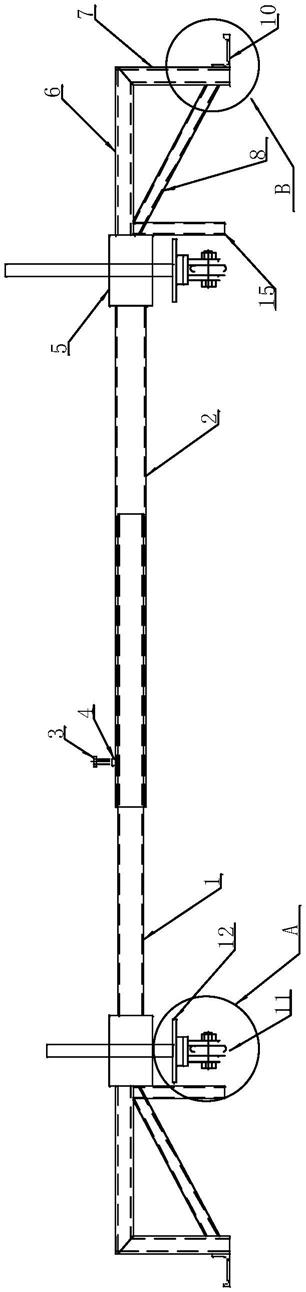
1.本技术涉及船舶建造技术领域,特别涉及一种船舶舱室单元运输车。
背景技术:
2.船舶舱室,尤其是豪华游轮的舱室,一般都采用模块化制造技术,在车间预制好后再运入船舱进行定位安装。为了提高舱室单元运输效率,需要借助运输小车。
3.目前的运输小车的尺寸比较单一,在造船的时候,通常根据船舱模块的尺寸专门设计制作几种不同尺寸的运输小车,在使用的时候需要进行更换,效率较低。而且这一套运输小车只适用于这一型号船舶的制造,通用性比较差。
4.申请内容
5.本技术的目的在于提供一种船舶舱室单元运输车,以提高其在船舶舱室单元运输过程中的通用性和运输效率。
6.本技术的技术方案是这样实现的:
7.一种船舶舱室单元运输车,包括伸缩模块和装载模块;
8.所述伸缩模块包括第一钢架、第二钢架和固定装置,所述第一钢架和所述第二钢架分别包括多根能够相互插接的钢管,通过改变相对应的所述钢管的插接深度,能够调整所述伸缩模块的宽度;所述固定装置设置于所述第一钢架或所述第二钢架上,用于使所述第一钢架和所述第二钢架的位置相对固定;
9.所述伸缩模块的底部还设置有多个脚轮;
10.所述装载模块设置在所述伸缩模块上,或设置在所述伸缩模块的两侧,用于承接船舶舱室单元。
11.在本技术较佳的技术方案中,该船舶舱室单元运输车还包括至少两个升降模块,所述升降模块的底部通过底座安装板与所述脚轮连接,各所述升降模块的主体部分分别与所述第一钢架和所述第二钢架连接,用于带动所述伸缩模块相对地面做升降运动。
12.在本技术较佳的技术方案中,所述升降模块为伞齿轮丝杠升降机。
13.在本技术较佳的技术方案中,各所述伞齿轮升降机之间通过传动杆连接,从而实现联动升降。
14.在本技术较佳的技术方案中,所述伞齿轮丝杠升降机的驱动机构采用手摇把柄或电机。
15.在本技术较佳的技术方案中,所述船舶舱室单元运输车还包括刹车组件,所述刹车组件用于对所述脚轮制动。
16.在本技术较佳的技术方案中,所述第一钢架和所述第二钢架中的其中一个包括若干根外钢管,另一个包括若干根内钢管,所述外钢管的内径略大于所述内钢管的外径。
17.在本技术较佳的技术方案中,所述固定装置包括固定螺栓和紧固螺母;所述外钢管上设置螺纹孔,所述固定螺栓的螺纹端穿过所述外钢管上的螺纹孔并抵接所述内钢管,所述紧固螺母与所述固定螺栓螺纹连接,用于将所述固定螺栓与所述外钢管紧固连接。
18.在本技术较佳的技术方案中,所述装载模块设置于所述伸缩模块的两侧时,包括多根桁架和撑脚;多根所述桁架组成三角桁架结构,所述撑脚设置在所述三角桁架结构的下端外侧,用于承载所述船舶舱室单元。
19.在本技术较佳的技术方案中,所述撑脚的外侧边缘向上方弯折,形成倒钩,以防止所述船舶舱室单元从所述撑脚上脱落。
20.在本技术较佳的技术方案中,所述底座安装板的底面设置相互交叉的第一加强筋和第二加强筋。
21.在本技术较佳的技术方案中,在装载模块的左右两侧还分别设置一沿竖向布置的限位杆,防止升降模块发生转动。
22.本技术的有益效果为:
