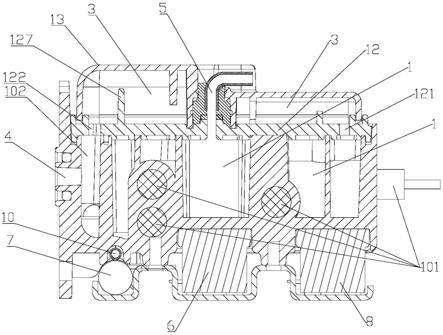
1.本实用新型涉及蒸汽发生装置,具体是一种双腔的蒸汽发生器。
背景技术:
2.1、现有目前手持式挂烫器体积较小,蒸汽发生器的功率及体积受限,导致产品寿命短,投诉率高等;用于手持式挂烫器的即热式蒸汽发生器通过电加热并在环绕流道内交换并汽化,由于只有一个汽化腔,其空间小,久用后手持式挂烫机存在蒸汽量变小、蒸汽不连续、使用时有喷水或蒸汽喷出水分过大等不足;2、只有一个汽化腔的蒸汽发生器久用生产生的水垢会残留在内部水道壁容易堵塞。
技术实现要素:
3.为了解决上述技术问题,本实用新型提供一种结构简单、设计合理,在有限的空间内分成两层腔体,提高气化效果的双腔的蒸汽发生器。
4.解决上述技术问题的方案为:
5.一种双腔的蒸汽发生器,蒸汽发生器内部的下层设有蒸汽腔、上层设有气化腔,气化腔与蒸汽腔之间设有导热金属薄板层,通过导热金属薄板层隔开分为上、下布置的腔体,导热金属薄板层的后端设有蒸汽经过孔,气化腔通过蒸汽经过孔连通蒸汽腔;
6.所述蒸汽发生器的前端设有蒸气出气孔,蒸气出气孔与气化腔连通,蒸汽经过孔与蒸气出气孔前后错位布置;
7.所述蒸汽发生器上设置有连通蒸汽腔的进水管道;
8.所述蒸汽腔的腔底固定有发热管,发热管的两个接电线端穿出在蒸汽发生器的后端;
9.所述蒸汽发生器的底部固定有第一温控器。
10.优选技术方案的进一步:所述蒸汽发生器包括铝制造的底座、铝制造的导热金属薄板层、顶盖;
11.所述底座内的中后部设有独立的蒸汽腔,蒸汽腔底部的底座本体内包裹固定有发热管,发热管的两个接电线端穿出在底座的后端;
12.所述底座的中部外底壁嵌入式固定有第一温控器;
13.所述底座内的前部设有独立的气化流通道,气化流通道对出的位置是蒸气出气孔;
14.所述导热金属薄板层密封盖合在底座的顶部,导热金属薄板层将蒸汽腔、气化流通道密封分隔;
15.所述导热金属薄板层的前端设有气化流通孔;
16.所述顶盖密封盖合在导热金属薄板层的顶部,顶盖与导热金属薄板层之间形成气化腔,蒸汽腔、蒸汽经过孔、气化腔、气化流通孔、气化流通道、蒸气出气孔依次连通;
17.所述进水管道包括设置在导热金属薄板层上的入水孔、密封穿接在顶盖上进水
管,进水管插入在入水孔处,进水管上穿接有密封圈,密封圈被夹紧在导热金属薄板层与顶盖之间,用于密封水孔处、进水管的连接处。
18.优选技术方案的进一步:所述底座内设有迂回弯曲的水道挡壁,迂回弯曲的水道挡壁使之形成迂回弯曲的水道,迂回弯曲的水道组成蒸汽腔;所述导热金属薄板层的反面设有与水道挡壁对应的迂回弯曲的密封槽,导热金属薄板层盖合底座后,水道挡壁顶部嵌入在密封槽内。
19.优选技术方案的进一步:所述迂回弯曲的水道挡壁由蒸汽腔的中心处往外绕过出形成,蒸汽腔的中心处与入水孔垂直对位;所述第一温控器与入水孔垂直对应。
20.优选技术方案的进一步:所述发热管中部为螺旋形,螺旋形发热管的两端延伸接电线端。
21.优选技术方案的进一步:所述底座的前部外底壁嵌入式固定有熔断体,第一温控器先连接电源的火线,另一端与发热管连接,发热管的另一端连接熔断体,熔断体的另一端连接电源的零线。
22.优选技术方案的进一步:所述底座的后部外底壁嵌入式固定有第二温控器;所述进水管连接有水泵,水泵连接有电开关,电开关连接第二温控器,水泵、电开关、第二温控器串连连接,第二温控器连接电源的火线,水泵的另一端连接在发热管、熔断体之间;所述底座的前部外底壁嵌入式固定有温度传感器;所述第一温控器、第二温控器、熔断体、温度传感器通过金属支架夹装固定连接在底座的底部。
