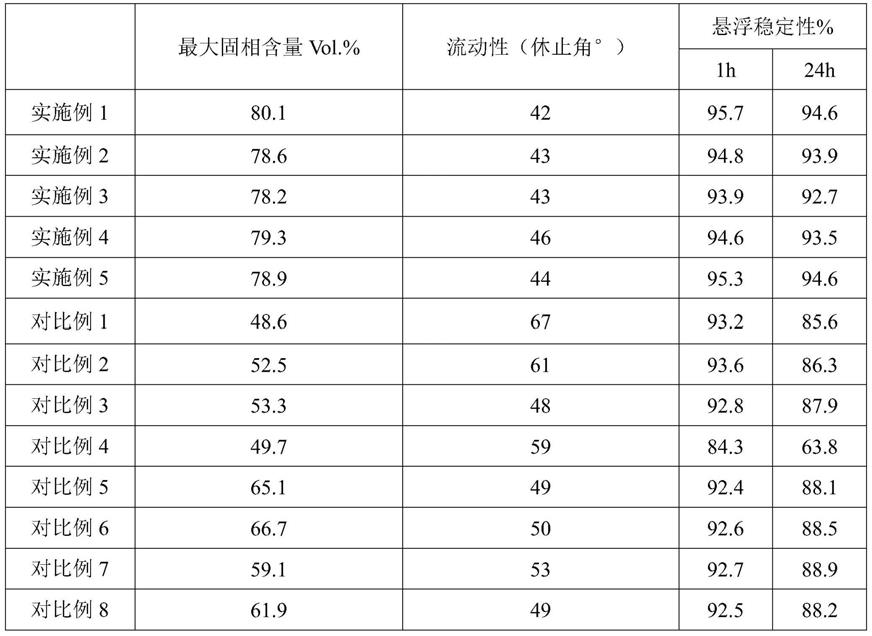
1.本发明涉及陶瓷粉体技术领域,具体的,涉及一种用于注浆注射挤压成型碳化硅陶瓷粉体的制备方法。
背景技术:
2.碳化硅陶瓷是现代国民经济和国防工业所需要的先进功能和结构材料,目前正处于深入研究和广泛应用的发展阶段。
3.目前碳化硅陶瓷生坯的成型方式较多,但一些异型、特异型复杂几何结构或多层超薄超大制件的成型仍以注浆、注射和挤压方法为主。众所周知粉体技术是陶瓷技术的前提,尤其是注浆成型类粉体,要求水基分散时其料浆必须具备极高的固相含量,并在高固含量的基础上兼具高流动性,高分散性,高悬浮稳定性等功能,使制成的生坯不但要有高填充密度,而且坯体内部颗粒分散均匀性好,孔径孔距均匀,只有这样才能最终制得高性能的碳化硅陶瓷制品。目前我国用于注浆类成型的高性能碳化硅陶瓷粉体,在一定程度上还依赖于进口,国内少数厂家虽有生产,但由于和国外产品在功能性方面还存有较大差距,用其所制备的产品体积密度低,只限于在温度较低和技术性能相对要求不高的环境下使用,从而制约了高性能产品生产和发展。
4.本专利旨在针对高性能注浆类成型碳化硅陶瓷粉体进行瓶颈性技术突破,并实现产业化和国产化。
技术实现要素:
5.本发明提出一种用于注浆注射挤压成型碳化硅陶瓷粉体的制备方法,填补了国内高性能碳化硅陶瓷粉体技术的空白,制备得到的碳化硅陶瓷粉体在水基分散时有效流动下的固相含量可达到78%-80%,并兼具高流动性,高分散性,高悬浮稳定性,可用于注浆注射挤压成型工艺,使制备得到的坯体内部颗粒分散均匀性好,孔径孔距均匀。
6.本发明的技术方案如下:
7.一种用于注浆注射挤压成型碳化硅陶瓷粉体的制备方法,包括以下步骤:
8.(1)粗粒度碳化硅预混料的制备:将高粒度碳化硅磨料自磨整形至显微镜下观察呈土豆圆形,得到粗粒度碳化硅预混料,备用;
9.(2)中粒度碳化硅预混料的制备:将中粒度碳化硅磨料自磨整形至显微镜下观察呈土豆圆形,得到中粒度碳化硅预混料,备用;
10.(3)细粒度碳化硅预混料的制备:将碳化硅磨料湿法研磨,得到细粒度碳化硅预混料,备用;
11.(4)粉体高自身密度的级配:向细粒度碳化硅预混料中依次添加粗粒度碳化硅预混料、中粒度碳化硅预混料、水和分散剂,形成浆料,分散后加入硅烷偶联剂,干燥,即得;
12.其中,碳化硅预混料粒度满足以下规定:粗粒度碳化硅预混料>中粒度碳化硅预混料>细粒度碳化硅预混料。
13.进一步地,上述制备方法中,碳化硅磨料采用sic成分含量>98%的绿碳化硅。
14.进一步地,所述步骤(1)和(2)中自磨整形采用气流整形机,在喷嘴前压力力度范围为5.8-6.5mpa下,采用循环的方式将颗粒反复自磨整形。
15.进一步地,所述步骤(1)中粗粒度碳化硅磨料为d50:3-15μm的磨料,整形后得到的粗粒度碳化硅预混料d50减小1.0-2.5μm。
16.进一步地,所述步骤(2)中中粒度碳化硅磨料为d50:1-11.5μm的磨料,整形后得到的中粒度预混料d50减小0.5-1.5μm。
17.进一步地,所述步骤(3)中碳化硅磨料研磨至d50:0.1-3.0μm时停止。
