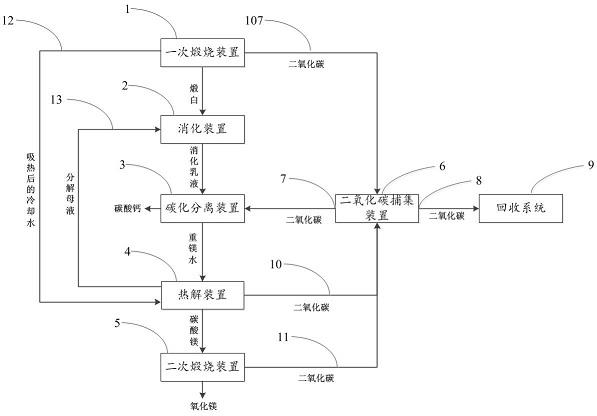
1.本发明涉及白云石的加工,尤其涉及一种白云石资源化深度利用成套处理系统和方法。
背景技术:
2.白云石是重要的钙镁资源,从白云石中获得钙镁材料的主要方法有碳化法、酸解法、铵浸法和卤化法;其中碳化法因生产成本较低,生产过程稳定尤为受到重视。
3.白云石碳化法的基本工艺包括:将白云石矿破碎后煅烧得到活性氧化钙和氧化镁,煅粉经消化除杂后转至碳化塔内,通入二氧化碳后,消化液中的氢氧化钙先发生沉淀反应生成碳酸钙,随着二氧化碳的持续加入,氢氧化镁转化为可溶性碳酸氢镁;当氢氧化镁完全转化时,停止碳化,过滤反应液,滤液为重镁水即碳酸氢镁溶液,滤渣为含杂碳酸钙;将上述滤液(重镁水)热解可以得到碱式碳酸镁沉淀,碱式碳酸镁沉淀经煅烧得到氧化镁。
4.例如:公告号为cn105271845b的中国发明专利公开了一种由白云石制备高性能硅钢用氧化镁的方法,其先将白云石通过煅烧,与水进行化合后在碳化塔中进行碳化,然后过滤分离固体碳酸钙与碳酸氢镁水溶液,得到的碳酸氢镁水溶液通过热解过滤,得到碳酸镁后分步煅烧,经气流粉碎包装后即得到高性能硅钢用氧化镁。该专利中的白云石经碳化法加工虽然获得了高性能的硅钢用氧化镁,但是,其是利用多次煅烧提纯才获得了性能上的提升,也未在白云石煅烧过程中获得含高纯二氧化碳的烟气,增加了整个加工过程的资源浪费与能耗。
5.又例如,公告号为cn103145166b的中国发明专利公开了一种用于白云石碳化工艺中的钙镁分离方法,向消化乳液中通入二氧化碳至ph为12.5-9.5,得到初步碳化体系;向初步碳化体系中加入乙酰丙酮,混合得到混合体系;向混合体系中通入二氧化碳至ph为9.5-7.5,以产生碳酸钙固体,分离固体,液相为精制重镁水,实现了高效的钙镁分离。但是本专利技术方案中增加了乙酰丙酮的使用,不仅增加了成本,而且乙酰丙酮为有毒物质。
6.白云石碳化法的核心问题来自于钙镁分离不彻底,如果不进行后续提纯,很难得到高纯度的钙镁分离产物。首先,传统的白云石碳化法的白云石煅烧多采用直接煅烧,由于焦炭和燃气的使用通常会引入硫和其他金属离子,对后续钙镁产品的品质产生较大影响,同时会造成烟气中二氧化碳回收的成本和难度。其次,在碳化过程中,重镁水中仍然是存在一定溶解度的钙,在重镁水的热解过程中,钙和二氧化碳存在仍然会有少量的碳酸钙沉淀与碳酸镁沉淀共存。
7.因此,如何提高白云石资源化中钙镁的彻底分离和降低白云石资源化过程中的能耗是目前亟需解决的技术问题。鉴于此,有必要提供一种白云石资源化深度利用成套处理系统和方法,以解决或至少缓解上述钙镁分离不彻底、烟气中二氧化碳纯度低、以及资源浪费与能耗高的技术缺陷。
技术实现要素:
8.本发明的主要目的是提供一种白云石资源化深度利用成套处理系统和方法,旨在解决现有技术中工艺过长、能耗高、资源利用度低、钙镁分离不完全的技术问题。
9.为实现上述目的,本发明提供一种白云石资源化深度利用成套处理系统,包括一次煅烧装置、二氧化碳捕集装置、消化装置、碳化分离装置、热解装置以及二次煅烧装置:其中,所述一次煅烧装置包括对白云石进行间接处理的白云石煅烧炉、多块围板以及排气管,所述围板与白云石煅烧炉的顶部以及落料仓的外壁的之间围绕形成排气腔室,所述白云石煅烧炉的进料口、所述落料仓的落料口以及所述白云石煅烧炉的排气口均与所述排气腔室连通,所述排气腔室通过所述排气管与所述二氧化碳捕集装置的进气口连通;所述二氧化碳捕集装置包括第一出气口、第二出气口、回收系统、第一回收管道以及第二回收管道,所述第二出气口连通所述回收系统;所述碳化分离装置包括碳化反应罐,所述碳化反应罐的进气口与所述二氧化碳捕集装置通过第一出气口连通;所述热解装置包括热解釜以及真空泵,所述真空泵与所述热解釜连通,所述第一回收管道连通所述热解釜的出气口和所述二氧化碳捕集装置的进气口;其中,所述热解装置热解反应后的分解母液通过分解母液回流管道回流至所述消化装置的进液口;所述二次煅烧装置包括二次煅烧炉,所述二次煅烧炉的烟气出口通过所述第二回收管道连通所述二氧化碳捕集装置的进气口。
10.进一步地,所述白云石煅烧炉包括自上至下依次设置的落料仓、炉体、及出料仓;其中,所述炉体的外壁上覆设有保温层,所述落料仓设置于炉体的进料口的上方,所述落料仓的落料口通过所述进料口对应设置,所述落料口的尺寸小于所述进料口的尺寸,所述进料口同时作为所述炉体的排气口;所述落料仓的外壁与所述炉体的外壁之间通过所述围板围绕形成所述排气腔室,所述排气腔室通过所述进料口与所述炉体内部连通。
11.进一步地,所述出料仓的外壁上设有循环水冷组件;所述循环水冷组件的热水出口与所述热解釜的水浴热水进水口通过循环水回流管道连通连通,升温后的循环水用于向所述热解釜进行供热。
12.进一步地,所述碳化反应装置包括所述碳化反应罐、气液混合反应器以及循环泵;所述碳化反应罐的顶部开设有加料口和气路循环出口;所述碳化反应罐的底部开设有水路循环出口和排流口,所述排流口处安装有排流阀;所述气液混合反应器包括所述气液混合管、进料管以及喷气管;其中,所述气液混合管安装于所述碳化反应罐的内部,所述气液混合管的侧壁上部开设有喷气管安装口,所述气液混合管的下端与所述碳化反应罐的内部连通设置;所述进料管自上至下依次穿过所述碳化反应罐的顶部和所述密封件后伸入所述气液混合管的内部,且所述进料管的出料口位于所述喷气管安装口的下方;所述喷气管的进气口同时与所述第一出气口和所述气路循环出口连通,所述喷气管的排气口安装于所述喷气管安装口;所述循环泵的进液口与所述水路循环出口连通,所述循环泵的出液口与所述进料
