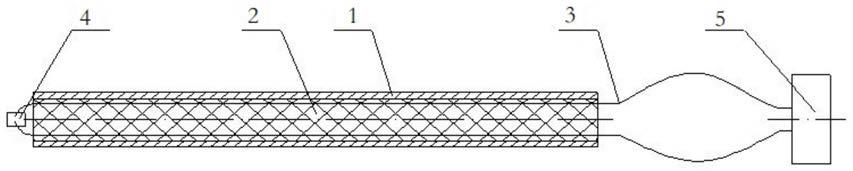
1.本发明涉及轻合金铸造技术领域,尤其涉及一种轻合金铸造内嵌管路组件及其制备方法和带内嵌管路的轻合金件的铸造方法。
背景技术:
2.由于工艺要求,铸造管路在轻合金铸件中的应用越来越多,形状也越来越复杂。现有的含管路铸件的铸造生产中,管路成型工艺一般分为砂芯成型、金属管路嵌铸后再腐蚀成型和直接嵌铸成型等多种成型方式。对于管路直接嵌铸成型,为保证金属管路与铸件之间的结合力,防止出现不同金属之间的界面分离,必须保证在浇注过程中金属管路有足够高的温度。所以,浇注前或浇注过程中必须对金属管路进行加热处理。
3.一般来说,管路加热工艺分为组型后金属管路与铸型共同加热、金属管路单独加热后再组型和组型后金属管路单独加热等方式。但组型后金属管路与铸型共同加热和金属管路单独加热后再组型既无法满足金属管路足够高温度的要求也无法实现对温度的精确控制。而现阶段采用的管路单独电流加热技术实现管路温度控制的整个过程需人手工操作,难以保证管路温度的均匀性和管路温度的控制精确,且存在较大的安全隐患。
技术实现要素:
4.鉴于上述的分析,本发明实施例旨在提供一种轻合金铸造内嵌管路组件及其制备方法和带内嵌管路的轻合金件的铸造方法,用以解决现有铸造过程中管路加热操作的安全性差和不能精确控制管路温度的问题。
5.一方面,本发明实施例提供了一种轻合金铸造内嵌管路组件,该轻合金铸造内嵌管路组件包括金属管路以及设置在所述金属管路内的保温绝缘件、加热元件和过载保护元件;
6.所述加热元件通过保温绝缘件固定在金属管路中;所述过载保护元件设置在加热元件的加热电路中,当加热温度达到所需温度时,过载保护元件工作,加热元件停止加热。
7.基于上述轻合金铸造内嵌管路组件的进一步改进,所述加热元件为电阻丝,所述电阻丝的数量为两根以上,所述电阻丝贯穿所述金属管路;
8.所述过载保护元件为金属块,所述金属块熔化后电阻丝断电,停止加热;
9.所述保温绝缘件为石膏芯,所述电阻丝镶嵌固定在石膏芯中,所述石膏芯填充在金属管路中,并将电阻丝间隔开。
10.优选地,所述电阻丝的数量为2根,所述电阻丝的两端均超出所述金属管路的两端至少20mm。
11.优选地,所述电阻丝的一端与金属块连接,另一端跟调压器连接。
12.优选地,所述金属块为铝块。
13.优选地,所述金属管路为不锈钢管。
14.另一方面,本发明实施例提供了一种本发明的轻合金铸造内嵌管路组件的制备方法,该制备方法包括:
15.a.将至少两根电阻丝贯穿入金属管路,整个过程保证电阻丝的分开并且电阻丝与金属管路不接触;
16.b.将石膏浆灌入金属管路中,待石膏浆凝固形成石膏芯后,对其进行加热并保温,待石膏芯中结晶水完全挥发后进行干燥处理;
17.c.将电阻丝通过金属块连接,使得金属块熔化后电阻丝断电,连接时每根电阻丝之间不得接触,电阻丝还跟调压器连接。
18.基于上述方法的进一步改进,步骤b中,所述加热的温度为 350-400℃,所述保温的时间为4-5h。
19.再一方面,本发明实施例提供了一种带内嵌管路的轻合金件的铸造方法,采用本发明的轻合金铸造内嵌管路组件,该铸造方法包括:
20.步骤1:在铸型组型时,将轻合金铸造内嵌管路组件置于铸型中;
21.步骤2:组型完成后,将电阻丝与电源接通进行加热;
22.步骤3:通过调压器控制电阻丝的两端电压,待金属块熔化后,进行铸件浇注;
23.步骤4:浇注完成后,除砂以及除去金属管路中的石膏芯和电阻丝,完成带内嵌管路的轻合金件的铸造。
24.优选地,步骤2中,所述电源为交流电源或直流电源。
25.与现有技术相比,本发明至少可实现如下有益效果之一:
26.(1)本发明的轻合金铸造内嵌管路组件设置了加热元件(如电阻丝)、绝缘保温件(如石膏芯)和过载保护元件(如金属块),基于电阻发热原理,当电阻丝接通电源时,电阻丝温度会不断升高,当电阻丝温度达到金属块的熔点时(例如铝的熔点660℃),金属块发生熔化,电阻丝断电,实现加热过程自动过载保护和温度的精确控制。
