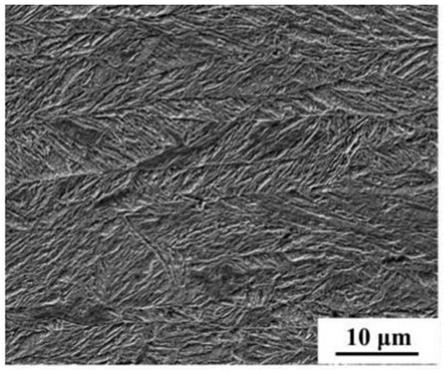
一种nm400级dq型马氏体耐磨钢板及其制备方法
技术领域
1.本发明属于冶金技术领域,具体涉及一种nm400级dq型马氏体耐磨钢板及其制备方法。
背景技术:
2.低合金耐磨钢一般来说具有几个特点:合金含量较低,一般为3%~5%,甚至更低,所添加的元素多为资源较为丰富的元素,少含或不含贵重稀有元素,成本低,易于推广使用;具有良好的强韧性能配合等综合性能,可在较大范围进行强韧性配合,从而使其在各类工况下得到良好的耐磨性。成分简单,在设计上存在与普通碳钢之间的互换性,因此生产简易灵活,价格相对低廉。国内耐磨钢板以nm360和nm400为主,能生产400hbw级别以上的耐磨钢板企业较少,且热处理工艺并不成熟,且整体的成分设计合金含量较高。
3.目前马氏体耐磨钢生产主要采取离线热处理(淬火+回火)工艺,其基体组织均为板条马氏体,得到高的强度和硬度,保证了耐磨性能,但马氏体本身具有高脆性的特点,使得钢板的成型性较差,且传统生产工艺为轧后进行离线淬火+回火处理不仅流程长,工艺能耗大,对轧制后热处理设备要求高,导致成本高、生产效率低,产量远不能满足市场需求,为马氏体耐磨钢的普及应用增添了很多障碍。随着tmcp设备与技术的发展,在线淬火(dq)工艺逐渐应用到中厚板生产中。在线淬火工艺可以省去离线奥氏体化过程,缩短生产流程,提高生产效率,降低生产能耗和生产成本。目前,国内对在线淬火生产马氏体耐磨钢技术仍不成熟,在线淬火后表面及芯部组织均匀性较差,导致性能均匀性较差。
4.专利文献cn106987760a公开了一种在线淬火生产薄规格高ti耐磨钢nm400的方法,其化学成分为c:0.12-0.20%,si:0.20-0.40%,mn:1.2-1.8%,mo:0.15-0.30%,cr:0.20-0.50%,nb:0.030-0.060%,ti:0.10-0.15%,al:0.015-0.045%,b:0.0006-0.0015%,p≤0.015%,s≤0.010%,其钢带采用薄板坯连铸连轧和超快速冷却淬火工艺生产耐磨钢,但生产成品仅试用于板厚小于4mm的钢板,-20℃条件下,夏比v形冲击功分别为58j、69j、63j,冲击性能较差。
5.专利文献cn111440996a公开一种6-8mm tmcp在线淬火低屈强比高强耐磨钢nm400卷板及其制备方法,其化学成分为c:0.18-0.22%、si:0.30-0.50%、mn:1.30-1.45%、p≤0.012%、s≤0.003%、nb:0.015-0.025%、ti:0.010-0.025%、cr:0.25-0.40%、b:0.0005-0.0020、ca:0.0010-0.0030%、al:0.020-0.050%、h≤2ppm,o≤30ppm,n≤50ppm,余量为fe和不可避免的杂质。采用该文献所述的成分和在线淬火工艺生产的耐磨钢性能满足要求。但该生产钢板的厚度范围较小,同时冷却工艺采用两阶段冷却方式,对冷却设备和控温设备要求较高,所生产钢板-20℃冲击功≥56j,冲击韧性较低。
6.专利文献cn108754317a公开一种低合金耐磨钢nm400厚板及制造方法,其化学成分为c:0.20-0.33%,si:0.20-0.60%,mn:0.50-1.10%,p≤0.012%,s≤0.003%,cr:0.30-1.00%,mo:0.20-0.60%,ni:0.30-0.80%,ti:0.008-0.030%,nb:0.015-0.050%,b:0.0008-0.0025%,n≤0.0040%,o≤0.0025%,余量为fe和不可避免的杂质。其钢板厚度较高,需要添
