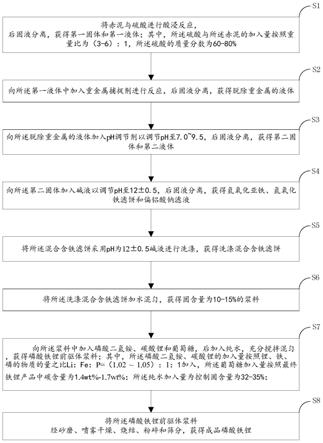
1.本发明涉及锂电池材料制备的技术领域,更具体地,涉及一种以高铁拜耳法赤泥为铁源制备磷酸铁锂正极材料的方法。
背景技术:
2.赤泥是制铝工业提取氧化铝时排出的污染性废渣,一般平均每生产1吨氧化铝,附带产生1.0~2.0吨赤泥。中国作为世界第4大氧化铝生产国,每年排放的赤泥高达数百万吨。目前,赤泥综合利用仍属世界性难题,现有的赤泥综合利用主要包括赤泥提取有价金属,配料生产水泥、建筑用砖、矿山胶结充填胶凝材料、路基固结材料和高性能混凝土掺合料、化学结合陶瓷(cbc)复合材料、保温耐火材料、环保材料等。但这些研究尚处于实验室阶段,还未实现产业化。
3.现阶段新能源汽车销量快速增长,而由于磷酸铁锂具有的低成本高安全等优点,磷酸铁锂电池的装机量也呈现出爆发式增长的态势。目前磷酸铁锂主流制备工艺采用磷酸铁作为铁源,其制备工艺较为复杂,导致铁锂制造成本相对较高。由于赤泥中含有较高含量的铁,若能够将其运用于磷酸铁锂制备的铁源,不仅会丰富磷酸铁锂的铁源路径,实现赤泥的高价值利用,而且也能够降低磷酸铁锂的制造成本。
4.现有技术中还没有以高铁拜耳法赤泥为铁源制备磷酸铁锂正极材料的相关报道,如何开发一种以高铁拜耳法赤泥为铁源制备磷酸铁锂正极材料的方法,为该类巨大堆存量固体废物的高值化利用提供新途径,成为亟待解决的技术问题。
技术实现要素:
5.针对现有技术所存在的技术问题,本发明提供了一种以高铁拜耳法赤泥为铁源制备磷酸铁锂正极材料的方法,实现了高铁拜耳法赤泥的资源化利用,制备得到超细纳米磷酸铁锂,可用于制备高倍率的磷酸铁锂正极材料。
6.本发明采用如下技术方案:
7.一种以高铁拜耳法赤泥为铁源制备磷酸铁锂正极材料的方法,所述方法包括:
8.将赤泥与硫酸进行酸浸反应,后固液分离,获得第一固体和第一液体;其中,所述硫酸与所述赤泥的加入量按照重量比为(3-6):1,所述硫酸的质量分数为60-80%;
9.向所述第一液体中加入重金属捕捉剂进行反应,后固液分离,获得脱除重金属的液体;
10.向所述脱除重金属的液体加入ph调节剂以调节ph至7.0-9.5,后固液分离,获得第二固体和第二液体;
11.向所述第二固体加入碱液以调节ph至12
±
0.5,后固液分离,获得氢氧化亚铁和氢氧化铁混合滤饼以及偏铝酸钠滤液;
12.将所述混合含铁滤饼采用ph为12
±
0.5碱液进行洗涤,获得洗涤混合含铁滤饼;
13.将所述洗涤混合含铁滤饼加水混匀,获得固含量为10-15%的浆料;
14.向所述浆料中加入磷酸二氢铵、碳酸锂和葡萄糖,后加入纯水,充分搅拌混匀,获得磷酸铁锂前驱体浆料;其中,所述磷酸二氢铵、碳酸锂的加入量按照锂、铁、磷的物质的量之比li:fe:p=(1.02-1.05):1:1加入;所述葡萄糖加入量为最终铁锂产品中碳含量的1.4wt%-1.7wt%;所述纯水加入量为控制固含量为32-35%;所述固含量是指浆料中固相质量与总质量的比值。
15.将所述磷酸铁锂前驱体浆料经砂磨、喷雾干燥、烧结、粉碎和筛分除铁,获得成品磷酸铁锂。
16.在上述技术方案中,所述硫酸与所述赤泥的加入量按照重量比为(3-6):1,所述硫酸的质量分数为60-80%;
17.优选地,所述硫酸与所述赤泥的加入量按照重量比为(4-5):1,所述硫酸的质量分数为65-75%。
