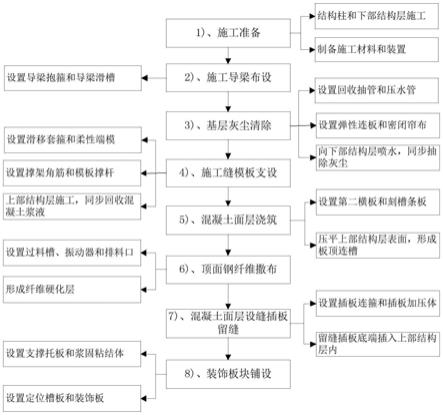
1.本发明涉及高强度混凝土路面工程,特别涉及一种可提高施工效率、降低留缝难度、改善纤维层撒布质量的钢纤维混凝土地面硬化施工方法。
背景技术:
2.建筑工业厂房中,为改善地面的防尘效果、提升地面强度,常采用钢纤维混凝土地面。在钢纤维混凝土地面施工时,如何改善混凝土施工质量、降低施工缝留缝难度、提高现场施工质量,一直是工程控制的重点和难点。
3.现有技术中已有一种锂基耐磨硬化地面施工方法,结合锂基混凝土固化剂与混凝土中大量的半水化水泥、游离石灰、钙发生化学反应,形成一种永久性凝胶。该凝胶虽可达到密封、硬化、防尘的效果,但该技术难以同步满足降低留缝施工难度、提升现场施工效率、提升结构整体性等问题。
4.鉴于此,为提升钢纤维混凝土地面硬化工程的施工质量、降低施工难度,目前亟待发明一种可以提升施工效率、降低留缝施工的难度、提升装饰板安装结构的整体性、改善纤维层撒布质量的钢纤维混凝土地面硬化施工方法。
技术实现要素:
5.本发明的目的在于提供一种不但可以降低后续施工缝界面处理的难度,而且可以改善纤维层撒布的质量,还可以提升装饰板安装结构整体性的钢纤维混凝土地面硬化施工方法。
6.为实现以上目的,本方案提供一种钢纤维混凝土地面的施工方法,包括以下步骤:1)施工准备:进行结构柱和下部结构层施工,制备施工所需的材料和装置;
7.2)施工导梁布设:在结构柱上分别设置导梁抱箍,并在相邻的导梁抱箍之间设置施工导梁,在施工导梁上设置横断面呈“t”形的导梁滑槽;
8.3)基层灰尘清除:使第一滑块顶部与施工导梁的导梁滑槽连接、底部设置第一横板,并在第一横板的上表面和下表面分别设置回收抽管和压水管,使回收抽管和压水管分别与回收管口和喷水头连通;使第一拉索与第一滑块连接,通过第一拉索控制第一滑块的位置;在第一横板的四周均匀间隔设置面向下部结构层的弹性连板,并在弹性连板的内侧沿环向粘贴密闭帘布;通过压水管及喷水头向下部结构层喷水,同步通过回收抽管和回收管口抽除下部结构层表面的灰尘;
9.4)施工缝柔性端模支设:在施工导梁上套设滑移套箍,并根据施工缝位置要求,确定滑移套箍在施工导梁上的位置;采用撑架横筋和撑架竖筋焊接成网格状的模板撑架,并在撑架横筋背离撑架竖筋侧粘贴柔性端模,在撑架竖筋背离撑架横筋侧焊接横断面呈直角三角形的撑架角筋;在滑移套箍与模板撑架之间设置模板撑杆,并使模板撑杆的两端通过撑杆转动铰分别与滑移套箍和撑架角筋连接;进行上部结构层混凝土灌注施工,同步通过余浆回收槽回收从柔性端模空隙溢出的混凝土浆液;
10.5)混凝土面层浇筑:使第二滑块与导梁滑槽连接,并在第二滑块的下表面设置第二横板;使第二横板的下表面分别通过连板调节栓和滚轮调节栓与条板连板和滚轮连轴连接,并在条板连板的下表面均匀间隔设置刻槽条板,使滚轮连轴与弹性滚轮连接;使第二拉索与第二横板连接,通过第二拉索控制第二横板的位置,先通过弹性滚轮对上部结构层上表面进行压平,再通过刻槽条板在上部结构层的上表面形成板顶连槽;
11.6)顶面钢纤维撒布:使第三滑块与导梁滑槽连接,并在第三滑块的下表面设置料槽连板横板;在料槽连板的下表面设置纤维供料槽,并在纤维供料槽的下方设置过料槽;使过料槽与料槽连板通过料槽连筋连接,并在过料槽的侧壁上设置振动器,在过料槽的底板上设置排料口;在过料槽的下表面设置纤维刷板;通过第三拉索控制第三滑块及料槽连板的横向位置,同步通过振动器震动过料槽,使纤维经排料口撒布在上部结构层的上表面,先通过纤维刷板控制纤维撒布层的厚度,再采用人工对纤维层进行振捣密实,使纤维层与混凝土上部结构层混合形成纤维硬化层;
