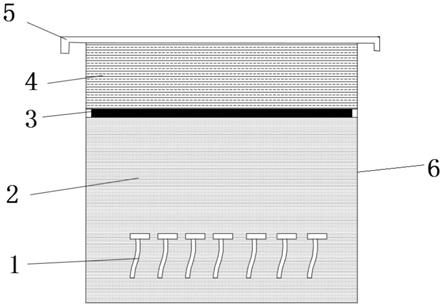
1.本发明属于航空发动机叶片的表面加工技术领域,特别地,涉及一种航空发动机钢制叶片低温渗铝的装包方法。
背景技术:
2.为了使钢制叶片具有更好的抗高温氧化及抗高温气流腐蚀性能,从而提升其工作寿命,往往需要对叶片表面进行低温渗铝。在低温渗铝过程中,由于铝粉渗剂具有较强的活性且渗铝温度接近铝粉渗剂燃点550℃,极易造成铝粉在渗铝过程中发生燃烧甚至爆炸,给生产带来很大的安全隐患及质量隐患。
3.中国人民解放军第5719工厂公开的发明专利:航空发动机钢制叶片低温渗铝工艺,cn1105789c,2003-04-16中提供了一种航空发动机钢制叶片低温渗铝工艺,该工艺采用氩气保护以防止铝粉在低温渗铝过程发生燃烧。该工艺方法虽然通过氩气保护的方式解决了铝粉在低温渗铝过程中发生的燃烧(爆炸)问题,但是长达十多个小时甚至二十多个小时的氩气保护过程无形中增加了许多氩气成本,最为关键的是,该渗铝工艺过程中由于需要往炉子内充氩气及排气,故对渗铝炉提出更高的要求,同时该工艺中叶片装入渗包后其渗剂未充分振实排出空气故其渗铝层致密性欠佳,从而使渗层的抗高温气流腐蚀及抗高温氧化能力有所下降,降低了叶片渗铝的效果。
4.为了解决低温渗铝过程中可能会出现的燃烧(爆炸)问题,现有技术要么是改进渗剂的配方(在纯铝粉中加入其它阻燃剂),要么是通入惰性气体进行保护,但是这两种方式的效果经过实践验证都不如预期,前者会导致渗剂中的含铝量降低,并影响了铝的扩散,后者增加了渗铝时间和渗铝设备的进排气、密封性要求等。
技术实现要素:
5.为解决上述技术问题,本发明旨在提供一种航空发动机钢制叶片低温渗铝的装包方法,可以实现叶片在无氩气保护的条件下或者未加入阻燃剂的情况下,确保其低温渗铝过程中铝粉不会发生燃烧甚至爆炸,同时降低对渗铝设备的要求,选用一般的空气炉即可满足低温渗铝工艺过程,进一步,在保证渗铝层满足渗层深度要求的同时其致密性更好。
6.为实现上述目的,本发明采用了下述技术方案:
7.一种航空发动机钢制叶片低温渗铝的装包方法,包括,
8.将叶片装入渗包,然后向渗包内填充渗剂,采用振动的方式处理渗包,直到渗包内渗剂的自由表面高度不再下降,其中,叶片装入渗包时,叶片距离渗包底部有一段距离,向渗包内填充渗剂时,渗剂的自由表面没过叶片一段距离。
9.优选的,所述叶片距离渗包底部的距离大于等于1cm,所述渗剂的自由表面没过叶片的距离大于等于5cm。
10.进一步,当渗包内渗剂的自由表面高度不再下降时,渗剂的自由表面仍然没过叶片一段距离。
11.作为一种选择,所述振动方式为将装有叶片和渗剂的渗包放置在振荡机上振实。
12.进一步,将装有叶片和渗剂的渗包沿着上、下方向往复振实。
13.优选的,振实方向为上、下震动,振实温度在常温下进行,当采用振荡机时,振荡电机功率0.5kw~3kw,振幅2cm~10cm。
14.作为一种选择,航空发动机钢制叶片低温渗铝的装包方法还包括,
