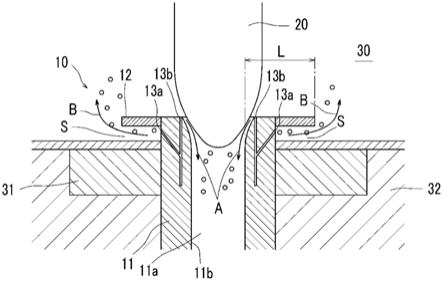
1.本发明涉及具备气体吹入功能的浇口盘上喷嘴结构体及连续铸造方法。
背景技术:
2.在钢的连续铸造中,多是进行有从浇口盘上喷嘴吹入气体的操作。该气体的吹入主要以如下情况为目的。(1)通过使气泡从浇口盘上喷嘴的内孔向下方流动,可抑制夹杂物向该浇口盘上喷嘴或其下方的喷嘴的内孔面附着,或者因夹杂物的附着而导致的内孔阻塞。(2)从浇口盘上喷嘴的下方对铸型内的钢液的流动形态进行控制。(3)在浇口盘上喷嘴的下方或铸型内使夹杂物上浮。(4)在浇口盘内使夹杂物上浮。这些会给铸造操作的稳定性和生产性、铸片的质量带来影响。
3.对于上述(1)~(4),以往以各种各样的形态进行有从浇口盘上喷嘴的气体吐出。主要针对上述(1)~(3),例如在专利文献1中提出有一种结构,在浇口盘上喷嘴的内孔中设置有气体吐出用的多孔部的同时,设置在浇口盘上喷嘴的上端部外周上的环状耐火物的环状锷部覆盖了该浇口盘上喷嘴的上部。由此,可切实地进行向浇口盘上喷嘴的内孔的供气。
4.此外,在专利文献2中,提出有一种浇口盘底部的塞棒承接喷嘴,其目的在于,防止夹杂物或生铁附着在塞棒和上喷嘴的接触部附近,以便进行稳定的流量控制来得到良好的铸片,其特征在于,以与塞棒的接触部为边界,在其上下各个钢液接触面上设置有多孔耐火物,且从各个多孔耐火物可独立吹出氩气。
5.并且,着眼于上述(4),在专利文献3中提出有一种连续铸造方法,在浇口盘的底部上设置有喷嘴,并且,在从设置在喷嘴的上部上的环状的上多孔耐火物吹入惰性气体的同时,可从设置在所述喷嘴的下部上的环状的下多孔耐火物吹入惰性气体。由此,上多孔耐火物可朝向浇口盘的钢液吹入惰性气体,下多孔耐火物可朝向喷嘴的开口吹入惰性气体。
6.专利文献专利文献1:日本特开2003-220450号公报专利文献2:日本特开平6-297118号公报专利文献3:日本特开2016-182612号公报
技术实现要素:
7.为了提高铸片的质量,上述(4)的在浇口盘内使夹杂物上浮也很重要。上述(1)~(3)与(4)的平衡是根据个别的操作条件(包含技术诀窍)、钢种、质量目标等而适当确定的性质。然而,在前述专利文献等现有技术的气体吹入方法等中,可知吹入的气体的大部分会流向浇口盘上喷嘴的内孔侧,导致无法使气体向上方即在浇口盘内的钢液中上浮。
8.另外,为了前述(4)即在浇口盘内使夹杂物上浮,还存在有一种在浇口盘底部的浇口盘上喷嘴以外的任意位置上,向浇口盘内吹入气体的方法。然而,为了在浇口盘底部的浇口盘上喷嘴以外的任意位置上将气体吹入到浇口盘内,需要专用的设备,会导致初始成本及运行成本升高,此外,操作时的漏钢等危险性也会增大。并且,该方法还被指出有在钢液内夹杂物去除效果上存在有不足。从这种观点出发,为了在浇口盘内利用气体来去除夹杂物,优选使用浇口盘上喷嘴,形成向浇口盘内钢液的气体的上浮流,并且对其比例进行调整。
9.本发明所要解决的技术问题是,提供一种可在从浇口盘上喷嘴吹入气体的方式下,使从该喷嘴的特定部位吹入的全部气体在浇口盘内(从浇口盘上喷嘴向上方)上浮,或对向浇口盘上喷嘴的内孔侧或下方的气体流量与向浇口盘内(浇口盘上喷嘴至上方)上浮的气体流量的平衡进行任意调整的浇口盘上喷嘴结构体及连续铸造方法。另外,在一个浇口盘上喷嘴上,吐出位置、多孔体或通孔等吐出孔的形态、吐出孔的数量等有各种各样,因而本发明的“从该喷嘴的特定部位吹入的全部气体”是指一个气体流出部分,换言之是指,“从一个通孔吐出的全部气体,或者是着眼于非常小的吐出孔的汇合部分,而分别从该汇合部分吐出的全部气体,所述非常小的吐出孔的汇合部分为,即使是包含多孔体等的多个吐出孔,刚吐出后的多个气泡也会合并成一个气泡的,可以说是形成一个气泡的非常小的汇合部分”,而不是以从一个浇口盘上喷嘴吐出的全部气体为对象。
