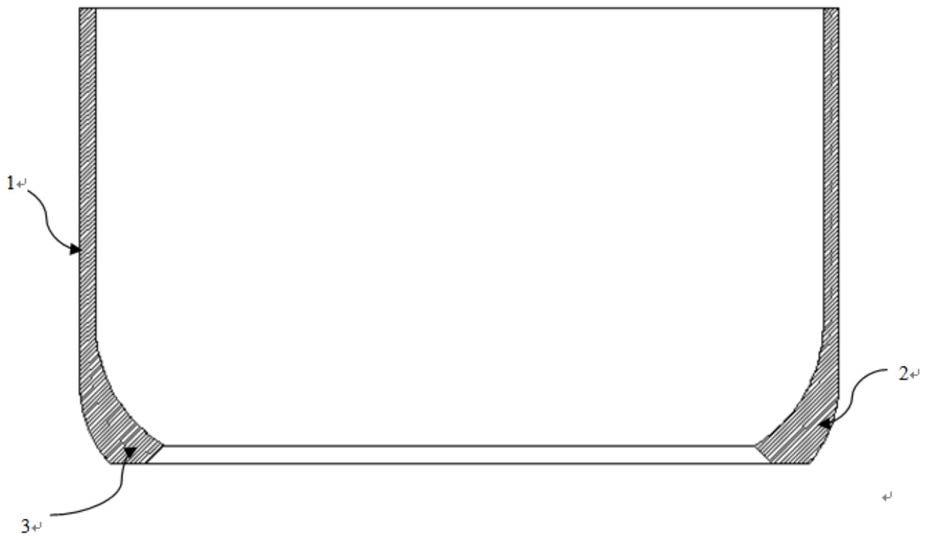
1.本发明属于光伏拉晶技术领域,尤其涉及一种高寿命碳碳埚帮的制备方法。
背景技术:
2.碳/碳复合材料是20世纪60年代发展起来的一种性能独特的新型高温材料,它综合了纤维增强复合材料优良的力学性能及碳质材料优异的高温性能,具有高的比强度、比模量,良好的韧性以及高温下优良的强度保持率、耐蠕变和抗热震等一系列优异性能。它是目前所知的惰性气氛下最为理想的高温结构材料。因此被广泛应用与单晶炉、铸锭炉热场部件中。
3.单晶炉热场中,埚帮是最常用的碳碳复合材料热场之一。埚帮主要分为直筒埚帮和r弧埚帮两种。在使用的过程中,直筒埚帮需要和单独的埚托环配合,而r弧埚帮可以直接使用,并且寿命比直筒埚帮场,性价比较高,因此在单晶热场中使用的越来越广泛。r弧碳碳埚帮主要是通过预制体成形、沉积、石墨化处理、机加、涂层等过程进行制备。其预制体端最主要的辅材为碳纤维,碳纤维价格占据预制体成本的80%以上。埚帮的预制体的制备过程包括:采用碳纤维编织成碳布;采用短切碳纤维制备成网胎;将碳布缠绕在埚帮模具上,然后通过针刺网胎,将碳布与碳布层与层之间连接起来,起到固定作用。最终再切除多余的部分形成预制体。由于预制体容易变形,为了保证一定的加工余量,通常预制体壁厚都制备的非常厚,最终机加时,将近一半的碳纤维都被机加掉,造成成本浪费。然而直接降低预制体的壁厚,又会导致产品在沉积时容易变形,最后无法加工出合格产品,造成巨大的成本浪费。
4.单晶炉热场中,埚帮主要分为直筒埚帮和r弧埚帮两种。在使用的过程中,直筒埚帮需要和单独的埚托环配合,而r弧埚帮可以直接使用,并且寿命比直筒埚帮长,性价比较高,因此在单晶热场中使用的越来越广泛。r弧碳碳埚帮主要是通过预制体成形、沉积、石墨化处理、机加、涂层等过程进行制备。其预制体端最主要的辅材为碳纤维,碳纤维价格占据预制体成本的80%以上。由于预制体容易变形,为了保证一定的加工余量,通常预制体壁厚都制备的非常厚,最终机加时,将近一半的碳纤维都被机加掉,造成成本浪费。然而直接降低预制体的壁厚,又会导致产品在沉积时容易变形,最后无法加工出合格产品,造成巨大的成本浪费。在埚帮的使用过程中,由于硅蒸汽的腐蚀,埚口和r弧处是最容易腐蚀的地方,常常是埚帮埚口、r弧处已经开裂,而直筒部分完好。
技术实现要素:
5.有鉴于此,本发明的目的在于提供一种高寿命碳碳埚帮的制备方法,本发明提供的方法能够提升埚帮预制体碳纤维利用率的方法,进而减少碳纤维使用量,降低成本。
6.本发明提供了一种高寿命碳碳埚帮的制备方法,包括:
7.制备高寿命碳碳埚帮过程中的埚帮预制体的内径的单边加工余量为2~4mm,外径的单边加工余量为1~3mm,r弧处的单边加工余量为2~10mm;
8.r弧处补圆弧的次数为5~10层;
9.对埚底进行1~3层的复合布的修补。
10.优选的,还包括:
11.制备高寿命碳碳埚帮过程中埚口处的碳布重量为400~450g/m2;
12.针刺密度为35~55针/cm2。
13.优选的,还包括:
14.制备高寿命碳碳埚帮过程中采用水溶性树脂对预制体进行喷淋定型。
15.优选的,所述埚帮预制体的r弧处的弧度为115
°
~120
°
。
16.优选的,所述埚帮预制体的碳布层数为16~18层。
17.优选的,所述高寿命碳碳埚帮的制备方法具体包括:
18.制备埚帮预制体;
19.采用水溶性树脂对所述埚帮预制体进行喷胶;
20.对喷胶后的埚帮预制体进行干燥;
21.对干燥后的埚帮预制体及进行沉积;
22.将沉积后的埚帮预制体进行石墨化处理;
23.对石墨化处理后的埚帮预制体进行机加工;