27.(2)金属块熔化后,内嵌金属管路温度达到金属块熔点附近温度(例如550-650℃),且由于石膏芯的保温作用,金属管路的温度可保持在熔点附近温度120-180s,避免在铸件凝固过程中因金属管路冷却速度与铸件冷却速度不一致而出现的金属管路与铸件本体分离的现象,有效提高了金属管路与铸件的结合力和结合的稳定性,从而保证制备较高整体性能的轻合金铸件。
28.(3)本发明可以根据实际铸件铸造过程中所需的温度选择相应熔点的金属块,电阻丝断电后,金属管路的温度仍可以保持在铸造温度左右,从而实现温度的精确控制以及保证铸件性能。
29.(4)本发明采用电流加热技术对金属管路进行间接加热,能够实现管路的快速加热,但整个过程无需人手工操作,消除了安全隐患。通过将电阻丝贯穿设置在需内嵌的金属管路组件中,结合石膏芯的保温作用,可以提高管路加热的均匀性,保证成型质量。
30.本发明中,上述各技术方案之间还可以相互组合,以实现更多的优选组合方案。本发明的其他特征和优点将在随后的说明书中阐述,并且,部分优点可从说明书中变得显而易见,或者通过实施本发明而了解。本发明的目的和其他优点可通过说明书以及附图中所特别指出的内容中来实现和获得。
附图说明
31.附图仅用于示出具体实施例的目的,而并不认为是对本发明的限制,在整个附图中,相同的参考符号表示相同的部件。
32.图1为本发明的轻合金铸造内嵌管路组件。
33.附图标记:
34.1-金属管路;2-石膏芯;3-电阻丝;4-金属块;5-调压器。
具体实施方式
35.下面结合附图来具体描述本发明的优选实施例,其中,附图构成本技术一部分,并与本发明的实施例一起用于阐释本发明的原理,并非用于限定本发明的范围。
36.现有的铸造生产中,管路成型工艺一般分为砂芯成型、金属管路嵌铸后再腐蚀成型和直接嵌铸成型等多种成型方式。对于管路直接嵌铸成型,为保证金属管路与铸件之间的结合力,防止出现不同金属之间的界面分离,必须保证在浇注过程中金属管路有足够高的温度。所以,浇注前或浇注过程中必须对金属管路进行加热处理。
37.管路加热工艺分为组型后金属管路与铸型共同加热、金属管路单独加热后再组型和组型后金属管路单独加热等方式,若组型后金属管路与砂型共同加热,加热温度不能超过200℃,否则砂型强度会消失;若金属管路加热后再组型,则较高的加热温度会导致组型工作无法进行,且管路加热后至最终浇注时间间隔较长,导致管路加热效果消失;组型后金属管路再单独加热技术则在砂型铸造中优势非常明显,可在浇注前短时实现较高温度。
38.在组型后金属管路再单独加热工艺中,如果采用直接将金属管路连接电源进行电流加热,需要通过控制加热时间来间接实现对管路加热温度的估算,由于通电时间仅5-10s,不仅对操作速度有较高要求,还无法实现对管路温度的精确控制,导致每次加热温度不一致,无法保证工艺的稳定性;此外,采用对金属管路直接进行电流加热技术时,要实现管路的快速加热,管路自身需要在短时间内通过较大电流,且整个过程需人手工操作,否则无法进行下一铸件管路的加热和浇注,因而具有较大的安全隐患;另外,由于管路在有电流通过时会在表面出现“集肤”效应,且由于管路材质的不均匀或形状变化等情况,也会导致管路温度的不均匀性。
39.针对上述技术问题,一方面,本发明提供了一种轻合金铸造内嵌管路组件,如图1所示,该轻合金铸造内嵌管路组件包括金属管路1以及设置在所述金属管路1内的保温绝缘件、加热元件和过载保护元件;
40.所述加热元件通过保温绝缘件固定在金属管路1中;所述过载保护元件设置在加热元件的加热电路中,当加热温度达到所需温度时,过载保护元件工作,加热元件停止加热。