23.该运输车可以横向伸缩,实现宽度的调节,从而可以满足不同跨度的船舶舱室单元的运输需要,能够适用于各类船舶的制造过程中,通用性强,也提高了建造效率。
附图说明
24.为了更清楚地说明本技术实施例的技术方案,下面将对实施例中所需要使用的附图作简单地介绍,应当理解,以下附图仅示出了本技术的某些实施例,因此不应被看作是对范围的限定,对于本领域普通技术人员来讲,在不付出创造性劳动的前提下,还可以根据这些附图获得其他相关的附图。
25.图1为本技术实施例提供的船舶舱室单元运输车整体结构的正向示意图;
26.图2为图1中区域a所示的底座组件的侧向示意图;
27.图3为底座下表面的示意图;
28.图4为图1中区域b所示的撑脚组件的侧向示意图。
29.图中标号:
[0030]1‑
第一钢架;
ꢀꢀꢀꢀꢀꢀꢀꢀ2‑
第二钢架;
[0031]3‑
固定螺栓;
ꢀꢀꢀꢀꢀꢀꢀꢀ4‑
紧固螺母;
[0032]5‑
升降模块;
ꢀꢀꢀꢀꢀꢀꢀꢀ6‑
第一桁架;
[0033]7‑
第二桁架;
ꢀꢀꢀꢀꢀꢀꢀꢀ8‑
第三桁架;
[0034]9‑
第四桁架;
ꢀꢀꢀꢀꢀꢀꢀꢀ
10
‑
撑脚;
[0035]
11
‑
脚轮;
ꢀꢀꢀꢀꢀꢀꢀꢀꢀꢀꢀ
12
‑
底座安装板;
[0036]
13
‑
第一加强筋;
ꢀꢀꢀꢀꢀ
14
‑
第二加强筋;
[0037]
15
‑
限位杆;
[0038]
a
‑
底座组件;
ꢀꢀꢀꢀꢀꢀꢀꢀ
b
‑
撑脚组件。
具体实施方式
[0039]
为使本技术实施例的目的、技术方案和优点更加清楚,下面将结合本技术实施例中的附图,对本技术实施例中的技术方案进行清楚、完整地描述,显然,所描述的实施例是本技术一部分实施例,而不是全部的实施例。通常在此处附图中描述和示出的本技术实施例的组件可以以各种不同的配置来布置和设计。
[0040]
因此,以下对在附图中提供的本技术的实施例的详细描述并非旨在限制要求保护
的本技术的范围,而是仅仅表示本技术的选定实施例。基于本技术中的实施例,本领域普通技术人员在没有作出创造性劳动前提下所获得的所有其他实施例,都属于本技术保护的范围。
[0041]
应注意到:相似的标号和字母在下面的附图中表示类似项,因此,一旦某一项在一个附图中被定义,则在随后的附图中不需要对其进行进一步定义和解释。
[0042]
在本技术的描述中,需要说明的是,术语“中心”、“上”、“下”、“左”、“右”、“竖直”、“水平”、“内”、“外”等指示的方位或位置关系为基于附图所示的方位或位置关系,或者是该申请产品使用时惯常摆放的方位或位置关系,仅是为了便于描述本技术和简化描述,而不是指示或暗示所指的装置或元件必须具有特定的方位、以特定的方位构造和操作,因此不能理解为对本技术的限制。此外,术语“第一”、“第二”、“第三”等仅用于区分描述,而不能理解为指示或暗示相对重要性。
[0043]
此外,术语“水平”、“竖直”、“悬垂”等术语并不表示要求部件绝对水平或悬垂,而是可以稍微倾斜。如“水平”仅仅是指其方向相对“竖直”而言更加水平,并不是表示该结构一定要完全水平,而是可以稍微倾斜。
[0044]