管的进料口连通。
13.进一步地,所述气液混合反应器还包括连通所述气液混合管的出口和所述碳化反应罐的对流混合喷射管,所述对流混合喷射管设置于所述气液混合管的下方,且所述对流混合喷射管自上至下依次设有正向流混合器和反向流混合器。
14.进一步地,所述热解釜中设有防止物料沉积结壁的螺带式搅拌器。
15.进一步地,所述二氧化碳捕集装置还包括压缩缓存气罐组件和二氧化碳循环子系统;所述所述压缩缓存气罐组件的进气口通过所述排气管与所述排气腔室连通,所述压缩缓存气罐组件包括所述第一出气口和所述第二出气口;所述二氧化碳循环子系统包括所述输气管道、所述第一回收管道、所述第二回收管道、二氧化碳水汽回收管以及气液分离器;其中,所述二氧化碳水汽回收管连通所述热解釜的烟气出口和所述气液分离器的进气口,所述气液分离器的出气口连通所述二氧化碳捕集装置的进气口。
16.本发明还提供一种采用如上述任一项所述的白云石资源化深度利用成套处理系统进行白云石资源利用的方法。
17.进一步地,还包括步骤:在所述一次煅烧装置的白云石加热至600-700℃时,开启所述二氧化碳捕集装置进行二氧化碳的回收与循环利用。
18.进一步地,还包括以下步骤中的一项或者多项:向所述消化装置中添加抑制剂,所述抑制剂包括乙二胺四乙酸、六偏磷酸钠、聚丙烯酸、聚顺丁烯二酸、氨三乙酸中的一种或多种;向所述含钙重镁水溶液中添加分散剂,所述分散剂包括甲醇、酒精、甘油、聚丙烯酰胺、纤维素衍生物、水玻璃中的一种或多种;所述消化装置中的所述煅白与所述水或所述分解母液的固液比为1kg:10~30l;所述消化装置中的首批所述煅白采用50~80℃的水进行消化,其余批次的所述煅白采用未冷却的所述分解母液进行消化;维持所述热解釜内的负压状态,以使所述热解釜内的含钙重镁水溶液的沸点位于碳酸氢镁的热解温度与碳酸氢钙的热解温度之间。
19.与现有技术相比,本发明具有以下优点:1、本发明能使钙镁分离更加彻底,获得高纯的轻质碳酸和轻质氧化镁,生产产品之一轻质碳酸钙含镁率可控制在小于1%,满足《hg/t2226-2010》标准;生产产品之二高纯轻质氧化镁纯度可达98%以上,满足《hg/t2573-2012》标准。通过对白云石进行间接煅烧,避免了因煤气、天然气或助燃气体与白云石的直接接触,从源头上杜绝了外部杂质的引入;通过将所述一次煅烧装置1中白云石煅烧炉产生的高纯二氧化碳用于所述碳化工段中,不仅实现了资源的循环利用,还保证了碳化工段中所用二氧化碳气体的纯度,避免了所述碳化工段中杂质的引入。
20.2、碳化反应罐通过以高速流动的消化乳液带动二氧化碳气体的流入,并将二氧化碳气体切割成微气泡,可以提高二氧化碳气体与消化乳液的混合度,促进碳化反应的进行;通过将二氧化碳气体与消化乳液的气液混合物进行对流混合,可以促进二氧化碳和消化乳液的进一步结合;通过在所述碳化反应工段的碳化反应中引入所述抑制剂,可以抑制生成
的碳酸钙转换为碳酸氢钙,避免了钙的溶出。
21.3、通过在所述热解工段进行负压调节,可以确保热解釜中的沸点温度处于碳酸氢钙和碳酸氢镁的热解温度之间,避免了碳酸氢钙的热解,保证了碳酸镁的纯度;通过在所述热解工段引入所述分散剂,可以促进碳酸镁的形成。
22.4、通过控制白云石在煅烧过程中不与外部直接接触,并设置独立的排气系统,保证了烟气中的气体仅来源于白云石的分解;本发明能提升烟气中二氧化碳的纯度,使得烟气中二氧化碳的纯度约为85%。
23.5、通过控制气体回收的时间节点,白云石加热至650-750℃时开启气体回收,使二氧化碳捕集装置6的开启时间与碳酸镁的初始分解时间保持一致,不仅可以降低能源消耗,还能为白云石的预热干燥提供缓冲时间,避免了烟气中混入大量水汽;并且,后续煅烧区内的热量会有部分经物料堆积和气体流动而传输至待煅烧的白云石,因此,后续白云石在煅烧过程中产生的水汽较少,不会使烟气在后续煅烧过程中混入大量水汽。
24.6、本发明能提高资源利用度并降低能耗。在煅烧过程中,热量主要集中在炉膛的煅烧区内,少量逸散的热量只能向上通过物料堆积和气体流动传递给待煅烧的白云石,或向下传递给循环冷却组件中的冷却水,加热后的冷却水可以用作所述热解工段中的热源;此外,通过将所述热解工段中产生的分解母液用于消化工段的消化,不仅可以实现抑制剂的循环使用,还可以实现对热量的再利用,即热量自白云石的煅烧区传递给冷却水,然后自加热后的冷却水传递至热解工段,最后还可自热解工段的分解母液传递至消化工段。
附图说明
25.为了更清楚地说明本发明实施方式或现有技术中的技术方案,下面将对实施方式或现有技术描述中所需要使用的附图作简单地介绍,显而易见地,下面描述中的附图仅仅是本发明的一些实施方式,对于本领域普通技术人员来讲,在不付出创造性劳动的前提下,还可以根据这些附图示出的结构获得其他的附图。
26.图1为本发明一个实施例中成套处理系统的模块示意图;图2为本发明一个实施例中白云石煅烧炉的立面示意图;图3为本发明一个实施例中排气腔室的结构示意图;图4为本发明一个实施例中碳化反应装置的结构示意图;图5为本发明一个实施例中气液混合反应器的结构示意图。
