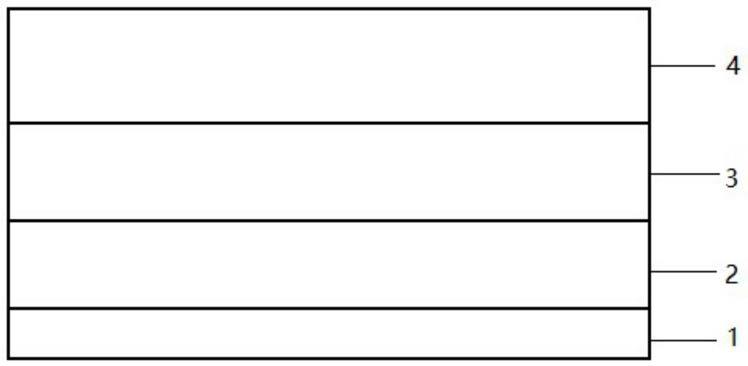
1.本发明涉及耐高温抗冲刷涂层技术领域,尤其涉及一种含稀土铝酸盐的耐高温复合涂层及制备方法。
背景技术:
2.在航空航天飞行器中,含有许多高温工况零件,比如位于助推器尾喷口处的合金零件。高温工况,比如助推器尾喷口为高温高压燃气流场以及al2o3粒子侵蚀冲刷环境,因此需要在整流罩表面制备耐高温抗冲刷涂层来防止高温、高压和高速气流冲刷而不被烧穿。
3.传统的解决方案是将整流罩改为高温合金材料,同时在气流冲刷表面增加碳碳复合材料,该方案结构设计复杂,材料成本较高,结构整体增重较多。
4.目前,对稀土铝酸盐的研究主要集中在其稀土掺杂后的发光性能和磁学性能研究中,国内外研究者在实验室和理论研究方面己做了大量工作,已经制成了各种磁光传感器、磁光光盘、磁光调节器等。但是,对稀土铝酸盐的热学性能研究报道较少。
技术实现要素:
5.鉴于上述的分析,本发明实施例旨在提供一种含稀土铝酸盐的耐高温复合涂层及制备方法,具有低导热率、耐高温、耐腐蚀的高熔点性能,可用于高温抗冲刷涂层。
6.一方面,本发明提供了一种含稀土铝酸盐的耐高温复合涂层,沿远离合金基体表面的方向,依次包括微弧氧化膜层、金属粘结层、大气等离子喷涂层;
7.所述微弧氧化膜层为金红石型和锐钛矿型tio2的陶瓷涂层;
8.所述金属粘结层为nicocraly;
9.所述大气等离子喷涂层的喷涂粉末为稀土铝酸盐喷涂粉末,所述稀土铝酸盐喷涂粉末为稀土氧化物与al2o3、mgo采用高温固相合成得到的稀土铝酸盐粉末经喷雾干燥处理得到。
10.进一步地,所述稀土氧化物为la2o3,la2o3与mgo、al2o3质量比满足:15-25:5-10:65-78;
11.所述高温固相合成的温度为1000~1600℃,时间为12~64h。
12.本发明还提供了一种含稀土铝酸盐的耐高温复合涂层的制备方法,其特征在于,包括以下步骤:
13.步骤1:对合金基体进行微弧氧化处理,得到微弧氧化膜层,膜层厚度为10~20μm;
14.步骤2:在微弧氧化膜层上制备一层金属粘结层;
15.步骤3:采用大气等离子喷涂工艺将稀土铝酸盐喷涂粉末沉积在步骤2的金属粘结层表面得到大气等离子喷涂稀土铝酸盐陶瓷层,完成含稀土铝酸盐的耐高温复合涂层的制备。
16.进一步地,所述步骤3中,稀土铝酸盐喷涂粉末的制备方法,包括以下步骤:
17.步骤301:将稀土氧化物与氧化铝、氧化镁采用高温固相合成得到稀土铝酸盐粉
末;
18.步骤302:将步骤301得到的稀土铝酸盐粉末与去离子水、聚乙烯醇混合,通过球磨工艺混合均匀得到浆料;
19.步骤303:将步骤302得到的浆料进行喷雾干燥处理得到稀土铝酸盐喷涂粉末。
20.进一步地,所述步骤302中,稀土铝酸盐粉末的质量分数为30~70%,聚乙烯醇的质量分数为0.1~6.0%,余量为去离子水。
21.进一步地,所述步骤302中,球磨工艺在行星式球磨机上球磨混合,所述行星式球磨机的公转速度为150~300r/min,自转速度为350~550r/min,搅拌时间为24~72h。
22.进一步地,所述步骤303中,喷雾干燥处理参数:出口温度为100~150℃,进口温度为150~300℃,浆料送料速度为0.5~5.0l/min,雾化盘转速为15000~30000r/min。
