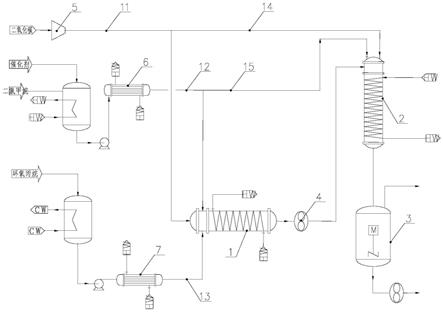
一种ppc合成系统及其合成工艺
技术领域
1.本发明涉及化学领域,特别涉及一种ppc合成系统及其合成工艺。
背景技术:
2.ppc(二氧化碳基可降解塑料),产品标准为gb/t 31124-2014,是po(环氧丙烷)、co2(二氧化碳)的共聚物。ppc既具有良好的延展性、断裂伸长、耐热性和抗冲击功能,又具有优良的生物降解性,是目前低碳环保、生物降解塑料之一。是可降解塑料中为数不多的可拉膜及高性能可降解塑料。ppc与pla(聚乳酸)和pbat(聚己二酸/对苯二甲酸丁二酯)共混改性后的可降解塑料,适用范围更大用途更广,如:包装薄膜、农用地膜、购物袋、垃圾袋、连卷袋、快递袋、外卖一次餐盒等,ppc农用地膜与传统地膜相比,具有降解优势,能节省回收土地污染的废塑料人工成本,在各地和多种农作物应用效果较好,如山东土豆、花生、洋葱等作物,除可降解优势外,还具有一定增产作用。
3.因此,如何低消耗、高效率的生产ppc,是本领域技术人员亟待解决的问题。
技术实现要素:
4.本发明的目的之一是针对现有技术的不足,提供一种ppc合成系统,其结构简单、操作方便、运行效率大幅提高,可低成本满足大规模生产ppc的生产需求。
5.本发明的目的之二是提供采用上述合成系统合成ppc的工艺,可有效提高原料po的聚合率达到99.9%以上。
6.实现本发明目的之一的技术方案是:一种ppc合成系统,包括预聚合反应器、终聚合反应器、终聚合闪蒸罐,所述预聚合反应器的进料口分别通过第一管路与二氧化碳源相连、第二管路与溶剂源相连、第三管路与po源相连,所述预聚合反应器的排料口经预聚合出料泵对终聚合反应器供料,终聚合反应器的进料口分别通过第四管路与二氧化碳源相连、第五管路与溶剂源相连,所述终聚合反应器的排料口与所述终聚合闪蒸罐相连。
7.进一步的,所述预聚合反应器为微界面绕管式固定床反应器,包括封闭的预聚合壳体,所述预聚合壳体内设置的预聚合绕管管内为预聚合冷媒介质通道,预聚合绕管和预聚合壳体之间的空间为预聚合物料通道,所述预聚合物料通道的上游端设置微界面发生器。
8.进一步的,所述预聚合冷媒介质通道为管道,包括第一段管道和第二段管道,第一段管道位于第二段管道的上方,所述第一段管道、第二段管道均呈往复折弯延伸,且第一段管道所在平面相对于第二段管道所在平面旋转90
°
。
9.进一步的,所述终聚合反应器为微界面绕管式固定床反应器,包括封闭的终聚合壳体,所述终聚合壳体内设置的终聚合绕管管内为终聚合物料通道,终聚合绕管和终聚合壳体之间的空间为终聚合冷媒介质通道,所述终聚合物料通道的上游端设置微界面发生器。
10.进一步的,所述终聚合物料通道为管道,由第三段管道和第四段管道连接构成,第
三段管道位于第四段管道的上方,所述第三段管道、第四段管道均呈往复折弯延伸,且第三段管道所在平面相对于第四段管道所在平面旋转90
°
。
11.进一步的,第一管路上设有二氧化碳压缩机,第二管路上设有溶剂加热器,第三管路上设有po加热器,所述第四管路与第一管路相连,位于二氧化碳压缩机的下游,所述第五管路与第二管路相连,位于溶剂加热器的下游。
12.实现本发明目的之二的技术方案是:采用任一上述合成系统合成ppc的工艺,包括以下步骤:
13.1)混合有催化剂的二氯甲烷、po、二氧化碳经微界面发生器进入预聚合反应器的预聚合物料通道,其中po和二氧化碳的摩尔比为1:0.52,控制预聚合温度为60-90℃、压力为1.0-4.0mpag,po聚合率为40-60%,得到预聚合物料,其中催化剂为柠檬酸盐络合物;
14.2)步骤1)得到的预聚合物料、补充的二氧化碳以及补充的混合有催化剂的二氯甲烷经微界面发生器进入终聚合反应器的终聚合物料通道,其中po和二氧化碳的摩尔比为1:1.10,控制终聚合温度为60-90℃、压力为1.0-4.0mpag,po聚合率为99.9%,得到终聚合物料;
15.3)终聚合物料进入终聚合闪蒸罐,排出的汽相送至二氧化碳单元回收二氧化碳及pc,排出的液相送至溶剂回收单元,脱除催化剂、少量未聚单体及回收溶剂后,得到ppc产品。
16.进一步的,步骤1)二氯甲烷的温度为50-80℃,po的温度为50-80℃,二氧化碳为50-80℃。
