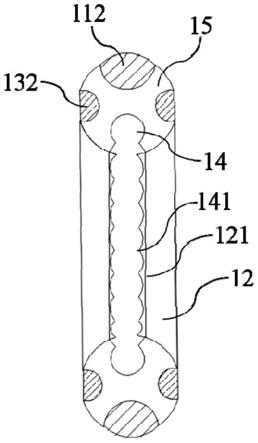
1.本实用新型涉及免充气轮胎技术领域,更具体地说是一种内腔延展周期性波浪式免充气轮胎。
背景技术:
2.免充气轮胎因其无需充气维护方便、使用寿命长、不怕扎、耐磨等优点而被广泛关注与推广应用,免充气轮胎包括免充气实心轮胎和免充气空心轮胎,传统模压工艺对于免充气实心轮胎的生产已十分成熟,但免充气空心轮胎难以依靠传统模压工艺完成。与此同时,免充气轮胎在骑行中的舒适性问题未得到根本性解决且生产工艺也相对较为复杂。
3.经检索,为解决上述问题,如中国专利,公开号为:cn109109352a、公开日为:2019 年1月1日;公开了一种橡胶制品一次性注射、中空以及硫化成型生产方法,该方法能够在同一模腔内完成注射、中空和硫化工序,所述模腔包括上半模具、下半模具和模芯,模芯为模腔的中空奠定基础,中空后具备了充入硫化所需要的高温高压气体的条件,进而将注射成型、中空以及硫化装置集成化,避免了现有技术中各工序流转造成的热量流失和工序流转成本,虽然大大改善了传统工艺工序复杂的缺点,简化了制作工序,但是通过对该工艺的使用,发现该工艺虽理论上可实现全自动化生产,但在实际生产过程中因中空轮胎硫化成型时,需通入高温气体或压缩空气等对其内腔加热,发现中空轮胎成品率较低,同时需要高温气体或压缩空气等发生设备运行过程中而存在安全隐患且增加产品实现工艺的负责系数,故难以实现大规模工业化生产。
技术实现要素:
4.1.实用新型要解决的技术问题
5.针对传统轮胎骑行易被扎破而出现安全事故及其维护困难等问题,本实用新型提出一种内腔延展周期性波浪式免充气轮胎,将混炼好的胶料经过螺杆挤出机挤出胎腹上形成胎腹凹槽的轮胎胚条,再借助工件将轮胎胚条包覆在模芯构件上,使得模芯构件等间距嵌入胎腹凹槽内形成若干组内腔凹槽,各内腔凹槽相连形成延展周期性波浪式的内腔,从而保证轮胎既具备传统环腔结构的舒适性,又具备传统囊腔结构的支撑强度。
6.2.技术方案
7.为达到上述目的,本实用新型提供的技术方案为:
8.一种内腔延展周期性波浪式免充气轮胎,包括经过螺杆挤出机挤出的轮胎胚条,所述轮胎胚条包括胎冠和胎腹,所述胎腹上沿其周向开设有胎腹凹槽,所述胎腹凹槽内部沿其周向等间距设置有若干组内腔凹槽,所述内腔凹槽首尾相连形成延展周期性波浪式的内腔,所述内腔包括间隔设置的凸出部,相邻所述凸出部之间向内凹陷形成凹陷部,使得本实用新型的轮胎既具备传统环腔结构的舒适性,又具备传统囊腔结构的支撑强度。
9.进一步的技术方案,所述胎冠上沿其周向开设有胎冠凹槽,所述胎冠凹槽内填充有物料 a,所述物料a为高耐磨、抗湿滑胎面橡胶材料,以解决模压工艺中轮胎接头处凹凸
不平而引发的轮胎跳动、甚至出现断裂而造成安全隐患并可进行其消除或事先预警等问题。
10.进一步的技术方案,还包括胎侧部,所述胎侧部的中部沿其周向开设有胎侧部凹槽,所述胎侧部凹槽内填充有物料b,所述物料b为发泡等有关轻质缓冲材料,将不与地面接触的胎侧部使用轻质缓冲材料,并与使用高耐磨、抗湿滑胎面橡胶材料的胎冠复合,从而尽可能减轻胎体重量、节约成本,还能够保证胎体足够的支撑强度、提高轮胎的使用寿命。