41.本发明的轻合金铸造内嵌管路组件在实施时,将轻合金铸造内嵌管路组件置于砂型中,组型完成后,对加热元件通电进行加热,同时将热量传递给金属管路,当达到一定温度后,过载保护元件工作使得加热元件停止加热,此时由于保温绝缘件的保温作用,金属管路的温度能够保持在铸造温度附近一段时间,精准控制铸造温度,并且整个过程安全、无需人工操作。
42.示例性地,如图1所示,所述加热元件为电阻丝3,所述电阻丝3的数量为两根以上,
所述电阻丝3贯穿所述金属管路1;
43.所述过载保护元件为金属块4,所述金属块4熔化后电阻丝3断电,停止加热;
44.所述保温绝缘件为石膏芯2,所述电阻丝镶嵌固定在石膏芯2中,所述石膏芯2填充在金属管路1中,并将电阻丝3间隔开。
45.本发明的轻合金铸造内嵌管路组件可以用于砂型铸型中,实施时,在组型时,将轻合金铸造内嵌管路组件置于砂型中,组型完成后,将电源与电阻丝3接通,电阻丝3通电后温度开始升高,加热金属管路1,当电阻丝3的温度达到金属块4的熔点时,金属块4开始熔化,连接电阻丝3的金属块4熔化后,电阻丝断开,从而自动断电,实现加热过程自动过载保护,此时,由于石膏芯2的保温作用,金属管路1的温度可以保持在金属块4的熔点附近时间长达120-180s,实现金属管路1温度的精确控制,从而提高金属管路1与铸件之间的结合力和结合的稳定性,并且整个操作过程安全可靠。
46.与现有技术相比,本发明的轻合金铸造内嵌管路组件可实现加热过程自动过载保护,安全性高,温度控制精确;并且,由于石膏芯2的保温作用,避免了在铸件凝固过程中因金属管路1的冷却速度与铸件的冷却速度不一致而出现的金属管路1与铸件本体分离的现象,有效提高了金属管路1与铸件的结合力和结合的稳定性,从而保证制备较高整体性能的轻合金铸件。
47.本发明中,对所述电阻丝的具体设置方式没有特别的限定,只要能够使得金属块4熔化后电阻丝3断电即可,例如,所述电阻丝3设置为并联或者串联。当电阻丝3设置为并联时,可以将每根电阻丝3的一端连接在同一个金属块4上,另一端外接电源;当电阻丝设置为串联时,可以将电阻丝3的首尾串联连接,并在其中两根电阻丝3之间设置金属块4。
48.在实际应用中,可以将多个轻合金铸造内嵌管路组件设置于砂型中,此时,可以将多个轻合金铸造内嵌管路组件中的电阻丝3串联,并在至少一个轻合金铸造内嵌管路组件中的电阻丝3的连接处设置金属块4,使得金属块4熔化后,整个电阻丝3断电。
49.本发明中,所述电阻丝3的数量可以根据金属管路1的内径大小进行选择,金属管路1的内径较大时可以选择较多条电阻丝3,以实现电阻丝3对金属管路1的加热效果。
50.考虑到轻合金铸造过程中的实际金属管路情况,优选地,所述电阻丝3的数量为2根;同时,考虑到电阻丝3的两端要设置金属块4以及连接电源,优选地,所述电阻丝3的两端均超出所述金属管路1的两端至少20mm。
51.当电阻丝3数量为2条时,2条所述电阻丝3的一端通过金属块4连接,同时,为了控制电阻丝3的电压大小,2条电阻丝3的另一端跟调压器5连接。通过调压器5控制电阻丝3两端电压大小,从而实现对电阻丝3中电流大小和电阻丝3加热速度的调节。
52.本发明中,所述金属块4的具体选择可以根据实际铸件铸造过程中所需的温度选择相应熔点的金属块,例如,所述金属块4可以为铝块、铅块或锡块。优选地,当用于铸造铝合金铸件时,所述金属块4为铝块。铝的熔点是660℃,电阻丝3断电后,金属管路1的温度仍可以保持 550-650℃,从而实现温度的精确控制以及保证铸件性能。
53.需要注意的是,在选择金属块4的材料时,金属块4的熔点不能高于电阻丝的熔点。
54.本发明中,所述电阻丝3为本领域的常规选择,只要电阻丝3的耐温性能能够满足铸件浇注温度即可,例如,所述电阻丝可以为cr15ni60、 cr20ni35或0cr27al7mo2。
55.本发明中,对所述金属管路1的选择没有特别的限定,可以为本领域的常规选择,
