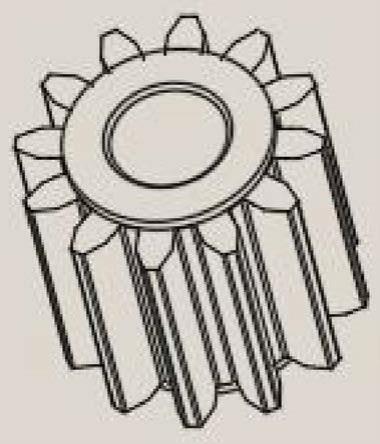
1.本发明涉及一种钛合金制品的制备方法,尤其涉及一种微米级钛合金制品的制备方法。
背景技术:
2.进入21世纪,人们对产品的轻量化要求日益增长。一系列的微系统技术应运而生,并显示出越来越重要的地位。随着微型结构这一领域的不断拓展,将需求有更多的微型结构件,满足性能和规模化生产的要求。传统的加工技术针对此类微结构零部件已明显力不从心,现有的先进硅刻蚀技术、石英晶体深槽湿法刻蚀技术、特种微型机械加工技术(微细电火花加工、微细激光成形加工、微细机械加工等)等加工技术虽然可以制备出符合使用要求的微型零件,但成本昂贵,且存在材料的局限性。粉末微注射成形(upim)技术,就是将粉末注射成形(pim)技术有机地运用到外形尺寸达微米级器件的制备上,并能满足高性价比的要求,从而成为制备微型元器件最具潜力的新技术。从基本工序看,upim与pim是相同的,由于制品的微型特征,导致了upim技术在成形工艺及成形设备等方面与传统的pim技术相比,都提出了更严格的要求,比如粉末的选择、粘结剂的配方、脱脂烧结工艺参数等。
3.钛及钛合金具有密度小、比强度高、无磁性、抗腐蚀以及生物相容性好等优点,是优质的金属结构材料和功能材料,在航空航天、汽车、发电、生物医药等领域得到了广泛应用,被誉为继钢铁、铝材之后处于发展中的“第三金属”和“战略金属”。但钛及钛合金的熔点和硬度高,加工、成型及切削性能差,因此,采用upim技术制备钛及钛合金的微型零件中的应用价值显得更为突出。目前微注射成形技术的研究大多集中于粘结剂制备以及陶瓷等材料体系。北京科技大学的尹海清公开了公开了一种粉末微注射成形用热塑性粘结剂的制备的使用方法,该粘结剂的成分为5~40%pw+5~20%bw+10~32%hdpe+10~ 40%eva+5~25%sa,其中各成分的含量为质量百分比(cn102775673a)。海精科粉末冶金科技有限公司的宋金帅公开了一种粉末微注射成形用水溶性粘结剂及制备方法,在恒温装置中,先将低熔点的聚乙二醇完全融化,然后放入称好的乙烯-乙酸乙烯酯和硬脂酸并不停搅拌,最后分批加入聚乙烯醇缩丁醛并强力搅拌直至得到均匀的乳状物,待其冷却后取出得到粘结剂成品;粘结剂中各组元质量分数为:分子量1000~2000的聚乙二醇20~40%、乙烯-乙酸乙烯酯20~40%、聚乙烯醇缩丁醛20~40%、硬脂酸5~10%(cn106589562a)。这些粘结剂体系都在不同程度上存在缺陷,蜡基体系虽然流动性较好,但溶剂脱脂效率低,所得制品的碳含量高,而水基体系的强度不够,且容易增加制品中的氧含量,钛合金的性能受杂质含量如碳、氧的影响很大,间隙杂质含量一旦控制不当,就会导致产品质量失控,造成废品,当产品具有微型特征后,这样的影响程度将大幅增加。哈尔滨工业大学的卢振提供了一种打印头陶瓷基板的微注射成型方法。具体步骤为:选取陶瓷粉末,粘结剂的配制,喂料的制备,微注射成型,将制备的喂料加入到微注射成形机中成型为注射坯,微注射成形机料筒的温度加热到180~240℃,喷嘴的温度加热到175~240℃,微注射压力为30~100mpa;热脱脂和预烧结,烧结,将成型坯料放入高温烧结炉中于空气气氛下进行烧结得到陶瓷基板,烧结温度为1400~2200℃,保温1~
3小时;后处理工艺,对陶瓷基板进行研磨和抛光(cn 101691086a)。综上所述,目前尚未有对钛合金的upim相关技术进行报道。
技术实现要素:
4.本发明为解决现有技术中存在的不足,提供一种微米级钛合金制品的制备方法,在粉末微注射成形的基础上,首次采用粉末级配技术与高流动性粘结剂体系相结合制备出尺寸精度高、力学性能优异的微米级钛合金零件,具有生产成本低、易于实现批量化生产等优势。