18.调节溶液ph至7.0-9.5以使铁离子(亚铁和三价铁)和铝离子发生反应,生成氢氧化铁、氢氧化亚铁和氢氧化铝沉淀,若ph小于7.0则不利于亚铁离子沉淀反应完全,若大于9.5,镁离子也会发生沉淀反应,导致引入杂质镁离子,同时还会造成ph调节剂浪费。
19.调节ph至12
±
0.5,充分搅拌使氢氧化铝溶解生成偏铝酸钠溶液,若ph小于11.5,氢氧化铝转化不完全,若大于12.5,会造成碱液浪费;
20.上述技术方案中,去除重金属(如铜、铅、锌、镍、镉等),加入重金属捕捉剂;所述重金属捕捉剂包括硫化钠,硫化铵,硫化钾中的至少一种。所述重金属捕捉剂的加入量(质量)按照溶液总体积的(0.02-0.04)g/l加入,加入后继续搅拌反应15-30min;
21.作为一种可选的技术方案,所述酸浸反应的温度为20-30℃,所述酸浸反应的时间为50-80min。
22.在上述技术方案中,酸浸反应的温度在常温下即可,酸浸反应的时间为50-80min,有利于提高铁的浸出率,高达90-93%,若酸浸的时间过短,不利于提高铁的浸出率,若酸浸的时间过长,会降低生产效率;
23.优选地,所述ph调节剂包括氢氧化钠、碳酸钠、碳酸氢钠、氨水、碳酸铵和碳酸氢铵中的一种,所述ph调节剂的质量分数为25-35%。
24.优选地,所述第二液体含有硫酸钠/硫酸铵,可用于制备副产芒硝或者硫酸铵肥料。
25.上述技术方案中,所述洗涤中,向洗水中通入二氧化碳时不会产生白色沉淀为止。
26.上述技术方案中,所述磷酸二氢铵、碳酸锂的加入量按照锂、铁、磷的物质的量之比li:fe:p=(1.02-1.05):1:1的原因为:锂略过量,有利于细化晶粒,缓解晶粒间的烧结融合,有助于提高磷酸铁锂材料的倍率放电性能。
27.所述纯水加入量为控制固含量为32-35%的原因:若固含量过高,会导致浆料粘度过大,喷雾干燥过程中容易堵塞雾化器;若固含量过低则喷雾产能较低,能耗较高。
28.优选地,所述砂磨中,采用砂磨机进行研磨,研磨介质采用直径0.3mm的氧化锆珠,研磨至浆料粒径d50为350-500nm。
29.优选地,所述喷雾干燥中,采用离心式喷雾干燥机,雾化轮的线速度控制在7500-8500m/s,干燥过程采用热空气做为热源,热空气的温度为240-250℃,出料温度为85-90℃,控制干燥后的物料粒径d50:4-8μm,水分《1.0%。
30.优选地,所述烧结中,采用气氛辊道炉进行烧结,惰性气体采用氮气,在750-780℃条件下保温8-10h,控制炉内氧含量<1ppm,炉内压力10-15pa。
31.烧结过程中发生的反应如下:
32.2fe(oh)2+li2co3+2nh4h2po4=2lifepo4+2nh3↑
+co2↑
+5h2o
↑
33.2fe(oh)3+li2co3+2nh4h2po4+c=2lifepo4+2nh3↑
+co2↑
+co
↑
+6h2o
↑
34.优选地,所述粉碎和筛分中,将所述烧结获得的烧结料经过气流粉碎至粒径d50为0.6-1.5μm后,过超声波振动筛进行筛分,筛网目数为60-80目,采用2级电磁除铁器进行除铁,除铁至磁性物质<0.3ppm后停止。
35.其中,所述赤泥的成分以质量分数计包括:fe2o3:25-60%,al2o3:10-30%,si2o2:5-25%,cao:2-10%,na2o:5-10%,tio2:2-6%,mgo:0.5-2%,feo:2-5%。
36.与现有技术相比,本发明的有益效果为:
