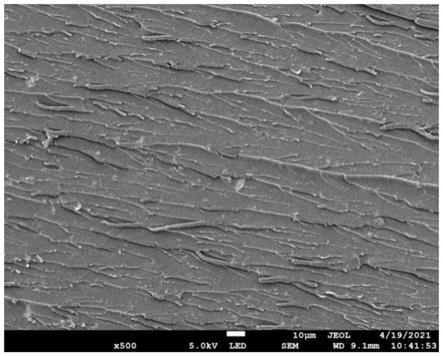
1.本发明涉及复合材料技术领域,尤其涉及氨基化脱碱赤泥材料、氨基化脱碱赤泥增韧环氧树脂复合材料及制备方法。
背景技术:
2.环氧树脂(ep)是指一类分子结构中存在两个或两个以上环氧基团,以脂肪族、脂环族、芳香族有机化合物为骨架的低分子量聚合物及其交联固化产物的总称。这种化学结构赋予了环氧树脂极高的粘结性、良好的机械性能与优异的化学稳定性。同时环氧树脂在固化过程中几乎不产生小分子挥发物质,这也使得环氧树脂更易加工成型且固化收缩率较低。然而,过高的交联密度也使得环氧树脂内应力较大,这直接导致其耐磨性、耐冲击性与耐疲劳性较差。
3.为解决以上问题,诸如纤维增韧、聚合物增韧、无机纳米粒子增韧等方法被相继开发。在这其中,无机纳米粒子具有小尺寸效应、表面效应、量子尺寸效应等优势,通过无机纳米粒子增韧环氧树脂可极大的提高该材料的冲击强度。然而,无机纳米粒子在环氧树脂体系中存在界面相容性差的问题,导致复合材料弯曲强度较低,严重制约了无机纳米粒子增韧法在环氧树脂体系中的应用。
4.通过对无机纳米粒子进行表面改性与两相复合分散可有效的增强无机纳米粒子在环氧树脂体系中的分散性。例如发明专利cn111763405a公开了一种纳米二氧化硅修饰的氧化石墨烯-环氧树脂复合材料的制备方法,该专利通过超支化聚合物为桥梁,制备了二氧化硅修饰的石墨烯材料,并以其为改性剂对环氧树脂进行改性,最终制备得到了力学性能优异的二氧化硅-氧化石墨烯-环氧树脂复合材料。然而,石墨烯与纳米二氧化硅较为高昂的价格与复杂的处理工艺极大地限制了这种复合材料的应用。
技术实现要素:
5.本发明的目的在于提供一种氨基化脱碱赤泥材料、氨基化脱碱赤泥增韧环氧树脂复合材料及制备方法,本发明提供的氨基化脱碱赤泥材料的制备工艺简单且成本低,以本发明提供的氨基化脱碱赤泥材料作为环氧树脂的增韧剂,能够使所得复合材料在具有较好的韧性的同时还具有较高的弯曲强度。
6.为了实现上述发明目的,本发明提供以下技术方案:
7.本发明提供了一种氨基化脱碱赤泥材料的制备方法,包括以下步骤:
8.将赤泥、有机酸与水混合,依次进行脱碱处理和沉降分离处理,得到脱碱赤泥;
9.将所述脱碱赤泥、氨基偶联剂与有机溶剂混合,进行氨基化处理,得到氨基化脱碱赤泥材料。
10.优选地,所述有机酸包括乙酸、草酸、马来酸或硬脂酸;所述赤泥与有机酸的质量比为(30~300):(5~50)。
11.优选地,所述脱碱处理的温度为50~120℃,时间为30~300min。
12.优选地,所述沉降分离处理包括:将脱碱处理后所得体系依次进行分散和静置,将静置后所得上层分散液进行固液分离,所得固体物料为脱碱赤泥。
13.优选地,所述氨基偶联剂包括3-氨丙基三乙氧基硅烷、3-脲丙基三甲氧基硅烷或异丙氧基三(乙二胺基n-乙氧基)钛酸酯;所述脱碱赤泥与氨基偶联剂的质量比为(20~200):(2~40)。
14.优选地,所述氨基化处理的温度为80~200℃,时间为1~10h。
15.本发明提供了上述技术方案所述制备方法制备得到的氨基化脱碱赤泥材料。
16.本发明提供了一种氨基化脱碱赤泥增韧环氧树脂复合材料,按质量份数计,制备原料包括:
17.环氧树脂10~100份;
18.氨基化脱碱赤泥材料4~40份,所述氨基化脱碱赤泥材料为上述技术方案所述氨基化脱碱赤泥材料;
19.固化剂5~50份。
20.优选地,所述环氧树脂为双酚a类环氧树脂。
21.本发明提供了上述技术方案所述氨基化脱碱赤泥增韧环氧树脂复合材料的制备方法,包括以下步骤:
22.将环氧树脂与氨基化脱碱赤泥材料混合,进行分散处理,得到分散处理体系;
23.将所述分散处理体系与固化剂混合,进行固化处理,得到氨基化脱碱赤泥增韧环氧树脂复合材料。
24.本发明提供了一种氨基化脱碱赤泥材料的制备方法,包括以下步骤:将赤泥、有机酸与水混合,依次进行脱碱处理和沉降分离处理,得到脱碱赤泥;将所述脱碱赤泥、氨基偶联剂与有机溶剂混合,进行氨基化处理,得到氨基化脱碱赤泥材料。本发明首先采用有机酸对赤泥进行脱碱处理,再经沉降分离处理,之后采用氨基偶联剂对所得脱碱赤泥进行氨基化处理,最终所得氨基化脱碱赤泥材料表面具有丰富的氨基,在环氧树脂中具有较好的分散性;且将赤泥进行脱碱处理和沉降分离处理,赤泥本身通过分离提纯与na2o脱除,去除烧结团聚的大颗粒疏水赤泥,最终形成具有多尺寸分布的微纳米级赤泥,使其单分散性进一步增强;同时,氨基化脱碱赤泥材料表面的氨基与环氧树脂基团之间的共价键交联作用显著的增强了复合材料的界面相容性。本发明提供的氨基化脱碱赤泥材料的制备工艺简单且成本低,以本发明提供的氨基化脱碱赤泥材料作为环氧树脂的增韧剂,能够使所得复合材料在具有较好的韧性的同时还具有较高的弯曲强度。具体的,利用本发明提供的氨基化脱碱赤泥材料作为环氧树脂的增韧剂,环氧树脂从硬而脆向硬而韧转变,进而显著增强环氧树脂的冲击强度与压缩强度;同时氨基化脱碱赤泥材料表面的氨基也可以起到固化剂的作用,参与环氧树脂的固化过程,有利于增强氨基化脱碱赤泥材料与环氧树脂之间的界面相容性,进而在使复合材料增韧的同时,保证其具有较高的弯曲强度。