在本技术的描述中,还需要说明的是,除非另有明确的规定和限定,术语“设置”、“安装”、“相连”、“连接”应做广义理解,例如,可以是固定连接,也可以是可拆卸连接,或一体地连接;可以是机械连接,也可以是电连接;可以是直接相连,也可以通过中间媒介间接相连,可以是两个元件内部的连通。对于本领域的普通技术人员而言,可以具体情况理解上述术语在本技术中的具体含义。
[0045]
下面结合附图,对本技术的一些实施方式作详细说明。在不冲突的情况下,下述的实施例及实施例中的特征可以相互组合。
[0046]
如图1所示,本实施例提供了一种船舶舱室单元运输车,包括伸缩模块和装载模块;
[0047]
伸缩模块包括第一钢架1、第二钢架2和固定装置,第一钢架1包括若干根并列摆放的外钢管,第二钢架2包括若干根并列摆放的内钢管,且,外钢管的内径略大于内钢管的外径。外钢管与内钢管的数量与位置分别一一对应,从而使内钢管可以插入进外钢管中。通过改变相对应的内钢管与外钢管的插接深度,能够调整伸缩模块的宽度,从而调节运输车的宽度。
[0048]
固定装置包括固定螺栓3和紧固螺母4;外钢管上设置螺纹孔,固定螺栓3的螺纹端穿过外钢管上的螺纹孔并抵接内钢管,紧固螺母4与固定螺栓3螺纹连接,用于将固定螺栓3与外钢管紧固连接,从而实现外钢管与内钢管之间的紧固连接。
[0049]
在其他的实施方式中,还可以在外钢管的管壁上设置一个孔,内钢管的管壁设置多个孔,通过插销来实现外钢管的孔与内钢管上不同的孔之间连接,从而实现伸缩模块的伸缩调节和固定。
[0050]
伸缩模块的底部还设置有至少三个脚轮11,脚轮11的数量以偶数个为佳,可以提高运输车车体的平稳性;每个脚轮11还分别包括一刹车组件,用于实现对脚轮11的制动。
[0051]
装载模块设置在伸缩模块上,或设置在伸缩模块的两侧,用于承载船舶舱室单元。
[0052]
本实施例中,装载模块设置于伸缩模块的两侧,包括第一桁架6、第二桁架7、第三桁架8、第四桁架9和撑脚10。
[0053]
第一桁架6为横向设置,其一端与伸缩模块连接,并向运输车的外侧延伸;第二桁架7沿竖向设置,其上端与第一桁架6的外端连接;第三桁架8的两端分别连接第一桁架6和第二桁架7,从而,第一桁架6、第二桁架7和第三桁架8共同组成三角桁架结构。
[0054]
图1中的底座组件a的具体结构如图4所示,在第二桁架7的下端设置沿运输车长度方向设置的条形的撑脚10,撑脚10的横截面为l形,用于承载所述船舶舱室单元。第四桁架9的两端分别与第二桁架7和撑脚10连接,用于提高撑脚10与三角桁架结构之间的连接强度。
[0055]
传统结构中,通常是承载结构进行伸缩从而调节车体宽度,采用这种结构形式,承载结构的连接杆较细,且随着承载结构的伸长,其强度是在变低,不利于大重量物体的承载。本方案中进行伸缩的是运输车的主体钢架结构,而承载模块在伸缩过程中保持不变,可以保证承载模块始终具有较高的强度,而主体钢架结构的强度通常是高于承载模块的刚度,因此,本技术的结构形式可以更好的满足大重量大体积物体的运输。
[0056]