10.本发明者发现,像前述专利文献那样,从浇口盘上喷嘴的上端附近吹入的大部分气体流动到浇口盘上喷嘴的内孔侧,导致无法使气体向上方即在浇口盘内的钢液中上浮的原因为,浇口盘上喷嘴的上端附近的吐气孔附近的向该喷嘴内孔的钢液流形成主体,且该钢液流比气泡的上浮流更强。
11.即,本发明为一种浇口盘上喷嘴结构体及使用了该浇口盘上喷嘴结构体的连续铸造方法,其要点在于,为了使气泡的上浮流比向该喷嘴内孔的钢液流更强劲,应使气体在向该喷嘴内孔的钢液流速小于气泡的上浮流速的位置上吐出,并且可对向该喷嘴内孔的气体流量与上浮的气体流量的平衡进行调整。
12.具体而言,本发明为下述1~11的浇口盘上喷嘴结构体及12的连续铸造方法。1.一种浇口盘上喷嘴结构体,其特征在于,在浇口盘上喷嘴的上端部外周的一部分或整周上,具备比该浇口盘上喷嘴上端部的外形更大的锷状物,且在所述锷状物的下面、外周面、上面以及比所述锷状物更靠下方的所述浇口盘上喷嘴的外周面中的任意一个或多个面上,具备一个或多个吐气孔。2.根据前述1所述的浇口盘上喷嘴结构体,其特征在于,所述锷状物的吐气孔为,从该锷状物内的空间即气体流通路径的端部或该锷状物的下面起贯穿上面的孔。3.根据前述1或2所述的浇口盘上喷嘴结构体,其特征在于,在所述锷状物的下面上,具备一个或多个气体可通过的槽。4.根据前述1或2所述的浇口盘上喷嘴结构体,其特征在于,在将该浇口盘上喷嘴结构体安装到浇口盘后的状态下,在所述锷状物的下面的一部分或整体上,具备气体可通过的空间。5.根据前述1至前述4中任意一项所述的浇口盘上喷嘴结构体,其特征在于,该浇口盘上喷嘴结构体用于钢的连续铸造,所述钢的连续铸造通过塞棒来进行钢
液的流量控制,从所述浇口盘上喷嘴的下端的内孔面的铅垂位置起至所述锷状物的上面的吐气孔或外周面为止的长度l(mm)满足下述式1,l≧-1.875m2+26.332m-0.3929
…
式1在此,m:铸造速度(t/min)。6.根据前述1至前述4中任意一项所述的浇口盘上喷嘴结构体,其特征在于,该浇口盘上喷嘴结构体用于钢的连续铸造,所述钢的连续铸造通过塞棒来进行钢液的流量控制,从所述浇口盘上喷嘴的下端的内孔面的铅垂位置起至所述锷状物的上面的吐气孔或外周面为止的长度l(mm)满足下述式2,l《-1.875m2+26.332m-0.3929
…
式2在此,m:铸造速度(t/min)。7.根据前述1至前述5中任意一项所述的浇口盘上喷嘴结构体,其特征在于,从所述浇口盘上喷嘴的下端的内孔面的铅垂位置起至所述锷状物的上面的吐气孔或外周面为止的长度l(mm)为60mm以上。8.根据前述1至前述7中的任意一项所述的浇口盘上喷嘴结构体,其特征在于,所述锷状物与所述浇口盘上喷嘴接合。9.根据前述8所述的浇口盘上喷嘴结构体,其特征在于,所述锷状物与所述浇口盘上喷嘴是通过螺钉或插扣式结构或粘接材料而接合。10.根据前述1至前述7中的任意一项所述的浇口盘上喷嘴结构体,其特征在于,所述锷状物与所述浇口盘上喷嘴的外周嵌合,并与邻接于该浇口盘上喷嘴的风口或浇口盘底部耐火物层接合。11.根据前述10所述的浇口盘上喷嘴结构体,其特征在于,所述锷状物与所述风口或所述浇口盘底部耐火物层是通过螺钉或插扣式结构或粘接材料而接合。12.一种连续铸造方法,使用有前述1至前述4中的任意一项所述的浇口盘上喷嘴结构体,其特征在于,所述浇口盘上喷嘴结构体用于钢的连续铸造,所述钢的连续铸造通过塞棒来进行钢液的流量控制,使从所述浇口盘上喷嘴的下端的内孔面的铅垂位置起至所述锷状物的上面的吐气孔或外周面为止的长度l(mm)为,在满足下述式3的边界长度lb(mm)以上,以便使大致全部气体上浮,或者,使其小于所述边界长度lb(mm),以便对向气体的内孔侧下方的流量和上浮的量进行调整,lb=-1.875m2+26.332m-0.3929