12.7)混凝土面层设缝插板留缝:在施工导梁上套设插板连箍,并根据留缝位置,通过连箍固定栓将插板连箍与施工导梁连接牢固;在插板连箍的下表面设置插板加压体,通过导槽控位栓控制导槽侧板的竖直度;使留缝插板的顶端与板顶连接槽连接牢固,通过插板加压体对板顶连接槽及留缝插板施加下压力,使留缝插板的底端插入上部结构层内;
13.8)装饰板块铺设:在上部结构层内钻设与浆固螺栓连接的螺栓连接孔;在立柱底板的上表面均匀间隔设置托板支柱,并在托板支柱的顶端设置支撑托板;先向螺栓连接孔内灌注浆固粘结体,再将浆固螺栓压入螺栓连接孔内;将支撑桁梁设于支撑托板的上表面,并通过托板紧固栓将桁梁耳板与支撑托板连接牢固;在支撑桁梁的上表面设置定位槽板,并将装饰板设于定位槽板内。
14.根据本方案的另一方面,本方案提供一种根据上述钢纤维混凝土地面的硬化施工方法施工得到的钢纤维混凝土地面。
15.相较现有技术,本技术方案具有以下特点和有益效果:
16.(1)本发明在第一横板的上表面和下表面分别设置回收抽管和压水管,可通过压水管及喷水头向下部结构层喷水,同步通过回收抽管和回收管口抽除下部结构层表面的灰尘;在第一横板的四周沿环向设置弹性连板和密闭帘布,可快速清除基层灰尘。
17.(2)本发明撑架横筋和撑架竖筋焊接成网格状的模板撑架,并在模板撑架的两侧分别设置柔性端模和余浆回收槽,实现了上部结构层施工缝部位的柔性支挡,降低了后续施工缝界面处理的难度。
18.(3)本发明在第二横板的下表面设置连板调节栓和滚轮调节栓,可先通过弹性滚轮对上部结构层上表面进行压平,再通过刻槽条板在上部结构层的上表面形成板顶连槽,实现了上部结构层的快速找平和板顶连槽施工。
19.(4)本发明在料槽连板的下表面设置纤维供料槽,并在纤维供料槽的下方设置过料槽,在过料槽的底板上设置排料口;通过振动器震动过料槽,使纤维经排料口撒布在上部结构层的上表面,先通过纤维刷板控制纤维撒布层的厚度,并形成纤维硬化层,提升了纤维层撒布的质量。
20.(5)本发明在插板连箍的下表面设置插板加压体,并通过导槽控位栓控制导槽角筋控制导槽侧板的竖直度,通过插板加压体对板顶连接槽及留缝插板施加下压力,使留缝
插板的底端插入上部结构层内,实现了留缝插板的控制性压入,降低了留缝施工的难度。
21.(6)本发明采用整体式立柱底板限定托板支柱的位置,先向螺栓连接孔内灌注浆固粘结体,再将浆固螺栓压入螺栓连接孔内,通过托板紧固栓将桁梁耳板与支撑托板连接牢固,将装饰板设于定位槽板内,提升了装饰板的安装结构的整体性。
附图说明
22.图1是本发明钢纤维混凝土地面硬化施工流程图;
23.图2是图1基层灰尘清除结构示意图;
24.图3是图1施工缝模板支设结构示意图;
25.图4是图3施工缝模板结构示意图;
26.图5是图1混凝土面层整平结构示意图;
27.图6是图1钢纤维撒布结构示意图;
28.图7是图1设缝插板压设施工结构示意图;
29.图8是图7设缝插板结构示意图;
30.图9是图1装饰板块铺设结构纵断面示意图;
31.图10是图9装饰板块与组合支架连接结构示意图。
32.图中:1-结构柱;2-下部结构层;3-导梁抱箍;4-施工导梁;5-导梁滑槽;6-第一滑块;7-第一横板;8-回收抽管;9-压水管;10-回收管口;11-喷水头;12-第一拉索;13-弹性连板;14-密闭帘布;15-滑移套箍;16-撑架横筋;17-撑架竖筋;18-模板撑架;19-柔性端模;20-撑架角筋;21-模板撑杆;22-撑杆转动铰;23-上部结构层;24-余浆回收槽;25-第二滑块;26-第二横板;27-连板调节栓;28-滚轮调节栓;29-条板连板;30-滚轮连轴;31-刻槽条板;32-弹性滚轮;33-