37.1、本发明提供的一种以高铁拜耳法赤泥为铁源制备磷酸铁锂正极材料的方法通过控制酸浸反应的条件(所述硫酸与所述赤泥的加入量按照重量比为(3-6):1,所述硫酸的质量分数为60-80%)以提高铁的浸出率;通过加入重金属捕捉剂去除重金属离子;通过调节溶液ph至7.0-9.5以使铁离子(亚铁和三价铁)和铝离子发生沉淀反应,生成氢氧化铁、氢氧化亚铁和氢氧化铝混合沉淀,再调节混合沉淀的ph至12
±
0.5,充分搅拌使氢氧化铝沉淀溶解生成偏铝酸钠溶液,得到含铁沉淀,经洗涤后中加入磷酸二氢铵、碳酸锂、葡萄糖和纯水,混匀反应,获得磷酸铁锂前驱体浆料,经砂磨、喷雾干燥、烧结、粉碎和筛分,获得成品磷酸铁锂;从而实现了高铁拜耳法赤泥的资源化利用。
38.2、本发明方法中铁的利用率达到90%以上,可有效利用赤泥中的铁资源;同时由于氢氧化(亚)铁胶体颗粒较小,容易制备得到超细纳米磷酸铁锂,本发明方法获得的电池级纳米无水磷酸铁锂粒径分布均匀,分散性好;可用于制备倍率型的磷酸铁锂电池。
附图说明
39.图1为本发明实施例提供的一种以高铁拜耳法赤泥为铁源制备磷酸铁锂正极材料的方法的流程图;
40.图2为本发明实施例1所得的磷酸铁锂正极材料的在1μm尺度下电镜图;
41.图3为本发明实施例1所得的磷酸铁锂正极材料的粒度分布图;
42.图4为本发明实施例1所得的磷酸铁锂正极材料的在100nm尺度下的电镜图。
具体实施方式
43.下文将结合具体实施方式和实施例,具体阐述本发明实施例,本发明实施例的优点和各种效果将由此更加清楚地呈现。本领域技术人员应理解,这些具体实施方式和实施例是用于说明本发明实施例,而非限制本发明实施例。
44.本发明实施例提供的技术方案为解决上述技术问题,总体思路如下:
45.本发明首先将赤泥进行酸浸,固液分离后,第一液体中主要含有硫酸铝、硫酸铁、硫酸亚铁、硫酸镁和硫酸钠,第一固体中主要是硫酸钙、二氧化硅和二氧化钛;铁的浸出率为90-93%;
46.然后通过加入重金属捕捉剂去除重金属离子,固液分离后获得脱除重金属的液
体;
47.接着向所述脱除重金属的液体加入ph调节剂以调节ph至7.0-9.5提铁铝。以使铁离子(亚铁和三价铁)和铝离子发生沉淀反应,生成氢氧化亚铁、氢氧化铁和氢氧化铝沉淀;
48.向所述第二固体加入碱液以调节ph至12
±
0.5,后固液分离,获得氢氧化亚铁和氢氧化铁混合含铁滤饼和偏铝酸钠滤液;偏铝酸钠溶液可以用来提铝;
49.将所述混合含铁滤饼采用ph为12
±
0.5碱液进行洗涤,获得洗涤混合含铁滤饼;
50.将所述洗涤混合含铁滤饼加水混匀,获得固含量为10-15%的浆料;
51.向所述浆料中加入磷酸二氢铵、碳酸锂、葡萄糖和纯水,混匀反应,获得磷酸铁锂前驱体浆料;其中,所述磷酸二氢铵、碳酸锂的加入量按照锂、铁、磷的物质的量之比li:fe:p=(1.02-1.05):1:1加入;所述葡萄糖加入量按照最终铁锂产品中碳含量为1.4wt%-1.7wt%;所述纯水加入量为控制固含量为32-35%;
52.将所述磷酸铁锂前驱体浆料经砂磨、喷雾干燥、烧结、粉碎和筛分,获得成品磷酸铁锂。
53.下面将结合实施例、对比例及实验数据对本技术的一种碳化硅捣打料的成型方法进行详细说明。
54.以下各实施例,仅用于说明本发明,但不止用来限制本发明的范围。基于本发明中的具体实施例,本领域普通技术人员在没有做出创造性劳动的情况下,所获得的其他所有实施例,都属于本发明的保护范围。
