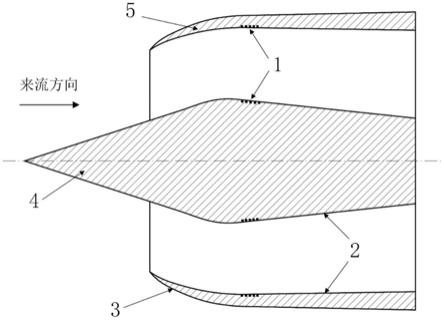
1.本实用新型涉及进气道强制转捩领域,尤其涉及一种基于宏观孔隙结构的高超声速进气道强制转捩装置。
背景技术:
2.飞机进气道作为动力系统的组成部分,主要作用是供给发动机一定流量的空气,并保证进气流场能满足压气机和燃烧室正常工作的要求。相关飞行试验表明,吸气式高超声速飞行器进气道压缩面边界层通常为层流状态,无法保证进气道按预期设计状态工作。因此,通常在进气道前体压缩面安装强制转捩装置来获得湍流,以确保发动机的正常工作。
3.目前应用较为广泛的有钻石形和后掠斜坡形强制转捩方法。研究发现,这两种转捩方法能够在边界层内诱导产生一系列沿流向运动的涡对,进而快速触发边界层转捩,这类强制转捩方法已广泛应用于高超声速飞行器中,如x-43a、x-51a和hifire等。
4.现阶段使用于高超声速飞行器的钻石型和后掠斜坡形强制转捩方法均为外凸形,在实际加工时需要切除的多余材料较多,不仅会浪费材料也会使得加工时间长,其中后掠斜坡形转捩装置为不规则的五面体形状,实际加工困难。此外,凸出的外形会使得流道面积有所减小,导致发动机的进气量减少,降低发动机的推力。
技术实现要素:
5.本实用新型的目的在于解决现有技术中的上述问题,提供一种基于宏观孔隙结构的高超声速进气道强制转捩装置,所述宏观孔隙结构由多排转捩单元沿着进气道的流向方向前后排列组成。
6.为达到上述目的,本实用新型采用如下技术方案:
7.所述转捩单元由多个立方体凹腔单元呈直线分布于材料表面而形成,前后排凹腔的相对位置为交错分布形式。
8.所述材料可以为金属材料,也可以为编织复合材料。该材料能承受飞行器与空气相互摩擦产生的热量而不发生变形并且易于在其表面加工出凹腔结构,若为编织复合材料,则应易于在其表面编织出凹腔结构。
9.所述立方体凹腔的尺寸由三个值决定,分别为:长度a、宽度d和深度h,a、d和h的取值均介于1mm~2mm之间。
10.所述交错分布形式由三个值决定,分别为:同一排相邻凹腔之间的展向距离u、前后相邻两排凹腔之间流向距离v和前后相邻凹腔之间的偏置距离w。u和v的取值均为1mm~2mm,w的取值为具体尺寸根据实际需求与试验结果,综合考虑转捩效果、转捩位置、热防护、结构强度和加工制造等因素选取。
11.一种基于宏观孔隙结构的进气道强制转捩方法,实现步骤如下:
12.1、确定宏观孔隙的结构尺寸,即所述宏观孔隙结构凹腔单元的a、d、h、u、v和w六个
值。
13.(1)先确定凹腔单元的长度a、宽度d和深度h三个尺寸;
14.精确设计a、d及h的值,可通过数值模拟或者试验得到的结果对其进行修正,数值模拟可以由γ-reθt模型得出的间歇因子γ的值来反映凹腔单元的转捩效果,在流经相同长度后,γ值的变化量越大则转捩效果越好。由上述条件确定在设计工况下满足转捩效果的凹腔尺寸。
15.(2)确定同一排相邻凹腔间的展向距离u;
16.凹腔之间的展向距离u取值不应大于凹腔单元的宽度d,以确保流动方向上所有层流都能得到转捩,并且基于当前的加工工艺及制造水平尽量取较小值。在确定宽度d和展向距离u后,便可以得到前后两个凹腔间的偏置距离
17.(3)确定相邻前后两排凹腔之间的流向距离v;
18.流向距离v尽量选取较小值,最大不得超过凹腔单元的长度a,并根据实际转捩效果和加工水平选取。
19.2、确定宏观孔隙结构在进气道表面沿流向的安装位置。
20.宏观孔隙结构中的凹腔的安装位置应同时满足以下条件:
21.(1)强制转捩装置布置在表面光滑平坦的区域。宏观孔隙结构要获得较好的转捩效果,布置的凹腔排数必须达到一定的量,建议沿流向凹腔长度范围最小值应大于5个扰动波长范围。扰动波长的计算方法采用基于流场当地变量的γ-reθt转捩模型,通过对进气道进行数值仿真进行确定。
22.(2)最后一排凹腔与进气道出口位置之间应当保持足够的距离,即需保证沿流向凹腔长度应在最大值以下。凹腔长度最大值的确定方法如下:在最不容易发生转捩的状态(最不容易发生转捩的状态根据飞行马赫数、飞行高度、攻角以及壁温来确定),根据γ-reθt转捩模型仿真得到间歇因子γ值,当进气道出口处边界层内全部由高γ值(大于0.95)主导时,则表示转捩过程完成,此时γ=0.95的流向位置即为凹腔长度最大值点。
23.(3)凹腔安装方向应与来流方向垂直:在与来流垂直的方向安装宏观孔隙结构,能使后方流场均匀分布,也便于宏观孔隙结构的加工。