第二拉索;34-板顶连槽;35-第三滑块;36-料槽连板;37-纤维供料槽;38-过料槽;39-料槽连筋;40-振动器;41-排料口;42-纤维刷板;43-第三拉索;44-纤维撒布层;45-纤维硬化层;46-插板连箍;47-连箍固定栓;48-插板加压体;49-导槽控位栓;50-导槽侧板;51-留缝插板;52-板顶连接槽;53-浆固螺栓;54-螺栓连接孔;55-立柱底板;56-托板支柱;57-支撑托板;58-浆固粘结体;59-支撑桁梁;60-托板紧固栓;61-桁梁耳板;62-定位槽板;63-装饰板;64-弹性控位筋;65-紧固螺栓;66-导槽角筋;67-控位栓转铰;68-结构层钢筋;69-钢筋插设槽。
具体实施方式
33.下面将结合本发明实施例中的附图,对本发明实施例中的技术方案进行清楚、完整地描述,显然,所描述的实施例仅仅是本发明一部分实施例,而不是全部的实施例。基于本发明中的实施例,本领域普通技术人员所获得的所有其他实施例,都属于本发明保护的范围。
34.本领域技术人员应理解的是,在本发明的揭露中,术语“纵向”、“横向”、“上”、“下”、“前”、“后”、“左”、“右”、“竖直”、“水平”、“顶”、“底”“内”、“外”等指示的方位或位置关系是基于附图所示的方位或位置关系,其仅是为了便于描述本发明和简化描述,而不是指示或暗示所指的装置或元件必须具有特定的方位、以特定的方位构造和操作,因此上述术语不能理解为对本发明的限制。
35.可以理解的是,术语“一”应理解为“至少一”或“一个或多个”,即在一个实施例中,一个元件的数量可以为一个,而在另外的实施例中,该元件的数量可以为多个,术语“一”不能理解为对数量的限制。
36.混凝土浇筑施工技术要求、模板支设施工技术要求、型钢轧制及焊接施工技术要求、螺栓紧固施工技术要求等,本实施方式中不再赘述,重点阐述本发明涉及方法的实施方式。
37.图1是本发明钢纤维混凝土地面硬化施工流程图,参照图1所示,钢纤维混凝土地面的硬化施工方法,包括以下施工步骤:
38.1)施工准备:进行结构柱(1)和下部结构层(2)施工,制备施工所需的材料和装置;其中至少两结构柱(1)竖直立设在下部结构层(2)两边侧;
39.2)施工导梁布设:在结构柱(1)上设置导梁抱箍(3),并在置于不同结构柱(1)上的相邻的导梁抱箍(3)之间设置施工导梁(4),在施工导梁(4)上设置横断面呈“t”形的导梁滑槽(5);其中导梁抱箍(3)套置在结构柱(1)上,且施工导梁(4)平行于下层结构柱(2)所在位置连接于两侧的导梁抱箍(3);
40.3)基层灰尘清除:使第一滑块(6)顶部与施工导梁(4)的导梁滑槽(5)连接,第一滑块(6)的底部设置第一横板(7),并在第一横板(7)的上表面和下表面分别设置回收抽管(8)和压水管(9),使回收抽管(8)和回收管口(10)连通,压水管(9)和喷水头(11)连通;使第一拉索(12)与第一滑块(6)连接,通过第一拉索(12)拉动第一滑块(6)沿着导梁滑槽(5)滑动,进而控制第一滑块(6)的位置;在第一横板(7)的四周间隔设置面向下部结构层(2)的弹性连板(13),在一些实施例中,弹性连板(13)均匀间隔设置,并在弹性连板(13)的内侧沿环向粘贴密闭帘布(14);通过压水管(9)及喷水头(11)向下部结构层(2)喷水,同步通过回收抽管(8)和回收管口(10)抽除下部结构层(2)表面的灰尘;在一些实施例中,喷水头(11)设置在压水管(9)的下方且面向下部结构层(2)设置,回收管口(10)设置在回收抽管(8)的下方且面向下部结构层(2)设置。