23.进一步地,所述步骤3中,所述稀土铝酸盐喷涂粉末粒径为20~80μm,大气等离子喷涂工艺参数为:氩气流量为25~45l/min,氢气流量为5~15l/min,电流大小控制为500~600a,功率为25~45kw,送粉氩气流量为0.5~4.0l/min,送粉速度为30~80g/min,喷涂距离为80~120mm。
24.进一步地,所述步骤1中,微弧氧化工艺为:电流波形:单向脉冲或双向方波,脉冲波形频率:在50hz~1500hz;正向电流密度为180a/dm2~300a/dm2;负向电流密度为0a/dm2~100a/dm2;正向占空比10%~50%,负向占空比10%~50%;微弧氧化时间:为10min~30min;微弧氧化槽液温度:10℃~30℃。
25.进一步地,所述步骤2中,采用大气等离子喷涂工艺制备金属粘结层,金属粘结层的喷涂粉末粒径为30~74μm,大气等离子喷涂工艺参数为:氩气流量为15~35l/min,氢气流量为1~8l/min,电流大小控制为500~550a,功率为20~35kw,送粉氩气流量为0.5~3.5l/min,送粉速度为30~80g/min,喷涂距离为60~120mm。
26.与现有技术相比,本发明至少可实现如下有益效果之一:
27.1、本发明通过将稀土氧化物与氧化铝、氧化镁采用高温固相合成得到稀土铝酸盐粉末,再将稀土铝酸盐粉末与去离子水、聚乙烯醇球磨混合,进行喷雾干燥处理得到稀土铝酸盐喷涂粉末;得到的喷涂粉末采用大气等离子喷涂工艺将稀土铝酸盐喷涂粉末沉积在金属粘结层表面,经测试,涂层最外层的稀土铝酸盐陶瓷层热导率为0.20~0.40w/(m
·
k),具有优异的抗高温烧蚀特性,并具有优异的隔热性能。
28.2、本发明的涂层还包括微弧氧化膜层、金属粘结层;沿远离合金表面的方向,依次包括:微弧氧化膜层、金属粘结层、大气等离子喷涂稀土铝酸盐陶瓷层;稀土铝酸盐陶瓷层采用低热导率稀土铝酸盐陶瓷材料具有优异的抗高温烧蚀特性,并提供优异的隔热性能;金属粘结层与合金基体具有良好的热膨胀系数匹配性;微弧氧化膜层提供更高的粗糙系数,使得各涂层附着力增强。该涂层总厚度仅为0.20mm~0.35mm,使待喷零件轻量化;而且涂层具有优异的抗高温烧蚀特性、优异的隔热性能,结合强度可达28.6~33.6mpa满足工况使用。
29.3、零件在喷涂过程前,需对其进行前处理以粗化零件表面、保障涂层与基体的结合力。现有技术前处理最常用的方式喷砂可能使薄壁钛合金基体采用较大的变形,为了降低基体的变形风险,同时保障基体与涂层界面的结合力,本发明采用微弧氧化前处理工艺,摒弃了传统的吹砂工艺。
30.本发明中,上述各技术方案之间还可以相互组合,以实现更多的优选组合方案。本发明的其他特征和优点将在随后的说明书中阐述,并且,部分优点可从说明书中变得显而易见,或者通过实施本发明而了解。本发明的目的和其他优点可通过说明书以及附图中所特别指出的内容中来实现和获得。
附图说明
31.附图仅用于示出具体实施例的目的,而并不认为是对本发明的限制,在整个附图中,相同的参考符号表示相同的部件。
32.图1为本发明提供的含稀土铝酸盐的耐高温复合涂层的结构示意图。
33.附图标记:
34.1-基体;2-微弧氧化膜层;3-金属粘结层;4-大气等离子喷涂稀土铝酸盐陶瓷层。