5.本发明一种微米级钛合金制品的制备方法,包括以下步骤:首先将钛合金粉末与粘结剂混炼、制粒,得到喂料;然后在微注射成形机中得到生坯;最后将生坯依次进行热脱脂、烧结致密化得到钛合金制品;所述钛合金粉末为粗粉和细粉混合而成,所述粗粉的平均粒度为15~30um,所述细粉的平均粒度为2~5um,细粉所占的质量百分比为10~20%;所述粘结剂,按质量百分比计由下述组分组成:聚丙烯腈65~75%,乙烯-醋酸乙烯共聚物10~20%,高密度聚乙烯10~20%,硬脂酸1~5%;所述烧结工艺为加压烧结、热等静压烧结、等离子放电烧结中任一一种。
6.作为优选方案,本发明一种微米级钛合金制品的制备方法,所述钛合金粉末由惰性气体雾化、等离子束旋转电极雾化和电极感应熔炼气雾化中的一种制备而得。
7.作为优选方案,本发明一种微米级钛合金制品的制备方法,所述钛合金粉末的牌号为tc4、tc9、tc11、tc21中的任一一种。
8.作为优选方案,本发明一种微米级钛合金制品的制备方法,所述混炼时,混炼温度为150~200℃、混炼时间为1~4h、混炼机转速为80~120r/min。
9.作为优选方案,本发明一种微米级钛合金制品的制备方法,所述喂料中,按体积比计,粘结剂:粉末=30~40%:60~70%。
10.作为优选方案,本发明一种微米级钛合金制品的制备方法,所述注射时,注射温度为150~180℃、注射压力为90~150mpa、模具温度为40~60℃。
11.作为优选方案,本发明一种微米级钛合金制品的制备方法,所述热脱脂工艺为:在氩气气氛保护下,先以1~3℃/min的升温速率加热至300~450℃保温1~4h,再以1~3℃/min的升温速率加热至500~600℃保温1~4h后随炉冷却至室温。
12.作为优选方案,本发明一种微米级钛合金制品的制备方法,所述加压烧结的保护气氛为氩气,烧结温度为800~1000℃,保温时间为1~2h,保压压力为100~300mpa,升温速率为10~20℃/min;所述热等静压烧结的保护气氛为氩气,烧结温度为900~1000℃,保温时间为0.5~1h,保压压力为100~300mpa,升温速率为100~300℃/min;所述等离子放电烧结的的保护气氛为氩气,烧结温度为800~900℃,保温时间为20~40min,保压压力为50~150mpa,升温速率为100~300℃/min。
13.作为优选方案,本发明一种微米级钛合金制品的制备方法,所述钛合金制品的最大尺寸不大于500um。
14.作为优选方案,本发明一种微米级钛合金制品的制备方法,所得钛合金制品的氧含量不大于0.25wt.%,抗拉强度不小于835mpa,屈服强度不小于765mpa,延伸率不小于5%,
尺寸精度为
±
0.3~0.5%。
15.原理与优势本发明基于粉末微注射成形技术,首先将钛合金粉末与粘结剂混炼、制粒,得到喂料;然后在微注射成形机中得到生坯;最后将生坯依次进行热脱脂、烧结致密化得到钛合金制品。粉末微注射成形与常规粉末注射成形工艺是相同的,但由于制品的微型特征,导致upim技术在工艺、设备等方面与传统的pim技术有更严格的要求。因此,针对钛合金的upim技术需从粉末选择、粘结剂的配制、注射工艺、脱脂工艺以及烧结工艺各方面逐一研究。
16.粉末的选择在整个upim工艺中起着关键的作用。upim所使用的粉末平均粒度一般小于3um,并且很多陶瓷粉末的平均粒度达到1um以下。同时,粉末的球形度越好,制品的形状精度和表面质量越好。但是,与不锈钢或者陶瓷不同,随着粒度的减小,比表面积增加,杂质元素含量也会随之增加,而钛合金的性能对杂质元素十分敏感,当氧含量超过0.3wt.%或碳含量超过0.1wt.%时,材料的延伸率降低到2%以下,无法满足作为功能结构材料的应用要求。因此,本发明采用粉末级配的方法,通过有效调控平均粒度为2~5um的钛合金细粉与平均粒度为15~30um的钛合金粗粉的比例,既可以避免杂质含量的增加,又能保证微型结构的尺寸和精度要求。同时,采用惰性气体雾化、等离子束旋转电极雾化或电极感应熔炼气雾化能够在完全惰性的气氛下进行,从而保持原料粉的高纯度,制得粉末形状呈球形且粒度分布相当宽,堆积性能好,也由此保证了制品的表面质量。