17.优选的,步骤1)预聚合反应器的预聚合冷媒介质通道的第一段管道通入40℃的温水作为冷媒介质,第二段管道通入50℃的温水作为冷媒介质。
18.优选的,步骤2)终聚合反应器的终聚合冷媒介质通道的第一段管道通入第一段管道通入40℃温水作为冷媒介质,第二段管道通入50℃的温水作为冷媒介质。
19.进一步的,步骤3)终聚合闪蒸罐的真空度为0.1bar(a)。
20.采用上述技术方案具有以下有益效果:
21.1、本发明ppc合成系统,通过预聚合反应器进行本体连续聚合、终聚合反应器进行溶液连续聚合,实现单线生产能力大、消耗低、三废少、投资低的技术效果。
22.2、本发明ppc合成系统,预聚合反应器的预聚合物料通道上游端设置有微界面发生器,使液相的po、气相的二氧化碳、固相的催化剂以微米形态均匀分布在溶剂中,增大气液固三相接触面积。其中的预聚合物料通道为预聚合绕管和预聚合壳体之间的空间,实现在预聚合绕管间强化预聚合物料掺混和扰动的目的。其中的预聚合绕管管内为预聚合冷媒介质通道,且预聚合冷媒介质通道为管道,包括第一段管道和第二段管道,第一段管道位于第二段管道的上方,所述第一段管道、第二段管道均呈往复折弯延伸,且第一段管道所在平面相对于第二段管道所在平面旋转90
°
,对管间流动的聚合物料起到变向掺混作用,有利于提高聚合转化率。通过增加绕管的数量、长度及截面积,可提供足够的换热面积,有效解决了传统搅拌聚合釜的传热系数过低的问题,且避免了预聚合物料的返混问题,可根据产能要求,设计单台产能5-50万吨/年的聚合釜,满足大规模生产的需求。由于预聚合反应器一段为聚合反应初期,反应放热较大,为快速移出反应热,预聚合反应器第一段管道内冷媒介质为40℃温水,增加预聚合反应器第一段管道冷媒介质与反应物料之间的温差,相同的换
热面积移出更多热量,有效控制预聚合反应器内聚合温度,预聚合反应器二段为聚合反应后期,反应放热较小,第二段管道内冷媒介质为50℃温水,减少预聚合反应器第二段管道冷媒介质与反应物料之间的温差,冷媒介质温度接近聚合温度,使得预聚合反应器内物料聚合更加平稳、温和。
23.3、本发明ppc合成系统,终聚合反应器的终聚合物料通道上游端设置有微界面发生器,补充的二氧化碳(过量)、补充的含有催化剂的溶剂,以及预聚合物料以微米形态均匀部分在溶剂中,增大气液固三相接触面积。其中的终聚合物料通道为终聚合绕管管内,强化终聚合物料扰动。其中的终聚合绕管管内为终聚合物料通道,且终聚合物料通道为管道,由第三段管道和第四段管道连接构成,第三段管道位于第四段管道的上方,所述第三段管道、第四段管道均呈往复折弯延伸,且第三段管道所在平面相对于第四段管道所在平面旋转90
°
,对于管内流动的聚合物料起到变向掺混作用,有利于提高聚合转化率。由于终聚合反应器内新补充原料二氧化碳,使得终聚合反应器内一段为反应初期,反应放热较大,为快速移出反应热,终聚合反应器第三段管道内冷媒介质为40℃温水,增加终聚合反应器一段冷媒介质与反应物料之间的温差,相同的换热面积移出更多热量,有效控制终聚合反应器一段的聚合温度,终聚合反应器二段为反应后期,反应放热较小,终聚合反应器第二段管道内冷媒介质为50℃温水,减少终聚合反应器二段冷媒介质与反应物料之间的温差,冷媒介质温度接近聚合温度,让二段聚合更加平稳温和。
24.4、本发明ppc的合成工艺,通过控制预聚合反应器中,环氧丙烷和二氧化碳配比,使40-60%环氧丙烷完成聚合任务。
25.5、本发明ppc的合成工艺,通过控制终聚合反应器中二氧化碳和催化剂添加量,使99.9%以上的环氧丙烷聚合。
26.经申请人试验验证,采用本发明ppc合成系统及方工艺,由于采用微界面技术,缩短聚合所需时间,物料停留时间为0.5h,只需设计聚合空间为15m3的预聚合反应器和终聚合反应器各一台,即可满足10万吨/年的ppc产能需要。如采用传统夹套搅拌聚合釜,由于受到换热面积限制,单台搅拌聚合釜产能最大为1万吨/年,同时由于物料停留时间长达10h,同样10万吨/年ppc装置,20m3的预聚合釜和终聚合釜各需要10台。本发明可有效缩短聚合时间、减少设备台数、节约投资、节省占地面积及降低能耗。
27.下面结合具体实施例作进一步的说明。
28.说明书附图