具体实施方式
35.下面结合附图来具体描述本发明的优选实施例,其中,附图构成本技术一部分,并与本发明的实施例一起用于阐释本发明的原理,并非用于限定本发明的范围。
36.一方面,本发明提供了一种含稀土铝酸盐的耐高温复合涂层,沿远离基体表面的方向,依次包括微弧氧化膜层、金属粘结层、大气等离子喷涂层;
37.所述微弧氧化膜层为金红石型和锐钛矿型tio2的陶瓷涂层;
38.所述金属粘结层为nicocraly;
39.所述大气等离子喷涂层的喷涂粉末为稀土铝酸盐喷涂粉末,所述稀土铝酸盐喷涂粉末为稀土氧化物与al2o3、mgo采用高温固相合成得到的稀土铝酸盐粉末经喷雾干燥处理得到。
40.也就是说,大气等离子喷涂层为大气等离子喷涂稀土铝酸盐陶瓷层。稀土铝酸盐陶瓷外层为将稀土氧化物与al2o3、mgo采用高温固相合成得到稀土铝酸盐粉末经喷雾干燥处理得到的稀土铝酸盐喷涂粉末的大气等离子喷涂层。
41.具体地,上述稀土氧化物为la2o3,la2o3与mgo、al2o3质量比满足:15-25:5-10:65-78;
42.固相合成的温度为1000~1600℃,时间为12~64h。
43.la2o3是一种无机化合物,常态为白色固体粉末,微溶于水,易溶于酸而生成相应的盐类,密度:6.51g/ml熔点很高可达2315℃,具有耐高温性能。
44.mgo是典型的碱土金属氧化物,常态为白色固体粉末,有高度耐火绝缘性能;因其热膨胀系数和导热率高,而具有良好的光透过性;广泛用作高温耐热材料,本发明加入氧化镁,可使产品在高温下具有优良的耐碱性和电绝缘性。
45.al2o3是一种高硬度的化合物,熔点高可达2054℃,硬度高,不溶于酸碱耐腐蚀,绝缘性好,在高温下可电离的离子晶体,常用于制造耐火材料。
46.聚乙烯醇作为粘结剂在稀土铝酸盐陶瓷粉末制备过程中可以提升粉末与去离子水混合的浆料粘度,使得浆料在喷雾干燥过程中形成的球形粉末有内聚强度。
47.另一方面,本发明提供了一种含稀土铝酸盐的耐高温复合涂层的制备方法,包括以下步骤:
48.步骤1:对合金基体进行微弧氧化处理,得到微弧氧化膜层,膜层厚度为10~20μm;
49.步骤2:在微弧氧化膜层上制备一层金属粘结层;
50.步骤3:采用大气等离子喷涂工艺将稀土铝酸盐喷涂粉末沉积在步骤2的金属粘结层表面得到大气等离子喷涂稀土铝酸盐陶瓷层,完成含稀土铝酸盐的耐高温复合涂层的制备。
51.具体地,上述步骤1中,微弧氧化工艺为:电流波形:单向脉冲或双向方波,脉冲波形频率:在50hz~1500hz;正向电流密度为180a/dm2~300a/dm2;负向电流密度为0a/dm2~100a/dm2;正向占空比10%~50%,负向占空比10%~50%;微弧氧化时间:为10min~30min;微弧氧化槽液温度:10℃~30℃。
52.在步骤1之前,还需采用酒精擦拭合金零件基体表面油污,擦拭干净后进行微弧氧化处理;微弧氧化是利用电化学手段,通过等离子体微孤产生的瞬时高温高压作用,在钛合金表面原位生长出金红石型和锐钛矿型tio2的陶瓷膜层,膜层厚度为10~20μm;该微弧氧化膜层粗糙度ra为2~3μm,微弧氧化后基体变形量≤0.2mm,该工艺在提升基体粗糙度(基体ra为0.3μm)的同时有效控制了变形程度。