18.进一步地,所述步骤(3)中碳化硅磨料湿法研磨具体采用砂磨机。
19.更进一步地,所述湿法研磨采用的磨砂介质为高纯碳化硅研磨球。
20.更进一步地,所述高纯碳化硅研磨球为本公司专利产品,申请号为201410097403.2中的碳化硅球。
21.进一步地,所述步骤(4)中细粒度碳化硅预混料、粗粒度碳化硅预混料和中粒度碳化硅预混料质量比为:4:1-3:2-7。
22.进一步地,所述步骤(4)中添加水的量为使形成的浆料固相比为50-70%。
23.进一步地,所述步骤(4)中分散剂为聚丙稀酸盐类分散剂,添加量为固体总量的0.5-1.5%。
24.更进一步地,所述步骤(4)中聚丙烯酸盐类分散剂选自聚丙烯酸钠、聚丙烯酸钾、聚丙烯酸铵中的一种或多种。
25.进一步地,所述步骤(4)中加入分散剂分散5-15min后再添加硅烷偶联剂。
26.进一步地,所述步骤(4)中硅烷偶联剂的添加量为浆料中固体总量的1-2%。
27.更进一步地,所述步骤(4)中加入硅烷偶联剂后继续搅拌5-15min后,静置5-15min。
28.进一步地,所述步骤(4)中干燥采用微波干燥,温度60-90℃。
29.更进一步地,所述步骤(4)中进行干燥后再分散15-25min,得到用于注浆注射挤压成型碳化硅陶瓷粉体。
30.本发明还提供上述制备方法制备得到的用于注浆注射挤压成型碳化硅陶瓷粉体。
31.本发明的有益效果为:
32.1、国内注浆注射用碳化硅陶瓷粉体性能与国外产品相差较大,严重限制了高性能产品的生产和发展,本发明的发明人在实际研发过程中经过不断摸索和研究,发现了提高碳化硅陶瓷粉体性能的关键因素在于提高水基分散粉体中的固相含量,而实现这个目标是一个多项措施并举的系统化系统工程,它包括:
33.①
粉体的高纯化,高纯化的超细粉体颗粒表面会一定程度的降低表面能,减少团聚并有利于提高粉体颗粒表面改性的有效性;
34.②
粒度级配的最佳化,实践证明理论上的连续粒度在实现粉体高密度上并不成立,因此需要人为选择不同的较单一粒径的粉体做适合的粒度级配,使粉体形成高密度以达到高填充性;
35.③
粉体颗粒的高球形化,高球形化的粉体颗粒能直接减小颗粒间的接触面提高流动性;
36.④
粉体表面改性,对粉体颗粒表面进行有机化包覆改性,可使颗粒表面产生疏水基团,是实现粉体在水基分散下实现高固相含量的重要条件;
37.只有将上述系统措施都得以充分完善才能制备出适于注浆类成型的高性能粉体。本发明对粗、中粒度的碳化过磨料的整形过程也是对颗粒表面的物理清洗和提纯过程,实现粉体的高纯化和高球形化的要求,即:颗粒表面所附有的杂质将在颗粒表层自冲涮至表层被剥离后实现纯化。另外,整形过程中形成的较小微粒会通过气流分级方式被分离到除尘器内,从而可使两种整形后粉体粒度仍保持窄分布成度。最后,本发明对粗、中、细三种粒度的碳化硅预混料级配进行优化,从而实现高性能注浆注射用碳化硅陶瓷粉体的制备。
38.2、本发明制备方法制备得到的碳化硅陶瓷粉体在水基分散时有效流动下的固相含量可达到78-80vol.%,国外进口同类先进产品水基分散时有效流动下的固相含量为78vol.%,比国外进口同类先进产品水平相当,甚至还有更进一步的潜力,突破了国内对于高性能注浆类成型碳化硅陶瓷粉体的技术瓶颈,打破了进口产品在国内的市场垄断,实现国产化和产业化。