11.一种内腔延展周期性波浪式免充气轮胎的加工方法,包括如下步骤:
12.步骤一、挤出轮胎胚条:将混炼好的胶料使用螺杆挤出机挤出胎腹上沿其周向开设有胎腹凹槽的轮胎胚条;
13.步骤二、预成型准备:将挤出的轮胎胚条依据所述尺寸裁取成段,然后借助工装将其包覆在模芯构件上,使得模芯构件沿着胎腹等间距嵌入胎腹凹槽内,所述胎腹凹槽能够保证模芯构件准确对准插入,还能够起到限位与卡紧的作用,以保证后续成型工序的顺利进行;
14.步骤三、预成型:将步骤二中的轮胎胚条放置在预成型模具中,并使得轮胎胚条完全置于上模腔和下模腔的内部后盖合上模和下模,使得模芯构件前端的模芯构件头端置于胎腹凹槽内,模芯构件后端的模芯构件尾端通过出模通孔预留在轮胎胚条外部,以便于模芯构件取出,并降低开模取放模芯构件所产生的能耗;
15.步骤四、胎冠处注射成型:沿着注射管i向胎冠凹槽内注射物料a,所述物料a为高耐磨、抗湿滑胎面橡胶材料;
16.步骤五、胎侧部注射成型:沿着注射管ii向胎侧部凹槽内注射物料b,所述物料b为发泡等有关轻质缓冲材料;
17.步骤六、硫化成型:对预成型模具内部的轮胎胚条进行硫化处理,硫化处理过程中,模芯构件留置于轮胎胚条内部,以避免硫化反应时胎腹凹槽精度出现尺寸公差;
18.步骤七、取出模芯构件:沿着出模通孔轴线方向将所述模芯构件取出后,由所述模芯构件在胎腹凹槽内形成的各个相邻的内腔凹槽首尾相连形成延展周期性波浪式的内腔,以起到兼具加强轮胎结构强度和提高轮胎胎体的缓冲能力的作用,进一步增强骑行舒适性,节省骑行电耗;
19.步骤八、出模:拆除上模和下模,打开上模腔和下模腔,取出成型后的轮胎。
20.进一步的技术方案,所述模芯构件的水平面投影形状为半椭圆形,包括模芯构件头端和模芯构件尾端;所述模芯构件头端和模芯构件尾端接触面的最大外径小于等于所述出模通孔的外径,使得模芯构件头端易于从出模通孔中拔出。
21.3.有益效果
22.采用本实用新型提供的技术方案,与现有技术相比,具有如下有益效果:
23.(1)本实用新型的一种内腔延展周期性波浪式免充气轮胎,将混炼好的胶料经过螺杆挤出机挤出胎腹上形成胎腹凹槽的轮胎胚条,再借助工件将轮胎胚条包覆在模芯构件上,使得模芯构件等间距嵌入胎腹凹槽内形成若干组内腔凹槽,所述胎腹凹槽能够保证模芯构件准确对准插入,还能够起到限位与卡紧的作用,以保证后续成型工序的顺利进行;各内腔凹槽相连形成延展周期性波浪式的内腔,从而保证轮胎既具备传统环腔结构的舒适性,又具备传统囊腔结构的支撑强度;
24.(2)本实用新型的一种内腔延展周期性波浪式免充气轮胎,模芯构件的水平面投影形状为半椭圆形,包括模芯构件头端和模芯构件尾端;所述模芯构件头端和模芯构件尾端接触面的最大外径小于等于所述出模通孔的外径,使得模芯构件头端易于从出模通孔中拔出。
25.(3)本实用新型的一种内腔延展周期性波浪式免充气轮胎,所述轮胎胚条包括胎冠,所述胎冠上沿其周向开设有胎冠凹槽,所述胎冠凹槽内填充有物料a,所述物料a为高耐磨、抗湿滑胎面橡胶材料,以解决模压工艺中轮胎接头处凹凸不平而引发的轮胎跳动、甚至出现断裂而造成安全隐患并可进行其消除或事先预警等问题;
