮70的冷却区702降温用。第二种实施方式该第一净气排放管路62设有一第一净气连通管路621,而该第一净气连通管路621的另一端与该第二冷却气进气管路72连接(如图3及图4所示),以能通过该第一净气连通管路621来将该第一净气排放管路62内的气体输送到该第二吸附转轮70的冷却区702以进行降温使用,该第一净气连通管路621设有一第一净气连通控制阀门6211,以控制该第一净气连通管路621的风量。
101.下一步进行的步骤s180输送第二热气脱附:通过与第二热交换器30的第二冷侧管路31的另一端所连接的第二热气输送管路74来将热气输送到该第二吸附转轮70的脱附区703进行脱附,再通过该第二脱附浓缩气体管路75的另一端来输出。而完成上述步骤s180后即进行下一步骤s190。
102.其中上述的步骤s180中的该第二脱附浓缩气体管路75的另一端有两种实施方式,而第一种实施方式是该第二脱附浓缩气体管路75的另一端与该废气进气管路61相连接(如图1及图3所示),使该浓缩气体能再通过该废气进气管路61来进入该第一吸附转轮60的吸附区601内,以进行再次吸附。第二种实施方式是该第二脱附浓缩气体管路75的另一端与该第一冷却气进气管路63相连接(如图2及图4所示),使该浓缩气体能再通过该第一冷却气进气管路63来进入该第一吸附转轮60的冷却区602内,以供进行冷却使用。此外,该第二脱附浓缩气体管路75设有一风机751,能将脱附浓缩气体来推拉进入该废气进气管路61或该第一冷却气进气管路63内。使通过第二吸附转轮70的脱附区703所产生的脱附气体能进入该第一吸附转轮60的吸附区601或是该第一吸附转轮60的冷却区602来进行循环利用,以使有机废气的处理效率能提升。
103.下一步进行的步骤s190冷侧比例风门调控:在该第一脱附浓缩气体管路66与该第一冷侧输送管路23之间设一冷侧比例风门901,以通过该冷侧比例风门901来调控该第一脱附浓缩气体管路66与该第一冷侧输送管路23的风量。
104.其中上述步骤s190中该冷侧比例风门901的一端与该第一脱附浓缩气体管66路连接,且该冷侧比例风门901的另一端与该第一冷侧输送管路23连接(如图1所示),以通过该冷侧比例风门901来调控该第一脱附浓缩气体管路66与该第一冷侧输送管路23的风量,因此,当该第一冷侧输送管路23内的挥发性有机化合物(vocs)浓度变高时,能通过该冷侧比例风门901来将该第一脱附浓缩气体管路66内的部分脱附浓缩气体输送到该第一冷侧输送管路23内,使该第一冷侧输送管路23内的脱附浓缩气体能与该第一脱附浓缩气体管路66内的部分脱附浓缩气体再一次的混合,使温度较低的该第一脱附浓缩气体管路66内的部分脱
附浓缩气体能让温度较高的该第一冷侧输送管路23内的脱附浓缩气体进行降温,由此,当挥发性有机化合物(vocs)浓度变高时,能通过该冷侧比例风门901来调控风量的大小,以具有调节热回收量或浓度的功能,使有机废气在处理时,能防止直燃式焚烧炉(to)10不会因炉温太高而发生过温的现象,甚至导致停机的情况发生。
105.此外,本发明的节能型双转轮高浓度冷侧旁通过温控制方法,主要是有四种的实施例,而第一种实施例(如图5所示)的步骤s100输入待吸附的气体、步骤s110第一吸附转轮吸附、s120输入第一冷却气体、步骤s130输送第一热气脱附、步骤s140脱附浓缩气体输送、步骤s150焚烧后的气体输送、步骤s160第二吸附转轮吸附、步骤s170输入第二冷却气体、步骤s180输送第二热气脱附及步骤s190冷侧比例风门调控,已于上述提出说明,请参考上述的说明内容。
106.第二种实施例(如图6所示)中的步骤s200输入待吸附的气体、步骤s210第一吸附转轮吸附、s220输入第一冷却气体、步骤s230输送第一热气脱附、步骤s240脱附浓缩气体输送、步骤s250焚烧后的气体输送、步骤s260第二吸附转轮吸附、步骤s270输入第二冷却气体及步骤s280输送第二热气脱附,与第三种实施例(如图7所示)中的步骤s300输入待吸附的气体、步骤s310第一吸附转轮吸附、s320输入第一冷却气体、步骤s330输送第一热气脱附、步骤s340脱附浓缩气体输送、步骤s350焚烧后的气体输送、步骤s360第二吸附转轮吸附、步骤s370输入第二冷却气体及步骤s380输送第二热气脱附,第四实施例(如图8所示)中的步骤s400输入待吸附的气体、步骤s410第一吸附转轮吸附、s420输入第一冷却气体、步骤s430输送第一热气脱附、步骤s440脱附浓缩气体输送、步骤s450焚烧后的气体输送、步骤s460第二吸附转轮吸附、步骤s470输入第二冷却气体及步骤s480输送第二热气脱附,都是采用与第一种实施例(如图1所示)中的步骤s100输入待吸附的气体、步骤s110第一吸附转轮吸附、s120输入第一冷却气体、步骤s130输送第一热气脱附、步骤s140脱附浓缩气体输送、步骤s150焚烧后的气体输送、步骤s160第二吸附转轮吸附、步骤s170输入第二冷却气体、步骤s180输送第二热气脱附的相同的设计,差异仅在于步骤s190冷侧比例风门调控的内容。
