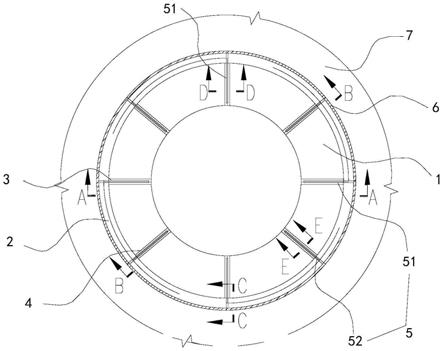
1.本发明涉及船舶建造技术领域,特别是涉及一种全回转推进器基座下封板的安装方法。
背景技术:
2.为提高船舶航行操作的灵活性及满足船舶规范中dp动力定位的要求,大部分的海洋工程船均采用电力推进系统为船舶提供推进动力。全回转推进器是电力推进系统的重要组成部分,通常全回转推进器设置在船舶尾部的舵机舱内,通过全回转推进装置基座与船体结构连接固定,而为保证全回转推进器的安装,需在船底板下方开设较大的开孔,保证全回转推进器的上半部分可整体穿过船底板安装到舵机舱内的基座上。
3.因船底开孔远大于全回转推进器的外形,全回转舵桨处船体结构、舵桨基座和设备形成的空腔,对船舶水动力性能产生不利影响,同时船舶航行过程中的水流直接冲击也会加速设备的损伤。因此需在基座筒体与推进器的间隙处增设封板,以尽可能减小开孔与全回转推进器间之间的间隙。因封板需要在全回转推进器安装完后才能进行施工,而此时因全回转推进器挡住封板上方的施工空间,无法从舵机舱上方进行施工,只能在船底下方进行封板与船底板的单面焊接,但此区域存在全回转推进器振动及水流冲击双重作用,单面焊无法满足结构强度要求。
技术实现要素:
4.本发明要解决的技术问题是提供一种能有效降低施工难度以便完成焊接施工,同时保证封板结构的安装质量和结构强度的全回转推进器基座下封板的安装方法。
5.为了实现上述目的,本发明提供了一种全回转推进器基座下封板的安装方法,包括以下步骤:
6.步骤一:制作封板,所述封板呈圆环形,然后在所述封板上开设板缝将所述封板四等分形成四块分板,在所述分板上开设多个塞焊孔,多个所述塞焊孔沿所述分板的中心轴分布;
7.步骤二:制作角接焊钢衬垫,所述角接焊钢衬垫呈圆环形,所述角接焊钢衬垫的外径与全回转推进器的基座筒体的内径相适,然后在所述角接焊钢衬垫上开设板缝将所述角接焊钢衬垫四等分形成四块衬垫分板;
8.步骤三:制作对接焊钢衬垫和塞焊钢衬垫,所述对接焊钢衬垫和所述塞焊钢衬垫呈条形;
9.步骤四:安装加强肘板,将所述加强肘板焊接固定在所述基座筒体的内侧,所述加强肘板设置八块,八块所述加强肘板围绕所述基座筒体的轴线均匀分布,所述加强肘板的底部与所述加强肘板对应位置的船底板的结构相适,所述加强肘板包括第一肘板和第二肘板,所述第一肘板沿船体的长度或宽度方向分布,所述第二肘板设于相邻的所述第一肘板之间;
10.步骤五:安装所述角接焊钢衬垫,先将所述衬垫分板进行定位,使得相邻的所述衬垫分板之间的板缝与所述第一肘板的位置错开,然后对所述衬垫分板进行点焊固定,接着对相邻的所述衬垫分板之间的板缝进行焊接固定,最后对所述角接焊钢衬垫与所述基座筒体的内侧的角接缝进行焊接固定。
11.步骤六:安装对接焊钢衬垫及塞焊钢衬垫,将所述对接焊钢衬垫焊接固定在所述第一肘板的下方,将所述塞焊钢衬垫焊接固定在所述第二肘板的下方;
12.步骤七:安装封板,先将所述分板进行定位,使得相邻的所述分板之间的板缝与所述第一肘板的位置对应,使得所述塞焊孔的位置与所述塞焊钢衬垫的位置对应,然后对所述分板进行点焊固定,接着对相邻的所述分板之间的板缝进行焊接固定,再对所述封板与所述角接焊钢衬垫的角接缝进行焊接固定,最后对所述塞焊孔的侧壁与所述塞焊钢衬垫进行焊接固定。
