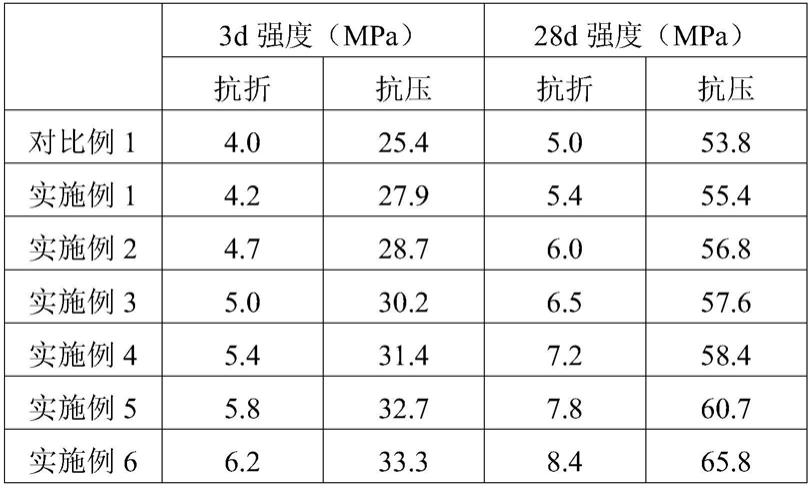
1.本发明涉及水泥建材领域,尤其涉及一种环保型高强度水泥及其制备方法。
背景技术:
2.水泥是一种粉状水硬性无机胶凝材料,加水搅拌后成浆体,能在空气中硬化或者在水中硬化,并能把砂、石等材料牢固地胶结在一起。水泥工业作为传统产业,是资源、能源消耗大户和碳排放大户,特别是我国正处于基础建设的高峰期,水泥产量和需求量巨大且逐年增长。
3.工业废渣是在钢铁和冶金等工业中产生的工业废弃物,工业废渣中含有许多金属、过渡金属以及非金属元素,如钙、镁、铝、硅、铁、铜、锰等,大量工业废渣不仅占用土地、污染环境,同时也是一种巨大的资源浪费。各种工业废弃物可用作辅助性胶凝材料生产复合水泥,是水泥工业发展的重要方向之一。
4.从混凝土角度来看,随着社会的发展,建筑工程对混凝土强度等级的要求越来越高,水泥作为混凝土中提供胶凝性的主要材料,其强度等级对混凝土的强度、配制成本及耐久性能均有着非常重要的影响。水泥胶砂强度越高,配制混凝土的水泥浆体强度越高,水泥浆体与集料的粘结力越大,混凝土强度就会越高。
5.但是目前工业废弃物在水泥中的利用效率不高,并且各种工业废弃物的结合会导致水泥出现分子不稳固性,导致制作的水泥存在强度不高、抗渗能力差等问题,无法作为高品质水泥使用。
6.中国专利cn 108083660 a公开了页岩气油钻屑水泥熟料、其生产的下料装置及水泥,该水泥熟料的生料干基按质量百分比计,包括:页岩气油基钻屑3.0~12.0%,以及余量的主料,主料按质量百分比计,包括:石灰石84.0~86.0%、砂岩3.0~5.0%、页岩0.5~4.5%、赤泥0.5~1.5%。水泥包括脱硫石膏及该水泥熟料;该发明充分利用了页岩气油基钻屑的潜在价值,实现了对采矿业废渣的循环再利用。但是该发明掺入页岩气油基钻屑太高会引起水泥强度的下降。
7.中国专利cn 1398812 a公开了一种环保水泥及其制作方法,该发明人采用电气石、医王石、贵宝石为主料制成的对人体有益的绿色环保水泥,这种水泥能够增强抗压性,水泥中有害物质被清除,能发出红外线负离子,对人体有益,但是这三种具有保健功效的石料对水泥性能的提升没起作用,同时这三种石料均不是常规石料,成本较高,不适合工业化大生产。
技术实现要素:
8.有鉴于现有技术的上述缺陷,本发明所要解决的技术问题是:(1)回收工业废弃物制备环保水泥;(2)解决工业废弃物掺入引起的水泥强度不够的问题。
9.为实现上述目的,本发明提供了一种环保型高强度水泥及其制备方法,该方法采用油基泥浆钻屑、电炉渣、粉煤灰、铜渣、赤泥等工业废弃物合理的搭配石灰石、页岩、二水
石膏作为生产水泥的主要原料,制得的水泥具有良好的安定性且强度能作为高品质水泥使用。
10.为了实现上述发明目的,本发明采用了如下的技术方案:
11.一种环保型高强度水泥的制备方法,包括如下步骤,以重量份计:
12.s1生料的破碎:称取10-30份油基泥浆钻屑、80-100份石灰石、10-20份铜渣、1-5份页岩、1-5份赤泥分别进行破碎、混合均匀得破碎后的生料;
13.s2生料的研磨:向s1步骤制得的破碎后的生料中加入助磨剂进行细磨,混合均匀得细磨后的生料;