26.(4)本实用新型的一种内腔延展周期性波浪式免充气轮胎,还包括胎侧部,所述胎侧部的中部沿其周向开设有胎侧部凹槽,所述胎侧部凹槽内填充有物料b,所述物料b为发泡等有关轻质缓冲材料,将不与地面接触的胎侧部使用轻质缓冲材料,并与使用高耐磨、抗湿滑胎面橡胶材料的胎冠复合,从而尽可能减轻胎体重量、节约成本,还能够保证胎体足够的支撑强度、提高轮胎的使用寿命。
附图说明
27.图1为实用新型的免充气双密度层轮胎立体结构示意图;
28.图2为图1的免充气双密度层轮胎物料填充后结构示意图;
29.图3为图1的左视图;
30.图4为图1的纵向剖切结构示意图;
31.图5为图1的横向剖切结构示意图;
32.图6为图4物料充填完成后的纵向剖切结构示意图;
33.图7为图5中内腔凹槽的凹陷部纵向剖切结构示意图;
34.图8为本实用新型的免充气双密度层轮胎成型模具结构示意图;
35.图9为本实用新型的中模模芯构件结构示意图。
36.图中:1-轮胎胚条、2-预成型模具、3-注射管i、4-注射管ii、5-模芯构件、11-胎冠、12
‑ꢀ
胎腹、13-胎侧部、14-内腔凹槽、21-上模、22-下模、23-上模腔、24-下模腔、25-出模通孔、 51-模芯构件头端、52-模芯构件尾端、111-胎冠凹槽、112-物料a、121-胎腹凹槽、131-胎侧部凹槽、132-物料b、141-内腔、142-凸出部、143-凹陷部。
具体实施方式
37.为进一步了解本实用新型的内容,结合附图对实用新型作详细描述。
38.实施例1
39.本实施例的一种内腔延展周期性波浪式免充气轮胎,如图2所示,包括经过螺杆挤出机挤出的轮胎胚条1,所述轮胎胚条1包括胎冠11和胎腹12,如图4~5所述胎腹12上沿其周向开设有胎腹凹槽121,所述胎腹凹槽121内部沿其周向等间距设置有若干组内腔凹槽14,所述内腔凹槽14首尾相连形成延展周期性波浪式的内腔141,如图6~7所示,所述内腔141 包括间隔设置的凸出部142,相邻所述凸出部142之间向内凹陷形成凹陷部143。骑行过程中,波浪式凸出部142呈圆润椭球状(椭球且扁平);间隔的凹陷部143从凸出部142向内凹陷,并由厚变薄再变厚,使得本实用新型的轮胎既具备传统环腔结构的舒适性,又具备传统
囊腔结构的支撑强度。
40.实施例2
41.本实施例的一种内腔延展周期性波浪式免充气轮胎,基本结构同实施例1,不同和改进之处在于:如图1、3、6所示,所述胎冠11上沿其周向开设有胎冠凹槽111,所述胎冠凹槽 111内填充有物料a112,所述物料a112为高耐磨、抗湿滑胎面橡胶材料,以解决模压工艺中轮胎接头处凹凸不平而引发的轮胎跳动、甚至出现断裂而造成安全隐患并可进行其消除或事先预警等问题。
42.如图4、6所示,还包括胎侧部13,所述胎侧部13的中部沿其周向开设有胎侧部凹槽131,所述胎侧部凹槽131内填充有物料b132,所述物料b132为发泡等有关轻质缓冲材料,将不与地面接触的胎侧部13使用轻质缓冲材料,并与使用高耐磨、抗湿滑胎面橡胶材料的胎冠 11复合,从而尽可能减轻胎体重量、节约成本,还能够保证胎体足够的支撑强度、提高轮胎的使用寿命。
43.实施例3
