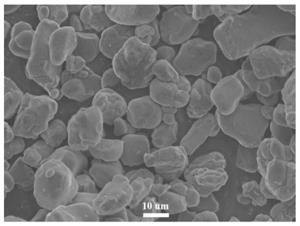
1.本发明涉及锂电池正极材料回收与修复再生处理领域,尤其是一种废旧锂电池中钴酸锂的回收方法。
背景技术:
2.锂离子电池具有体积小、能量密度大、没有记忆效应且工作范围较宽的优点,在移动设备、电动汽车等领域得到越来越广泛的应用,其中,钴酸锂电池主要用作手机、笔记本电脑等小型便携式电子设备的电源。钴酸锂电池的使用寿命一般为2-3年,失效后的电池如果不作处理任意废弃,那么不但它含有的重金属会对环境产生污染,而且钴、锂等贵金属不回收也是一种资源浪费。随着便携式电子设备的广泛应用,钴酸锂电池的使用量逐年增加,所以废旧钴酸锂电池回收利用研究是一项十分必要且紧迫的工作。
3.目前,锂电池中金属元素回收的各种方法主要是基于干法冶金、生物冶金和湿法冶金等冶金技术原理而建立的。湿法冶金法在锂电池回收中常用酸浸法,利用盐酸、硫酸、硝酸等无机强酸浸出有价金属离子,然后再使这些金属离子成盐后沉淀出来得以回收。无机酸在浸出过程中会释放c
l2
、so3和nox等有害气体,废酸也对环境构成威胁。
4.中国专利公开号cn108258351a,公开了一种废旧钴酸锂电池的正极材料的回收方法,其特征在于,包括下述步骤:将钴酸锂电池的正极在400~700℃下煅烧0.5~3小时,得到钴酸锂粉末;将钴酸锂粉末、酸性溶液及过氧化氢混合,并于超声波环境下搅拌反应,得到反应液;将反应液与草酸混合,并在40~100℃的条件下反应,经过滤,得到滤液及草酸钴;将滤液与碳酸钠混合反应,得到碳酸锂。其不足之处在于,草酸根离子和碳酸根离子并不能特异性与钴离子和锂离子结合,在沉淀过程中会有大量的杂质生成,降低了回收产物的纯度,且回收得到的是草酸钴和碳酸锂,仍需进一步处理方能得到钴酸锂,没有达到对钴酸锂整体回收的效果。
技术实现要素:
5.本发明是为了克服现有的钴酸锂回收方法回收产物的纯度低,无法直接回收钴酸锂的不足,提供一种回收产物纯度高,可直接得到钴酸锂的废旧锂电池中钴酸锂的回收方法。
6.为了实现上述发明目的,本发明采用的技术方案如下:一种废旧锂电池中钴酸锂的回收方法,包括以下步骤:a.将废旧锂电池彻底放电,拆解正极片;b.对步骤a所得正极片进行裁剪、真空煅烧、粉碎得到正极粉体;c.对步骤b所得正极粉体进行分级分离,得到钴酸锂粗粉;d. 将步骤c所得钴酸锂粗粉于还原性酸溶液中浸出,加入配体溶液进行络合后再加入氧化剂氧化,分离得络合物溶液;e. 调节步骤d所得络合物溶液中钴、锂元素浓度比,干燥,煅烧,粉碎得再生钴酸
锂。
7.通过煅烧、粉碎、分级分离得到钴酸锂粗粉,对正极材料中的杂质进行初步的分离,再经浸出后在配体作用下稳定得到低杂质含量的络合物溶液,调整价态后再调节络合物溶液中钴、锂元素的浓度比,干燥、煅烧、粉碎后即可得到高纯度钴酸锂,本发明的方法简单易操作,可直接得到高纯度的钴酸锂,方便了钴酸锂的回收再利用。
8.优选的,步骤b中,真空煅烧的温度为400~550℃,煅烧时间为0.5~3h,真空度为-0.1mpa~-1mpa。
9.优选的,步骤c中,分级分离方式为超声振动筛分级,超声振动筛分两层,上层震动筛目数50~100目,下层震动筛目数为250~350目。