14.s3熟料的制备:将步骤s2制得的细磨后的生料与水、助烧剂搅拌均匀压制成试饼,试饼烘干后煅烧,冷却,得熟料;
15.s4水泥的制备:将步骤s3制得的熟料与20-40份电炉渣、20-40份粉煤灰、二水石膏、增强剂进行破碎后粉磨混合均匀得环保型高强度水泥。
16.所述助磨剂为硅酸盐水泥助磨剂;优选为三聚甘油单月桂酸酯、三聚甘油单硬酸酯、n,n-二甲基甲酰胺中的一种或两种及两种以上的混合;进一步优选的,所述助磨剂为三聚甘油单月桂酸酯,添加量为破碎后的生料质量的0.03-1%。本发明添加的助磨剂质量稳定,效果显著,能够降低水泥筛余,避免颗粒的过粉磨,即可提高粉磨效率,降低粉磨能耗,又可促进硅酸盐矿物的水化,提高水泥的活性,有利于水泥后期强度的提高。
17.所述助烧剂为二磷酸四钠和/或木质素磺酸钠。优选的,所述助烧剂为二磷酸四钠和木质素磺酸钠的混合物,两者质量比为2-3:3-5。所述助烧剂的添加量为细磨后的生料质量的0.1-0.5%。
18.发明人发现,通过加入助烧剂二磷酸四钠和木质素磺酸钠的混合物,降低了生料的反应活化能,强化了fe2o3、sio2、cao、al2o3的反应能力,高温下反应能力增强的fe2o3、sio2、cao、al2o3能吸收燃烧过程中产生的二氧化硫、氮氧化物等污染气体,减少了二氧化硫、氮氧化物等污染气体的排放,减少了环境污染,同时降低了水泥熟料中游离的氧化钙的含量。
19.所述步骤s1中破碎为将原料破碎至平均尺寸小于2~3mm;
20.所述步骤s2中生料细磨后细度保持在80μm筛余为10~15%,200μm筛余小于1~1.5%;
21.所述步骤s3中生料与水的质量比为1:10~20;所述煅烧步骤为设置升降炉0℃~950℃区间段的升温速率为5~10℃/min,950℃保温30~60min,950~1300℃区间段的升温速率为3~5℃/min,1300℃保温时间为10~20min,煅烧结束。
22.所述步骤s4中二水石膏的质量为熟料质量的2~5%;粉磨后的水泥细度保持在80μm筛余为小于5~10%。
23.所述增强剂为水苏糖和/或三乙胺,添加量为熟料质量的0.01-0.05%;
24.优选的,所述增强剂为质量比为1:2-3的水苏糖和三乙胺的混合物。
25.发明人发现,使用增强剂水苏糖和三乙胺的混合物提高了水泥熟料的助磨性,在水泥表面形成水化点,从而促进钙矾石的形成,加快了水在水泥颗粒内部的渗透,促进了水泥熟料矿物相的水解,改变了水泥的颗粒分布,增大了水泥均匀性系数,形成相对均匀密实的结构,从而增强了水泥的强度,作为高品质水泥使用。
26.本发明中部分原材料的说明如下:
27.(1)油基泥浆钻屑
28.油基泥浆钻屑属于含油污泥的一种,是一种难以处理的残渣,主要特征是一种油包水的结构,其主要矿物为白云石、石英和硫酸钡,其中硫酸钡含量较高;泥浆部分含有多种有机物,主要以长链烃为主,主要碳链长度为11-28,在水泥体系中起矿化剂的作用。本发明所用油基泥浆钻屑来自四川省东南部,油基泥浆钻屑的含水率为15%
±
2%,含油率为20%
±
1%,放射性ira=0.194≤1.0;ir=0.114≤1.3,满足gb6566-2001《室内装饰装修材料建筑材料放射性核素限量》的要求。
29.(2)石灰石
