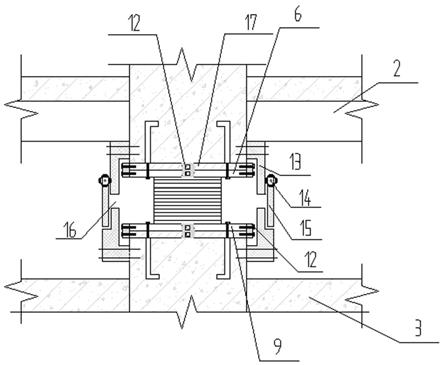
1.本发明属于既有隔震建筑维护施工方法领域,具体涉及一种既有隔震建筑隔震支座无扰动更换施工方法。
背景技术:
2.随着建筑防灾减灾技术不断提高,隔震技术在国内得到快速发展,相当数量的学校、医院、应急指挥中心等建筑应用了隔震技术,经过历次地震的检验,隔震建筑具有良好的隔震性能,从而大大降低了上部结构的地震作用,减小了上部结构的地震损伤,确保建筑功能的正常运行,是一项经济、高效的防灾减灾技术。
3.隔震技术以其显著的减震效果和良好的经济适用性已经得到工程界的普遍认可。特别是汶川地震以后至今,国家相继在建筑防震减灾方面力度逐渐加大,逐渐开始推广隔震和消能减震在工程中的应用。国内隔震建筑数量逐年增加,其中存在一些隔震建筑因缺少维护或受到环境侵蚀的影响,造成隔震支座的性能大大降低,隔震支座的减震效果不显著,亟待需要对支座进行更换。
4.隔震支座在上部竖向荷载作用下,发生竖向压缩变形,如果直接顶升梁柱节点,隔震支座的竖向压力释放后,其竖向压缩变形必然恢复,这样为了将隔震支座更容易的水平推出,首先要顶升节点使支座恢复竖向高度,然后再顶升一定的高度,才有可能把支座水平推出,这就大大增加了顶升高度,也增加了由于顶升对上部结构产生不良的影响。
5.在隔震支座更换过程中减小因支座的压缩变形会导致上部结构发生附加变形,造成上部结构的损伤,影响隔震建筑的隔震效果。如何避免支座压缩变形产生的不利影响,将直接对隔震支座更换的成败取决定性作用。隔震支座无扰动更换方法能够避免支座更换后产生的压缩变形,使各支撑点无附加变形产生,避免上部结构附加变形产生的损伤,保证隔震建筑的隔震性能。
技术实现要素:
6.本发明要解决的技术问题是提供一种机械化程度高、控制精度高、更换效率高、施工成本低,便于现场管理与实际操作既有隔震建筑隔震支座无扰动更换施工方法。
7.为解决上述技术问题本发明所采取的技术方案是:一种既有隔震建筑隔震支座无扰动更换装置,其包括同步顶升支撑系统以及隔震支座预压缩装置;所述同步顶升支撑系统包括plc同步顶升支撑控制系统、动力装置、信号采集装置以及千斤顶;所述动力装置为液压泵站,所述液压泵站与千斤顶连接;所述信号采集装置包括位移传感器和压力传感器,所述信号采集装置与plc同步顶升支撑控制系统连接;所述千斤顶设置于隔震层顶梁和隔震层底板之间;
所述压力传感器设置于千斤顶与隔震层顶梁底面接触部位。
8.进一步的,所述隔震支座预压缩装置包括通过上固定螺栓固定在支座顶板上的上预压连接件、通过下固定螺栓固定在支座底板上的下预压连接件以及连接所述上预压连接件和下预压连接件的预加力螺栓螺母组合。
9.进一步的,所述位移传感器为拉线式位移计,所述位移传感器的位移计设置于隔震层顶梁底部,所述位移传感器的拉线端固定设置于隔震层底板的顶面。
10.进一步的,所述位移传感器、压力传感器与千斤顶成对布置。
11.进一步的,所述千斤顶为两个以上。
12.一种如权利要求1所述的既有隔震建筑隔震支座无扰动更换装置的使用方法,其包括以下步骤:s1:安装千斤顶临时支撑,采用长行程机械自锁千斤顶作为临时支撑,安装在支撑点附近指定部位,校准千斤顶的垂直度,避免千斤顶倾斜产生侧向支撑分力,确保千斤顶临时支撑的安全和有效;s2:安装plc同步顶升支撑系统,在支撑点附近安装plc同步顶升支撑系统,通过信号采集装置的数据反馈,plc同步顶升支撑控制系统给液压泵站发送指令,控制千斤顶临时支撑的顶力大小,保证支撑点无竖向变