29.图1为本发明ppc合成系统的连接示意图。
30.其中,1为预聚合反应器,2为终聚合反应器,3为终聚合闪蒸罐,4为预聚合出料泵,5为二氧化碳压缩机,6为溶剂加热器,7为po加热器,11为第一管路,12为第二管路,13为第三管路,14为第四管路,15为第五管路。
具体实施方式
31.参见图1,为一种ppc合成系统的具体实施例。
32.ppc合成系统包括预聚合反应器1、终聚合反应器2、终聚合闪蒸罐3。所述预聚合反应器1的进料口分别通过第一管路11与二氧化碳源相连、第二管路12与溶剂源相连、第三管路13与po源相连,具体的,所述第一管路11上设有二氧化碳压缩机5,第二管路12上设有溶
剂加热器6,第三管路13上设有po加热器7,分别用于压缩二氧化碳、升温溶剂、升温po,进一步的,第二管路上设有溶剂泵,位于溶剂加热器的上游,第二管路的上游端连接溶剂罐,第三管路上设有po泵,位于po加热器的上游,第三管路的上游端设有po罐。所述预聚合反应器1的排料口经预聚合出料泵4对终聚合反应器2供料。终聚合反应器2的进料口分别通过第四管路14与二氧化碳源相连、第五管路15与溶剂源相连,本实施例中,所述第四管路14与第一管路11相连,位于二氧化碳压缩机5的下游,所述第五管路15与第二管路12相连,位于溶剂加热器6的下游,显然的,第一管路、第二管路、第三管路、第四管路、第五管路上分别设有阀。所述终聚合反应器2的排料口与所述终聚合闪蒸罐3相连。
33.进一步的,预聚合反应器1为微界面绕管式固定床反应器,包括封闭的预聚合壳体,预聚合壳体内设置的预聚合绕管管内为预聚合冷媒介质通道,预聚合绕管和预聚合壳体之间的空间为预聚合物料通道,所述预聚合物料通道的上游端设置微界面发生器,其中,所述预聚合冷媒介质通道为管道,包括第一段管道和第二段管道,第一段管道位于第二段管道的上方,所述第一段管道、第二段管道均呈往复折弯延伸,且第一段管道所在平面相对于第二段管道所在平面旋转90
°
。
34.进一步的,终聚合反应器2为微界面绕管式固定床反应器,包括封闭的终聚合壳体,所述终聚合壳体内设置的终聚合绕管管内为终聚合物料通道,终聚合绕管和终聚合壳体之间的空间为终聚合冷媒介质通道,所述终聚合物料通道的上游端设置微界面发生器,其中,终聚合物料通道为管道,由第三段管道和第四段管道连接构成,第三段管道位于第四段管道的上方,所述第三段管道、第四段管道均呈往复折弯延伸,且第三段管道所在平面相对于第四段管道所在平面旋转90
°
。
35.实施例2
36.采用实施例1的ppc合成系统合成ppc,以10万吨/年合成系统合成ppc为例,包括以下步骤:
37.1)混合有催化剂的7.5t/h二氯甲烷和8.27t/h的po以及3.29t/h二氧化碳,合计总量为19.06t/h物料经微界面发生器进入预聚合反应器的预聚合物料通道,其中po和二氧化碳的摩尔比为1:0.52,控制预聚合温度为60-90℃、压力为1.0-4.0mpag,po聚合率为40-60%,得到预聚合物料,其中催化剂为柠檬酸盐络合物;
38.2)步骤1)得到的预聚合物料和未聚po合计19.06t/h,进入终聚反应器,在终聚反应器补充3.29t/h二氧化碳以及补充的混合有催化剂的7.5t/h二氯甲烷经微界面发生器进入终聚合反应器的终聚合物料通道,其中po和二氧化碳的摩尔比为1:1.10,控制终聚合温度为60-90℃、压力为1.0-4.0mpag,po聚合率为99.9%,得到终聚合物料29.85t/h;
39.3)终聚合物料进入终聚合闪蒸罐,排出的汽相送至二氧化碳单元回收二氧化碳及pc,排出的液相送至溶剂回收单元,脱除催化剂、少量未聚单体及回收溶剂后,得到ppc产品。
40.进一步的,步骤1)二氯甲烷的温度为50-80℃,po的温度为50-80℃,二氧化碳为50-80℃。
41.优选的,步骤1)预聚合反应器的预聚合冷媒介质通道的第一段管道通入40℃的温水作为冷媒介质,第二段管道通入50℃的温水作为冷媒介质。
42.优选的,步骤2)终聚合反应器的终聚合冷媒介质通道的第一段管道通入第一段管
道通入40℃温水作为冷媒介质,第二段管道通入50℃的温水作为冷媒介质。
43.进一步的,步骤3)终聚合闪蒸罐的真空度为0.1bar(a)。