在更优选的实施方式中,撑脚10的外侧边缘向上方弯折,形成倒钩,以防止船舶舱室单元从撑脚10上脱落。倒钩的向上弯折高度不宜过大,过高的倒钩会导致撑脚10船舶舱室单元的搬上搬下比较困难。
[0057]
一般情况下,船舶舱室单元运输车的总体宽度在2600mm~3300mm之间可调,两侧脚轮11之间的间距不超过2300mm为宜。该宽度可以满足绝大多数邮轮的船舱单元的运输要求,而且具有较强的稳定性。
[0058]
为了满足船舶舱室单元的抬升需要,本实施例中所述的船舶舱室单元运输车还包括若干个升降模块5,一般情况下,升降模块5的数量与脚轮11相同,各升降模块5的底部通过底座安装板12与各脚轮11连接,各升降模块5的主体部分分别与第一钢架1和第二钢架2固定连接,用于带动伸缩模块相对地面做升降运动。
[0059]
具体的,升降模块5为伞齿轮丝杠升降机,伞齿轮丝杠升降机的丝杠与第一钢架1或第二钢架2通过螺纹连接,通过丝杠的旋转,带动第一钢架1和第二钢架2的升降。
[0060]
为保证多个升降模块5升降运动的一致性,从而提高船舶舱室单元抬升的平稳性,各伞齿轮升降机之间通过传动杆连接,从而实现各伞齿轮升降机的丝杠旋转的一致性,实现多个升降模块5的联动升降,使第一钢架1和第二钢架2可以基本保持水平的做升降运动。
[0061]
伞齿轮丝杠升降机的驱动机构可以采用手摇把柄或电机。单个伞齿轮丝杠升降机的主尺寸高度为170mm
×
125mm
×
100mm,最小承载为500kg。丝杠的长度不小于400mm,丝杠的直径不小于30mm。
[0062]
在装载模块的左右两侧还分别设置一沿竖向布置的限位杆15,防止升降模块5发生转动。
[0063]
图1中的撑脚组件b如图2和图3所示,底座安装板12的底面设置呈交叉布置的第一加强筋13和第二加强筋14,用以增强底座安装板12的强度,提高安全性。
[0064]
在更优选的实施方式中,伸缩模块和承载模块中的各钢板、钢管需要焊接的位置均采用焊接连接的方式,焊缝均需满焊,在有钢板时,焊脚高度通常为较薄板厚度的0.7倍。
[0065]
在更优选的实施方式中,脚轮11的材质可以采用粘合包橡胶或聚氨酯。脚轮11的轮外径可以为100mm,轮宽可以为50mm,安装高度可以为145mm,轮轴采用滚柱型轴承,使单个脚轮11的承载力不小于200kg。
[0066]
在更优选的实施方式中,脚轮11可以采用万向轮,在遇到弯道或直角通道时,可以
从侧向推送运输车。
[0067]
在使用时,首先使用撬棍将船舶舱室单元的底部撬起一定高度;拉出第一钢架1或第二钢架2,使伸缩模块变长,从而使撑脚10伸进船舶舱室单元的底部,然后拧紧固定螺栓3,固定伸缩模块的长度。可以通过升降模块5来实现装载模块的升降,从而实现船舶舱室单元的升降。在经过局部路面较窄的运输通道时,可以将装载模块升起,两侧脚轮11的间距不超过2300mm,远小于运输车的宽度,从而可以保障运输车能顺利通过绝大多数运输通道。
[0068]
以上所述仅为本技术的优选实施例而已,并不用于限制本技术,对于本领域的技术人员来说,本技术可以有各种更改和变化。凡在本技术的精神和原则之内,所作的任何修改、等同替换、改进等,均应包含在本技术的保护范围之内。