形产生,并通过压力和位移的数据传输反馈,控制千斤顶的支撑顶力,实现动力不间断且平稳可控;s3:预压装置制作及安装,在旧隔震支座上均匀安装预压装置,首先通过上固定螺栓将上预压连接件固定在旧隔震支座顶板上,通过下固定螺栓将下预压连接件固定在旧隔震支座底板上,安装预加力螺栓,以旋转90度为加载步,依次紧固预加力螺栓,逐步实现旧隔震支座的预压,在预加力螺栓紧固的同时,旋松旧隔震支座固定螺栓,当旧隔震支座顶板与上预埋板之间出现微缝隙时,停止预压缩;s4:临时支撑和预压缩协同,在旧隔震支座施加预压缩的同时,通过位移计反馈数据监控支撑点的竖向变形情况,通过plc同步顶升支撑控制系统控制千斤顶临时支撑施加顶力,使支撑点不产生竖向变形;s5:上下预埋板板面抛光除尘,旧隔震支座移出支撑点后,对上下预埋板板面进行锈蚀、抛光和除尘,保证板面的平整光滑,不得过度打磨,损伤上下预埋板,最后涂刷防锈油;s6:新隔震支座预压缩,选取与旧隔震支座同规格的新隔震支座,对应隔震支座顶板、隔震支座底板上均留设螺栓孔,在新隔震支座四周均匀安装预压装置,并按照预加力螺栓单次旋转90度为一加载步,依次紧固预加力螺栓,直至新隔震支座的高度满足安装为止,最后新隔震支座顶板、新隔震支座底板上刷防锈油;s7:新隔震支座安装,安装新隔震支座前,首先对支撑点上下预埋板和新隔震支座顶(底)板涂刷润滑剂,将新隔震支座移入支撑点处,矫正位置,先用支座固定螺栓预固定,然后按照预压装置预加力螺旋单次旋转90度为荷载步,依次旋松预加力螺栓,保证在旋松的过程中每个预加力螺栓旋松长度相同,使预压新隔震支座顶板与上预埋板平稳贴合,拆除预压装置,同时,依次紧固支座固定螺栓,完成新隔震支座安装。
13.进一步的,还包括步骤s8:安装加强连接件,支座固定螺栓紧固完毕后,在新隔震支座顶(底)板与上下预埋板相应侧面安装加强连接件,作为连接节点的补强措施,用于补
偿新隔震支座顶(底)板与上下预埋板之间因润滑剂造成的摩阻力降低的问题,增强新隔震支座连接部位抵抗水平作用,保证新隔震支座有可靠连接,同时方便后期的隔震支座再更换。
14.进一步的,还包括步骤s9:拆除更换装置,新隔震支座连接完毕后,拆除plc同步顶升支撑控制系统、位移传感器、压力传感器、千斤顶等。
15.进一步的,还包括步骤s10:安装防护装置,在支撑点周侧安装防护装置,用于防火、防尘、防外界腐蚀,并留设可开启的检查窗口,便于定期检测检查。
16.采用上述技术方案所产生的有益效果在于:本发明涉及的隔震建筑隔震支座无扰动更换施工方法,利用plc同步顶升支撑系统作为临时支撑的动力源,采用位移计监测并控制支撑点处竖向变形,在旧隔震支座上安装预压装置,预压装置能够限制旧隔震支座产生回弹变形,然后将旧隔震支座从支撑点处移出,对上下预埋板板面抛光打磨、除尘;在新隔震支座上安装预压装置,将新隔震支座预压缩至工作高度,支座顶(底)板抛光打磨、除尘,分别对上下预埋板板面和新支座顶(底)板面涂抹润滑剂,将新隔震支座移入支撑点处并固定,拆除预压缩装置,在上下预埋板与支座顶(底)板端部设置加强连接件,对新隔震支座与预埋板的连接进一步加强,提高连接点处抵抗水平荷载能力,最后安装新增支座防护装置,该方法能够保证在隔震支座更换过程中,plc同步顶升支撑系统能够控制结构的竖向变形,预压装置能够对隔震支座进行预压缩,方便于旧隔震支座的水平推出与新隔震支座的安装。更换后隔震支座全过程无附加压缩变形产生,各个支撑点处不会产生附加变形,结构无附加内力,对结构楼板未造成不良影响,隔震建筑性能实现最优化,并且该方法机械化程度高、不用顶升梁柱节点、控制精度高、更换效率高、同时施工、施工成本低等优点,便于现场管理与实际操作。
