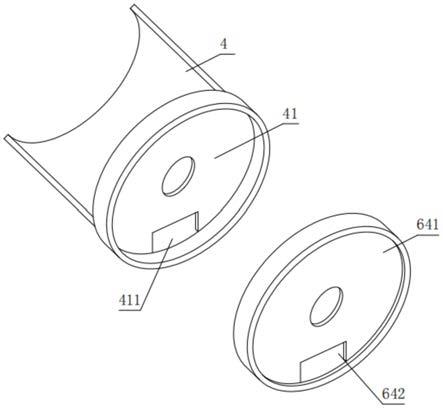
1.本发明涉及到铸造废覆膜砂烧制技术领域,特别涉及一种利用铸造废覆膜砂烧制轻质陶粒的方法。
背景技术:
2.造型材料是用来制造铸型(包括砂芯)材料的统称,铸造生产中使用的铸型有砂型、金属型、陶瓷型、石膏型、石墨型等。由于砂型铸造的原材料价廉易得,铸型制造简便,对铸件的单件生产、成批生产和大量生产均能适应,一直是铸造生产中的基本工艺,应用砂型生产的铸件占应用各种铸型生产铸件的80%以上。
3.1、现有的铸造废覆膜砂再利用后,其与其他材料融合不均匀,导致烧制过程中质量不均匀,影响成品质量;
4.2、其次现有的铸造废覆膜砂烧制结构整体没有预热,且冷却时间过长,导致生产效率慢。
技术实现要素:
5.本发明的目的在于提供一种利用铸造废覆膜砂烧制轻质陶粒的方法,能够保证在破碎后的物料的均匀性,提高后期陶坯融合效率,提高后期烧结效率和质量,通过设置多组透气孔,提高热量传输的均匀性,增加烧制成品的质量,提前预热能够有效防止直接烧制导致开裂的问题,提高成品的完整度,防止出现烧制瑕疵,将烧制好的物料输送到冷却筒体内,通过重合的方式进行输料,减少直接贯通导致冷气浪费的问题,防止冷热互通,导致资源浪费,以解决上述背景技术中提出的问题。
6.为实现上述目的,本发明提供如下技术方案:
7.一种利用铸造废覆膜砂烧制轻质陶粒的方法,包括如下步骤:
8.s1:将铸造废覆膜砂和废灰收集后,放入料仓内,通过搅拌器在料仓内进行搅匀,并通过板式喂料机将搅拌均匀的废料进行下料和输送;
9.s2:板式喂料机将废料输送到颚式破碎机内,通过颚式破碎机进行破碎,并将破碎后的物料进行收集,并由皮带机进行输送;
10.s3:皮带机将破碎后的物料输送到回转筛内进行筛分,将破碎后的废料根据回转筛的筛目进行分级筛分,颗粒大的废料通过另一组皮带机输送到颚式破碎机内重新进行加工,合格的废料进行处理;
11.s4:按照一定比例在废料内加入水和胶粉,并通过搅拌器进行搅拌融合,在由造粒机将混合后的物料进行造粒,并将成粒后的物料进行烘干;
12.s5:烘干后的物料输送到回转窑内进行烧制,在设置过程中,先进行预热,并由回转窑边烧制边运输,烧制成型后得到轻质陶粒;
13.s6:将烧制好的轻质陶粒输送到冷却处进行冷却,并将冷却后的轻质陶粒进行下料和收集。
14.进一步地,针对s3,回转筛上设置有多组筛目,当破碎的废料进行回转筛上不同孔径的筛目时,能够对破碎的废料进行多级筛分,保证筛分的精细度。
15.进一步地,针对s5中,回转窑内设置有用于对铸造废覆膜砂进行处理的烧制装置,烧制装置前端的回转窑内设置有预热装置,预热装置的上方设置有烟雾处理装置,回转窑内设置有烧制腔烧制腔下方的回转窑下设置有动力组件,烧制腔一端连接冷却组件。
16.进一步地,烧制装置包括煤粉仓、支架、安装座、煤粉管、燃烧器和烧制内管,煤粉仓通过支架设置在安装座的上方,煤粉仓的下方与煤粉管连接,煤粉管一端连接有风机,煤粉管另一端与设置在回转窑内的烧制内管连接,烧制内管前端设置有燃烧器,烧制内管的外表面上开设有多组透气孔,透气孔与烧制腔内互通。
17.进一步地,预热装置包括预热座、预热筒和连接环,预热座的内部设置有预热筒,预热筒一端通过连接环与回转窑的炉体连接。
18.进一步地,烟雾处理装置包括处理箱体、水槽、进气管、过滤网、喷淋管和排出口,水槽开设在处理箱体的底端,水槽侧端连接进气管,水槽上方的处理箱体内设置过滤网,过滤网上方的处理箱体内设置喷淋管,喷淋管上方处理箱体的顶端开设有排出口。
19.进一步地,动力组件包括底接座、动力电机、小齿轮和套接齿环,底接座设置在回转窑的下方,底接座上安装有动力电机,动力电机的输出轴杆上套接有小齿轮,小齿轮上方与套接齿环啮合,套接齿环套接在回转窑的外表面上。