24.对机加工后的埚帮预制体进行封孔。
25.优选的,所述埚帮预制体的直筒壁厚为20~25mm。
26.优选的,所述干燥的温度为150~250℃。
27.优选的,所述沉积的温度为900~1200℃。
28.优选的,所述石墨化处理的温度为1700~2100℃。
29.本发明首先对埚帮和埚帮的模具尺寸进行调整,进而增大预制体内径。其次对针刺工艺进行调整,采用复合布增加r弧处补圆弧的次数,并对埚底进行一定层数的修补,以保证最容易变形导致无法加工出来的r弧和埚底部分有充足的加工余量。最后,通过多次试验确定最终外径尺寸。为了降低预制体变形的风险,采用水溶性树脂对预制体进行喷淋,然后进行烘干,烘干后预制体具有一定的强度,降低了其在沉积过程中被其他预制体压变形的风险。采用本发明提供的方法能够降低预制体的碳纤维用量,同时降低预制体壁厚,以利于沉积。本发明可以在基本不改变r弧埚帮成品的前提下大幅度降低碳纤维用量,提升针刺效率;降低预制体沉积时间,提升沉积效率。
附图说明
30.图1为本发明实施例制备的r弧埚帮成品示意图,r弧埚帮主要有以下三个主要部分:1直筒部分、2r弧部分、3埚底;成品埚帮直筒部门较薄,r弧处相对较厚。
具体实施方式
31.下面将结合本发明实施例中的附图,对本发明实施例中的技术方案进行清楚、完整地描述,显然,所描述的实施例仅仅是本发明一部分实施例,而不是全部的实施例。基于本发明中的实施例,本领域普通技术人员在没有做出创造性劳动前提下所获得的所有其他实施例,都属于本发明保护的范围。
32.本发明提供了一种高寿命碳碳埚帮的制备方法,包括:
33.制备高寿命碳碳埚帮过程中的埚帮预制体的内径的单边加工余量为2~4mm,外径的单边加工余量为1~3mm,r弧处的单边加工余量为2~10mm;
34.r弧处补圆弧的次数为5~10层;
35.对埚底进行1~3层数的修补。
36.在本发明中,32吋埚帮预制体的内径优选为800~806mm,更优选为802~804mm,最优选为803mm;外径优选为858~864mm,更优选为860~862mm,最优选为861mm;36吋埚帮预制体的内径优选为900~910mm,更优选为903~907mm,最优选为905mm;外径优选为964~972mm,更优选为966~970mm,最优选为968mm;37吋预制体的内径优选为938~946mm,更优选为940~944mm,最优选为942mm;外径优选为990~998mm,更优选为992~996mm,最优选为994mm。
37.在本发明中,所述埚帮预制体内径的单边加工余量优选为2~4mm,更优选为2.5~3.5mm,最优选为3mm;外径的单边加工余量优选为1~3mm,更优选为1.5~2.5mm,最优选为2mm;r弧处的单边加工余量优选为2~10mm,更优选为3~8mm,最优选为4~6mm。
38.在本发明中,所述r弧处补圆弧的次数优选为6~9层,更优选为7~8层。
39.在本发明中,优选对埚底进行2层数的修补。
40.本发明通过增大r弧埚帮预制体内径、降低外径;调整针刺工艺,采用复合布增加r弧处补圆弧的次数,并对埚底进行一定层数的修补;以保证最容易变形导致无法加工出来的r弧和埚底部分有充足的加工余量。
41.在本发明中,所述高寿命碳碳埚帮的制备方法优选还包括:
42.制备高寿命碳碳埚帮过程中埚口处的碳布重量为400~450g/m2;
43.针刺密度为35~55针/cm2。
44.在本发明中,所述埚口处的碳布重量优选为410~440g/m2,更优选为420~430g/m2。
45.在本发明中,所述针刺密度优选为40~50针/cm2,最优选为45针/cm2。
46.本发明通过对埚口处增加大克重碳布和针刺密度,提升埚帮埚口强度。