23.优选技术方案的进一步:所述导热金属薄板层与底座之间通过耐高温密封垫圈、螺丝拧紧密封盖合连接;所述顶盖与导热金属薄板层之间通过耐高温密封垫圈、螺丝拧紧密封盖合连接;所述顶盖为铝制造。
24.优选技术方案的进一步:所述蒸气出气孔通过密封环圈连接有变径环圈,变径环圈密封连接有出气面板,出气面板上设有若干蒸气分布小孔。
25.优选技术方案的进一步:所述导热金属薄板层的顶部延伸凸起有若干块不同高度的气流缓冲变道档板。
26.本实用新型的一种双腔的蒸汽发生器优点为:本产品在内部的下层设有蒸汽腔、上层设有气化腔,气化腔与蒸汽腔之间设有导热金属薄板层,水进入蒸汽腔后经发热管电加热将水汽化后产生高温高压蒸汽,此时水分比较多,高温高压蒸汽然后通过蒸汽经过孔进入气化腔,由于蒸汽腔是高温高压蒸汽,导热金属薄板层受热也高温,其温度与刚产生高温高压蒸汽相当,进入气化腔的水蒸汽受导热金属薄板层的二次间接加热,使水蒸汽往气化演进,提高气化率,最后再由蒸气出气孔喷出,使喷出蒸气水分少、干润细腻,可以快速去除衣物皱纹效果及提高熨烫体验。
附图说明
27.图1、图2、图3为本实用新型产品的立体图;
28.图4为本实用新型产品没有温控器的立体图;
29.图5为本实用新型产品的剖视图;
30.图6为本实用新型产品的俯视图;
31.图7为本实用新型产品发热管的立体图;
32.图8为本实用新型产品底座的立体图;
33.图9为本实用新型产品的爆炸图;
34.图10为本实用新型产品电子元件连接关系示意图;
35.图11为本实用新型产品顶盖的立体图;
36.图12、图13为本实用新型产品导热金属薄板层的立体图;
37.图14、图15、图16为本实用新型产品连接密封环圈、变径环圈、出气面板、蒸气分布小孔,形成挂烫器出蒸气部分的立体图。
38.蒸汽腔1、底座11、发热管101、气化流通道102、水道挡壁103、水道104、导热金属薄板层12、蒸汽经过孔121、气化流通孔122、入水孔123、进水管124、密封圈125、密封槽126、气流缓冲变道档板127、顶盖13、气化腔3、蒸气出气孔4、进水管道5、第一温控器6、熔断体7、第二温控器8、水泵9、温度传感器10、金属支架a、密封环圈41、变径环圈42、出气面板43、蒸气分布小孔431。
具体实施方式
39.一种双腔的蒸汽发生器,包括蒸汽发生器本体,蒸汽发生器内部的下层设有蒸汽腔1、上层设有气化腔3,气化腔3与蒸汽腔1之间设有导热金属薄板层12,通过导热金属薄板层12隔开分为上、下布置的两个腔体,导热金属薄板层12的后端设有蒸汽经过孔121,气化腔3通过蒸汽经过孔121连通蒸汽腔1;
40.所述蒸汽发生器的前端设有蒸气出气孔4,蒸气出气孔4与气化腔3连通,蒸汽经过孔121与蒸气出气孔4前后错位布置,目的在于加长水蒸气进行气化的路程;
41.所述蒸汽发生器上设置有连通蒸汽腔1的进水管道5,用于接外来水;
42.所述蒸汽腔1的腔底固定有发热管101,发热管101的两个接电线端穿出在蒸汽发生器的后端,用于接外部的电源(电源可以直流或交流);发热管101为即热式发热管101。
43.所述蒸汽发生器的底部固定有第一温控器6,第一温控器6为正向电源导通,常态下属于导通状态,用于防止蒸汽发生器干烧,防止温度过高,如果超温工作时,第一温控器6会自动切断电源。第一温控器6可以与连接发热管101的电源线连接,也可以与使用产品的控制系统连接,视实际使用产品的电路设计而定;例如:第一温控器6最高受热温度为180℃,如果蒸汽发生器的底部温度高于180℃,那么第一温控器6内部自动断开断电,停止发热管101的加热,低于设定温度后又能自动复位通电。