30.石灰石的主要成分为碳酸钙,在高温下分解成氧化钙和二氧化碳,磨细的石灰石粉可以加速硅酸盐水泥水化,改善水泥基材料孔结构和硬化水泥浆体界面,从而提高基体强度。
31.(3)电炉渣
32.电炉渣是采用电炉冶炼金属的过程中排出的固体废物,主要成分是钙、铁、铜、硅、镁、铝、锰、磷等氧化物,在适当条件下可获得较好的胶凝活性,可作为水泥等辅助性胶凝材料,电炉渣的掺入不会降低复合水泥的后期强度,还可显著改善水泥浆体的微观结构、提高水泥的耐久性。
33.(4)粉煤灰
34.粉煤灰又称飞灰或烟灰,是煤粉在高温中燃烧、冷却而形成。大部分呈球状,表面光滑,微孔较小,含有大量硅、铁、铝、钙、镁、钠、钾、硫的氧化物以及各种微量元素,属于火山灰性质的混合材料,具有潜在的化学活性,粉煤灰单独与水拌合不具有水硬活性,但在有ca(oh)2存在的条件下,能够与水反应生产类似于水泥胶凝体的胶凝物质,并具有一定的强度,在水泥生产中因和粘土的化学组成具有相似性,除了作为生产水泥的添加剂外,还能代替粘土作为生产硅酸盐水泥的熟料,降低水泥生产中的电耗能和碳排放,提高水泥的掺量,降低生产成本。
35.(5)铜渣
36.铜渣是炼铜过程中产生的渣,属有色金属渣的一种,含有fe、cu、zn、pb、co、ni等多种有价金属和少量贵金属。在水泥制造中可以替代铁粉作矿化剂,作铁质校正剂生产硅酸盐水泥水泥。
37.(6)页岩
38.页岩是由黏土物质硬化形成的微小颗粒易裂碎,很容易分裂成为明显的岩层,以黏土类矿物(高岭石、水云母等)为主,其化学成分sio2含量为45%~80%,al2o3含量为12%~25%,fe2o3含量为2%~10%,cao含量为0.2%~12%。
39.(7)赤泥
40.赤泥是制铝工业提取氧化铝时排出的工业固体废弃物,隐含氧化铁量大,外观与赤色泥土相似,故被称为赤泥,主要成分为sio2、al2o3、cao、fe2o3等。
41.(8)二水石膏
42.二水石膏,即生石膏,是硫酸钙的二水合物,是水泥的重要组成材料,不仅可以起到缓凝作用,还作为提高水泥活性的硫酸盐激发剂,同时水泥中so3含量的多少可以直接影
响水泥的强度。
43.与现有技术相比,本发明的有益效果:
44.1、在生料煅烧过程中加入特种比例的助烧剂,降低了生料的反应活化能,强化了生料煅烧过程中产生的fe2o3、sio2、cao、al2o3的反应能力,高温下反应能力增强的fe2o3、sio2、cao、al2o3能吸收燃烧过程中产生的二氧化硫、氮氧化物等污染气体,减少了二氧化硫、氮氧化物等污染气体的排放,减少了环境污染,同时降低了水泥熟料中游离的cao的含量。
45.2、在水泥制备过程中使用增强剂水苏糖和三乙胺的混合物提高了水泥熟料的分散性,在水泥表面形成水化点,从而促进钙矾石的形成,加快了水在水泥颗粒内部的渗透,促进了水泥熟料矿物相的水解,改变了水泥的颗粒分布,增大了水泥均匀性系数,形成相对均匀密实的结构,从而增强了水泥的强度,达到了工程施工所需要的强度。
46.3、本发明制备的水泥具有良好的安定性,且利用了大量的工业废料,减少了对环境的污染,降低了水泥生产的成本。
具体实施方式
47.下面通过实施例的方式进一步说明本发明,但并不因此将本发明限制在所述的实施例范围之中。下列实施例中未注明具体条件的实验方法,按照常规方法和条件,或按照商品说明书选择。