55.在本发明实施例中,若无特殊说明,所有原料组分均为本领域技术人员熟知的市售产品;在本发明实施例中,若未具体指明,所用的技术手段均为本领域技术人员所熟知的常规手段。在本发明实施例中,所使用的原料均为常规市售产品。
56.本发明实施例中步骤s1中铁的浸出率,乘以后面步骤铁的得率即为最后铁的利用率(即回收率)。
57.实施例1
58.本发明实施例提供了一种以高铁拜耳法赤泥为铁源制备磷酸铁锂正极材料的方法,如图1所示,所述方法包括:
59.步骤s1、酸浸。高铁拜耳法赤泥与硫酸发生酸浸反应,硫酸与赤泥的加入量按照重量比5:1,硫酸浓度为70%,反应时间为60min,反应温度为常温;过滤得滤液和滤渣;滤液中主要含有硫酸铝、硫酸铁、硫酸亚铁、硫酸镁和硫酸钠,滤渣中主要是硫酸钙、二氧化硅和二氧化钛;铁的浸出率为90-93%。
60.步骤s2、除重金属:向所述第一液体中加入硫化钠进行反应,后固液分离,获得脱除重金属的液体;其中,硫化钠的加入量按照溶液总体积的0.03g/l加入;
61.步骤s3、提铁铝。通过调节溶液ph至8.5以使铁离子(亚铁和三价铁)和铝离子发生沉淀反应,生成氢氧化亚铁、氢氧化铁和氢氧化铝的混合沉淀;
62.步骤s4、提铁。再调节混合沉淀的ph至12,充分搅拌使氢氧化铝沉淀溶解生成偏铝酸钠溶液,得到混合含铁沉淀;偏铝酸钠溶液可以用来提铝;
63.步骤s5、洗涤。将上述混合含铁滤饼采用ph=12氢氧化钠溶液进行洗涤,去除滤饼中残留的偏铝酸钠,洗涤至向洗水中通入二氧化碳时不会产生白色沉淀。
64.步骤s6、磷酸铁锂制备。
65.向步骤s5中洗涤后的氢氧化亚铁滤饼中加入纯水制浆,浆料固含量为12%,取样测试全铁含量。
66.向所述浆料中加入磷酸二氢铵、碳酸锂和葡萄糖,后加入纯水,充分搅拌混匀,获得磷酸铁锂前驱体浆料;其中,所述磷酸二氢铵、碳酸锂的加入量按照锂、铁、磷的物质的量之比li:fe:p=1.03:1:1加入,所述葡萄糖加入量按照最终铁锂产品中碳含量为1.5wt%;所述纯水加入量为控制固含量为33%;
67.将所述磷酸铁锂前驱体浆料经砂磨、喷雾干燥、烧结、粉碎和筛分,获得成品磷酸铁锂。
68.实施例2
69.本发明实施例提供了一种以高铁拜耳法赤泥为铁源制备磷酸铁锂正极材料的方法,所述方法包括:
70.步骤s1、酸浸。高铁拜耳法赤泥与硫酸发生酸浸反应,硫酸与赤泥的加入量按照重量比3:1,硫酸浓度为60%,反应时间为50min,反应温度为常温;过滤得滤液和滤渣;滤液中主要含有硫酸铝、硫酸铁、硫酸亚铁、硫酸镁和硫酸钠,滤渣中主要是硫酸钙、二氧化硅和二氧化钛;铁的浸出率为90-93%。
71.步骤s2、除重金属:向所述第一液体中加入硫化钠进行反应,后固液分离,获得脱除重金属的液体;其中,硫化钠的加入量按照溶液总体积的0.02g/l加入;
72.步骤s3、提铁铝。通过调节溶液ph至7以使铁离子(亚铁和三价铁)和铝离子发生沉淀反应,生成氢氧化亚铁、氢氧化铁和氢氧化铝混合沉淀;
73.步骤s4、提铁。再调节混合沉淀的ph至11.5,充分搅拌使氢氧化铝沉淀溶解生成偏铝酸钠溶液,得到氢氧化亚铁和氢氧化铁混合含铁沉淀;偏铝酸钠溶液可以用来提铝;
74.步骤s5、洗涤。将上述混合含铁滤饼采用ph=11.5氢氧化钠溶液进行洗涤,去除滤饼中残留的偏铝酸钠,洗涤至向洗水中通入二氧化碳时不会产生白色沉淀。
75.步骤s6、磷酸铁锂制备。
76.向步骤s5中洗涤后的混合含铁滤饼中加入纯水制浆,浆料固含量为12%,取样测试铁含量。
