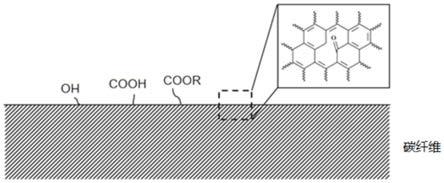
1.本发明涉及建筑材料技术领域,特别是涉及一种碳纤维增强的超高性能混凝土及其制备方法。
背景技术:
2.超高性能混凝土(uhpc),也叫做活性粉末混凝土,有着超强的抗压强度(120mpa以上)、低孔隙率以及优异的耐久性,在土木建筑领域中得到了广泛重视,尤其是往超高层、轻质化、大跨度方向发展。由于超高性能混凝土存在抗拉能力弱、韧性差的问题,通常会将钢纤维作为增韧材料掺入超高性能混凝土中,以提高其韧性和延性。
3.在二十世纪时期,超高性能混凝土的研究追求高强度高性能的发展。随后,研究重心发生了转移,主要集中于减少二氧化碳排放以及降低初始材料成本,以遵循环保与经济的理念。现如今海洋资源储备充足,但是利用率很低。海水海砂中有着氯离子、硫酸根离子等大量侵蚀性离子,易导致超高性能混凝土中的钢纤维发生锈蚀,引起开裂,缩减了构件的使用寿命。
4.因此,有必要研发一种具有较强耐蚀性、韧性好的超高性能混凝土。
技术实现要素:
5.针对现有技术中存在的技术问题,本发明的目的之一在于:提供一种碳纤维增强的超高性能混凝土,其碳纤维-基体界面结构不容易受海水海砂中侵蚀性离子破坏,具有较强的耐蚀性。
6.针对现有技术中存在的技术问题,本发明的目的之二在于:提供一种碳纤维增强的超高性能混凝土的制备方法,制备得到的超高性能混凝土具有较强的耐蚀性。
7.为了达到上述目的,本发明采用如下技术方案:
8.一种碳纤维增强的超高性能混凝土,以重量份计,包括以下组分,胶凝材料535~700份、骨料0~420份、水70~150份、减水剂7~35份和碳纤维1~10份。
9.进一步,以重量份计,包括以下组分,胶凝材料535~665份、骨料35~420份、水70~150份、减水剂7~35份和碳纤维1~7份。
10.进一步,碳纤维为经过表面氧化处理的pan基碳纤维。
11.进一步,碳纤维长2~5毫米,直径6~8微米,拉伸强度为4000~5000mpa,弹性模量为230~300gpa,断裂延伸率为1.7%~2.3%。
12.进一步,骨料包括河砂和或海砂,水包括淡水和或海水。
13.进一步,胶凝材料为硅酸盐水泥和硅灰,减水剂为固含量占20%且减水率为33.4%的聚羧酸型减水剂。
14.一种碳纤维增强的超高性能混凝土的制备方法,包括以下步骤,
15.将以重量份计的535~700份胶凝材料、0~420份骨料、70~150份水、7~35份减水剂和1~10份碳纤维混合搅拌得到浆体;
16.将浆体固化后,放入水中养护,得到碳纤维增强的超高性能混凝土。
17.进一步,碳纤维为pan基碳纤维,pan基碳纤维加入混合搅拌前先经过表面氧化处理,以增加pan基碳纤维表面的含氧官能团数量。
18.进一步,pan基碳纤维表面氧化处理的步骤为,将pan基碳纤维置于施加有电流的nh4h2po4电解液中进行表面氧化处理。
19.进一步,浆体的制备过程包括以下步骤,
20.将水与碳纤维按照预设的配比混合,然后进行超声分散得到混合溶液;将胶凝材料、减水剂与骨料按照预设的分量混合,得到混合干料;将混合溶液加入混合干料搅拌后得到浆体。
21.总的说来,本发明具有如下优点:
22.碳纤维本身是一种化学稳定性良好的材料,当cl-、so
42-等侵蚀性离子侵入到碳纤维与水化产物的界面时,由于碳纤维表面c元素十分稳定,不与cl-、so
42-发生化学反应,所以碳纤维增强的超高性能混凝土表面的碳纤维-基体界面结构不容易受海水海砂中侵蚀性离子破坏,具有较强的耐蚀性。
附图说明
23.图1为碳纤维表面活性官能团示意图。
24.图2为碳纤维桥连作用示意图。
具体实施方式
25.下面结合实施例对本发明作进一步详细地描述。对比例以及所有实施例中制备的超高性能混凝土原材料中,胶凝材料为普通硅酸盐水泥(p.ⅱ.52.5r)和硅灰(比表面积为20000m2/kg,烧失量为4%,二氧化硅的质量百分比为92%);减水剂为固含量占20%且减水率为33.4%的聚羧酸型高效减水剂。海水和海砂均来源于广东珠江口。
26.现如今淡水资源匮乏、河砂成本上升,反观海洋资源储备充足,但是利用率很低。现有技术的超高性能混凝土中通常掺有钢纤维,而海水和海砂等海洋资源中含有大量的侵蚀性离子(cl-、so
