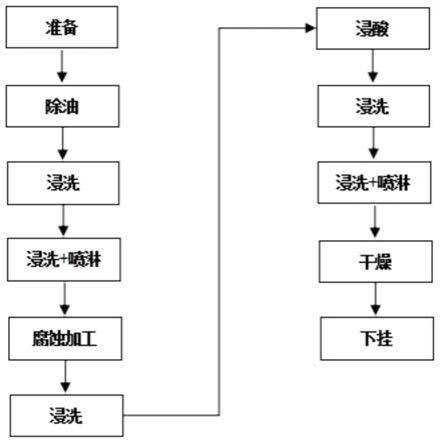
1.本发明涉及腐蚀加工技术领域,具体涉及一种高铌钛铝合金的腐蚀加工方法。
背景技术:
2.钛铝合金由于密度小、高温强度优异、抗氧化性和抗蠕变性良好等优异性能,因而成为有巨大应用潜力的先进高温结构材料。但普通钛铝合金的室温塑性和断裂韧性较差,在800℃以上抗高温蠕变和抗高温氧化性能较差,这些缺点严重限制了钛铝合金在航空航天、汽车等领域中的应用范围。
3.为了改善钛铝合金的室温塑性和高温抗氧化性能,添加高含量、高熔点的过渡族元素nb,可以有效提高合金的熔点,使用温度达到900℃以上,具有优异的抗氧化性能。但是其机械加工性能较普通钛合金更差,给实际应用带来较大困难。腐蚀加工是解决钛铝合金机械加工困难的一种有效方法,它是依靠化学溶解对工件表面溶解的一种加工技术。钛合金腐蚀加工在航空航天领域有着广阔的应用前景:(1)加工薄壁工件,减重,满足轻量化的要求;(2)去除铸件表面α层,降低铸件表面粗糙度,满足应用要求。
4.高铌钛铝合金是一种新金属材料,高铌钛铝合金是由ti、a1、nb、c、w、y组成,其中a1含量为45~46%,nb含量为8~10%,c含量为0~0.2%,w含量为о~0.2%、y含量为0~0.1%(以上均为原子百分比),余量为ti,合金的组织由y和α2两个有序相组成,在变形合金和铸造合金中得到均匀的细晶全片层组织,晶粒100~150um,片间距0.3~0.4um,其优点在于:高铌钛铝合金的使用温可达到840~900℃,它比现在使用的一般银钛合金有更高的使用温度,被国际上普遍接受,并认为高铌钛铝合金可以替代高性能变形镍基高温合金,密度大约是镍基高温合金的一半,使部件有显著的减少重量的作用。
5.而作为新一代航空航天用发动机材料的高铌钛铝合金材料即将步入产业化阶段,这一技术将使我国航空航天发动机材料居世界领先水平,高铌钛铝合金的应用将开辟航空航天、船舰、汽车等重要领域的新发展,使现有装备得到突破性发展,将使产品的设计和市场产生全新改变、有更新换代和突破性意义与巨大效益。
6.现有技术存在以下不足:铸造高铌钛铝合金机械加工困难,目前腐蚀加工工艺处理铸造高铌钛铝合金速率极低(单面0.001mm/min-0.003mm/min),粗糙度很大,表面暗黑无金属光泽,无法达到应用要求,且无法及时掌握以及控制高铌钛铝合金铸件的腐蚀状态、速度以及某些与腐蚀相关的参数,确定高铌钛铝合金铸件的腐蚀状况,给出明确的腐蚀诊断信息。
技术实现要素:
7.为此,本发明提供一种高铌钛铝合金的腐蚀加工方法,以解决现有技术中铸造高铌钛铝合金机械加工困难,目前腐蚀加工工艺处理铸造高铌钛铝合金速率极低(单面0.001mm/min-0.003mm/min),粗糙度很大,表面暗黑无金属光泽,无法达到应用要求的问题。
8.为了实现上述目的,本发明实施例提供如下技术方案:一种高铌钛铝合金的腐蚀加工方法,包括以下具体步骤:
9.步骤一、静电除尘:通过高压直流电使得两个金属阳极和阴极上形成维持一个气体电离的电场;
10.步骤二、吹砂:介质棕刚玉,颗粒大小为54-120目,吹砂距离10-12cm,压力0.4-0.6mpa;
11.步骤三、除油:经步骤二处理的高铌钛铝合金铸件用丙酮进行物理除油,去除表面残余的油污或记号,辅以超声波搅拌,之后用流动水清洗;
12.步骤四、腐蚀加工:经步骤三处理的高铌钛铝合金铸件置于腐蚀加工溶液中,辅以机械和空气搅拌处理10-30min,腐蚀加工后高铌钛铝合金铸件经流动水洗;
13.步骤五、腐蚀程度检测:根据金属探针被腐蚀后的电阻变化情况,间接反映出金属的腐蚀速率;