39.3、本发明整个制备过程都是在环境友好下进行,包括改性步骤也是在机械能的作用下有效完成,过程中无任何有毒有害助剂,不仅为国内高性能碳化硅陶瓷粉体的发展奠定基础,同时还为环境保护作出突出贡献。
具体实施方式
40.下面将结合本发明实施例,对本发明实施例中的技术方案进行清楚、完整地描述,显然,所描述的实施例仅仅是本发明一部分实施例,而不是全部的实施例。基于本发明中的实施例,本领域普通技术人员在没有作出创造性劳动前提下所获得的所有其他实施例,都涉及本发明保护的范围。
41.以下实施例1-5中碳化硅磨料均采用sic成分》98%的绿sic。
42.实施例1
43.本实施例制备d50:2μm的注浆注射挤压成型碳化硅陶瓷粉体,包括以下步骤:
44.(1)粗粒度碳化硅预混料的制备:将d50:6.7μm碳化硅磨料采用气流整形机,在喷嘴前压力为6.2mpa下,采用循环的方式将磨料自磨整形至在显微镜下观察呈土豆圆形,得到粗粒度碳化硅预混料(d50:4.5-5.0μm),备用;
45.(2)中粒度碳化硅预混料的制备:将d50:4.0μm碳化硅磨料采用气流整形机,在喷嘴前压力为6.2mpa下,采用循环的方式将磨料自磨整形至在显微镜下观察呈土豆圆形,得到中粒度碳化硅预混料(d50:2.5-3.0μm),备用;
46.(3)细粒度碳化硅预混料的制备:将d50:7.0μm碳化硅磨料采用砂磨机湿法研磨,研磨介质采用申请号为201410097403.2中的碳化硅球,研磨至d50:0.5μm时停止,得到细粒度碳化硅预混料,备用;
47.(4)粉体高自身密度的级配:按照质量比为4:2:5向细粒度碳化硅预混料中依次添加粗粒度碳化硅预混料、中粒度碳化硅预混料和水,形成固相比为60%的浆料,同时按固体含量的1.0%添加聚丙烯酸钠作为分散剂,分散10min后,在料浆处于高分散状态下按固体含量的1.5%加入硅烷偶联剂kh-540,在机械能作用下进行10min的颗粒表面包覆后停止分散,静置10min,得到改性后浆料;
48.(5)将步骤(4)的改性料浆用隔膜泵打入周转容器内,转运至微波干燥器内60℃烘干,得到碳化硅干料;
49.(6)将步骤(5)的干料转入锤形混料机内分散20min,得到d50:2μm的注浆注射挤压成型碳化硅陶瓷粉体。
50.实施例2
51.本实施例制备d50:5μm的注浆注射挤压成型碳化硅陶瓷粉体,包括以下步骤:
52.(1)粗粒度碳化硅预混料的制备:将d50:9.5μm碳化硅磨料采用气流整形机,在喷嘴前压力为5.8mpa下,采用循环的方式将磨料自磨整形至在显微镜下观察呈土豆圆形,得到粗粒度碳化硅预混料(d50:7-8μm),备用;
53.(2)中粒度碳化硅预混料的制备:将d50:3μm碳化硅磨料采用气流整形机,在喷嘴前压力为5.8mpa下,采用循环的方式将磨料自磨整形至在显微镜下观察呈土豆圆形,得到中粒度碳化硅预混料(d50:1.5-2.0μm),备用;