42-),如果用于常规的钢纤维增韧超高性能混凝土中,容易使钢纤维发生锈蚀,产生的锈蚀产物甚至是原来体积的三倍,易发生体积膨胀致使混凝土出现开裂、失效的问题。因此制约了钢纤维超高性能混凝土中的使用。
27.由此,为了拓展海水海砂的利用程度,克服长期以来淡水资源匮乏的问题,本技术提出了一种碳纤维增强的超高性能混凝土,包括:胶凝材料535~700份、骨料0~420份、水70~150份、减水剂7~35份和碳纤维1~10份。
28.在一些实施例中,胶凝材料可以包括水泥,其中可以采用p.ⅱ.52.5r硅酸盐水泥,其比表面积≥300m2/kg,28天抗压强度≥52.5mpa,28天抗折强度≥7mpa。
29.在一些实施例中,胶凝材料还可以包括硅灰,其中,硅灰中二氧化硅质量百分比大于90%,且硅灰的比表面积不低于14000m2/kg。
30.在一些实施例中,骨料可以包括天然砂和或机制砂,比如河砂、海砂、石英砂等的其中一种或多种。
31.在一些实施例中,水可以包括淡水和或海水。
32.在一些实施例中,上述超高性能混凝土还可以包括液态的聚羧酸减水剂,其中,所述聚羧酸减水剂的固含量为20%~35%,且减水率不低于35%。
33.作为对比,提供了以下对比例:
34.对比例1:本对比例中采用的骨料为26~40目和40~70目两种石英砂,拌合水采用普通的淡水,且未掺入碳纤维。按照本发明要求进行搅拌、成型和养护。
35.对比例2:本对比例中以海砂代替石英砂,以海水代替普通淡水,且未掺入碳纤维。按照本发明要求进行搅拌、成型和养护。
36.对比例3:本对比例在对比例1的基础上,掺入长度为5mm未改性的pan基碳纤维,其他步骤一致。
37.实施例1:本实施例在对比例1的配合比基础上,掺入纤维长度为2mm的pan基改性碳纤维,碳纤维掺量占总质量的0.28%(约占总体积的0.5%)。按照本发明要求进行搅拌、成型和养护。
38.实施例2:本实施例在对比例1的配合比基础上,掺入纤维长度为5mm的pan基改性碳纤维,碳纤维掺量占总质量的0.28%(约占总体积的0.5%)。按照本发明要求进行搅拌、成型和养护。
39.实施例3:本实施例在对比例1的配合比基础上,掺入纤维长度为10mm的pan基改性碳纤维,碳纤维掺量占总质量的0.28%(约占总体积的0.5%)。按照本发明要求进行搅拌、成型和养护。
40.实施例4:本实施例在对比例2的配合比基础上,掺入纤维长度为2mm的pan基改性碳纤维,碳纤维掺量占总质量的0.28%(约占总体积的0.5%)。按照本发明要求进行搅拌、成型和养护。
41.实施例5:本实施例在对比例2的配合比基础上,掺入纤维长度为5mm的pan基改性碳纤维,碳纤维掺量占总质量的0.28%(约占总体积的0.5%)。按照本发明要求进行搅拌、成型和养护。
42.实施例6:本实施例在对比例2的配合比基础上,掺入纤维长度为10mm的pan基改性碳纤维,碳纤维掺量占总质量的0.28%(约占总体积的0.5%)。按照本发明要求进行搅拌、成型和养护。
43.通过比较实施例2和5发现,海水海砂的使用对碳纤维增强的超高性能混凝土的力学性能和工作性能影响很小,其力学性能与工作性能的下降可能是受海砂中的贝壳含量影响。碳纤维本身是一种化学稳定性良好的材料,当cl-、so
42-等侵蚀性离子侵入到碳纤维与水化产物的界面时,由于碳纤维表面c元素十分稳定,不与cl-、so
42-发生化学反应,碳纤维-基体界面结构不受破坏,所以其表面呈现很强的耐蚀性,不易受海水以及海砂中的侵蚀性离子的腐蚀。
44.此外,发明人还发现,由于超高性能混凝土不同于常规混凝土,一是其新拌浆体流动性差、屈服应力大,二是浆体硬化后的结构的孔隙率很低,并且碳纤维表面呈现化学惰性,使得碳纤维与基体间的粘结力差,对混凝土的力学性能和工作性能有不利影响。
45.为此,本技术提供的一种碳纤维增强的超高性能混凝土,在一些实施例中,碳纤维可以是经过表面氧化处理的pan基碳纤维。所述经过表面氧化处理的pan基碳纤维是在施加有电流的nh4h2po4电解液中进行表面氧化处理的pan基碳纤维。经过表面氧化处理后的pan
基碳纤维表面的含氧官能团,如羟基、羰基、羧基或酯基,的数量增加。