…
式3在此,m:铸造速度(t/min)。
13.根据本发明,由于在浇口盘上喷嘴的上端部外周的一部分或整周上设置有比该浇口盘上喷嘴的外形更大的锷状物,因此可将气体引导到浇口盘上喷嘴的外周侧,即引导到向内孔的钢液流速较小的区域,并可使气体从其附近朝向上方。由此,可使气体在浇口盘内上浮,因而可得到在浇口盘内使夹杂物上浮的效果。进而可改善铸片质量。此外,通过任意调节长度(前述l),可根据个别的操作等来任意调节气体的向喷嘴
内孔侧下方的流量和向浇口盘内的上浮流量,所述长度为(前述l),从比该浇口盘上喷嘴的外形更大的锷状物的内孔下端的铅垂位置起,至吐气孔或沿着锷状物流动之后向上方释放的部位为止的至气体吐出部分的长度。
附图说明
14.图1是表示本发明的一个实施方式即浇口盘上喷嘴结构体的主要部分的示意剖视图。图2是将所述的式1及式2的右边图形化后的图。图3是表示图1的浇口盘上喷嘴结构体上的气体举动分析结果的图。符号说明10-浇口盘上喷嘴结构体;11-浇口盘上喷嘴;11a-内孔;11b-内孔面;12-锷状物;13a、13b-吐气孔;20-塞棒;30-浇口盘;31-风口;32-浇口盘底部耐火物层;s-空间。
具体实施方式
15.在图1中表示有本发明的一个实施方式即浇口盘上喷嘴结构体的主要部分。本实施方式的浇口盘上喷嘴结构体10用于钢的连续铸造,所述钢的连续铸造通过塞棒20来进行钢液的流量控制,在浇口盘上喷嘴11的上端部外周的整周上,具备比该浇口盘上喷嘴1的外形(外径)更大的锷状物12。此外,本实施方式的浇口盘上喷嘴结构体10在比锷状物12更靠下方的浇口盘上喷嘴11的外周面上,具备多个(在周向上以等间隔为6个)吐气孔13a。并且,本实施方式的浇口盘上喷嘴结构体10在浇口盘上喷嘴11的上端面上还具备多个(在周向上以等间隔为24个)吐气孔13b。另外,如图1所示,浇口盘上喷嘴结构体10在将其安装到浇口盘30后的状态下,在锷状物10的下面的一部分或整体上,具备气体可通过的空间s(由于铸造中在浇口盘内充满钢液,因此在该空间中存在有钢液)。
16.如此,通过在本实施方式的浇口盘上喷嘴结构体10上设置锷状物12,可将气体引导到浇口盘上喷嘴11的外周侧,即引导到向内孔11a的钢液流速(箭头a方向)较小的区域(箭头b方向),并可使气体从其附近朝向上方。由此,可使气体在浇口盘30内上浮,因而可得到在浇口盘30内使夹杂物上浮的效果。进而可改善铸片质量。
17.并且,本发明者们发现,在这样的浇口盘上喷嘴结构体10上,气体的向内孔11a侧下方的流量与向浇口盘30内的上浮量的比例较大地依存于图1所示的长度l(mm)及铸造速度m(t/min)。在此,图1所示的长度l是指,从浇口盘上喷嘴11的下端的内孔面11b的铅垂位置起至锷状物12的上面的吐气孔或外周面为止的长度,铸造速度m(t/min)则与钢液的通过量同义。
18.另外,使该长度l从浇口盘上喷嘴11的下端的内孔面11b的铅垂位置开始的原因为,虽然浇口盘上喷嘴的外周或上端附近可以是各种各样的形状,但如果铸造速度相同,则下端的内孔面的位置(与内孔径大致相同)几乎不发生变化,即,向内孔流入的钢液的速度上没有较大的不同,并且,在塞棒控制的情况下,其嵌合部位置与该内孔的直径对应而在大致相同的半径方向位置上。
19.即,本发明者们发现,在该长度l(mm)满足下述式1时,可使大致全部气体在浇口盘
内上浮,在满足下述式2时,可调整气体的向内孔侧下方的流量和上浮的量。l≧-1.875m2+26.332m-0.3929
…