53.具体地,上述步骤2中,可采用大气等离子喷涂工艺制备金属粘结层,喷涂nicocraly粉末粒径为30~74μm,大气等离子喷涂工艺参数为:氩气流量为15~35l/min,氢气流量为1~8l/min,电流大小控制为500~550a,功率为20~35kw,送粉氩气流量为0.5~3.5l/min,送粉速度为30~80g/min,喷涂距离为60~120mm。
54.采用大气等离子喷涂工艺在步骤1处理后的微弧氧化膜层上制备一层金属粘结层;金属粘结层为nicocraly金属层,与合金基体具有良好的热膨胀系数匹配性,作为金属基体与稀土铝酸盐陶瓷层的过渡。
55.具体地,上述步骤3中,采用大气等离子喷涂工艺将稀土铝酸盐喷涂粉末沉积在金属粘结层表面,稀土铝酸盐喷涂粉末粒径为20~80μm,大气等离子喷涂工艺参数为:氩气流量为25~45l/min,氢气流量为5~15l/min,电流大小控制为500~600a,功率为25~45kw,送粉氩气流量为0.5~4.0l/min,送粉速度为30~80g/min,喷涂距离为80~120mm。
56.具体地,上述步骤3中,稀土铝酸盐喷涂粉末的制备方法,包括以下步骤:
57.步骤301:将稀土氧化物与氧化铝、氧化镁采用高温固相合成得到稀土铝酸盐粉末;
58.步骤302:将步骤301得到的稀土铝酸盐粉末与去离子水、聚乙烯醇混合,通过球磨工艺混合均匀得到浆料;
59.步骤303:将步骤302得到的浆料进行喷雾干燥处理得到稀土铝酸盐喷涂粉末。
60.具体地,上述步骤301中,将稀土氧化物与氧化铝、氧化镁按照15-25:5-10:65-78的质量百分比比例混合;
61.高温固相合成的温度为1000~1600℃,时间为12~64h。
62.需要说明的是,将稀土氧化物与氧化铝、氧化镁按照15-25:5-10:65-78的质量百分比比例混合,采用马弗炉进行固相烧结工艺,具体方法为:从室温升温至500℃后,保温1~2h,然后升温至1200℃~1600℃,保温2h~8h,再随炉冷却至室温,升温速率控制在5℃/min~15℃/min。
63.具体地,上述步骤302中,混合料中,稀土铝酸盐粉末的质量分数为30~70%,聚乙
烯醇的质量分数为0.1~6.0%,余量为去离子水;球磨工艺为在行星式球磨机上球磨混合,所述行星式球磨机的公转速度为150~300r/min,自转速度为350~550r/min,搅拌时间为24~72h。
64.优选地,将稀土铝酸盐粉末与去离子水、聚乙烯醇按40~60:39.4~59.7:0.3~0.6质量百分比比例混合,通过球磨工艺混合均匀得到浆料;聚乙烯醇作为粘结剂可以提升粉末与去离子水混合的浆料粘度,使得浆料在喷雾干燥过程中形成的球形粉末有内聚强度。
65.具体地,上述步骤303中,采用离心式喷雾干燥机进行喷雾干燥处理,喷雾干燥处理参数:出口温度为100~150℃,进口温度为150~300℃,浆料送料速度为0.5~5.0l/min,雾化盘转速为15000~30000r/min。
66.本发明得到的含稀土铝酸盐的耐高温复合涂层测量其总厚度为0.20mm~0.35mm,并通过拉伸试验机设备进行结合强度测试,结果为28.6~33.6mpa。
67.本发明得到的含稀土铝酸盐的耐高温复合涂层,经火焰灼烧30秒,涂层表面温度达到850
±
50℃,从30秒到1500秒后,基体背部温度600
±
