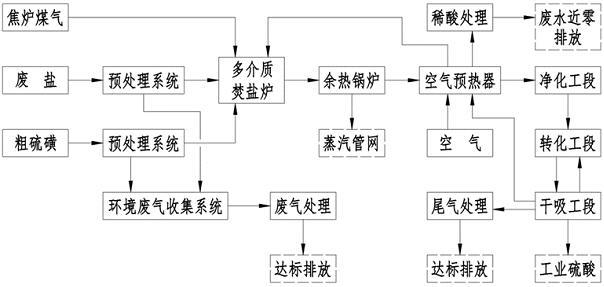
1.本发明属于硫酸制备领域,具体涉及一种焦化脱硫废盐及粗硫磺制酸的工艺。
背景技术:
2.目前,我国焦化行业较多采用以hpf、pds等为催化剂的氨法湿式氧化脱硫脱氰工艺脱除煤气中的h2s和hcn。该工艺运行成本较低、脱硫脱氰效率较高、无需额外碱源等优点。
3.但该工艺仍存在两个最大的缺点:一是从煤气中脱除h2s后生成的焦化硫磺,由于含有煤粉、焦油、萘等杂质,产品纯度低,市场销售困难,为避免形成焦化固废,影响环境,目前焦化粗硫磺多数以低价售出或免费送给用户使用,经济效益差,硫资源未能得到有效循环利用;二是对上述脱硫工艺在脱硫脱氰过程中产生的硫氰酸铵及硫代硫酸铵等废盐废液,缺少完善和有效的后处理工艺技术。
4.利用焦化粗硫磺和以及产生的含硫废盐溶液焚烧制备硫酸是一个良好的工艺路线,目前焦化废盐和焦化粗硫磺制备浓硫酸主要有两种技术路线:第一类是将硫泡沫和含废盐废水一起直接喷入焚烧炉燃烧制备硫酸(cn 106379868),由于浆液含水量较高,故而此方法燃烧过程需要消耗大量燃料。
5.第二类是将硫泡沫和含废盐废液浓缩干燥后送入焚烧炉燃烧(cn 108275659),此类技术虽然减少了原料中的水分,但其原料中杂质没有分离,出料系统容易堵塞并造成焚烧炉、余热锅炉结焦和堵塞;此外,因其液体原料需要制成干粉,需要消耗大量的蒸汽,运行成本高。
6.以上两种方法会导致系统稳定性下降和能耗增加,此外以上两种方法均以硫泡沫或者焦化废液为原料,而大部分焦化厂都已建有熔硫、蒸氨或提盐装置,可以将硫泡沫或者焦化废液制备成焦化固体废盐和粗硫磺,所以会使得原有融硫、蒸氨或提盐装置闲置,导致重复建设。
技术实现要素:
7.为解决现有技术存在的上述问题,本发明提供一种焦化脱硫废盐及粗硫磺制酸的工艺。
8.本发明的实现方法如下:本发明提供一种焦化脱硫废盐及粗硫磺制酸的工艺,包括以下步骤:s1、将焦炉煤气湿法脱硫熔硫工段产生的焦化固态粗硫磺送入焦化粗硫磺预处理系统中进行预处理,将预处理后得到的干净的液态硫磺送入焚烧系统;s2、将焦炉煤气湿法脱硫提盐工段产生的焦化固态废盐送入焦化废盐预处理系统中进行预处理,将预处理后得到的精盐浆送入焚烧系统;s3、由步骤s1所得的液态硫磺在硫磺喷枪内经高温空气雾化后喷入焚烧系统的多介质焚盐炉,由步骤s2所得的精盐浆在盐浆喷枪中经高温空气雾化后喷入焚烧系统的多介
质焚盐炉,雾化后的液态硫磺和精盐浆在多介质焚盐炉中经高温条件下燃烧分解产生高温炉气,离开多介质焚盐炉的高温炉气送入余热回收系统;s4、高温炉气经余热回收系统回收热量后温度降低至350~400℃;s5、离开余热回收系统的炉气进入制酸系统制备成品浓硫酸,尾气经处理后达标排放。
9.进一步地,所述焦化固态粗硫磺送入焦化粗硫磺预处理系统中进行预处理的步骤如下:焦化固态粗硫磺经破碎后送入熔硫反应器,加热后将固态焦化固态粗硫磺熔为液态,液态硫磺依次经过分离器、硫磺澄清塔和过滤器去除包括焦油和煤粉在内的杂质,得到干净的液态硫磺。
10.进一步地,所述熔硫反应器、分离器和硫磺澄清塔均采用蒸汽加热,维持内部液体硫磺温度为120℃~150℃。
11.进一步地,所述焦化固态废盐送入焦化废盐预处理系统中进行预处理的步骤如下:焦化固态废盐经破碎后进入溶盐反应器加热溶解后得废盐浆液,废盐浆液送入氧化分离塔,氧化分离塔底部浆液经固液分离装置去除滤渣后得到精盐浆。
12.进一步地,所述溶盐反应器采用蒸汽加热,维持溶盐反应器内浆液温度为45℃至90℃。
13.进一步地,所述焦化固态粗硫磺中硫单质含量为50~90wt%,水含量为2~15%,焦油、煤粉含量为1~15%。