20.进一步地,回转窑的两端通过轴承与预热装置和冷却组件密封活动连接,回转窑由动力组件驱动转动,烧制装置一端穿透设置在回转窑内部的烧制腔内。
21.进一步地,冷却组件包括输气管、制冷套座、制冷弯管、冷却筒体和收集座,输气管的一端与处理箱体上方的排出口连接,输气管的另一端与制冷套座内连接,制冷套座的内壁上缠绕设置有制冷弯管,制冷套座的尾端通过管道与冷却筒体连接,冷却筒体的下方设置有收集座。
22.进一步地,冷却筒体前端设置有隔热板,隔热板底端面板上设置有进料口,烧制腔与冷却筒体对接端设置有封闭板,封闭板与隔热板贴合设置,封闭板的板面上设置有与进料口对应的出料口。
23.与现有技术相比,本发明的有益效果是:
24.1、本发明提出的利用铸造废覆膜砂烧制轻质陶粒的方法,回转筛上设置有多组筛目,当破碎的废料进行回转筛上不同孔径的筛目时,能够对破碎的废料进行多级筛分,保证筛分的精细度,通过在破碎之前将铸造废覆膜砂和废灰进行搅拌均匀,能够保证在破碎后的物料的均匀性,提高后期陶坯融合效率,提高后期烧结效率和质量。
25.2、本发明提出的利用铸造废覆膜砂烧制轻质陶粒的方法,透气孔与烧制腔内互通,煤粉仓的煤粉由煤粉管尾端的风机进行吹送,将煤粉输送到烧制内管内的燃烧器处,由燃烧器点燃后通过烧制内管将燃烧的热量输送到烧制腔内,从而对烧制腔内的陶坯进行烧制,通过设置多组透气孔,提高热量传输的均匀性,增加烧制成品的质量。
26.3、本发明提出的利用铸造废覆膜砂烧制轻质陶粒的方法,在烧制装置烧制过程中产生的热量通过烧制腔输送到预热筒内,对预热筒内的废料制成的陶坯进行预热,提前预热能够有效防止直接烧制导致开裂的问题,提高成品的完整度,防止出现烧制瑕疵。
27.4、本发明提出的利用铸造废覆膜砂烧制轻质陶粒的方法,喷淋管上方处理箱体的
顶端开设有排出口,水槽内灌满石灰石水,含硫气体进入石灰石水内,增加与石灰石水接触面积,使气体与石灰石水充分反映,提高处理效率,喷淋管将水槽内的石灰石水喷出与初步过滤后的气体充分接触,提高脱硫效果,形成一个湿法脱硫循环,增加利用效率,减少资源浪费。
28.5、本发明提出的利用铸造废覆膜砂烧制轻质陶粒的方法,封闭板与隔热板贴合设置,封闭板的板面上设置有与进料口对应的出料口,处理后的气体输送到制冷套座内由制冷弯管进行制冷,并输送到冷却筒体内对进入到冷却筒体烧制成品进行冷却,提高冷却效率,可快速对轻质陶粒进行冷却,增加生产效率,且当回转窑转动时,使出料口与进料口重合,将烧制好的物料输送到冷却筒体内,通过重合的方式进行输料,减少直接贯通导致冷气浪费的问题,防止冷热互通,导致资源浪费。
附图说明
29.图1为本发明的流程图;
30.图2为本发明的整体结构示意图;
31.图3为本发明的烧制装置结构示意图;
32.图4为本发明的烟雾处理装置结构剖面图;
33.图5为本发明图2的a处放大图;
34.图6为本发明的动力组件结构示意图;
35.图7为本发明的冷却组件冷却组件;
36.图8为本发明的冷却组件与动力组件局部结构示意图。
37.图中:1、烧制装置;11、煤粉仓;12、支架;13、安装座;14、煤粉管;141、风机;15、燃烧器;16、烧制内管;161、透气孔;2、预热装置;21、预热座;22、预热筒;23、连接环;3、烟雾处理装置;31、处理箱体;32、水槽;33、进气管;34、过滤网;35、喷淋管;36、排出口;4、烧制腔;41、封闭板;411、出料口;5、动力组件;51、底接座;52、动力电机;53、小齿轮;54、套接齿环;6、冷却组件;61、输气管;62、制冷套座;63、制冷弯管;64、冷却筒体;641、隔热板;642、进料口;65、收集座。