24.3、确定宏观孔隙结构沿进气道展向的长度和凹腔单元排数。
25.以二元进气道为例,建议沿进气道展向全部布置宏观孔隙结构,沿流向的凹腔排数量亦可由流向距离v、凹腔单元的长度a进行确定。凹腔排数量越多则总体转捩效果越好,但应结合空间结构适当选取凹腔排的数量。
26.相对于现有技术,本实用新型技术方案取得的有益效果是:
27.本实用新型提出一种基于宏观孔隙结构的高超声速进气道强制转捩装置,相比于现有的钻石形和后掠斜坡形转捩装置的外凸形状,宏观孔隙结构为内凹形状,隐藏于进气道内壁的内部,这种形式的转捩装置不会改变流道的流通面积,其在提前触发转捩的同时也能保证发动机进气的流量不因转捩装置的存在而减小。此外,由于本实用新型加工简单,只需在进气道的内壁加工出若干排的沉头孔即可,其具有流动损失小、转捩效果好等优点。
附图说明
28.图1为宏观孔隙结构凹腔单元的结构示意图。
29.图2为宏观孔隙结构凹腔单元在所安装表面的分布示意图。
30.图3为宏观孔隙结构在边界层内,由数值模拟得出的间歇因子γ沿流向随着流经长度的变化。
31.图4为本实施例所应用的高超声速进气道的示意图。
32.图5为宏观孔隙结构在进气道的安装位置轴测示意图(局部)。
33.图6为宏观孔隙结构在进气道的安装位置右视示意图(局部)。
34.图1~6中,各标记表示:
35.a.凹腔单元的长度;d.凹腔单元的宽度;h.凹腔单元的深度;u.同一排相邻凹腔之间的展向距离;v.前后相邻两排凹腔之间流向距离;w.前后相邻凹腔之间的偏置距离;1.宏观孔隙结构的凹腔单元;2.高超声速进气道的内壁面;3.高超声速进气道的外壁面;4.中心锥;5.进气道机匣;γ.由γ-reθt模型得出的间歇因子;l/a.斜板表面的点距斜板最前端的长度l与凹腔单元长度a之比。
具体实施方式
36.为了使本实用新型所要解决的技术问题、技术方案及有益效果更加清楚、明白,以下结合附图和实施例,对本实用新型做进一步详细说明。
37.参见图1~6,本实施例所述一种基于宏观孔隙结构的高超声速进气道强制转捩装置,由宏观孔隙结构的凹腔单元作为触发转捩的基本单元沿着流向方向前后排列组成,布置于进气道表面光滑平坦的区域;凹腔单元呈直线分布于材料表面而形成,前后排凹腔的相对位置为交错分布形式。
38.本实施例装置的具体实施方式包括:
39.1、结合实际需求和数值仿真得到的结果,将凹腔单元1设计为长度a、宽度d和深度h均为2mm的立方体结构。
40.2、根据实际安装位置的空间大小,选定凹腔排数量和宏观孔隙结构的分布形式。在本实施例中,同一排相邻凹腔之间的展向距离u为2mm,前后相邻两排凹腔之间流向距离v为1mm,前后相邻凹腔单元之间的偏置距离由可知为2mm,凹腔排数量为5排。
41.3、在高超声速进气道表面选定安装的位置,高超声速进气道表面包括高超声速进气道的内壁面2和高超声速进气道的外壁面3。在高超声速进气道的内壁面2安装宏观孔隙结构,该安装的局部区域可以简化为斜板,其简化后的轴测图如图5所示,右视图如图6所示。在本实施例中,将宏观孔隙结构安装在距进气道入口60mm处,即图3中l/a=30处,l/a表示斜板表面的点距斜板最前端的长度l与凹腔单元长度a之比,该无量纲数表征气流流过的距离。由图3可得,气流在流经宏观孔隙结构所处区域(30《l/a《42)时,γ值(γ-reθt模型得出的间歇因子)出现大幅增加,由约0.03增大至0.23,增量为0.2。当气流位于l/a》120的位置后,γ值已经大于0.95,可以认为在l/a=120处转捩已经完成。由图3可以得出结论,宏观孔隙结构的安装位置后端与进气道出口位置之间的距离不小于156mm时,可使气流在经强制转捩后满足后方部件对流场的要求。
42.4、在所选部件表面加工出宏观孔隙结构。本实施例中,所应用的高超声速进气道外形如图4所示,在中心锥4的表面和进气道机匣5的内表面安装宏观孔隙结构。共5排凹腔单元交错分布形成宏观孔隙结构,凹腔单元底部与高超声速进气道的内壁面平行。由于该宏观孔隙结构制作在高超声速进气道的内壁面,对流经进气道的气流起到强制转捩的效果。
43.在实际应用情况下,应当根据强制转捩装置与进气道出口位置之间的最小距离和高超声速进气道的结构安装空间决定强制转捩装置在高超声速进气道的内壁面的安装范围。安装方式可通过铆接等将预先制作好的宏观孔隙结构板安装于高超声速进气道的内壁面,也可直接在进气道主体上加工出凹腔单元。在加工凹腔单元的直角结构时,基于现有的加工技术,可适当对直角部分进行倒圆角处理。