加的淬透性cr、ni元素含量较高,容易产生回火脆性,同时采用离线热处理工艺,工艺流程长,对离线热处理设备要求高,提高生产成本。
7.专利文献cn112322976a公开一种具有优良耐低温韧性的稀土耐磨钢nm400卷板及其制备方法,其化学成分为c:0.18-0.20%、si:0.30-0.50%、mn:1.30-1.45%、p≤0.012%、s≤0.003%、nb:0.015-0.025%、ti:0.010-0.025%、cr:0.25-0.40%、ce:0.0005-0.0015%、ca:0.0010-0.0030%、als:0.020-0.050%、h≤2ppm,o≤30ppm,n≤50ppm,余量为fe和不可避免的杂质。其成品冲击韧性好,-40℃冲击功≥64j,但添加稀土元素使得成本上升。
技术实现要素:
8.为解决上述技术问题,本发明提供一种工艺简单、生产成本低、生产周期短且综合性能良好的nm400级dq型马氏体耐磨钢板及其制备方法。
9.为实现上述目的,本发明采取的技术方案是:一种nm400级dq型马氏体耐磨钢板,其化学成分组成及质量百分含量为:c:0.14~0.16%,si:0.25~0.30%,mn:1.00~1.40%,mo:0.20~0.25%,cr:0.20~0.25%,ti:0.010~0.015%,nb:0.025~0.030%,ni:0.20~0.25%,v:0.0030~0.0040%,b:0.0014~0.0016%,p≤0.010%,s≤0.003%,n≤0.005%,余量为fe及不可避免的杂质;所述耐磨钢板采用在线淬火+离线回火的热处理工艺制备。
10.所述耐磨钢板的厚度为10~25mm;其维氏硬度为390~420hv,抗拉强度rm:1100~1400mpa,屈服强度rp0.2:1000~1200mpa,伸长率:10~12%,-40℃低温冲击韧性≥100j/cm2。
11.上述nm400级dq型马氏体耐磨钢板的制备方法,包括加热、粗轧、精轧、热处理工序,采用在线淬火+离线回火的热处理工艺,具体操作为:钢板精轧后层流冷却至100~120℃,冷却速度20~30℃/s,随后空冷至室温,再进行离线回火。
12.所述离线回火的温度为200~220℃,回火时间70~150min。
13.所述回火时间为5~6min/mm,且回火时间不低于70min。
14.所述加热工序,加热至1200~1300℃保温120~180min。
15.所述粗轧工序,粗轧温度为930~1200℃,为5~7道次轧制,单道次变形量为20~30%。
16.所述精轧工序,精轧温度为800~930℃,为4~6道次轧制,单道次变形量为10~15%。
17.本发明的化学成分组成及其质量百分含量设计思路为:(1)本发明中碳是影响钢板强度、硬度、韧性及淬透性、耐磨性的至关重要的元素,碳量过高,热处理后形成的高碳马氏体硬度高,热处理时易形成裂纹,同时碳元素含量过高又会对钢的韧性和焊接性能造成不利的影响,耐磨钢材料对韧性和焊接性能有一定的要求,所以在满足耐磨钢强度和硬度的条件下,应该把碳元素的含量保持在比较低的范围内。综合考虑,碳含量为0.14%~0.16%时,钢板既能获得高硬度,又具备一定的韧塑性和焊接性能。