附图说明
17.图1为本发明更换安装完成结构示意图图2为本发明完成同步顶升支撑系统安装完成后结构示意图;图3为本发明预压装置安装完成结构示意图;图4为本发明加强连接件安装完成结构示意图;图5为本发明预压装置安装状态结构示意图;图6为本发明预压装置主视结构示意图;图7为本发明预压装置左视结构示意图;图8为本发明隔震支座俯视结构示意图;其中,1、千斤顶,2、隔震层顶梁,3、隔震层底板,4、位移传感器,5、上固定螺栓,6、支座顶板,7、上预压连接件,8、下固定螺栓,9、支座底板,10、下预压连接件,11、预加力螺栓螺母组合,12、加强连接件,13、防火板维护罩,14、铰轴,15、悬挂防火板,16、检查窗口,17、预埋板,18、加强连接件螺栓孔,19、预压螺栓孔,20、支座固定螺栓孔。
具体实施方式
18.下面结合附图对本发明做进一步说明。
19.如附图1-8所示,本实施例提供一种既有隔震建筑隔震支座无扰动更换装置,其包
括同步顶升支撑系统以及隔震支座预压缩装置;所述同步顶升支撑系统包括plc同步顶升支撑控制系统、动力装置、信号采集装置以及千斤顶;所述动力装置为液压泵站,所述液压泵站与千斤顶1连接为千斤顶1提供动力输出;所述信号采集装置包括位移传感器4和压力传感器,所述信号采集装置与plc同步顶升支撑控制系统连接,为plc同步顶升支撑控制系统提供信号输出;所述千斤顶设置于隔震层顶梁2和隔震层底板3之间;所述压力传感器设置于千斤顶1与隔震层顶梁2底面接触部位,用于监测施力点施力情况。
20.所述位移传感器4、压力传感器与千斤顶1成对布置,所述千斤顶1为两个以上,所述位移传感器4为拉线式位移计,控制精度0.01m,位移计拉出线保证垂直,所述位移传感器4的位移计设置于隔震层顶梁底部,所述位移传感器的拉线端固定设置于隔震层底板的顶面,位移计连接plc同步顶升控制系统,通过位移计的数据反馈实现plc同步顶升控制系统的有效临时支撑。
21.plc同步顶升支撑控制系统包括挠度模块、载荷模块、校核模块、供电模块、主控模块、报警模块、交互界面等,载荷模块负责采集、处理压力传感器的实时荷载检测值并发送至主控模块进行处理计算进行荷载监测控制,挠度模块通过将位移传感器采集到的信息传输至主控模块处理计算进行挠度监测控制,同步顶升支撑过程中,载荷模块、挠度模块等将采集到的检测数据实时传送到主控模块,主控模块按照预定算法进行计算、分析、判断进行输出显示,并将数据存储至数据库中,保证支撑顶升的同步、平衡、准确、稳定,控制千斤顶临时支撑的顶力大小,保证支撑点无竖向变形产生,在隔震支座更换过程中实现临时支撑的智能化控制,操作更简便,管理更便捷。
22.所述隔震支座预压缩装置包括通过上固定螺栓5穿过预压螺栓孔19固定在支座顶板6上的上预压连接件7、通过下固定螺栓8穿过预压螺栓孔19固定在支座底板9上的下预压连接件10以及连接所述上预压连接件7和下预压连接件10的预加力螺栓螺母组合11,隔震支座预压装置是利用金属拉结件通过预加力螺栓螺母组合11的紧固连接形成的拉紧装置,通过隔震支座周侧预加力螺栓螺母组合11依次紧固,实现隔震支座的预压缩,能够限制隔震支座产生回弹变形,方便于旧隔震支座的水平推出与新隔震支座的安装,减少顶升量,便于隔震支座的更换,减小因支座的压缩变形会导致上部结构发生附加变形,造成上部结构的损伤,影响隔震建筑的隔震效果,对结构楼板未造成不良影响,隔震建筑性能实现最优化。