50℃。用火焰对涂层样品循环灼烧5次,每次灼烧时间均为1500秒,5次热循环后,涂层仍然完整,基体金属结构完好,涂层未出现任何剥落与脱落。
68.将最终得到的含稀土铝酸盐的耐高温复合涂层进行导热系数测试,用加拿大c-therm tci导热系数仪对含稀土铝酸盐的耐高温复合涂层切面样品于室温下进行测试,将十次重复测试值的算术平均值作为材料的导热系数值。
69.本发明得到的含稀土铝酸盐的耐高温复合涂层,金属粘接层的热膨胀系数(单位:10-6
/℃)为12.8~14.5,大气等离子喷涂稀土铝酸盐陶瓷层的热膨胀系数(单位:10-6
/℃)为9.6~10.1。
70.本发明得到的含稀土铝酸盐的耐高温复合涂层,1000℃条件下的热导率(单位w/m/k),稀土铝酸盐陶瓷层热导率为0.20~0.40。
71.实施例1
72.本实施例提供了一种含稀土铝酸盐的耐高温复合涂层的制备方法,采用该方法在某合金零件基体表面制备含稀土铝酸盐的耐高温复合涂层,具体细节如下:
73.步骤1:对合金零件基体进行微弧氧化处理,膜层厚度为18μm;
74.微弧氧化工艺为:电流波形为双向方波,脉冲波形频率180hz;正向电流密度为240a/dm2;负向电流密度为70a/dm2;正向占空比35%,负向占空比30%;微弧氧化时间为18min;微弧氧化槽液温度25℃。
75.步骤2:采用大气等离子喷涂工艺在步骤1处理后的微弧氧化膜层上制备一层金属粘结层;
76.喷涂粉末的成分是nicocraly,喷涂粉末粒径为35μm。
77.采用美科multicoat等离子喷涂设备大气等离子喷涂工艺参数为:氩气流量为30l/min,氢气流量为2l/min,电流大小控制为520a,功率为24kw,送粉氩气流量为1.5l/min,送粉速度为54g/min,喷涂距离为90mm,喷涂厚度为0.08mm。
78.步骤3:采用大气等离子喷涂工艺将稀土铝酸盐喷涂粉末沉积在步骤2的金属粘结层表面得到大气等离子喷涂稀土铝酸盐陶瓷层,从而完成合金零件表面涂层制备;
79.稀土铝酸盐喷涂粉末为将稀土氧化物与al2o3、mgo采用高温固相合成得到稀土铝酸盐粉末经喷雾干燥处理得到,la2o3与al2o3、mgo质量比满足:19.80wt%la2o3、7.92wt%mgo、71.29wt%al2o3、0.99wt%聚乙烯醇。稀土铝酸盐喷涂粉末粒径为30μm。
80.采用美科multicoat等离子喷涂设备大气等离子喷涂工艺参数为:氩气流量为35l/min,氢气流量为10l/min,电流大小控制为550a,功率为42kw,送粉氩气流量为2.2l/min,送粉速度为45g/min,喷涂距离为100mm,喷涂厚度为0.15mm。
81.上述制备方法中步骤3中的稀土铝酸盐喷涂粉末的制备方法包括以下步骤:
82.步骤301:将la2o3、mgo、al2o3按照20:8:72的质量百分比比例混合,采用马弗炉高温固相合成得到稀土铝酸盐粉末;高温固相合成的温度为1500℃,时间为48h;
83.步骤302:将步骤401得到的稀土铝酸盐粉末与去离子水、聚乙烯醇按照60:39.4:0.6比例混合,通过球磨工艺混合均匀得到浆料;球磨工艺为在行星式球磨机上球磨混合,所述行星式球磨机的公转速度为250r/min,自转速度为400r/min,搅拌时间为48h;