14.步骤六、浸酸:经步骤四处理的高铌钛铝合金铸件置于浸酸液中,辅以机械和空气搅拌处理1-5min,浸酸后高铌钛铝合金铸件经至少两道流动水洗;
15.步骤七、干燥:80-120℃烘箱烘干或65-95℃热水洗后烘干。
16.进一步的,在步骤一中,静电除尘的过程为:将两个曲率半径相差较大的金属阳极和阴极上,金属阳极由不同几何形状的金属板制成,也称为集尘电极,阴极由不同断面形状的金属导线制成,也称为放电电极,通过高压直流电,维持一个足以使气体电离的电场,气体电离后所产生的电子:阴离子和阳离子,吸附在通过电场的粉尘上,使粉尘获得电荷,荷电极性不同的粉尘在电场力的作用下,分别向不同极性的电极运动,沉积在电极上,而达到粉尘和气体分离的目的。
17.进一步的,在步骤三中,除油液组分及参数为:
18.daraclean282
ꢀꢀꢀꢀꢀꢀꢀꢀꢀꢀꢀ
5%-15%(v%);
19.去离子水(<20μs/cm)
ꢀꢀꢀꢀ
剩余;
20.温度为40℃-50℃。
21.进一步的,在步骤四中,腐蚀加工液组分及参数为:
22.氢氟酸
ꢀꢀꢀꢀꢀꢀꢀꢀꢀꢀꢀꢀꢀꢀ
30g/l-120g/l;
23.硝酸/氢氟酸质量比
ꢀꢀꢀꢀꢀꢀ
1.5-4;
24.去离子水(<20μs/cm)
ꢀꢀꢀꢀ
剩余;
25.温度为20℃-40℃。
26.进一步的,在步骤五中,将安装有一个高铌钛铝合金材质的试片的电阻探针插入腐蚀加工溶液中,则试片横截面积将因腐蚀而减小,导致其电阻增大,如果试片的腐蚀基本上是均匀的,则电阻的变化与试片的腐蚀量成正比,经过多次周期性地精准测量这种电阻的增加,实际测量的是试片与不受腐蚀的参考试片时间的电阻比的变化量,便能够计算出经过该段时间后的总腐蚀量,从而算出高铌钛铝合金铸件的腐蚀加工速率。
27.进一步的,在步骤六中,浸酸液组分及参数为:
28.氢氟酸
ꢀꢀꢀꢀꢀꢀꢀꢀꢀꢀꢀꢀꢀꢀ
15g/l-30g/l;
29.硝酸/氢氟酸质量比
ꢀꢀꢀꢀꢀꢀ
10-25;
30.去离子水(<20μs/cm)
ꢀꢀꢀꢀ
剩余;
31.温度为15℃-35℃。
32.进一步的,高铌钛铝合金铸件表面粗糙度ra≤3.0μm,具有金属光泽,表面晶粒明显。
33.进一步的,通过电阻探针实时监测高铌钛铝合金铸件的腐蚀加工速率,以便腐蚀加工速率能达到单面0.005mm/min-0.020mm/min,且公差达到10%以内。
34.本发明实施例具有如下优点:
35.1、本发明能以较高的速率(0.005mm/min-0.020mm/min)腐蚀加工,无需任何添加剂,加工温度范围(15-40℃)较宽易达到,过程中辅以机械循环泵喷嘴喷射和压缩空气双搅拌,加工后表面粗糙度小于3.0μm,与现有技术相比,表面具有金属光泽和明显晶粒,可以满足多领域的应用;
36.2、本发明通过在吹砂工艺之前先进行静电除尘,提高高铌钛铝合金铸件的表面的清洁度,使得吹砂工艺达到更好的效果,并在腐蚀加工的过程中对高铌钛铝合金铸件的俯腐蚀程度进行监测,以便更及时地掌握高铌钛铝合金铸件的腐蚀精度,与现有技术相比,对高铌钛铝合金铸件的腐蚀状态、速度以及某些与腐蚀相关的参数进行计算,确定高铌钛铝合金铸件的腐蚀状况,给出明确的腐蚀诊断信息。
附图说明
37.为了更清楚地说明本发明的实施方式或现有技术中的技术方案,下面将对实施方式或现有技术描述中所需要使用的附图作简单地介绍。显而易见地,下面描述中的附图仅仅是示例性的,对于本领域普通技术人员来讲,在不付出创造性劳动的前提下,还可以根据提供的附图引伸获得其它的实施附图。