41.4)施工缝柔性端模支设:在施工导梁(4)上套设滑移套箍(15),并根据施工缝位置要求,确定滑移套箍(15)在施工导梁(4)上的位置;采用撑架横筋(16)和撑架竖筋(17)连接成网格状的模板撑架(18),模板撑架(18)置于下部结构层(2)的表面上,在一些实施例中可选用撑架横筋(16)和撑架竖筋(17)焊接的方式;在滑移套箍(15)与模板撑架(18)之间转动设置模板撑杆(21),并使模板撑杆(21)的两端通过撑杆转动铰(22)分别与滑移套箍(15)和撑架角筋(20)连接;在模板撑架(18)和结构柱(1)之间进行上部结构层(23)混凝土灌注施工,同步通过设置在模板撑架(18)边侧的余浆回收槽(24)回收从模板撑架(18)内溢出的混凝土浆液;具体的是,在撑架横筋(16)背离撑架竖筋(17)侧粘贴柔性端模(19),在撑架竖筋(17)背离撑架横筋(16)侧连接横断面呈直角三角形的撑架角筋(20),在一些实施例中可选用撑架角筋(20)和撑架竖筋(17)焊接的方式;余浆回收槽(24)设置在撑架竖筋(17)背离撑架横筋(16)侧,用于回收从柔性端模(19)空隙溢出的混凝土浆液;
42.5)混凝土面层浇筑:使第二滑块(25)与导梁滑槽(5)连接,并在第二滑块(25)的下表面设置第二横板(26);使第二横板(26)的下表面通过连板调节栓(27)与条板连板(29)连接,第二横板(26)的下表面通过滚轮调节栓(28)和滚轮连轴(30)连接,并在条板连板(29)的下表面间隔设置刻槽条板(31),使滚轮连轴(30)与弹性滚轮(32)连接,在一些实施例中,
刻槽条板(31)均匀设置,弹性滚轮(32)和条板连板(29)置于上部结构层(23)上表面;使第二拉索(33)与第二横板(26)连接,通过第二拉索(33)拉动第二滑块(25)沿着导梁滑槽(5)移动以控制第二横板(26)的位置,先通过弹性滚轮(32)对上部结构层(23)上表面进行压平,再通过刻槽条板(31)在上部结构层(23)的上表面形成板顶连槽(34);
43.6)顶面钢纤维撒布:使第三滑块(35)与导梁滑槽(5)连接,并在第三滑块(35)的下表面设置料槽连板(36),在一些实施例中,料槽连板(36)为横置的横板;在料槽连板(36)的下表面设置纤维供料槽(37),并在纤维供料槽(37)的下方设置过料槽(38),纤维供料槽(37)内的纤维落入过料槽(38)内;使过料槽(38)与料槽连板(36)通过料槽连筋(39)连接,并在过料槽(38)的侧壁上设置振动器(40),在过料槽(38)的底板上设置排料口(41),在一些实施例中,料槽连筋(39)垂直设置以连接过料槽(38)和料槽连板(36);在过料槽(38)的下表面设置纤维刷板(42);使第三拉索(43)和料槽连板(36)连接,通过第三拉索(43)拉动第三滑块(35)在导梁滑槽(5)内移动以控制第三滑块(35)及料槽连板(36)的横向位置,同步通过振动器(40)震动过料槽(38),使置于过料槽(38)内的纤维经排料口(41)撒布在上部结构层(23)的上表面形成纤维撒布层(44),先通过纤维刷板(42)控制纤维撒布层(44)的厚度,再采用人工对纤维撒布层(44)进行振捣密实,使纤维撒布层(44)与上部结构层(23)混合形成纤维硬化层(45);
44.7)混凝土面层设缝插板留缝:在施工导梁(4)上套设插板连箍(46),并根据留缝位置,通过连箍固定栓(47)将插板连箍(46)与施工导梁(4)连接牢固;在插板连箍(46)的下表面设置插板加压体(48)和导槽控位栓(49),通过导槽控位栓(49)控制置于留缝插板(51)边侧的导槽侧板(50)的竖直度;留缝插板(51)插入上部结构层(23)的留缝内,使留缝插板(51)的顶端与板顶连接槽(52)连接牢固,插板加压体(48)置于板顶连接槽(52)上方,进而通过插板加压体(48)对板顶连接槽(52)及留缝插板(51)施加下压力,使留缝插板(51)的底端插入上部结构层(23)内;在本方案的实施例中,导槽控位栓(49)分置于留缝插板(51)的两侧,且导槽控位栓(49)的一端和插板连箍(46)转动连接,导槽控位栓(49)的另一端连接于导槽侧板(50),导槽侧板(50)置于留缝插板(51)边侧。