27.附图标号说明:一次煅烧装置1;消化装置2;碳化分离装置3;热解装置4;二次煅烧装置5;二氧化碳捕集装置6;第一出气口7;第二出气口8;回收系统9;第一回收管道10;第二回收管道11;循环水回流管道12;分解母液回流管道13;胶带运输机101;移动卸料车102;落料仓103;落料斗104;挡板105;物位控制器106;排气管107;排气腔室108;围板109;顶板110;入料口111;煅烧区112;加热棒113;加热板114;保温层115;震动器116;出料仓117;循环水冷组件118;板式输送机119;碳化反应罐201;加料口202;气路循环出口203;水路循环出口204;排流口205;温度显示接口206;压力显示接口207;液位显示接口208;检修口209;气液混合反应器210;进料管211;喷气管212;减压阀213;气路循环单向阀214;气液混合管215;对流混合喷射管
216;正向流混合器217;反向流混合器218;循环泵219;循环泵进口阀220;循环泵出口阀221。
28.本发明目的的实现、功能特点及优点将结合实施方式,参照附图做进一步说明。
具体实施方式
29.下面将结合本发明实施方式中的附图,对本发明实施方式中的技术方案进行清楚、完整地描述,显然,所描述的实施方式仅仅是本发明的一部分实施方式,而不是全部的实施方式。基于本发明中的实施方式,本领域普通技术人员在没有作出创造性劳动前提下所获得的所有其他实施方式,都属于本发明保护的范围。
30.需要说明,本发明实施方式中所有方向性指示(诸如上、下
……
)仅用于解释在某一特定姿态(如附图所示)下各部件之间的相对位置关系、运动情况等,如果该特定姿态发生改变时,则该方向性指示也相应地随之改变。
31.另外,在本发明中如涉及“第一”、“第二”等的描述仅用于描述目的,而不能理解为指示或暗示其相对重要性或者隐含指明所指示的技术特征的数量。由此,限定有“第一”、“第二”的特征可以明示或者隐含地包括至少一个该特征。
32.并且,本发明各个实施方式之间的技术方案可以相互结合,但是必须是以本领域普通技术人员能够实现为基础,当技术方案的结合出现相互矛盾或无法实现时应当认为这种技术方案的结合不存在,也不在本发明要求的保护范围之内。
33.如图1-5所示,本发明提供了一种白云石资源化深度利用成套处理系统,括一次煅烧装置1、二氧化碳捕集装置6、消化装置2、碳化分离装置3、热解装置4以及二次煅烧装置5。
34.具体的,所述一次煅烧装置1包括对白云石进行间接煅烧处理的白云石煅烧炉、多块围板109以及排气管107。所述围板109与白云石煅烧炉的顶部以及落料仓103的外壁的之间围绕形成排气腔室108,所述白云石煅烧炉的进料口、落料仓的落料口以及所述白云石煅烧炉的排气口均与所述排气腔室108连通;所述排气腔室108通过所述排气管107与所述二氧化碳捕集装置6的进气口连通。进一步地,所述白云石煅烧炉的进料口和所述白云石煅烧炉的排气口可以为同一个开口,统称为入料口111。
35.其中,申请人需要说明的是,本技术中的“间接处理”、“间接加热处理”和“间接煅烧处理”均指的是区别于现有的对白云石的直接煅烧,例如对白云石通过非添加焦炭、煤粉的点火直接烧结煅烧加热的方式,或者通过通入燃气等直接在明火中直接煅烧的方式;本技术中的“间接处理”、“间接加热处理”和“间接煅烧处理”指的是通过对炉膛内的物料或者炉壁采用电加热、又或者对炉壁进行加热,使热量传导至物流从而对物料进行煅烧的方式。在一可选地实施例中,通过对白云石进行间接煅烧处理的白云石煅烧炉可以以电力或燃气作为煅烧的能源对所述白云石进行间接煅烧,得煅白与二氧化碳气体;并通过所述白云石煅烧炉中白云石的堆积和二氧化碳气体的流动对未煅烧的白云石进行预热和干燥处理。
36.以下以一具体示例来说明一次煅烧装置1,所述对白云石进行间接煅烧处理的白云石煅烧炉为竖炉或者竖窑。所述白云石煅烧炉包括自上至下依次设置的落料仓103、炉体、及出料仓117。
37.其中,所述炉体可以包括炉膛,所述炉膛的顶部设置有用于封闭所述炉膛的炉口的且具有至少一个所述入料口111的顶板110。
38.在一具体示例中,所述炉膛的外壁上覆设有保温层115,所述炉膛的内部形成有至少一个由加热板114围绕而成的煅烧区112,所述顶板110上固定有至少一个伸入所述煅烧区112内的加热棒113;一般情况下,每个所述煅烧区112内均均匀布置有多个所述加热棒113,以对所述煅烧区112内的白云石进行均匀煅烧。
39.需指出的是,相邻所述加热棒113之间及所述加热棒113与所述加热板114间之间的距离可以根据实际情况确定,作为一种较优的选择,具体可以设置在100~500mm之间。
40.所述落料仓103设置于所述顶板110的上方,所述落料仓103的至少一个落料口通过所述入料口111与所述煅烧区112连通,所述落料口的尺寸小于所述入料口111的尺寸。
41.所述围板109与所述落料仓103的外壁以及所述顶板110之间围绕形成有密闭的所述排气腔室108,所述排气腔室108通过所述入料口111与所述煅烧区112连通。其中,所述落料口可以与所述入料口111平齐,也可略微伸入所述煅烧区112内,以避免所述入料口111被白云石完全堵塞。
42.所述出料仓117设置于所述炉膛的下方,以使所述煅烧区112内的白云石物料穿过所述出料仓117后出料至所述传送机构上。