具体实施方式
38.下面将结合本发明实施例中的附图,对本发明实施例中的技术方案进行清楚、完整地描述,显然,所描述的实施例仅仅是本发明一部分实施例,而不是全部的实施例。基于本发明中的实施例,本领域普通技术人员在没有做出创造性劳动前提下所获得的所有其他实施例,都属于本发明保护的范围。
39.请参阅图1,一种利用铸造废覆膜砂烧制轻质陶粒的方法,包括如下步骤:
40.s1:将铸造废覆膜砂和废灰收集后,放入料仓内,通过搅拌器在料仓内进行搅匀,并通过板式喂料机将搅拌均匀的废料进行下料和输送;
41.s2:板式喂料机将废料输送到颚式破碎机内,通过颚式破碎机进行破碎,并将破碎后的物料进行收集,并由皮带机进行输送;
42.s3:皮带机将破碎后的物料输送到回转筛内进行筛分,将破碎后的废料根据回转筛的筛目进行分级筛分,颗粒大的废料通过另一组皮带机输送到颚式破碎机内重新进行加
工,合格的废料进行处理;
43.s4:按照一定比例在废料内加入水和胶粉,并通过搅拌器进行搅拌融合,在由造粒机将混合后的物料进行造粒,并将成粒后的物料进行烘干;
44.s5:烘干后的物料输送到回转窑内进行烧制,在设置过程中,先进行预热,并由回转窑边烧制边运输,烧制成型后得到轻质陶粒;
45.s6:将烧制好的轻质陶粒输送到冷却处进行冷却,并将冷却后的轻质陶粒进行下料和收集。
46.回转筛上设置有多组筛目,当破碎的废料进行回转筛上不同孔径的筛目时,能够对破碎的废料进行多级筛分,保证筛分的精细度,通过在破碎之前将铸造废覆膜砂和废灰进行搅拌均匀,能够保证在破碎后的物料的均匀性,提高后期陶坯融合效率,提高后期烧结效率和质量。
47.请参阅图2,针对s5中,回转窑内设置有用于对铸造废覆膜砂进行处理的烧制装置1,烧制装置1前端的回转窑内设置有预热装置2,预热装置2的上方设置有烟雾处理装置3,回转窑内设置有烧制腔4烧制腔4下方的回转窑下设置有动力组件5,烧制腔4一端连接冷却组件6。
48.请参阅图3,烧制装置1包括煤粉仓11、支架12、安装座13、煤粉管14、燃烧器15和烧制内管16,煤粉仓11通过支架12设置在安装座13的上方,煤粉仓11的下方与煤粉管14连接,煤粉管14一端连接有风机141,煤粉管14另一端与设置在回转窑内的烧制内管16连接,烧制内管16前端设置有燃烧器15,烧制内管16的外表面上开设有多组透气孔161,透气孔161与烧制腔4内互通,煤粉仓11的煤粉由煤粉管14尾端的风机141进行吹送,将煤粉输送到烧制内管16内的燃烧器15处,由燃烧器15点燃后通过烧制内管16将燃烧的热量输送到烧制腔4内,从而对烧制腔4内的陶坯进行烧制,通过设置多组透气孔161,提高热量传输的均匀性,增加烧制成品的质量。
49.请参阅图4,预热装置2包括预热座21、预热筒22和连接环23,预热座21的内部设置有预热筒22,预热筒22一端通过连接环23与回转窑的炉体连接,在烧制装置1烧制过程中产生的热量通过烧制腔4输送到预热筒22内,对预热筒22内的废料制成的陶坯进行预热,提前预热能够有效防止直接烧制导致开裂的问题,提高成品的完整度,防止出现烧制瑕疵。
50.请参阅图5,烟雾处理装置3包括处理箱体31、水槽32、进气管33、过滤网34、喷淋管35和排出口36,水槽32开设在处理箱体31的底端,水槽32侧端连接进气管33,水槽32上方的处理箱体31内设置过滤网34,过滤网34上方的处理箱体31内设置喷淋管35,喷淋管35上方处理箱体31的顶端开设有排出口36,水槽32内灌满石灰石水,含硫气体进入石灰石水内,增加与石灰石水接触面积,使气体与石灰石水充分反映,提高处理效率,喷淋管35将水槽32内的石灰石水喷出与初步过滤后的气体充分接触,提高脱硫效果,形成一个湿法脱硫循环,增加利用效率,减少资源浪费。