附图说明
25.图1为实施例2制备的氨基化脱碱赤泥的sem图;
26.图2为实施例2制备的氨基化脱碱赤泥的粒径分布图;
27.图3为实施例2制备的氨基化脱碱赤泥增韧环氧树脂复合材料的冲击断面的sem图。
具体实施方式
28.本发明提供了一种氨基化脱碱赤泥材料的制备方法,包括以下步骤:
29.将赤泥、有机酸与水混合,依次进行脱碱处理和沉降分离处理,得到脱碱赤泥;
30.将所述脱碱赤泥、氨基偶联剂与有机溶剂混合,进行氨基化处理,得到氨基化脱碱赤泥材料。
31.赤泥是一种具有强碱性的矿渣,其是铝矿冶炼过程中的主要副产物,主要由sio2、cao、al2o3、tio2、na2o、fe2o3组成。根据铝矿冶炼工艺的不同,赤泥可被分为拜耳法赤泥、烧结法赤泥、联合法赤泥三种,其中联合法赤泥是在拜耳-烧结联合法冶铝工艺中产生的赤泥,该赤泥中存在β-2cao
·
sio2,通过联合法冶铝工艺生产金属铝时,每冶炼1吨铝会产生1.5~2.5吨的赤泥。大量的赤泥多采用大坝露天堆放的存储方法,然而这种存储方法维护成本高昂,且土地浪费严重。同时,赤泥中的碱性物质会不可避免地渗入地下,造成土壤与地下水的污染;更为严重的是,裸露且颗粒极小的赤泥容易形成粉尘污染。这些污染严重破坏了生态环境,并对人类、动物和植物的生存造成了不利影响。同时,作为一种不需开采且具有多种元素、多种结构的混合物,赤泥也是一种丰富的资源。本发明通过对赤泥进行脱碱处理、沉降分离处理以及氨基化处理,最终所得氨基化脱碱赤泥材料表面具有丰富的氨基,在环氧树脂中具有较好的分散性,以其作为环氧树脂的增韧剂,能够使所得复合材料具有较好的冲击强度与压缩强度,同时保证复合材料具有较为优异的弯曲强度,使环氧树脂从硬而脆向硬而韧转变。因此,本发明技术方案一方面能够解决了其大量露天堆放的问题,另一面制备得到性能优异的环氧树脂基复合材料,将赤泥变废为宝,实现了其有效利用。
32.本发明将赤泥、有机酸与水混合,依次进行脱碱处理和沉降分离处理,得到脱碱赤泥。本发明对所述赤泥(rm)的来源没有特殊限定,采用本领域技术人员熟知来源的赤泥即可,在本发明的实施例中,具体可以为联合法冶铝工艺中产生的赤泥。在本发明中,联合法冶铝工艺中产生的赤泥多为黄赤泥与黑赤泥混合形成的棕赤泥,其中,黄赤泥中s
2-的含量较低(《0.1wt%),颗粒尺寸较小,亲水性较强,在水中分散性能更佳;黑赤泥中s
2-含量较高(》0.25wt%),s
2-的存在极大程度上促进了feo与fes的结晶与晶体生长,进而使赤泥颗粒较大,表面亲水基团较少,且多呈电中性,在水中分散性差;当赤泥中s
2+
含量处于0.1~0.25wt%范围内时,赤泥多为黄赤泥与黑赤泥的混合物,其颜色呈棕色,即为棕赤泥。本发明首先通过有机酸脱碱与沉降分离法对棕赤泥进行脱碱与粒径分离,得到脱碱赤泥(即脱碱的黄赤泥)。随后通过共价键表面改性法,在脱碱赤泥的基础上制备了具有氨基结构的高分散性赤泥,即氨基化脱碱赤泥材料(rm-nh2),将其作为增韧剂加入环氧树脂固化体系,最终制备得到具有优异力学性能的氨基化脱碱赤泥增韧环氧树脂(ep/rm-nh2)复合材料。
33.在本发明中,所述赤泥在使用前优选进行粉碎处理,然后过100目筛网,将筛下所得赤泥进行脱碱处理;本发明对所述粉碎处理的具体操作方法没有特殊限定,能够得到所需粒度的赤泥即可,在本发明的实施例中,具体是将赤泥加入固体粉碎机中,在23000rpm转速条件下进行粉碎处理。
34.在本发明中,所述有机酸优选包括乙酸、草酸、马来酸或硬脂酸;所述赤泥与有机
酸的质量比优选为(30~300):(5~50),更优选为(100~280):(20~50),进一步优选为(160~230):(30~45),更进一步优选为(200~220):(35~45)。在本发明中,所述水优选为蒸馏水,所述赤泥与水的用量比优选为(30~300)g:(300~800)ml,更优选为(100~280)g:(400~750)ml,进一步优选为(160~230)g:(500~700)ml,更进一步优选为(200~220)g:(550~600)ml。本发明对所述赤泥、有机酸与水混合的方式没有特殊限定,能够将各组分混合均匀即可。