18.(2)本发明中硅元素在钢中起固溶强化作用,固溶于奥氏体或铁素体中,固溶强化
作用仅次于碳元素,提高硅含量有利于提高钢的强度和硬度,且能提高奥氏体的稳定性,降低钢的临界冷却速度并提高钢的淬透性;硅还能使钢发生低温回火脆性的温度范围提高,能有效地提高钢的抗回火性能。硅元素提高钢中固溶体的强度和冷加工变形硬化率的作用极强,仅次于磷。同时硅元素在一定程度上也会降低钢的韧性和塑性,对耐磨钢的耐磨性和焊接性有不利影响。综合考虑硅元素对钢的各种影响,本发明硅含量控制在0.25%~0.30%。
19.(3)本发明中锰是良好的脱氧剂和脱硫剂,锰能降低钢的临界冷却速度,促进马氏体的形成,显著提高淬透性,锰对钢的硬度和冲击韧度影响很大,锰能与铁素体形成无限固溶体,从而提高铁素体和奥氏体的强度和硬度,起到强化钢机体的作用,硬度随锰含量的提高而上升,冲击韧度则随之下降并使钢的晶粒有粗化倾向,增加钢回火脆性的敏感度。综合考虑,锰含量为1.00%~1.40%。
20.(4)本发明中硫元素在钢中易与锰元素等结合形成硫化夹杂物,尤其对钢的横向塑性和韧性不利,因此硫的含量应尽可能地低;磷也是钢中的有害元素,严重损害钢板的塑性和韧性;硫和磷均是不可避免的杂质元素,应该越低越好,考虑到实际的炼钢水平,要求p≤0.010%、s≤0.003%。
21.(5)本发明中铬是耐磨材料的基本元素这一,主要作用是提高钢的淬透性,同时固溶强化基体,细化组织,显著改善钢的抗氧化作用,增加其抗腐蚀的能力,铬和铁形成连续固溶体,与碳形成多种化合物,铬的复杂碳化物(cr,fe)7c3对于钢的性能有显著的影响,特别是提高耐磨性;铬与铁形成金属间化合物σ相(fecr),铬能显著增加钢的淬透性,但亦有增加钢的回火脆性的倾向;铬提高钢的回火脆性,降低钢的马氏体点ms,提高强度和硬度。综合考虑,铬含量控制为0.20%~0.25%。
22.(6)本发明中钼是中强碳化物形成元素,在钢中主要以固溶体相和碳化物的形式存在,缩小γ区,降低ms点,提高钢的淬透性,促进马氏体的形成。在钢中mo与c形成moc,弥散地分布在基体中强化基体,提高钢的硬度,并通过固溶强化来强化基体,提高硬化相的密度,同时也提高碳化物的稳定性,和其他回火脆性元素并存时,mo可以降低或抑制其它元素导致的回火脆性。钼在钢中还能够有效细化铸态组织,提高断面的均匀性,稳定提高回火稳定性,在相变过程中能减缓马氏体板状基体晶界碳化物的析出,从而改善钢的冲击韧度,提高综合性能。但是,随着钼含量的提高,钼碳化物的数量增多,分布在晶界处的碳化物对基体的割裂作用加强,导致钢的韧性下降。综合考虑,钼元素含量为0.20%~0.25%。
23.(7)本发明中镍元素是非碳化物形成元素,也是稳定奥氏体的元素,低合金时细化钢的组织,强化基体,提高钢的强度而不显著降低韧性,同时ni能降低钢的过热敏感性、提高钢的淬透性,且不改变钢的回火脆性,在调质钢中加镍元素可以大幅提高钢的韧性尤其是低温韧性,同时考虑到镍元素属于贵重合金元素,镍含量控制为0.20%~0.25%。
24.(8)本发明中钛是良好的脱氧剂和固定碳和氮的有效元素,细化晶粒、强化铁素体,形成碳化物,缩小γ区;使奥氏体等温转变图右移,降低过热敏感性;同时钛可降低钢的过热敏感性,阻止焊接时钢的晶粒细化而改善焊接性,固溶于固溶体时提高钢的淬透性,形成碳化物时降低钢的淬透性,延迟钢的回火温度,使钢可以在较高的温度下进行回火,ti的加入量也不能太高。综合考虑,钛含量宜控制在0.010%~0.015%。
