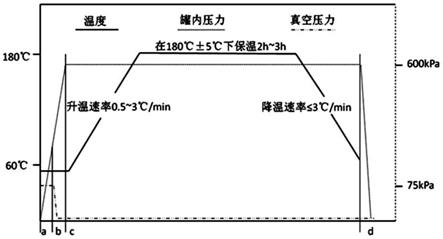
1.本发明涉及一种纳米合金热塑粒子、纳米合金膜及其制备方法和应用,属于环氧预浸料技术领域。
背景技术:
2.碳纤维基复合材料具有轻质高强的特点,在航空航天、军工兵器以及轨道交通等领域应用十分广泛。在推广应用之初,研究人员就发现复合材料的低速冲击分层损伤对碳纤维增强复合材料层压板的性能造成巨大危害,这也限制了复合材料向更高要求领域的应用,而造成复合材料层板对冲击分层损伤敏感的主要原因是基体树脂的脆性。因此,提高复合材料韧性成为复合材料学科的重要研究课题。经过多年研究摸索,形成了多种增韧技术,主要包括:共混增韧技术、插层增韧技术、离位增韧技术等等。借助这些增韧技术,出现大量高韧性树脂产品,8551、f3900等作为优秀的增韧产品已在波音787等机型上得到应用。
3.然而,目前纤维增强预浸料增韧手段存仍存在各种各样的问题,主要表现为:1)增韧剂多为一种或多种增韧材料的简单物理分散,增韧效果遇到瓶颈,无法兼顾韧性与其他热力学性能的平衡;2)为实现高增韧效果,通常增韧剂添加量比较大,甚至达到树脂体系总质量分数的35%以上,树脂粘性低、成膜性差导致预浸料工艺操作性差。3)航空用铺丝预浸料对冲击后压缩性能有很高要求,而目前常规含浸工艺无法保证预浸料含浸度,导致铺丝预浸料毛丝问题非常严重;4)无论采用何种增韧技术,所用增韧剂多为单组份热塑或多组分热塑颗粒、膜、织物等的组合,环氧树脂与热塑材料之间的弱界面直接影响到纤维强度的转化率;5)大量增韧剂的存在,降低树脂塑性变形能力,树脂流变特性随温度变化的敏感性降低,在高韧性预浸料体系中影响最终复合材料制件内部质量,表现出结构疏松或分层缺陷,该问题在厚度大于10mm的制件制造中更加显著。高韧性rtm树脂同样存在这样的问题,无法兼顾树脂流动性和韧性。
技术实现要素:
4.本发明所要解决的技术问题是克服现有技术的缺陷,提供一种纳米合金热塑粒子、纳米合金膜及其制备方法和应用,能够实现预浸料增韧与预浸料韧性、操作性和其他热力学性能的平衡,同时延伸应用于rtm成型工艺中,解决航空复合材料存在的诸多技术难点,推动复合材料向更加轻质、安全、低成本方向发展。
5.为解决上述技术问题,本发明提供一种纳米合金热塑粒子的制备方法,包括:将热塑材料、树脂、第一固化剂通过溶剂溶解,加入装有聚乙二醇、水的容器中,机械搅拌形成均匀乳液,然后充氮气去除溶剂,剩余物质进行水洗过滤、干燥、固化、粉碎过筛,得到d90粒径<100μm的纳米合金热塑粒子,优选地,d90粒径<35μm。
6.优选地,所述热塑材料包括pa、pes、pps、peek、peak、pei、pi、ps、pp、pc中的两种或两种以上。
7.优选地,所述树脂为第一热固性树脂,包括缩水甘油胺型环氧树脂、缩水甘油酯型
环氧树脂、缩水甘油醚型环氧树脂、双酚a型环氧树脂、双酚f型环氧树脂、聚合度在0~5的线型酚醛环氧树脂、双环戊二烯环氧树脂、bmt型短链双马来酰亚胺树脂、ddm型双马来酰亚胺树脂、含醚键双马来酰亚胺树脂中的一种或多种。
8.优选地,所述第一固化剂为脂肪胺类、酯环胺类、咪唑类、改性胺类、酸酐类固化剂中的一种或多种;所述溶剂为二氯甲烷、二氯乙烷、氯苯、丙二醇苯醚、乙二醇苯醚、n甲基吡咯烷酮中的一种或多种。
9.优选地,所述树脂和第一固化剂质量按照环氧基团与活泼氢摩尔比1:(0.8~1.2)进行配合,所述树脂和第一固化剂的总质量与热塑材料的质量比为(5~20):100。
10.优选地,所述固化温度为80~230℃,所述固化时间为30~360min,所述干燥温度为60
±
5℃,水洗过滤次数为5-10次。