35.在本发明中,所述脱碱处理的温度优选为50~120℃,更优选为70~110℃,进一步优选为80~90℃;本发明优选通过油浴锅提供脱碱处理的温度。在本发明中,所述脱碱处理的时间优选为30~300min,更优选为60~240min,更优选为90~150min,进一步优选为100~140min,更进一步优选为120~130min。在本发明中,所述脱碱处理优选在机械搅拌条件下进行,所述搅拌的速率优选为100~1000rpm,更优选为200~600rpm,进一步优选为300~500rpm。在本发明中,所述脱碱处理的过程中,赤泥中na2o与水反应:na2o+h2o=2naoh,这是造成赤泥碱污染的主要原因;同时,naoh的浓度进一步影响了反应的进程,抑制了na2o在水中的溶解,这导致单纯的h2o洗涤很难去除na2o。本发明在有机酸作用进行脱碱处理,以草酸为例,草酸与na2o产生的naoh反应:hooc-cooh+2naoh=naooc-coona+2h2o,可以促进na2o与水反应,进而增加na2o溶解性,达到除去na2o的效果。
36.在本发明中,所述沉降分离处理优选包括:将脱碱处理后所得体系依次进行分散和静置,将静置后所得上层分散液进行固液分离,所得固体物料为脱碱赤泥。在本发明中,所述分散的温度优选为25~100℃,更优选为60~90℃,进一步优选为70~75℃;在本发明中,所述分散的温度优选低于所述脱碱处理的温度,具体的,所述脱碱处理与分散的温度差值优选为5~30℃,更优选为10~20℃;所述分散的时间优选为2~5min;所述分散优选在玻璃棒搅拌条件下进行。在本发明中,所述分散优选是将脱碱处理后所得体系降温5~30℃,在玻璃棒搅拌条件下进行分散2~5min。本发明优选在上述条件下进行分散,能够调控脱碱处理后所得体系的粘度,有利于控制大颗粒赤泥与小颗粒赤泥的沉降速率,进而选择合适的沉降时间将以上两种赤泥分离。在本发明中,所述静置的时间优选为1~10min,更优选为2~5min;本发明通过静置使体系分层,其中上层分散液呈黄色,即分散有小颗粒的黄赤泥;下层固液混合料含有大颗粒赤泥。
37.在本发明中,所述沉降分离处理的次数优选为1~10次,更优选为3~6次。当所述沉降分离处理的次数≥2次时,本发明优选按照上述方式将脱碱处理后所得体系依次进行分散和静置后,将下层固液混合料加水稀释,之后按照上述方式将所得体系依次进行分散和静置,以此循环,实现多次沉降分离处理。
38.最后一次静置后,本发明将所得上层分散液进行固液分离,所得固体物料为脱碱赤泥。在本发明中,可以将每次静置后所得上层分散液分别进行固液分离,也可以将每次静置后所得上层分散液合并后再进行固液分离,本发明对此不作特殊限定。本发明对所述固液分离的方式没有特殊限定,具体可以为过滤。
39.本发明优选将固液分离后所得固体物料依次进行干燥和粉碎,得到脱碱赤泥。在本发明中,所述干燥的温度优选为100~200℃,更优选为125~180℃;时间优选为10~15h,更优选为12h。
40.在本发明中,所述脱碱赤泥主要由片层状微米片与颗粒状纳米微球组成,材料单
分散性较好,且粒径存在梯度性分布;具体的,所述纳米微球的粒度优选为20~100nm,微米片的尺寸优选为10~20μm。
41.得到脱碱赤泥后,本发明将所述脱碱赤泥、氨基偶联剂与有机溶剂混合,进行氨基化处理,得到氨基化脱碱赤泥材料。在本发明中,所述氨基偶联剂优选包括3-氨丙基三乙氧基硅烷、3-脲丙基三甲氧基硅烷或异丙氧基三(乙二胺基n-乙氧基)钛酸酯;所述脱碱赤泥与氨基偶联剂的质量比优选为(20~200):(2~40),更优选为(50~150):(5~20),进一步优选为(100~120):(8~15)。在本发明中,所述有机溶剂优选包括异丙醇、乙醇、甲苯或四氢呋喃;所述氨基偶联剂与有机溶剂的质量比优选为1:(0.5~4.5),更优选为1:(1.5~4),进一步优选为1:(3~4)。在本发明中,所述脱碱赤泥、氨基偶联剂与有机溶剂混合的方式优选为将氨基偶联剂与有机溶剂混合,得到氨基偶联剂溶液,将所述氨基偶联剂溶液喷洒于脱碱赤泥上进行搅拌混合;所述搅拌混合时搅拌的速率优选为20000~30000rpm,更优选为25000rpm,搅拌的时间优选为10~20min,更优选为12~15min。
42.在本发明中,所述氨基化处理的温度优选为80~200℃,更优选为120~150℃,进一步优选为130~140℃;时间优选为1~10h,更优选为2~7h,进一步优选为4~6h。在本发明中,所述氨基化处理过程中,氨基偶联剂在有机溶剂的作用下均匀分散在脱碱赤泥的表面,并与脱碱赤泥实现偶联,最终得到氨基化脱碱赤泥材料。
43.本发明提供了上述技术方案所述制备方法制备得到的氨基化脱碱赤泥材料。本发明提供的氨基化脱碱赤泥材料表面具有丰富的氨基,在环氧树脂中具有较好的分散性,以其作为环氧树脂的增韧剂,能够使所得复合材料具有较好的冲击强度、弯曲强度与压缩强度,使环氧树脂从硬而脆向硬而韧转变。
44.本发明提供了一种氨基化脱碱赤泥增韧环氧树脂复合材料,按质量份数计,制备原料包括:
45.环氧树脂10~100份;
46.氨基化脱碱赤泥材料4~40份,所述氨基化脱碱赤泥材料为上述技术方案所述氨基化脱碱赤泥材料;
47.固化剂5~50份。