45.8)装饰板块铺设:在上部结构层(23)内钻设与浆固螺栓(53)连接的螺栓连接孔(54);在立柱底板(55)的上表面均匀间隔设置托板支柱(56),并在托板支柱(56)的顶端设置支撑托板(57),立柱底板(55)的下表面设置紧固螺栓(53);先向螺栓连接孔(54)内灌注浆固粘结体(58),再将浆固螺栓(53)压入螺栓连接孔(54)内;将支撑桁梁(59)设于支撑托板(57)的上表面,并通过托板紧固栓(60)将支撑桁梁(59)边侧的桁梁耳板(61)与支撑托板(57)连接牢固;在支撑桁梁(59)的上表面设置定位槽板(62),并将装饰板(63)设于定位槽板(62)内。
46.步骤3)所述第一横板(7)采用钢板轧制而成,上表面与同一横向位置的2~3个第一滑块(6)连接,在一些实施例中,第一横板(7)和第一滑块(6)焊接连接,在第一横板(7)上预设供回收管口(10)穿设的孔洞,回收管口(10)穿过第一横板(7)设置,所述回收抽管(8)采用钢管或pvc管切割而成,与外部真空泵连通;所述压水管(9)采用钢管或pvc管,与外部压水泵连通;喷水头(11)采用360度节水喷头。
47.所述弹性连板(13)横断面呈“l”形,采用橡胶板切割而成,与第一横板(7)之间设置弹性控位筋(64),弹性连板(13)的一端与弹性控位筋(64)粘贴连接,弹性连板(13)的另
一端与第一横板(7)粘贴连接;所述弹性控位筋(64)采用弹簧轧制而成;在一些实施例中,所述弹性连板(13)置于下部结构层(2)上,弹性连板(13)的顶端和第一横板(7)连接,弹性控位筋(64)置于所述弹性连板(13)和第一横板(7)之间。所述密闭帘布(14)采用橡胶片或土工膜切割而成。
48.步骤4)所述柔性端模(19)采用密目网或钢丝网,与撑架横筋(16)焊接连接;所述滑移套箍(15)采用钢板轧制而成,套设于施工导梁(4)上,在滑移套箍(15)上预设与紧固螺栓(65)连接的螺孔;所述模板撑杆(21)包括螺杆和螺母,并使螺母两侧螺杆的紧固方向相反,使螺杆与撑杆转动铰(22)焊接连接;所述撑杆转动铰(22)采用万向球铰;所述模板撑架(18)包括撑架横筋(16)和撑架竖筋(17),并使撑架横筋(16)与撑架竖筋(17)垂直焊接连接。
49.步骤5)所述滚轮调节栓(28)和连板调节栓(27)均包括螺杆和螺母,并使螺母两侧螺杆的紧固方向相反;所述弹性滚轮(32)采用橡胶滚轮;所述刻槽条板(31)采用钢板轧制而成,横断面呈直角梯形,与条板连板(29)焊接连接。
50.步骤6)所述纤维撒布层(44)采用钢纤维或玻璃纤维或植物纤维;所述过料槽(38)采用钢板轧制而成,横断面呈“u”形,在过料槽(38)的底板上设置横断面呈倒梯形的排料口(41)。
51.步骤7)所述导槽控位栓(49)包括螺母和螺杆,并使螺母两侧螺杆的紧固方向相反,与插板连箍(46)和导槽角筋(66)通过控位栓转铰(67)连接;所述留缝插板(51)采用钢板轧制而成,在留缝插板(51)上预设供结构层钢筋(68)穿过的钢筋插设槽(69)。
52.步骤8)所述支撑桁梁(59)采用钢板轧制而成,在支撑桁梁(59)的两侧设置桁梁耳板(61),并在桁梁耳板(61)上预设供托板紧固栓(60)连接的孔洞。