10.优选的,步骤c中,钴酸锂粗粉为下层振动筛筛下部分。
11.在经超声振动筛分离后,下层振动筛下物主要为失效的钴酸锂及少量杂质,大部分有机物在煅烧阶段被去除,由铝集流体带来的铝杂质主要集中在上层振动筛上,其他颗粒较大的杂质也会集中于下层振动筛上,至此已通过物理分离的形式对正极材料进行了较好的初步处理。
12.优选的,步骤d中,还原性酸溶液为抗坏血酸水溶液,配体溶液为氨水,氧化剂为过氧化氢。
13.抗坏血酸一方面可以起到对锂离子的溶出作用,另一方面,钴酸根离子中+3价的钴也会被抗坏血酸还原为+2价的钴离子,浸出的+2价钴离子再与氨络合,形成强还原性的[co(nh3)6]
2+
络合物,在过氧化氢作用下,[co(nh3)6]
2+
又被氧化为稳定的[co(nh3)6]
3+
,而浸出液中的其他含量较低的金属离子如镍离子、锰离子、亚铁离子、铁离子、镁离子、钙离子、铜离子都在碱性条件下形成沉淀,氨在作为配体的同时又可以进行除杂,从而在过滤后实现了对钴、锂的进一步纯化分离。
[0014]
优选的,步骤d中,还原性酸溶液浓度为0.5~2.5mol/l,浸出固液比为10~30g/l,浸出温度为20~100℃,浸出时间为20~120min,配体溶液质量分数为5%~15%,氧化剂的质量分数为1~4%。
[0015]
优选的,氧化剂溶液与配体溶液的质量比为1:1.5~2.5。
[0016]
优选的,步骤d中,调节后的络合物溶液中钴、锂元素浓度比为1:1~1.05,煅烧温度为600~800℃,煅烧时间为2~5小时。
[0017]
由于采用以上的技术方案,本发明具有这样的有益效果:对正极材料经物理分离和化学纯化之后煅烧得到低杂质含量的钴酸锂,实现了失效钴酸锂的再生回收;再生回收的过程简单易操作,并可直接得到钴酸锂,不需对锂和钴分别处理,省时省力;得到的钴酸锂纯度较高,性能优良。
附图说明
[0018]
图1是本发明实施例1再生后钴酸锂的sem图。
[0019]
图2是本发明实施例1再生后的钴酸锂与标准钴酸锂样品的xrd对比图。
[0020]
图3是本发明实施例1~3和对比例1~4的锂电池在0.1c充放电曲线图。
[0021]
图4是本发明实施例1~3和对比例1~4的锂电池放电倍率性能图。
[0022]
图5是本发明实施例1~3和对比例1~4的锂电池循环性能对比图。
具体实施方式
[0023]
下面结合附图与具体实施方式对本发明做进一步的描述。
[0024]
总实施例一种废旧锂电池中钴酸锂的回收方法,包括以下步骤:a. 采用盐水放电或放电柜放电使废旧锂电池彻底放电,拆解分选出正极片;b.将步骤a所得正极片裁剪为10cm
×
10cm的小块,置于330mm
×
330mm
×
100mm尺寸的莫来石匣钵中,放入箱式炉中真空煅烧,真空度为-0.1mpa~-1mpa ,煅烧温度为400~550℃,煅烧时间为0.5~3h,煅烧过程中定时抽出废气,废气导入碱缸吸收。煅烧后的正极片经气流粉碎得到正极粉体;c.对步骤b所得正极粉体置于超声震动筛内振动分离,上层选用50目振动筛,下层选用300振动筛,收集300目筛下物,得到钴酸锂粗粉;d. 