84.步骤303:对步骤402得到的浆料采用离心式喷雾干燥机进行喷雾干燥处理得到稀土铝酸盐喷涂粉末;喷雾干燥处理参数:出口温度为120℃,进口温度为280℃,浆料送料速度为2.8l/min,雾化盘转速为22000r/min。
85.实施例1得到的含稀土铝酸盐的耐高温复合涂层,从钛合金基底开始,由内到外依次为微弧氧化膜层、金属粘结层、大气等离子喷涂稀土铝酸盐陶瓷层。其中,微弧氧化膜层为金红石型和锐钛矿型tio2;金属粘结层为nicocraly。
86.实施例1得到的含稀土铝酸盐的耐高温复合涂层,其中,微弧氧化膜层的厚度为18μm,金属粘结层的厚度为0.08mm,稀土铝酸盐陶瓷层的厚度为0.15mm,该复合涂层总厚度为0.23mm。
87.实施例1得到的含稀土铝酸盐的耐高温复合涂层,金属粘结层的热膨胀系数(单位:10-6
/℃)为12.8,稀土铝酸盐陶瓷层的热膨胀系数(单位:10-6
/℃)为9.6。
88.实施例1得到的含稀土铝酸盐的耐高温复合涂层,1000℃条件下的热导率(单位w/m/k),稀土铝酸盐陶瓷层热导率为0.25。
89.实施例1得到的含稀土铝酸盐的耐高温复合涂层,经实验测得,结合强度达到33.6mpa。
90.实施例1得到的含稀土铝酸盐的耐高温复合涂层,经火焰灼烧30秒,涂层表面温度达到850℃,从30秒到1500秒后,基体背部温度580℃。用火焰对涂层样品循环灼烧5次,每次灼烧时间均为1500秒,5次热循环后,涂层仍然完整,基体金属结构完好,涂层未出现任何剥落与脱落。
91.实施例2
92.本实施例提供了一种含稀土铝酸盐的耐高温复合涂层的制备方法,采用该方法在某合金零件基体表面制备含稀土铝酸盐的耐高温复合涂层,具体细节如下:
93.步骤1:对合金零件基体进行微弧氧化处理,膜层厚度为20μm;
94.微弧氧化工艺为:电流波形:双向方波,脉冲波形频率300hz;正向电流密度为200a/dm2;负向电流密度为50a/dm2;正向占空比35%,负向占空比40%;微弧氧化时间为18min;微弧氧化槽液温度:30℃。
95.步骤2:采用大气等离子喷涂工艺在步骤1处理后的微弧氧化膜层上制备一层金属
粘结层;
96.喷涂粉末的成分是nicocraly,喷涂粉末粒径为50μm。
97.采用美科multicoat等离子喷涂设备大气等离子喷涂工艺参数为:氩气流量为20l/min,氢气流量为5l/min,电流大小控制为550a,功率为32kw,送粉氩气流量为2.5l/min,送粉速度为70g/min,喷涂距离为110mm,喷涂厚度为0.10mm。
98.步骤3:采用大气等离子喷涂工艺将稀土铝酸盐喷涂粉末沉积在步骤2的金属粘结层表面得到大气等离子喷涂稀土铝酸盐陶瓷层,从而完成合金零件表面复合涂层制备;
99.采用美科multicoat等离子喷涂设备大气等离子喷涂工艺参数为:氩气流量为45l/min,氢气流量为15l/min,电流大小控制为600a,功率为45kw,送粉氩气流量为3.2l/min,送粉速度为75g/min,喷涂距离为120mm,喷涂厚度为0.14mm。
100.稀土铝酸盐喷涂粉末为将稀土氧化物与al2o3、mgo采用高温固相合成得到稀土铝酸盐粉末经喷雾干燥处理得到,la2o3与al2o3、mgo质量比满足:14.89wt%la2o3、9.93wt%mgo、74.44wt%al2o3、0.74wt%聚乙烯醇。稀土铝酸盐喷涂粉末粒径为50μm。