48.本发明对照例及实施例中部分原材料参数如下:
49.油基泥浆钻屑,来自泸州阳10h-40钻井平台取得的油基泥浆钻屑。
50.石灰石:购买自南召县青山建材有限公司,caco3含量为95%,含钙量为53.73%,含镁量为2.0%,含铁量为0.56%,堆密度为32.8g/cm3,颜色为灰色,大小为1-3cm。
51.铜渣:主要化学组成为sio2含量为27.59%,cao含量为5.26%,mgo含量为2.2%,al2o3含量为5.26%,fe2o3含量为59.16%。
52.页岩:购买自石家庄飞吉矿产品有限公司,外观为片状,品级为一级,货号为078。
53.赤泥:购买灵寿亿鑫矿产品加工厂,为粉末状,货号为h858558,品级为一级。
54.电炉渣:烧失量为1.04%,sio2含量为20.67%,al2o3含量为6.35%,fe2o3含量为38.97%,cao含量为23.87%,mgo含量为4.47%。
55.粉煤灰为ii级粉煤灰,购买自武汉阳逻电厂,比表面积449m2/kg。
56.二水石膏,购买自贺州市福众建材有限公司,抗折强度为2.35mpa,标准稠度为95.23%,膨胀系数为6.3,初凝时间3.45分,终凝时间为59.36分。
57.对比例1
58.一种环保型高强度水泥的制备方法,包括如下步骤:
59.s1生料的破碎:称取20g油基泥浆钻屑、100g石灰石、10g铜渣、5g页岩、5g赤泥分别用鄂式破碎机进行破碎,混合均匀得破碎后的生料,生料破碎后的平均尺寸为1.5mm以下;
60.s2生料的研磨:向s1步骤制得的破碎后的生料中加入7g三聚甘油单月桂酸酯进行细磨,混合均匀得细磨后的生料,生料细磨后的细度保持在80μm筛余为10%,200μm筛余为1%以下;
61.s3熟料的制备:将步骤s2制得的细磨后的生料与1500g水搅拌后加入到压片模具
中,使用tye-300型压力试验机以11kn的力保载10s得试饼,将试饼置于80℃干燥箱中干燥10h后将其置于sjf-1600升降炉中煅烧,设置升降0℃~950℃区间段的升温速率为10℃/min,950℃保温30min,950~1300℃区间段的升温速率为5℃/min,1300℃保温时间为10min,煅烧结束;熟料冷却至30℃,得熟料;
62.s4水泥的制备:将步骤s3制得的熟料与20g电炉渣、30g粉煤灰、二水石膏进行破碎后粉磨混合均匀得环保型高强度水泥;所述二水石膏的添加量为熟料质量的2.5%。
63.实施例1
64.一种环保型高强度水泥的制备方法,包括如下步骤:
65.s1生料的破碎:称取20g油基泥浆钻屑、100g石灰石、10g铜渣、5g页岩、5g赤泥分别用鄂式破碎机进行破碎,混合均匀得破碎后的生料,生料破碎后的平均尺寸为1.5mm以下;
66.s2生料的研磨:向s1步骤制得的破碎后的生料中加入7g三聚甘油单月桂酸酯进行细磨,混合均匀得细磨后的生料,生料细磨后的细度保持在80μm筛余为10%,200μm筛余为1%以下;