14.进一步地,所述焦化固态废盐中无机盐含量为70~95wt%,水为含量5~25%,硫单质含量为1~10%。
15.进一步地,所述多介质焚盐炉的温度维持在1000~1200℃,当温度低于1000℃时通入焦炉煤气燃烧以维持温度。
16.进一步地,所述制酸系统包括净化工段、转化及干吸以及尾气吸收工段,所述步骤s5具体包括:在净化工段,离开余热回收系统的炉气进入制酸系统净化工段的高效增湿器,在高效增湿器内通过绝热蒸发使炉气增湿、冷却和初步净化,高效增湿器出口的湿炉气进入填料塔洗涤冷却,炉气温度降低至38℃左右,洗涤塔出来的炉气经两级电除雾去除残留的粉尘和酸雾进入转化及干吸工段;在转化及干吸工段,来自净化工段的炉气在干燥塔内和93%的硫酸逆流接触,使炉气内水分降低至0.1g/nm3以下,干燥后的炉气送入氧化器将炉气中二氧化硫氧化为三氧化硫,含三氧化硫的炉气进入一吸塔用98%的硫酸吸收炉气中三氧化硫制得硫酸,从一吸塔出来的炉气再次进入氧化器发生氧化反应,再次氧化后的炉气进入二吸塔,用98%的硫酸吸收炉气中的三氧化硫再次制得硫酸;在尾气吸收工段,二吸塔出来的炉气采用碱液吸收酸雾后达标排放。
17.进一步地,还包括:制酸系统净化工段产生的废水和转化及干吸工段中二吸塔出来的尾气进入稀酸处理系统,废水和二吸塔出来的尾气在稀酸处理系统的浓缩塔中逆流接触,废水经蒸发浓缩后送入焦化废盐预处理系统作为溶解废盐溶剂使用。
18.与现有技术相比,本发明具有以下有益效果:(1)以干态的焦化固态废盐和焦化固态粗硫磺为原料,避免过多的水分进入多介质焚盐炉,降低焚烧能耗;(2)以焦化固态粗硫磺和焦化固态废盐为原料,可以利用焦化车间原有熔硫釜和提盐设备,避免设备闲置和重复建设;(3)焦化固态废盐和固态粗硫磺分别经预处理后再进入焚烧系统,可以避免原料杂质导致多介质焚盐炉积灰积碳的问题,避免了余热锅炉积碳堵塞;(4)将制酸系统净化工段废水经稀酸处理系统处理后送入焦化废盐预处理系统使用,减少了废液的排放,提高了资源的过程价值。
附图说明
19.图1为本发明实施例提供的焦化脱硫废盐及粗硫磺制酸的工艺的流程图。
具体实施方式
20.下面将结合本发明实施例中的附图,对本发明实施例中的技术方案进行清楚、完整地描述,显然,所描述的实施例仅仅是本发明一部分实施例,而不是全部的实施例。基于本发明中的实施例,本领域普通技术人员在没有做出创造性劳动前提下所获得的所有其它实施例,都属于本发明保护的范围。
21.如图1所示,本发明实施例提供一种焦化脱硫废盐及粗硫磺制酸的工艺,包括以下步骤:s1、将焦炉煤气湿法脱硫熔硫工段产生的焦化固态粗硫磺送入焦化粗硫磺预处理系统中进行预处理,将预处理后得到的干净的液态硫磺送入焚烧系统。
22.所述焦化固态粗硫磺的主要成分包括硫单质、煤粉、焦油以及水,其中硫单质含量为50~90wt%,水含量为2~15%,焦油、煤粉含量为1~15%。
23.具体地,所述焦化固态粗硫磺送入焦化粗硫磺预处理系统中进行预处理的步骤如下:焦化固态粗硫磺经破碎后送入熔硫反应器,加热后将固态焦化固态粗硫磺熔为液态,液态硫磺依次经过分离器、硫磺澄清塔和过滤器去除焦油和煤粉等杂质,得到干净的液态硫磺。预处理后的干净的液态硫磺经精硫浆储罐之后输送至焚烧系统。优选地,所述熔硫反应器、分离器和硫磺澄清塔均采用蒸汽加热,维持内部液体硫磺温度为120℃~150℃。
24.s2、将焦炉煤气湿法脱硫提盐工段产生的焦化固态废盐送入焦化废盐预处理系统中进行预处理,将预处理后得到的精盐浆送入焚烧系统。
25.所述焦化固态废盐的主要成分包括无机盐、水以及硫单质,其中无机盐(硫氰酸盐、硫代硫酸盐和硫酸盐)含量为70~95wt%,水为含量5~25%,硫单质含量为1~10%。