47.在本发明中,所述高寿命碳碳埚帮的制备方法优选还包括:
48.制备高寿命碳碳埚帮过程中采用水溶性树脂对预制体进行喷淋定型。
49.在本发明中,所述水溶性树脂可以为酚醛树脂、环氧树脂或丙烯酸树脂;可以采用上海博立尔水溶性丙烯酸树脂bm723。
50.本发明采用水溶性树脂对预制体进行喷淋定型以降低预制体变形的风险,然后进行烘干,烘干后预制体具有一定的强度,降低了其在沉积过程中被其他预制体压变形的风险。
51.本发明首先对埚帮和埚帮的模具尺寸进行调整,进而增大预制体内径。其次对针刺工艺进行调整,采用复合布增加r弧处补圆弧的次数,并对埚底进行一定层数的修补,进而增加r弧处的厚度与密度。同理,对埚口处采用大克重碳布进行增补,增加针刺密度,进而提升埚帮处的预制体密度。为了降低预制体变形的风险,采用水溶性树脂对预制体进行喷淋,然后进行烘干,烘干后预制体具有一定的强度,降低了其在沉积过程中被其他预制体压变形的风险。采用本发明提供的方法能够降低预制体的碳纤维用量,同时降低预制体壁厚,
以利于沉积。
52.在本发明中,所述埚帮预制体的r弧处的弧度优选为115
°
~120
°
,更优选为116~118
°
。
53.在本发明中,所述埚帮预制体的碳布层数优选为16~18层,更优选为17层。
54.在本发明中,所述埚帮预制体的制备过程中优选单数层补2~4层复合布,更优选为3层;双数层补1~3层复合布,优选补2层。
55.在本发明中,所述埚帮预制体制备过程中从第3层起,采用复合布补r弧处和埚底处;所述r弧处优选补2~5层,更优选为3~4层;所述埚底处优选补2~5层(r弧和埚底分别补2~5层),更优选为4层;优选从第15层后补埚底1~3层,更优选为2层。
56.在本发明中,所述高寿命碳碳埚帮的制备方法优选具体包括:
57.制备埚帮预制体;
58.采用水溶性树脂对所述埚帮预制体进行喷胶;
59.对喷胶后的埚帮预制体进行干燥;
60.对干燥后的埚帮预制体及进行沉积;
61.将沉积后的埚帮预制体进行石墨化处理;
62.对石墨化处理后的埚帮预制体进行机加工;
63.对机加工后的埚帮预制体进行封孔。
64.在本发明中,所述埚帮预制体的直筒壁厚优选为20~25mm,更优选为21~24mm,最优选为23mm。
65.在本发明中,所述埚帮预制体的制备方法优选包括:
66.在木模上铺设一层碳布,再铺设2层网胎,针刺碳布制备得到埚帮预制体。
67.在本发明中,优选在木模上粘贴一层pvc(聚氯乙烯),pvc和木模之间用热缩膜隔开,以保证将来埚帮预制体能够顺利从木模上脱模。
68.在本发明中,所述pvc的厚度优选为8~12mm,更优选为9~11mm,最优选为10mm。
69.在本发明中,所述碳布优选选自平纹布、斜纹布和单向布中的一种或几种,更优选为平纹布。
70.在本发明中,所述网胎优选为碳纤维经过切割成短切纤维后,经过梳理机梳理形成的薄碳毡。
71.在本发明中,所述针刺碳布过程中优选针刺15~21层,更优选16~20层,更优选为17~19层,最优选为18层。
72.在本发明中,所述针刺碳布过程中优选从第3层起,用复合布对圆弧处进行修补,单数层修补的层数优选为2~4层,更优选为3层;双数层修补的层数优选为1~3层,更优选为2层。
73.在本发明中,所述针刺碳布过程中优选从第15层起,测量埚底厚度,若埚底厚度不足28mm,用复合布修补埚底;修补的层数优选为1~2层。
74.在本发明中,所述复合布的制备方法优选包括:
75.将网胎针刺至碳布上,制备得到复合布。
76.在本发明中,所述针刺优选采用平板针刺机。
77.在本发明中,所述针刺碳布过程中优选从第四层起,采用380~420g/m2重碳布,更
