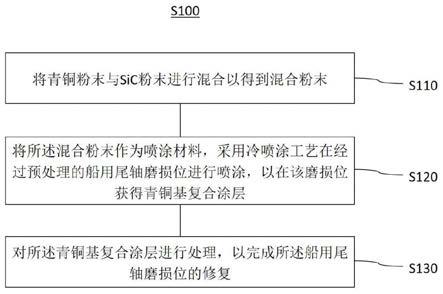
1.本发明属于表面工程技术中的增材制造技术领域,具体涉及一种船用尾轴磨损位修复方法与涂层。
背景技术:
2.船舶尾轴穿过尾轴管伸出船尾部末端安装螺旋桨传递动力,伸出船体尾部的尾轴可采用水作为润滑剂,而阻止船外水大量内漏入船体需要靠密封实现。水润滑尾轴大多为采用牛油盘根的密封方式,为了防止碳钢材质的尾轴被海、淡水腐蚀以及为了减少轴与轴承的摩擦磨损,在尾轴外部常采用热套的方法包覆一层青铜衬套。船舶尾轴在盘根密封处的青铜衬套常因为过度磨损而导致该处密封失效,造成船外水大量漏入船体内,增加船舶安全隐患。
3.目前船舶修、造企业几乎没有什么理想的措施来应对尾轴密封区域失效的问题;目前所能采用的技术措施有下述两类:第一、船舶修造企业将尾轴取出后经机床车削磨损段,然后需要加大填料装复。该方法需要铜套预留厚度有较大车削裕量且需要重新配填料压盖。第二、换新水封位青铜衬套,该方案需将填料位处整段青铜衬套经机床车削掉后换新青铜衬套,需要有相同规格的备用青铜衬套,否则要重新铸造。上述方案存在工序多、工期长、费用高等不利因素;而且采用上述修复方案,船舶尾轴仍大约每隔2年就需要对其水封位进行一次机床光车处理,每隔4-5年就需要换新一次青铜衬套,增加了船舶修理费用和船舶停航时间。
4.因此,需要寻找新的更简单、费用更低、更为耐用的磨损青铜衬套修复工艺来解决行业面临的共性技术问题,即本发明提出一种新的船用尾轴磨损位修复方法。
技术实现要素:
5.本发明旨在至少解决现有技术中存在的技术问题之一,提供一种船用尾轴磨损位修复方法与涂层。
6.本发明的一方面,提供一种船用尾轴磨损位修复方法,包括:
7.将青铜粉末与sic粉末进行混合以得到混合粉末;
8.将所述混合粉末作为喷涂材料,采用冷喷涂工艺在经过预处理的船用尾轴磨损位进行喷涂,以在该磨损位获得青铜基复合涂层;
9.对所述青铜基复合涂层进行处理,以完成所述船用尾轴磨损位的修复。
10.可选的,所述青铜粉末的粒度范围为5μm~50μm。
11.可选的,所述青铜粉末的化学式为cusn10。
12.可选的,所述sic粉末的粒度范围为5μm~50μm。
13.可选的,所述混合粉末中sic体积百分含量范围为5%-30%。
14.可选的,所述冷喷涂工艺采用的主气体为空气或氮气。
15.可选的,所述主气体温度范围为500℃~800℃,所述主气体压力范围为3mpa~
10mpa。
16.可选的,所述涂层厚度与预设的磨削裕量或车削裕量相匹配。
17.可选的,所述预处理包括表面清洁或喷砂。
18.本发明的另一方面,提供一种船用尾轴磨损位修复涂层,采用前文记载的所述的方法制得。
19.本发明提供一种船用尾轴磨损位修复方法,包括:将青铜粉末与sic粉末进行混合以得到混合粉末;将所述混合粉末作为喷涂材料,采用冷喷涂工艺在经过预处理的船用尾轴磨损位进行喷涂,以在该磨损位获得青铜基复合涂层;对所述青铜基复合涂层进行处理,以得到具有预设尺寸与表面精度的船用尾轴。本发明的修复方法无需备用青铜衬套,避免了原先采用换新备用青铜衬套技术方案中所涉及的繁琐工序及高修理费用。另外,采用本发明提供的粉末配方制备得到的青铜基复合涂层,可有效减轻青铜衬套的摩擦、磨损,复合青铜衬套更加耐用,延长了尾轴使用寿命,减少船舶停航时间及尾轴修理费用等。
附图说明
20.图1为本发明一实施例的一种船用尾轴磨损位修复方法的流程框图。
具体实施方式
21.为使本领域技术人员更好地理解本发明的技术方案,下面结合附图和具体实施方式对本发明作进一步详细描述。显然,所描述的实施例是本发明的一部分实施例,而不是全部的实施例。基于所描述的本发明的实施例,本领域普通技术人员在无需创造性劳动的前提下所获得的所有其他实施例,都属于本发明保护范围。
22.需要说明的是,针对由于磨损而导致失效的尾轴青铜衬套,本发明提出一种适合于使用工况的青铜基复合涂层制备技术,目的不仅在于恢复磨损青铜衬套的原有几何尺寸,还可使得复合涂层具备比原有基体材料更为优良的摩擦学性能,有助于改善青铜衬套的工作条件,降低运转工件的摩擦磨损,提高部件工作的可靠性、延长其服役寿命,为解决修复磨损船舶尾轴青铜衬套提供新的简便的修复技术。
23.如图1所示,本发明的一方面,提供一种船用尾轴磨损位修复方法s100,包括下述具体步骤s110~s130:
24.s110、将青铜粉末与sic粉末进行混合以得到混合粉末。