101.上述制备方法中步骤3中的稀土铝酸盐喷涂粉末的制备方法包括以下步骤:
102.步骤301:将la2o3、mgo、al2o3按照15:10:75的质量百分比比例混合,采用马弗炉高温固相合成得到稀土铝酸盐粉末;高温固相合成的温度为1600℃,时间为48h;
103.步骤302:将步骤301得到的稀土铝酸盐粉末与去离子水、聚乙烯醇按照40:59.7:0.3比例混合,通过球磨工艺混合均匀得到浆料;球磨工艺为在行星式球磨机上球磨混合,所述行星式球磨机的公转速度为280r/min,自转速度为500r/min,搅拌时间为60h;
104.步骤303:对步骤302得到的浆料采用离心式喷雾干燥机进行喷雾干燥处理得到稀土铝酸盐喷涂粉末;喷雾干燥处理参数:出口温度为120℃,进口温度为300℃,浆料送料速度为4.8l/min,雾化盘转速为28000r/min。
105.实施例2得到的含稀土铝酸盐的耐高温复合涂层,从钛合金基底开始,由内到外依次为微弧氧化膜层、金属粘结层、稀土铝酸盐陶瓷层。其中,微弧氧化膜层为金红石型和锐钛矿型tio2;金属粘结层为nicocraly。
106.实施例2得到的含稀土铝酸盐的耐高温复合涂层,其中,微弧氧化膜层的厚度为20μm,金属粘结层的厚度为0.10mm,稀土铝酸盐陶瓷层的厚度为0.14mm,该含稀土铝酸盐的耐高温复合涂层总厚度为0.24mm。
107.实施例2得到的含稀土铝酸盐的耐高温复合涂层,金属粘结层的热膨胀系数(单位:10-6
/℃)为13.6,稀土铝酸盐陶瓷层的热膨胀系数(单位:10-6
/℃)为9.8。
108.实施例2得到的含稀土铝酸盐的耐高温复合涂层,1000℃条件下的热导率(单位w/m/k),稀土铝酸盐陶瓷层热导率为0.28。
109.实施例2得到的含稀土铝酸盐的耐高温复合涂层,经实验测得,结合强度达到30.6mpa。
110.实施例2得到的含稀土铝酸盐的耐高温复合涂层,经火焰灼烧30秒,涂层表面温度达到841℃,从30秒到1500秒后,基体背部温度604℃。用火焰对涂层样品循环灼烧5次,每次灼烧时间均为1500秒,5次热循环后,涂层仍然完整,基体金属结构完好,涂层未出现任何剥落与脱落。
111.实施例3
112.本实施例提供了一种含稀土铝酸盐的耐高温复合涂层的制备方法,采用该方法在某合金零件基体表面制备含稀土铝酸盐的耐高温复合涂层,具体细节如下:
113.步骤1:对合金零件基体进行微弧氧化处理,膜层厚度为10μm;
114.微弧氧化工艺为:电流波形:双向方波,脉冲波形频率200hz;正向电流密度为280a/dm2;负向电流密度为80a/dm2;正向占空比45%,负向占空比20%;微弧氧化时间为30min;微弧氧化槽液温度:18℃。
115.步骤2:采用大气等离子喷涂工艺在步骤1处理后的微弧氧化膜层上制备一层金属粘结层;
116.喷涂粉末的成分是nicocraly,喷涂粉末粒径为74μm。
117.采用美科multicoat等离子喷涂设备大气等离子喷涂工艺参数为:氩气流量为35l/min,氢气流量为8l/min,电流大小控制为500a,功率为22kw,送粉氩气流量为1.3l/min,送粉速度为40g/min,喷涂距离为70mm,喷涂厚度为0.09mm。