25.(9)本发明中铌元素在钢中可以阻止再结晶和阻碍再结晶晶粒长大,提高强度;同时,铌元素在钢中可强烈地形成稳定铌的碳化物和氮化物,起到沉淀强化的作用,形成细小
的均匀析出相具有较高硬度,可以提高钢的耐磨性。铌元素能降低钢的过热敏感性及回火脆性,但铌的价格较高不利于降低成本。综合考虑,铌含量控制为0.025%~0.030%。
26.(10)本发明中钒能细化晶粒,提高钢的韧性;但含量高时,形成v4c3,提高钢的高温强度和抗蠕变性能。钒溶于固溶体时提高钢的淬透性,形成碳化物时降低钢的淬透性。同时钒形成碳化物时延迟钢的回火温度,可以使钢在较高的温度下回火。此外,钒还降低钢的过热敏感性,改善钢的焊接性能,并有使钢增加回火脆性的倾向。综合考虑,钒含量控制为0.0030%~0.0040%。
27.(11)本发明中硼是淬透性元素,对提高钢板淬透性尤其是厚规格钢板的淬透性有着重要作用,钢中添加少量的硼元素即可起到较大的增加钢板的淬透性,添加少量的硼可以显著的减少锰、镍、铬、钼等贵重的合金元素添加;但过多的硼元素会增加晶界的偏聚,从而降低钢铁材料的韧塑性,硼元素的含量大于0.007%时,会导致热脆现象。综合考虑,硼含量为0.0014%~0.0016%。
28.本发明采用低碳微合金化的成分设计,提高耐磨钢产品后期可加工性及焊接性能;利用向钢中添加适量合金元素mn、cr、mo、ni等提高钢的淬透性,抑制铁素体转变,促进更多过冷奥氏体发生马氏体体相变;同时添加nb、v、ti等微合金元素,利用其沉淀析出硬质碳氮化物颗粒,提高钢的硬度和耐磨性能;在控制成本下得到优异的性能。通过上述合金元素的相互配合作用,并辅助控制轧制、在线淬火和离线回火的方法,所得钢板截面硬度均匀,表面硬度大于400hv,心部硬度大于390hv,-40℃低温冲击韧性≥100j。板条马氏体中过饱和的碳在低温回火过程中发生扩散,以少量碳化物的形式存在,减小了晶格畸变,缓解了应力集中的情况,使得裂纹不易扩展;nb、v、ti等微合金元素在淬火后以碳化物的形式均匀分布,保证产品在不同厚度上硬度的均匀性;此外,随着回火时间的增加,部分板条状马氏体逐渐合并降低界面能,因此实验钢低温冲击韧性逐渐提高。然而,回火温度超过250℃时,随着回火温度与时间的增加,回火碳化物析出增多,马氏体板条间及表面弥散分布着大量的回火碳化物会降低低温冲击韧性,所以回火温度要低于250℃;同时总结出离线回火时间的特征,离线回火时间=板厚(mm)*5~6min,且回火时间不低于70min,离线回火处理后能达到最优的匹配性能。
29.本发明是基于tmcp工艺技术的在线淬火+离线回火工艺,可以突破高硬度下强韧性匹配的技术难点,实现钢带在线复相组织的精准调控,在保证韧性的基础上获得高硬度、高强度等综合力学性能优异的耐磨钢热轧板,且生产流程短、工艺绿色环保;钢板成型性、焊接性良好,可以实现工业化应用。有效解决了传统马氏体耐磨钢生产工艺流程长,热处理设备要求高,且生产成本高、效率低难题,为马氏体耐磨钢低成本高效益生产创造了更大的空间。
30.本发明具有成本低廉、周期短和工艺简单的特点,所制备的耐磨钢板具有优异的综合性能,能够广泛应用于矿山机械、煤炭挖掘、抓斗斗齿、电力机械以及冶金机械等机械产品上,具有较高工程应用价值。
附图说明