用浓度为0.5~2.5mol/l抗坏血酸溶液对步骤c所得钴酸锂粗粉进行浸出,固液比为10~30g/l,温度为20~100℃,浸出时间为20~120min,过滤得到浸出液;向浸出液中加入质量分数为5%~15%的氨水至浸出液中不再有沉淀析出也不再有沉淀溶解,再加入氨水质量一半的质量分数为1~4%的双氧水溶液进行氧化,分离得络合物溶液;e.向步骤d所得络合物溶液中加入碳酸锂或碳酸钴调节络合物溶液中钴、锂元素浓度比为1:1~1.05,搅拌均匀后冻干,于箱式炉中600~800℃煅烧2~5小时,冷却后固体经气流粉碎得再生钴酸锂。
[0025]
实施例1a. 采用盐水放电使废旧锂电池彻底放电,拆解分选出正极片;b.将步骤a所得正极片裁剪为10cm
×
10cm的小块,置于330mm
×
330mm
×
100mm尺寸的莫来石匣钵中,放入箱式炉中真空煅烧,保持维持真空度为-0.7mpa,煅烧温度为500℃,煅烧时间为2h,煅烧过程中定时抽出废气,废气导入碱缸吸收。煅烧后的正极片经气流粉碎得到正极粉体;c.对步骤b所得正极粉体置于超声震动筛内振动分离,上层选用50目振动筛,下层选用300振动筛,收集300目筛下物,得到钴酸锂粗粉;d. 用浓度为1.5mol/l抗坏血酸溶液对步骤c所得钴酸锂粗粉进行浸出,固液比为20g/l,60℃下超声浸出70min,过滤得到浸出液;向浸出液中加入质量分数为10%的氨水至浸出液中不再有沉淀析出也不再有沉淀溶解,加入氨水质量一半的质量分数为3%的双氧水溶液继续搅拌0.5h,过滤分离得络合物溶液;e. 用电耦合等离子体原子发射光谱icp-aes测定步骤d所得络合物溶液中钴、锂元素的质量浓度,加入碳酸锂调节溶液中钴、锂元素摩尔浓度比为1:1,搅拌均匀后冻干溶剂,于箱式炉中700℃煅烧4h,冷却后固体经气流粉碎得再生钴酸锂。
[0026]
图1为本实施例再生后的钴酸锂的sem图,由图1可知,再生后的钴酸锂尺寸均匀,具有良好的微观形貌;图2为本实施例再生后钴酸锂与标准钴酸锂样品的xrd对比图,可见再生后钴酸锂与标准品相同,且相纯度与标准品没有显著差别,几乎不含其他杂质。
[0027]
实施例2a. 采用放电柜使废旧锂电池彻底放电,拆解分选出正极片;b.将步骤a所得正极片裁剪为10cm
×
10cm的小块,置于330mm
×
330mm
×
100mm尺寸
的莫来石匣钵中,放入箱式炉中真空煅烧,保持维持真空度为-0.1mpa,煅烧温度为400℃,煅烧时间为3h,煅烧过程中定时抽出废气,废气导入碱缸吸收。煅烧后的正极片经气流粉碎得到正极粉体;c.对步骤b所得正极粉体置于超声震动筛内振动分离,上层选用50目振动筛,下层选用300振动筛,收集300目筛下物,得到钴酸锂粗粉;d. 用浓度为0.5mol/l抗坏血酸溶液对步骤c所得钴酸锂粗粉进行浸出,固液比为10g/l,20℃下超声浸出120min,过滤得到浸出液;向浸出液中加入质量分数为5%的氨水至浸出液中不再有沉淀析出也不再有沉淀溶解,加入氨水质量一半的质量分数为1%的双氧水溶液继续搅拌0.5h,过滤分离得络合物溶液;e. 用icp-aes测定步骤d所得络合物溶液中钴、锂元素的质量浓度,加入碳酸锂调节溶液中钴、锂元素摩尔浓度比为1:1,搅拌均匀后冻干溶剂,于箱式炉中600℃煅烧5h,冷却后固体经气流粉碎得再生钴酸锂。