优选为390~410g/m2,最优选为400g/m2;针刺密度优选为40~50针/平方厘米,更优选为42~48针/平方厘米,最优选为44~46针/平方厘米。
78.在本发明中,针刺碳布过程中前三层的碳布重优选为380~420g/m2,更优选为390~410g/m2,最优选为400g/m2;针刺密度优选为35~45针/平方厘米,更优选为38~42针/平方厘米,最优选为40针/平方厘米。
79.在本发明中,所述制备埚帮预制体过程中优选对r弧部分采用样板进行矫正。
80.在本发明中,所述制备埚帮预制体过程中优选采用复合布对埚口进行补足,所述复合布中的碳布优选为大克重碳布,所述大克重碳布的重量优选为400~450g/m2,更优选为410~440g/m2,最优选为420~430g/m2;所述复合布的宽幅优选为5~30mm,更优选为10~25mm,最优选为15~20mm;所述针刺碳布过程中优选每针刺4层碳布对埚口补足一层复合布,补埚口时复合布优选一边紧贴埚口上沿。
81.本发明通过埚帮预制体埚口增强的方法,以提升埚口的强度和抗氧化性,对埚帮预制体埚口进行设计,埚口的碳纤维含量比其它部分高;在不改变埚帮成品尺寸基础上,通过补埚口来提高埚口碳纤维的含量,增强埚口的力学性能和抗氧化、抗腐蚀性能。
82.在本发明中,所述喷胶之后优选还包括:
83.进行自然晾干,使埚帮预制体具有一定的硬度。
84.在本发明中,所述干燥优选在烘箱中进行烘干,所述干燥的温度优选为150~250℃,更优选为180~220℃,最优选为200℃;时间优选为2~6小时,更优选为3~5小时,最优选为4小时。
85.在本发明中,所述沉积的时间优选为600~750h,更优选为650~700h,最优选为660~680h;温度优选为900~1200℃,更优选为1000~1100℃,最优选为1050℃。
86.在本发明中,所述沉积过程中优选采用天然气作为前驱体,使预制体密度达到1.3左右后再进行石墨化处理。
87.在本发明中,所述石墨化处理的温度优选为1700~2100℃,更优选为1800~2000℃,最优选为1900℃。
88.在本发明中,所述机加工过程中优选车基准时,单次进刀量为1mm,以确保没有未见光情况。
89.本发明的关键在于需要通过大量的试验分析找出合适的加工余量,重新设计预制体模具、样板及预制体;降低了r弧埚帮预制体直筒部分壁厚,而保障了r弧部分有充足的加工余量;本发明对埚帮预制体进行重新设计,降低预制体直筒部分厚度,增加r弧处厚度;并且需要调整预制体针刺工艺,增加补r弧和补埚底的过程;同时,对最容易腐蚀的埚口处,采用大克重碳布进行增补,并增加针刺密度;最后再采用水溶性树脂对预制体进行定型以降低预制体变形风险,从而实现预制体碳纤维用量大幅度降低,由于壁厚降低,同时也提高了沉积效率;而埚口、r弧等容易损坏的地方得到了加强,进而提升寿命。采用本发明提供的方法能够提升埚帮寿命,降低预制体的碳纤维用量,同时降低预制体壁厚,以利于沉积。
90.实施例1
91.采用大直径木模,在木模上紧紧粘贴上一层pvc,pvc厚度约为10mm;pvc和木模之间用热缩膜隔开,以保证将来预制体能够顺利从木模上脱模;
92.用平板针刺机,将网胎针刺至碳布上,制备成复合布;碳布为平纹布;
93.制备直筒壁厚为25mm、r弧壁厚约为40mm的32吋埚帮预制体(内径为808mm,外径为858mm,内径单边机加余量3mm,外径单边机加余量2mm;r弧处单边机加余量7mm);铺设一层碳布,用碳纤维缠绕将碳布勒紧至模具上,在铺设2层网胎,用针刺机对其进行针刺;