31.图1为实施例1nm400级dq型马氏体耐磨钢板的金相组织图;图2为实施例2nm400级dq型马氏体耐磨钢板的金相组织图;
图3为实施例3nm400级dq型马氏体耐磨钢板的金相组织图;图4为实施例4nm400级dq型马氏体耐磨钢板的金相组织图;图5为实施例5nm400级dq型马氏体耐磨钢板的金相组织图;图6为实施例6nm400级dq型马氏体耐磨钢板的金相组织图;图7为实施例7nm400级dq型马氏体耐磨钢板的金相组织图;图8为实施例8nm400级dq型马氏体耐磨钢板的金相组织图。
具体实施方式
32.下面结合具体实施例对本发明作进一步详细的说明。
33.本发明nm400级dq型马氏体耐磨钢板的化学成分组成及质量百分含量为:c:0.14~0.16%,si:0.25~0.30%,mn:1.00~1.40%,mo:0.20~0.25%,cr:0.20~0.25%,ti:0.010~0.015%,nb:0.025~0.030%,ni:0.20~0.25%,v:0.0030~0.0040%,b:0.0014~0.0016%,p≤0.010%,s≤0.003%,n≤0.005%,余量为fe及不可避免的杂质。钢板厚度为10~25mm,维氏硬度为390~420hv,抗拉强度rm:1100~1400mpa,屈服强度rp0.2:1000~1200mpa,伸长率:10~12%,-40℃低温冲击韧性≥100j/cm2。
34.上述nm400级dq型马氏体耐磨钢板的制备方法,包括加热、粗轧、精轧、在线淬火、离线回火工序,具体操作为:按上述成分配比使用真空冶炼炉熔炼,冶炼完成后加热至1200~1300℃保温120~180min后轧制。粗轧工序,粗轧温度为930~1200℃,5~7道次轧制,单道次变形量为20~30%。精轧工序,精轧温度为800~930℃,4~6道次轧制,单道次变形量为10~15%。精轧后层流冷却至100~120℃,冷却速度20~30℃/s,随后空冷至室温,再进行离线回火。离线回火的温度为200~220℃,回火时间为5~6min/mm,且回火时间不低于70min。
35.实施例1-8,nm400级dq型马氏体耐磨钢板的化学成分及质量百分含量见表1,制备方法中各步骤控制参数见表2、3。
36.对实施例1-8的钢板进行力学性能测试,其中强度按照gb/t228-2002金属材料室温拉伸试验方法进行,低温冲击韧性按gb/t229-2007金属夏比冲击试验方法测定,硬度按照gb/t231.1-2009方法测定,测试结果见表4。
37.表1、实施例1-8耐磨钢板的化学成分及含量(wt%)表2、实施例1-8的轧制各道次分配及出口厚度
表3、实施例1-8加热、轧制、在线淬火和离线回火工艺控制参数表4、实施例1-8钢板的力学性能测试结果由附图1-8可知,本发明耐磨钢板的显微组织主要为板条状马氏体与回火碳化物组成,主要是通过回火马氏体的高硬度和良好的韧性来提高耐磨性能,由表4中数据可知,本发明钢板具有优异的综合力学性能,维氏硬度为390~420hv,抗拉强度rm为1100~1400mpa,屈服强度rp0.2为1000~1200mpa,伸长率为10~12%,-40℃低温冲击韧性≥100j/cm2。与对比例1、2相比,本发明的耐磨钢具有良好的耐磨性能,同时也具有良好的低温冲击韧性。
38.除上述实施例外,本发明还可以有其他实施方式。凡采用等同替换或等效变换形成的技术方案,均落在本发明要求的保护范围。