43.所述排气管107同时与所述排气腔室108和二氧化碳捕集装置6连通设置,以将所述煅烧区112内产生的气体依次通过所述入料口111、所述排气腔室108及所述排气管107排放至二氧化碳捕集装置6中。
44.在本技术中,由于所述排气腔室108四周的围板109围绕所述落料仓103的外壁,在回收气体的过程中,会将部分热量传输至所述落料仓103中,从而对白云石进行预热和干燥,这样后续白云石煅烧分解过程中,二氧化碳中的水汽含量会很低;再者,特别新颖的是,由于所述落料仓103中的白云石与所述煅烧区112内的白云石为堆积关系,所述落料仓103内的堆积物料将外界与所述白云石煅烧炉的内部分隔,此外,还会有部分热量随白云石的堆积传输至所述落料仓103中,进一步对落料仓103中的物料进行预热。
45.在具体实施方式中,所述围板109可以通过焊接、法兰连接的方式与所述落料仓103的外壁以及所述顶板110固定连接,以对所述落料仓103的外壁与所述顶板110之间的间隙进行封闭。所述围板1099还可以与落料仓1033一体的设置,通过调整落料仓103的高度,使围板109的底部抵持在炉体的顶部即可。
46.具体的,当所述白云石中的碳酸镁(一般为白云石被加热到700度左右时)开始分解时,再开启所述二氧化碳捕集装置6中的引风机,以将所述煅烧区112内产生的气体输送至所述二氧化碳捕集装置6中。如:由于白云石中含有水分,当碳酸镁开始分解时,物料温度在700℃左右,此时白云石中的水分基本被蒸发,因此,回收的二氧化碳中所含水分会较少,后续由于所述落料仓103中会存在预热,因此后续所产生的二氧化碳所含水分也较少。
47.所述排气管107与所述排气腔室108的连通处还可以设置阀门,以避免前期产生的水分进入所述排气管107中,所述阀门可以与位于外部的控制器通信连接。
48.进一步地,为了准确地控制所述落料仓103的仓位,所述落料仓103上或进料机构上可以安装有物位控制器106,所述物位控制器106可以为声波物位控制器106或音叉物位控制器106,所述进料机构可以为带移动卸料车102的胶带运输机101;所述物位控制器106监测所述落料仓103的仓位并控制所述运输机上的所述移动卸料车102向所述落料仓103内投料,以实现所述落料仓103与所述胶带运输机101的联锁控制。
49.其中,所述落料仓103可以包括多个开设有所述落料口的落料斗104,所述落料斗104呈漏斗状,具体地,所述落料仓103可以全部由多个所述落料斗104组成,也可以使所述落料仓103的下部由多个所述落料斗104组成,所述落料仓103的上部由挡板105围绕而成。且,每个所述落料斗104均开设一个所述落料口,相邻两个所述落料斗104的侧壁顶端之间、及所述落料斗104与所述围板109之间均需密封连接,以确保所述排气腔室108的密封性。为了精准投料,所述物位控制器106还可以安装在所述落料斗104或所述挡板105上,以实现对每个所述落料斗104中仓位的控制,当然,将所述物位控制器106设于所述移动卸料车102上也可实现此目的。
50.此外,为了使所述炉体的进料出料更加顺畅,所述出料仓117的外壁上设有震动器116,以使白云石物料的排出地更加均匀和稳定。为了便于对所述煅烧区112内生产的高温煅白进行降温,从而保证向外输料所述传送机构不因过高温而烧损,所述出料仓117的外壁上设有循环水冷组件118,以用于对煅烧后生成的煅白进行降温,所述传送机构可以为板式输送机119。进一步地,所述循环水冷组件118可以设置于所述出料仓117的中下部,且所述循环水冷组件118可以为水冷夹壁,所述水冷夹壁与所述出料仓117的外壁之间可以围绕形成水冷室,以供冷却水的进入及升温后排出。所述循环水冷组件的热水出口与所述热解釜的水浴热水进水口通过循环水回流管道12连通连通,所述水冷室中的升温后的热水用于向所述热解釜供热。
51.应明确的是,一次煅烧装置1主要对白云石煅烧及气体回收,采用所述白云石煅烧炉替代传统炉窑,该炉煅烧白云石无需添加粉煤、焦炭或重油等燃辅料,采用清洁电能或燃气间接处理,在前端即解决了粉煤灰、焦油等物质对轻烧白云石的污染,因此该炉生产的轻烧白云石纯度高、活性好、无污染,可有效降低后续工段除杂成本及提高生产效率;该炉还具有煅烧过程中无需鼓入大量助燃风的特点,因此煅烧分解的co2气体纯度高且不含so2、co、h2s等,炉气成分约为85%co2、11.85%n2及3.15%o2,可直接除尘后通过二次压缩进入中间气包缓存后供碳化工段使用,无废气及二氧化碳排放。
52.而且,所述白云石煅烧炉可采用电间接加热也可采用燃气燃烧器提供热风间接加热,生产时白云石矿破碎至5~10cm投入内炉膛中,当采用电间接加热时,所述加热棒113和所述加热板114以电力作为能量来源对所述煅烧区112进行升温加热;当采用燃气加热时,热源在所述炉膛的外壁加热,由于所述落料仓、所述隔板和所述顶板的结构设计、以及所述排气腔室的设置,在堆积白云石的情况下,可以避免所述煅烧区内的物料与热源和助燃风的接触,保证了物料的洁净度,在此基础上,还确保了白云石进料、密闭排气和热交换等功能的实现。所述煅烧区112内的热量通过白云石的堆积和气体的流动向所述落料仓103中的白云石传递,从而对白云石进行预热和干燥,此外,当采用燃气加热时外壁时,间接加热的内炉膛外侧加热空气上升后也可用于物料的预热,不需担心其对煅白产品和二氧化碳造成影响。