53.在一些实施例中,本方案提供一种根据上述施工方法施工得到的钢纤维混凝土地面。
54.图2是图1基层灰尘清除结构示意图,图3是图1施工缝模板支设结构示意图,图4是图3施工缝模板结构示意图,图5是图1混凝土面层整平结构示意图,图6是图1钢纤维撒布结构示意图,图7是图1设缝插板压设施工结构示意图,图8是图7设缝插板结构示意图,图9是图1装饰板块铺设结构纵断面示意图,图10是图9装饰板块与组合支架连接结构示意图。
55.参照图2~图10所示,钢纤维混凝土地面的施工过程:在第一横板(7)的四周设置弹性连板(13)和密闭帘布(14),通过喷水头(11)向下部结构层(2)喷水,并通过回收抽管(8)抽除灰尘;在模板撑架(18)的两侧分别设置柔性端模(19)和余浆回收槽(24);先通过弹性滚轮(32)进行上部结构层(23)上表面压平,再通过刻槽条板(31)施工形成板顶连槽(34);通过振动器(40)震动过料槽(38),使纤维经排料口(41)撒布在上部结构层(23)的上表面,并通过纤维刷板(42)控制纤维撒布层(44)的厚度,形成纤维硬化层(45);在插板连箍(46)的下表面设置插板加压体(48),并通过导槽控位栓(49)控制导槽侧板(50)的竖直度;采用立柱底板(55)整体限定托板支柱(56)的位置,并通过浆固粘结体(58)将浆固螺栓(53)与螺栓连接孔(54)连接牢固。
56.在本方案的具体实施例中,施工中所用到的各种元件可选用的具体尺寸和结构如下描述:
57.结构柱(1)采用强度等级为c35的混凝土材料浇筑,横断面尺寸为400
×
400mm。
58.下部结构层(2)采用强度等级为c25的素混凝土层。
59.导梁抱箍(3)包括两块围合成闭合圆形的弧形钢板,采用厚度2mm的钢板轧制而成。
60.施工导梁(4)采用厚度10mm的钢板轧制而成,宽度为20cm、高度为10cm。
61.导梁滑槽(5)横断面呈“t”形,槽口宽2cm。
62.第一滑块(6)、第二滑块(25)和第三滑块(35)均采用钢板轧制而成,,横断面呈“t”形,宽度为15cm。
63.第一横板(7)采用厚度为2mm的钢板轧制而成,上表面与同一横向位置的2个第一滑块(6)焊接连接,在第一横板(7)上预设供回收管口(10)穿设的孔洞。回收管口(10)直径为100mm。
64.回收抽管(8)采用直径60mm的钢管切割而成,与外部真空泵连通;压水管(9)采用直径50mm的钢管,与外部压水泵连通。
65.喷水头(11)采用高压水喷头。
66.第一拉索(12)、第二拉索(33)和第三拉索(43)均采用直径20mm的钢丝绳。
67.弹性连板(13)横断面呈“l”形,采用厚度2mm的橡胶板切割而成,与第一横板(7)之间设置弹性控位筋(64)。弹性控位筋(64)采用直径10mm的弹簧轧制而成。
68.密闭帘布(14)采用厚度1mm的橡胶片切割而成。
69.柔性端模(19)采用密目网,与撑架横筋(16)焊接连接。
70.模板撑架(18)包括撑架横筋(16)和撑架竖筋(17),均采用厚度为10mm、宽度为5cm的钢板。
71.滑移套箍(15)采用厚度为10mm的钢板轧制而成,套设于施工导梁(4)上,在滑移套箍(15)上预设与紧固螺栓(65)连接的螺孔。紧固螺栓(65)采用直径为30mm的螺杆轧制而成。
72.撑架角筋(20)采用厚度为10mm的钢板轧制而成。
73.模板撑杆(21)包括直径30mm螺杆和螺母,并使螺母两侧螺杆的紧固方向相反,使螺杆与撑杆转动铰(22)焊接连接;撑杆转动铰(22)采用直径30mm的球铰。
74.上部结构层(23)采用强度等级为c35mm的钢筋混凝土材料,厚度为20cm。