48.按质量份数计,本发明提供的氨基化脱碱赤泥增韧环氧树脂复合材料的制备原料包括环氧树脂10~100份,优选为40~90份,进一步优选为60~80份。在本发明中,所述环氧树脂优选为双酚a类环氧树脂,更优选为环氧树脂e-51、环氧树脂e-44、环氧树脂e-12或环氧树脂e-10。
49.以所述环氧树脂的质量份数为基准,本发明提供的氨基化脱碱赤泥增韧环氧树脂复合材料的制备原料包括氨基化脱碱赤泥材料4~40份,优选为5~35份,进一步优选为10~30份,更进一步优选为15~20份;所述氨基化脱碱赤泥材料优选为上述技术方案所述氨基化脱碱赤泥材料。
50.以所述环氧树脂的质量份数为基准,本发明提供的氨基化脱碱赤泥增韧环氧树脂复合材料的制备原料包括固化剂5~50份,优选为8~25份,进一步优选为10~20份。在本发明中,所述固化剂优选包括二乙烯基三胺(deta)、二氨基二苯基甲烷(ddm)、异氟尔酮二胺(ipd)或己二胺(hmd)。
51.本发明提供了上述技术方案所述氨基化脱碱赤泥增韧环氧树脂复合材料的制备
方法,包括以下步骤:
52.将环氧树脂与氨基化脱碱赤泥材料混合,进行分散处理,得到分散处理体系;
53.将所述分散处理体系与固化剂混合,进行固化处理,得到氨基化脱碱赤泥增韧环氧树脂复合材料。
54.本发明将环氧树脂与氨基化脱碱赤泥材料混合,进行分散处理,得到分散处理体系。在本发明中,所述分散处理的温度优选为50~150℃,更优选为70~140℃,进一步优选为80~130℃,更进一步优选为100~120℃;所述分散处理的时间优选为2~10min,更优选为4~5min;所述分散处理优选在搅拌条件下进行,所述搅拌的转速优选为1000~10000rpm,更优选为4000~7000rpm,进一步优选为5000~6000rpm。本发明优选将环氧树脂与氨基化脱碱赤泥材料置于高速搅拌罐中,选择聚四氟乙烯球磨搅拌头,在50~150℃、1000~10000rpm条件下进行分散处理2~10min。
55.所述分散处理后,本发明优选将所得体系进行第一真空脱气,得到分散处理体系;所述第一真空脱气的温度优选为50~150℃,更优选为70~140℃,进一步优选为80~130℃,更进一步优选为100~120℃;时间优选为1~10min,更优选为2~5min;所述第一真空脱气优选在真空烘箱中进行。
56.得到分散处理体系后,本发明将所述分散处理体系与固化剂混合,进行固化处理,得到氨基化脱碱赤泥增韧环氧树脂复合材料。在本发明中,为了保证固化剂充分溶解,所述分散处理体系与固化剂混合优选在50~170℃条件下进行,更优选为100~120℃;所述混合的时间优选为2~10min,更优选为5~8min;所述混合优选在搅拌条件下进行,所述搅拌的转速优选为1000~10000rpm,更优选为3000~8000rpm,进一步优选为4000~6000rpm。
57.所述分散处理体系与固化剂混合后,本发明优选将所得体系进行第二真空脱气,之后将所得体系进行固化处理。在本发明中,所述第二真空脱气的温度优选为50~170℃,更优选为100~140℃;所述第二真空脱气的时间优选为1~10min,更优选为3~6min;所述第二真空脱气优选在真空烘箱中进行。
58.在本发明中,所述固化处理包括依次进行的第一固化处理和第二固化处理,所述第一固化处理的温度优选为50~150℃,更优选为70~120℃,进一步优选为90~100℃;第一固化处理的时间优选为1~5h,更优选为2~3h;所述第二固化处理的温度优选为100~250℃,更优选为120~180℃,进一步优选为140~160℃,所述第二固化处理的温度优选高于第一固化处理的温度,具体的,所述第二固化处理与第一固化处理的温度差值优选为30~80℃,更优选为50~70℃,进一步优选为40~60℃;第二固化处理的时间优选为1~5h,更优选为2~4h。本发明优选将第二真空脱气后所得体系置于模具中进行固化处理。
59.所述固化处理后,本发明优选将所得材料自然降温至室温,得到氨基化脱碱赤泥增韧环氧树脂复合材料。本发明具体在烘箱中进行所述固化处理,固化处理结束后,优选将烘箱断电,所得材料于烘箱中自然降温至室温。
60.下面将结合本发明中的实施例,对本发明中的技术方案进行清楚、完整地描述。显然,所描述的实施例仅仅是本发明一部分实施例,而不是全部的实施例。基于本发明中的实施例,本领域普通技术人员在没有做出创造性劳动前提下所获得的所有其他实施例,都属于本发明保护的范围。
61.实施例1
62.(1)脱碱赤泥的制备
63.将100g的赤泥(rm)加入固体粉碎机中,在23000rpm转速条件下进行粉碎,将粉碎后的rm过100目筛网,将筛下所得rm转移入圆底烧瓶中,加入400ml蒸馏水和50g乙酸,在200rpm机械搅拌条件下,控制油浴锅反应温度为110℃,反应240min,得到第一rm分散液;将所述第一rm分散液的温度降至90℃,采用玻璃棒搅拌3min,使rm进一步分散,得到第二rm分散液;将所述第二rm分散液静置2min,体系分层,收集上层黄色分散液,完成1次沉降分离处理步骤;将静置后所得下层固液混合料加水稀释,之后重复上述沉降分离处理步骤,共进行沉降分离处理步骤6次,将每次沉降分离处理收集的上层黄色分散液合并后进行抽滤,得到rm滤饼,将所述rm滤饼于125℃烘箱中干燥12h,采用固体粉碎机在23000rpm转速条件下进行粉碎,得到脱碱赤泥。