26.具体地,所述焦化固态废盐送入焦化废盐预处理系统中进行预处理的步骤如下:焦化固态废盐经破碎后进入溶盐反应器加热溶解后得废盐浆液,在溶盐反应器中以工艺水和来自稀酸处理系统的废液作为溶剂,废盐浆液送入氧化分离塔,氧化分离塔底部浆液经固液分离装置去除滤渣后得到精盐浆。精盐浆经盐浆缓冲罐后送入焚烧系统,滤渣则送入地坑。优选地,所述溶盐反应器采用蒸汽加热,维持溶盐反应器内浆液温度为45℃至90℃。所述固液分离装置可以采用过滤分离或者离心分离。所述精盐浆中水的质量分数为30%~
80%。
27.s3、由步骤s1所得的液态硫磺在硫磺喷枪内经高温空气高效雾化后喷入焚烧系统的多介质焚盐炉,由步骤s2所得的精盐浆在盐浆喷枪中经高温空气雾化后喷入焚烧系统的多介质焚盐炉,雾化后的液态硫磺和精盐浆在多介质焚盐炉中经高温条件下燃烧分解产生高温炉气(1000~1200℃),焚盐炉内采用富氧空气助燃,所需富氧空气由富氧机组制得或者由厂区氧气源提供,离开多介质焚盐炉的高温炉气送入余热回收系统。进一步地,所述多介质焚盐炉的温度维持在1000~1200℃,当温度低于1000℃时通入焦炉煤气燃烧以维持温度。
28.s4、高温炉气经余热回收系统回收热量后温度降低至350~400℃。
29.具体地,高温炉气经余热回收系统的余热锅炉降低烟气的温度,然后通过空气预热器再次降低温度,最终温度降低至350~400℃。
30.s5、离开余热回收系统的炉气进入制酸系统制备成品浓硫酸,尾气经处理后达标排放。
31.具体地,所述制酸系统包括净化工段、干吸工段、转化工段以及尾气吸收工段,离开余热回收系统的炉气依次经过制酸系统的净化工段、转化及干吸工段采用“两转两吸”工艺制备成品浓硫酸,尾气经尾气吸收工段处理后达标排放,具体过程如下:在净化工段,离开余热回收系统的炉气进入制酸系统净化工段的高效增湿器,在高效增湿器内通过绝热蒸发使炉气增湿、冷却和初步净化,高效增湿器出口的湿炉气进入填料塔洗涤冷却,炉气温度降低至38℃左右,洗涤塔出来的炉气经两级电除雾去除残留的粉尘和酸雾进入转化及干吸工段;在转化及干吸工段,来自净化工段的炉气在干燥塔内和93%的硫酸逆流接触,使炉气内水分降低至0.1g/nm3以下,干燥后的炉气送入氧化器将炉气中二氧化硫氧化为三氧化硫,含三氧化硫的炉气进入一吸塔用98%的硫酸吸收炉气中三氧化硫制得硫酸,从一吸塔出来的炉气再次进入氧化器发生氧化反应,再次氧化后的炉气进入二吸塔,用98%硫酸吸收炉气中的三氧化硫再次制得硫酸;在尾气吸收工段,二吸塔出来的炉气采用碱液吸收酸雾后达标排放。
32.进一步地,制酸系统净化工段产生的废水和转化及干吸工段中二吸塔出来的尾气进入稀酸处理系统,废水和二吸塔出来的尾气与浓缩塔中逆流接触,废水经蒸发浓缩后送入焦化废盐预处理系统作为溶解废盐溶剂使用,尾气经吸收塔、碱洗塔、电除雾后达标排放。其中,稀酸处理系统可以通过空气预热器产生的蒸汽进行加热,实现资源的循环利用。
33.本发明实施例提供的这种焦化脱硫废盐及粗硫磺制酸的工艺,以焦化固态废盐和焦化固态粗硫磺为原料,依次经焦化废盐预处理系统、焦化粗硫磺预处理系统、焚烧系统、余热回收系统和制酸系统制备硫酸;制酸系统产生废水经稀酸处理系统处理后送入焦化废盐预处理系统作为溶剂使用;产生废气经处理系统处理后达标排放;生产出的硫酸既可以作为焦化煤气净化生产硫铵的原料,也可以作为商用硫酸外销,实现了资源的再利用和环境保护的双重目标。本发明立足焦化流程系统资源平衡,系统考虑固废、废液和废气的耦合处理,变废为宝,提高了资源的过程价值。
34.以上所述仅为本发明的较佳实施例而已,并不用以限制本发明,凡在本发明的精神和原则之内,所作的任何修改、等同替换、改进等,均应包含在本发明的保护范围之内。