式1l《-1.875m2+26.332m-0.3929
…
式2
20.如前所述,对本发明中的气体的内孔侧或上浮的比例的控制是针对分别从每个吐出孔吐出的气体而进行的。因而,在确定该长度l(mm)的作为其中一方的基准的所述锷状物的上面上具有吐气孔时,无论是存在有一个或多个,均是与每个吐出孔相关的所述长度,或者,在从所述锷状物的下方的任意位置或外周面流动有气体且气体在锷状物的外周面上向上方释放时,是指至其锷状物的外周面为止的长度。即使它们并存,各自的吐出气体也通过其l(mm)而分别确定了前述式的内孔侧/上浮的比例。是否并存和数量如何与浇口盘上喷嘴整体上的气体的吐出量和形态的控制有关,这一点可根据个别的操作条件(任意)来设定。
21.另外,如果将这些式1及式2的右边曲线化,则如图2所示,在长度l处于该近似线以上的区域时,可使大致全部气体在浇口盘内上浮,而处于小于近似线的区域时,则可对气体的向内孔侧下方的流量和上浮的量进行调整。
22.接下来,对所述的式1及式2的技术依据(导出依据)等进行说明。
23.首先,使用流动分析软件(fluent)在以下的条件下进行了模拟。
·
浇口盘上喷嘴的内孔径为
·
作为塞棒控制,相对于全部关闭时的嵌合部的直径空间约为12mm,
·
吐气孔为的通孔,
→
13b(24孔)、13a(6孔)
·
气泡径为
·
铸造速度为0~5t/min。并且,进行了下述条件下的水模型实验。
·
浇口盘上喷嘴的内孔径为
·
作为塞棒控制,相对于全部关闭时的嵌合部的直径空间约为15mm,
·
吐气孔为的通孔(气泡径其结果为约),
·
铸造速度为3t/min。
24.另外,本发明者在至此的实验中,由实际操作中的结果等发现,在水模型中,在吐气孔的直径为时,气泡径约为在钢液中则进一步变为其2~3倍,且还发现,该吐气孔的通孔和氧化铝-石墨质的多孔体(所谓的多孔耐火物,平均气孔径≒100~120μm)的气泡径几乎为相同的尺寸。
25.通过改变铸造速度并模拟,得到了作为边界值的前述的长度l(mm)(图2的各标示位置),所述边界值可使从外周吹入(13a)的大致全部的气体上浮,并且,用回归分析的近似线及近似公式对该结果进行了表示,从而得到了下述式3。lb=-1.875m2+26.332m-0.3929
…
式3
26.在这些模拟与水模型实验的比较中,前述的长度l(mm)大致一致。
27.换言之,通过使前述长度l(mm)大于满足前述式3的边界长度lb(mm),则可使大致全部气体上浮,或者,通过使其小于边界长度lb(mm),则可对气体的向内孔侧下方的流量和
上浮的量进行调整。
28.另外,由于在该图2中,纵轴l(mm)是距浇口盘上喷嘴内孔下端的铅垂位置的长度,因此是包括了该浇口盘上喷嘴结构体的锷状物设置位置的壁厚的长度。因而,锷状物的前述的壁厚(mm)《lb(mm)的情况也属于本发明的范围。此外,在通常(多数的)铸造中,在每个这样的浇口盘上喷嘴的铸造速度在约3(t/min)以上时,气体的上浮量多会减少,考虑到这样的实际情况,如果长度l(mm)为大致60mm以上,则大致全部的气体会向上方上浮。即,在通常(多数的)铸造中,为了使从外周吹入的(13a)气体全部向上方上浮,需要l≧60mm,此外,在l《60mm时,l变得越小,则气体的向内孔侧下方的流量会变得越多(参照图3)。
29.下面,对本实施方式(图1)的变形例进行例示。(a)虽然在本实施方式中,锷状物12是设置在浇口盘上喷嘴11的上端部外周的整周上,但也可以设置在浇口盘上喷嘴11的上端部外周的一部分上。即使锷状物12的设置位置为浇口盘上喷嘴11的上端部外周的一部分,也可得到很大的使气体在浇口盘内上浮的效果(使夹杂物在浇口盘内上浮的效果)。此外,锷状物12的俯视形状不局限于圆形,例如也可以为椭圆形或多边形。