64.(2)氨基化脱碱赤泥(rm-nh2)的制备
65.将20g氨基偶联剂3-氨丙基三乙氧基硅烷(sca-a10e)溶于甲苯(按质量比计,sca-a10e:甲苯=1:3)中,得到sca-a10e的甲苯溶液;取50g脱碱赤泥置于固体粉碎机中,通过喷壶将所述sca-a10e的甲苯溶液喷洒进入固体粉碎机中,在25000rpm条件下搅拌15min,以确保sca-a10e充分分散于脱碱赤泥表面;之后将所得体系放入烘箱中,于130℃条件下反应5h,得到氨基化脱碱赤泥。
66.(3)氨基化脱碱赤泥增韧环氧树脂(ep/rm-nh2)复合材料的制备
67.将80g环氧树脂e-51与10g氨基化脱碱赤泥置于高速搅拌罐中,选择聚四氟乙烯球磨搅拌头,在120℃、6000rpm条件下进行分散处理4min,之后将所得体系置于真空烘箱中,在120℃条件下进行真空脱气3min;将所得第一脱气物料与20g固化剂deta混合,在170℃、4000rpm条件下混合5min,之后将所得体系置于真空烘箱中,在170℃条件下进行真空脱气3min;将所得第二脱气物料置于模具中,将盛放有第二脱气物料的模具置于烘箱中,在70℃条件下固化3h,之后在100℃条件下固化4h,将烘箱断电,所得材料于烘箱中经4h自然降温至室温(25℃),得到氨基化脱碱赤泥增韧环氧树脂复合材料。
68.实施例2
69.(1)脱碱赤泥的制备
70.将160g的赤泥(rm)加入固体粉碎机中,在23000rpm转速条件下进行粉碎,将粉碎后的rm过100目筛网,将筛下所得rm转移入圆底烧瓶中,加入600ml蒸馏水和20g乙酸,在1000rpm机械搅拌条件下,控制油浴锅反应温度为80℃,反应120min,得到第一rm分散液;将所述第一rm分散液的温度降至60℃,采用玻璃棒搅拌3min,使rm进一步分散,得到第二rm分散液;将所述第二rm分散液静置3min,体系分层,收集上层黄色分散液,完成1次沉降分离处理步骤;将静置后所得下层固液混合料加水稀释,之后重复上述沉降分离处理步骤,共进行沉降分离处理步骤5次,将每次沉降分离处理收集的上层黄色分散液合并后进行抽滤,得到rm滤饼,将所述rm滤饼于125℃烘箱中干燥12h,采用固体粉碎机在23000rpm转速条件下进行粉碎,得到脱碱赤泥。
71.(2)氨基化脱碱赤泥(rm-nh2)的制备
72.将2.5g氨基偶联剂异丙氧基三(乙二胺基n-乙氧基)钛酸酯(tca-k44)溶于异丙醇(按质量比计,tca-k44:异丙醇=1:4)中,得到tca-k44的异丙醇溶液;取100g脱碱赤泥置于固体粉碎机中,通过喷壶将所述tca-k44的异丙醇溶液喷洒进入固体粉碎机中,在25000rpm
条件下搅拌15min,以确保tca-k44充分分散于脱碱赤泥表面;之后将所得体系放入烘箱中,于120℃条件下反应2h,得到氨基化脱碱赤泥。
73.(3)氨基化脱碱赤泥增韧环氧树脂(ep/rm-nh2)复合材料的制备
74.将100g环氧树脂e-51与5g氨基化脱碱赤泥置于高速搅拌罐中,选择聚四氟乙烯球磨搅拌头,在70℃、5000rpm条件下进行分散处理10min,之后将所得体系置于真空烘箱中,在70℃条件下进行真空脱气5min;将所得第一脱气物料与20g固化剂ddm混合,在70℃、4000rpm条件下混合10min,之后将所得体系置于真空烘箱中,在70℃条件下进行真空脱气5min;将所得第二脱气物料置于模具中,将盛放有第二脱气物料的模具置于烘箱中,在100℃条件下固化2h,之后在160℃条件下固化2h,将烘箱断电,所得材料于烘箱中经4h自然降温至室温(25℃),得到氨基化脱碱赤泥增韧环氧树脂复合材料。
75.实施例3
76.(1)脱碱赤泥的制备
77.将200g的赤泥(rm)加入固体粉碎机中,在23000rpm转速条件下进行粉碎,将粉碎后的rm过100目筛网,将筛下所得rm转移入圆底烧瓶中,加入600ml蒸馏水和30g马来酸,在500rpm机械搅拌条件下,控制油浴锅反应温度为70℃,反应130min,得到第一rm分散液;将所述第一rm分散液的温度升至60℃,采用玻璃棒搅拌5min,使rm进一步分散,得到第二rm分散液;将所述第二rm分散液静置3min,体系分层,收集上层黄色分散液,完成1次沉降分离处理步骤;将静置后所得下层固液混合料加水稀释,之后重复上述沉降分离处理步骤,共进行沉降分离处理步骤5次,将每次沉降分离处理收集的上层黄色分散液合并后进行抽滤,得到rm滤饼,将所述rm滤饼于150℃烘箱中干燥12h,采用固体粉碎机在23000rpm转速条件下进行粉碎,得到脱碱赤泥。
