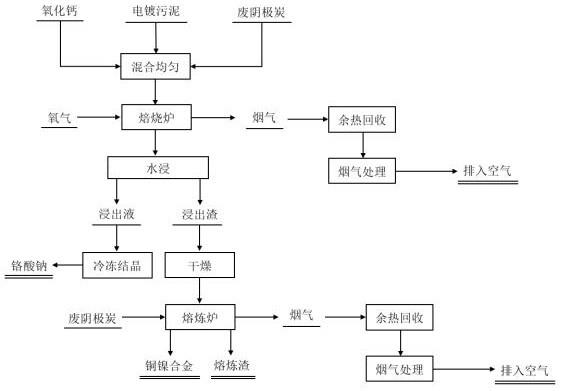
1.本发明涉及工业危废资源化处置技术领域,具体涉及一种以废阴极炭为添加剂氧化-还原两步法回收电镀污泥内铜、镍、铬的方法。
2.
背景技术:
3.电镀污泥是电镀行业中重金属沉淀而产生的固体废物,因其重金属含量高,故被列为危险废物。污泥中含有多种金属如铜、镍、铬、铁、锌等,并以氢氧化物的形式存在,同时还包括一些有机组分和复杂的金属氧化物。在中国,每年会产生超过1000万吨电镀污泥,如果不进行正确及时的处置,重金属会迁移至环境中,污染土壤和地下水,影响动植物的生存,甚至威胁到人类的生命健康。现有的处理方法主要包括固化稳定化、中温钠化氧化、酸碱浸出等。固化稳定化即通过水泥、石灰和粉煤灰对电镀污泥进行固化后填埋,但该方法会释放有毒物质到环境中产生二次污染,也会造成金属资源的浪费。中温钠化氧化通过将电镀污泥和碳酸钠按一定比例混合焙烧,使三价铬氧化成六价铬,即生成铬酸钠,铝、锌生成相应的氧化物,再通过水浸使铬、铝、锌溶于液体生成各自的盐,再对滤液水解酸化实现铬与锌、铝的分离,从而实现铬的回收,该方法为电镀污泥中金属铬的回收提供了新思路,但过程中碳酸钠添加量过多,工艺成本高。酸碱浸出即利用电镀污泥中不同金属化合物和酸碱的化学反应实现金属的浸出分离,但此方法选择性较差,并会产生大量废液。
4.废阴极炭是电解制铝过程中产生的一种危险固体废物,主要由石墨碳、氟化物(naf、na3alf6、caf2等)、氰化物(nacn、na3fe(cn)6等)和其他无机化合物组成。中国每年会产生约36万吨废阴极炭,平均没生产一吨铝,会产生10千克废阴极炭,随着电解铝行业的不断发展,废阴极炭产生量也呈现不断上升的趋势。因其含有氟化物和氰化物,若处理不当,也会对环境产生巨大的危害。但由于其碳质资源丰富,故具有很高的回收价值。目前,有超过50%的废阴极炭填埋处置,操作简单、成本低,但浪费了大量碳质资源,并造成土壤和地下水的污染。故一些学者从物质本身的性质出发,研究了大量物化法、湿法及火法处理工艺,如浮选利用碳和氟化物表面润湿性的差异实现其物理分离、高温燃烧利用废阴极炭中碳质材料的高热值实现氟化物的转化和氰化物的降解。但这些方法回收的产品纯度较低,或能耗高、浪费了大量的资源,即实现了无害化转化但没有最大程度地实现资源化回收。湿法中的酸浸和碱浸虽然能够实现较高纯度的回收,但选择性较差,过程中产生的废液的处理也是较为严重的问题。
5.