[0028]
实施例3a. 采用放电柜使废旧锂电池彻底放电,拆解分选出正极片;b.将步骤a所得正极片裁剪为10cm
×
10cm的小块,置于330mm
×
330mm
×
100mm尺寸的莫来石匣钵中,放入箱式炉中真空煅烧,保持维持真空度为-1mpa,煅烧温度为550℃,煅烧时间为0.5h,煅烧过程中定时抽出废气,废气导入碱缸吸收。煅烧后的正极片经气流粉碎得到正极粉体;c.对步骤b所得正极粉体置于超声震动筛内振动分离,上层选用50目振动筛,下层选用300振动筛,收集300目筛下物,得到钴酸锂粗粉;d. 用浓度为2.5mol/l抗坏血酸溶液对步骤c所得钴酸锂粗粉进行浸出,固液比为30g/l,120℃下超声浸出20min,过滤得到浸出液;向浸出液中加入质量分数为15%的氨水至浸出液中不再有沉淀析出也不再有沉淀溶解,加入氨水质量一半的质量分数为4%的双氧水溶液继续搅拌0.5h,过滤分离得络合物溶液;e. 用icp-aes测定步骤d所得络合物溶液中钴、锂元素的质量浓度,加入碳酸钴调节溶液中钴、锂元素摩尔浓度比为1:1,搅拌均匀后冻干溶剂,于箱式炉中800℃煅烧2h,冷却后固体经气流粉碎得再生钴酸锂。
[0029]
对比例1对比例1相较于实施例1未对正极粉体进行分级分离;a. 采用盐水放电使废旧锂电池彻底放电,拆解分选出正极片;b.将步骤a所得正极片裁剪为10cm
×
10cm的小块,置于330mm
×
330mm
×
100mm尺寸的莫来石匣钵中,放入箱式炉中真空煅烧,保持维持真空度为-0.7mpa,煅烧温度为500℃,煅烧时间为2h,煅烧过程中定时抽出废气,废气导入碱缸吸收。煅烧后的正极片经气流粉碎得到正极粉体;c.用浓度为1.5mol/l抗坏血酸溶液对步骤b所得正极粉体进行浸出,固液比为20g/l,60℃下超声浸出70min,过滤得到浸出液;向浸出液中加入质量分数为10%的氨水至浸出液中不再有沉淀析出也不再有沉淀溶解,加入氨水质量一半的质量分数为3%的双氧水溶液继续搅拌0.5h,过滤分离得络合物溶液;d. 用icp-aes测定步骤c所得络合物溶液中钴、锂元素的质量浓度,加入碳酸锂调
节溶液中钴、锂元素摩尔浓度比为1:1,搅拌均匀后冻干溶剂,于箱式炉中700℃煅烧4h,冷却后固体经气流粉碎得再生钴酸锂。
[0030]
在对钴、锂元素质量浓度进行测定时,同时检出了钴元素质量浓度0.1倍左右的铝元素。
[0031]
对比例2对比例2相较于实施例1使用盐酸替换抗坏血酸;a. 采用盐水放电使废旧锂电池彻底放电,拆解分选出正极片;b.将步骤a所得正极片裁剪为10cm
×
10cm的小块,置于330mm
×
330mm
×
100mm尺寸的莫来石匣钵中,放入箱式炉中真空煅烧,保持维持真空度为-0.7mpa,煅烧温度为500℃,煅烧时间为2h,煅烧过程中定时抽出废气,废气导入碱缸吸收。煅烧后的正极片经气流粉碎得到正极粉体;c.对步骤b所得正极粉体置于超声震动筛内振动分离,上层选用50目振动筛,下层选用300振动筛,收集300目筛下物,得到钴酸锂粗粉;d. 用浓度为1.5mol/l盐酸溶液对步骤c所得钴酸锂粗粉进行浸出,固液比为20g/l,60℃下超声浸出70min,过滤得到浸出液;向浸出液中加入质量分数为10%的氨水至浸出液中不再有沉淀析出也不再有沉淀溶解,加入氨水质量一半的质量分数为3%的双氧水溶液继续搅拌0.5h,过滤分离得络合物溶液;e. 用icp-aes测定步骤d所得络合物溶液中钴、锂元素的质量浓度,加入碳酸锂调节溶液中钴、锂元素摩尔浓度比为1:1,搅拌均匀,蒸出氯化铵后冻干溶剂,于箱式炉中700℃煅烧4h,冷却后固体经气流粉碎得再生钴酸锂。