67.s3熟料的制备:将步骤s2制得的细磨后的生料与1500g水、助烧剂搅拌后加入到压片模具中,使用tye-300型压力试验机以11kn的力保载10s得试饼,将试饼置于80℃干燥箱中干燥10h后将其置于sjf-1600升降炉中煅烧,设置升降0℃~950℃区间段的升温速率为10℃/min,950℃保温30min,950~1300℃区间段的升温速率为5℃/min,1300℃保温时间为10min,煅烧结束;熟料冷却至30℃,得熟料;所述助烧剂为二磷酸四钠,添加量为细磨后的生料质量的0.5%。
68.s4水泥的制备:将步骤s3制得的熟料与20g电炉渣、30g粉煤灰、二水石膏进行破碎后粉磨混合均匀得环保型高强度水泥;所述二水石膏的添加量为熟料质量的2.5%。
69.实施例2
70.一种环保型高强度水泥的制备方法,包括如下步骤:
71.s1生料的破碎:称取20g油基泥浆钻屑、100g石灰石、10g铜渣、5g页岩、5g赤泥分别用鄂式破碎机进行破碎,混合均匀得破碎后的生料,生料破碎后的平均尺寸为1.5mm以下;
72.s2生料的研磨:向s1步骤制得的破碎后的生料中加入7g三聚甘油单月桂酸酯进行细磨,混合均匀得细磨后的生料,生料细磨后的细度保持在80μm筛余为10%,200μm筛余为1%以下;
73.s3熟料的制备:将步骤s2制得的细磨后的生料与1500g水、助烧剂搅拌后加入到压片模具中,使用tye-300型压力试验机以11kn的力保载10s得试饼,将试饼置于80℃干燥箱中干燥10h后将其置于sjf-1600升降炉中煅烧,设置升降0℃~950℃区间段的升温速率为10℃/min,950℃保温30min,950~1300℃区间段的升温速率为5℃/min,1300℃保温时间为10min,煅烧结束;熟料冷却至30℃,得熟料;所述助烧剂为木质素磺酸钠,添加量为细磨后的生料质量的0.5%。
74.s4水泥的制备:将步骤s3制得的熟料与20g电炉渣、30g粉煤灰、二水石膏进行破碎后粉磨混合均匀得环保型高强度水泥;所述二水石膏的添加量为熟料质量的2.5%。
75.实施例3
76.一种环保型高强度水泥的制备方法,包括如下步骤:
77.s1生料的破碎:称取20g油基泥浆钻屑、100g石灰石、10g铜渣、5g页岩、5g赤泥分别
用鄂式破碎机进行破碎,混合均匀得破碎后的生料,生料破碎后的平均尺寸为1.5mm以下;
78.s2生料的研磨:向s1步骤制得的破碎后的生料中加入7g三聚甘油单月桂酸酯进行细磨,混合均匀得细磨后的生料,生料细磨后的细度保持在80μm筛余为10%,200μm筛余为1%以下;
79.s3熟料的制备:将步骤s2制得的细磨后的生料与1500g水、助烧剂搅拌后加入到压片模具中,使用tye-300型压力试验机以11kn的力保载10s得试饼,将试饼置于80℃干燥箱中干燥10h后将其置于sjf-1600升降炉中煅烧,设置升降0℃~950℃区间段的升温速率为10℃/min,950℃保温30min,950~1300℃区间段的升温速率为5℃/min,1300℃保温时间为10min,煅烧结束;熟料冷却至30℃,得熟料;所述助烧剂为质量比为2:3的二磷酸四钠和木质素磺酸钠混合物,添加量为细磨后的生料质量的0.5%。
80.s4水泥的制备:将步骤s3制得的熟料与20g电炉渣、30g粉煤灰、二水石膏进行破碎后粉磨混合均匀得环保型高强度水泥;所述二水石膏的添加量为熟料质量的2.5%。
81.测试例1
82.水泥熟料游离氧化钙(f