13.作为本发明的优选方案,在步骤三中,所述对接焊钢衬垫和所述塞焊钢衬垫的宽度大于所述加强肘板的宽度,所述对接焊钢衬垫和所述塞焊钢衬垫的厚度与所述封板的厚度相等。
14.作为本发明的优选方案,在步骤四中,所述加强肘板的底面与所述基座筒体的底面的距离为所述封板的厚度与其对应的所述对接焊钢衬垫或所述塞焊钢衬垫的厚度的总和。
15.作为本发明的优选方案,在步骤五中,对所述角接焊钢衬垫与所述基座筒体的内侧的角接缝进行焊接固定时采用分段退焊法。
16.作为本发明的优选方案,在步骤七中,对所述封板与所述角接焊钢衬垫的角接缝进行焊接固定时采用分段退焊法。
17.作为本发明的优选方案,在步骤五中,在相邻的所述衬垫分板之间的板缝上方粘贴陶瓷衬垫,在所述衬垫分板的下方进行焊接,待相邻的所述衬垫分板之间的板缝焊接完成后,撕下所述陶瓷衬垫,打磨焊渣。
18.作为本发明的优选方案,在步骤六中,所述对接焊钢衬垫靠近所述基座筒体的中心轴的一端到所述基座筒体的内侧的距离小于所述第一肘板靠近所述基座筒体的中心轴的一端到所述基座筒体的内侧的距离,所述塞焊钢衬垫靠近所述基座筒体的中心轴的一端到所述基座筒体的内侧的距离小于所述第二肘板靠近所述基座筒体的中心轴的一端到所述基座筒体的内侧的距离。
19.作为本发明的优选方案,在步骤一中,所述封板的板缝处开设有从上至下逐渐扩张的坡口。
20.作为本发明的优选方案,在步骤六中,所述对接焊钢衬垫与所述第一肘板为双面角接焊连接,所述塞焊钢衬垫与所述第二肘板为双面角接焊连接。
21.作为本发明的优选方案,在步骤六中,所述封板的外侧与所述基座筒体的内侧之间存在间隙。
22.本发明实施例一种全回转推进器基座下封板的安装方法,与现有技术相比,其有益效果在于:通过对封板增加板缝,将封板划分为四块分板进行安装,降低了整块封板的转运和安装定位的难度;通过设置塞焊孔,避免将封板划分为八块导致划分过小而发生焊接变形较大的问题;加强肘板的设置,将封板受力通过加强肘板分散传递到船体结构,增加了
封板的结构强度;采用对接钢衬垫及角接钢衬垫组合的工艺方式,保证封板所有需焊接处均可在船底的一侧施工,同时达到了单面焊接双面成形的效果;通过合理的安装工序及焊接顺序,可将焊接过程封板变形将至最低。
附图说明
23.图1是本发明的全回转推进器基座的俯视图;
24.图2是本发明的封板的俯视图;
25.图3是本发明的角接焊钢衬垫的俯视图;
26.图4是本发明的角接焊钢衬垫的焊接顺序示意图;
27.图5是图1的a-a剖视图;
28.图6是图2的b-b剖视图;
29.图7是图3的c-c剖视图;
30.图8是图4的d-d剖视图;
31.图9是图5的e-e剖视图;
32.图中,1、封板;11、分板;12、塞焊孔;13、封板的板缝;2、角接焊钢衬垫;21、衬垫分板;22、角接焊钢衬垫的板缝;3、对接焊钢衬垫;4、塞焊钢衬垫;5、加强肘板;51、第一肘板;52、第二肘板;6、基座筒体;7、船底板。
具体实施方式
33.下面结合附图和实施例,对本发明的具体实施方式作进一步详细描述。以下实施例用于说明本发明,但不用来限制本发明的范围。