118.步骤3:采用大气等离子喷涂工艺将稀土铝酸盐喷涂粉末沉积在步骤2的金属粘结层表面得到大气等离子喷涂稀土铝酸盐陶瓷层,从而完成合金零件表面复合涂层制备;
119.稀土铝酸盐喷涂粉末为将稀土氧化物与al2o3、mgo采用高温固相合成得到稀土铝酸盐粉末经喷雾干燥处理得到,la2o3与al2o3、mgo质量比满足:14.89wt%la2o3、9.93wt%mgo、74.44wt%al2o3、0.74wt%聚乙烯醇。稀土铝酸盐喷涂粉末粒径为80μm。
120.采用美科multicoat等离子喷涂设备大气等离子喷涂工艺参数为:氩气流量为25l/min,氢气流量为5l/min,电流大小控制为500a,功率为25kw,送粉氩气流量为1.3l/min,送粉速度为35g/min,喷涂距离为85mm,喷涂厚度为0.14mm。
121.上述制备方法中步骤3中的稀土铝酸盐喷涂粉末的制备方法包括以下步骤:
122.步骤301:将la2o3、mgo、al2o3按照15:10:75的质量百分比比例混合,采用马弗炉高温固相合成得到稀土铝酸盐粉末;高温固相合成的温度为1200℃,时间为40h;
123.步骤302:将步骤301得到的稀土铝酸盐粉末与去离子水、聚乙烯醇按照40:59.7:0.3比例混合,通过球磨工艺混合均匀得到浆料;球磨工艺为在行星式球磨机上球磨混合,所述行星式球磨机的公转速度为170r/min,自转速度为380r/min,搅拌时间为30h;
124.步骤303:对步骤302得到的浆料采用离心式喷雾干燥机进行喷雾干燥处理得到稀土铝酸盐喷涂粉末;喷雾干燥处理参数:出口温度为100℃,进口温度为160℃,浆料送料速度为1.8l/min,雾化盘转速为18000r/min。
125.实施例3得到的含稀土铝酸盐的耐高温复合涂层,从钛合金基底开始,由内到外依次为微弧氧化膜层、金属粘结层、大气等离子喷涂稀土铝酸盐陶瓷层。其中,微弧氧化膜层为金红石型和锐钛矿型tio2;金属粘结层为nicocraly。
126.实施例3得到的含稀土铝酸盐的耐高温复合涂层,其中,微弧氧化膜层的厚度为10μm,金属粘结层的厚度为0.09mm,稀土铝酸盐陶瓷层的厚度为0.14mm,该涂层总厚度为0.23mm。
127.实施例3得到的含稀土铝酸盐的耐高温复合涂层,金属粘结层的热膨胀系数(单位:10-6
/℃)为14.5,稀土铝酸盐陶瓷层的热膨胀系数(单位:10-6
/℃)为10.1。
128.实施例3得到的含稀土铝酸盐的耐高温复合涂层,1000℃条件下的热导率(单位w/m/k),稀土铝酸盐陶瓷层热导率为0.33。
129.实施例3得到的含稀土铝酸盐的耐高温复合涂层,经实验测得,结合强度达到28.6mpa。
130.实施例3得到的含稀土铝酸盐的耐高温复合涂层,经火焰灼烧30秒,涂层表面温度达到846℃,从30秒到1500秒后,基体背部温度611℃。用火焰对涂层样品循环灼烧5次,每次灼烧时间均为1500秒,5次热循环后,涂层仍然完整,基体金属结构完好,涂层未出现任何剥落与脱落。
131.以上所述,仅为本发明较佳的具体实施方式,但本发明的保护范围并不局限于此,任何熟悉本技术领域的技术人员在本发明揭露的技术范围内,可轻易想到的变化或替换,都应涵盖在本发明的保护范围之内。