cao
)的测定:依据gb/t176-2008《水泥化学成分分析》中乙二醇法,通过游离氧化钙测定仪,用苯甲酸-无水乙醇标准滴定溶液滴定,对对比例1、实施例1-3制备的水泥熟料样品进行游离氧化钙含量的测定。测试结果如表1所示:
83.表1:水泥熟料游离氧化钙的测定
[0084] 游离氧化钙(f
cao
)含量(%)对比例11.96实施例10.82实施例20.78实施例30.64
[0085]
游离氧化钙是衡量水泥质量的一个重要指标,其含量会直接影响水泥熟料的安定性,进而影响水泥的安定性,一般立窑生产的水泥熟料中游离氧化钙的含量≤1.0%才算合格。从以上结果可以看出,加入助烧剂后制得的水泥熟料安定性均在合格范围内。
[0086]
实施例4
[0087]
一种环保型高强度水泥的制备方法,包括如下步骤:
[0088]
s1生料的破碎:称取20g油基泥浆钻屑、100g石灰石、10g铜渣、5g页岩、5g赤泥分别用鄂式破碎机进行破碎,混合均匀得破碎后的生料,生料破碎后的平均尺寸为1.5mm以下;
[0089]
s2生料的研磨:向s1步骤制得的破碎后的生料中加入7g三聚甘油单月桂酸酯进行细磨,混合均匀得细磨后的生料,生料细磨后的细度保持在80μm筛余为10%,200μm筛余为1%以下;
[0090]
s3熟料的制备:将步骤s2制得的细磨后的生料与1500g水、助烧剂搅拌后加入到压片模具中,使用tye-300型压力试验机以11kn的力保载10s得试饼,将试饼置于80℃干燥箱中干燥10h后将其置于sjf-1600升降炉中煅烧,设置升降0℃~950℃区间段的升温速率为10℃/min,950℃保温30min,950~1300℃区间段的升温速率为5℃/min,1300℃保温时间为10min,煅烧结束;熟料冷却至30℃,得熟料;所述助烧剂为质量比为2:3的二磷酸四钠和木质素磺酸钠混合物,添加量为细磨后的生料质量的0.5%。
[0091]
s4水泥的制备:将步骤s3制得的熟料与20g电炉渣、30g粉煤灰、二水石膏、增强剂
进行破碎后粉磨混合均匀得环保型高强度水泥;所述二水石膏的添加量为熟料质量的2.5%;所述增强剂为水苏糖,添加量为熟料质量的0.03%。
[0092]
实施例5
[0093]
一种环保型高强度水泥的制备方法,包括如下步骤:
[0094]
s1生料的破碎:称取20g油基泥浆钻屑、100g石灰石、10g铜渣、5g页岩、5g赤泥分别用鄂式破碎机进行破碎,混合均匀得破碎后的生料,生料破碎后的平均尺寸为1.5mm以下;
[0095]
s2生料的研磨:向s1步骤制得的破碎后的生料中加入7g三聚甘油单月桂酸酯进行细磨,混合均匀得细磨后的生料,生料细磨后的细度保持在80μm筛余为10%,200μm筛余为1%以下;
[0096]
s3熟料的制备:将步骤s2制得的细磨后的生料与1500g水、助烧剂搅拌后加入到压片模具中,使用tye-300型压力试验机以11kn的力保载10s得试饼,将试饼置于80℃干燥箱中干燥10h后将其置于sjf-1600升降炉中煅烧,设置升降0℃~950℃区间段的升温速率为10℃/min,950℃保温30min,950~1300℃区间段的升温速率为5℃/min,1300℃保温时间为10min,煅烧结束;熟料冷却至30℃,得熟料;所述助烧剂为质量比为2:3的二磷酸四钠和木质素磺酸钠混合物,添加量为细磨后的生料质量的0.5%。