15.当渗剂的自由表面高度不再下降时,在渗剂自由表面上方放置金属材质的隔板。
16.作为一种选择,所述隔板的面积完全覆盖渗剂的自由表面。
17.作为一种选择,航空发动机钢制叶片低温渗铝的装包方法还包括,
18.在隔板的上表面继续填充惰性粉末,且此时不再对装有叶片、渗剂、隔板和惰性粉末的渗包整体进行振动处理,所述惰性粉末为渗铝温度下呈惰性的粉末,不会在渗铝温度下与渗剂发生反应,惰性粉末的密度比铝粉的密度高,一般取惰性粉末的密度为铝粉密度的1.5倍及以上。
19.进一步,当所述惰性粉末的自由表面与渗包的上端面基本平齐,然后盖上渗包的盖板完成装包。惰性粉末的自由表面是指在隔板上填充惰性粉末时,最上方的惰性粉末表面。
20.优选的,所述隔板为45#钢,所述惰性粉末为al2o3粉末。
21.进一步,所述隔板外周向与渗包之间有间隙,该间隙作为装配间隙,一般取单边2~10mm左右,目的是为了防止渗铝入炉后隔板因为热处理变形导致卡在渗包内无法取出或者取出困难。
22.本发明的主要构思是:在低温渗铝过程,叶片及渗剂装入渗包后通过不断压实铝粉来排出铝粉间隙中的空气以使铝粉缺乏燃烧(爆炸)的条件,在压实铝粉后铺上一块一定厚度的耐高温金属隔板,并在金属隔板上再铺上一层密度较高(密度比铝粉或空气高)的耐高温细金属粉末或陶瓷粉末(该粉末在渗铝温度下呈惰性,不会与渗剂发生反应)。操作步骤为:叶片装包
→
填充渗剂
→
振实渗剂
→
放置金属隔板
→
填充惰性粉末或陶瓷粉末并盖上盖板
→
平缓入炉。
23.本发明通过排出渗剂中的空气后,铝粉就已缺乏燃烧条件故不再需要氩气或阻燃剂保护,而铺上金属隔板及耐高温金属粉末是防止渗铝过程中渗剂的化学反应作用使其发生松动,随后空气通过松动的间隙回流至渗剂中;同时按本发明实施的装包方法在渗铝过程不需氩气或阻燃剂保护后对相应的渗铝炉或渗剂也降低了要求;通过压实的铝粉渗剂在渗铝过程与叶片紧密接触,其深层致密性将得到提高。
24.本发明的航空发动机钢制叶片低温渗铝的装包方法,在低温渗铝前,叶片及渗剂装入渗包后通过不断压实铝粉来排出铝粉间隙中的空气以使铝粉达不到燃烧(爆炸)的条件,在压实铝粉后铺上一块一定厚度的耐高温金属板,并在金属板上再铺上一层密度较高(密度比空气高)的耐高温细金属粉末或陶瓷粉末(该粉末渗铝温度下呈惰性,不会与渗剂发生反应)。
25.需要指出的是,本发明既不是改进渗剂的配方(加入阻燃剂),也不是改进渗铝的方法,而是改进渗铝前的叶片装包(渗包)方法,是另一种解决低温渗铝过程中铝粉燃烧或爆炸的技术途径。
26.与现有技术相比,本发明在叶片和渗剂装入渗包后通过振动压实排出渗剂间隙中