17.对于注射成型来说,粘结剂的组成是材料成型的关键。与常规的pim模具相比,微型模具的流道与型腔的壁厚比例更大,这就要求upim的注射料具有更好的流动性,以避免注射过程中注射料过早的凝固。另一方面,对于形状特别复杂的微小注射件,又要求能够完整地、安全地脱模。如果脱模失败,那么型芯的清洁工作就变得十分困难,而且其复杂、精细的微观结构也很可能被损坏。所以,粘结剂就扮演了一个十分重要的角色,来平衡和保证注射料良好的流动性和注射件较高的强度。pim钛合金常用的粘结剂体系有蜡基体系、聚甲醛体系和水基体系。蜡基体系粘结剂在pim工艺中占据着重要地位,但其溶剂脱脂效率低,所得制品的碳含量高,因此发展受限。对于聚甲醛体系而言,在注射过程中,由于聚甲醛可能发生分解产生毒性较大的甲醛,且催化脱脂过程中使用的强酸对设备的腐蚀作用较大,同时增加了后续热脱脂的时间,可能会出现氧含量的激增,所以,其规模化生产受到了限制。而水基体系的强度不够,且容易增加制品中的氧含量。如之前所述,钛合金的性能受杂质含量的影响很大,且当产品微型化后,这样的恶化程度将大幅增加。因此,本发明选择选择软化温度点低(95℃左右),流动性很好的聚丙烯腈作为填充剂,高密度聚乙烯和乙烯-醋酸乙烯共聚物作为骨架材料以提供生坯足够的强度,以及少量的硬脂酸作为表面分散剂或活性剂,不仅可以在粘结剂和粉末颗粒之间起桥接作用,以防止两相分离,保证混料均匀,而且可以在粉末颗粒之间、粉末颗粒与模壁之间起到润滑作用。通过调控配方比例获得高流动性高强度的upim钛合金新型粘结剂。
18.注射成形工序是指将混炼后的物料(喂料)进行注射成形的过程,在此工序中形成的缺陷在后续工艺中无法消除,因此必须严格控制该过程参数。在注射成形环节中,由于每次注射量都非常小,热量散失快,因此在注射时模具需要加热,同时注射后模具温度应能迅速降低,因为高的模具温度将使生坯的强度降低,进一步增加脱模的难度。除模具温度外,注射温度和注射压力等因素都对微注射过程有很大的影响。当注射温度提高时,熔体的黏
度降低,有利于塑料熔体进行充模;当注射温度保持在较高水平时,也有利于保压阶段的补缩,从而生坯制品密度较大,单重较大,成形的制品尺寸精度较高。在较大的注射压力下充模可以获取均匀的填充效果,减少制品残余应力的缘故。因为注射压力提高时,聚合物熔体能在较短的时间内充满型腔,熔体在凝固之前有充足的松弛时间,从而减少制品内部的残余应力。本发明通过调节注射温度、注射压力以及模具温度等重要upim注射参数以得到良好的注射坯,防止产品表面出现起泡、裂纹、孔隙等缺陷。
19.脱脂过程是最费时、最难控制的环节,包括几个不同的阶段,每一阶段只能除去黏结剂中的一种或几种成分;分阶段脱脂的目的是为了保持坯体形状,避免坍塌。从工艺和成本来说,脱脂时间应尽量短以防止坯体出现缺陷或发生变形,且控制碳、氧含量。目前,脱脂主要有溶剂脱脂、热脱脂和催化脱脂三种方式。本发明在充分分析现有粘结剂以及脱脂方法的优缺点后,确定采用流动性更好的聚丙烯腈作为填充剂,高密度聚乙烯和乙烯-醋酸乙烯共聚物作为骨架材料以提供生坯足够的强度,为了避免溶剂脱脂带来的碳含量的增加,采用热脱脂一步脱脂法来除去粘结剂,并有效控制相应的升温速率以及保温时间,将氧的增量控制在最小范围内,同时确保有机粘结剂脱除干净,避免残余的有机粘结剂在烧结过程中形成碳化物,引起碳含量的增加。与传统的脱脂工艺相比,提高了生产效率约,同时碳含量可以控制在800ppm以内,可以媲美铸造钛合金的性能。