38.本说明书所绘示的结构、比例、大小等,均仅用以配合说明书所揭示的内容,以供熟悉此技术的人士了解与阅读,并非用以限定本发明可实施的限定条件,故不具技术上的实质意义,任何结构的修饰、比例关系的改变或大小的调整,在不影响本发明所能产生的功效及所能达成的目的下,均应仍落在本发明所揭示的技术内容得能涵盖的范围内。
39.图1为本发明的方法流程图;
40.图2为本发明腐蚀加工后的铸造高铌钛铝合金表面形貌图。
具体实施方式
41.以下由特定的具体实施例说明本发明的实施方式,熟悉此技术的人士可由本说明书所揭露的内容轻易地了解本发明的其他优点及功效,显然,所描述的实施例是本发明一部分实施例,而不是全部的实施例。基于本发明中的实施例,本领域普通技术人员在没有做出创造性劳动前提下所获得的所有其他实施例,都属于本发明保护的范围。
42.实施例1:
43.本发明提供了一种高铌钛铝合金的腐蚀加工方法,包括以下具体步骤:
44.步骤一、静电除尘:通过高压直流电使得两个金属阳极和阴极上形成维持一个气体电离的电场;
45.静电除尘的过程为:将两个曲率半径相差较大的金属阳极和阴极上,金属阳极由不同几何形状的金属板制成,也称为集尘电极,阴极由不同断面形状的金属导线制成,也称
为放电电极,通过高压直流电,维持一个足以使气体电离的电场,气体电离后所产生的电子:阴离子和阳离子,吸附在通过电场的粉尘上,使粉尘获得电荷,荷电极性不同的粉尘在电场力的作用下,分别向不同极性的电极运动,沉积在电极上,而达到粉尘和气体分离的目的。
46.步骤二、将铸造高铌钛铝合金(8.0nb)先进行吹砂处理,吹砂介质棕刚玉,颗粒大小为80目,吹砂距离10cm,压力0.4mpa。
47.步骤三、除油:经步骤二处理的铸件用丙酮进行物理除油,去除表面残余的油污或记号,辅以超声波搅拌,之后用流动水清洗;化学除油的成分为:daraclean282体积分数10%,去离子水(<20μs/cm),将铸件放入45℃的化学除油液中处理12min,铸件除油后经两道流动水洗并喷淋后,必须保证整个铸件表面亲水,连续水膜30s以上,则认为除油合格。
48.步骤四、腐蚀加工:经步骤三处理的铸件置于腐蚀加工溶液中,辅以机械和空气搅拌处理15min,温度为30℃
±
2℃,腐蚀加工后铸件经流动水洗;腐蚀加工液组分为:氢氟酸90g/l,硝酸/氢氟酸质量比4。
49.步骤五、腐蚀程度检测:根据金属探针被腐蚀后的电阻变化情况,间接反映出金属的腐蚀速率;
50.将安装有一个高铌钛铝合金材质的试片的电阻探针插入腐蚀加工溶液中,则试片横截面积将因腐蚀而减小,导致其电阻增大,如果试片的腐蚀基本上是均匀的,则电阻的变化与试片的腐蚀量成正比,经过多次周期性地精准测量这种电阻的增加,实际测量的是试片与不受腐蚀的参考试片时间的电阻比的变化量,便能够计算出经过该段时间后的总腐蚀量,从而算出高铌钛铝合金铸件的腐蚀加工速率。
51.步骤六、浸酸:经步骤四处理的铸件置于浸酸液中,辅以机械和空气搅拌处理2min,温度为20℃,浸酸后铸件经至少两道流动水洗;浸酸液组分为:氢氟酸20g/l,硝酸/氢氟酸质量比18。
52.步骤七、干燥:80℃热水洗后压缩空气吹干。
53.高铌钛铝合金铸件表面粗糙度ra≤3.0μm,具有金属光泽,表面晶粒明显。
54.通过电阻探针实时监测高铌钛铝合金铸件的腐蚀加工速率,以便腐蚀加工速率能达到单面0.005mm/min-0.020mm/min,且公差达到10%以内。
55.实施例2:
56.本发明提供了一种高铌钛铝合金的腐蚀加工方法,包括以下具体步骤:
57.步骤一、静电除尘:荷电粉尘的捕集过程:通过高压直流电使得两个金属阳极和阴极上形成维持一个气体电离的电场;