34.在本发明的描述中,应当理解的是,本发明采用术语“中心”、“纵向”、“横向”、“上”、“下”、“前”、“后”、“左”、“右”、“竖直”、“水平”、“顶”、“底”“内”、“外”等指示的方位或位置关系为基于附图所示的方位或位置关系,仅是为了便于描述本发明和简化描述,而不是指示或暗示所指的装置或元件必须具有特定的方位、以特定的方位构造和操作,因此不能理解为对本发明的限制。此外,术语“第一”、“第二”、“第三”仅用于描述目的,而不能理解为指示或暗示相对重要性。
35.如图1~9所示,本发明优选实施例的一种全回转推进器基座下封板的安装方法,包括以下步骤:
36.步骤一:制作封板1,封板1呈圆环形,然后在封板1上开设板缝将封板1四等分形成四块分板11,在分板11上开设多个塞焊孔12,多个塞焊孔12沿分板11的中心轴分布,如图2所示,本实施例中,塞焊孔12的长度为75mm,塞焊孔12的宽度为封板1厚度的两倍,相邻的塞焊孔12的间距为75mm;
37.步骤二:制作角接焊钢衬垫2,角接焊钢衬垫2呈圆环形,角接焊钢衬垫2的外径与全回转推进器的基座筒体6的内径相适,然后在角接焊钢衬垫2上开设板缝将角接焊钢衬垫2四等分形成四块衬垫分板21,如图3所示,本实施例中,角接焊钢衬垫2的内环与外环之间的距离为100mm;
38.步骤三:制作对接焊钢衬垫和塞焊钢衬垫4,对接焊钢衬垫和塞焊钢衬垫4呈条形;
39.步骤四:安装加强肘板5,将加强肘板5焊接固定在基座筒体6的内侧,加强肘板5的
一侧与基座筒体6的内侧焊接固定,加强肘板5设置八块,八块加强肘板5围绕基座筒体6的轴线均匀分布,加强肘板5的底部与加强肘板5对应位置的船底板7的结构相适,使得结构合理,如图1所示,例如第一肘板51的底面与其外侧的船底板7的底面平行,均为倾斜设置,加强肘板5包括分别设置四块的第一肘板51和第二肘板52,第一肘板51沿船体的长度或宽度方向分布,第二肘板52设于相邻的第一肘板51之间;
40.步骤五:安装角接焊钢衬垫2,先将衬垫分板21进行定位,衬垫分板21设于基座筒体6内且拼接形成角接焊钢衬垫2,使得相邻的衬垫分板21之间的板缝与第一肘板51的位置错开,避免第一肘板51阻碍导致无法从衬垫分板21的上方进行焊接,然后对衬垫分板21进行点焊固定,接着对相邻的衬垫分板21之间的板缝进行焊接固定,最后对角接焊钢衬垫2与基座筒体6的内侧的角接缝进行焊接固定,角接焊钢衬垫2的焊接可从角接焊钢衬垫2的上方和下方进行焊接操作,不会受阻,操作简便;
41.步骤六:安装对接焊钢衬垫3及塞焊钢衬垫4,将对接焊钢衬垫3焊接固定在第一肘板51的下方,将塞焊钢衬垫4焊接固定在第二肘板52的下方,在本实施例中,对接焊钢衬垫3或塞焊钢衬垫4靠近基座筒体6的内侧的一端与角接焊钢衬垫2的内侧连接;
42.步骤七:安装封板1,先将分板11进行定位,使得相邻的分板11之间的板缝与第一肘板51的位置对应,使得塞焊孔12的位置与塞焊钢衬垫4的位置对应,然后对分板11进行点焊固定,接着对相邻的分板11之间的板缝进行焊接固定,再对封板1与角接焊钢衬垫2的角接缝进行焊接固定,最后对塞焊孔12的侧壁与塞焊钢衬垫4进行焊接固定。
43.通过对封板1增加板缝,将封板1划分为四块块进行安装,降低了整块封板1的转运和安装定位的难度;通过设置塞焊孔12,避免将封板1划分为八块导致划分过小而发生焊接变形较大的问题;加强肘板5的设置,将封板1受力通过加强肘板5分散传递到船体结构,增加了封板1的结构强度;采用对接钢衬垫及角接钢衬垫组合的工艺方式,保证封板1所有需焊接处均可在船底的一侧施工,同时达到了单面焊接双面成形的效果;通过合理的安装工序及焊接顺序,可将焊接过程封板1变形将至最低。
