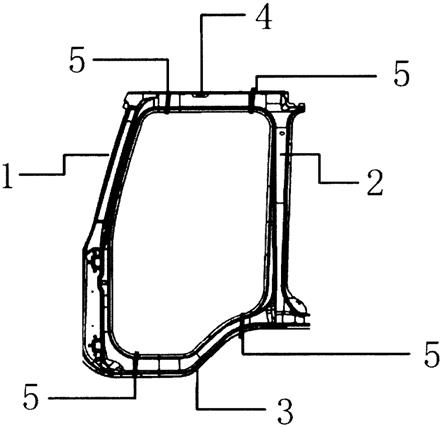
1.本发明涉及汽车制造领域,特别是一种四片式激光拼焊商用车侧围门框及其加工方法。
背景技术:
2.随着国家第六阶段机动车污染物排放标准的发布和实施,对商用车汽车的二氧化碳排放量限制越来越严格,同时国家对商用汽车的碰撞安全性要求越来越高。因此,未来商用车新车型开发必须考虑轻量化方案,提高驾驶室材料利用率,同时又确保驾驶室的侧碰满足要求,而驾驶室侧围门框是影响驾驶室轻量化及碰撞安全性能最重要的零件。传统的商用车侧围门框通过减少侧围门框厚度(厚度为1.0mm)满足轻量化需求,导致侧围门框a柱和b柱区域刚度不足,需要增加多层补丁板才能满足国标要求。通过增加加强板的方式可以满足碰撞法规要求,但成本较高,同时无法满足轻量化需求。而采用四片式激光拼焊板形式的侧围门框,可以通过合理分片、优化排样和高强减薄,大幅提升材料利用率,降低材料成本,并实现结构轻量化。
技术实现要素:
3.为了解决上述技术问题,本发明提供了一种四片式激光拼焊商用车侧围门框及其加工方法,有效提升材料利用率,降低材料成本,并实现结构轻量化。
4.根据本发明的一个方面,涉及了一种四片式激光拼焊商用车侧围门框,采用四片式激光拼焊坯料整体式冲压成形的侧围门框。
5.所述的四片式激光拼焊商用车侧围门框的加工方法,其特征在于,采用分序拼焊法,步骤如下:
6.1)将第一料片、第二料片、第三料片激光拼焊成“u”型;
7.2)采用精剪设备剪去第一料片、第二料片的端部;
8.3)将第四料片激光拼焊在“u”型结构的开口处。
9.根据本发明的至少一个实施方式,所述第一料片为a柱、第二料片为b柱、第三料片为横梁、第四料片为上边梁。
10.根据本发明的至少一个实施方式,所述拼焊的焊缝分布在横梁、上边梁。
11.根据本发明的至少一个实施方式,所述第一料片为上边梁、第二料片为横梁、第三料片为a柱、第四料片为b柱。
12.根据本发明的至少一个实施方式,所述拼焊的焊缝分布在a柱、b柱。。
13.本发明的实质性特点和进步是:
14.本发明的技术方案考虑激光拼焊板的优势,可以将不同材质、不同厚度及不同表面状态的板材拼接在一起,商用车侧围门框采用四片式激光拼焊板冲压成形,四片料片可以不同材质、不同厚度及不同表面状态,满足产品各种使用性能要求的同时,大幅提升材料利用率,降低材料成本,并实现结构轻量化。本发明的的优点:
15.1.本发明通过四片式激光拼焊板冲压成形的商用车侧围门框,可提升材料利用率,降低材料成本,实现结构轻量化;
16.2.本发明采用的四片式激光拼焊加工方法,适用于直线激光拼焊设备和曲线激光拼焊设备;
17.3.本发明采用的四片式激光拼焊加工方法,能有效控制激光拼焊精度和质量,避免四片式激光拼焊板框架式结构冲压成形时因应力集中而开裂。
附图说明
18.图1是根据本发明一个实施方式的在上边梁、横梁上分缝的侧围门框结构示意图。
19.图2是图1的侧围门框结构的四片式激光拼焊板及分序拼焊示意图。
20.图3是根据本发明一个实施方式的在a柱、b柱上分缝的侧围门框结构示意图。
21.图4是图3的侧围门框结构的四片式激光拼焊板及分序拼焊示意图。
22.图中零部件序号及名称:
23.a柱1、b柱2、横梁3、上边梁4、焊缝5。
具体实施方式
24.下面结合附图和实施方式对本发明作进一步的详细说明。可以理解的是,此处所描述的具体实施方式仅用于解释相关内容,而非对本发明的限定。另外还需要说明的是,为了便于描述,附图中仅示出了与本发明相关的部分。