53.还需了解的是,所述白云石煅烧炉不仅在保证气体密闭回收的前提下,实现了气料之间及料料之间的热交换,还具有更进一步的节能效果。如:因所述炉膛的外壁设有所述保温层115,因此,所述炉膛内部的热量只能向上或向下传递,且由于所述炉膛的上方存在气料之间及料料之间的热交换,因此,向上传递的热量会被所述落料仓103中的白云石充分利用,此外,由于所述出料仓117的外壁上设有所述循环水冷组件118,少部分向下传递的热
量会被所述循环水冷组件118中的冷却水吸收,所述冷却水在升温后可以用于白云石的其他工序,以将提高热量的利用率。
54.二氧化碳捕集装置6包括压缩缓存气罐组件、二氧化碳循环子系统以及回收系统9,所述压缩缓存气罐组件的进气口通过所述排气管与所述排气腔室连通,所述压缩缓存气罐组件包括第一出气口7和第二出气口8,所述第二出气口8连通所述回收系统9,所述二氧化碳循环子系统包括输气管道、第一回收管道10以及第二回收管道11。
55.其中,压缩缓存气罐组件通过所述第一出气口7可以将部分二氧化碳排至碳化分离装置3,以完成碳化反应。所述第二出气口8可以将另一部分多余的二氧化碳排至所述回收系统9中储存;由于白云石加工过程中一直存在二氧化碳的分解,且二氧化碳可以循环利用,因此,多余的二氧化碳可以存储至所述回收系统9中。
56.所述消化装置2可以通过回转消化机添加水溶液对所述煅白进行消化,得消化乳液;通过回转冷却机对所述消化乳液进行冷却处理,得冷却后的消化乳液。
57.其中,所述消化工段中的所述水溶液包括水或热解装置4反应后得到的分解母液,可以向经水消化后得到的所述消化乳液中加入抑制剂,以保证钙镁的分离。所述抑制剂包括乙二胺四乙酸、六偏磷酸钠、聚丙烯酸、聚顺丁烯二酸、氨三乙酸中的一种或多种,所述抑制剂的添加量可以为所述消化乳液质量分数的0.01~0.05%。此外,所述煅白与所述水或所述分解母液的固液比为1kg:10~30l;首批所述煅白采用50~80℃的水进行消化,其余批次的所述煅白采用未冷却的所述分解母液进行消化。
58.应明确的是,本发明在所述回转消化机中采用热解工段固液分离后的分解母液消化所述消化乳液,加之消化过程煅白释放的热量,可使连续生产时不必考虑消化用水的加热。另外,回转消化机后设置有高低阶梯布置的回转冷却机,消化乳液溢流至回转冷却机完成冷却,冷却至30℃左右经泵进入所述碳化工段的碳化反应器;消化滤渣洗砂后满足《gb/t14684-2011》建筑用砂标准,可做建材外售,无废渣产生或外排,洗水全部返回消化机循环使用,无废水排放。采用所述回转消化机及回转冷却机替代传统搅拌式消化槽、冷却槽可良好的避免消化浆液沉钙严重,堵塞设备及管道等影响正常生产的问题。
59.所述碳化分离装置3包括碳化反应罐201,所述碳化反应罐201的进气口与所述压缩缓存气罐组件的所述第一出气口7连通。
60.具体的,以下举例来说明本发明一实施例中的所述碳化分离装置3。为了确保消化乳液与二氧化碳气体的充分反应,所述碳化反应装置可以为水环式碳化反应器,具体地,包括:所述碳化反应罐201、气液混合反应器210以及循环泵219;当然,还可以包括多条用于输送消化乳液或二氧化碳的且起连通作用的管路。
61.所述碳化反应罐201的顶部开设有加料口202和气路循环出口203;所述碳化反应罐201的底部开设有水路循环出口204和排流口205,所述排流口205处安装有排流阀;此外,所述碳化反应罐201上还可以开设温度显示接口206、压力显示接口207、液位显示接口208、以及检修口209,以便于工作人员对碳化反应进行监测和对所述碳化反应罐201进行维护。
62.所述气液混合反应器210包括所述气液混合管215、进料管211以及喷气管212;其中,所述气液混合管215安装于所述碳化反应罐201的内部,具体可以安装在所述碳化反应罐201的上部,从而在所述碳化反应罐201中预留出充分的容置空间,以便于碳化反应的充分进行。所述气液混合管215的顶部设有密封件,所述气液混合管215的侧壁上部开设有喷
气管212安装口,所述气液混合管215的下端与所述碳化反应罐201的内部连通设置。
63.为了使消化乳液与二氧化碳成分混合,所述进料管211自上至下依次穿过所述碳化反应罐201的顶部和所述密封件后伸入所述气液混合管215的内部,且所述进料管211的出料口位于所述喷气管212安装口的下方。所述喷气管212的进气口同时与供气装置(即所述第一出气口7)和所述气路循环出口203连通,所述喷气管212的排气口安装于所述喷气管212安装口的位置处,并与所述气液混合管215连通设置;以使二氧化碳在高速流动的消化乳液的带动下进入所述气液混合管215中,并被所述消化乳液切割成微气泡。
64.为了进一步地对消化乳液和二氧化碳的气液混合物进行对流混合,所述气液混合反应器210还包括分别与所述气液混合管215的下端和所述碳化反应罐201连通设置的所述对流混合喷射管216,所述对流混合喷射管216设置于所述气液混合管215的下方,且所述对流混合喷射管216自上至下依次设有正向流混合器217和反向流混合器218。
65.所述对流混合喷射管216和所述气液混合管215可以一体设置,也可以固定连接,所述气液混合管215中得到的气液混合物自所述气液混合管215的下端开口进入所述对流混合管中,并经由所述正向流混合器217和所述反向流混合器218的对流混合后喷射至所述碳化反应罐201中。