30.(b)虽然在本实施方式中,在比锷状物12更靠下方的浇口盘上喷嘴11的外周面上设置了多个(在周向上以等间隔有6个)吐气孔13a,但也可以在锷状物12的下面、外周面、上面中的任意一个或多个面上设置一个或多个吐气孔13a。如此,在将吐气孔13a设置在锷状物12上时,该锷状物12的吐气孔13a可形成从锷状物12内的空间即气体流通路径的端部或从锷状物12的下面贯穿上面的孔。
31.(c)虽然在本实施方式中,在锷状物12的下面上具备气体可通过的空间s,但也可在锷状物12的下面上具备一个或多个气体可通过的槽。此外,所述槽包含下述形态,即,使锷状物12的下面在圆周方向上弯曲,使圆周方向的一部分形成为凹状,并使该凹状部朝向半径方向延伸存在的形态。即,所述槽只要具备可使气体集中向外周侧方向流动的作为气体流通路径的结构即可。并且,也可以在所述空间s的位置上设置透气性高的多孔性的耐火物来代替空间。
32.(d)在本实施方式中,锷状物12是通过粘接材料而与浇口盘上喷嘴11接合,但也可以通过螺钉或插扣式(bayonet)结构而与浇口盘上喷嘴11接合。此外,锷状物12也可以与浇口盘上喷嘴11的外周嵌合,并与邻接于该浇口盘上喷嘴11的风口31或浇口盘底部耐火物层32接合。该接合可通过螺钉或插扣式结构或粘接材料来进行。
33.(e)虽然本实施方式的浇口盘上喷嘴结构体10用于钢的连续铸造,所述钢的连续铸造通过塞棒20来进行钢液的流量控制,但也可以用于通过滑动喷嘴装置来进行钢液的流量控制的钢的连续铸造。即,也可应用于在浇口盘上喷嘴上方改变钢液的流动的所谓的无障碍物的结构。实施例
34.在下述的铸造条件及浇口盘上喷嘴条件下,使用未设置有锷状物12的以往品(比较例)和设置有锷状物12且前述长度l(mm)在30~60mm的范围内变化的本发明品(实施例),
实施了钢的连续铸造试验,该试验通过塞棒来进行钢液的流量控制,而后对浇口盘上喷嘴内的氧化铝附着厚度以及产品即卷材的表面缺陷的产生数量进行了评价。具体而言,是将以往品上的浇口盘上喷嘴内的氧化铝附着厚度作为1.0,并对本发明品上的浇口盘上喷嘴内的氧化铝附着厚度进行指数化。该喷嘴内氧化铝附着厚度指数越小,则浇口盘上喷嘴内的氧化铝附着厚度越小。此外,将以往品上的卷材的表面缺陷的产生数量作为1.0,并对本发明品上的卷材的表面缺陷的产生数量进行了指数化。该卷材表面缺陷产生指数越小,则卷材的表面缺陷的产生数量越少,即,铸片的质量越好。
35.(铸造条件)
·
钢种:普通铝镇静钢
·
铸造尺寸:250mm(厚度)
×
1250mm(宽度)
·
铸造速度(钢液的通过量):约3(t/min)(浇口盘上喷嘴条件)
·
内孔径:80mm
·
吐气孔的直径
×
数量:0.3(mm)
×
13b(24孔)、13a(6孔)
·
气体(ar)吐出量:10(l/min)
·
气体(ar)吐出流速:1.56(m/min)
36.表1示出有连续铸造试验的结果。另外,由于在本连续铸造试验中铸造速度(钢液的通过量)为约3(t/min),因此前述的式3中的边界长度lb为约60mm。
37.气泡的上浮量(比例)为,以总量为100的指数计,由目测及水模型实验等得出的推测值(实施例),100是指大致全部上浮,0是指全部向内孔侧流入。
38.(表1)
39.如表1所示,对于l(mm)为边界长度lb(约60mm)以上的本发明品(实施例3),与以往品(比较例1)相比,浇口盘上喷嘴内的氧化铝附着厚度变小,卷材的表面缺陷的产生数量也变少。另外,对于l(mm)小于边界长度lb(约60mm)的本发明品(实施例1、2),通过调整l(mm),可对气泡的上浮量/内孔侧量的比例进行调整,其表明也可调整铸片的质量。