44.使用时,发热管101通电发热后(例如发热:30秒~2分钟,根据使用器具的控制系统设定),然后水从进水管道5进入到蒸汽腔1并高温高压蒸汽,导热金属薄板层因此受热也高温,导热金属薄板层的温度与刚产生高温高压蒸汽相当,蒸汽腔1的蒸汽从蒸汽经过孔121往上走进入气化腔3,进入气化腔的水蒸汽受导热金属薄板层的高温使原存在较多大颗粒水分子的水蒸汽得到二次间接加热,使原存在较多大颗粒水分子的水蒸汽进一步升华,由水蒸汽往水蒸气进行气化演进,最终得到水分少、干润细腻的高温蒸气,最后在蒸气出气孔4喷出。
45.优选技术方案的进一步:所述蒸汽发生器包括铝制造的底座11、铝制造的导热金属薄板层12、顶盖13;用铝制造的底座11、导热金属薄板层12其的导热效果高,性能好;
46.所述底座11内的中后部设有独立的蒸汽腔1,蒸汽腔1底部的通过压铸方法在底座
11本体内包裹固定有发热管101,发热管101的两个接电线端穿出在底座11的后端;目的在于不用使发热管101直接与水直接接触加热,减少蒸汽腔1内部水垢的产生,同时也使蒸汽腔1底部整体受热高温,提高换热效果;蒸汽腔1的腔底与发热管101之间的底座11底壁厚在2毫米~3毫米。
47.所述底座11的中部外底壁嵌入式固定有第一温控器6,使第一温控器6更加与发热管101接近,提高温控的灵敏度,同时也好稳定地固定第一温控器6;优选方案为:在底座11的中部外底壁设一个洞,第一温控器6嵌入在洞内固定;
48.所述底座11内的前部设有独立的气化流通道102,气化流通道102对出的位置是蒸气出气孔4;由于发热管101是设置在底座11内,发热管101发热时,气化流通道102壁也会受到加热,当水蒸气流经此气化流通道102时也受到高温保持继续加热,保证水蒸气高温输出;
49.所述导热金属薄板层12密封盖合在底座11的顶部,导热金属薄板层12将蒸汽腔1、气化流通道102密封分隔,各自为独立的腔体;
50.所述导热金属薄板层12的前端设有气化流通孔122,用于水蒸气流通;
51.所述顶盖13密封盖合在导热金属薄板层12的顶部,顶盖13与导热金属薄板层12之间形成气化腔3,蒸汽腔1、蒸汽经过孔121、气化腔3、气化流通孔122、气化流通道102、蒸气出气孔4依次连通,也是蒸汽往水蒸气的演进过程;
52.所述进水管道5包括设置在导热金属薄板层12上的入水孔123、密封穿接在顶盖13上进水管124,进水管124插入在入水孔123处,进水管124上穿接有密封圈125,密封圈125夹紧在导热金属薄板层12与顶盖13之间,用于密封水孔处、进水管124的连接处,更加合理布局进水的位置及结构。
53.优选技术方案的进一步:所述底座11内设有迂回弯曲的水道挡壁103,迂回弯曲的水道挡壁103使之形成迂回弯曲的水道104,迂回弯曲的水道104组成蒸汽腔1,增加水流路径,蒸汽形成更加快速、有序、合理、顺流;所述导热金属薄板层12的反面设有与水道挡壁103对应的迂回弯曲的密封槽126,导热金属薄板层12盖合底座11后,水道挡壁103顶部嵌入在密封槽126内,由于导热金属薄板层12是铝做的,导热金属薄板层12受高温会有冷热系数产生,防止导热金属薄板层12与水道挡壁103的接触产生缝隙,防止水形成蒸汽后串水、串汽,只能让水变成水蒸汽后直接往水道顺着走。密封槽126可以由导热金属薄板层12的板面设置两条凸筋之间形成,也可是在导热金属薄板层12的板面设置下凹形成。
54.优选技术方案的进一步:所述迂回弯曲的水道挡壁103由蒸汽腔1的中心处往外绕过出形成,蒸汽腔1的中心处与入水孔123垂直对位,因为中心是最热的,有利于更加合理布置水道的进水起点位置;所述第一温控器6与入水孔123垂直对应,第一温控器6布置在冷热交替的敏感位置,提高第一温控器6的温度控制灵敏度。