107.因此,上述与步骤s100输入待吸附的气体、步骤s110第一吸附转轮吸附、s120输入第一冷却气体、步骤s130输送第一热气脱附、步骤s140脱附浓缩气体输送、步骤s150焚烧后的气体输送、步骤s160第二吸附转轮吸附、步骤s170输入第二冷却气体、步骤s180输送第二热气脱附的相同的内容不再重复,请参考上述的说明内容。下列将针对第二种实施例(如图6所示)中的步骤s290冷侧比例风门调控、第三种实施例(如图7所示)中的步骤s390冷侧比例风门调控及第四种实施例(如图8所示)中的步骤s490冷侧比例风门调控来进行说明。
108.而第二种实施例(如图6所示)的差异为步骤s290冷侧比例风门调控:在该第一脱附浓缩气体管路66与该第四冷侧输送管路53之间设一冷侧比例风门902,来通过该冷侧比例风门902来调控该第一脱附浓缩气体管路66与该第四冷侧输送管路53的风量。
109.其中上述步骤s290中该冷侧比例风门902的一端与该第一脱附浓缩气体管66路连接,且该冷侧比例风门902的另一端与该第四冷侧输送管路53连接(如图2所示),来通过该冷侧比例风门902来调控该第一脱附浓缩气体管路66与该第四冷侧输送管路53的风量,因此,当该第四冷侧输送管路53内的挥发性有机化合物(vocs)浓度变高时,能通过该冷侧比例风门902来将该第一脱附浓缩气体管路66内的部分脱附浓缩气体输送到该第四冷侧输送管路53内,使该第四冷侧输送管路53内的脱附浓缩气体能与该第一脱附浓缩气体管路66内
的部分脱附浓缩气体再一次的混合,使温度较低的该第一脱附浓缩气体管路66内的部分脱附浓缩气体能让温度较高的该第四冷侧输送管路53内的脱附浓缩气体进行降温,由此,当挥发性有机化合物(vocs)浓度变高时,能通过该冷侧比例风门902来调控风量的大小,以具有调节热回收量或浓度的功能,使有机废气在处理时,能防止直燃式焚烧炉(to)10不会因炉温太高而发生过温的现象,甚至导致停机的情况发生。
110.第三种实施例(如图7所示)的差异为步骤s390冷侧比例风门调控:在该第一冷侧输送管路23与该第四冷侧输送管路53之间设一冷侧比例风门903,来通过该冷侧比例风门903来调控该第一冷侧输送管路23与该第四冷侧输送管路53的风量。
111.其中上述的步骤s390中该冷侧比例风门903的一端与该第一冷侧输送管路23路连接,且该冷侧比例风门903的另一端与该第四冷侧输送管路53连接(如图3所示),来通过该冷侧比例风门903来调控该第一冷侧输送管路23与该第四冷侧输送管路53的风量,因此,当该第四冷侧输送管路53内的挥发性有机化合物(vocs)浓度变高时,能通过该冷侧比例风门903来将该第一冷侧输送管路903内的部分脱附浓缩气体输送该第四冷侧输送管路53内,使该第一冷侧输送管路23内的脱附浓缩气体能与该第四冷侧输送管路53内的脱附浓缩气体再一次的混合,使温度较低的该第一冷侧输送管路23内的脱附浓缩气体能让温度较高的该第四冷侧输送管路53内的脱附浓缩气体进行降温,由此,当挥发性有机化合物(vocs)浓度变高时,能通过该冷侧比例风门903来调控风量的大小,以具有调节热回收量或浓度的功能,使有机废气在处理时,能防止直燃式焚烧炉(to)10不会因炉温太高而发生过热的现象,甚至导致停机的情况发生。
112.此外,第四种实施例(如图8所示)的差异为步骤s490冷侧比例风门调控:于该第一脱附浓缩气体管路66上设有一冷侧比例风门904,而该冷侧比例风门904的另一端供外气进入,来通过该冷侧比例风门904来调控该第一脱附浓缩气体管路66的风量。
113.其中上述步骤s490中该冷侧比例风门904的另一端供外气进入(如图4所示),其中该外气可为新鲜空气或是其他气体,来通过该冷侧比例风门904来调控该第一脱附浓缩气体管路66的风量。因此,当由该第一吸附转轮60的脱附区603所产生的脱附浓缩气体在进入该第一脱附浓缩气体管路66后,且该第一脱附浓缩气体管路66内的温度变得较高或是浓度变得较高时,可通过该冷侧比例风门904的另一端所输入外气来进行调节,使该第一脱附浓缩气体管路66内的脱附浓缩气体能达到降温的效果或是浓度降低的效果。
114.上述内容,仅为本发明的优选实施例,但不能以此限定本发明实施的范围;所以,凡依本发明权利要求书及发明说明书内容所作的简单的等效变化与修饰,皆应仍属本发明专利涵盖的范围内。