优选地,所述金属管路1为不锈钢管。
56.另一方面,本发明提供了一种本发明的轻合金铸造内嵌管路组件的制备方法,该制备方法包括:
57.a.将至少两根电阻丝3贯穿入金属管路1,整个过程保证电阻丝3的分开,并且电阻丝3与金属管路1不接触;
58.b.将石膏浆灌入金属管路1中,待石膏浆凝固形成石膏芯2后,对其进行加热并保温,待石膏芯2中结晶水完全挥发后进行干燥处理;
59.c.将电阻丝3通过金属块4连接,使得金属块4熔化后电阻丝3断电,连接时每根电阻丝3之间不得接触,电阻丝3还跟调压器5连接。
60.步骤b中,对将石膏浆灌入金属管路1中的具体操作方法没有特别的限定,只要能够使石膏凝固在金属管路1中,并且使得电阻丝3相互之间不接触、电阻丝3与金属管路1之间不接触即可。例如,可以在灌石膏之前,将金属管路1的一端封口,并将封口一端的电阻丝3穿过封口,将电阻丝3拉直使其相互之间不接触,并与金属管路1不接触,向金属管路1中灌入石膏浆,待石膏浆凝固后,将封口拆除。
61.步骤b中,所述加热的方式可以为本领域的常规选择,只要能够使石膏的结晶水挥发即可,优选地,所述加热的方式是将含有石膏芯2的轻合金铸造内嵌管路组件置于电阻炉中加热,进一步优选地,所述加热的温度为350-400℃,所述保温的时间为4-5h。通过加热后的保温过程,可以使石膏中的结晶水完全挥发。
62.步骤b中,所述干燥的方式可以为本领域的常规选择,例如,可以将含有石膏芯2的轻合金铸造内嵌管路组件置于干燥容器中进行干燥。
63.步骤c中,电阻丝3与金属块4之间的连接方式可以为本领域的常规方法,例如,可以通过焊接方式连接,连接时连接处的电阻丝3之间不能接触,仅能通过金属块4进行连接,以便金属块4熔化后电阻丝3 之间断开。
64.另一方面,本发明还提供了一种带内嵌管路的轻合金件的铸造方法,采用本发明的轻合金铸造内嵌管路组件,该轻合金铸造方法包括:
65.步骤1:在铸型组型时,将轻合金铸造内嵌管路组件置于铸型中;
66.步骤2:组型完成后,将电阻丝3与电源接通进行加热;
67.步骤3:通过调压器5控制电阻丝3的两端电压,待金属块4熔化后,进行铸件浇注;
68.步骤4:浇注完成后,除砂以及除去金属管路1中的石膏芯2和电阻丝3,完成带内嵌管路的轻合金件的铸造。
69.本发明中,步骤2中,所述电源为交流电源或直流电源。
70.步骤3中,所述调压器5控制电阻丝3的两端电压优选为220-380v。
71.步骤3中,考虑到金属块4熔化后,轻合金铸造内嵌管路组件的温度能保持120-180s,因此,在金属块4熔化后,要迅速进行铸件浇注并迅速完成浇注。
72.步骤4中,可以使用高压水枪除去金属管路1中的石膏芯2和电阻丝3。
73.下面,通过具体实施例进一步说明本发明的技术方案和技术效果。
74.以下实施例中,电阻丝为cr15ni60。
75.实施例1
76.制备轻合金铸造内嵌管路组件。
77.(1)将两根电阻丝穿入不锈钢管路中,整个过程保证电阻丝的分开,且两端均露出25mm长度,并且电阻丝与不锈钢管路不接触;
78.(2)将混合好的石膏浆灌入不锈钢管路中,待石膏浆凝固成石膏芯后置于电阻炉中加热,加热温度为350℃,保温5h,待石膏芯中的结晶水完全挥发后取出,并置于干燥器中干燥;
79.(3)将两根电阻丝的一端分别焊接在同一块铝块上,焊接时,两根电阻丝不接触,仅通过铝块连接,电阻丝的另一端与调压器连接。
80.实施例2
81.采用实施例1制备的轻合金铸造内嵌管路组件铸造带内嵌管路的铝合金铸件。采用砂型铸造。
82.(1)在砂型组型时,将轻合金铸造内嵌管路组件置于砂型中;
83.(2)砂型组型完成后,将电阻丝与电源接通;
84.(3)调节调压器至380v,对不锈钢管路进行加热,待不锈钢管路达到660℃时,铝块开始熔化,熔化后电阻丝断开连接,加热结束;