58.静电除尘的过程为:将两个曲率半径相差较大的金属阳极和阴极上,金属阳极由不同几何形状的金属板制成,也称为集尘电极,阴极由不同断面形状的金属导线制成,也称为放电电极,通过高压直流电,维持一个足以使气体电离的电场,气体电离后所产生的电子:阴离子和阳离子,吸附在通过电场的粉尘上,使粉尘获得电荷,荷电极性不同的粉尘在电场力的作用下,分别向不同极性的电极运动,沉积在电极上,而达到粉尘和气体分离的目的。
59.步骤二、将铸造高铌钛铝合金(7.5nb)先进行吹砂处理,吹砂介质棕刚玉,颗粒大小为120目,吹砂距离10cm,压力0.6mpa。
60.步骤三、除油:经步骤二处理的铸件用丙酮进行物理除油,去除表面残余的油污或记号,辅以超声波搅拌,之后用流动水清洗;化学除油的成分为:daraclean282体积分数12%,去离子水(<20μs/cm),将铸件放入45℃的化学除油液中处理12min,铸件除油后经两道流动水洗并喷淋后,必须保证整个铸件表面亲水,连续水膜30s以上,则认为除油合格。
61.步骤四、腐蚀加工:经步骤三处理的铸件置于腐蚀加工溶液中,辅以机械和空气搅拌处理15min,温度为40℃
±
2℃,腐蚀加工后铸件经流动水洗;腐蚀加工液组分为:氢氟酸120g/l,硝酸/氢氟酸质量比3。
62.步骤五、腐蚀程度检测:根据金属探针被腐蚀后的电阻变化情况,间接反映出金属的腐蚀速率;
63.将安装有一个高铌钛铝合金材质的试片的电阻探针插入腐蚀加工溶液中,则试片横截面积将因腐蚀而减小,导致其电阻增大,如果试片的腐蚀基本上是均匀的,则电阻的变化与试片的腐蚀量成正比,经过多次周期性地精准测量这种电阻的增加,实际测量的是试片与不受腐蚀的参考试片时间的电阻比的变化量,便能够计算出经过该段时间后的总腐蚀量,从而算出高铌钛铝合金铸件的腐蚀加工速率。
64.步骤六、浸酸:经步骤四处理的铸件置于浸酸液中,辅以机械和空气搅拌处理2min,温度为20℃,浸酸后铸件经至少两道流动水洗;浸酸液组分为:氢氟酸22g/l,硝酸/氢氟酸质量比15。
65.步骤七、干燥:80℃热水洗后压缩空气吹干。
66.高铌钛铝合金铸件表面粗糙度ra≤3.0μm,具有金属光泽,表面晶粒明显。
67.通过电阻探针实时监测高铌钛铝合金铸件的腐蚀加工速率,以便腐蚀加工速率能达到单面0.005mm/min-0.020mm/min,且公差达到10%以内。
68.上述两个实施例腐蚀加工后的表面如图2所示,左边a-i为铸造高铌钛铝合金(8.0nb)加工后表面形貌,实施例1是c图;右边a-i为铸造高铌钛铝合金(7.0nb)加工后表面形貌,实施例2是d图。采用德国马尔公司的marsurf ps 10表面粗糙度测量仪进行测试,粗糙度均在3.0μm以下,表面粗糙度良好,有金属光泽,符合工艺要求。使用电子天平称量试片重量p1并记录,而后将试片,吊挂试片材料应为聚丙烯丝线,使用秒表测试腐蚀加工时间,取出测试片后用水冲洗、测试干燥后,称量测试片重量p2并记录,根据以下公式计算溶解速率(毫米/分钟mm/min)。测试片尺寸约为100mm
×
50mm
×
(1-5)mm。天平分度值:0.001g。r=(1000(p1-p2)/(s
×
d))/t0,其中:r试片的溶解速率mm/min,p1腐蚀前试片重量g
±
0.001g,p2腐蚀后试片重量g
±
0.001g,s测试片全面积mm2,d材料密度g/cm3,t0腐蚀时间min。两个实施例腐蚀加工速率均高于单面0.005mm/min,符合腐蚀加工要求。
69.虽然,上文中已经用一般性说明及具体实施例对本发明作了详尽的描述,但在本发明基础上,可以对之作一些修改或改进,这对本领域技术人员而言是显而易见的。因此,在不偏离本发明精神的基础上所做的这些修改或改进,均属于本发明要求保护的范围。