54.(3)细粒度碳化硅预混料的制备:将d50:8.0μm碳化硅磨料采用砂磨机湿法研磨,研磨介质采用申请号为201410097403.2中的碳化硅球,研磨至d50:1μm时停止,得到细粒度碳化硅预混料,备用;
55.(4)粉体高自身密度的级配:按照质量比为4:1:2向细粒度碳化硅预混料中依次添加粗粒度碳化硅预混料、中粒度碳化硅预混料和水,形成固相比为50%的浆料,同时按固体含量的0.5%添加聚丙烯酸铵作为分散剂,分散5min后,在料浆处于高分散状态下按固体含量的1.0%加入硅烷偶联剂kh-562,在机械能作用下进行5min的颗粒表面包覆后停止分散,静置5min,得到改性后浆料;
56.(5)将步骤(4)的改性料浆用隔膜泵打入周转容器内,转运至微波干燥器内90℃烘干,得到碳化硅干料;
57.(6)将步骤(5)的干料转入锤形混料机内分散15min,得到d50:5μm的注浆注射挤压成型碳化硅陶瓷粉体。
58.实施例3
59.本实施例制备d50:10μm的注浆注射挤压成型碳化硅陶瓷粉体,包括以下步骤:
60.(1)粗粒度碳化硅预混料的制备:将d50:15μm碳化硅磨料采用气流整形机,在喷嘴前压力为6.5mpa下,采用循环的方式将磨料自磨整形至在显微镜下观察呈土豆圆形,得到粗粒度碳化硅预混料(d50:12.5-13.5μm),备用;
61.(2)中粒度碳化硅预混料的制备:将d50:11.5μm碳化硅磨料采用气流整形机,在喷嘴前压力为6.2mpa下,采用循环的方式将磨料自磨整形至在显微镜下观察呈土豆圆形,得到中粒度碳化硅预混料(d50:10-10.5μm),备用;
62.(3)细粒度碳化硅预混料的制备:将d50:10μm碳化硅磨料采用砂磨机湿法研磨,研磨介质采用申请号为201410097403.2中的碳化硅球,研磨至d50:3.0μm时停止,得到细粒度碳化硅预混料,备用;
63.(4)粉体高自身密度的级配:按照质量比为4:3:3向细粒度碳化硅预混料中依次添加粗粒度碳化硅预混料、中粒度碳化硅预混料和水,形成固相比为70%的浆料,同时按固体含量的1.5%添加聚丙烯酸钾作为分散剂,分散15min后,在料浆处于高分散状态下按固体含量的1.5%加入硅烷偶联剂a-171,在机械能作用下进行15min的颗粒表面包覆后停止分
散,静置15min,得到改性后浆料;
64.(5)将步骤(4)的改性料浆用隔膜泵打入周转容器内,转运至微波干燥器内75℃烘干,得到碳化硅干料;
65.(6)将步骤(5)的干料转入锤形混料机内分散25min,得到d50:10μm的注浆注射挤压成型碳化硅陶瓷粉体。
66.实施例4
67.本实施例制备d50:1μm的注浆注射挤压成型碳化硅陶瓷粉体,包括以下步骤:
68.(1)粗粒度碳化硅预混料的制备:将d50:5.0μm碳化硅磨料采用气流整形机,在喷嘴前压力为6.0mpa下,采用循环的方式将磨料自磨整形至在显微镜下观察呈土豆圆形,得到粗粒度碳化硅预混料(d50:2.5-3.5μm,),备用;
69.(2)中粒度碳化硅预混料的制备:将d50:2.5μm碳化硅磨料采用气流整形机,在喷嘴前压力为6.0mpa下,采用循环的方式将磨料自磨整形至在显微镜下观察呈土豆圆形,得到中粒度碳化硅预混料(d50:1.0-1.5μm,),备用;