技术实现要素:
6.针对上述存在的问题,本发明提供一种以废阴极炭为添加剂氧化-还原两步法回收电镀污泥内铜、镍、铬的方法。本发明以废阴极炭为添加剂,通过氧化、还原两步法进行电
镀污泥中铬、铜、镍的分步提取和有效回收,并废阴极碳中氰化物完全分解实现无害化处置,氟以氟化钙形式稳定存在于熔炼渣相中。方法实现了以废治废,并同时具备流程短、成本低等优点,推广应用前景良好。本发明通过以下技术方案实现。
7.一种以废阴极炭为添加剂氧化-还原两步法回收电镀污泥内铜、镍、铬的方法,其具体步骤如下:(1)首先将电镀污泥、废阴极炭和氧化钙按照一定比例混合均匀,废阴极炭的添加量为废阴极碳:电镀污泥=1:0.5-2.5,氧化钙添加量为氧化钙:电镀污泥=0.09-0.2:1;(2)将混合物送入焙烧炉进行焙烧,过程中控制焙烧温度、焙烧时间、通氧量等参数,完成铬的定向转化和氟的初步固定,焙烧温度为400-800℃,焙烧时间为1-3h,通氧量为阴极碳完全燃烧所需氧量的1.5-3.5倍;(3)对焙烧渣进行水浸,控制水浸温度、时间和水固比,实现铬酸钠的浸出分离,水浸温度为20-50℃,水浸时间为30-100min,水固比为(3-7):1;(4)浸出液冷冻结晶后得到铬酸钠产品,浸出渣干燥后转移至熔炼炉中,以废阴极炭为还原剂对其进行高温熔融还原,过程中控制造渣剂加入量、熔融还原温度和时间,铜、镍物相充分还原后以铜镍合金形式进行沉降富集,造渣剂二氧化硅添加量控制为cao/sio2比1:1-2,废阴极碳添加量为浸出渣质量的4-10%,熔融还原温度为1150℃-1300℃,熔融还原时间为1-3h;(5)还原过程完成后,铜镍合金由熔炼炉下部金属液出口排出,熔炼渣由出渣口排出,冶炼烟气经过余热回收和烟气处理达标后排入大气。
8.本发明的有益效果是:1、本发明的制备方法通过电镀污泥与废阴极碳耦合处置,废阴极碳中毒害组分氰化物可实现完全分解实现无害化处置,并氟以氟化钙形式稳定存在于熔炼渣相中;2、本发明的制备方法中电镀污泥中铬组分可定向转化为铬酸钠,并继而通过水浸实现高效分离回收,突破了传统工艺中铬大量分散和回收率低的问题;(3)本发明的制备方法以废制废,具备流程短、成本低等优点,推广应用前景良好。
9.附图说明
10.图1是本发明工艺流程图。
11.具体实施方式
12.下面结合附图和具体实施方式,对本发明作进一步说明。
13.实施例1采用某电镀厂的电镀污泥和某电解铝厂的废阴极炭进行耦合处理,电镀污泥中铜、镍、铬含量分别为6.51%、7.27%、4.22%,废阴极炭中碳含量为73.24%,氟含量为9.49%。将电镀污泥、废阴极炭和氧化钙按照质量比废阴极碳:电镀污泥=1:0.5、氧化钙:电镀污泥=0.1:1混合均匀后,送入焙烧炉进行焙烧,过程中控制焙烧温度600℃,焙烧时间2h,通氧量为阴极碳完全燃烧所需氧量的3倍,焙烧工艺结束后,对焙烧渣进行水浸,控制水浸温度30
℃,水浸时间90min,水固比为3:1;其后浸出液冷冻结晶后得到铬酸钠产品,浸出渣干燥后转移至熔炼炉中,以废阴极炭为还原剂对其进行高温熔融还原,过程中控制造渣剂二氧化硅添加量为cao/sio2比1:1,废阴极碳添加量为浸出渣质量的5%,熔融还原温度为1250℃,熔融还原时间为2h,还原过程完成后,铜镍合金由熔炼炉下部金属液出口排出,熔炼渣由出渣口排出,冶炼烟气经过余热回收和烟气处理达标后排入大气。处理完成后,经检测,弃渣中铜、镍、铬含量可分别降至0.55%、0.62%、0.33%,实现了电镀污泥中铜、镍、铬的高效回收,并废阴极碳中氟在其中封存效率达97%,国标法渣中氟的浸出毒性值为5mg/l,远低于氟的浸出毒性鉴别标准(100mg/l),国标法渣中氰的浸出毒性值为0.006mg/l,远低于氰的浸出毒性鉴别标准(5mg/l),本发明的制备方法实现了废阴极炭中氟和氰的无害化处置。