[0032]
在对钴、锂元素质量浓度进行测定时,同时检出了远超钴、锂元素浓度的氯离子。
[0033]
对比例3对比例3相较于实施例1未添加氨水进行络合;a. 采用盐水放电使废旧锂电池彻底放电,拆解分选出正极片;b.将步骤a所得正极片裁剪为10cm
×
10cm的小块,置于330mm
×
330mm
×
100mm尺寸的莫来石匣钵中,放入箱式炉中真空煅烧,保持维持真空度为-0.7mpa,煅烧温度为500℃,煅烧时间为2h,煅烧过程中定时抽出废气,废气导入碱缸吸收。煅烧后的正极片经气流粉碎得到正极粉体;c.对步骤b所得正极粉体置于超声震动筛内振动分离,上层选用50目振动筛,下层选用300振动筛,收集300目筛下物,得到钴酸锂粗粉;d. 用浓度为1.5mol/l抗坏血酸溶液对步骤c所得钴酸锂粗粉进行浸出,固液比为20g/l,60℃下超声浸出70min,过滤得到浸出液;加入抗坏血酸溶液等体积质量分数为3%的双氧水溶液继续搅拌0.5h,过滤分离得混合溶液;e. 用icp-aes测定步骤d所得混合溶液中钴、锂元素的质量浓度,加入碳酸锂调节溶液中钴、锂元素摩尔浓度比为1:1,搅拌均匀,冻干后于箱式炉中700℃煅烧4h,冷却后固体经气流粉碎得再生钴酸锂。
[0034]
在对钴、锂元素质量浓度进行测定时,同时检出了浓度不等的镍离子、锰离子、铁离子、镁离子、钙离子、铜离子。
[0035]
使用未再生处理的钴酸锂作为对比例4,将实施例1~3及对比例1~4所得钴酸锂分
别分散于nmp中,加入粘结剂pvdf制得正极活性物质浆料,并涂覆于铝箔上烘干作为正极极片,用涂碳铜箔作为负极极片,加入电解液和隔膜,分别组装锂离子电池,对实施例1~3,对比例1~4的锂离子电池的重量比容量、放电倍率性能、循环性能进行测试。
[0036]
如图3所示,在0.1c充放电时,实施例1的锂电池比容量优于对比例2~4,且明显优于未对钴酸锂再生处理的对比例4,而对比例1的锂电池比容量要略优于实施例1,这可能与对比例1中钴酸锂含有铝元素掺杂有关,可以在具体应用中提高钴酸锂的性能。
[0037]
如图4所示,在不同的放电电流下,实施例1~3的质量比容量都要优于对比例1~4,可见对比例1的钴酸锂中铝元素未除尽,对比例2的钴酸锂中混入氯元素,对比例3的钴酸锂中未除尽的镍离子、锰离子、铁离子、镁离子、钙离子、铜离子,都会降低锂电池整体的放电倍率性能。
[0038]
如图5所示,实施例1~3及对比例1~4的锂电池在循环20次以内比容量均基本保持不变,但实施例1的锂电池的质量比容量要明显高于对比例1~4,相较于对比例4未对钴酸锂进行再生的锂电池,实施例1的质量比容量有大幅提升,而对比例1~3的钴酸锂纯度较低,杂质元素会对循环过程中的比容量产生明显影响。