77.向所述浆料中加入磷酸二氢铵、碳酸锂和葡萄糖,后加入纯水,充分搅拌混匀,获得磷酸铁锂前驱体浆料;其中,所述磷酸二氢铵、碳酸锂的加入量按照锂、铁、磷的物质的量之比li:fe:p=1.02:1:1加入,所述葡萄糖加入量按照最终铁锂产品中碳含量为1.4wt%;所述纯水加入量为控制固含量为32%;
78.将所述磷酸铁锂前驱体浆料经砂磨、喷雾干燥、烧结、粉碎和筛分,获得成品磷酸铁锂。
79.实施例3
80.本发明实施例提供了一种以高铁拜耳法赤泥为铁源制备磷酸铁锂正极材料的方法,所述方法包括:
81.步骤s1、酸浸。高铁拜耳法赤泥与硫酸发生酸浸反应,硫酸与赤泥的加入量按照重量比6:1,硫酸浓度为80%,反应时间为80min,反应温度为常温;过滤得滤液和滤渣;滤液中主要含有硫酸铝、硫酸铁、硫酸亚铁、硫酸镁和硫酸钠,滤渣中主要是硫酸钙、二氧化硅和二氧化钛;铁的浸出率为90-93%。
82.步骤s2、除重金属:向所述第一液体中加入硫化钠进行反应,后固液分离,获得脱除重金属的液体;其中,硫化钠的加入量按照溶液总体积的0.04g/l加入;
83.步骤s3、提铁铝。通过调节溶液ph至9.5以使铁离子(亚铁和三价铁)和铝离子发生沉淀反应,生成氢氧化亚铁、氢氧化铁和氢氧化铝沉淀;
84.步骤s4、提铁。再调节混合沉淀的ph至12.5,充分搅拌使氢氧化铝沉淀溶解生成偏铝酸钠溶液,得到氢氧化亚铁和氢氧化铁混合含铁沉淀;偏铝酸钠溶液可以用来提铝;
85.步骤s5、洗涤。将上述混合含铁滤饼采用ph=12.5氢氧化钠溶液进行洗涤,去除滤饼中残留的偏铝酸钠,洗涤至向洗水中通入二氧化碳时不会产生白色沉淀。
86.步骤s6、磷酸铁锂制备。
87.向步骤s5中洗涤后的混合含铁滤饼中加入纯水制浆,浆料固含量为12%,取样测试铁含量。
88.向所述浆料中加入磷酸二氢铵、碳酸锂和葡萄糖,后加入纯水,充分搅拌混匀,获得磷酸铁锂前驱体浆料;其中,所述磷酸二氢铵、碳酸锂的加入量按照锂、铁、磷的物质的量之比li:fe:p=1.05:1:1加入;所述葡萄糖加入量按照最终铁锂产品中碳含量为1.7wt%;所述纯水加入量为控制固含量为35%;
89.将所述磷酸铁锂前驱体浆料经砂磨、喷雾干燥、烧结、粉碎和筛分,获得成品磷酸铁锂。
90.对比例1
91.该对比例中,所述酸浸反应中,所述硫酸与所述赤泥的加入量按照重量比为2:1;其他步骤均同实施例1。
92.实验例1
93.1、对各实施例和各对比例中铁的利用率(即回收率)统计如表1所示。
94.表1
95.组别铁的利用率%实施例192.03实施例291.95实施例392.27对比例182.56
96.由表1的数据,可知:
97.对比例1中,浸出过程中硫酸用量偏低,导致赤泥中铁的浸出率较低,铁的利用率偏低;
98.实施例1-实施例3中,铁的利用率达到90%以上。
99.2、对实施例1的磷酸铁锂以及外购市售磷酸铁锂材料进行检测,检测结果如表2所示;
100.表2
[0101][0102]
由表2对比数据可知,与市售商品化磷酸铁锂产品相比,本发明实施例得到的铁锂产品各项指标均达到了电池级磷酸铁锂的标准,部分杂质元素,如ca、mg、na、al等,含量均低于商业料。
[0103]
在此有必要指出的是,以上实施例仅限于对本发明的技术方案做进一步的阐述和说明,并不是对本发明的技术方案的进一步的限制,本发明的方法仅为较佳的实施方案,并非用于限定本发明的保护范围。凡在本发明的精神和原则之内,所作的任何修改、等同替换、改进等,均应包含在本发明的保护范围之内。