14.实施例2采用某电镀厂的电镀污泥和某电解铝厂的废阴极炭进行耦合处理,电镀污泥中铜、镍、铬含量分别为7.23%、5.66%、4.28%,废阴极炭中碳含量为74.18%,氟含量为8.49%。将电镀污泥、废阴极炭和氧化钙按照质量比废阴极碳:电镀污泥=1:0.8、氧化钙:电镀污泥=0.15:1混合均匀后,送入焙烧炉进行焙烧,过程中控制焙烧温度650℃,焙烧时间1.5h,通氧量为阴极碳完全燃烧所需氧量的2.5倍,焙烧工艺结束后,对焙烧渣进行水浸,控制水浸温度40℃,水浸时间80min,水固比4:1;其后对浸出液进行冷冻结晶得到铬酸钠产品,浸出渣干燥后转移至熔炼炉中,以废阴极炭为还原剂对其进行高温熔融还原,过程中控制造渣剂二氧化硅添加量为cao/sio2比1:1.5,废阴极碳添加量为浸出渣质量的7%,熔融还原温度为1180℃,熔融还原时间为2.5h,还原过程完成后,铜镍合金由熔炼炉下部金属液出口排出,熔炼渣由出渣口排出,冶炼烟气经过余热回收和烟气处理达标后排入大气。处理完成后,弃渣中铜、镍、铬含量可分别降至0.42%、0.72%、0.28%,实现了电镀污泥中铜、镍、铬的高效回收,并氟在其中封存效率达95%,国标法渣中氟的浸出毒性值为8mg/l,远低于氟的浸出毒性鉴别标准(100mg/l),国标法渣中氰的浸出毒性值为0.002mg/l,远低于氰的浸出毒性鉴别标准(5mg/l),本发明的制备方法实现了废阴极炭中氟和氰的无害化处置。
15.实施例3采用某电镀厂的电镀污泥和某电解铝厂的废阴极炭进行耦合处理,电镀污泥中铜、镍、铬含量分别为6.51%、7.27%和4.22%,废阴极炭中碳含量为71.78%,氟含量为9.43%。将电镀污泥、废阴极炭和氧化钙按照质量比废阴极碳:电镀污泥=1:1、氧化钙:电镀污泥=0.3:1混合均匀后,送入焙烧炉进行焙烧,过程中控制焙烧温度700℃,焙烧时间2h,通氧量为阴极碳完全燃烧所需氧量的3.5倍,焙烧工艺结束后,对焙烧渣进行水浸,控制水浸温度45℃,水浸时间90min,水固比3.5:1;其后对浸出液进行冷冻结晶得到铬酸钠产品,浸出渣干燥后转移至熔炼炉中,以废阴极炭为还原剂对其进行高温熔融还原,过程中控制造渣剂二氧化硅添加量为cao/sio2比1:2,废阴极碳添加量为浸出渣质量的8%,熔融还原温度为1300℃,熔融还原时间为3h,还原过程完成后,铜镍合金由熔炼炉下部金属液出口排出,熔炼渣由出渣口排出,冶炼烟气经过余热回收和烟气处理达标后排入大气。处理完成后,弃渣中铜、镍、铬含量可分别降至0.42%、0.33%、0.12%,实现了电镀污泥中铜、镍、铬的高效回收,并氟在其中封存效率达98%,国标法渣中氟的浸出毒性值为4mg/l,远低于氟的浸出毒性鉴别标准(100mg/l),国标法渣中氰的浸出毒性值为0.01mg/l,远低于氰的浸出毒性鉴别标准(5mg/l),本发明的制备方法实现了废阴极炭中氟和氰的无害化处置。