[0097]
s4水泥的制备:将步骤s3制得的熟料与20g电炉渣、30g粉煤灰、二水石膏、增强剂进行破碎后粉磨混合均匀得环保型高强度水泥;所述二水石膏的添加量为熟料质量的2.5%;所述增强剂为三乙胺,添加量为熟料质量的0.03%。
[0098]
实施例6
[0099]
一种环保型高强度水泥的制备方法,包括如下步骤:
[0100]
s1生料的破碎:称取20g油基泥浆钻屑、100g石灰石、10g铜渣、5g页岩、5g赤泥分别用鄂式破碎机进行破碎,混合均匀得破碎后的生料,生料破碎后的平均尺寸为1.5mm以下;
[0101]
s2生料的研磨:向s1步骤制得的破碎后的生料中加入7g三聚甘油单月桂酸酯进行细磨,混合均匀得细磨后的生料,生料细磨后的细度保持在80μm筛余为10%,200μm筛余为1%以下;
[0102]
s3熟料的制备:将步骤s2制得的细磨后的生料与1500g水、助烧剂搅拌后加入到压片模具中,使用tye-300型压力试验机以11kn的力保载10s得试饼,将试饼置于80℃干燥箱中干燥10h后将其置于sjf-1600升降炉中煅烧,设置升降0℃~950℃区间段的升温速率为10℃/min,950℃保温30min,950~1300℃区间段的升温速率为5℃/min,1300℃保温时间为10min,煅烧结束;熟料冷却至30℃,得熟料;所述助烧剂为质量比为2:3的二磷酸四钠和木质素磺酸钠混合物,添加量为细磨后的生料质量的0.5%;
[0103]
s4水泥的制备:将步骤s3制得的熟料与20g电炉渣、30g粉煤灰、二水石膏、增强剂进行破碎后粉磨混合均匀得环保型高强度水泥;所述二水石膏的添加量为熟料质量的2.5%;所述增强剂为质量比为1:2的水苏糖与三乙胺的混合物,添加量为熟料质量的0.03%。
[0104]
测试例2
[0105]
水泥强度测试:胶砂制备按照国标gb/t17671-1999《水泥胶砂强度试验》进行,水泥胶砂成型按照gb/t175-2007《通用硅酸盐水泥》由一份水泥、三份中国iso标准砂,用0.5的水灰比进行配比,成型24h之后拆模放入20
±
1℃水中养护,待测其3d、28d抗折强度、抗压
强度。测试结果如表2所示:
[0106]
表2:水泥胶砂的强度
[0107][0108]
工程中使用高强度等级水泥配制高标号混凝土有利于降低成本和改善混凝土的耐久性,从表2中的数据可以看出,添加了增强剂制备的水泥强度能达到62.5强度等级硅酸盐水泥的强度要求。可能原因是增强剂提高了水泥的分散性和加快了水在水泥颗粒内部的渗透,促进c3s的水化,改变了水泥的颗粒分布,同时延缓了水泥的水化速度,使得水泥颗粒周围溶液的c-s-h等水化产物的分布更加均匀,网架结构更致密,最终使得水泥内部结构更加密实从而提高了水泥的强度。
[0109]
以上详细描述了本发明的较佳具体实施例。应当理解,本领域的普通技术人员无需创造性劳动就可以根据本发明的构思作出诸多修改和变化。因此,凡本技术领域中技术人员依本发明的构思在现有技术的基础上通过逻辑分析、推理或者有限的实验可以得到的技术方案,皆应在由权利要求书所确定的保护范围内。