20.烧结是upim工艺中非常重要的工序,对制品的组织、致密性能及化学性质均匀性起着决定性作用。钛合金的烧结一般为固相烧结,其主要传质方式为蒸发-凝聚传质和扩散传质,相对于液相烧结,其致密化比较困难。常常通过提高烧结温度来加快原子的扩散,以提高制品的相对密度,但这样很难防止晶粒的长大。同时,upim使用的小尺寸颗粒的比表面积较常规pim大颗粒粉末的大,烧结时驱动力大,采用相同烧结温度会导致晶粒长大的行为更突出。因此,本发明采用加压烧结、热等静压烧结或等离子放电烧结的方式,在低于粉体通常的烧结温度下,不会使晶粒聚集长大,并向钛合金粉末施加高压,使粉末颗粒出现了变形,增加粉末的实际接触面积,原子迁移距离缩小,致密化的完成较为迅速,得到细晶结构的制品。由此,通过应用这些烧结工艺,钛合金制品可达到100%致密,且具有晶粒细小,组织均匀,成分无偏析等良好的微观结构。再通过并控制升温速率以及保温时间避免坯体在烧结过程中出现变形,开裂等缺陷。
21.与现有技术相比,本发明在粉末微注射成形技术的基础上,采用粉末级配技术与高流动性粘结剂体系相结合制备出尺寸精度高、力学性能优异的微米级钛合金零件,其特点如下:1)高致密度,产品性能优异,可以媲美铸造钛合金的性能;2)新型粘结剂体系,杂质含量低;3)一步脱脂法,生产效率高,易于实现大批量生产;综上所述,本发明在粉末微注射成形技术的基础上,首次提出的粉末级配技术与高流动性粘结剂体系,并同步优化upim所涉及的注射、脱脂以及烧结工艺参数,大幅降低碳、氧杂质含量,获得性能可以媲美铸造钛合金的微米级钛合金零件,具有尺寸精度高、生产成本低、易于实现批量化生产等优势,能很好的满足商业化需求。
附图说明
22.图1是钛合金制品示意图。
具体实施方式
23.以下结合三个实施例对本发明方法作进一步说明。
24.实施例1:一种微米级钛合金制品的制备方法,其过程如下:a、原料准备:钛合金粉末由惰性气体雾化法制得,由粗粉和细粉混合而成,粗粉的平均粒度为25um,所述细粉的平均粒度为3um,细粉所占的质量百分比为10%。
25.b、制备粘结剂:按质量百分比,取聚丙烯腈68%,乙烯-醋酸乙烯共聚物12%,高密度聚乙烯17%,硬脂酸3%制成粘结剂;c、制备喂料:将粘结剂与钛合金材料按照体积比32%:68%进行混炼、制粒制成喂料,混炼温度为180℃,混炼机转速为90r/min,混炼时间为4h;d、注射成形:利用微注射成形机将喂料注入到模腔中得到产品生坯;注射温度为160℃,注射压力为110mpa,模具温度为60℃;e、脱脂:将产品生坯在真空脱脂炉中进行热脱脂,在氩气气氛保护中,先以2℃/min的升温速率加热至350℃保温1h,再以1℃/min的升温速率加热至500℃保温2h后随炉冷却至室温;f、烧结:将脱脂后的产品坯体在加压炉内进行烧结;充氩气前炉内真空度为5*10-3pa,再升温并充入氩气,烧结压力为300mpa(由氩气提供),以10℃/min的升温速率加热至900℃保温1h随炉冷却至室温,即可获得成品。
26.g、性能检测,所得钛合金制品的氧含量为0.23wt.%,抗拉强度为845mpa,屈服强度为770mpa,延伸率为8%,尺寸精度为
±
0.35%。
27.实施例2:一种微米级钛合金制品的制备方法,其过程如下:a、原料准备:钛合金粉末由等离子束旋转电极雾化法制得,由粗粉和细粉混合而成,粗粉的平均粒度为20um,所述细粉的平均粒度为4um,细粉所占的质量百分比为15%。
28.b、制备粘结剂:按质量百分比,取聚丙烯腈69%,乙烯-醋酸乙烯共聚物13%,高密度聚乙烯15%,硬脂酸3%制成粘结剂;c、制备喂料:将粘结剂与钛合金材料按照体积比32%:68%进行混炼、制粒制成喂料,混炼温度为180℃,混炼机转速为90r/min,混炼时间为4h;d、注射成形:利用微注射成形机将喂料注入到模腔中得到产品生坯;注射温度为160℃,注射压力为120mpa,模具温度为60℃;e、脱脂:将产品生坯在真空脱脂炉中进行热脱脂,在氩气气氛保护中,先以2℃/min的升温速率加热至350℃保温1h,再以1℃/min的升温速率加热至500℃保温2h后随炉冷却至室温;f、烧结:将脱脂后的产品坯体在热等静压炉内进行烧结;充氩气前炉内真空度为5*10-3pa,再升温并充入氩气,烧结压力为200mpa(由氩气提供),以300℃/min的升温速率加热至900℃保温0.5h随炉冷却至室温,即可获得成品。