46.其中,nh4h2po4电解液可以是质量分数为5~10wt%的nh4h2po4电解液。nh4h2po4电解液中施加的电流可以是电流密度为0.1~1.0a/cm2的微弱电流。表面氧化处理时间可以是50~100秒。表面氧化处理可以在恒温50℃度下进行。在表面氧化处理完成后,还可以用去离子水反复清洗pan基碳纤维表面,并在105℃烘箱中烘干12小时。
47.优选地,在一些实施例中,pan基碳纤维的表面氧化处理过程可以包括:将所述pan基碳纤维置于质量分数8wt%的nh4h2po4电解液中,施加电流密度为1.0a/cm2的微弱电流,在恒温50℃度下氧化处理60秒,然后用去离子水反复清洗,105℃烘箱烘干12小时,以使所述pan基碳纤维表面的含氧官能团数量增加。
48.通过比较对比例3和实施例2发现,如图1所示,由于超高性能混凝土致密的基体以及改性后碳纤维表面的活性官能团(羟基、羰基、羧基或酯基)数量增加,碳纤维与超高性能混凝土基体间形成氢键或更强的化学键,提高了碳纤维-基体间的界面粘结力。
49.此外,在现有的相关技术中,大多采用长度为7~20mm的纤维,因为理论上来说纤维越长,抵抗裂纹扩展的能力就越好。然而,发明人创造性地发现,随着裂纹穿越基体并不断增长,如果纤维自身强度能够承受裂纹尖端应力,那么裂纹则会穿过纤维,完整的纤维则会继续连接已经断裂的基体两端,形成“桥连裂缝”的作用,如图2所示。但碳纤维本身受剪切力能力非常差,碳纤维如果在超高性能混凝土基体的埋入长度过长,容易在搅拌过程以及纤维弯折处发生无效断裂(即碳纤维并非是在混凝土受外力时,为抵抗裂缝扩展而发生的断裂),没有充分利用纤维本身的抗拉强度,使其无法起到桥联裂缝的作用;此外,碳纤维过长在超高性能混凝土中容易团聚,使其分散不均,影响超高性能混凝土的工作性能。
50.为此,本技术提供的一种碳纤维增强的超高性能混凝土,首次提出了可以选用长2~5mm的碳纤维,其中,碳纤维的直径可以是6~8微米。
51.通过上述实施例1~3的对比以及实施例4~6的对比可知,本发明碳纤维增强的超高性能混凝土中添加了长度为2~5mm的改性碳纤维,在保持碳纤维掺量不变的同时减小纤维长度,能够有效提高纤维的桥联作用,同时也能改善超高性混凝土的流动性。
52.碳纤维本身优异的化学稳定性可以实现对海水海砂的资源化利用;表面改性的碳纤维与超高性能混凝土基体形成更致密的界面,优化碳纤维在超高性能混凝土中的临界长度,使相同体积分数掺量下,减小纤维长度,提高超高性能混凝土的韧性和延性,在利用海水、海砂制备超高性能混凝土时,碳纤维能够有效地抵抗侵蚀性离子的化学侵蚀,解决了海水海砂无法用于制备超高性能混凝土的技术问题。
53.表1本发明的碳纤维增强的超高性能混凝土对比例和实施例配比
[0054][0055]
表2本发明对比例和实施例的力学性能和工作性能
[0056]
编号扩展度(mm)抗压强度(mpa)抗折强度(mpa)对比例1235135.714.5对比例2233130.214.0对比例3215143.316.3实施例1220140.516.1实施例2216146.817.8实施例3193139.115.8实施例4215137.715.4实施例5210140.416.9实施例6190135.415.6
[0057]
碳纤维增强的超高性能混凝土具体的制备过程可以包括以下步骤:
[0058]
(1)按原材料配比称好各组分的量,首先将海水与聚羧酸减水剂混合并搅拌均匀,再加入称好的碳纤维,搅拌1min,并进行超声分散以利于碳纤维的分散,得到碳纤维分散均匀的水溶液。
[0059]
(2)将水泥、硅灰以及海砂三种干料预混合,搅拌0.5~1.5min,得到均匀的混合干料。
[0060]
(3)将步骤(1)所得的混合碳纤维的溶液加入到步骤(2)中的混合干料中,先以低速搅拌约2~3min;形成浆状后,再进行快搅2~3min,充分混合,将新拌浆体倒入模具中,放入相对湿度不低于95%、温度恒定在23℃的恒温恒湿箱中固化1天后,拆模。
[0061]
(4)采用常温养护加水养的方式,将已经固化的混凝土放入水中常规养护,直到28天,得到碳纤维增强的超高性能混凝土。
[0062]
上述实施例为本发明较佳的实施方式,但本发明的实施方式并不受上述实施例的限制,其他的任何未背离本发明的精神实质与原理下所作的改变、修饰、替代、组合、简化,均应为等效的置换方式,都包含在本发明的保护范围之内。