94.一共针刺约17层,从第3层起,单数层用窄复合布补3层圆弧,双数层用窄复合布补2层圆弧,第15层时,测量埚底厚度,如果厚度不足28mm,用宽复合布补1至2层埚底;
95.从第4层起,每3层用补埚口的复合布补1层埚口,针刺工艺与其它层相同;
96.r弧部分采用样板进行矫正;
97.埚口处从第四层起,采用420g/m2重碳布,针刺密度为45针/平方厘米;碳纤维用量(包括碳布、网胎、绕丝用的碳纤维)24kg;
98.采用水溶性树脂(上海博立尔水溶性丙烯酸树脂bm723),对针刺好的埚帮进行喷胶,自然晾干,使埚帮预制体有一定的硬度;
99.对预制体在烘箱中进行烘干,烘干温度为150℃,时间为4h;
100.对埚帮预制体进行沉积,沉积时间为350h,温度为1050℃,前驱体采用天然气,预制体密度需达到1.3左右,然后进行石墨化处理,温度为2000℃;
101.对预制体进行机加,机加埚帮时,车基准时,单次进刀量为1mm,以确保没有未见光情况;
102.对机加后的埚帮进行封孔。
103.本发明实施例1制备的埚帮结构示意图如图1所示。
104.实施例1制备的产品在头部单晶厂单晶端使用时,使用平均寿命为310天。
105.对比例1
106.采用普通直径木模,在木模上紧紧粘贴上一层pvc,pvc厚度约为10mm;pvc和木模之间用热缩膜隔开,以保证将来预制体能够顺利从木模上脱模;
107.用平板针刺机,将网胎针刺至碳布上,制备成复合布;碳布为平纹布;
108.制备直筒壁厚为32mm、r弧壁厚约为40mm的32吋埚帮预制体(内径为802mm,外径为866mm,内径单边机加余量6mm,外径单边机加余量6mm;r弧处单边机加余量7mm);铺设一层碳布,用碳纤维缠绕将碳布勒紧至模具上,在铺设2层网胎,用针刺机对其进行针刺;
109.一共针刺约22层,采用330g/m2重碳布,针刺密度为35针/平方厘米;r弧部分采用样板进行矫正;碳纤维用量28kg;
110.对预制体在烘箱中进行烘干,烘干温度为150℃,时间为4h;
111.对埚帮预制体进行沉积,沉积时间为420h,温度为1000℃,前驱体采用天然气,预制体密度需达到1.3左右,然后进行石墨化处理,温度为2000℃;
112.对预制体进行机加;
113.对机加后的埚帮进行封孔。
114.与比较例1相比,实施例1可降低碳纤维使用量4kg/件,提升沉积效率70h,提高埚口的碳纤维含量,以达到提高埚口强度和抗氧化的目的。
115.对比例1制备的产品在头部单晶厂单晶端使用时,使用平均寿命为220天。
116.实施例2
117.采用大直径木模,在木模上紧紧粘贴上一层pvc,pvc厚度约为12mm;pvc和木模之间用热缩膜隔开,以保证将来预制体能够顺利从木模上脱模;
118.用平板针刺机,将网胎针刺至碳布上,制备成复合布;碳布为斜纹布;
119.制备直筒壁厚为22mm、r弧壁厚约为45mm的36吋埚帮预制体(内径为907mm,外径为951mm,内径单边机加余量2mm,外径单边机加余量1mm;r弧处单边机加余量8mm);铺设一层碳布,用碳纤维缠绕将碳布勒紧至模具上,在铺设2层网胎,用针刺机对其进行针刺;
120.一共针刺约15层,从第3层起,单数层用窄复合布补3层圆弧,双数层用窄复合布补2层圆弧,第15层时,测量埚底厚度,如果厚度不足28mm,用宽复合布补1至2层埚底;
121.从第4层起,每3层用补埚口的复合布补1层埚口,针刺工艺与其它层相同;
122.r弧部分采用样板进行矫正;
123.埚口处从第四层起,采用420g/m2重碳布,针刺密度为45针/平方厘米;碳纤维用量26kg;
124.采用水溶性树脂(上海博立尔水溶性丙烯酸树脂bm723),对针刺好的埚帮进行喷胶,自然晾干,使埚帮预制体有一定的硬度;