25.需要说明的是,在不冲突的情况下,本发明中的实施方式及实施方式中的特征可以相互组合。下面将参考附图并结合实施方式来详细说明本发明。
26.在本发明的至少一个实施例中,如图1-4所示,本发明提供了一种四片式激光拼焊商用车侧围门框,采用四片式激光拼焊坯料整体式冲压成形的侧围门框。
27.四片式激光拼焊商用车侧围门框的加工方法,采用分序拼焊法,步骤如下:
28.1)将第一料片、第二料片、第三料片激光拼焊成“u”型;
29.2)采用精剪设备剪去第一料片、第二料片的端部;
30.3)将第四料片激光拼焊在“u”型结构的开口处。
31.根据本发明的又一个实施方式,所述第一料片为a柱1、第二料片为b柱2、第三料片为横梁3、第四料片为上边梁4。
32.所述拼焊的焊缝5分布在横梁3、上边梁4。
33.这是以满足侧围门框成型性能、使用性能、外观要求为主的分缝方法
34.根据本发明的又一个实施方式,所述第一料片为上边梁4、第二料片为横梁3、第三料片为a柱1、第四料片为b柱2。所述拼焊的焊缝5分布在a柱1、b柱2。
35.这是以满足侧围门框材料提升和低成本为主的分缝方法。
36.本发明采用四片式激光拼焊板整体式冲压成形的商用车侧围门框,大幅提升材料利用率,降低材料成本,并实现结构轻量化;采用的四片式激光拼焊板加工方法,能保证四片式激光拼焊坯料的加工精度及质量,生产上易于实现,经济效果明显,且可实现汽车车身轻量化,节能环保。
37.以上所述,仅为本发明的具体实施方式,但本发明的保护范围并不局限于此,任何
不经过创造性劳动想到的变化或替换,都应涵盖在本发明的保护范围之内。因此,本发明的保护范围应该以权利要求书所限定的保护范围为准。
技术特征:
1.一种四片式激光拼焊商用车侧围门框,其特征在于:采用四片式激光拼焊坯料整体式冲压成形的侧围门框。2.根据权利要求1所述的四片式激光拼焊商用车侧围门框的加工方法,其特征在于,采用分序拼焊法,步骤如下:1)将第一料片、第二料片、第三料片激光拼焊成“u”型;2)采用精剪设备剪去第一料片、第二料片的端部;3)将第四料片激光拼焊在“u”型结构的开口处。3.根据权利要求2所述的四片式激光拼焊商用车侧围门框的加工方法,其特征在于:所述第一料片为a柱、第二料片为b柱、第三料片为横梁、第四料片为上边梁。4.根据权利要求3所述的四片式激光拼焊商用车侧围门框的加工方法,其特征在于:所述拼焊的焊缝分布在横梁、上边梁。5.根据权利要求2所述的四片式激光拼焊商用车侧围门框的加工方法,其特征在于:所述第一料片为上边梁、第二料片为横梁、第三料片为a柱、第四料片为b柱。6.根据权利要求5所述的四片式激光拼焊商用车侧围门框的加工方法,其特征在于:所述拼焊的焊缝分布在a柱、b柱。
技术总结
本发明公开了一种四片式激光拼焊商用车侧围门框,采用四片式激光拼焊坯料整体式冲压成形的侧围门框。加工方法采用分序拼焊法,步骤如下:1)将第一料片、第二料片、第三料片激光拼焊成“U”型;2)采用精剪设备剪去第一料片、第二料片的端部;3)将第四料片激光拼焊在“U”型结构的开口处。本发明大幅提升材料利用率,降低材料成本,并实现结构轻量化;采用的四片式激光拼焊板加工方法,能保证四片式激光拼焊坯料的加工精度及质量,生产上易于实现,经济效果明显,且可实现汽车车身轻量化,节能环保。节能环保。节能环保。
技术研发人员:唐铖锽 王承刚 王作孔
受保护的技术使用者:柳州宝钢汽车零部件有限公司
技术研发日:2021.09.22
技术公布日:2022/1/28