11.本发明还提供一种上述的方法制备得到的纳米合金热塑粒子。
12.本发明还提供一种纳米合金膜的制备方法,包括:通过真空混合设备将上述的纳米合金热塑粒子、第二热固性树脂、第二固化剂进行物理混合,形成纳米合金膜树脂体系,再经过涂膜设备进行涂膜,形成均匀的波浪纹路结构树脂膜。波浪纹路结构能够使得树脂膜呈厚薄不均类网状结构,避免该合金膜因增韧剂量过大形成致密层,有利于树脂渗透。利用层间增韧理论,本发明纳米合金膜可直接用于预浸料生产,也可用于rtm成型技术中,均实现提高复合材料韧性的作用。所述纳米合金热塑粒子在整个纳米合金膜树脂体系中的质量百分比为30%~50%,更优选地,质量百分比为40%~48%。
13.优选地,所述第二热固性树脂包括缩水甘油胺型环氧树脂、缩水甘油酯型环氧树脂、缩水甘油醚型环氧树脂、双酚a型环氧树脂、双酚f型环氧树脂、双酚s型环氧树脂、线型酚醛环氧树脂、邻甲酚醛环氧树脂、双环戊二烯环氧树脂、萘基环氧树脂、溴化环氧树脂、bmt型短链双马来酰亚胺树脂、ddm型双马来酰亚胺树脂、含醚键双马来酰亚胺树脂、二元胺改性双马来酰亚胺树脂中的一种或多种;所述第二固化剂为脂肪胺类、酯环胺类、咪唑类、改性胺类、酸酐类固化剂中的一种或多种。
14.优选地,所述物理混合温度为60~110℃,物理混合时间为10~60min;树脂粘度为150000~400000cp,涂膜速度为4~15m/s;在涂膜过程中,控制涂胶辊与汲胶辊之间的间隙为0.1~0.4mm,控制涂胶辊与汲胶辊的速度比值为0.5~0.95。
15.本发明还提供一种上述的方法制备得到的纳米合金膜。
16.本发明还提供一种上述的纳米合金膜在预浸料生产中的应用,所述预浸料采用二次含浸工艺,将非增韧树脂体系一次含浸完成后,保持含浸工艺不变,通过二次含浸过程,将上述的纳米合金膜附着在预浸料上下表面,最终得到高韧性预浸料,所述非增韧树脂与纳米合金膜的质量比为1:(0.4~0.7)。此时,整体增韧剂用量不超过树脂体系质量的25%。
17.本发明涉及的纳米合金膜用于热固性树脂增强纤维四膜法预浸料生产。四膜预浸料已作为成熟的预浸料含浸工艺得到应用,主要思路是通过两步含浸过程将四层树脂膜与增强纤维浸渍制得预浸料,本纳米合金膜用于第二步含浸过程。所涉及的热固性树脂可以为乙烯基树脂、环氧树脂、双马来酰亚胺树脂、聚酰亚胺树脂、氰酸酯树脂等;纤维可以是丝束数量为1k~50k的沥青基碳纤维、pan基纤维、粘胶剂碳纤维、无碱玻纤、高强玻纤、芳纶纤维等。
18.本发明还提供一种上述的纳米合金膜在rtm工艺中的应用,通过70~120℃高温加
压方式,将上述的纳米合金膜附着于干织物上表面,形成复合增韧织物,所述rtm工艺中树脂注胶温度为80~110℃,保证纳米合金膜中树脂充分流动且具有较长的适用期,最终得到高冲击韧性复合材料制品。
19.本发明所达到的有益效果:
20.本发明核心在于通过特殊工艺手段实现多种热塑材料在纳米尺度的互穿共熔,并通过特定成膜技术应用于预浸料生产工艺中。带来的有益效果为:
21.1)本发明所得到的纳米合金热塑粒子具有官能团环氧基,在树脂固化过程中参与固化反应,形成统一固化结构,有利于应力传递,拉伸强度转化率高,制得的复合材料层压板仍能保持较高的力学性能,同时具有优异的纳米尺度相界面,有效阻止裂纹扩展,能够发挥出优于普通微米尺度合金塑料的增韧效果;
22.2)本发明将纳米合金热塑粒子制备成波浪结构的合金树脂膜,应用于预浸料生产中,大大提升热固性复合材料的冲击后压缩强度,同时不影响复合材料耐热及其他力学性能,比如dma tg、拉伸强度、压缩强度等;