125.对预制体在烘箱中进行烘干,烘干温度为150℃,时间为4h;
126.对埚帮预制体进行沉积,沉积时间为300h,温度为1200℃,前驱体采用天然气,预制体密度需达到1.3左右,然后进行石墨化处理,温度为2000℃;
127.对预制体进行机加,机加埚帮时,车基准时,单次进刀量为1mm,以确保没有未见光情况;
128.对机加后的埚帮进行封孔。
129.实施例2制备的产品在头部单晶厂单晶端使用时,平均寿命达到300天。
130.对比例2
131.采用普通直径木模,在木模上紧紧粘贴上一层pvc,pvc厚度约为10mm;pvc和木模之间用热缩膜隔开,以保证将来预制体能够顺利从木模上脱模;
132.用平板针刺机,将网胎针刺至碳布上,制备成复合布;碳布为单向布;
133.制备直筒壁厚为28mm、r弧壁厚约为45mm的的36吋埚帮预制体(内径为902mm,外径为958mm,内径单边机加余量6mm,外径单边机加余量6mm,r弧处单边机加余量10mm);铺设一层碳布,用碳纤维缠绕将碳布勒紧至模具上,在铺设2层网胎,用针刺机对其进行针刺;
134.一共针刺约21层,r弧部分采用样板进行矫正;针刺密度为36针/平方厘米;采用330g/m2重碳布,碳纤维用量为30kg;
135.对预制体在烘箱中进行烘干,烘干温度为150℃,时间为4h;
136.对埚帮预制体进行沉积,沉积时间为430h,温度为1200℃,前驱体采用天然气,预制体密度需达到1.3左右,然后进行石墨化处理,温度为2000℃;
137.对预制体进行机加;
138.对机加后的埚帮进行封孔。
139.与对比例2相比,实施例2可降低碳纤维使用量4kg/件,提升沉积效率130h,提高埚口的碳纤维含量,以达到提高埚口强度和抗氧化的目的。
140.对比例2制备的产品在头部单晶厂单晶端使用时,平均寿命达到180天。
141.由以上实施例可知,本发明首先对埚帮和埚帮的模具尺寸进行调整,进而增大预制体内径。其次对针刺工艺进行调整,采用复合布增加r弧处补圆弧的次数,并对埚底进行一定层数的修补,进而增加r弧处的厚度与密度。同理,对埚口处采用大克重碳布进行增补,
增加针刺密度,进而提升埚帮处的预制体密度。本发明在不改变埚帮成品尺寸基础上,有效减薄预制体直筒部分的壁厚,并且保证r弧处有充足的加工余量,降低了碳纤维用量;同时,减薄埚帮预制体更有利于提高沉积效率,进而降低成本。为了降低预制体变形的风险,采用水溶性树脂对预制体进行喷淋,然后进行烘干,烘干后预制体具有一定的强度,降低了其在沉积过程中被其他预制体压变形的风险。采用本发明提供的方法能够降低预制体的碳纤维用量,同时降低预制体壁厚,以利于沉积。本发明在不改变埚帮成品尺寸基础上,有效减薄的预制体直筒部分的壁厚,并且保证r弧处有充足的加工余量,降低了碳纤维用量;同时,减薄埚帮预制体更有利于提高沉积效率,进而降低成本。本发明在不改变埚帮成品尺寸基础上,通过补埚口来提高埚口碳纤维的含量,增强的埚口的力学性能和抗氧化、抗腐蚀性能。
142.虽然已参考本发明的特定实施例描述并说明本发明,但是这些描述和说明并不限制本发明。所属领域的技术人员可清晰地理解,在不脱离如由所附权利要求书定义的本发明的真实精神和范围的情况下,可进行各种改变,以使特定情形、材料、物质组成、物质、方法或过程适宜于本技术的目标、精神和范围。所有此类修改都意图在此所附权利要求书的范围内。虽然已参考按特定次序执行的特定操作描述本文中所公开的方法,但应理解,可在不脱离本发明的教示的情况下组合、细分或重新排序这些操作以形成等效方法。因此,除非本文中特别指示,否则操作的次序和分组并非本技术的限制。