70.(3)细粒度碳化硅预混料的制备:将d50:5μm碳化硅磨料采用砂磨机湿法研磨,研磨介质采用申请号为201410097403.2中的碳化硅球,研磨至d50:0.1μm时停止,得到细粒度碳化硅预混料,备用;
71.(4)粉体高自身密度的级配:按照质量比为4:2:6向细粒度碳化硅预混料中依次添加粗粒度碳化硅预混料、中粒度碳化硅预混料和水,形成固相比为60%的浆料,同时按固体含量的1.0%添加聚丙烯酸钠作为分散剂,分散10min后,在料浆处于高分散状态下按固体含量的2.0%加入硅烷偶联剂kh-540,在机械能作用下进行10min的颗粒表面包覆后停止分散,静置10min,得到改性后浆料;
72.(5)将步骤(4)的改性料浆用隔膜泵打入周转容器内,转运至微波干燥器内80℃烘干,得到碳化硅干料;
73.(6)将步骤(5)的干料转入锤形混料机内分散20min,得到d50:2μm的注浆注射挤压成型碳化硅陶瓷粉体。
74.实施例5
75.本实施例制备d50:0.5μm的注浆注射挤压成型碳化硅陶瓷粉体,包括以下步骤:
76.(1)粗粒度碳化硅预混料的制备:将d50:3.0μm碳化硅磨料采用气流整形机,在喷嘴前压力为6.2mpa下,采用循环的方式将磨料自磨整形至在显微镜下观察呈土豆圆形,得到粗粒度碳化硅预混料(d50:1.5-2.0μm),备用;
77.(2)中粒度碳化硅预混料的制备:将d50:1.0μm碳化硅磨料采用气流整形机,在喷嘴前压力为6.2mpa下,采用循环的方式将磨料自磨整形至在显微镜下观察呈土豆圆形,得到中粒度碳化硅预混料(d50:0.2-0.5μm),备用;
78.(3)细粒度碳化硅预混料的制备:将d50:5μm碳化硅磨料采用砂磨机湿法研磨,研磨介质采用申请号为201410097403.2中的碳化硅球,研磨至d50:0.1μm时停止,得到细粒度碳化硅预混料,备用;
79.(4)粉体高自身密度的级配:按照质量比为4:1:7向细粒度碳化硅预混料中依次添加粗粒度碳化硅预混料、中粒度碳化硅预混料和水,形成固相比为60%的浆料,同时按固体含量的1.0%添加聚丙烯酸钠作为分散剂,分散10min后,在料浆处于高分散状态下按固体
含量的1.5%加入硅烷偶联剂kh-571,在机械能作用下进行10min的颗粒表面包覆后停止分散,静置10min,得到改性后浆料;
80.(5)将步骤(4)的改性料浆用隔膜泵打入周转容器内,转运至微波干燥器内60℃烘干,得到碳化硅干料;
81.(6)将步骤(5)的干料转入锤形混料机内分散20min,得到d50:0.5μm的注浆注射挤压成型碳化硅陶瓷粉体。
82.对比例1
83.粗、中粒度碳化硅磨料不经过整形,直接采用d50:4.5-5.0μm和d50:2.5-3.0μm的碳化硅粉进行制备,其余同实施例1。
84.对比例2
85.细粒度碳化硅磨料不经过磨细和整形,直接采用d50:0.5μm的碳化硅粉进行制备,其余同实施例1。
86.对比例3
87.粗、中粒度碳化硅磨料整形采用普通整形机将其打磨为土豆圆型,其余同实施例1。