23.一种既有隔震建筑隔震支座无扰动更换施工方法,其包括以下步骤:s1:安装千斤顶临时支撑,采用长行程机械自锁千斤顶作为临时支撑,安装在支撑点附近指定部位,校准千斤顶的垂直度,避免千斤顶倾斜产生侧向支撑分力,确保千斤顶临时支撑的安全和有效;位移计与千斤顶成对布置,与plc同步顶升控制系统连接,通过压力和位移的数据传输反馈,控制千斤顶的支撑顶力,实现动力不间断且平稳可控;千斤顶就位后,采用压力和位移双控制,以支撑点处的反力为参照,给千斤顶施加压力,使千斤顶完全支撑上部结构的重量;s2:安装plc同步顶升支撑系统,在支撑点附近安装plc同步顶升支撑系统,通过信号采集装置的数据反馈,plc同步顶升支撑控制系统给液压泵站发送指令,控制千斤顶临时支撑的顶力大小,稳定支撑并保证支撑点无竖向变形产生,并通过压力和位移的数据传输反馈,控制千斤顶的支撑顶力,实现动力不间断且平稳可控,确保顶升支撑过程的同步、平
衡以及稳定性;s3:预压装置制作及安装,在旧隔震支座上均匀安装预压装置,首先通过上固定螺栓将上预压连接件固定在旧隔震支座顶板上,通过下固定螺栓将下预压连接件固定在旧隔震支座底板上,安装预加力螺栓,以旋转90度为加载步,依次紧固预加力螺栓,逐步实现旧隔震支座的预压,在预加力螺栓紧固的同时,旋松穿过支座固定螺栓孔20的旧隔震支座固定螺栓,当旧隔震支座顶板与上预埋板之间出现微缝隙时,停止预压缩,预压装置能够对隔震支座进行预压缩,方便于旧隔震支座的水平推出与新隔震支座的安装;s4:临时支撑和预压缩协同,在旧隔震支座施加预压缩的同时,通过位移计反馈数据监控支撑点的竖向变形情况,通过plc同步顶升支撑控制系统控制千斤顶临时支撑施加顶力,使支撑点不产生竖向变形;s5:上下预埋板板面抛光除尘,旧隔震支座移出支撑点后,对预埋板17的板面进行锈蚀、抛光和除尘,保证板面的平整光滑,不得过度打磨,损伤上下预埋板,最后涂刷防锈油;s6:新隔震支座预压缩,选取与旧隔震支座同规格的新隔震支座,对应隔震支座顶板、隔震支座底板上均留设螺栓孔,在新隔震支座四周均匀安装预压装置,并按照预加力螺栓单次旋转90度为一加载步,依次紧固预加力螺栓,直至新隔震支座的高度满足安装为止,最后新隔震支座顶板、新隔震支座底板上刷防锈油;s7:新隔震支座安装,安装新隔震支座前,首先对支撑点上下预埋板和新隔震支座顶(底)板涂刷润滑剂,将新隔震支座移入支撑点处,矫正位置,先用支座固定螺栓预固定,然后按照预压装置预加力螺旋单次旋转90度为荷载步,依次旋松预加力螺栓,保证在旋松的过程中每个预加力螺栓旋松长度相同,使预压新隔震支座顶板与上预埋板平稳贴合,拆除预压装置,同时,依次紧固支座固定螺栓,完成新隔震支座安装。
24.s8:安装加强连接件,支座固定螺栓紧固完毕后,在新隔震支座顶(底)板与上下预埋板相应侧面安装加强连接件12,在新隔震支座顶(底)板上预留加强连接件螺栓孔18,在预埋板17上分别开设连接件螺栓孔,通过紧固螺栓作为紧固件将新隔震支座顶板、上预埋板,新隔震支座底板、下预埋板通过加强连接件12进行连接,作为连接节点的补强措施,用于补偿新隔震支座顶(底)板与上下预埋板之间因润滑剂造成的摩阻力降低的问题,增强新隔震支座连接部位抵抗水平作用,保证新隔震支座有可靠连接,同时方便后期的隔震支座再更换。
25.步骤s9:拆除更换装置,新隔震支座连接完毕后,拆除plc同步顶升支撑控制系统、位移传感器、压力传感器、千斤顶等。