51.请参阅图6,动力组件5包括底接座51、动力电机52、小齿轮53和套接齿环54,底接座51设置在回转窑的下方,底接座51上安装有动力电机52,动力电机52的输出轴杆上套接有小齿轮53,小齿轮53上方与套接齿环54啮合,套接齿环54套接在回转窑的外表面上,在烧制过程中,动力电机52通过小齿轮53带动套接齿环54转动,从而带动回转窑转动,便于对物料均匀加热的同时,驱动物料移动。
52.请参阅图7-图8,回转窑的两端通过轴承与预热装置2和冷却组件6密封活动连接,回转窑由动力组件5驱动转动,烧制装置1一端穿透设置在回转窑内部的烧制腔4内,冷却组件6包括输气管61、制冷套座62、制冷弯管63、冷却筒体64和收集座65,输气管61的一端与处理箱体31上方的排出口36连接,输气管61的另一端与制冷套座62内连接,制冷套座62的内壁上缠绕设置有制冷弯管63,制冷套座62的尾端通过管道与冷却筒体64连接,冷却筒体64的下方设置有收集座65,冷却筒体64前端设置有隔热板641,隔热板641底端面板上设置有进料口642,烧制腔4与冷却筒体64对接端设置有封闭板41,封闭板41与隔热板641贴合设置,封闭板41的板面上设置有与进料口642对应的出料口411,处理后的气体输送到制冷套座62内由制冷弯管63进行制冷,并输送到冷却筒体64内对进入到冷却筒体64烧制成品进行冷却,提高冷却效率,可快速对轻质陶粒进行冷却,增加生产效率,且当回转窑转动时,使出料口411与进料口642重合,将烧制好的物料输送到冷却筒体64内,通过重合的方式进行输料,减少直接贯通导致冷气浪费的问题,防止冷热互通,导致资源浪费。
53.综上所述,本发明提出的利用铸造废覆膜砂烧制轻质陶粒的方法,回转筛上设置有多组筛目,当破碎的废料进行回转筛上不同孔径的筛目时,能够对破碎的废料进行多级筛分,保证筛分的精细度,通过在破碎之前将铸造废覆膜砂和废灰进行搅拌均匀,能够保证在破碎后的物料的均匀性,提高后期陶坯融合效率,提高后期烧结效率和质量,透气孔161与烧制腔4内互通,煤粉仓11的煤粉由煤粉管14尾端的风机141进行吹送,将煤粉输送到烧制内管16内的燃烧器15处,由燃烧器15点燃后通过烧制内管16将燃烧的热量输送到烧制腔4内,从而对烧制腔4内的陶坯进行烧制,通过设置多组透气孔161,提高热量传输的均匀性,增加烧制成品的质量,在烧制装置1烧制过程中产生的热量通过烧制腔4输送到预热筒22内,对预热筒22内的废料制成的陶坯进行预热,提前预热能够有效防止直接烧制导致开裂的问题,提高成品的完整度,防止出现烧制瑕疵,喷淋管35上方处理箱体31的顶端开设有排出口36,水槽32内灌满石灰石水,含硫气体进入石灰石水内,增加与石灰石水接触面积,使气体与石灰石水充分反映,提高处理效率,喷淋管35将水槽32内的石灰石水喷出与初步过滤后的气体充分接触,提高脱硫效果,形成一个湿法脱硫循环,增加利用效率,减少资源浪费,封闭板41与隔热板641贴合设置,封闭板41的板面上设置有与进料口642对应的出料口411,处理后的气体输送到制冷套座62内由制冷弯管63进行制冷,并输送到冷却筒体64内对进入到冷却筒体64烧制成品进行冷却,提高冷却效率,可快速对轻质陶粒进行冷却,增加生产效率,且当回转窑转动时,使出料口411与进料口642重合,将烧制好的物料输送到冷却筒体64内,通过重合的方式进行输料,减少直接贯通导致冷气浪费的问题,防止冷热互通,导致资源浪费。
54.以上所述,仅为本发明较佳的具体实施方式,但本发明的保护范围并不局限于此,任何熟悉本技术领域的技术人员在本发明披露的技术范围内,根据本发明的技术方案及其发明构思加以等同替换或改变,都应涵盖在本发明的保护范围之内。