66.作为对所述正向流混合器217和所述反向流混合器218的说明:所述正向流混合器217主要用于使下流的气液混合物产生正向旋转,所述反向流混合器218主要用于使下流的气液混合物产生反向旋转,所述正向旋转和所述反向旋转为相对的概念,两者之间只需的旋转方向相反即可,一般情况下,所述正向旋转可以理解为顺时针旋转,所述反向旋转可以理解为逆时针旋转。
67.具体地,所述正向流混合器217包括第一管体和凸设于所述第一管体的管腔内壁的第一螺旋凸起,所述反向流混合器218包括第二管体和凸设于所述第二管体的管腔内壁的第二螺旋凸起,所述第一螺旋凸起和所述第二螺旋凸起的螺旋方向相反。所述第一管体和所述第二管体可以一体设置,也可以通过固定件固定连接。作为一种选择,所述第一螺旋凸起的螺旋方向可以为顺时针方向,所述第二螺旋凸起的螺旋方向可以为逆时针方向,且所述第一螺旋凸起和所述第二螺旋凸起均可以为双螺旋结构,当然,也可以为单螺旋结构。此外,需明确的是,所述正向流混合器217和所述反向流混合器218可以使气液形成高速对流,以使混合反应更充分,反应更高效。
68.作为对所述气液混合反应器210的结构设计,为了使所述消化乳液、以所述消化乳液与二氧化碳混合后的气液混合物具有更高的喷射速度,所述进料管211下部的管腔内径逐渐减小,所述对气液混合管215下部管腔的内径也可以逐渐减小设置,在此基础上,所述进料管211的出料口可以延伸至所述对气液混合管215的下部,且所述进料管211与所述气液混合管215的内壁之间需保持有间隙,以供二氧化碳气体的流动。
69.为了便于对所述气液混合管215中供气,及对未反应的二氧化碳进行循环利用,所述喷气管212的进气口与所述供气装置之间设有减压阀213,以对所述供气装置提供的二氧化碳进行气压调节,所述喷气管212的进气口与所述气路循环出口203之间设有气路循环单向阀214,以防止所述供气装置提供的二氧化碳在进气过程中产生分流。此外,为了使所述喷气管212能同时接收所述供气装置提供的二氧化碳和循环中的二氧化碳,所述减压阀213及其对应的管路可以和所述气路循环单向阀214及其对应的管路并联设置。
70.需了解的是,所述碳化反应罐201的正常工作气压约20~40kpa,当所述碳化反应罐201搭配水力循环泵219连续运行时,所述碳化反应罐201内的消化乳液会不断吸收co2,使反应器内压力降低,因此配备恒压阀可以使得连续作业时一直保持co2的供给及所需压力。在此基础上,所述减压阀213可以与恒压阀搭配使用,所述恒压阀可以设置于所述进料管211上,也可以设置于所述进料管211与所述减压阀213的连通管路上。
71.为了保证消化乳液的高速流动,所述循环泵219的进液口与所述水路循环出口204连通,所述循环泵219的出液口与所述进料管211的进料口连通,以将所述碳化反应罐201中的消化乳液高速地泵如所述进料管211中,从而使得进入所述所述进料管211中的消化乳液以较高的流速自上至下地进入所述气液混合管215内,并将二氧化碳气体进行切割。其中,所述循环泵219与所述水路循环出口204之间设有循环泵进口阀220,所述循环泵219与所述进料管211的进料口之间设有循环泵出口阀221。以对循环中的液体进行控制。
72.应明确的是,上述的所述碳化反应装置采用了所述气液混合反应器210,所述碳化反应装置在完全密闭且加压的情况下通过所述循环泵219进行液体的循环,气液两相在循环过程中不仅使二氧化碳被消化乳液分隔成微气泡,还会产生螺旋对流。此外,所述碳化反应装置中产生的循环气路还可使一次未充分吸收的co2气体通过循环泵219产生的负压二次进入气液混合反应器210中再次气液混合碳化,直至完全吸收。本发明中的所述碳化反应装置不仅效率高,且不会造成co2反应气体的外泄和浪费。夏日高温生产期,碳化过程因环境及机械热的影响较难控制碳化温度低于35℃,会有少量碳酸轻钙分解溶入重镁水(碳酸氢镁溶液)中,进而影响产品纯度,因此,高温生产期在消化乳液中添加0.01~0.05%质量分数的抑制剂,可有效控制碳化过程碳酸氢钙的溶解。
73.所述热解装置4包热解釜以及真空泵,所述真空泵与所述热解釜连通,维持所述热解釜内的负压状态,以使所述热解釜内的含钙重镁水溶液的沸点位于碳酸氢镁的热解温度与碳酸氢钙的热解温度之间;其中,所述热解装置4热解反应后的分解母液通过分解母液回流管道13回流至所述消化装置2的进液口。所述第一回收管道10连通所述热解釜的出气口和所述二氧化碳捕集装置6的进气口。
74.具体的,热解装置4是通过真空泵抽取热解釜中的气体,控制所述碳酸氢镁的沸点处于碳酸氢镁的热解温度与碳酸氢钙的热解温度之间,使所述碳酸氢镁溶液在负压状态的所述热解釜中进行热解,得分解母液、碳酸镁沉淀和二氧化碳气体。
75.需说明的是,在所述热解工段中,通过真空泵使所述真空热解釜的内部形成负压,可以降低所述热解处理所需的温度,并其还能抽取所述螺带真空热解釜中产生的二氧化碳。由于碳酸氢钙和碳酸氢镁的热解温度均低于100℃,且碳酸氢钙的热解温度高于碳酸氢镁,通过使所述真空热解釜内部抽负压至接近真空,可以控制溶液的沸点位于碳酸氢镁的热解温度与碳酸氢钙的热解温度之间,以此避免钙镁同时沉淀而造成的掺杂。
76.具体地,所述热解工段中的热解釜作业时会产生带有一定水汽的高浓co2气体,该气通过所述反应釜配备的负压水环式真空泵抽出,负压压力控制一般小于0.02mpa。含有一定水汽的高浓co2气体中所含的水分会在所述水环式真空泵水箱中富集,其中的富co2气体会经气液分离器分离后进入所述二氧化碳捕集装置6,以用于所述碳化工段的碳化反应或二氧化碳的收集。