78.(2)氨基化脱碱赤泥(rm-nh2)的制备
79.将5g氨基偶联剂3-脲丙基三甲氧基硅烷(sca-u60m)溶于四氢呋喃(按质量比计,sca-u60m:四氢呋喃=1:3.5)中,得到sca-u60m的四氢呋喃溶液;取150g脱碱赤泥置于固体粉碎机中,通过喷壶将所述sca-u60m的四氢呋喃溶液喷洒进入固体粉碎机中,在25000rpm条件下搅拌15min,以确保sca-u60m充分分散于脱碱赤泥表面;之后将所得体系放入烘箱中,于150℃条件下反应4h,得到氨基化脱碱赤泥。
80.(3)氨基化脱碱赤泥增韧环氧树脂(ep/rm-nh2)复合材料的制备
81.将80g环氧树脂e-10与10g氨基化脱碱赤泥置于高速搅拌罐中,选择聚四氟乙烯球磨搅拌头,在130℃、6000rpm条件下进行分散处理5min,之后将所得体系置于真空烘箱中,在130℃条件下进行真空脱气5min;将所得第一脱气物料与10g固化剂ipd混合,在100℃、3000rpm条件下混合5min,之后将所得体系置于真空烘箱中,在100℃条件下进行真空脱气5min;将所得第二脱气物料置于模具中,将盛放有第二脱气物料的模具置于烘箱中,在120℃条件下固化2h,之后在180℃条件下固化2h,将烘箱断电,所得材料于烘箱中经4h自然降温至室温,得到氨基化脱碱赤泥增韧环氧树脂复合材料。
82.实施例4
83.(1)脱碱赤泥的制备
84.将280g的赤泥(rm)加入固体粉碎机中,在23000rpm转速条件下进行粉碎,将粉碎后的rm过100目筛网,将筛下所得rm转移入圆底烧瓶中,加入300ml蒸馏水和45g马来酸,在
500rpm机械搅拌条件下,控制油浴锅反应温度为70℃,反应60min,得到第一rm分散液;将所述第一rm分散液的温度升至50℃,采用玻璃棒搅拌4min,使rm进一步分散,得到第二rm分散液;将所述第二rm分散液静置5min,体系分层,收集上层黄色分散液,完成1次沉降分离处理步骤;将静置后所得下层固液混合料加水稀释,之后重复上述沉降分离处理步骤,共进行沉降分离处理步骤5次,将每次沉降分离处理收集的上层黄色分散液合并后进行抽滤,得到rm滤饼,将所述rm滤饼于150℃烘箱中干燥12h,采用固体粉碎机在23000rpm转速条件下进行粉碎,得到脱碱赤泥。
85.(2)氨基化脱碱赤泥(rm-nh2)的制备
86.将8g氨基偶联剂3-脲丙基三甲氧基硅烷(sca-u60m)溶于乙醇(按质量比计,sca-u60m:乙醇=1:1.5)中,得到sca-u60m的乙醇溶液;取150g脱碱赤泥置于固体粉碎机中,通过喷壶将所述sca-a10e的乙醇溶液喷洒进入固体粉碎机中,在25000rpm条件下搅拌15min,以确保sca-u60m充分分散于脱碱赤泥表面;之后将所得体系放入烘箱中,于150℃条件下反应4h,得到氨基化脱碱赤泥。
87.(3)氨基化脱碱赤泥增韧环氧树脂(ep/rm-nh2)复合材料的制备
88.将60g环氧树脂e-44与20g氨基化脱碱赤泥置于高速搅拌罐中,选择聚四氟乙烯球磨搅拌头,在120℃、7000rpm条件下进行分散处理5min,之后将所得体系置于真空烘箱中,在120℃条件下进行真空脱气5min;将所得第一脱气物料与15g固化剂ddm混合,在120℃、8000rpm条件下混合5min,之后将所得体系置于真空烘箱中,将盛放有第二脱气物料的模具置于烘箱中,在120℃条件下进行真空脱气5min;将所得第二脱气物料置于模具中,在80℃条件下固化1h,之后在150℃条件下固化3h,将烘箱断电,所得材料于烘箱中经4h自然降温至室温,得到氨基化脱碱赤泥增韧环氧树脂复合材料。
89.实施例5
90.(1)脱碱赤泥的制备
91.将230g的赤泥(rm)加入固体粉碎机中,在23000rpm转速条件下进行粉碎,将粉碎后的rm过100目筛网,将筛下所得rm转移入圆底烧瓶中,加入750ml蒸馏水和30g草酸,在300rpm机械搅拌条件下,控制油浴锅反应温度为90℃,反应60min,得到第一rm分散液;将所述第一rm分散液的温度降至70℃,采用玻璃棒搅拌5min,使rm进一步分散,得到第二rm分散液;将所述第二rm分散液静置5min,体系分层,收集上层黄色分散液,完成1次沉降分离处理步骤;将静置后所得下层固液混合料加水稀释,之后重复上述沉降分离处理步骤,共进行沉降分离处理步骤6次,将每次沉降分离处理收集的上层黄色分散液合并后进行抽滤,得到rm滤饼,将所述rm滤饼于150℃烘箱中干燥12h,采用固体粉碎机在23000rpm转速条件下进行粉碎,得到脱碱赤泥。
92.(2)氨基化脱碱赤泥(rm-nh2)的制备