26.步骤s10:安装防护装置,在支撑点周侧安装防护装置,防护装置包括通过固定螺栓固定在隔震层顶梁2和隔震层底板3上的防火板维护罩13,对应的两个防火板维护罩13之间留有用于防火、防尘、防外界腐蚀,并留设可开启的检查窗口16,便于定期检测检查,上侧的防火板维护罩13上通过铰轴14设置悬挂防火板15,所述悬挂防火板15对检查窗口16形成有效遮挡。
27.施工工作过程原理如下:本发明涉及的更换装置的施工方法中,首先进行安装千斤顶临时支撑,采用长行程机械自锁千斤顶作为临时支撑,安装在支撑点附近指定部位,校准千斤顶的垂直度,避免
千斤顶倾斜产生侧向支撑分力,确保千斤顶临时支撑的安全和有效;然后安装plc同步顶升支撑系统,在支撑点附近安装plc同步顶升支撑系统,通过信号采集装置的数据反馈,plc同步顶升支撑控制系统给液压泵站发送指令,控制千斤顶临时支撑的顶力大小,保证支撑点无竖向变形产生,并通过压力和位移的数据传输反馈,控制千斤顶的支撑顶力,实现动力不间断且平稳可控;再进行预压装置制作及安装,在旧隔震支座上均匀安装预压装置,首先通过上固定螺栓将上预压连接件固定在旧隔震支座顶板上,通过下固定螺栓将下预压连接件固定在旧隔震支座底板上,安装预加力螺栓,以旋转90度为加载步,依次紧固预加力螺栓,逐步实现旧隔震支座的预压,在预加力螺栓紧固的同时,旋松旧隔震支座固定螺栓,当旧隔震支座顶板与上预埋板之间出现微缝隙时,停止预压缩;随后进行临时支撑和预压缩协同,在旧隔震支座施加预压缩的同时,通过位移计反馈数据监控支撑点的竖向变形情况,通过plc同步顶升支撑控制系统控制千斤顶临时支撑施加顶力,使支撑点不产生竖向变形;对上下预埋板板面抛光除尘,旧隔震支座移出支撑点后,对上下预埋板板面进行锈蚀、抛光和除尘,保证板面的平整光滑,不得过度打磨,损伤上下预埋板,最后涂刷防锈油;对新隔震支座预压缩,选取与旧隔震支座同规格的新隔震支座,对应隔震支座顶板、隔震支座底板上均留设螺栓孔,在新隔震支座四周均匀安装预压装置,并按照预加力螺栓单次旋转90度为一加载步,依次紧固预加力螺栓,直至新隔震支座的高度满足安装为止,最后新隔震支座顶板、新隔震支座底板上刷防锈油;然后对新隔震支座安装,安装新隔震支座前,首先对支撑点上下预埋板和新隔震支座顶(底)板涂刷润滑剂,将新隔震支座移入支撑点处,矫正位置,先用支座固定螺栓预固定,然后按照预压装置预加力螺旋单次旋转90度为荷载步,依次旋松预加力螺栓,保证在旋松的过程中每个预加力螺栓旋松长度相同,使预压新隔震支座顶板与上预埋板平稳贴合,拆除预压装置,同时,依次紧固支座固定螺栓,完成新隔震支座安装,采用此种更换装置和更换方法该方法能够保证在隔震支座更换过程中,plc同步顶升支撑系统能够控制结构的竖向变形,预压装置能够对隔震支座进行预压缩,方便于旧隔震支座的水平推出与新隔震支座的安装。预压装置能够对隔震支座进行预压缩,更换后隔震支座全过程无附加压缩变形产生,各个支撑点处不会产生附加变形,结构无附加内力,对结构楼板未造成不良影响,隔震建筑性能实现最优化,并且该方法机械化程度高、不用顶升梁柱节点、控制精度高、更换效率高、同时施工、施工成本低等优点,便于现场管理与实际操作。
28.对所公开的实施例的上述说明,使本领域专业技术人员能够实现或使用本发明。对这些实施例的多种修改对本领域的专业技术人员来说将是显而易见的,本文中所定义的一般原理可以在不脱离本发明的精神或范围的情况下,在其它实施例中实现。因此,本发明将不会被限制于本文所示的这些实施例,而是要符合与本文所公开的原理和新颖特点相一致的最宽的范围。