77.为了提升碳酸氢镁的分解速度,在采用所述热解釜对所述碳酸氢镁溶液进行热解
之前,向所述碳酸氢镁溶液中加入分散剂,以促进热解过程中碳酸镁的形成;其中,所述分散剂包括甲醇、酒精、甘油、聚丙烯酰胺、纤维素衍生物、水玻璃中的一种或多种。所述分散剂的添加量可以为所述碳酸氢镁溶液0.1%~2%的体积百分比。
78.此外,所述热解釜可以为螺带热解釜,所述螺带热解釜中可以设有防止物料沉积结壁的螺带式搅拌器,以避免物料沉积结壁而降低对所述热解釜供热效果。
79.应明确的是,上述实施例采用带所述螺带式搅拌器的所述真空热解釜进行热解,该反应釜外壁设置有加热夹套,夹套内加热热源来至一次煅烧工段中所述循环水冷组件118中的循环冷却水;所述热解釜内设置的所述螺带式搅拌器,用以防止釜内物料沉积结壁造成热传导率降低而能耗增高,并可加速重镁水的分解反应。该反应釜还配备水环式真空泵,作业过程中由所述水环式真空泵提供负压使其内部形成真空,以降低所述反应釜内重镁水的分解温度,并结合分散剂的添加使碳酸氢镁的分解速度大幅加速的同时,使得碳酸镁结晶更细且形状规律,纯度更高。热解产生的大量高浓co2气体所含水分在所述水环式真空泵水箱中富集,分离富co2气经气液分离器进入所述煅烧工段二氧化碳捕集装置6,然后一同进行再利用。
80.本发明中的白云石资源化深度利用成套处理系统,进一步的,还可以包括压滤与干燥工段装置:分别对所述碳酸钙沉淀和所述碳酸镁沉淀依次进行过滤、洗涤、和干燥,得轻质碳酸钙和轻质碳酸镁。
81.具体地,在所述压滤与干燥工段装置,可以采用集过滤、滤饼洗涤、挤压、风干、自动卸料、自动清洗滤布等功能于一体的全自动立式压滤机/带式压滤机替代传统板框压滤机,碳化工段所产轻质碳酸钙与热解工段所产轻质碳酸镁分区分机压滤,二者压滤后滤饼分别送至分区分机的快速旋转闪蒸干燥机,所述快速旋转闪蒸干燥机自带打散功能,加料连续稳定不架桥,气密性好,可将轻质碳酸钙的终水份干燥至小于0.1%,并使轻质碳酸镁干燥至的终水含量小于20%。所得轻质碳酸钙即可包装待售,轻质碳酸镁进入二次煅烧工段制备轻质氧化镁。
82.上述实施例中采用的全自动立式压滤机具有自动清洗滤带及滤饼的功能,使压滤更彻底的同时通过清洗滤饼提升产品回收率。压滤物料轻质碳酸镁及轻质碳酸钙均为结晶物质,吸水率较大,传统板框压滤机最大0.18mpa难以滤出太多水分,影响后续干燥生产。所述立式压滤机具备自动保压功能,最大滤压可达到1.6mpa,再通过其配置的自动风干系统,可实现对产品的进一步地干燥。
83.所述二次煅烧装置5对所述轻质碳酸镁进行间接煅烧,使所述轻质碳酸镁分解为轻质氧化镁和二氧化碳气体。所述二次煅烧装置5包括二次煅烧炉,所述二次煅烧炉的烟气出口通过所述第二回收管道11连通所述二氧化碳捕集装置6的进气口。
84.应明确的是,因所述轻质碳酸镁密度较小,质量较轻,无法用所述白云石煅烧炉进行煅烧,因此,所述二次煅烧工段可以采用间接加热式回转煅烧炉进行煅烧,即采用间接煅烧回转炉,该回转炉采用密闭螺旋进料,煅烧物料轻质碳酸镁置于内炉膛,然后通过燃气火焰加热内炉膛的外壁,在此过程中,燃气与燃气热风均不与物料接触,保证了煅烧物料的洁净度。
85.在二次煅烧过程中,轻质碳酸镁分解为高纯轻质氧化镁及co2,co2分解至一定量时从进料端顶部排气通道自然溢出进入沉降室,沉降室沉降的少量物料粉尘为未充分分解的
轻质碳酸镁及轻质氧化镁,该物料粉尘经星型卸料阀排出收集后可以返回所述回转煅烧炉的进料装置。沉降室后方设置有过滤气体中粉尘的布袋收尘器,以使co2气体在被过滤微量粉尘后,可以并入煅烧工段中的二氧化碳捕集装置6中,从而实现二氧化碳的循环利用,确保无二氧化碳与废气的排放。此外,所述间接加热式回转炉排料采用带冷却功能的密闭螺旋输送机排出,排出落料口处设置微负压抽滤,可以经旋风及布袋回收部分轻质氧化镁扬尘。
86.针对本发明,还应明确的是,所述碳化工段中的所述二氧化碳气体包括所述一次煅烧工段中煅烧白云石得到的二氧化碳气体、所述热解工段中热解所述碳酸氢镁溶液得到二氧化碳气体、以及所述二次煅烧工段中煅烧所述轻质碳酸镁得到的二氧化碳气体,以保证二氧化碳的充分利用,且避免废弃的排放。此外,所述碳化工段加压碳化之压力来至所述二氧化碳捕集装置6的co2炉气压缩气包,所述co2炉气压缩气包内贮存co2炉气压力为0.8mpa,所述一次煅烧工段、所述热解工段、及所述二次煅烧工段中产生的co2均可先进入所述二氧化碳捕集装置6的co2炉气压缩气包后,再用于所述碳化工段的碳化反应。
87.在本发明中,本专利技术均采用全新或新式的成套装备,具有自动化程度高,一次性投资少,运行稳定、维护简单、无废气及二氧化碳排放等各项优点。生产产品之一轻质碳酸钙纯度可达98%以上,含镁率可控制在小于1%,生产产品之二高纯轻质氧化镁纯度可达98%以上。
88.作为对上述实施方式的细化,上述实施方式具体还可以包括:白云石破碎至5~10cm后经进料机构进入所述白云石煅烧炉的所述煅烧区112,所述煅烧区112的热气上升后进入所述落料仓103中预热原料,以充分利用余热;所述煅烧区112内的白云石矿升温至700℃左右时开启所述二氧化碳捕集装置6,收集的co2炉气经净化后加压至0.8mpa进入所述co2炉气压缩气包中贮存。最终煅烧温度控制在物料温度1050℃以内,煅烧过程升温约30min,保温约1~2.5h,后续通过控制所述间接式煅烧竖炉底部的用于排料的板式输送机119的运输速度,控制炉内物料均停留约2.5小时左右。