93.将6g氨基偶联剂3-脲丙基三甲氧基硅烷(sca-u60m)溶于甲苯(按质量比计,sca-u60m:甲苯=1:4.5)中,得到sca-u60m的甲苯溶液;取100g脱碱赤泥置于固体粉碎机中,通过喷壶将所述sca-u60m的甲苯溶液喷洒进入固体粉碎机中,在25000rpm条件下搅拌15min,以确保sca-u60m充分分散于脱碱赤泥表面;之后将所得体系放入烘箱中,于130℃条件下反应7h,得到氨基化脱碱赤泥。
94.(3)氨基化脱碱赤泥增韧环氧树脂(ep/rm-nh2)复合材料的制备
95.将90g环氧树脂e-10与90g氨基化脱碱赤泥置于高速搅拌罐中,选择聚四氟乙烯球磨搅拌头,在80℃、4000rpm条件下进行分散处理5min,之后将所得体系置于真空烘箱中,在80℃条件下进行真空脱气2min;将所得第一脱气物料与8g固化剂deta混合,在100℃、6000rpm条件下混合8min,之后将所得体系置于真空烘箱中,在140℃条件下进行真空脱气6min;将所得第二脱气物料置于模具中,将盛放有第二脱气物料的模具置于烘箱中,在70℃条件下固化5h,之后在120℃条件下固化5h,将烘箱断电,所得材料于烘箱中经4h自然降温至室温,得到氨基化脱碱赤泥增韧环氧树脂复合材料。
96.对比例1
97.ep材料的制备:
98.将100g环氧树脂e-51与35g固化剂ddm置于高速搅拌罐中,选择聚四氟乙烯球磨搅拌头,在70℃、5000rpm条件下进行分散处理10min,之后将所得体系置于真空烘箱中,在70℃条件下进行真空脱气5min;将所得脱气物料置于模具中,将盛放有第二脱气物料的模具置于烘箱中,在100℃条件下固化2h,之后在160℃条件下固化2h,将烘箱断电,所得材料于烘箱中经4h自然降温至室温,得到ep材料。
99.对比例2
100.ep/rm复合材料的制备:
101.将100g赤泥(rm)加入固体粉碎机中,在23000rpm转速条件下进行粉碎,将粉碎后的rm过100目筛网,将筛下所得rm置于高速搅拌罐中,加入50g环氧树脂e-51,选择聚四氟乙烯球磨搅拌头,在120℃、5000rpm条件下进行分散处理6min,之后将所得体系置于真空烘箱中,在120℃条件下进行真空脱气6min;将所得第一脱气物料与12.5g固化剂ddm混合,在120℃、4000rpm条件下混合4min,之后将所得体系置于真空烘箱中,在120℃条件下进行真空脱气3min;将所得第二脱气物料置于模具中,将盛放有第二脱气物料的模具置于烘箱中,在80℃条件下固化3h,之后在150℃条件下固化3h,将烘箱断电,所得材料于烘箱中经4h自然降温至室温,得到ep/rm复合材料。
102.对比例3
103.(1)脱碱赤泥的制备
104.将100g的赤泥(rm)加入固体粉碎机中,在23000rpm转速条件下进行粉碎,将粉碎后的rm过100目筛网,将筛下所得rm转移入圆底烧瓶中,加入400ml蒸馏水和50g乙酸,在200rpm机械搅拌条件下,控制油浴锅反应温度为110℃,反应240min,得到第一rm分散液;将所述第一rm分散液的温度降至90℃,采用玻璃棒搅拌4min,使rm进一步分散,得到第二rm分散液;将所述第二rm分散液静置2min,体系分层,收集上层黄色分散液,完成1次沉降分离处理步骤;将静置后所得下层固液混合料加水稀释,之后重复上述沉降分离处理步骤,共进行沉降分离处理步骤6次,将每次沉降分离处理收集的上层黄色分散液合并后进行抽滤,得到rm滤饼,将所述rm滤饼于125℃烘箱中干燥12h,采用固体粉碎机在23000rpm转速条件下进行粉碎,得到脱碱赤泥。
105.(2)ep/rm复合材料的制备
106.将100g环氧树脂e-51和40g脱碱赤泥置于高速搅拌罐中,选择聚四氟乙烯球磨搅拌头,在120℃、5000rpm条件下进行分散处理6min,之后将所得体系置于真空烘箱中,在120℃条件下进行真空脱气6min;将所得第一脱气物料与25g固化剂ddm混合,在120℃、4000rpm
条件下混合4min,之后将所得体系置于真空烘箱中,将盛放有第二脱气物料的模具置于烘箱中,在120℃条件下进行真空脱气3min;将所得第二脱气物料置于模具中,在80℃条件下固化3h,之后在150℃条件下固化3h,将烘箱断电,所得材料于烘箱中经4h自然降温至室温,得到ep/rm复合材料。
107.对比例4
108.(1)氨基化赤泥的制备
109.将6g氨基偶联剂3-脲丙基三甲氧基硅烷(sca-u60m)溶于甲苯(按质量比计,sca-u60m:甲苯=1:4.5)中,得到sca-u60m的甲苯溶液;将150g赤泥(rm)加入固体粉碎机中,在23000rpm转速条件下进行粉碎,将粉碎后的rm过100目筛网,将筛下所得rm置于固体粉碎机中,通过喷壶将所述sca-u60m的甲苯溶液喷洒进入固体粉碎机中,在25000rpm条件下搅拌15min,以确保sca-u60m充分分散于脱碱赤泥表面;之后将所得体系放入烘箱中,于120℃条件下反应2h,得到氨基化赤泥。
110.(2)氨基化赤泥增韧环氧树脂复合材料的制备