85.(4)加热结束后迅速完成浇注,铸件浇注完成后,除砂,使用高压水枪除去不锈钢管路中的石膏芯和电阻丝。
86.本实施例铸造的带内嵌管路的铝合金铸件中,不锈钢管路与铸件本体之间没有发生分离。
87.实施例3
88.制备轻合金铸造内嵌管路组件。
89.(1)将两根电阻丝穿入不锈钢管路中,整个过程保证电阻丝的分开,且两端均露出21mm长度,并且电阻丝与不锈钢管路不接触;
90.(2)将混合好的石膏浆灌入不锈钢管路中,待石膏浆凝固成石膏芯后置于电阻炉中加热,加热温度为400℃,保温4h,待石膏芯中的结晶水完全挥发后取出,并置于干燥器中干燥;
91.(3)将两根电阻丝的一端分别焊接在同一块铝块上,焊接时,两根电阻丝不接触,仅通过铝块连接,电阻丝的另一端与调压器连接。
92.实施例4
93.采用实施例3制备的轻合金铸造内嵌管路组件铸造带内嵌管路的铝合金铸件。采用砂型铸造。
94.(1)在砂型组型时,将轻合金铸造内嵌管路组件置于砂型中;
95.(2)砂型组型完成后,将电阻丝与电源接通;
96.(3)调节调压器至300v,对不锈钢管路进行加热,待不锈钢管路达到660℃时,铝块开始熔化,熔化后电阻丝断开连接,加热结束;
97.(4)加热结束后迅速完成浇注,铸件浇注完成后,除砂,使用高压水枪除去不锈钢管路中的石膏芯和电阻丝。
98.本实施例铸造的带内嵌管路的铝合金铸件中,不锈钢管路与铸件本体之间没有发生分离。
99.实施例5
100.制备轻合金铸造内嵌管路组件。
101.(1)将两根电阻丝穿入不锈钢管路中,整个过程保证电阻丝的分开,且两端均露出30mm长度,并且电阻丝与不锈钢管路不接触;
102.(2)将混合好的石膏浆灌入不锈钢管路中,待石膏浆凝固成石膏芯后置于电阻炉中加热,加热温度为380℃,保温4h,待石膏芯中的结晶水完全挥发后取出,并置于干燥器中干燥;
103.(3)将两根电阻丝的一端分别焊接在同一块铅块上,焊接时,两根电阻丝不接触,仅通过铅块连接,电阻丝的另一端与调压器连接。
104.实施例6
105.采用实施例5制备的轻合金铸造内嵌管路组件铸造带内嵌管路的铝合金铸件。采用砂型铸造。
106.(1)在砂型组型时,将轻合金铸造内嵌管路组件置于砂型中;
107.(2)砂型组型完成后,将电阻丝与电源接通;
108.(3)调节调压器至260v,对不锈钢管路进行加热,待不锈钢管路达到327℃时,铅块开始熔化,熔化后电阻丝断开连接,加热结束;
109.(4)加热结束后迅速完成浇注,铸件浇注完成后,除砂,使用高压水枪除去不锈钢管路中的石膏芯和电阻丝。
110.本实施例铸造的内嵌管路的铝合金铸件中,不锈钢管路与铸件本体之间没有发生分离。
111.实施例7
112.按照实施例1的方法制备轻合金铸造内嵌管路组件,不同的是,不锈钢管路中设置3根电阻丝,且3根电阻丝并联,即将三根电阻丝的一端分别焊接在同一块铝块上,焊接时,三根电阻丝之间互相不接触,仅通过铝块连接,电阻丝的另一端与调压器连接。
113.实施例8
114.按照实施例1的方法铸造带内嵌管路的铝合金铸件,不同的是,采用的是实施例7制备的轻合金铸造内嵌管路组件。
115.本实施例铸造的带内嵌管路的铝合金铸件中,不锈钢管路与铸件本体之间没有发生分离。
116.对比例1
117.采用不锈钢管路铸造带内嵌管路的铝合金铸件。采用砂型铸造。
118.(1)在砂型组型时,将不锈钢管路置于砂型中;
119.(2)砂型组型完成后,将不锈钢管路与电源接通,对不锈钢管路进行加热,通电10s后断电,结束加热;
120.(3)加热结束后浇注。
121.对比例1铸造的带内嵌管路的铝合金铸件中,不锈钢管路与铸件本体之间发生了分离。
122.以上所述,仅为本发明较佳的具体实施方式,但本发明的保护范围并不局限于此,任何熟悉本技术领域的技术人员在本发明揭露的技术范围内,可轻易想到的变化或替换,都应涵盖在本发明的保护范围之内。