23.3)本发明所得到的纳米合金膜,能够采用更少的增韧剂用量达到同样的增韧效果,有利于解决预浸料难以含浸和流动性差的问题,满足大厚度制件的生产需求;
24.4)本发明所得到的纳米合金膜,能够创新性地用于rtm工艺中,在不影响树脂渗透效率的同时,起到高效增韧的作用。
附图说明
25.图1是本发明固化工艺曲线图。
具体实施方式
26.下面结合实施例对本发明作进一步描述。以下实施例仅用于更加清楚地说明本发明的技术方案,而不能以此来限制本发明的保护范围。
27.实施例1
28.一种纳米合金膜的制备方法,具体步骤如下:
29.1.将100g的pes、80g的pps、18g的四缩水甘油胺环氧树脂、6.2g的4,4
’‑
二氨基二苯砜溶解于2000g的二氯甲烷中,然后加入装有4000g的水、170g的聚乙烯醇容器中,采用机械搅拌高速分散60min,形成均匀乳液,通过充氮气去除溶剂,剩余物质进行水洗过滤7次,60℃左右温度下干燥去除水,在180℃温度下固化2h,固化完成后粉碎过筛,得到d90粒径在34μm的纳米合金热塑粒子。
30.2.按照质量分数将44份上述纳米合金热塑粒子、26份四缩水甘油胺环氧树脂、5份双酚f环氧、10份线型酚醛环氧、15份4,4
’‑
二氨基二苯砜加入真空混合釜中,在100℃混合20min,75℃下树脂粘度达到260000cp,以9m/s的涂膜速度在75℃温度下进行涂膜,控制涂胶辊与汲胶辊间隙为0.25mm,控制涂胶辊与汲胶辊的速度比为0.85,形成面密度为20g/m2的波浪纹路结构纳米合金膜。
31.实施例2
32.一种纳米合金膜的制备方法,具体步骤如下:
33.1.将100g的pa、80g的pps、18g的三缩水甘油胺环氧树脂、7.2g的4,4
’‑
二氨基二苯
砜溶解于2000g的二氯甲烷中,然后加入装有4000g的水、170g的聚乙烯醇容器中,采用机械搅拌高速分散60min,形成均匀乳液,通过充氮气去除溶剂,剩余物质进行水洗过滤7次,60℃左右温度下干燥去除水,在180℃温度下固化2h,固化完成后粉碎过筛,得到d90粒径在30μm的纳米合金热塑粒子。
34.2.按照质量分数将52份上述纳米合金热塑粒子、20份三缩水甘油胺环氧树脂、16份e51环氧树脂、12份4,4
’‑
二氨基二苯砜加入真空混合釜中,在105℃混合20min,75℃下树脂粘度达到240000cp,以9m/s的涂膜速度在75℃温度下进行涂膜,控制涂胶辊与汲胶辊间隙为0.24mm,控制涂胶辊与汲胶辊的速度比为0.88,形成面密度为20g/m2的波浪纹路结构纳米合金膜。
35.实施例3
36.一种纳米合金膜的制备方法,具体步骤如下:
37.1.将70g的pp、90g的pps、18g的二缩水甘油醚环氧树脂、6.2g的异佛尔酮二胺溶解于2000g的二氯甲烷中,然后加入装有4000g的水、170g的聚乙烯醇容器中,采用机械搅拌高速分散60min,形成均匀乳液,通过充氮气去除溶剂,剩余物质进行水洗过滤7次,60℃左右温度下干燥去除水,在180℃温度下固化2h,固化完成后粉碎过筛,得到d90粒径在28μm的纳米合金热塑粒子。
38.2.按照质量分数将46份上述纳米合金热塑粒子、23份二缩水甘油醚环氧树脂、6份双酚f环氧、10份线型酚醛环氧、15份二氨基二苯甲烷加入真空混合釜中,在85℃混合20min,75℃下树脂粘度达到212000cp,以9m/s的涂膜速度在75℃温度下进行涂膜,控制涂胶辊与汲胶辊间隙为0.21mm,控制涂胶辊与汲胶辊的速度比为0.8,形成面密度为20g/m2的波浪纹路结构纳米合金膜。
39.实施例4
40.一种纳米合金膜在预浸料中的应用,具体步骤如下:
41.采用面密度为30g/m2的非增韧树脂膜、面密度为200g/m2的恒神hf40单向碳纤维进行一次含浸,保持含浸工艺不变,通过二次含浸过程,将本发明实施例1制得的纳米合金膜附着在预浸料上下表面,得到最终预浸料。
42.实施例5
43.一种纳米合金膜在预浸料中的应用,具体步骤如下:
44.采用面密度为30g/m2的恒神eh103韧性型树脂膜、面密度为200g/m2的恒神hf40单向碳纤维进行一次含浸,保持含浸工艺不变,通过二次含浸过程,将本发明实施例2制得的纳米合金膜附着在预浸料上下表面,得到最终预浸料。
45.实施例6
46.一种纳米合金膜在预浸料中的应用,具体步骤如下:
47.采用面密度为30g/m2的非增韧树脂膜、面密度为200g/m2的恒神hf40单向碳纤维进行一次含浸,保持含浸工艺不变,通过二次含浸过程,将本发明实施例3制得的纳米合金膜附着在预浸料上下表面,得到最终预浸料。
48.性能测试
49.将得到的预浸料制备成复材板,并进行性能测试,具体性能测试过程如下:
50.1)母料通过热压罐固化工艺制备测试板及500*500*10mm层板,固化制度见附图1,
按照相应的测试标准进行试样加工及测试,主要测试项包括:超声波无损检测、0
°
拉伸强度及模量、0
°
压缩强度及模量、冲击后压缩强度、dma tg;
51.2)分切成6.35mm铺丝料,按照如下工艺进行平板铺贴:铺丝头压力为1000n、铺丝头温度为35℃、铺丝速率为0.5m/s,连续铺贴8小时,评价铺丝工艺性。
52.具体性能结果如下表所示:
53.表1.实施例4-6的性能测试结果
[0054][0055]
注:1#高韧预浸料为铺丝预浸料,纤维面密度为194g/m2,树脂含量为35%,180℃固化。
[0056]
从表1测试结果可以看出,纳米合金膜在预浸料中应用后表现出如下优点:1)增韧后复合材料层压板cai数据较原始有大幅度提升,能够达到第四代增韧效果;2)本发明应用在预浸料上,能够保持树脂良好流动性,未出现厚板无损问题;3)因纳米合金热塑粒子具有官能团环氧基,在树脂固化过程中参与固化反应,形成统一固化结构,有利于应力传递,拉伸强度转化率高;4)增韧剂添加量较少,耐热性没有明显下降,远优于市售高韧预浸料(0
°
拉伸强度、压缩强度、dma tg较低);5)采用两次含浸工艺,增韧剂集中在外膜上,保证内膜树脂能够充分浸润纤维,预浸料含浸度有明显提升,因此保持良好的铺丝工艺性。
[0057]
实施例7
[0058]
一种纳米合金膜在rtm工艺中的应用,具体步骤如下:
[0059]
通过80℃加压,将实施例1制得的纳米合金膜附着与面密度为150g/m2恒神hf40碳纤维平纹织物上表面,形成复合增韧织物,采用恒神eh301高温液体环氧树脂,在85℃的注胶温度下制备测试板,在烘箱中固化,固化制度为180℃*2h,按照相应的测试标准进行试样加工及测试,主要测试项包括:经向拉伸强度及模量、经向压缩强度及模量、冲击后压缩强度、
[0060]
层间剪切强度、dma tg。表2.实施例7的性能测试结果
[0061][0062]
从表2测试结果可以看出,纳米合金膜在rtm工艺中应用后表现出如下特点:1)增韧后复合材料层压板cai数据较原始有大幅度提升,增韧效果明显;2)因纳米合金热塑粒子具有官能团环氧基,在树脂固化过程中参与固化反应,形成统一固化结构,有利于应力传递,拉伸强度转化率高,制得的复合材料层压板仍能保持较高的力学性能。
[0063]
以上所述仅是本发明的优选实施方式,应当指出,对于本技术领域的普通技术人员来说,在不脱离本发明技术原理的前提下,还可以做出若干改进和变形,这些改进和变形也应视为本发明的保护范围。