88.由于打磨过程中形成的杂质粉仍然存在体系中,实际上整形后的粉体仅仅改变了表面的形状,粒度分布依旧较宽。
89.对比例4
90.不添加硅烷偶联剂,其余同实施例1。
91.对比例5
92.级配时,低、粗、中粒度碳化硅磨料的质量比为:4:2:1,其余同实施例1。
93.对比例6
94.级配时,低、粗、中粒度碳化硅磨料的质量比为:4:2:8,其余同实施例1。
95.对比例7
96.级配时,低、粗、中粒度碳化硅磨料的质量比为:4:0.5:5,其余同实施例1。
97.对比例8
98.级配时,低、粗、中粒度碳化硅磨料的质量比为:4:4:5,其余同实施例1。
99.实验例不同方法制备得到的碳化硅陶瓷粉的性能测定
100.将实施例1-5,对比例1-8制备得到的碳化硅粉体,进行浆料最大固相含量的测定,流动性和悬浮稳定性的测定,结果见表1,具体测试方法如下:
101.浆料最大固相含量:是指从加粉直至浆料不能流动时为止的固相含量,具体操作为:用分析天平精准称取蒸馏水10g,向水中逐渐加入sic粉,直至浆料不能流动时停止,根据加粉量计算固相含量:vol.%=(m
粉
/ρ
粉
)/(m
粉
/ρ
粉
+m
水
/ρ
水
)
×
100%。
102.流动性:采用丹东市百特公司bt-1000粉体综合特定测试仪对粉体的流动性进行测试,休止角越大流动性越差。
103.悬浮稳定性:将各组sic粉加水配置成20vol.%的悬浮液,将该悬浮液装在带有刻度的圆筒中,筒上端用膜密封以减小挥发,振荡、超声分散30min,静置放置,观察1h和24h时沉降情况,以相对沉降高度(沉降后浑浊部分的高度和悬浮液整体高度的比值)进行评价。
104.表1不同碳化硅陶瓷粉性能评价结果
[0105][0106]
上表数据表明,本发明提供的碳化硅陶瓷粉制备方法制备得到的陶瓷粉具有78-80%的固相含量,同时兼具良好的流动性和悬浮稳定性。
[0107]
对比例1和2中采用的碳化硅磨料不经过整形,所采用的原料不是土豆圆形,粉体的流动性显著降低,颗粒表面能升高,易发生聚集,不利于后续的改性,进而影响粉体固相含量。对比例3的粗、中粒度碳化硅磨料整形采用普通整形机将其打磨为土豆型,由于打磨过程中形成的杂质粉仍然存在体系中,实际上整形后的粉体仅仅改变了表面的形状,粒度分布依旧较宽,并非是采用的单一粒径的粉体做级配,因此填充性能下降,固相含量显著降低。对比例4未对碳化硅粉体进行改性,最终粉体的流动性,悬浮稳定性和固相含量均显著降低。对比例5-8改变了粗、中、低三种粒度的陶瓷粉体的级配比例,固相含量、流动性和悬浮稳定性都有所下降,说明合适的级配比例对于提高陶瓷粉体的固相含量及其他性能有很大影响。
[0108]
对比例1-8表明,对陶瓷粉体高度纯化、表面形态高球形化、级配方案的优化以及进行表面改性这四个方面都会影响最终碳化硅陶瓷粉的固相含量,只有将这4方面系统措施都得以充分完善才能制备出适于注浆类成型的高性能粉体。
[0109]
以上仅为本发明的较佳实施例而已,并不用以限制本发明,凡在本发明的精神和原则之内,所作的任何修改、等同替换、改进等,均应包含在本发明的保护范围之内。