75.余浆回收槽(24)采用厚度为1mm的钢板轧制而成,深度为0.1m、宽度为0.2m。
76.第二横板(26)采用厚度为10mm的钢板轧制而成。
77.滚轮调节栓(28)和连板调节栓(27)均包括直径30mm的螺杆和螺母,并使螺母两侧螺杆的紧固方向相反。
78.条板连板(29)采用厚度为10mm的钢板轧制。
79.滚轮连轴(30)采用直径为30mm的轴承。
80.弹性滚轮(32)采用轮胎压力为0.3mpa的橡胶滚轮。
81.刻槽条板(31)采用厚度为10mm钢板轧制而成,高度为20mm,横断面呈直角梯形,与条板连板(29)焊接连接。
82.板顶连槽(34)深度为20mm、宽度为10mm。
83.料槽连板(36)采用厚度为10mm的钢板轧制而成。
84.纤维供料槽(37)横截面呈矩形,采用厚度为2mm的钢板轧制而成,高度为10cm、宽
度为20cm、长度为2m。
85.纤维撒布层(44)采用钢纤维,厚度为2mm。
86.过料槽(38)采用采用厚度为1mm的钢板轧制而成,高度为5cm、宽度为40cm、长度为2m;在过料槽(38)的底板上设置横断面呈倒梯形的排料口(41)。排料口(41)直径为60mm。
87.料槽连筋(39)采用直径10mm的弹簧轧制而成。
88.振动器(40)采用额定功率为220v的表面振动器。
89.纤维刷板(42)采用厚度为2mm的橡胶片切割而成。
90.纤维硬化层(45)为纤维撒布层(44)与上部结构层(23)混合而成。
91.插板连箍(46)采用厚度10mm的钢板轧制而成。
92.连箍固定栓(47)采用直径30mm的螺杆轧制而成。
93.插板加压体(48)采用液压千斤顶。
94.导槽控位栓(49)包括直径30mm的螺杆和螺母,并使螺母两侧螺杆的紧固方向相反,与插板连箍(46)和导槽角筋(66)通过控位栓转铰(67)连接。控位栓转铰(67)采用直径30mm的球铰。
95.导槽侧板(50)采用厚度为10mm的钢板轧制而成,高度为20cm。
96.留缝插板(51)采用厚度10mm的钢板轧制而成,高度为50cm,在留缝插板(51)上预设供结构层钢筋(68)穿过的钢筋插设槽(69)。结构层钢筋(68)采用直径20mm的螺纹钢筋。钢筋插设槽(69)宽15mm,高150mm。
97.板顶连接槽(52)采用厚度为10mm的钢板轧制而成,槽深为5cm。
98.浆固螺栓(53)采用直径为32mm的螺纹钢筋。
99.螺栓连接孔(54)直径为50mm,深度为10cm。
100.立柱底板(55)采用厚度为2mm的钢板轧制而成,宽度为10cm。
101.托板支柱(56)采用规格为150
×
150
×7×
10的h型钢切割而成,高度为5cm。
102.支撑托板(57)采用厚度为10mm的钢板轧制而成。
103.浆固粘结体(58)采用强度等级为c35的灌浆料。
104.支撑桁梁(59)采用横断面尺寸为5cm
×
10cm的方钢管,在支撑桁梁(59)的两侧设置桁梁耳板(61),并在桁梁耳板(61)上预设供托板紧固栓(60)连接的孔洞。
105.托板紧固栓(60)采用直径为20mm的螺栓。
106.桁梁耳板(61)采用厚度为1cm的钢板切割而成,高度为1cm,与支撑桁梁(59)垂直焊接连接。
107.定位槽板(62)采用厚度为10mm的钢板轧制而成。
108.装饰板(63)采用大理石板,平面尺寸为50cm
×
50cm,厚度为20mm。
109.导槽角筋(66)采用10mm的钢板轧制而成。
110.本发明不局限于上述最佳实施方式,任何人在本发明的启示下都可得出其他各种形式的产品,但不论在其形状或结构上作任何变化,凡是具有与本技术相同或相近似的技术方案,均落在本发明的保护范围之内。