89.煅烧后得到的煅白经所述板式输送机119连续输入所述回转消化机,所述回转消化机单程约15min即充分消化。消化后的消化乳液经溢流进入阶梯布置的所述回转冷却机,冷却约30~45min后至30℃左右经泵打入所述碳化反应罐201中;消化中得到的消化滤渣经提升机进入洗砂机洗砂后即可作为建筑砂外售,洗水全部返回回转消化机。
90.消化乳液进入所述碳化反应罐201中,同时所述co2炉气压缩气包(即中间气包)中的co2气体经减压阀213减压至40kpa左右后通过配置的恒压阀入口进入喷气管212中,在所述碳化反应装置配置的水力循环泵219的作业下,碳化反应时间约30min即可使乳液ph达至7.5~8.0之间。过程中根据实际生产环境及控制参数添加约0.01~0.05%的抑制剂。反应完全后排料进入全自动带式压滤机压滤,滤饼经输送机进入旋转闪蒸干燥机干燥后得到轻质碳酸钙包装待售;滤液为重镁水,经泵进入热解工段的所述热解釜;干燥水汽冷凝后可以返回所述回转消化机中使用。
91.重镁水进入所述热解釜之前,所述热解釜的内胆已被加热夹套内来自煅烧工段中所述循环冷却组件的循环水加热至一定温度。重镁水进入后开启所述热解釜中的低速螺带式搅拌机,同时开启配套的水环式真空泵抽负压至0.02mpa以下。此时重镁水开始分解成碳酸镁、co2及分解母液,co2夹有少量水汽经水环式真空泵进入气液分离器分离后返回至所述
二氧化碳捕集装置6;分解母液可用于消化工段中的消化。生产时根据实际情况添加0.1~0.2%的分散剂,使碳酸镁结晶速度更快,结晶更细且形状规则。热解釜连续作业约10~30min可使结晶基本完成,此时即将所得结晶排出进入压滤与干燥工段。
92.压滤与干燥工段设置两个区,碳酸钙及碳酸镁压滤及干燥均不使用同一台设备,碳酸钙已在前面完成压滤及干燥。碳酸镁经泵进入全自动立式压滤机压滤,滤饼经输送机进入旋转闪蒸干燥机,干燥后经密闭螺旋输送机进入二次煅烧工段;滤液及干燥水汽冷凝后全部返回消化工段。
93.在干燥后的碳酸镁进入回转煅烧炉之前,即将所述回转煅烧炉预热至一定温度,后续连续进料和排料始终保持一定温度,可防止碳酸镁结壁架桥等现象。碳酸镁煅烧时间约1~2h,温度700~750℃。升温至700℃时内炉膛开始大量分解co2并自然溢出进入沉降室沉降,沉降的微量粉尘返回进料系统,气体经过滤后返回二氧化碳捕集装置6。所述回转煅烧炉的内炉膛外壁处的加热空气可以输出至压滤与干燥工段中,以用于对碳酸钙和碳酸镁进行干燥,从而充分利用余热。所述回转煅烧炉内炉膛内的碳酸镁煅烧完成后即得到优质轻质氧化镁,经具备循环水冷功能的密闭螺旋输送机连续排出包装待售,其中的循环冷却水在受热后可以循环输至热解工段供热解使用,以实现全流程的余热充分利用。
94.作为对所述二氧化碳循环子系统的进一步说明:为了将白云石加工中所产生及消耗的二氧化碳构成循环回路,以实现资源的最大利用,所述二氧化碳循环子系统包括输气管道、二氧化碳水汽回收管、气液分离器、第一回收管道10以及第二回收管道11;其中,所述输气管道分别连通所述二氧化碳捕集装置6的出气口以及碳化反应罐的进气口,以将所述二氧化碳捕集装置6中部分的二氧化碳传输至所述碳化系统;所述二氧化碳水汽回收管分别连通所述热解釜的烟气出口和所述气液分离器的进气口,所述第一回收管道10连通所述气液分离器的出气口和所述二氧化碳捕集装置6的进气口,以将所述重镁水热解反应器中产生的二氧化碳气体回收后传输至所述二氧化碳捕集装置6回收;所述第二回收管道11分别连通所述二次煅烧装置5的烟气出口和所述二氧化碳捕集装置6的进气口,以将所述碳酸镁煅烧炉产生的二氧化碳在除尘后回收至所述二氧化碳捕集装置6中。
95.本发明还提供一种采用如上任一项所述的白云石资源化深度利用成套处理系统及其工艺进行白云石资源利用的方法。
96.所述白云石资源利用的方法还可以包括步骤:在所述一次煅烧装置1的白云石加热至600-700℃时,开启所述二氧化碳捕集装置6进行二氧化碳的回收与循环利用。
97.所述白云石资源利用的方法还可以包括以下步骤中的一项或者多项:向所述消化装置2中添加抑制剂,所述抑制剂包括乙二胺四乙酸、六偏磷酸钠、聚丙烯酸、聚顺丁烯二酸、氨三乙酸中的一种或多种;向所述含钙重镁水溶液中添加分散剂,所述分散剂包括甲醇、酒精、甘油、聚丙烯酰胺、纤维素衍生物、水玻璃中的一种或多种;所述消化装置2中的所述煅白与所述水或所述分解母液的固液比为1kg:10~30l;所述消化装置2中的首批所述煅白采用50~80℃的水进行消化,其余批次的所述煅白采用未冷却的所述分解母液进行消化。
98.本发明的上述技术方案中,以上仅为本发明的优选实施例,并非因此限制本发明的专利范围,凡是在本发明的技术构思下,利用本发明说明书及附图内容所作的等效结构
变换,或直接/间接运用在其他相关的技术领域均包括在本发明的专利保护范围本发明的上述技术方案中,以上仅为本发明的优选实施例,并非因此限制本发明的专利范围,凡是在本发明的技术构思下,利用本发明说明书及附图内容所作的等效结构变换,或直接/间接运用在其他相关的技术领域均包括在本发明的专利保护范围。