的空气,并在渗剂最上面加入金属隔板及惰性粉末,可使低温渗铝过程热涨及发生化学反应产生并排出气体的渗剂在发生瞬间松动时能在金属隔板及惰性粉末的重力作用下被瞬间压实(例如渗剂中的催化剂氯化铵会产生氯化氢气体,又如渗铝过程中产生的氢气,渗铝过程中会发生多个化学反应,部分反应的气体会通过渗剂间隙往上排出,而在渗剂最上层铺有金属隔板和密度比渗剂密度大得多的惰性粉末后,气体通过间隙排出的瞬间就会被金属隔板和惰性粉末的自重向下压实,从而阻止间隙的产生),使空气不能回流进入渗剂中,从而保证渗铝过程中铝粉达不到燃烧的条件,故渗铝过程不再需要氩气或阻燃剂进行保护。在渗铝过程不需氩气保护后,炉子的密封性及保护气体装置将不需更高的要求,故一般的空气炉即可实现低温渗铝工艺。通过压实的致密渗剂与叶片叶身紧密接触将使其渗铝层在满足渗层深度要求的同时更致密,抗高温氧化及抗高温气流腐蚀效果更佳。
27.目前,采用普通的中温箱式炉按照本发明中的装包方法实施低温渗铝,已经实现航空发动机钢制叶片的低温渗铝工艺大批量化生产,渗铝后的叶片渗层深度均匀,渗铝层形貌明显易见,渗层中al含量高。
附图说明
28.图1为本发明中装包后渗包的示意图;
29.图中,1.叶片、2.渗剂、3.隔板、4.惰性粉末、5.盖板、6.渗包。
具体实施方式
30.下面结合附图和具体实施例对本发明作进一步的说明,但不应就此理解为本发明所述主题的范围仅限于以下的实施例,在不脱离本发明上述技术思想情况下,凡根据本领域普通技术知识和惯用手段做出的各种修改、替换和变更,均包括在本发明的范围内。
31.下面结合附图1对本发明的具体实施例进行详细阐述,以使本发明的优点和特征能更易于被本领域技术人员理解,从而对本发明的保护范围作出更清楚明确的界定。
32.航空发动机钢制叶片低温渗铝的装包方法实施按如下步骤操作:
33.一、将叶片1或将叶片1及夹具放入渗包6(需要说明的是,渗包6是指用于渗铝的包装容器)中,叶片1离渗包6底部有一定距离,一般取该距离≥1cm(当用夹具时靠夹具来保证);
34.二、往渗包6中填充渗剂2,使渗剂2没过叶片1一定距离,一般取该距离≥5cm;
35.三、将渗剂2振实从而排出渗剂2间隙中的空气。将渗包6放到振实设备(如振荡机)上按照上、下方向振实渗剂2,渗剂2最高界面(自由表面)不再降低为止,填充并振实的渗剂2没过叶片1及夹具,并高出一定距离,一般取该距离≥5cm;
36.四、在最上层(自由表面)渗剂2上平放金属隔板3(如45#钢板)。此金属隔板3有一定厚度,一般取厚度δ≥3mm,且有一定重量,使渗包6在转运过程渗剂2中铝粉不漂浮乱飞。
37.五、在金属隔板3上填充一定厚度的惰性粉末4(如al2o3),一般取惰性粉末堆积厚度≥2cm,惰性粉末4可以先振实再填充,也可以直接填充,惰性粉末4的堆积高度与渗包6高度(即渗包6上端的开口处)基本平齐(此时不再对装有叶片1、渗剂2、隔板3和惰性粉末4的渗包6整体进行振实处理),并盖上渗包6的盖板5。金属隔板3和惰性粉末4的组合隔绝了空气,特别是阻断了渗铝过程中空气回流进入渗剂2中铝粉间隙内的通道,使得铝粉达不到燃
烧或爆炸的条件。
38.六、将渗包6平缓入炉进行低温渗铝,即升温、保温及后续的出炉冷却等过程。入炉过程中渗包6不能发生大幅振动、晃动或者高低不平的吊动,目的是为了防止渗剂2及惰性粉末4发生较大倾斜从而使空气漏入其中。
39.本发明的装包方法在排出渗剂2中可能存在的空气后,叶片渗铝层的致密性和均匀性都得到了提高。