29.g、性能检测,所得钛合金制品的氧含量为0.20wt.%,抗拉强度为862mpa,屈服强度为777mpa,延伸率为9%,尺寸精度为
±
0.35%。
30.实施例3:一种微米级钛合金制品的制备方法,其过程如下:a、原料准备:钛合金粉末由电极感应熔炼气雾化法制得,由粗粉和细粉混合而成,粗粉的平均粒度为30um,所述细粉的平均粒度为3um,细粉所占的质量百分比为20%。
31.b、制备粘结剂:按质量百分比,取聚丙烯腈70%,乙烯-醋酸乙烯共聚物15%,高密度聚乙烯13%,硬脂酸2%制成粘结剂;c、制备喂料:将粘结剂与钛合金材料按照体积比32%:68%进行混炼、制粒制成喂料,混炼温度为180℃,混炼机转速为90r/min,混炼时间为4h;d、注射成形:利用微注射成形机将喂料注入到模腔中得到产品生坯;注射温度为170℃,注射压力为150mpa,模具温度为60℃;e、脱脂:将产品生坯在真空脱脂炉中进行热脱脂,在氩气气氛保护中,先以2℃/min的升温速率加热至350℃保温1h,再以1℃/min的升温速率加热至500℃保温2h后随炉冷却至室温;f、烧结:将脱脂后的产品坯体在放电等离子炉内进行烧结;充氩气前炉内真空度为5*10-3pa,再升温并充入氩气,烧结压力为100mpa(由氩气提供),以300℃/min的升温速率加热至800℃保温20min随炉冷却至室温,即可获得成品。
32.g、性能检测,所得钛合金制品的氧含量为0.20wt.%,抗拉强度为878mpa,屈服强度为789mpa,延伸率为10%,尺寸精度为
±
0.35%。
33.对比例1-1:本对比例采用与实施例3基本相同的方法,不同的是,钛合金粉末只包含粗粉,所得钛合金制品的尺寸精度为
±
0.7%,表面质量不佳。
34.对比例1-2:本对比例采用与实施例3基本相同的方法,不同的是,钛合金粉末只包含细粉,所得钛合金制品的氧含量达到0.62wt.%,抗拉强度为825mpa,屈服强度为733mpa,延伸率为2%,力学性能因氧含量过高大幅降低。
35.对比例1-3:本对比例采用与实施例3基本相同的方法,不同的是,钛合金粉末中细粉的质量比为40%,所得钛合金制品的氧含量达到0.4wt.%,抗拉强度为834mpa,屈服强度为745mpa,延伸率为4%,力学性能因氧含量高而降低。
36.对比例2-1:本对比例采用与实施例3基本相同的方法,不同的是,粘结剂按如下质量百分比配制,聚丙烯腈85%,乙烯-醋酸乙烯共聚物8%,高密度聚乙烯5%,硬脂酸2%。结果发现喂料流动性过好,强度不够,烧结后变形。
37.对比例2-2:本对比例采用与实施例3基本相同的方法,不同的是,粘结剂按如下质量百分比配制,聚丙烯腈55%,乙烯-醋酸乙烯共聚物22%,高密度聚乙烯22%,硬脂酸1%。结果发现喂料强度高,但流动性性不好,成品率不到30%。
38.对比例3-1本对比例采用与实施例3基本相同的方法,不同的是,将产品生坯先通过二氯甲烷的溶剂脱脂,脱脂时间为4h温度为45℃,所得钛合金制品的碳含量达到0.2wt.%,延伸率仅为2.5%。
39.对比例3-2本对比例采用与实施例3基本相同的方法,不同的是,采用常压烧结工艺,具体步骤为:将脱脂后的产品坯体在真空烧结炉内进行烧结;炉内真空度为5*10-3pa,以5℃/min的速度加热至1250℃保温4h后随炉冷却至室温。检测性能,所得钛合金制品的氧含量达到0.35wt.%,抗拉强度为855mpa,屈服强度为756mpa,延伸率为5%,力学性能因氧含量和晶粒尺寸较高而降低。
40.以上所述实例仅是本发明较优的实施方法,故不能以此限定本发明的实施范围,其他按照本发明的原理和内容所做的等效改变、修饰、替代和组合,都仍属于本发明的保护范围。