111.将80g环氧树脂e-51与10g氨基化赤泥置于高速搅拌罐中,选择聚四氟乙烯球磨搅拌头,在90℃、8000rpm条件下反应5min,之后将所得体系置于真空烘箱中,在90℃条件下进行真空脱气3min;将所得第一脱气物料与20g固化剂ddm混合,在120℃、5000rpm条件下进行分散处理3min,之后将所得体系置于真空烘箱中,在120℃条件下进行真空脱气5min;将所得第二脱气物料置于模具中,将盛放有第二脱气物料的模具置于烘箱中,在120℃条件下固化1h,之后在160℃条件下固化1h,将烘箱断电,所得材料于烘箱中经4h自然降温至室温,得到氨基化赤泥增韧环氧树脂复合材料。
112.对比例5
113.二氧化硅增韧环氧树脂(ep/sio2)复合材料的制备:
114.将2.4g的sio2纳米颗粒(购买自上海麦克林生化科技有限公司s817565,比表面积(bet)为200m2/g;粒径为7~40nm)与120g环氧树脂e-51置于高速搅拌罐中,选择聚四氟乙烯球磨搅拌头,在70℃、5000rpm条件下进行分散处理5min,之后将所得体系置于真空烘箱中,在70℃条件下进行真空脱气5min;将所得第一脱气物料与30.0g固化剂ddm混合,在70℃、5000rpm条件下混合5min,之后将所得体系置于真空烘箱中,在70℃条件下进行真空脱气5min;将所得第二脱气物料置于模具中,将盛放有第二脱气物料的模具置于烘箱中,在100℃条件下固化2h,之后在160℃条件下固化2h,将烘箱断电,所得材料于烘箱中经4h自然降温至室温,得到二氧化硅增韧环氧树脂复合材料。
115.对比例6
116.二氧化钛增韧环氧树脂(ep/tio2)复合材料的制备:
117.将1.2g的tio2纳米颗粒(购买自上海麦克林生化科技有限公司t818936,规格为:99.8%metalsbasis,25nm,锐钛,亲水)与120g环氧树脂e-51置于高速搅拌罐中,选择聚四氟乙烯球磨搅拌头,在70℃、5000rpm条件下分散5min,之后将所得体系置于真空烘箱中,在70℃条件下进行真空脱气5min;将所得第一脱气物料与30.0g固化剂ddm混合,在70℃、5000rpm条件下混合5min,之后将所得体系置于真空烘箱中,在70℃条件下进行真空脱气5min;将所得第二脱气物料置于模具中,将盛放有第二脱气物料的模具置于烘箱中,在100℃条件下固化2h,之后在160℃条件下固化2h,将烘箱断电,所得材料于烘箱中经4h自然降
温至室温,得到二氧化钛增韧环氧树脂复合材料。
118.表征与性能测试
119.(1)将实施例2制备的氨基化脱碱赤泥(rm-nh2)以及氨基化脱碱赤泥增韧环氧树脂(ep/rm-nh2)复合材料进行表征,具体如下:
120.图1为实施例2制备的氨基化脱碱赤泥的sem图,由图1可知,rm-nh2主要由片层状微米片与颗粒状纳米微球组成,材料单分散性较好,且粒径存在梯度性分布。
121.图2为实施例2制备的氨基化脱碱赤泥的粒径分布图,由图2可知,rm-nh2在20nm~50μm的范围内均匀分布,且在20~100nm与10~20μm两个区域中分布比较集中,分别对应rm-nh2的纳米微球结构与微米片结构。
122.图3为实施例2制备的氨基化脱碱赤泥增韧环氧树脂复合材料的冲击断面的sem图,由图3可知,ep/rm-nh2复合材料的冲击断面处存在着密集的断裂条纹,这表明rm-nh2的加入极大的分散了环氧树脂内部的应力集中,进而有效的提高了复合材料的抗冲击性能。
123.(2)将实施例1~5以及对比例1~6制备的材料进行性能测试,具体的,冲击强度、弯曲强度、压缩强度的样品尺寸与测试方法分别依据国家标准gbt1843-2008、gbt9341-2008、gbt1041-2008在无尘锯中切割,通过电子万能材料试验机(ctm-50g,上海协强仪器制造有限公司)进行测试。测试结果如表1所示。
124.表1实施例1~5以及对比例1~6制备的材料的性能测试结果
125.材料来源冲击强度/mpa弯曲强度/mpa压缩强度/mpa实施例128.381.2133.2实施例231.589.6155.5实施例314.583.1152.6实施例421.0103.9112.9实施例513.5104.2142.8对比例115.396.6109.0对比例24.077.0119.5对比例311.281.9120.3对比例411.475.5178.7对比例524.779.7150.6对比例633.270.6132.1
126.由表1可知,以本发明提供的氨基化脱碱赤泥材料作为环氧树脂的增韧剂,所得复合材料的在具有较高冲击强度与压缩强度的同时,还具有较高的弯曲强度。综合性能与价格因素,本发明提供的氨基化脱碱赤泥材料作为环氧树脂的增韧剂具有多重优势。
127.以上所述仅是本发明的优选实施方式,应当指出,对于本技术领域的普通技术人员来说,在不脱离本发明原理的前提下,还可以做出若干改进和润饰,这些改进和润饰也应视为本发明的保护范围。