44.示例性的,在步骤三中,对接焊钢衬垫3和塞焊钢衬垫4的宽度大于加强肘板5的宽度,确保对接焊钢衬垫3和塞焊钢衬垫4与加强肘板5连接良好,角接焊钢衬垫2、对接焊钢衬垫3和塞焊钢衬垫4的厚度与封板1的厚度相等,以便制作。
45.示例性的,在步骤四中,加强肘板5的底面与基座筒体6的底面的距离为封板1的厚度与其对应的对接焊钢衬垫3或塞焊钢衬垫4的厚度的总和,即加强肘板5安装后,加强肘板5的下方预留了安装封板1以及对接焊钢衬垫3或塞焊钢衬垫4的空间,使得安装完毕后,封板1的底面与基座筒体6的底面持平,如图5和图6所示,其中第一肘板51对应的是对接焊钢衬垫3,第二肘板52对应的是塞焊钢衬垫4。
46.示例性的,在步骤五中,对角接焊钢衬垫2与基座筒体6的内侧的角接缝进行焊接固定时采用分段退焊法,分段退焊,指的是焊缝较长时,将焊件接缝划分成若干段,分段焊接,其焊接顺序和方向如图4所示,避免在焊接时角接焊钢衬垫2发生变形。同理,在步骤七中,对封板1与角接焊钢衬垫2的角接缝进行焊接固定时采用分段退焊法。
47.示例性的,在步骤五中,在相邻的衬垫分板21之间的板缝上方粘贴陶瓷衬垫,在衬垫分板21的下方进行焊接,便于操作,待相邻的衬垫分板21的板缝焊接完成后,撕下陶瓷衬垫,打磨焊渣,确保焊接后的表面平整。
48.示例性的,在步骤六中,对接焊钢衬垫3靠近基座筒体6的中心轴的一端到基座筒体6的内侧的距离大于第一肘板51靠近基座筒体6的中心轴的一端到基座筒体6的内侧的距离,如图5所示,即对接焊钢衬垫3靠近基座筒体6的中心轴的一端往靠近基座筒体6的中心轴的方向突出第一肘板51对应的端部,使对接焊钢衬垫3与第一肘板51焊接时,第一肘板51靠近基座筒体6的中心轴的一端能与对接焊钢衬垫3包角焊,同理塞焊钢衬垫4靠近基座筒体6的中心轴的一端到基座筒体6的内侧的距离大于第二肘板52靠近基座筒体6的中心轴的一端到基座筒体6的内侧的距离,如图6所示。
49.示例性的,在步骤一中,封板的板缝13处开设有从上至下逐渐扩张的坡口,如图8所示,本实施例中坡口的倾斜角度为20
°
,坡口的设置以便从封板1的下方对封板1的板缝处进行焊接,同时坡口的设置使得相邻的分板11焊接紧固。同理,角接焊钢衬垫的板缝22处同样开设有坡口。
50.示例性的,在步骤六中,对接焊钢衬垫3与第一肘板51为双面角接焊连接,如图8所示,第一肘板51的两侧均与对接焊钢衬垫3的顶部焊接固定,连接稳固,塞焊钢衬垫4与第二肘板52为双面角接焊连接,如图9所示,第二肘板52的两侧均与塞焊钢衬垫4的顶部焊接固定,连接稳固。
51.示例性的,在步骤六中,分板11定位后,四块分板11拼接成的封板1的外侧与基座筒体6的内侧之间存在间隙,在本实施例中,该间隙为50mm,如图7所示,预留间隙实现包角焊,将封板1的外侧包围,使得封板1的外侧与角接焊钢衬垫2的连接稳固。
52.以上所述仅是本发明的优选实施方式,应当指出,对于本技术领域的普通技术人员来说,在不脱离本发明技术原理的前提下,还可以做出若干改进和替换,这些改进和替换也应视为本发明的保护范围。