25.本实施例采用青铜粉末与sic粉末混合,有效提高涂层的强度,增加耐磨性。
26.具体的,本实施例的青铜粉末的粒度范围为5μm~50μm,青铜粉末的化学式为cusn10,其硬度高、耐磨性好,有较好的铸造性能和切削加工性能,可以满足轴承中减摩涂层材料的要求。
27.进一步的,本实施例的sic粉末的粒度范围为5μm~50μm。以及,本实施例得到的混合粉末中sic体积百分含量范围为5%-30%,由于其化学性能稳定,导热系数高,耐磨性能好,与青铜粉粉末混合可以有效提高涂层材料的强度与耐磨性。
28.s120、将所述混合粉末作为喷涂材料,采用冷喷涂工艺在经过预处理的船用尾轴磨损位进行喷涂,以在该磨损位获得青铜基复合涂层。
29.具体的,本实施例的冷喷涂工艺采用的主气体为空气或氮气,主气体温度范围为
500℃~800℃,主气体压力范围为3mpa~10mpa。
30.进一步的,涂层厚度与预设的磨削裕量或车削裕量相匹配。也就是说,涂层厚度预留一定的磨削或车削裕量。
31.更进一步的,本实施例的预处理包括表面清洁或喷砂,例如,采用棕刚玉砂进行吹砂毛化,喷完后用压缩空气吹走残留的砂粒。也就是说,本实施例先对船用尾轴磨损区域进行预处理,预处理之后再进行喷涂。
32.s130、对所述青铜基复合涂层进行处理,以完成所述船用尾轴磨损位的修复,即得到具有预设尺寸与表面精度的青铜衬套。
33.具体的,对获得的轴件涂层进行机加工后处理,获得需要的青铜衬套几何尺寸及表面精度。即根据轴件的修复位置与尺寸要求,采用机械打磨进行涂层加工,以完成对船用尾轴磨损位的修复,不仅可以恢复磨损青铜衬套的原有几何尺寸,还可使得复合涂层具备比原有基体材料更为优良的摩擦学性能,有助于改善青铜衬套的工作条件,降低运转工件的摩擦磨损。
34.需要说明的是,本实施例对于青铜衬套的几何尺寸不做具体限定,可以根据实际需求进行设置。
35.本实施例采用冷喷涂特定参数制备船舶尾轴衬套特定成分的青铜基复合涂层,该修复方法相当于复合涂层的制备方法,采用冷喷涂工艺将混合粉末均匀涂覆在轴件磨损表面,可以做到无死角、无漏点,以及,冷涂层还具有持久的热辐射吸收率、有效均衡炉温、提高热交换效率等。无需更换整段青铜衬套,即无需备用青铜衬套,并且,采用别的方案,会由于工艺过程中的热输入,而导致粉末氧化或分解等不利影响,从而导致涂层性能无法达到预期效果。
36.本发明的另一方面,提供一种船用尾轴磨损位修复涂层,采用前文记载的所述的方法制得,具体方法参考前文记载,在此不再赘述。
37.下面将以具体实施例对船用尾轴磨损位修复方法进行说明:
38.实施例1
39.s1、将粒度为25μm的青铜(cusn10)粉末与粒度为30μm的sic粉末机械混合均匀,混合粉末中sic体积百分含量为17%;
40.s2、采用合适的冷喷涂工艺参数在经过预处理的磨损轴表面喷涂,冷喷涂工艺过程中重要的参数为:
①
主气体采用氮气;
②
主气体温度650℃,
③
主气体压力7mpa。本实施例所得的青铜基复合涂层,该涂层厚度预留一定磨削或车削裕量。
41.s3、对获得的轴件涂层进行机加工后处理,获得需要的青铜衬套几何尺寸及表面精度。
42.实施例2
43.s1、将粒度为45μm的青铜(cusn10)粉末与粒度为15μm的sic粉末机械混合均匀,混合粉末中sic体积百分含量为25%;
44.s2、采用合适的冷喷涂工艺参数在经过预处理的磨损轴表面喷涂,冷喷涂工艺过程中重要的参数为:
①
主气体采用氮气;
②
主气体温度700℃,
③
主气体压力9mpa。本实施例所得的青铜基复合涂层,该涂层厚度预留一定磨削或车削裕量。
45.s3、对获得的轴件涂层进行机加工后处理,获得需要的青铜衬套几何尺寸及表面
精度。
46.本发明提供本发明提供一种船用尾轴磨损位修复方法与涂层,相对于现有技术而言具有以下有益效果:
47.第一、本发明的修复方法无需备用青铜衬套,避免了原先采用换新备用青铜衬套技术方案中所涉及的繁琐工序及高修理费用。
48.第二、本发明提供的粉末配方制备得到的青铜基复合涂层,可有效减轻青铜衬套的摩擦、磨损,复合青铜衬套更加耐用,延长了尾轴使用寿命,减少船舶停航时间及尾轴修理费用等。
49.可以理解的是,以上实施方式仅仅是为了说明本发明的原理而采用的示例性实施方式,然而本发明并不局限于此。对于本领域内的普通技术人员而言,在不脱离本发明的精神和实质的情况下,可以做出各种变型和改进,这些变型和改进也视为本发明的保护范围。