55.优选技术方案的进一步:所述发热管101中部为螺旋形,布置在底座内的中心区域,目的在于增加中心发热面积、换热效能,螺旋形发热管101的两端延伸接电线端。
56.优选技术方案的进一步:所述底座11的前部外底壁嵌入式固定有熔断体7,第一温控器6先连接电源的火线,另一端与发热管101连接,发热管101的另一端连接熔断体7,熔断体7的另一端连接电源的零线。熔断体7为的保险丝。当第一温控器6工作损坏失效后,蒸汽发生器依然工作,蒸汽发生器本体如果超温工作,超过熔断体7承受温度时,熔断体7自动断
开停电,停止加热,熔断体7为一次性使用,如果熔断体7烧坏后蒸汽发生器就不能再工作了;此举在于合理布置电子元件,目的在于保护安全用电,防止发生意外事故。
57.优选技术方案的进一步:所述底座11的后部外底壁嵌入式固定有第二温控器8;所述进水管124连接有水泵9,水泵9连接有电开关91,电开关91连接第二温控器8,水泵9、电开关91、第二温控器8串连连接,第二温控器8为反向导通工作,当底座11的本体温度被加热达到设定温度后第二温控器8才导通,导通后,启动电开关91才能导通电源,水泵9才能工作;第二温控器8连接电源的火线,水泵9的另一端连接在发热管101、熔断体7之间;如果底座11的本体温度没有达到第二温控器8所需导通的温度,第二温控器8是不导通的,例如:第二温控器8的导通温度是100℃,底座11的本体温度要被加热超过100℃,第二温控器8才导通,水泵9才能工作,否则不通电,水泵9不能工作。
58.所述底座11的前部外底壁嵌入式固定有温度传感器10;所述第一温控器6、第二温控器8、熔断体7、温度传感器10通过金属支架a夹装固定连接在底座11的底部。水泵9用于抽水进入蒸汽腔1,可以通过水泵9控制水流量来控制最终的水蒸气产生量及控制水蒸气的干/湿度。电子元件之间的连接关系为合理布置电子元件,目的在于安全用电,防止发生意外事故。温度传感器10用于与应用产品的控制系统连接,温度传感器10反馈温度信号给控制系统,探测蒸汽发生器的工作温度是否异常。
59.优选技术方案的进一步:所述导热金属薄板层12与底座11之间通过耐高温密封垫圈、螺丝拧紧密封盖合连接;所述顶盖13与导热金属薄板层12之间通过耐高温密封垫圈、螺丝拧紧密封盖合连接;所述顶盖13为铝制造。提高密封效果。优选方案:在底座11的边沿设有密封凹槽,密封凹槽内放置耐高温密封垫圈,在导热金属薄板层12的边沿设置对应的凸条环边,两者盖用螺丝拧紧后,凸条环边嵌入在密封凹槽内压紧耐高温密封垫圈,提高密封连接效果。
60.优选技术方案的进一步:所述蒸气出气孔4通过密封环圈41连接有变径环圈42,变径环圈42密封连接有出气面板43,出气面板43上设有若干蒸气分布小孔431;此结构适用于挂烫机,由于蒸气出气孔4比较小,为长条形状,为增大最终的水蒸气出气面积,所以要增加变径环圈42,然后连接出气面板43,出气面板43是直接接触织物的,在出气面板43上设有若干蒸气分布小孔431,增加出水蒸气的面积,使蒸气分散喷出并干润细腻,可以快速去除衣物皱纹效果及提高熨烫体验。
61.优选技术方案的进一步:所述导热金属薄板层12的顶部延伸凸起有若干块不同高度的气流缓冲变道档板127,防止气化腔3的水蒸气直接往前奔,让它降低流速,使水蒸气形成更加气化。
62.最后应说明的是:以上各实施例仅用以说明本实用新型的技术方案,而非对其限制;尽管参照前述各实施例对本实用新型进行了详细的说明,本领域的普通技术人员应当理解:其依然可以对前述各实施例所记载的技术方案进行修改,或者对其中部分或者全部技术特征进行等同替换;而这些修改或者替换,并不使相应技术方案的本质脱离本实用新型各实施例技术方案的范围。