44.本实施例的一种内腔延展周期性波浪式免充气轮胎的加工方法,基本结构同实施例2,不同和改进之处在于:如图4~8所示,包括如下步骤:
45.步骤一、挤出轮胎胚条1:将混炼好的胶料使用螺杆挤出机挤出胎腹12上沿其周向开设有胎腹凹槽121的轮胎胚条1;
46.步骤二、预成型准备:将挤出的轮胎胚条1依据所述尺寸裁取成段,然后借助工装将其包覆在模芯构件5上,使得模芯构件5沿着胎腹12等间距嵌入胎腹凹槽121内,所述胎腹凹槽121能够保证模芯构件5准确对准插入,还能够起到限位与卡紧的作用,以保证后续成型工序的顺利进行;
47.步骤三、预成型:将步骤二中的轮胎胚条1放置在预成型模具2中,并使得轮胎胚条1 完全置于上模腔23和下模腔24的内部后盖合上模21和下模22,使得模芯构件5前端的模芯构件头端51置于胎腹凹槽121内,模芯构件5后端的模芯构件尾端52通过出模通孔25预留在轮胎胚条1外部,以便于模芯构件5取出,并降低开模取放模芯构件5所产生的能耗;
48.步骤四、胎冠11处注射成型:沿着注射管i3向胎冠凹槽111内注射物料a112,所述物料a112为高耐磨、抗湿滑胎面橡胶材料;
49.步骤五、胎侧部13注射成型:沿着注射管ii4向胎侧部凹槽131内注射物料b132,所述物料b132为发泡等有关轻质缓冲材料;
50.步骤六、硫化成型:对预成型模具2内部的轮胎胚条1进行硫化处理,硫化处理过程中,模芯构件5留置于轮胎胚条1内部,以避免硫化反应时胎腹凹槽121精度出现尺寸公差;
51.步骤七、取出模芯构件5:沿着出模通孔25轴线方向将所述模芯构件5取出后,由所述模芯构件5在胎腹凹槽121内形成的各个相邻的内腔凹槽14首尾相连形成延展周期性波浪式的内腔141,以起到兼具加强轮胎结构强度和提高轮胎胎体的缓冲能力的作用,进一步增强骑行舒适性,节省骑行电耗;
52.步骤八、出模:拆除上模21和下模22,打开上模腔23和下模腔24,取出成型后的轮胎。
53.本实施例中,胎腹12(轮胎与轮辋贴合底面)到胎冠11的间距≤对应模腔之间的距离,以保证轮胎胚条1放入上模腔23和下模腔24中以后周向留有间隙;胎侧部13之间(上下
厚度)的距离大于上模腔23和下模腔24合模后的高度。合模时,上模21和下模22的压力使轮胎胚条1完成约束力下的形变(即在保证胶料灌满模腔的同时,胎腹凹槽121会全方位“咬合”槽内的模芯构件5),以保证轮胎胚条1内部结构和胎体的完整统一。
54.实施例4
55.本实施例的一种内腔延展周期性波浪式免充气轮胎的加工方法,基本结构同实施例3,不同和改进之处在于:如图8所示,所述模芯构件5的水平面投影形状为半椭圆形,包括模芯构件头端51和模芯构件尾端52;所述模芯构件头端51和模芯构件尾端52接触面的最大外径小于等于所述出模通孔25的外径,使得模芯构件头端51易于从出模通孔25中拔出。
56.以上示意性的对本实用新型及其实施方式进行了描述,该描述没有限制性,附图中所示的也只是本实用新型的实施方式之一,实际的结构并不局限于此。所以,如果本领域的普通技术人员受其启示,在不脱离本实用新型创造宗旨的情况下,不经创造性的设计出与该技术方案相似的结构方式及实施例,均应属于本实用新型的保护范围。